环境空气 挥发性有机物的测定 美国EPA Method TO-1
【推荐下载】美国环境挥发性有机物的检测技术
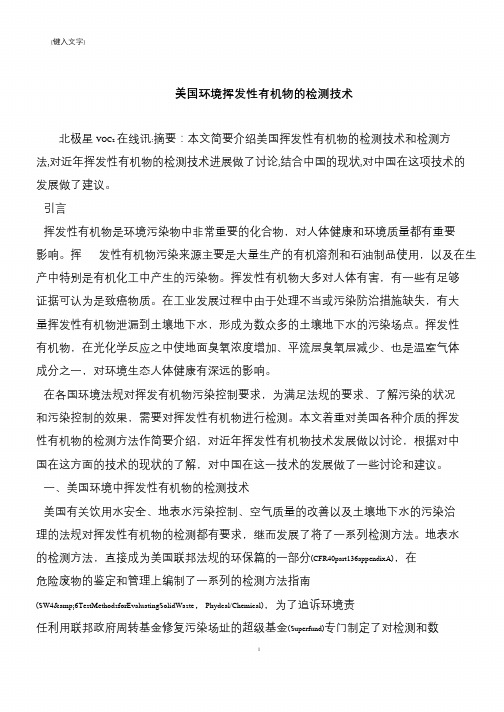
[键入文字]美国环境挥发性有机物的检测技术北极星VOCs 在线讯:摘要:本文简要介绍美国挥发性有机物的检测技术和检测方法,对近年挥发性有机物的检测技术进展做了讨论,结合中国的现状,对中国在这项技术的发展做了建议。
引言挥发性有机物是环境污染物中非常重要的化合物,对人体健康和环境质量都有重要影响。
挥发性有机物污染来源主要是大量生产的有机溶剂和石油制品使用,以及在生产中特别是有机化工中产生的污染物。
挥发性有机物大多对人体有害,有一些有足够证据可认为是致癌物质。
在工业发展过程中由于处理不当或污染防治措施缺失,有大量挥发性有机物泄漏到土壤地下水,形成为数众多的土壤地下水的污染场点。
挥发性有机物,在光化学反应之中使地面臭氧浓度增加、平流层臭氧层减少、也是温室气体成分之一,对环境生态人体健康有深远的影响。
在各国环境法规对挥发有机物污染控制要求,为满足法规的要求、了解污染的状况和污染控制的效果,需要对挥发性有机物进行检测。
本文着重对美国各种介质的挥发性有机物的检测方法作简要介绍,对近年挥发性有机物技术发展做以讨论,根据对中国在这方面的技术的现状的了解,对中国在这一技术的发展做了一些讨论和建议。
一、美国环境中挥发性有机物的检测技术美国有关饮用水安全、地表水污染控制、空气质量的改善以及土壤地下水的污染治理的法规对挥发性有机物的检测都有要求,继而发展了将了一系列检测方法。
地表水的检测方法,直接成为美国联邦法规的环保篇的一部分(CFR40part136appendixA),在危险废物的鉴定和管理上编制了一系列的检测方法指南(SW4&6TestMethodsforEvaluatingSolidWaste,Phydcal/Chemical),为了追诉环境责任利用联邦政府周转基金修复污染场址的超级基金(Superfund)专门制定了对检测和数1。
(环境管理)环境空气挥发性有机物的测定-T吸附GCMS法

(环境管理)环境空⽓挥发性有机物的测定-T吸附GCMS 法美国EPA TO-17 ⽅法分析环境空⽓中挥发性有机物研究施巍蔡浩洋(⼤连市环境监测中⼼⼤连 116023)摘要选⽤美国EPA TO-17⽅法中的⼀种类型的混合型填料吸附管,分析环境空⽓中挥发性有机物。
通过实验验证EPA TO-17⽅法的可⾏性和可操作性,并得到校正曲线、相关系数、检出限等数据。
关键词挥发性有机物吸附管吸附解析1 前⾔1.1 ⽅法概述本⽅法⽤于环境空⽓中挥发性有机化合物的采集和测定。
本次研究的挥发性有机化合物是指能由35mm Carbopack?B和10mm Carbosieve?SⅢ及Carboxen?1000组成的吸附管捕集,并能⽤热脱附GC/MS技术测定的挥发性有机化合物。
1.2 国内外概况随着⼯业的快速发展,有机物的污染逐步显现。
⽬前,许多国家都根据本国⼤⽓环境污染状况制定相应的防治法或环境标准。
对环境空⽓中的挥发性有机物测定,美国EPA TO-1⽅法采⽤的是Tenax采样GC-MS法,其分析的化合物为沸点⼤约在80℃-200℃的⾮极性有机化合物。
TO-2是采⽤碳分⼦筛采样GC-MS法,主要采集含碳数少的、挥发性强的有机物。
TO-14和TO-15采⽤的是采样罐采样GC-MS法,其与TO-1⽅法区别是进样⽅式不⼀样,能检测化合物⽐TO-1多,但因为其进样设备昂贵,现阶段很难在我国推⼴。
TO-17⽅法采⽤的是固体填料吸附管采样GC-MS法,不同的填料类型可测定不同的挥发性有机物,采集和测定的化合物种类较多。
我国《空⽓和废⽓监测分析⽅法》(第四版)采⽤了固体吸附GC-MS法和采样罐采样GC-MS法,这两种⽅法都是C类⽅法⽽且没有给出检出限和准确度等数据。
国标GB11737-89和GB14677-93也是采⽤固体吸附,⼆硫化碳洗脱或热解析的⽅法,但其能测定的⽬标化合物太少,只局限于苯系物。
综合分析,本论⽂在相关⽂献资料和EPA相关⽅法基础上,提出并建⽴⽤混合型填料吸附管吸附、GC-MS法测定环境空⽓中的挥发性有机物的⽅法。
环境空气voc限值

环境空气voc限值
VOC(挥发性有机物)是指在环境条件下易挥发的有机化合物。
不同国家和地区针对环境空气中的VOC都有不同的限值标准。
以下是一些国家和地区的环境空气VOC限值示例:
1.美国环保署(EPA)限值标准:
- 总非甲烷挥发性有机物(TVOC):9.0 ppm(小时平均)
- 苯:1.3 ppb(年平均)
2.欧盟限值标准(根据室内环境):
- TVOC:0.3 mg/m³(小时平均)
- 苯:5 μg/m³(小时平均)
3.中国环境空气质量标准(GB 3095-2012):
- TVOC:0.6 mg/m³(小时平均)
- 苯:5 μg/m³(小时平均)
需要注意的是,每个国家和地区的限值标准可能会根据特定情况和需求进行调整和更新。
另外,不同地区可能还会设定其他特定的VOC限制值,如甲醛、醋酸乙烯等。
因此,具体的环境空气VOC限值应以当地相关法规和标准为准。
epa standard method 533

epa standard method 533
EPA(美国环境保护局)Standard Method 533是关于气体监测的方法,具体名为《Method 533:Determination of Volatile Organic Compounds (VOCs) in Air by Adsorption on Activated Carbon and Gas Chromatography》。
这个方法主要用于测定空气中的挥发性有机化合物(VOCs)。
在这个方法中,样品通过吸附在活性炭上收集,然后使用气相色谱法进行分析。
方法涵盖了吸附剂的选择、采样设备、样品处理和分析等步骤。
活性炭吸附剂具有较高的吸附能力,可以有效地捕获空气中的VOCs。
气相色谱法用于分离和定量吸附剂上的VOCs,从而得出空气中VOCs的浓度。
EPA Standard Method 533为监测空气中的挥发性有机化合物提供了可靠的方法,有助于评估空气质量并制定相应的环境保护措施。
该方法在我国环保领域也有广泛应用,以保障空气质量和人民健康。
环境空气挥发性有机物的特征及来源
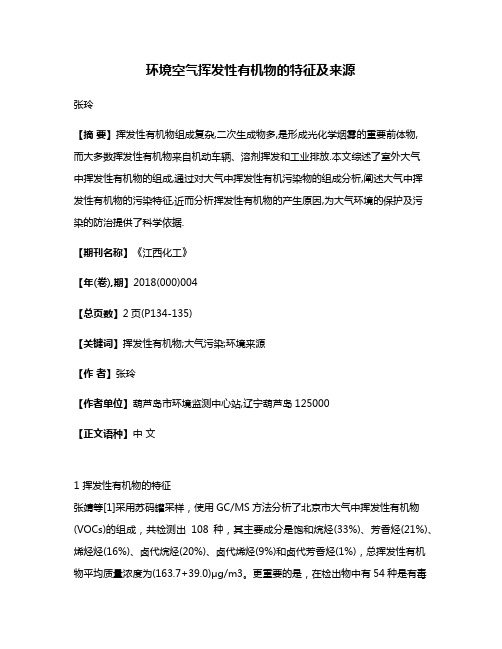
环境空气挥发性有机物的特征及来源张玲【摘要】挥发性有机物组成复杂,二次生成物多,是形成光化学烟雾的重要前体物,而大多数挥发性有机物来自机动车辆、溶剂挥发和工业排放.本文综述了室外大气中挥发性有机物的组成,通过对大气中挥发性有机污染物的组成分析,阐述大气中挥发性有机物的污染特征,近而分析挥发性有机物的产生原因,为大气环境的保护及污染的防治提供了科学依据.【期刊名称】《江西化工》【年(卷),期】2018(000)004【总页数】2页(P134-135)【关键词】挥发性有机物;大气污染;环境来源【作者】张玲【作者单位】葫芦岛市环境监测中心站,辽宁葫芦岛125000【正文语种】中文1 挥发性有机物的特征张靖等[1]采用苏码罐采样,使用GC/MS方法分析了北京市大气中挥发性有机物(VOCs)的组成,共检测出108种,其主要成分是饱和烷烃(33%)、芳香烃(21%)、烯烃烃(16%)、卤代烷烃(20%)、卤代烯烃(9%)和卤代芳香烃(1%),总挥发性有机物平均质量浓度为(163.7+39.0)μg/m3。
更重要的是,在检出物中有54种是有毒有害的物质,主要成分是苯系物和卤代烃,其中苯,甲苯,丙烯,1,3-丁二烯,氯乙烯和1,2-二氯乙烷是含量最高的组分。
魏思棋等[2]参照美国EPA TO-17的方法对天津市不同城市功能区中环境空气中挥发性有机物(VOCs)夏季和冬季中的组成及浓度水平,共检出62种挥发性有机物,冬季挥发性有机物浓度水平低于夏季;苯系物稳定存在于各功能区且所占比例最高;挥发性有机物的主要来源是机动车尾气。
最大的关键活性物种为丙烯乙烯甲苯二甲苯以及丁烯类物质。
杭维玲等[3]用安装分流旁路的KB-6A采样器及不锈钢气体采样管采样,用菲尼根GCQ气质联用仪分析。
得出南京市不同功能区(交通区、商业旅游区、居住区、工业区和清洁对照点)环境空气中挥发性有机物(VOCs)在一年四季中的组成及浓度水平。
共检出189种挥发性有机物,并随气温下降而减少;苯系物稳定存在于各功能区,浓度秋季最高。
挥发性有机物污染防治政策及监测技术综述
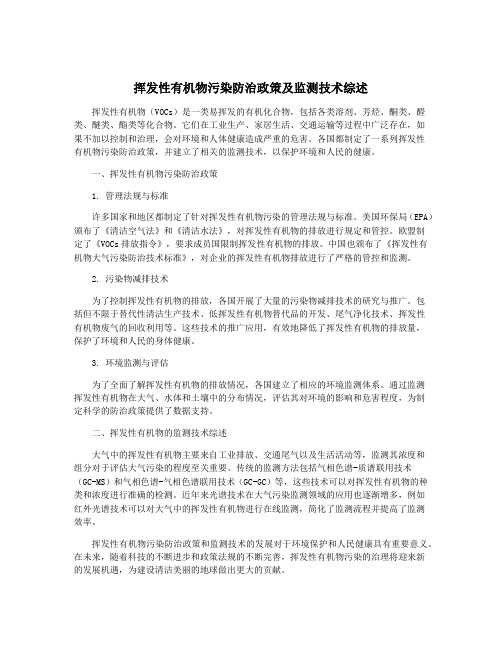
挥发性有机物污染防治政策及监测技术综述挥发性有机物(VOCs)是一类易挥发的有机化合物,包括各类溶剂、芳烃、酮类、醛类、醚类、酯类等化合物。
它们在工业生产、家居生活、交通运输等过程中广泛存在,如果不加以控制和治理,会对环境和人体健康造成严重的危害。
各国都制定了一系列挥发性有机物污染防治政策,并建立了相关的监测技术,以保护环境和人民的健康。
一、挥发性有机物污染防治政策1. 管理法规与标准许多国家和地区都制定了针对挥发性有机物污染的管理法规与标准。
美国环保局(EPA)颁布了《清洁空气法》和《清洁水法》,对挥发性有机物的排放进行规定和管控。
欧盟制定了《VOCs排放指令》,要求成员国限制挥发性有机物的排放。
中国也颁布了《挥发性有机物大气污染防治技术标准》,对企业的挥发性有机物排放进行了严格的管控和监测。
2. 污染物减排技术为了控制挥发性有机物的排放,各国开展了大量的污染物减排技术的研究与推广。
包括但不限于替代性清洁生产技术、低挥发性有机物替代品的开发、尾气净化技术、挥发性有机物废气的回收利用等。
这些技术的推广应用,有效地降低了挥发性有机物的排放量,保护了环境和人民的身体健康。
3. 环境监测与评估为了全面了解挥发性有机物的排放情况,各国建立了相应的环境监测体系。
通过监测挥发性有机物在大气、水体和土壤中的分布情况,评估其对环境的影响和危害程度,为制定科学的防治政策提供了数据支持。
二、挥发性有机物的监测技术综述大气中的挥发性有机物主要来自工业排放、交通尾气以及生活活动等,监测其浓度和组分对于评估大气污染的程度至关重要。
传统的监测方法包括气相色谱-质谱联用技术(GC-MS)和气相色谱-气相色谱联用技术(GC-GC)等,这些技术可以对挥发性有机物的种类和浓度进行准确的检测。
近年来光谱技术在大气污染监测领域的应用也逐渐增多,例如红外光谱技术可以对大气中的挥发性有机物进行在线监测,简化了监测流程并提高了监测效率。
挥发性有机物污染防治政策和监测技术的发展对于环境保护和人民健康具有重要意义。
环境空气 挥发性有机物的测定 美国EPA Method TO-3
METHOD TO-3 REVISION 1.0April, 1984 METHOD FOR THE DETERMINATION OF VOLATILE ORGANIC COMPOUNDSIN AMBIENT AIR USING CRYOGENIC PRECONCENTRATION TECHNIQUES AND GAS CHROMATOGRAPHY WITH FLAME IONIZATION ANDELECTRON CAPTURE DETECTION1.Scope1.1This document describes a method for the determination ofhighly volatile compounds having boiling points in therange of -10 to 200E C.1.2The methodology detailed in this document is currentlyemployed by numerous laboratories (1-4;8-11).Modifications to this methodology should be accompaniedby appropriate documentation of the validity andreliability of these changes.2.Applicable Documents2.1ASTM StandardsD1356 Definition of Terms Related to Atmospheric Samplingand AnalysisE 355 Recommended Practice for Gas Chromatography Termsand Relationships2.2Other DocumentsAmbient Air Studies (1-4).U. S. EPA Technical Assistance Document (5).3.Summary of Method3.1Ambient air analyses are performed as follows. Acollection trap, as illustrated in Figure 1, is submergedin either liquid oxygen or argon. Liquid argon is highlyrecommended for use because of the safety hazardassociated with liquid oxygen. With the sampling valvein the fill position an air sample is then admitted intothe trap by a volume measuring apparatus. In themeantime, the column oven is cooled to a sub-ambienttemperature (-50E C). Once sample collection iscompleted, the valve is switched so that the carrier gassweeps the contents of the trap onto the head of thecooled GC column. Simultaneously, the liquid cryogen isremoved and the trap is heated to assist the sampletransfer process. The GC column is temperatureprogrammed and the component peaks eluting from thecolumns are identified and quantified using flameionization and/or electron capture detection. Alternatedetectors (e.g., photoionization) can be used asappropriate. An automated system incorporating thesevarious operations as well as the data processingfunction has been described in the literature (8,9).3.2Due to the complexity of ambient air samples, highresolution (capillary column) GC techniques arerecommended. However, when highly selective detectors(such as the electron capture detector) are employed,packed column technology without cryogenic temperatureprogramming can be effectively utilized in some cases.4.Significance4.1Volatile organic compounds are emitted into theatmosphere from a variety of sources including industrialand commercial facilities, hazardous waste storagefacilities, etc. Many of these compounds are toxic,hence knowledge of the levels of such materials in theambient atmosphere is required in order to determinehuman health impacts.4.2Because these organic species are present at ppb levelsor below, some means of sample preconcentration isnecessary in order to acquire sufficient material foridentification and quantification. The two primarypreconcentration techniques are cryogenic collection andthe use of solid adsorbents. The method described hereininvolves the former technique.5.DefinitionsDefinitions used in this document and any user prepared SOPs should be consistent with ASTM D1356(6). All abbreviations and symbols are defined within this document at the point of use.6.Interferences/Limitations6.1Compounds having similar GC retention times willinterfere in the method. Replacing the flame ionizationdetector with more selective detection systems will helpto minimize these interferences. Chlorinated species, inparticular, should be determined using the electroncapture detector to avoid interference from volatilehydrocarbons.6.2An important limitation of the technique is thecondensation of moisture in the collection trap. Thepossibility of ice plugging the trap and stopping theflow is of concern, and water subsequently transferred tothe capillary column may also result in flow stoppage andcause deleterious effects to certain column materials.Use of permaselective Nafion® tubing in-line before thecryogenic trap avoids this problem; however, the materialmust be used with caution because of possible losses ofcertain compounds. Another potential problem iscontamination from the Nafion® tubing. The user shouldconsult the literature (7-12) for details on the use ofpermeation-type driers.7.Apparatus7.1Gas chromatograph/Flame Ionization/Electron CaptureDetection System - must be capable of subambienttemperature programming. A recent publication (8)describes an automated GC system in which the cryogenicsampling and analysis features are combined. This systemallows simultaneous flame ionization and electron capturedetection.7.2Six-port sampling valve - modified to accept a samplecollection trap (Figure 1).7.3Collection trap - 20 cm x 0.2 cm I.D. stainless steeltubing packed with 60/80 mesh silanized glass beads andsealed with glass wool. For the manual system (Section9.2) the trap is externally wrapped with 28 gauge (duplexand fiberglass insulated) type "K" thermocouple wire.This wire, beaded at one end, is connected to a powerstatduring the heating cycle. A thermocouple is alsoattached to the trap as shown in Figure 1.7.4Powerstat - for heating trap.7.5Temperature readout device - for measuring traptemperature during heating cycle.7.6Glass dewar flask - for holding cryogen.7.7Sample volume measuring apparatus - capable of accuratelyand precisely measuring a total sample volume up to 500cc at sampling rates between 10 and 200 cc/minute. SeeSection 9.7.8Stopwatch.7.9Dilution container for standards preparation - glassflasks or Teflon (Tedlar) bags, .002 inch film thickness(see Figure 2).7.10Liquid microliter syringes - 5-50 F l for injecting liquidstandards into dilution container.7.11Volumetric flasks - various sizes, 1-10 mL.7.12GC column - Hewlett Packard 50 meter methyl siliconecross-linked fused silica column (.3 mm I.D., thick film)or equivalent.7.13Mass flow controller - 10-200 mL/minute flow controlrange.7.14Permeation drier - PermaPure® - Model MD-125F, orequivalent. Alternate designs described in theliterature (7-12) may also be acceptable.8.Reagents and Materials8.1Glass beads - 60/80 mesh, silanized.8.2Glasswool - silanized.8.3Helium - zero grade compressed gas, 99.9999%.8.4Hydrogen - zero grade compressed gas, 99.9999%.8.5Air - zero grade compressed gas.8.6Liquid argon (or liquid oxygen).8.7Liquid nitrogen.8.8SRM 1805 - benzene in nitrogen standard. Available fromthe National Bureau of Standards. Additional suchstandards will become available in the future.8.9Chemical standards - neat compounds of interest, highestpurity available.9.Sampling and Analysis ApparatusTwo systems are described below which allow collection of an accurately known volume of air (100-1000 mL) onto a cryogenically cooled trap. The first system (Section 9.1) is an automated device described in the literature (8,9). The second system (Section 9.2) is a manual device, also described in the literature(2).9.1The automated sampling and analysis system is shown inFigure 3. This system is composed of an automated GC system (Hewlett Packard Model 5880A, Level 4, or equivalent) and a sample collection system (Nutech Model 320-01, or equivalent). The overall system is described in the literature (8).9.1.1The electronic console of the sampling unitcontrols the mechanical operation of the six-port valve and cryogenic trapping componentsas well as the temperatures in each of thethree zones (sample trap, transfer line, andvalve).9.1.2The valve (six-port air activated, SeiscorModel 8 or equivalent) and transfer line areconstantly maintained at 120E C. During samplecollection the trap temperature is maintainedat -160 + 5E C by a flow of liquid nitrogencontrolled by a solenoid valve. A cylindrical250 with heater, held in direct contact withthe trap, is used to heat the trap to 120E C in60 seconds or less during the sampledesorption step. The construction of thesample trap is described in Section 7.3.9.1.3The sample flow is controlled by a pump/massflow controller assembly, as shown in Figure3. A sample flow of 10-100 mL/minute isgenerally employed, depending on the desiredsampling period. A total volume of 100-1000mL is commonly collected.9.1.4In many situations a permaselective drier(e.g., Nafion®) may be required to removemoisture from the sample. Such a device isinstalled at the sample inlet. Twoconfigurations for such devices are available.The first configuration is the tube and shelltype in which the sample flow tube issurrounded by an outer shell through which acountercurrent flow of clean, dry air ismaintained. The dry air stream must be freefrom contaminants and its flow rate should be3-4 times greater than the sample flow toachieve effective drying. A secondconfiguration (7) involves placing a dryingagent, e.g., magnesium carbonate, on theoutside of the sample flow tube. Thisapproach eliminates the need for a source ofclean air in the field. However, contaminationfrom the drying agent can be a problem.V s ')P760×298TA%2739.2The manual sampling consists of the sample volumemeasuring apparatus shown in Figure 4 connected to the cryogenic trap/GC assembly shown in Figure 1. The operation of this assembly is described below.9.2.1Pump-Down PositionThe purpose of the pump-down mode of operationis to evacuate the ballast tank in preparationfor collecting a sample as illustrated inFigure 4. (While in this position, helium canalso be utilized to backflush the sample line,trap, etc. However, this cleaning procedureis not normally needed during most samplingoperations). The pump used for evacuating thesystem should be capable of attaining 200 torrpressure.9.2.2Volume Measuring PositionOnce the system has been sufficientlyevacuated, the 4-way ball valve is switched toprepare for sample collection. The 3-positionvalve is used to initiate sample flow whilethe needle valve controls the rate of flow.9.2.3Sample Volume CalculationThe volume of air that has passed through thecollection trap corresponds to a known changein pressure within the ballast tank (asmeasure by the Wallace Tiernan gauge).Knowing the volume, pressure change, andtemperature of the system, the ideal gas lawcan be used to calculate the number of molesof air sampled. On a volume basis, thisconverts to the following equation:whereV =Volume sampled at 760 mm Hg pressure ands25E C.)P =Change in pressure within the ballasttank, mm of Hg.V =Volume of ballast tank and gauge.T =Temperature of ballast tank, E C.AThe internal volume of the ballast tank and gauge can be determined either by H O displacement or by injecting2calibrated volumes of air into the system using large volume syringes, etc.10.Sampling and Analysis Procedure - Manual Device10.1This procedure assumes the use of the manual samplingsystem described in Section 9.2.10.2Prior to sample collection, the entire assembly should beleak-checked. This task is accomplished by sealing thesampling inlet line, pumping the unit down and placingthe unit in the flow measuring mode of operation. Aninitial reading on the absolute pressure gauge is takenand rechecked after 10 minutes. No apparent changeshould be detected.10.3Preparation for sample collection is carried out byswitching the 6-port valve to the "fill" position andconnecting the heated sample line to the sample source.Meanwhile the collection trap is heated to 150E C (orother appropriate temperature). The volume measuringapparatus is pumped-down and switched to the flowmeasuring mode. The 3-position valve is opened and aknown volume of sample is then passed through the heatedsample line and trap to purge the system.10.4After the system purge is completed, the 3-position valveis closed and the corresponding gauge pressure isrecorded. The collection trap is then immersed into adewar of liquid argon (or liquid oxygen) and the 3-position valve is temporarily opened to draw in a knownvolume of air, i.e. a change in pressure corresponds toa specific volume of air (see Section 9). Liquidnitrogen cannot be used as the cryogen since it will alsocondense oxygen from the air. Liquid oxygen representsa potential fire hazard and should not be employed unlessabsolutely necessary.10.5After sample collection is completed, the 6-port valve isswitched to the inject position, the dewar is removed andthe trap is heated to 150E C to transfer the samplecomponents to the head of the GC column which isinitially maintained at -50E C. Temperature programmingis initiated to elute the compounds of interest.10.6 A GC integrator (or data system if available) isactivated during the injection cycle to provide componentidentification and quantification.11.Sampling and Analysis Procedure - Automated Device11.1This procedure assumes the use of the automated systemshown in Figure 3. The components of this system arediscussed in Section 9.1.11.2Prior to initial sample collection the entire assemblyshould be leak-checked. This task is completed bysealing the sample inlet line and noting that the flowindication or the mass flow controller drops to zero(less than 1 mL/minute).11.3The sample trap, valve, and transfer line are heated to120E C and ambient air is drawn through the apparatus(-60mL/minute) for a period of time 5-10 minutes to flushthe system, with the sample valve in the inject position.During this time the GC column is maintained at 150E C tocondition the column.11.4The sample trap is then cooled to -160 + 5E C using acontrolled flow of liquid nitrogen. Once the traptemperature has stabilized, sample flow through the trapis initiated by placing the valve in the inject positionand the desired volume of air is collected.11.5During the sample collection period the GC column isstabilized at -50E C to allow for immediate injection ofthe sample after collection.11.6At the end of the collection period the valve isimmediately placed in the inject position, and thecryogenic trap is rapidly heated to 120E C to desorb thecomponents onto GC column. The GC temperature programand data acquisition are initiated at this time.11.7At the desired time the cryogenic trap is cooled to-160E C, the valve is returned to the collect position andthe next sample collection is initiated (to coincide withthe completion of the GC analysis of the previoussample).12.Calibration ProcedurePrior to sample analysis, and approximately every 4-6 hours thereafter, a calibration standard must be analyzed, using the identical procedure employed for ambient air samples (either Section 10 or 11). This section describes three alternative approaches for preparing suitable standards.12.1Teflon® (or Tedlar®) Bags12.1.1The bag (nominal size; 20L) is filled withzero air and leak checked. This can be easilyaccomplished by placing a moderate weight(text book) on the inflated bag and leavingovernight. No visible change in bag volumeindicates a good seal. The bag should also beequipped with a quick-connect fitting forsample withdrawal and an insertion port forliquid injections (Figure 2).12.1.2Before preparing a standard mixture, the bagis sequentially filled and evacuated with zeroair (5 times). After the 5th filling, asample blank is obtained using the samplingprocedure outlined in Section 10.12.1.3In order to prepare a standard mixture, thebag is filled with a known volume of zero air.This flow should be measured via a calibratedmass flow controller or equivalent flowmeasuring device. A measured aliquot of eachanalyte of interest is injected into the bagthrough the insertion port using a microlitersyringe. For those compounds with vaporpressures lower than benzene or for stronglyadsorbed species, the bag should be heated(60E C oven) during the entire calibrationperiod.12.1.4To withdraw a sample for analysis, thesampling line is directly connected to thebag. Quick connect fittings allow this hook-up to be easily accomplished and alsominimizes bag contamination from laboratoryair. Sample collection is initiated asdescribed.12.2Glass Flasks12.2.1If a glass flask is employed (Figure 2) theexact volume is determined by weighing theflask before and after filling with deionizedwater. The flask is dried by heating at200E C.12.2.2To prepare a standard, the dried flask isflushed with zero air until cleaned (i.e., ablank run is made). An appropriate aliquot ofeach analyte is injected using the sameprocedures as described for preparing bagstandards.12.2.3To withdraw a standard for analysis, the GCsampling line is directly connected to theflask and a sample obtained. However, becausethe flask is a rigid container, it will notremain at atmospheric pressure after samplinghas commenced. In order to prevent room airleakage into the flask, it is recommended thatno more than 10% of the initial volume beexhausted during the calibration period (i.e.,200cc if a 2 liter flask is used).12.3Pressurized Gas Cylinders12.3.1Pressurized gas cylinders containing selectedanalytes at ppb concentrations in air can beprepared or purchased. A limited number ofanalytes (e.g., benzene, propane) areavailable from NBS.12.3.2Specialty gas suppliers will prepare customgas mixtures, and will cross reference theanalyte concentrations to an NBS standard foran additional charge. In general, the usershould purchase such custom mixtures,ratherthan attempting to prepare them becauseof the special high pressure filling apparatusrequired. However, the concentrations shouldbe checked, either by the supplier or the userusing NBS reference materials.12.3.3Generally, aluminum cylinders are suitablesince most analytes of potential interest inthis method have been shown to be stable forat least several months in such cylinders.Regulators constructed of stainless steel andTeflon® (no silicon or neoprene rubber).12.3.4Before use the tank regulator should beflushed by alternately pressuring with thetank mixture, closing the tank valve, andventing the regulator contents to theatmosphere several times.12.3.5For calibration, a continuous flow of the gasmixture should be maintained through a glassor Teflon® manifold from which the calibrationstandard is drawn. To generate variouscalibration concentrations, the pressurizedgas mixture can be diluted, as desired, withzero grade air using a dynamic dilution system(e.g., CSI Model 1700).13.Calibration Strategy13.1Vapor phase standards can be prepared with either neatliquids or diluted liquid mixtures depending upon theconcentration levels desired. It is recommended thatbenzene also be included in this preparation scheme sothat flame ionization detector response factors, relativeto benzene, can be determined for the other compounds.The benzene concentration generated in this fashionshould be cross-checked with an NBS (e.g., SRM 1805) foraccuracy determinations.13.2Under normal conditions, weekly multipoint calibrationsshould be conducted. Each multipoint calibration shouldinclude a blank run and four concentration levels for thetarget species. The generated concentrations shouldbracket the expected concentration of ambient airsamples.13.3 A plot of nanograms injected versus area using a linearleast squares fit of the calibration data will yield thefollowing equation:Y'A%BXwhereY = quantity of component, nanogramsA = interceptB = slope (response factor)If substantial nonlinearity is present in the calibrationcurve a quadratic fit of the data can be used:Y'A%BX%CX2whereC = constantAlternatively, a stepwise multilevel calibration scheme may be used if more convenient for the data system in use.14.Performance Criteria and Quality AssuranceThis section summarizes the quality assurance (QA) measures and provides guidance concerning performance criteria which should be achieved within each laboratory.14.1Standard Operating Procedures (SOPs)14.1.1Each user should generate SOPs describing thefollowing activities as accomplished in theirlaboratories:1)assembly, calibration and operation ofthe sampling system.2)preparation and handling of calibrationstandards.3)assembly, calibration and operation ofthe GC/FID system and4)all aspects of data recording andprocessing.14.1.2SOPs should provide specific stepwiseinstructions and should be readily availableto, and understood by, the laboratorypersonnel conducting the work.14.2Method Sensitivity, Precision and Accuracy14.2.1System sensitivity (detection limit) for eachcomponent is calculated from the data obtainedfor calibration standards. The detectionlimit is defined asDL'A%3.3SwhereDL =calculated detection limit in nanogramsinjected.A =intercept calculated in Section 13.S =standard deviation of replicatedetermination of the lowest levelstandard (at least three determinationsare required).For many compounds detection limits of 1 to 5nanograms are found using the flame ionizationdetection. Lower detection limits can beobtained for chlorinated hydrocarbons usingthe electron capture detector.14.2.2 A precision of + 5% (relative standarddeviation) can be readily achieved atconcentrations 10 times the detection limit.Typical performance data are included in Table1.14.2.3Method accuracy is estimated to be within +10%, based on National Bureau of Standardcalibrated mixtures.REFERENCES1.Holdren, M., Spicer, C., Sticksel, P., Nepsund, K., Ward, G.,and Smith, R., "Implementation and Analysis of Hydrocarbon Grab Samples from Cleveland and Cincinnati 1981 Ozone Monitoring Study", EPA-905/4-82-001. U.S. Environmental Protection Agency, Research Triangle Park, North Carolina, 1982.2.Westberg, H., Rasmussen, R., and Holdren, M., "GasChromatographic Analysis of Ambient Air for Light Hydrocarbons Using a Chemically Bonded Stationary Phase", Anal. Chem. 46, 1852-1854, 1974.3.Lonneman, W. A., "Ozone and Hydrocarbon Measurements in RecentOxidant Transport Studies", in Int. Conf. on Photochemical Oxidant Pollutant and Its Control Proceedings, EPA-600/3-77-001a, 1977.4.Singh, H., "Guidance for the Collection and Use of AmbientHydrocarbon Species Data in Development of Ozone Control Strategies", EPA-450/4-80-008. U.S. Environmental Protection Agency, Research Triangle Park, North Carolina, 1980.5.Riggin, R. M., "Technical Assistance Document for Sampling andAnalysis of Toxic Organic Compounds in Ambient Air", EPA-600/4-83-027. U.S. Environmental Protection Agency, Research Triangle Park, North Carolina, 1983.6.Annual Book of ASTM Standards, Part 11.03, "AtmosphericAnalysis", American Society for Testing and Materials, Philadelphia, Pennsylvania, 1983.7.Foulger, B. E. and P. G. Sinamouds, "Drier for Field Use inthe Determination of Trace Atmospheric Gases", Anal. Chem., 51, 1089-1090, 1979.8.Pheil, J. D. and W. A. McClenney, "Reduced TemperaturePreconcentration Gas Chromatographic Analysis of Ambient Vapor-Phase Organic Compounds: System Automation", Anal.Chem., submitted, 1984.9.Holdren, M. W., W. A. McClenney, and R. N. Smith "ReducedTemperature Preconcentration and Gas Chromatographic Analysis of Ambient Vapor-Phase Organic Compounds: System Performance", Anal. Chem., submitted, 1984.10.Holdren, M., S. Rust, R. Smith, and J. Koetz, "Evaluation ofCryogenic Trapping as a Means for Collecting Organic Compounds in Ambient Air", Draft Final Report on Contract No. 68-02-3487, 1984.11.Cox, R. D. and R. E. Earp, "Determination of Trace LevelOrganics in Ambient Air by High-Resolution Gas Chromatography with Simultaneous Photoionization and Flame Ionization Detection", Anal. Chem. 54, 2265-2270, 1982.12.Burns, W. F., O. T. Tingy, R. C. Evans and E. H. Bates,"Problems with a Nafion® Membrane Dryer for Chromatographic Samples", J. Chrom. 269, 1-9, 1983.Figure 1. Schematic of Six-Port Valve Used for Sample Collection.Figure 2. Dilution Containers for Standard MixturesFigure 3. Automated Sampling and Analysis System for Cryogenic TrappingFigure 4. Sample Volume Measuring Apparatus。
浅论环境空气中挥发性有机物的测定方法及注意事项
浅论环境空气中挥发性有机物的测定方法及注意事项[摘要] 本文结合笔者多年实践工作经验,针对环境空气中挥发性有机物的测定方法做出分析。
环境空气中VOCs 的测定方法是国内外研究的焦点。
本文通过对国内外环境空气中VOCs 的测定方法进行总结,结合我国实际情况,对测定环境空气中VOCs的两种方法(固体吸附/热脱附/ GC 或GC-MS方法和罐采样/冷冻预浓缩/ GC 或GC-MS方法)进行分析,从而得出更具可操作性的测定环境空气中挥发性有机物的测定方法及注意事项。
[关键字]环境空气挥发性有机物测定方法0 引言环境空气中的挥发性有机物(V olatile organiccompounds,简称VOCs),在大气环境当中是主要的污染物,这类的化合物不仅存在一定的毒性,而且还容易致癌,并且还会产生光化学烟雾。
在实际空气当中,VOCs的成分相对而言比较复杂,不管是室内还是室外的空气质量都有着极大的影响,在实际生活中人们吸入气体也会影响身体健康的状况。
随着社会的不断高速发展,人们针对VOCs 所产生的负面影响也越来越显得重视,就目前而言其也同时成为了国内外重点的研究对象。
VOCs所体现出来的主要成分有烃类和氧烃以及含卤烃类等,这些成分普遍存在室内和室外空气当中,并且它们之间相互融合形成一类复杂的有机污染物。
综合实际情况,我们可以发现其产生的主要原因,是由于当前社会中使用的各种化工原料,而且还有烟草或者树木在燃烧的过程中没有达到完全燃烧的条件也会产生这些成分;还有在公路上行驶的汽车所排放出来的尾气,以及自然界中生长的植物也会自动排放而产生VOCs。
随着现代社会不断的高速发展,人们对于建筑的设计也是不断的推陈出新,建筑物的结构也发生了翻天覆地的变化,因此在实践中也使得新型的建材以及保温材料和室内装潢材料,在当今建筑中得到了前所未有的运用。
与此同时,还有各种的化妆品以及清香、除臭剂等诸多品种的洗涤剂,在现代社会家庭中广泛的得到应用,在这些物品当中有些能够直接挥发出有机化合物,而有些在长期缓解过程中释放出低分子化合物,那么针对当前的环境空气都会造成很大的影响。
voc收集标准
voc收集标准
VOC(挥发性有机化合物)是一类能够在常温下挥发进入大
气中的化合物。
由于VOC对环境和人体健康产生负面影响,
因此需要进行监测和控制。
为了统一监测和评估VOC,相关
的收集标准被制定出来。
以下是常见的VOC收集标准:
1. 美国环境保护局(EPA)方法:EPA制定了一系列方法来收集和分析VOC样品,如EPA Method 25A,Method 25B等。
2. 国际标准化组织(ISO)标准:ISO制定了一系列关于VOC
监测和控制的标准,如ISO 16000系列标准,用于评估室内空
气质量中的VOC含量。
3. 欧洲标准(EN):欧洲标准委员会制定了一系列关于VOC
监测和控制的标准,如EN 16516,EN 12338等。
4. ASTM国际标准:ASTM国际标准组织制定了一系列关于VOC收集和分析的标准,如ASTM D6196,ASTM D2369等。
这些收集标准提供了关于VOC样品收集和分析方法的指南,
以确保监测结果的准确性和可比性。
同时,它们也为政府、环境监测机构、研究机构和工业企业提供了参考,以制定相应的监测和控制策略。
挥发性有机物污染防治政策及监测技术综述
挥发性有机物污染防治政策及监测技术综述挥发性有机物污染是当前环境保护领域的一大难题,严重影响着人们的健康和生活质量。
为了有效防治挥发性有机物污染,各国都制定了相应的环境保护政策,并不断推动监测技术的发展,以提高污染防治的效果。
本文将结合挥发性有机物污染防治政策与监测技术的发展情况,进行综述,为加强环境保护、改善人民生活水平提供参考。
一、挥发性有机物污染防治政策1.1 美国挥发性有机物排放标准美国作为环保领域的领先国家,其挥发性有机物排放标准为世界公认的标杆。
美国环境保护署(EPA)颁布了《清洁空气法案》和《清洁水法案》,明确规定了各类挥发性有机物的排放标准和控制措施,其中包括VOCs的限制排放标准以及工业设施的排放监测要求等。
1.2 欧盟挥发性有机物排放标准欧盟也针对挥发性有机物制定了严格的排放标准,其中包括《大气污染物排放指令》和《工业废气排放指令》等相关法规,通过减少VOCs排放量、使用低挥发性涂料和溶剂等方式,要求各成员国在一定期限内实现挥发性有机物排放量的大幅降低。
1.3 中国挥发性有机物污染防治政策中国近年来也加大了对挥发性有机物的管理力度,相继颁布了《挥发性有机物大气污染防治技术政策》、《挥发性有机物大气排放标准》等法规,要求各类工业企业采取有效的治理措施,控制VOCs的排放量,提高环保意识和责任意识。
二、挥发性有机物污染监测技术2.1 VOCs在线监测技术VOCs在线监测技术是目前挥发性有机物污染监测的主流技术之一,通过在工业园区、城市环境中建立在线监测站点,实时采集并分析大气中的挥发性有机物浓度,利用监测数据进行污染源追踪、行为监督和治理决策,提高了对VOCs污染的认识和监管力度。
2.2 VOCs传感器技术随着传感器技术的不断进步,VOCs传感器技术逐渐成熟,并被广泛应用于环境监测领域。
传感器技术具有便携、低成本和实时性强的特点,可以实现对挥发性有机物在空气中的快速检测和准确定量,为环保部门和企业提供了更灵活、更有效的监测手段。
- 1、下载文档前请自行甄别文档内容的完整性,平台不提供额外的编辑、内容补充、找答案等附加服务。
- 2、"仅部分预览"的文档,不可在线预览部分如存在完整性等问题,可反馈申请退款(可完整预览的文档不适用该条件!)。
- 3、如文档侵犯您的权益,请联系客服反馈,我们会尽快为您处理(人工客服工作时间:9:00-18:30)。
METHOD TO-1 Revision 1.0April, 1984 METHOD FOR THE DETERMINATION OF VOLATILE ORGANIC COMPOUNDS IN AMBIENT AIR USING TENAX® ADSORPTION ANDGAS CHROMATOGRAPHY/MASS SPECTROMETRY (GC/MS)1.Scope1.1The document describes a generalized protocol forcollection and determination of certain volatile organiccompounds which can be captured on Tenax® GC (poly(2,6-Diphenyl phenylene oxide)) and determined by thermaldesorption GC/MS techniques. Specific approaches usingthese techniques are described in the literature (1-3).1.2This protocol is designed to allow some flexibility inorder to accommodate procedures currently in use.However, such flexibility also results in placement ofconsiderable responsibility with the user to documentthat such procedures give acceptable results (i.e.,documentation of method performance within eachlaboratory situation is required). Types ofdocumentation required are described elsewhere in thismethod.1.3Compounds which can be determined by this method arenonpolar organics having boiling points in the range ofapproximately 80E - 200E C. However, not all compoundsfalling into this category can be determined. Table 1gives a listing of compounds for which the method hasbeen used. Other compounds may yield satisfactoryresults but validation by the individual user isrequired.2.Applicable Documents2.1ASTM Standards:D1356Definitions of Terms Related to AtmosphericSampling and Analysis.E355Recommended Practice for Gas ChromatographyTerms and Relationships.2.2Other documents:Existing procedures (1-3).U. S. EPA Technical Assistance Document (4).3.Summary of Protocol3.1Ambient air is drawn through a cartridge containing -1-2grams of Tenax and certain volatile organic compounds aretrapped on the resin while highly volatile organiccompounds and most inorganic atmospheric constituentspass through the cartridge. The cartridge is thentransferred to the laboratory and analyzed.3.2For analysis the cartridge is placed in a heated chamberand purged with an inert gas. The inert gas transfersthe volatile organic compounds from the cartridge onto acold trap and subsequently onto the front of the GCcolumn which is held at low temperature (e.g., -70E C).the GC column temperature is then increased (temperatureprogrammed) and the components eluting from the columnare identified and quantified by mass spectrometry.Component identification is normally accomplished, usinga library search routine, on the basis of the GCretention time and mass spectral characteristics. Lesssophisticated detectors (e.g., electron capture or flameionization) may be used for certain applications buttheir suitability for a given application must beverified by the user.3.3Due to the complexity of ambient air samples only highresolution (i.e., capillary) GC techniques are consideredto be acceptable in this protocol.4.Significance4.1Volatile organic compounds are emitted into theatmosphere from a variety of sources including industrialand commercial facilities, hazardous waste storagefacilities, etc. Many of these compounds are toxic;hence knowledge of the levels of such materials in theambient atmosphere is required in order to determinehuman health impacts.4.2Conventional air monitoring methods (e.g., for workspacemonitoring) have relied on carbon adsorption approacheswith subsequent solvent desorption. Such techniquesallow subsequent injection of only a small portion,typically 1-5% of the sample onto the GC system.However, typical ambient air concentrations of thesecompounds require a more sensitive approach. The thermaldesorption process, wherein the entire sample isintroduced into the analytical (GC/MS) system fulfillsthis need for enhanced sensitivity.5.DefinitionsDefinitions used in this document and any user prepared SOPs should be consistent with ASTM D1356(6). All abbreviations and symbols are defined with this document at the point of use.6.Interferences6.1Only compounds having a similar mass spectrum and GCretention time compared to the compound of interest willinterface in the method. The most commonly encounteredinterferences are structural isomers.6.2Contamination of the Tenax cartridge with the compound(s)of interest is a commonly encountered problem in themethod. The user must be extremely careful in thepreparation, storage, and handling of the cartridgesthroughout the entire sampling and analysis process tominimize this problem.7.Apparatus7.1Gas Chromatograph/Mass Spectrometry system - should becapable of subambient temperature programming. Unit massresolution or better up to 800 amu. Capable of scanning30-400 amu region every 0.5-1 second. Equipped with datasystem for instrument control as well as dataacquisition, processing and storage.7.2Thermal Desorption Unit - Designed to accommodate Tenaxcartridges in use. See Figure 2a or b.7.3Sampling System - Capable of accurately and preciselydrawing an air flow of 10-500 ml/minute through the Tenaxcartridge. (See Figure 3a or b.)7.4Vacuum oven - connected to water aspirator vacuum supply.7.5Stopwatch.7.6Pyrex disks - for drying Tenax.7.7Glass jar - Capped with Teflon-lined screw cap. Forstorage of purified Tenax.7.8Powder funnel - for delivery of Tenax into cartridges.7.9Culture tubes - to hold individual glass Tenaxcartridges.7.10Friction top can (paint can) - to hold clean Tenaxcartridges.7.11Filter holder - stainless steel or aluminum (toaccommodate 1 inch diameter filter). Other sizes may be used if desired. (optional)7.12Thermometer - to record ambient temperature.7.13Barometer (optional).7.14Dilution bottle - Two-liter with septum cap for standardspreparation.7.15Teflon stirbar - 1 inch long.7.16Gas-tight glass syringes with stainless steel needles -10-500 µ1 for standard injection onto GC/MS system.7.17Liquid microliter syringes - 5.50 µL for injecting neatliquid standards into dilution bottle.7.18Oven - 60 + 5E C for equilibrating dilution flasks.7.19Magnetic stirrer.7.20Heating mantel.7.21Variac7.22Soxhlet extraction apparatus and glass thimbles - forpurifying Tenax.7.23Infrared lamp - for drying Tenax.7.24GC column - SE-30 or alternative coating, glass capillaryor fused silica.7.25Psychrometer - to determine ambient relative humidity.(optional)8.Reagents and Materials8.1Empty Tenax cartridges - glass or stainless steel (seeFigure 1a or b).8.2Tenax 60/80 mesh (2,6-diphenylphenylene oxide polymer).8.3Glasswool - silanized.8.4Acetone - Pesticide quality or equivalent.8.5Methanol - Pesticide quality or equivalent.8.6Pentane - Pesticide quality or equivalent.8.7Helium - Ultra pure, compressed gas. (99.9999%)8.8Nitrogen - Ultra pure, compressed gas. (99.9999%)8.9Liquid nitrogen.8.10Polyester gloves - for handling glass Tenax cartridges.8.11Glass Fiber Filter - one inch diameter, to fit in filterholder. (optional)8.12Perfluorotributylamine (FC-43).8.13Chemical Standards - Neat compounds of interest. Highestpurity available.8.14Granular activated charcoal - for preventingcontamination of Tenax cartridges during storage.9.Cartridge Construction and Preparation9.1Cartridge Design9.1.1Several cartridge designs have been reportedin the literature (1-3). The most common (1)is shown in Figure 1a. This design minimizescontact of the sample with metal surfaces,which can lead to decomposition in certaincases. However, a disadvantage of this designis the need to rigorously avoid contaminationof the outside portion of the cartridge sincethe entire surface is subjected to the purgegas stream during the desorption process.Clean polyester gloves must be worn at alltimes when handling such cartridges andexposure of the open cartridge to ambient airmust be minimized.9.1.2 A second common type of design (3) is shown inFigure 1b. While this design uses a metal(stainless steel) construction, it eliminatesthe need to avoid direct contact with theexterior surface since only the interior ofthe cartridge is purged.9.1.3The thermal desorption module and samplingsystem must be selected to be compatible withthe particular cartridge design chosen.Typical module designs are shown in Figure 2aand b. These designs are suitable for thecartridge designs shown in Figures 1a and b,respectively.9.2Tenax Purification9.2.1Prior to use the Tenax resin is subjected to aseries of solvent extraction and thermaltreatment steps. The operation should beconducted in an area where levels of volatileorganic compounds (other than the extractionsolvents used) are minimized.9.2.2All glassware used in Tenax purification aswell as cartridge materials should bethoroughly cleaned by water rinsing followedby an acetone rinse and dried in an oven at250E C.9.2.3Bulk Tenax is placed in a glass extractionthimble and held in place with a plug of cleanglasswool. The resin is then placed in thesoxhlet extraction apparatus and extractedsequentially with methanol and then pentanefor 16-24 hours (each solvent) atapproximately 6 cycles/hour. Glasswool forcartridge preparation should be cleaned in thesame manner as Tenax.9.2.4The extracted Tenax is immediately placed inan open glass dish and heated under aninfrared lamp for two hours in a hood. Caremust be exercised to avoid over heating of theTenax by the infrared lamp. The Tenax is thenplaced in a vacuum oven (evacuated using awater aspirator) without heating for one hour.An inert gas (helium or nitrogen) purge of 2-3ml/minute is used to aid in the removal ofsolvent vapors. The oven temperature is thenincreased to 110E C, maintaining inert gas flowand held for one hour. The oven temperaturecontrol is then shut off and the oven isallowed to cool to room temperature. Prior toopening the oven, the oven is slightlypressurized with nitrogen to preventcontamination with ambient air. The Tenax isremoved from the oven and sieved through a40/60 mesh sieve (acetone rinsed and ovendried) into a clean glass vessel. If theTenax is not to be used immediately forcartridge preparation it should be stored in aclean glass jar having a Teflon-lined screwcap and placed in a desiccator.9.3Cartridge Preparation and Pretreatment9.3.1All cartridge materials are pre-cleaned asdescribed in Section 9.2.2. If the glasscartridge design shown in Figure 1a isemployed all handling should be conductedwearing polyester gloves.9.3.2The cartridge is packed by placing a 0.5-lcmglasswool plug in the base of the cartridgeand then filling the cartridge to withinapproximately 1 cm of the top. A 0.5-1cmglasswool plug is placed in the top of thecartridge.9.3.3The cartridges are then thermally conditionedby heating for four hours at 270E C under aninert gas (helium) purge (100 - 200 ml/min).9.3.4After the four hour heating period thecartridges are allowed to cool. Cartridges ofthe type shown in Figure 1a are immediatelyplaced (without cooling) in clean culturetubes having Teflon-lined screw caps with aglasswool cushion at both the top and thebottom. Each tube should be shaken to ensurethat the cartridge is held firmly in place.Cartridges of the type shown in Figure 1b areallowed to cool to room temperature underinert gas purge and are then closed withstainless steel plugs.V MAX 'VbxW9.3.5The cartridges are labeled and placed in atightly sealed metal can (e.g., paint can orsimilar friction top container). Forcartridges of the type shown in Figure 1a theculture tube, not the cartridge, is labeled.9.3.6Cartridges should be used for sampling within2 weeks after preparation and analyzed withintwo weeks after sampling. If possible thecartridges should be stored at -20E C in aclean freezer (i.e., no solvent extracts orother sources of volatile organics containedin the freezer).10.Sampling10.1Flow Rate and Total Volume Selection10.1.1Each compound has a characteristic retentionvolume (liters of air per gram of adsorbent)which must not be exceeded. Since theretention volume is a function of temperature,and possibly other sampling variables, onemust include an adequate margin of safety toensure good collection efficiency. Someconsiderations and guidance in this regardareprovided in a recent report (5).Approximate breakthrough volumes at 38E C(100E F) in liters/gram of Tenax are providedin Table 1. These retention volume data aresupplied only as rough guidance and aresubject to considerable variability, dependingon cartridge design as well as samplingparameters and atmospheric conditions.10.1.2To calculate the maximum total volume of airwhich can be sampled use the followingequation:whereV is the calculated maximum total volume inMAXliters.V is the breakthrough volume for the leastbretained compound of interest (Table 1)in liters per gram of Tenax.W is the weight of Tenax in the cartridge,in grams.Q MAX 'VMAXtx1000 B'QMAXB r21.5 is a dimensionless safety factor to allowfor variability in atmospheric conditions.This factor is appropriate for temperatures inthe range of 25-30E C. If higher temperaturesare encountered the factor should be increased(i.e. maximum total volume decreased).10.1.3To calculate maximum flow rate use thefollowing equation:whereQ is the calculated maximum flow rate inMAXmilliliters per minute.t is the desired sampling time in minutes.Times greater than 24 hours (1440minutes) generally are unsuitable becausethe flow rate required is too low to beaccurately maintained.10.1.4The maximum flow rate Q should yield aMAXlinear flow velocity of 50-500 cm/minute.Calculate the linear velocity corresponding tothe maximum flow rate using the followingequation:whereB is the calculated linear flow velocity incentimeters per minute.r is the internal radius of the cartridgein centimeters.If B is greater then 500 centimeters perminute either the total sample flow rate (V)MAXshould be reduced or the sample flow rate(Q) should be reduced by increasing theMAXcollection time. If B is less then 50centimeters per minute the sampling rate (Q)MAXshould be increased by reducing the samplingtime. The total sample value (V) cannot beMAXincreased due to component breakthrough.10.1.5The flow rate calculated as described abovedefines the maximum flow rate allowed. Ingeneral, one should collect additional samplesin parallel, for the same time period but atlower flow rates. This practice yields ameasure of quality control and is furtherdiscussed in the literature (5). In general,flow rates 2 to 4 fold lower than the maximumflow rate should be employed for the parallelsamples. In all cases a constant flow rateshould be achieved for each cartridge sinceaccurate integration of the analyteconcentration requires that the flow beconstant over the sampling period.10.2Sample Collection10.2.1Collection of an accurately known volume ofair is critical to the accuracy of theresults. For this reason the use of mass flowcontrollers, rather than conventional needlevalves or orifices is highly recommended,especially at low flow velocities (e.g., lessthan 100 milliliters/minute). Figure 3aillustrates a sampling system utilizing massflow controllers. This system readily allowsfor collection of parallel samples. Figure 3bshows a commercially available system based onneedle valve flow controllers.10.2.2Prior to sample collection insure that thesampling flow rate has been calibrated over arange including the rate to be used forsampling, with a "dummy" Tenax cartridge inplace. Generally calibration is accomplishedusing a soap bubble flow meter or calibratedwet test meter. The flow calibration deviceis connected to the flow exit, assuming theentire flow system is sealed. ASTM MethodD3686 describes an appropriate calibrationscheme, not requiring a sealed flow systemdownstream of the pump.10.2.3The flow rate should be checked before andafter each sample collection. If the samplinginterval exceeds four hours the flow rateshould be checked at an intermediate pointduring sampling as well. In general, arotameter should be included, as shown inFigure 3b, to allow observation of thesampling flow rate without disrupting thesampling process.10.2.4To collect an air sample the cartridges areremoved from the sealed container just priorto initiation of the collection process. Ifglass cartridges (Figure 1a) are employed theymust be handled only with polyester gloves andshould not contact any other surfaces.10.2.5 A particulate filter and holder are placed onthe inlet to the cartridges and the exit endof the cartridge is connected to the samplingapparatus. In many sampling situations theuse of a filter is not necessary if only thetotal concentration of a component is desired.Glass cartridges of the type shown in Figure1a are connected using teflon ferrules andSwagelok (stainless steel or teflon) fittings.Start the pump and record the followingparameters on an appropriate data sheet(Figure 4): data, sampling location, time,ambient temperature, barometric pressure,relative humidity, dry gas meter reading (ifapplicable), flow rate, rotameter reading (ifapplicable), cartridge number and dry gasmeter serial number.10.2.6Allow the sampler to operate for the desiredtime, periodically recording the variableslisted above. Check flow rate at the midpointof the sampling interval if longer than fourhours. At the end of the sampling periodrecord the parameters listed in 10.2.5 andcheck the flow rate and record the value. Ifthe flows at the beginning and end of thesampling period differ by more than 10% thecartridge should be marked as suspect.10.2.7Remove the cartridges (one at a time) andplace in the original container (use glovesfor glass cartridges). Seal the cartridges orculture tubes in the friction-top cancontaining a layer of charcoal and package forimmediate shipment to the laboratory foranalysis. Store cartridges at reducedtemperature (e.g., -20E C) before analysis ifpossible to maximize storage stability.Q A 'Q1%Q2%...QNNVm'T×QAV s 'Vm×PA760×298273%tA10.2.8Calculate and record the average sample ratefor each cartridge according to the followingequation:whereQ = Average flow rate in ml/minute.AQ, Q, ....Q = Flow rates determined at 12Nbeginning, end, and intermediate points duringsampling.N = Number of points averaged.10.2.9Calculate and record the total volumetric flowfor each cartridge using the followingequation:whereV =Total volume sampled in liters atmmeasured temperature and pressure.T =Stop time.2T =Start time.1T =Sampling time = T = T, minutes2110.2.10The total volume (V) at standard conditions,s25E C and 760 mmHg, is calculated from thefollowing equation:whereP = Average barometric pressure, mmHgAt = Average ambient temperature, E C.A11.GC/MS Analysis11.1Instrument Set-up11.1.1Considerable variation from one laboratory toanother is expected in terms of instrumentconfiguration. Therefore each laboratory mustbe responsible for verifying that theirparticular system yields satisfactory results.Section 14 discusses specific performancecriteria which should be met.11.1.2 A block diagram of the typical GC/MS systemrequired for analysis of Tenax cartridges isdepicted in Figure 5. The operation of suchdevices is described in 11.2.4. The thermaldesorption module must be designed toaccommodate the particular cartridgeconfiguration. Exposure of the sample tometal surfaces should be minimized and onlystainless steel, or nickel metal surfacesshould be employed. The volume of tubing andfittings leading from the cartridge to the GCcolumn must be minimized and all areas must bewell-swept by helium carrier gas.11.1.3The GC column inlet should be capable of beingcooled to -70E C and subsequently increasedrapidly to approximately 30E C. This can bemost readily accomplished using a GC equippedwith subambient cooling capability (liquidnitrogen) although other approaches such asmanually cooling the inlet of the column inliquid nitrogen may be acceptable.11.1.4The specific GC column and temperature programemployed will be dependent on the specificcompounds of interest. Appropriate conditionsare described in the literature (1-3). Ingeneral a nonpolar stationary phase (e.g., SE-30, OV-1) temperature programmed from 30E C to200E C at 8E/minute will be suitable. Fusedsilica bonded phase columns are preferable toglass columns since they are more rugged andcan be inserted directly into the MS ionsource, thereby eliminating the need for aGC/MS transfer line.11.1.5Capillary column dimensions of 0.3 mm ID and50 meters long are generally appropriatealthough shorter lengths may be sufficient inmany cases.11.1.6Prior to instrument calibration or sampleanalysis the GC/MS system is assembled asshown in Figure 5. Helium purge flows(through the cartridge) and carrier flow areset at approximately 10 ml/minute and 1-2ml/minute respectively. If applicable, theinjector sweep flow is set at 2-4 ml/minute.11.1.7Once the column and other system componentsare assembled and the various flowsestablished the column temperature isincreased to 250E C for approximately fourhours (or overnight if desired) to conditionthe column.11.1.8The MS and data system are set according tothe manufacturer's instructions. Electronimpact ionization (70eV) and an electronmultiplier gain of approximately 5 x 10 should4be employed. Once the entire GC/MS system hasbeen setup the system is calibrated asdescribed in Section 11.2. The user shouldprepare a detailed standard operatingprocedure (SOP) describing this process forthe particular instrument being used.11.2Instrument Calibration11.2.1Tuning and mass standardization of the MSsystem is performed according tomanufacturer's instructions and relevantinformation from the user prepared SOP.Perfluorotributylamine should generally beemployed for this purpose. The material isintroduced directly into the ion source thougha molecular leak. The instrumental parameters(e.g., lens voltages, resolution, etc.) shouldbe adjusted to give the relative ionabundances shown in Table 2 as well asacceptable resolution and peak shape. Ifthese approximate relative abundances cannotbe achieved, the ion source may requirecleaning according to manufacturer'sinstructions. In the event that the user'sinstrument cannot achieve these relative ionabundances, but is otherwise operatingproperly, the user may adopt another set ofrelative abundances as performance criteria.However, these alternate values must berepeatable on a day-to-day basis.11.2.2After the mass standardization and tuningprocess has been completed and the appropriatevalues entered into the data system the usershould then calibrate the entire system byintroducing known quantities of the standardcomponents of interest into the system. Threealternate procedures may be employed for thecalibration process including 1) directsyringe injection of dilute vapor phasestandards, prepared in a dilution bottle, ontothe GC column, 2) injection of dilute vaporphase standards into a carrier gas streamdirected through the Tenax cartridge, and 3)introduction of permeation or diffusion tubestandards onto a Tenax cartridge. Thestandards preparation procedures for each ofthese approaches are described in Section 13.The following paragraphs describe theinstrument calibration process for each ofthese approaches.11.2.3If the instrument is to be calibrated bydirect injection of a gaseous standard, astandard is prepared in a dilution bottle asdescribed in Section 13.1. The GC column iscooled to -70E C (or, alternately, a portion ofthe column inlet is manually cooled withliquid nitrogen). The MS and data system isset up for acquisition as described in therelevant user SOP. The ionization filamentshould be turned off during the initial 2-3minutes of the run to allow oxygen and otherhighly volatile components to elute. Anappropriate volume (less than 1 ml) of thegaseous standard is injected onto the GCsystem using an accurately calibrated gastight syringe. The system clock is startedand the column is maintained at -70E C (orliquid nitrogen inlet cooling) for 2 minutes.The column temperature is rapidly increased tothe desired initial temperature (e.g., 30E C).The temperature program is started at aconsistent time (e.g., four minutes) afterinjection. Simultaneously the ionizationfilament is turned on and data acquisition isinitiated. After the last component ofinterest has eluted acquisition is terminatedand the data is processed as described inSection 11.2.5. The standard injectionprocess is repeated using different standardvolumes as desired.11.2.4If the system is to be calibrated by analysisof spiked Tenax cartridges a set of cartridgesis prepared as described in Sections 13.2 or13.3. Prior to analysis the cartridges arestored as described in Section 9.3. If glasscartridges (Figure 1a) are employed care mustbe taken to avoid direct contact, as describedearlier. The GC column is cooled to -70E C,the collection loop is immersed in liquidnitrogen and the desorption module ismaintained at 250E C. The inlet valve isplaced in the desorb mode and the standardcartridge is placed in the desorption module,making certain that no leakage or purge gasoccurs. The cartridge is purged for 10minutes and then the inlet valve is placed inthe inject mode and the liquid nitrogen sourceremoved from the collection trap. The GCcolumn is maintained at -70E C for two minutesand subsequent steps are as described in11.2.3. After the process is complete thecartridge is removed from the desorptionmodule and stored for subsequent use asdescribed in Section 9.3.11.2.5Data processing for instrument calibrationinvolves determining retention times, andintegrated characteristic ion intensities foreach of the compounds of interest. Inaddition, for at least one chromatographicrun, the individual mass spectra should beinspected and compared to reference spectra toensure proper instrumental performance. Sincethe steps involved in data processing arehighly instrument specific, the user shouldprepare a SOP describing the process forindividual use. Overall performance criteriafor instrument calibration are provided inSection 14. If these criteria are notachieved the user should refine theinstrumental parameters and/or operatingprocedures to meet these criteria.11.3Sample Analysis11.3.1The sample analysis process is identical tothat described in Section 11.2.4 for theanalysis of standard Tenax cartridges.。