多孔陶瓷材料的制备技术
多孔陶瓷材料的制备与力学性能分析
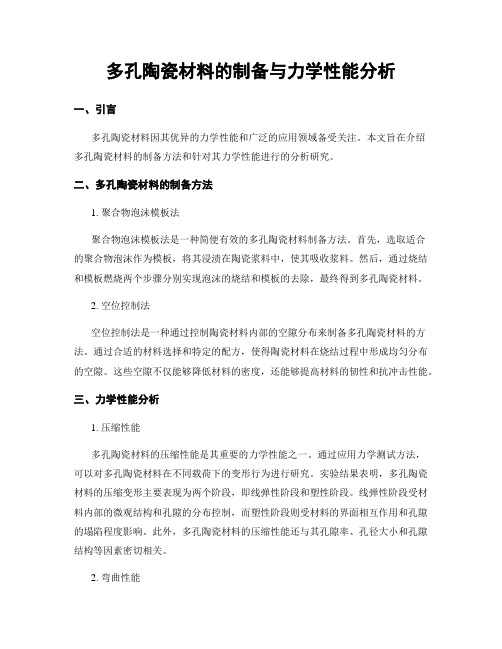
多孔陶瓷材料的制备与力学性能分析一、引言多孔陶瓷材料因其优异的力学性能和广泛的应用领域备受关注。
本文旨在介绍多孔陶瓷材料的制备方法和针对其力学性能进行的分析研究。
二、多孔陶瓷材料的制备方法1. 聚合物泡沫模板法聚合物泡沫模板法是一种简便有效的多孔陶瓷材料制备方法。
首先,选取适合的聚合物泡沫作为模板,将其浸渍在陶瓷浆料中,使其吸收浆料。
然后,通过烧结和模板燃烧两个步骤分别实现泡沫的烧结和模板的去除,最终得到多孔陶瓷材料。
2. 空位控制法空位控制法是一种通过控制陶瓷材料内部的空隙分布来制备多孔陶瓷材料的方法。
通过合适的材料选择和特定的配方,使得陶瓷材料在烧结过程中形成均匀分布的空隙。
这些空隙不仅能够降低材料的密度,还能够提高材料的韧性和抗冲击性能。
三、力学性能分析1. 压缩性能多孔陶瓷材料的压缩性能是其重要的力学性能之一。
通过应用力学测试方法,可以对多孔陶瓷材料在不同载荷下的变形行为进行研究。
实验结果表明,多孔陶瓷材料的压缩变形主要表现为两个阶段,即线弹性阶段和塑性阶段。
线弹性阶段受材料内部的微观结构和孔隙的分布控制,而塑性阶段则受材料的界面相互作用和孔隙的塌陷程度影响。
此外,多孔陶瓷材料的压缩性能还与其孔隙率、孔径大小和孔隙结构等因素密切相关。
2. 弯曲性能多孔陶瓷材料的弯曲性能是评估其在应力作用下的变形和破坏行为的重要指标。
通过三点弯曲测试等方法,可以研究多孔陶瓷材料在弯曲载荷下的应力分布、变形行为和破坏机制。
研究表明,多孔陶瓷材料在弯曲载荷下呈现出明显的脆性破坏特征,弯曲强度与孔隙率呈负相关。
此外,控制材料内部的孔隙结构和孔径大小可以显著影响多孔陶瓷材料的弯曲性能。
3. 抗冲击性能多孔陶瓷材料的抗冲击性能是其在受到冲击载荷下的抵抗能力。
通过进行冲击实验,可以研究多孔陶瓷材料在不同速度下的应力应变行为和破坏机制。
实验结果显示,多孔陶瓷材料的抗冲击性能随着孔隙率的增大而增加,而抗冲击强度则受材料的孔径大小和孔隙结构的影响。
多孔陶瓷材料的制备与表征研究

多孔陶瓷材料的制备与表征研究一、引子:多孔陶瓷材料是具有许多孔隙结构的特殊材料,广泛应用于过滤、吸附、催化等领域。
本文旨在探讨多孔陶瓷材料的制备方法和表征技术。
二、制备方法:1. 泡沫陶瓷材料泡沫陶瓷材料是一种具有高度结构有序和孔隙连通的多孔材料,制备方法多样。
一种常见的方法是以聚合物泡沫为模板,采用浇注、喷涂等方法制备泡沫预体,然后经过热解和烧结得到陶瓷材料。
2. 模板法模板法是一种常见的多孔陶瓷制备方法,通过采用不同孔隙大小的模板,可以制备出不同孔径的陶瓷材料。
常用的模板包括聚苯乙烯微球、树脂珠等,将模板与陶瓷原料混合,烧结后,通过溶解或者燃烧去除模板,从而得到多孔陶瓷材料。
3. 发泡法发泡法是一种常用的制备多孔陶瓷材料的方法,通过在陶瓷浆料中加入气泡剂,使其在烧结过程中发生气泡膨胀,形成孔隙结构。
发泡法制备的多孔陶瓷材料孔隙布局均匀,孔径可调。
4. 真空浸渍法真空浸渍法是一种制备高度有序多孔陶瓷材料的方法。
首先制备出二氧化硅或其他陶瓷材料的溶胶,然后将其浸渍到特殊的介孔硅胶膜上,经过多次浸渍和热解处理,最终得到孔径可调的多孔陶瓷材料。
三、表征技术:1. 扫描电子显微镜(SEM)SEM可以观察到材料的表面形貌和孔隙结构。
通过SEM图像可以评估多孔陶瓷材料的孔径分布、孔隙连通性等,并可以对制备方法进行优化改进。
2. 氮气吸附-脱附法(BET)BET技术可以用来测定纳米孔隙的孔径和比表面积。
通过测定材料在吸附和脱附过程中氮气的吸附量,可以计算出材料的比表面积和孔隙体积。
3. 压汞法压汞法是一种测量材料孔隙结构及孔隙分布的方法。
利用孔隙的连通性,通过施加不同的压力,测定压汞的饱和和释放曲线,从而得到材料的孔隙直径和孔隙分布。
4. X射线衍射法(XRD)XRD可以通过分析材料的衍射谱来确定多孔陶瓷材料的结晶相、晶粒尺寸等信息。
结合其他表征技术,可以评估材料的热稳定性和晶格缺陷等特性。
结语:多孔陶瓷材料的制备和表征是一个复杂而重要的领域。
多孔陶瓷材料的制备与力学特性

多孔陶瓷材料的制备与力学特性多孔陶瓷材料作为一种具有广泛应用前景的材料,其制备和力学特性研究成为材料科学领域的热点问题。
本文将从多角度探讨多孔陶瓷材料的制备方法及其力学特性的研究进展。
一、多孔陶瓷材料的制备方法多孔陶瓷材料的制备方法多样,常见的包括模板法、沉积法、发泡法和溶胶—凝胶法等。
其中,模板法是一种常用且成熟的制备方法。
通过选择不同的模板材料,可以制备出具有不同孔隙结构的多孔陶瓷材料。
沉积法则是通过在基底上逐层沉积陶瓷材料,随后去除模板材料,从而得到多孔陶瓷。
而发泡法是通过在材料中注入气体或气泡制得多孔结构。
溶胶—凝胶法则是将溶胶转变为凝胶,在凝胶中形成孔洞,制备多孔陶瓷材料。
二、多孔陶瓷材料的力学特性研究多孔陶瓷材料具有许多独特的力学特性,这些特性直接影响着其在不同领域的应用。
其中,强度是多孔陶瓷材料的重要力学特性之一。
研究表明,多孔陶瓷材料的强度主要受到孔隙率、孔隙形状和孔隙分布的影响。
当孔隙率较低时,多孔陶瓷材料的强度较高;相反,当孔隙率较高时,多孔陶瓷材料的强度较低。
此外,孔隙形状也会对多孔陶瓷材料的强度产生明显影响。
如球形孔隙比长方形孔隙更有利于提高多孔陶瓷材料的强度。
除了强度外,多孔陶瓷材料的韧性也是关注的焦点。
韧性是衡量材料抵抗断裂能力的重要指标,对材料的可靠性和安全性至关重要。
多孔陶瓷材料的韧性主要受到孔隙率、孔隙大小和材料本身的影响。
研究发现,当孔隙率较低、孔隙大小较小时,多孔陶瓷材料的韧性较高。
此外,选择适当的陶瓷材料也能提高多孔陶瓷材料的韧性。
三、未来的研究方向随着研究的深入,多孔陶瓷材料的制备和力学特性研究仍然面临一些挑战。
为了获得更好的制备方法和提高力学性能,未来的研究可以从以下几个方面展开:首先,可以进一步改进和优化现有的制备方法,提高多孔陶瓷材料的孔隙结构和均匀性。
其次,可以通过引入纳米材料、纤维等进行增强改性,以提高多孔陶瓷材料的力学性能。
此外,基于机器学习和计算模拟等技术,可以探索更广泛的多孔陶瓷材料设计空间,从而实现材料性能的定制化。
多孔陶瓷材料的的研究现状及应用

多孔陶瓷材料的的研究现状及应用近年来,多孔陶瓷材料作为一种新型的材料,已经受到了普遍的重视。
多孔陶瓷材料具有加工性好、耐久性强、热膨胀系数小、吸音和隔音性能良好等优点,可用于航空、航天、非金属材料的高温烧结、冶金和电镀、化工设备的催化剂床,以及医学技术、陶瓷艺术等多个领域。
本文就多孔陶瓷材料的研究现状及应用情况进行综述,旨在为多孔陶瓷材料的进一步开发和应用提供参考。
一、多孔陶瓷材料的研究现状1、烧结工艺研究多孔陶瓷材料的制备需要克服以下几个技术难题:首先,多孔陶瓷材料的烧结工艺。
多孔陶瓷材料的烧结技术主要包括萃取法、模压法、粉末技术和复合材料技术等。
其中,萃取法技术能够控制多孔陶瓷材料的结构和性能。
目前,萃取法烧结工艺仍处于萌芽阶段,但已在一定程度上实现了多孔陶瓷材料的高功能性。
2、微观结构和性能研究与传统陶瓷材料相比,多孔陶瓷材料的特殊结构与其特殊的功能有关。
因此,要更好地利用多孔陶瓷材料的性能,必须对材料的微观结构进行研究。
国内外学者已经对多孔陶瓷材料的微观结构与性能关系进行了深入的研究,取得了一定的进展。
二、多孔陶瓷材料的应用1、多孔陶瓷材料在新能源和节能方面的应用在新能源领域,多孔陶瓷材料可用于提高太阳能电池的光伏效率。
多孔陶瓷材料具有较高的热稳定性,可用于太阳能电池表面保护膜,防止太阳能电池表面受损。
此外,多孔陶瓷材料还可用于改善空调能源利用效率,从而节省能源。
2、多孔陶瓷材料在航空航天领域的应用在航空航天领域,多孔陶瓷材料可用于制作热吸收涂层和热隔离层,以有效抵御高温环境的影响,提高发射火箭和高空飞机的安全性能。
此外,多孔陶瓷材料还可作为消声器、过滤器和吸音材料,大大提高航空航天设备的静音和防腐能力。
三、结论多孔陶瓷材料具有许多优异的性能,已经应用于航空航天、能源、石油化工等领域。
它的研究是一个新兴的研究领域,国内外学者已经对多孔陶瓷材料的烧成工艺及其微观结构与性能关系进行了研究,取得了比较理想的结果。
冷冻干燥法制备多孔陶瓷研究进展

冷冻干燥法制备多孔陶瓷研究进展近年来,随着科技的不断进步,多孔陶瓷的制备技术越来越受到人们的。
多孔陶瓷具有优异的物理化学性能,如高透气性、高渗透性、耐高温、耐腐蚀等,使其在许多领域具有广泛的应用前景。
本文将重点冷冻干燥法制备多孔陶瓷的研究进展。
多孔陶瓷的制备方法有很多,包括物理法、化学法、模板法等。
物理法主要包括球磨法、烧结法等;化学法主要包括溶胶-凝胶法、聚合物泡沫浸渍法等。
这些方法在制备多孔陶瓷时都存在一定的局限性,如制备过程复杂、成本高、孔结构不易控制等。
因此,需要探索一种简单、高效、可控的制备方法。
冷冻干燥法是一种新型的制备多孔陶瓷的方法,该方法主要利用冰在低温下升华的原理,将含有陶瓷前驱体的溶液进行冷冻,然后在真空条件下进行干燥。
冷冻干燥法具有以下优点:1)可以制备具有复杂形状和结构的多孔陶瓷;2)可以控制孔径大小和分布;3)制备过程简单、节能环保。
然而,冷冻干燥法也存在一些不足,如制备周期长、成本较高,需要进一步改进和完善。
本文采用冷冻干燥法制备多孔陶瓷,进行了实验设计、材料制备、性能测试等方面的工作。
我们选取合适的陶瓷前驱体和溶剂,制备出具有一定粘度的溶液。
然后,将溶液进行快速冷冻,并在真空条件下进行干燥。
对制备出的多孔陶瓷进行性能测试,包括孔径大小、孔隙率、抗压强度等方面。
通过与其他制备方法相比,我们发现冷冻干燥法在制备多孔陶瓷方面具有明显的优势。
冷冻干燥法可以制备出具有复杂形状和结构的多孔陶瓷,这是其他方法难以实现的。
冷冻干燥法可以精确控制孔径大小和分布,从而满足不同领域的应用需求。
冷冻干燥法的制备过程简单、节能环保,具有很高的实际应用价值。
近年来,利用冷冻干燥法制备多孔陶瓷的研究取得了重要进展。
在机制分析方面,科研人员深入研究了冷冻干燥的原理和过程,提出了许多有价值的理论。
在工艺优化方面,通过不断改进制备工艺,提高了多孔陶瓷的性能和稳定性。
在产品应用方面,冷冻干燥法制备的多孔陶瓷在许多领域都得到了广泛的应用,如催化剂载体、过滤分离、生物医学等。
多孔陶瓷骨修复材料的制备和骨组织工程中的应用

多孔陶瓷骨修复材料的制备和骨组织工程中的应用随着人口老龄化的加剧和骨损伤等骨相关疾病的增加,对于骨修复材料的需求越来越高。
多孔陶瓷骨修复材料在骨组织工程中具有很大的潜力,逐渐成为骨修复领域的热点研究方向。
本文将介绍多孔陶瓷骨修复材料的制备方法以及在骨组织工程中的应用前景。
多孔陶瓷骨修复材料的制备主要包括原料选择、制备工艺、孔隙结构的控制等环节。
原料选择是多孔陶瓷骨修复材料制备的首要步骤。
通常选择的材料包括氧化锆(ZrO2)、羟基磷灰石(HA)、β-三磷酸钙(β-TCP)等。
这些材料具有良好的生物相容性和生物活性,能够促进骨组织再生。
制备工艺主要有烧结法、凝胶注模法、切割法等。
其中,烧结法制备的多孔陶瓷骨修复材料具有较高的力学性能和生物相容性,但孔隙结构不易调控;凝胶注模法制备的多孔陶瓷骨修复材料孔隙结构可控制性强,但力学性能相对较差。
因此,制备过程中需要根据具体需求选择合适的制备工艺,并通过后续的表面处理、改性等方法进一步优化材料性能。
多孔陶瓷骨修复材料在骨组织工程中具有广阔的应用前景。
首先,在骨缺损修复方面,多孔陶瓷骨修复材料能够提供良好的骨结合性和骨再生能力,促进骨组织的生长。
其孔隙结构可以提供生长因子的载体,有利于生长因子的控制释放,进而促进骨细胞的增殖和分化。
其次,多孔陶瓷骨修复材料还可以用于人工关节的替代。
通过与骨组织的无缝连接,可以实现生物力学功能的恢复。
此外,在口腔修复和植入材料领域,多孔陶瓷骨修复材料也得到了广泛应用。
其生物相容性和生物活性能够减少植入材料与机体之间的反应和排斥,提高植入材料的稳定性和生物学效应。
然而,多孔陶瓷骨修复材料仍然存在一些挑战和问题。
首先,材料的力学性能和孔隙结构之间存在矛盾。
孔隙结构越大,更有利于细胞的生长和骨成生,但相应地,材料的力学性能会降低。
因此,如何在兼顾力学性能的同时保持良好的孔隙结构成为需要解决的难题。
其次,多孔陶瓷骨修复材料的生物降解性也需要进一步研究。
添加造孔剂法制备多孔陶瓷及其强度与孔径控制

添加造孔剂法制备多孔陶瓷及其强度与孔径控制一、本文概述多孔陶瓷作为一种具有独特结构和性能的新型无机非金属材料,在过滤、分离、吸附、催化、载体、隔热、降噪、生物医疗等众多领域表现出广阔的应用前景。
其中,孔径大小及其分布、孔的数量、形状和连通性等孔结构参数对多孔陶瓷的性能起着决定性的作用。
因此,如何制备具有理想孔结构的多孔陶瓷材料成为了研究的关键。
添加造孔剂法作为一种制备多孔陶瓷的常用方法,通过引入造孔剂在陶瓷基体中形成孔洞,从而实现对多孔陶瓷孔结构的调控。
本文旨在探讨添加造孔剂法制备多孔陶瓷的工艺流程、影响多孔陶瓷强度和孔径的关键因素,以及如何通过调整制备参数实现对多孔陶瓷强度和孔径的有效控制,为多孔陶瓷的制备和应用提供理论指导和技术支持。
二、添加造孔剂法制备多孔陶瓷的原理添加造孔剂法制备多孔陶瓷是一种常见且有效的制备工艺,其基本原理是在陶瓷原料中加入一定数量的造孔剂,这些造孔剂在陶瓷烧结过程中会燃烧或分解,从而留下大量孔洞,形成多孔结构。
造孔剂的选择和添加量是影响多孔陶瓷孔结构和性能的关键因素。
造孔剂的种类应具有良好的热稳定性,能够在陶瓷烧结温度范围内不发生化学反应或分解,以保证孔洞的均匀性和稳定性。
常用的造孔剂包括炭黑、石墨、有机物等。
造孔剂的添加量决定了多孔陶瓷的孔隙率和孔径大小。
添加量过多,会导致陶瓷体积收缩过大,强度降低;添加量过少,则孔洞数量不足,影响多孔陶瓷的性能。
因此,合理控制造孔剂的添加量是制备多孔陶瓷的关键。
在制备过程中,造孔剂与陶瓷原料混合均匀后,通过成型和烧结工艺形成多孔陶瓷。
成型过程中,造孔剂颗粒随机分布在陶瓷基体中,形成初步的孔结构。
在烧结过程中,造孔剂燃烧或分解,形成大量孔洞,同时陶瓷基体发生致密化,形成最终的多孔陶瓷。
通过调整烧结温度和保温时间等工艺参数,可以进一步控制多孔陶瓷的孔结构和性能。
烧结温度过高或保温时间过长,可能导致孔洞坍塌,降低多孔陶瓷的孔隙率和比表面积;烧结温度过低或保温时间过短,则可能导致陶瓷基体致密化不足,影响多孔陶瓷的强度。
高性能多孔陶瓷材料的制备与性能优化

高性能多孔陶瓷材料的制备与性能优化多孔陶瓷材料是一种在工业领域中被广泛使用的材料,它具有轻质、高强度、高温稳定性和良好的化学稳定性等优势。
然而,传统的制备方法往往无法获得高性能的多孔陶瓷材料,因此,开发新的制备方法并优化其性能成为了当前研究的热点之一。
为了制备高性能的多孔陶瓷材料,研究人员采用了多种方法和工艺。
其中之一是模板法。
模板法通过使用不同类型的模板,如碳纳米管、纳米颗粒等,来控制陶瓷材料的孔隙结构和形貌。
这种方法不仅可以获得特定尺寸和形状的孔隙,还可以控制陶瓷材料的疏水性和亲水性。
另一种制备方法是溶胶-凝胶法。
这种方法通过将溶胶转化为凝胶,并利用凝胶的特殊结构来形成孔隙结构。
这种方法具有制备高孔隙率和大孔隙尺寸多孔陶瓷材料的优势。
在制备多孔陶瓷材料的同时,研究人员还在不断寻求性能的优化方法。
一种常用的方法是通过控制孔隙结构和孔隙分布来改善多孔陶瓷材料的强度和韧性。
例如,通过调整孔隙的尺寸和形状,可以增加陶瓷材料的承载能力和耐久性。
另外,添加一定量的增强剂,如纤维材料或金属颗粒,可以进一步提高多孔陶瓷材料的韧性和强度。
此外,表面修饰也是一种常用的方法。
通过在多孔陶瓷材料表面修饰一层功能性薄膜,可以增加材料的疏水性或亲水性,提高材料的稳定性和耐腐蚀性。
除了上述方法外,还有其他一些新颖的方法被用于制备高性能的多孔陶瓷材料。
一种是生物仿生法。
生物仿生法通过模仿自然界中生物体上的结构和功能,制备具有特定性能的多孔陶瓷材料。
例如,在蒙古包蜂窝的形状和结构上进行仿生,可以得到具有优异隔音性能的多孔陶瓷材料。
另一种方法是利用现代纳米技术。
纳米技术可以制备出具有纳米级孔隙和纳米级颗粒的陶瓷材料,其力学性能和热传导性能得到了显著提高。
这种方法在高温热电器件和微观流体传感器等领域具有广阔的应用前景。
此外,随着材料科学研究的不断发展,理论计算方法也被广泛应用于多孔陶瓷材料的制备和性能优化中。
通过建立模型和进行模拟计算,可以揭示材料内部孔隙结构、力学性能和热传导性能等的微观机制。
- 1、下载文档前请自行甄别文档内容的完整性,平台不提供额外的编辑、内容补充、找答案等附加服务。
- 2、"仅部分预览"的文档,不可在线预览部分如存在完整性等问题,可反馈申请退款(可完整预览的文档不适用该条件!)。
- 3、如文档侵犯您的权益,请联系客服反馈,我们会尽快为您处理(人工客服工作时间:9:00-18:30)。
1. 能制形状复杂的制品 粉浆浇注
2. 设备简单
1. 尺寸公差大 2. 生产率低
1. 需加入较多的塑化剂 2. 制品尺寸大小受限制
1. 生产率低 2. 原料受限制
大 尺 寸 管 材 及异 形制品
各 种 形 状 复 杂的 小件制品
复杂 形状制品, 多 层过滤器。
( 3) 成型
·3 5·
多孔陶瓷的成型方法与普通的陶瓷成型方法相似, 主要有模压、挤压、等静压、轧制、注射 和粉浆浇注等。表 2 是各种成型方法的比较 其中应用比较成功, 用得最多的是挤压成型[ 4, 6] , 特别是用于工业废气和汽车尾气净化的蜂窝 状陶瓷的成型。Auriol 等[6] 曾采用 9% 凡士林和 16% 的水胶( 1. 5% 甲基纤维素) 作增塑剂, 成 功制取了挤压泥料。Kiefer[4] 则用生淀粉作造孔剂, 用淀粉浆糊、甲基纤维素或聚乙烯醇等作 增塑剂, 挤压成型制备蜂窝状陶瓷。日本专利还采用过水合 Al2O3 加磷酸制备泥料。
2. 有机泡沫浸渍工艺 有机泡沫浸渍法是用有机泡沫浸渍陶瓷浆料, 干燥后烧掉有机泡沫, 获得多孔陶瓷的一种
方法。该法适于制备高气孔率, 开气孔的多孔陶瓷。 自从 Schwart zwalder [7]首先发明该法以来, 经过不断的改进与发展, 目前已日趋成熟。下
面就一些关键步骤予以分析。 ( 1) 有机泡沫的选择 选择有机泡沫首先要考虑的是孔径大小, 因为泡沫孔径的大小决定了最后制品的孔径尺
表 1 制取多孔陶瓷材料的各种工艺比较
成形方法
添加 造 孔 剂的方法
有机 泡 沫 浸渍方法
优 点 1. 采 用不 同 的成 形 方法, 可制 得形状复杂的制品 2. 可制取各 种气孔结 构的多孔 制品
1. 能制取高气孔率的制品 2. 试样强度好
缺 点
1. 气孔分布均匀性差 2. 不适合制取高气孔率的制品
【Key wor ds】 Porous cer amics, F abr ication, P or e-form ing mat er ials, F oam impregna tion
一、前 言
近年来表面与界面起突出作用的新型材料日益受到重视, 既发现一些新的物理现象和效 应, 在应用上又很有潜力, 具有广泛的发展前景[1]。多孔陶瓷材料正是一种利用物理表面的新 型材料。例如, 利用多孔陶瓷的均匀透过性, 可以制造各种过滤器、分离装置、流体分布元件、混 合元件、渗出元件和节流元件等; 利用多孔陶瓷发达的比表面积, 可以制成各种多孔电极、催化 剂载体、热交换器、气体传感器等; 利用多孔陶瓷吸收能量的性能, 可以用作各种吸音材料、减 震材料等; 利用多孔陶瓷低的密度、低的热传导性能, 还可以制成各种保温材料、轻质结构材料 等[2] , 加之其耐高温、耐气候性、抗腐蚀, 多孔陶瓷材料的应用已遍及冶金、化工、环保、能源、生 物等各个部门, 引起了全球材料学界的高度重视, 并得到了较快发展, 每年这方面的专利都有 近百篇, 而且有逐年增长的趋势。但由于绝大多数制备工艺参数及关键问题处于技术保密状 态, 目前尚无系统论述各种制备技术的文章, 本文结合作者研制用于高温固体氧化物燃料电池 的多孔 A l2O3 陶瓷支持管( 体) 的研究工作, 分析了多孔陶瓷材料制备技术的现状及今后的发 展趋势。
【关键词】 多孔陶瓷 制备 造孔剂 泡沫浸渍
Techniques For Pr epar ation of Por ous Ceramic Mater ials
Zhu Shizhen Zhao Zhenbo Beij ing Institute of Technology Beijing 100081
适用范围
尺寸 不大的管状、 片状、块状。
细而 长的管材、棒 材, 某 些异形截面 管材。
轧制
1. 能制取长而细的带材及箔材 2. 生产率高可连续生产
1. 制品形状简单 2. 粗粉末难加工
各种 厚度的带材, 多层过滤器。
等静压
1. 气孔分布均匀 2. 适于大尺寸制品
注射
1. 可制形状复杂的制品 2. 气孔沿长度方向分布均匀
表 2 多孔陶瓷的成形方法比较
成形方法 模压 挤压
优 点
1. 模具简单 2. 尺寸精度高 3. 操作方便, 生产率高 1. 能制取细而长的管材 2. 气孔沿长度方向分布均匀 3. 生产率高可连续生产
缺 点
1. 气孔分布不均匀 2. 制品尺寸受限制 3. 制品形状受限制 1. 需加入较多的增塑剂 2. 泥料制备麻烦 3. 对原料的粒度要求高
添加造孔剂法制备多孔陶瓷的工艺流程与普通的陶瓷工艺流程相似, 这种工艺方法的关
键在于造孔剂种类和用量的选择。( 1) 造孔剂Fra bibliotek类和用量的选择
造孔剂加入的目的在于促使气孔率增加, 它必须满足下列要求: 在加热过程中易于排除;
排除后在基体中无有害残留物; 不与基体反应。
造孔剂的种类有无机和有机二类。无机造孔剂有碳酸铵、碳酸氢铵、氯化铵等高温可分解
1. 适于制取微孔陶瓷 2. 适于制取薄膜材料 3. 气孔分布均匀
1. 原料受限制 2. 生产率低 3. 制品形状受限制
微 孔 分离 膜
1. 添加造孔剂工艺
该工艺通过在陶瓷配料中添加造孔剂, 利用造孔剂在坯体中占据一定的空间, 然后经过烧
结, 造孔剂离开基体而成气孔来制备多孔陶瓷。虽然在普通的陶瓷工艺中, 采用调整烧结温度
盐类[ 1] ,
以及其它可分解化合物如
Si3
N
[ 4
2]
,
或无机碳如煤粉、碳粉等。有机造孔剂主要是一些
天然纤维、高分子聚合物和有机酸等, 如锯末、萘、淀粉、及聚乙烯醇、尿素、甲基丙烯酸甲脂、聚
氯乙烯、聚苯乙烯等[ 3-4] 。造孔剂颗粒的大小和形状决定了多孔陶瓷材料气孔的大小和形状。
·34·
上述造孔剂均在远低于基体陶瓷烧结温度下分解或挥发, 由于是在较低温度形成孔, 因此 很可能有一部分、特别是较小的孔, 会在以后的高温烧结时封闭, 造成透过性能的降低。而采用 另一类型的透孔剂, 可以克服这些缺点。这种类型造孔剂的特点是: 造孔剂在基体陶瓷烧结温 度下不排除, 基体烧成后, 用水、酸或碱溶液浸出造孔剂而成为多孔陶瓷。这类造孔剂包括熔点 较高而又可溶于水、酸或碱溶液的各种无机盐或其它化合物, 要求在陶瓷烧结温度下不熔化、 不分解、不烧结、不与基体陶瓷反应。这类造孔剂特别适用于玻璃质较多的多孔陶瓷或多孔玻 璃的制造。例如, Kiefer [ 4] 申请了 Na2SO4、CaSO4、NaCl 、CaCl2 等作造孔剂制造多孔玻璃的专 利。而日本专利[ 5] 用 60% 的 Y2 O3 稳定的 Zr O2 与 40% 的 Y2 O3 混合, 在 1150℃烧结后, 浸在 30wt % 的热盐酸中 5 小时, 也制成了多孔的 ZrO2 陶瓷。
注浆工艺能使陶瓷粉料与造孔剂较好地混合, 制成的多孔陶瓷气孔分布均匀, 且设备简 单, 因而这种工艺也是制备多孔陶瓷常用的方法。该工艺的技术关键是料浆的制备。也有日本 专利用 30% -90% 陶瓷原料, 加 10-70% 的锯末作造孔剂, 制成悬浊液, 再加 0. 02% 的凝聚剂, 注浆或浇注成型, Auriol [6]则采用乙醇作分散剂, 加 0. 2% 的粘结剂来注浆成型。
( 2) 混料 为使多孔陶瓷制品的气孔分布均匀, 混料的均匀性非常重要。一般造孔剂的比重小于陶瓷 原料的比重, 另外它们的粒度大小往往不同, 因此, 难以使其很均匀混合。研究人员在这方面作 了许多努力。Sonuparlak 等[3] 采用二种不同的混料方法解决了上述问题。如果陶瓷粉末很细, 而造孔剂颗粒较粗或造孔剂溶于粘结剂中, 可以将陶瓷粉末与粘结剂混合造粒后, 再与造孔剂 混合。另一方法是将造孔剂和陶瓷粉末分别制成悬浊液, 再将二种料浆按一定比例喷雾干燥混 合。而日本专利则采用将造孔剂微粒与 ZrCl4 和稳定剂 YCl3 水溶液充分混合, 加氨水共沉淀, 得到一种胶状物质, 从而使造孔剂分布均匀。
和时间的方法, 可以控制烧结制品的气孔率和强度, 但对于多孔陶瓷烧结温度太高会使部分气
孔封闭或消失, 烧结温度太低, 则制品的强度低, 无法兼顾气孔率和强度, 而采用添加造孔剂的
方法则可以避免这种缺点, 使烧结制品既具有高的气孔率, 又具有很好的强度, 用该法制备的
多孔陶瓷, 气孔率一般在 50% 以下。
模压成型的最大优点是简单方便, 如果对制品的质量要求不高, 较小的片状、块状或管状 的多孔陶瓷都可用模压成型的方法制备。
( 4) 烧结 多孔陶瓷的烧结制度主要取决于原料, 添加剂及最后制品所需的性能。 一般, 当多孔陶瓷坯料中添加剂较多时, 为了不使坯体在烧结过程中破裂, 必须严格控制 升温速率。另外, 从方便排除各种有机添加剂考虑, 必须在添加剂排除温度下保持足够长的时 间。提高烧结温度, 延长烧结时间, 有利于提高烧结体的强度, 但会降低制品的气孔率。这目前 仍是多孔陶瓷实用化面临的问题之一。
·3 3·
二、多孔陶瓷材料的制备技术
多孔陶瓷材料的材质种类繁多, 由于使用目的不同, 对材料的性能要求各异, 因此, 近年来 逐渐开发出许多不同的制备技术。其中应用比较成功, 研究比较活跃的有: 添加造孔剂工艺, 发 泡工艺, 有机泡沫浸渍工艺, 溶胶-凝胶工艺等。表 1 比较了这几种工艺方法的特点及应用。
( 2) 陶瓷浆料的制备 浆料的基本组成是陶瓷颗粒、水和添加剂。陶瓷颗粒的成分选择取决于多孔陶瓷制品的具