锅炉系统毕业设计论文中英文资料对照外文翻译文献
锅炉蒸汽温度模糊神经网络的广义预测控制(毕业设计)

毕业设计(论文)外文翻译Neuro-fuzzy generalized predictive control ofboiler steam temperature锅炉蒸汽温度模糊神经网络的广义预测控制本 科 电气与信息学院 自 动 化 讲 师学生姓名学历层次 所在院系 所学专业 指导教师 教师职称锅炉蒸汽温度模糊神经网络的广义预测控制摘要:发电厂是非线性和不确定的复杂系统。
现代电厂在运作上的,为确保高效率和高负荷的能力,可靠的控制过热蒸汽温度是必要的。
本文提出了一类在非线性广义预测控制器的基础上的模糊神经网络( nfgpc )。
所提出的非线性控制器适用于控制一台200 MW电厂的过热蒸汽温度。
从实验的移植和仿真移植上获得比传统的控制器好得多的性能。
关键词:模糊神经网络;广义预测控制;过热蒸汽温度。
1 引言这种持续不断的电厂和电力站复杂系统的特点是非线性、不确定性和负载扰动。
蒸汽发电的过程中锅炉-汽轮机温度过热是一个重要的过程,蒸汽加热后,进入涡轮驱动发电机。
控制过热蒸汽温度不仅是在技术上具有挑战性,但在经济上也是十分重要的。
图 1锅炉过热器和蒸汽生成过程。
从图1看出,产生的蒸汽从锅炉汽包通过低温过热器后进入辐射型屏。
水变成喷涂的蒸汽,以控制过热蒸汽的温度。
适当的控制电厂过热蒸汽温度是极其重要的,可以确保整体效率和安全性。
蒸汽温度太高是不可取的地方,因为过热它可损害和高压力汽轮机,太低也不行,因为它会降低电厂效率的。
减少温度波动内过热也是重要的,因为它有助于减少在单位内机械应力造成的微裂纹,延长单位秩序寿命,并减少维修成本。
作为GPC的推导应该尽量减少这些波动,它是众多的控制器是最适合实现这一目标的。
多变量多步自适应调节已适用于控制过热蒸汽温度在150吨/ h锅炉,提出了广义预测控制以控制蒸汽温度。
非线性长程预测控制器基于神经网络发展是以控制主蒸汽温度和压力。
控制主蒸汽压力和温度的基础上,非线性模型的构成是非线性静力常数和非线性动力学。
燃煤锅炉 外文翻译 外文文献 英文文献 中英翻译

Controlling the Furnace Process in Coal-Fired BoilersThe unstable trends that exist in the market of fuel supplied to thermal power plants and the situations in which the parameters of their operation need to be changed (or preserved), as well as the tendency toward the economical and environmental requirements placed on them becoming more stringent, are factors that make the problem of controlling the combustion and heat transfer processes in furnace devices very urgent. The solution to this problem has two aspects. The first involves development of a combustion technology and,accordingly, the design of a furnace device when new installations are designed. The second involves modernization of already existing equipment. In both cases,the technical solutions being adopted must be properly substantiated with the use of both experimental and calculation studies.The experience Central Boiler-Turbine Institute Research and Production Association (Ts KTI) and Zi O specialists gained from operation of boilers and experimental investigations they carried out on models allowed them to propose several new designs of multicell and maneuverable—in other words, controllable—furnace devices that had been put in operation at power stations for several years. Along with this, an approximate zero-one-dimensional, zone wise calculation model of the furnace process in boilers had been developed at the Tsk Ti, which allowed Tsk Ti specialists to carry out engineering calculations of the main parameters of this process and calculate studies of furnaces employing different technologies of firing and combustion modes .Naturally, furnace process adjustment methods like changing the air excess factor, stack gas recirculation fraction, and distribution of fuel and air among the tiers of burners, as well as other operations written in the boiler operational chart, are used during boiler operation.However, the effect they have on the process is limited in nature. On the other hand, control of the furnace process in a boiler implies the possibility of making substantial changes in the conditions under which the combustion and heat transfer proceed in order to considerably expand the range ofloads, minimize heat losses, reduce the extent to which the furnace is contaminated with slag, decrease the emissions of harmful substances, and shift to another fuel. Such a control can be obtained by making use of the following three main factors:(i) the flows of oxidizer and gases being set to move in the flame in a desired aerodynamic manner;(ii) the method used to supply fuel into the furnace and the place at which it is admitted thereto;(iii) the fineness to which the fuel is milled.The latter case implies that a flame-bed method is used along with the flame method for combusting fuel.The bed combustion method can be implemented in three design versions: mechanical grates with a dense bed, fluidized-bed furnaces, and spouted-bed furnaces.As will be shown below, the first factor can be made to work by setting up bulky vorticisms transferring large volumes of air and combustion products across and along the furnace device. If fuel is fired in a flame, the optimal method of feeding it to the furnace is to admit it to the zones near the centers of circulating vorticisms, a situation especially typical of highly intense furnace devices. The combustion process in these zones features a low air excess factor (α< 1) and a long local time for which the components dwell in them, factors that help make the combustion process more stable and reduce the emission of nitrogen oxides .Also important for the control of a furnace process when solid fuel is fired is the fineness to which it is milled; if we wish to minimize incomplete combustion, the degree to which fuel is milled should be harmonized with the location at which the fuel is admitted into the furnace and the method for supplying it there, for the occurrence of unburned carbon may be due not only to incomplete combustion of large-size fuel fractions, but also due to fine ones failing to ignite (especially when the content of volatiles Daff < 20%).Owing to the possibility of pictorially demonstrating the motion of flows, furnace aerodynamics is attracting a great deal of attention of researchers and designers who develop and improve furnace devices. At the same time, furnace aerodynamics lies at the heart of mixing (mass transfer), a process the quantitativeparameters of which can be estimated only indirectly or by special measurements. The quality with which components are mixed in the furnace chamber proper depends on the number, layout, and momenta of the jets flowing out from individual burners or nozzles, as well as on their interaction with the flow of flue gases, with one another, or with the wall.It was suggested that the gas-jet throw distance be used as a parameter determining the degree to which fuel is mixed with air in the gas burner channel. Such an approach to estimating how efficient the mixing is may to a certain degree be used in analyzing the furnace as a mixing apparatus. Obviously, the greater the jet length (and its momentum), the longer the time during which the velocity gradient it creates in the furnace will persist there, a parameter that determines how completely the flows are mixed in it. Note that the higher the degree to which a jet is turbulence at the outlet from a nozzle or burner, the shorter the distance which it covers, and, accordingly, the less completely the components are mixed in the furnace volume. Once through burners have advantages over swirl ones in this respect.It is was proposed that the extent to which once through jets are mixed as they penetrate with velocity w2 and density ρ2 into a transverse (drift) flow moving with velocity w1 and having density ρ1 be correlated with the relative jet throw distance in the following wayWhere ks is a proportionality factor that depends on the “pitch” between the jet axes (ks= 1.5–1.8).The results of an experimental investigation in which the mixing of gas with air in a burner and then in a furnace was studied using the incompleteness of mixing as a parameter are reported in 5.A round once through jet is intensively mixed with the surrounding medium in a furnace within its initial section, where the flow velocity at the jet axis is still equal to the velocity w2 at the nozzle orifice of radius r0.The velocity of the jet blown into the furnace drops very rapidly beyond the confines of the initial section, and the axis it has in the case of wall-mounted burners bends toward the outlet from the furnace.One may consider that there are three theoretical models for analyzing the mixing of jets with flow rate G2 that enter into a stream with flow rate G1. The firstmodel is for the case when jets flow into a “free” space (G1= 0),the second model is for the case when jets flow into a transverse (drift) current with flow rate G1 G2,and the third model is for the case when jets flow into a drift stream with flow rateG1<G2. The second model represents mixing in the channel of a gas burner, and the third model represents mixing in a furnace chamber. We assume that the mixing pattern we have in a furnace is closer to the first model than it is to the second one, since 0 <G1/G2< 1, and we will assume that the throw distance h of the jet being drifted is equal to the length S0 of the “free” jet’s initial section. The ejection ability of the jet being drifted then remains the same as that of the “free” jet, and the length of the initial section can be determined using the well-known empirical formula of G.N. Amphibrachic [6] :S0= 0.67r0/a, (2)where a is the jet structure factor and r0 is the nozzle radius.At a = 0.07, the length of the round jet’s initial section is equal to 10 r0 and the radius the jet has at the transition section (at the end of the initial section) is equal to 3.3 r0. The mass flow rate in the jet is doubled in this case. The corresponding minimum furnace cross-sectional area Ff for a round once through burner with the outlet cross-sectional area Fb will then be equal to and t he ratio Ff/Fb≈20. This value is close to the actual values found in furnaces equipped with once through burners. In furnaces equipped with swirl burners, a= 0.14 and Ff/Fb≈10. In both cases, the interval between the burners is equal to the jet diameter in the transition section d tr , which differs little from the value that has been established in practice and recommended in [7].The method traditionally used to control the furnace process in large boilers consists of equipping them with a large number of burners arranged in several tiers. Obviously, if the distance between the tiers is relatively small, operations on disconnecting or connecting them affect the entire process only slightly. A furnace design employing large flat-flame burners equipped with means for controlling the flame core position using the aerodynamic principle is a step forward. Additional possibilities for controlling the process in TPE-214 and TPE-215 boilers with a steam output of 670 t/h were obtained through the use of flat-flame burners arranged in two tiers with a large distance between the tiers; this made it possible not only to raise orlower the flame, but also to concentrate or disperse the release of heat in it [1]. A very tangible effect was obtained from installing multicell (operating on coal andopen-hearth, coke, and natural gases) flat-flame burners in the boilers of cogeneration stations at metallurgical plants in Ukraine and Russia.Unfortunately, we have to state that, even at present, those in charge of selecting the type, quantity, and layout of burners in a furnace sometimes adopt technical solutions that are far from being optimal. This problem should therefore be considered in more detail.If we increase the number of burners nb in a furnace while retaining their total cross-sectional area (ΣFb=idem) and the total flow rate of air through them, their equivalent diameters deq will become smaller, as will the jet momentums GB, resulting in a corresponding decrease in the jet throw distance Hb and the mass they eject. The space with high velocity gradients also becomes smaller, resulting in poorer mixing in the furnace as a whole. This factor becomes especially important when the emissions of Box and CO are suppressed right inside the furnace using staged combustio n (at αb < 1) under the conditions of a Fortinbras nonuniform distribution of fuel among the burners.In [1], a quantitative relationship was established between the parameters characterizing the quality with which once through jets mix with one another as they flow into a limited space with the geometrical parameter of concentration = with nb = idem and GB = idem. By decreasing this parameter we improve the mass transfer in the furnace; however, this entails an increase in the flow velocity and the expenditure of energy (pressure drop) in the burners with the same Fb. At the same time, we know from experience and calculations that good mixing in a furnace can be obtained without increasing the head loss if we resort to large long-range jets. This allows a much less stringent requirement to be placed on the degree of uniformity with which fuel must be distributed among the burners. Moreover, fuel may in this case be fed to the furnace location where it is required from process control considerations.For illustration purposes, we will estimate the effect the number of burners has on the mixing in a furnace at = = idem. schematically shows the plan views of two furnace chambers differing in the number of once through round nozzles (two andfour) placed in a tier (on one side of the furnace). The furnaces have the same total outlet cross-sectional areas of the nozzles (ΣF b) and the same jet velocities related to these areas (wb). The well-known swirl furnace of the TsKTI has a design close to the furnace arrangement under consideration. According to the data of [1], the air fraction βair that characterizes the mixing and enters through once through burners into the furnace volume beneath them can be estimated using the formula βair = 1 – (3) which has been verified in the range = 0.03–0.06 for a furnace chamber equipped with two frontal once through burners. Obviously, if we increase the number of burners by a factor of 2, their equivalent diameter, the length of the initial section of jets S0 and the area they “serve” will reduce by a factor of Then, for example, at = 0.05, the fraction βair will decrease from 0.75 to 0.65. Thus, Eq. (3) may be written in the following form for approximately assessing the effect of once through burners on the quality of mixing in a furnace:βair = 1 – 3.5f nb ' ,where is the number of burners (or air nozzles) on one wall when they are arranged in one tier both in onesided and opposite manners.The number of burners may be tentatively related to the furnace depth af (at the same = idem) using the expression (5)It should be noted that the axes of two large opposite air nozzles ( = 1)—an arrangement implemented in an inverted furnace—had to be inclined downward by more than 50° [8].One well-known example of a furnace device in which once through jets are used to create a large vortex covering a considerable part of its volume is a furnace with tangentially arranged burners. Such furnaces have received especially wide usein combination with pulverizing fans. However, burners with channels having a small equivalent diameter are frequently used for firing low-calorific brown coals with high content of moisture. As a result, the jets of air-dust mixture and secondary air that go out from their channels at different velocities(w2/w1 = 2–3) become turbulence and lose the ability to be thrown a long distance; as a consequence, the flame comes closer to the water walls and the latter are contaminated with slag. One method by which the tangential combustion scheme can be improved consists of organizing the so-called concentric admission of large jets of air-dust mixture and secondary air with the fueland air nozzles spaced apart from one another over the furnace perimeter, accompanied by intensifying the ventilation of mills [9, 10]. Despite the fact that the temperature level in the flame decreases, the combustion does not become less stable because the fuel mixes with air in a stepwise manner in a horizontal plane.V ortex furnace designs with large cortices the rotation axes of which are arranged transversely with respect to the main direction of gas flow have wide possibilities in terms of controlling the furnace process. In [1], four furnace schemes with a controllable flame are described, which employ the principle of large jets colliding with one another; three of these schemes have been implemented. A boiler with a steam capacity of 230 t/h has been retrofitted in accordance with one of these schemes (with an inverted furnace) . Tests of this boiler, during which air-dust mixture was fed at a velocity of 25–30 m/s from the boiler front using a high concentration dust system, showed that the temperature of gases at the outlet from the furnace had a fairly uniform distribution both along the furnace width and depth . A simple method of shifting the flame core over the furnace height was checked during the operation of this boiler, which consisted of changing the ratio of air flow rates through the front and rear nozzles;this allowed a shift to be made from running the furnace in adry-bottom mode to a slag-tap mode and vice Versace. A bottom-blast furnace scheme has received rather wide use in boilers equipped with different types of burners and mills. Boilers with steam capacities ranging from 50 to 1650 t/h with such an aerodynamic scheme of furnaces manufactured by ZiO and Bergomask have been installed at a few power stations in Russia and abroad . We have to point out that, so far as the efficiency of furnace process control is concerned, a combination of the following two aerodynamic schemes is of special interest: the inverted scheme and the bottom-blast one. The flow pattern and a calculation analysis of the furnace process in such a furnace during the combustion of lean coal are presented in [13].Below, two other techniques for controlling the furnace process are considered. Boilers with flame–stoker furnaces have gained acceptance in industrial power engineering, devices that can be regarded to certain degree as controllable ones owing to the presence of two zones in them . Very different kinds of fuel can be jointly combusted in these furnaces rather easily. An example of calculating such a furnacedevice is given in [2]. As for boilers of larger capacity, work on developing controllable two-zone furnaces is progressing slowly . The development of a furnace device using the so-called VIR technology (the transliterated abbreviation of the Russian introduction, innovation, and retrofitting) can be considered as holding promise in this respect. Those involved in bringing this technology to the state of industry standard encountered difficulties of an operational nature (the control of the process also presented certain difficulties). In our opinion, these difficulties are due to the fact that the distribution of fuel over fractions can be optimized to a limited extent and that the flow in the main furnace volume has a rather sluggish aerodynamic structure. It should also be noted that the device for firing the coarsest fractions of solid fuel in a spouting bed under the cold funnel is far from being technically perfect.Centrifugal dust concentrators have received acceptance for firing high-reactive coals in schemes employing pulverizing fans to optimize the distribution of fuel as to its flow rate and fractions. The design of one such device is schematically shown in [9]. Figure shows a distribution of fuel flow rates among four tiers of burners that is close to the optimum one. This distribution can be controlled if we furnish dust concentrators with a device with variable blades, a solution that has an adequate effect on the furnace process.燃煤锅炉的燃烧进程控制存在于火电厂的市场的燃料供应,某些操作参数需要改变(或保留)的情况下,以及经济和环境方面倾向的要求使他们变得更加严格的不稳定趋势是导致使控制燃烧与传热过程炉设备非常紧迫的主要因素。
燃煤锅炉的燃烧进程控制大学毕业论文外文文献翻译及原文
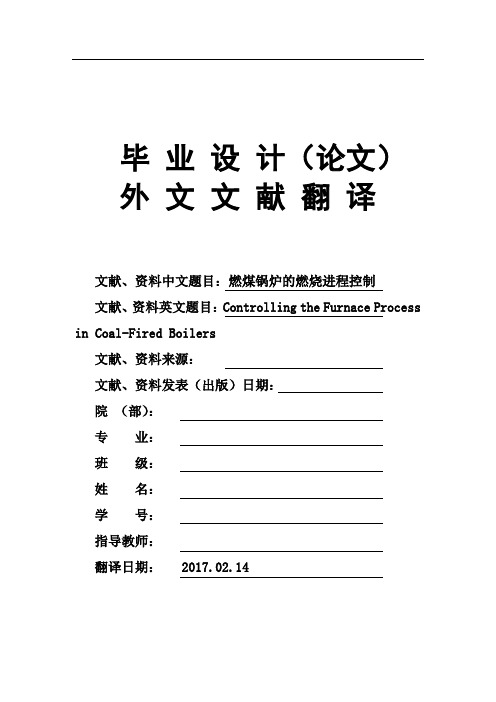
毕业设计(论文)外文文献翻译文献、资料中文题目:燃煤锅炉的燃烧进程控制文献、资料英文题目:Controlling the Furnace Process in Coal-Fired Boilers文献、资料来源:文献、资料发表(出版)日期:院(部):专业:班级:姓名:学号:指导教师:翻译日期: 2017.02.14Controlling the Furnace Process in Coal-Fired BoilersThe unstable trends that exist in the market of fuel supplied to thermal power plants and the situations in which the parameters of their operation need to be changed (or preserved), as well as the tendency toward the economical and environmental requirements placed on them becoming more stringent, are factors that make the problem of controlling the combustion and heat transfer processes in furnace devices very urgent. The solution to this problem has two aspects. The first involves development of a combustion technology and,accordingly, the design of a furnace device when new installations are designed. The second involves modernization of already existing equipment. In both cases,the technical solutions being adopted must be properly substantiated with the use of both experimental and calculation studies.The experience Central Boiler-Turbine Institute Research and Production Association (Ts KTI) and Zi O specialists gained from operation of boilers and experimental investigations they carried out on models allowed them to propose several new designs of multicell and maneuverable—in other words, controllable—furnace devices that had been put in operation at power stations for several years. Along with this, an approximate zero-one-dimensional, zone wise calculation model of the furnace process in boilers had been developed at the Tsk Ti, which allowed Tsk Ti specialists to carry out engineering calculations of the main parameters of this process and calculate studies of furnaces employing different technologies of firing and combustion modes .Naturally, furnace process adjustment methods like changing the air excess factor, stack gas recirculation fraction, and distribution of fuel and air among the tiers of burners, as well as other operations written in the boiler operational chart, are used during boiler operation.However, the effect they have on the process is limited in nature. On the other hand, control of the furnace process in a boiler implies the possibility of making substantial changes in the conditions under which the combustion and heat transfer proceed in order to considerably expand the range of loads, minimize heat losses, reduce the extent to which the furnace is contaminatedwith slag, decrease the emissions of harmful substances, and shift to another fuel. Such a control can be obtained by making use of the following three main factors:(i) the flows of oxidizer and gases being set to move in the flame in a desired aerodynamic manner;(ii) the method used to supply fuel into the furnace and the place at which it is admitted thereto;(iii) the fineness to which the fuel is milled.The latter case implies that a flame-bed method is used along with the flame method for combusting fuel.The bed combustion method can be implemented in three design versions: mechanical grates with a dense bed, fluidized-bed furnaces, and spouted-bed furnaces.As will be shown below, the first factor can be made to work by setting up bulky vorticisms transferring large volumes of air and combustion products across and along the furnace device. If fuel is fired in a flame, the optimal method of feeding it to the furnace is to admit it to the zones near the centers of circulating vorticisms, a situation especially typical of highly intense furnace devices. The combustion process in these zones features a low air excess factor (α< 1) and a long local time for which the components dwell in them, factors that help make the combustion process more stable and reduce the emission of nitrogen oxides .Also important for the control of a furnace process when solid fuel is fired is the fineness to which it is milled; if we wish to minimize incomplete combustion, the degree to which fuel is milled should be harmonized with the location at which the fuel is admitted into the furnace and the method for supplying it there, for the occurrence of unburned carbon may be due not only to incomplete combustion of large-size fuel fractions, but also due to fine ones failing to ignite (especially when the content of volatiles Daff < 20%).Owing to the possibility of pictorially demonstrating the motion of flows, furnace aerodynamics is attracting a great deal of attention of researchers and designers who develop and improve furnace devices. At the same time, furnace aerodynamics lies at the heart of mixing (mass transfer), a process the quantitative parameters of which can be estimated only indirectly or by special measurements. Thequality with which components are mixed in the furnace chamber proper depends on the number, layout, and momenta of the jets flowing out from individual burners or nozzles, as well as on their interaction with the flow of flue gases, with one another, or with the wall.It was suggested that the gas-jet throw distance be used as a parameter determining the degree to which fuel is mixed with air in the gas burner channel. Such an approach to estimating how efficient the mixing is may to a certain degree be used in analyzing the furnace as a mixing apparatus. Obviously, the greater the jet length (and its momentum), the longer the time during which the velocity gradient it creates in the furnace will persist there, a parameter that determines how completely the flows are mixed in it. Note that the higher the degree to which a jet is turbulence at the outlet from a nozzle or burner, the shorter the distance which it covers, and, accordingly, the less completely the components are mixed in the furnace volume. Once through burners have advantages over swirl ones in this respect.It is was proposed that the extent to which once through jets are mixed as they penetrate with velocity w2 and density ρ2 into a transverse (drift) flow moving with velocity w1 and having density ρ1 be correlated with the relative jet throw distance in the following wayWhere ks is a proportionality factor that depends on the ―pitch‖ between the jet axes (ks= 1.5–1.8).The results of an experimental investigation in which the mixing of gas with air in a burner and then in a furnace was studied using the incompleteness of mixing as a parameter are reported in 5.A round once through jet is intensively mixed with the surrounding medium in a furnace within its initial section, where the flow velocity at the jet axis is still equal to the velocity w2 at the nozzle orifice of radius r0.The velocity of the jet blown into the furnace drops very rapidly beyond the confines of the initial section, and the axis it has in the case of wall-mounted burners bends toward the outlet from the furnace.One may consider that there are three theoretical models for analyzing the mixing of jets with flow rate G2 that enter into a stream with flow rate G1. The first model is for the case when jets flow into a ―free‖ space (G1= 0),the second model isfor the case when jets flow into a transverse (drift) current with flow rate G1 G2,and the third model is for the case when jets flow into a drift stream with flow rateG1<G2. The second model represents mixing in the channel of a gas burner, and the third model represents mixing in a furnace chamber. We assume that the mixing pattern we have in a furnace is closer to the first model than it is to the second one, since 0 <G1/G2< 1, and we will assume that the throw distance h of the jet being drifted is equal to the length S0 of the ―free‖ jet’s initial section. The ejection ability of the jet being drifted then remains the same as that of the ―free‖ jet, and the length of the initial section can be determined using the well-known empirical formula of G.N. Amphibrachic [6] :S0= 0.67r0/a, (2)where a is the jet structure factor and r0 is the nozzle radius.At a = 0.07, the length of the round jet’s initial section is equal to 10 r0 and the radius the jet has at the transition section (at the end of the initial section) is equal to 3.3 r0. The mass flow rate in the jet is doubled in this case. The corresponding minimum furnace cross-sectional area Ff for a round once through burner with the outlet cross-sectional area Fb will then be equal to and the ratio Ff/Fb≈20. This value is close to the actual values found in furnaces equipped with once through burners. In furnaces equipped with swirl burners, a= 0.14 and Ff/Fb≈10. In both cases, the interval between the burners is equal to the jet diameter in the transition section d tr , which differs little from the value that has been established in practice and recommended in [7].The method traditionally used to control the furnace process in large boilers consists of equipping them with a large number of burners arranged in several tiers. Obviously, if the distance between the tiers is relatively small, operations on disconnecting or connecting them affect the entire process only slightly. A furnace design employing large flat-flame burners equipped with means for controlling the flame core position using the aerodynamic principle is a step forward. Additional possibilities for controlling the process in TPE-214 and TPE-215 boilers with a steam output of 670 t/h were obtained through the use of flat-flame burners arranged in two tiers with a large distance between the tiers; this made it possible not only to raise or lower the flame, but also to concentrate or disperse the release of heat in it [1]. A verytangible effect was obtained from installing multicell (operating on coal andopen-hearth, coke, and natural gases) flat-flame burners in the boilers of cogeneration stations at metallurgical plants in Ukraine and Russia.Unfortunately, we have to state that, even at present, those in charge of selecting the type, quantity, and layout of burners in a furnace sometimes adopt technical solutions that are far from being optimal. This problem should therefore be considered in more detail.If we increase the number of burners nb in a furnace while retaining their total cross-sectional area (ΣFb=idem) and the total flow rate of air through them, their equivalent diameters deq will become smaller, as will the jet momentums GB, resulting in a corresponding decrease in the jet throw distance Hb and the mass they eject. The space with high velocity gradients also becomes smaller, resulting in poorer mixing in the furnace as a whole. This factor becomes especially important when the emissions of Box and CO are suppressed right inside the furnace using staged combustion (at αb < 1) under the conditions of a Fortinbras nonuniform distribution of fuel among the burners.In [1], a quantitative relationship was established between the parameters characterizing the quality with which once through jets mix with one another as they flow into a limited space with the geometrical parameter of concentration = with nb = idem and GB = idem. By decreasing this parameter we improve the mass transfer in the furnace; however, this entails an increase in the flow velocity and the expenditure of energy (pressure drop) in the burners with the same Fb. At the same time, we know from experience and calculations that good mixing in a furnace can be obtained without increasing the head loss if we resort to large long-range jets. This allows a much less stringent requirement to be placed on the degree of uniformity with which fuel must be distributed among the burners. Moreover, fuel may in this case be fed to the furnace location where it is required from process control considerations.For illustration purposes, we will estimate the effect the number of burners has on the mixing in a furnace at = = idem. schematically shows the plan views of two furnace chambers differing in the number of once through round nozzles (two and four) placed in a tier (on one side of the furnace). The furnaces have the same totaloutlet cross-sectional areas of the nozzles (ΣF b) and the same jet velocities related to these areas (wb). The well-known swirl furnace of the TsKTI has a design close to the furnace arrangement under consideration. According to the data of [1], the air fraction βair that characterizes the mixing and enters through once through burners into the furnace volume beneath them can be estimated using the formula βair = 1 – (3) which has been verified in the range = 0.03–0.06 for a furnace chamber equipped with two frontal once through burners. Obviously, if we increase the number of burners by a factor of 2, their equivalent diameter, the length of the initial section of jets S0 and the area they ―serve‖ will reduce by a factor of Then, for example, at = 0.05, the fraction βair will decrease from 0.75 to 0.65. Thus, Eq. (3) may be written in the following form for approximately assessing the effect of once through burners on the quality of mixing in a f urnace:βair = 1 – 3.5f nb ' ,where is the number of burners (or air nozzles) on one wall when they are arranged in one tier both in onesided and opposite manners.The number of burners may be tentatively related to the furnace depth af (at the same = idem) using the expression (5)It should be noted that the axes of two large opposite air nozzles ( = 1)—an arrangement implemented in an inverted furnace—had to be inclined downward by more than 50° [8].One well-known example of a furnace device in which once through jets are used to create a large vortex covering a considerable part of its volume is a furnace with tangentially arranged burners. Such furnaces have received especially wide usein combination with pulverizing fans. However, burners with channels having a small equivalent diameter are frequently used for firing low-calorific brown coals with high content of moisture. As a result, the jets of air-dust mixture and secondary air that go out from their channels at different velocities(w2/w1 = 2–3) become turbulence and lose the ability to be thrown a long distance; as a consequence, the flame comes closer to the water walls and the latter are contaminated with slag. One method by which the tangential combustion scheme can be improved consists of organizing the so-called concentric admission of large jets of air-dust mixture and secondary air with the fuel and air nozzles spaced apart from one another over the furnace perimeter,accompanied by intensifying the ventilation of mills [9, 10]. Despite the fact that the temperature level in the flame decreases, the combustion does not become less stable because the fuel mixes with air in a stepwise manner in a horizontal plane.V ortex furnace designs with large cortices the rotation axes of which are arranged transversely with respect to the main direction of gas flow have wide possibilities in terms of controlling the furnace process. In [1], four furnace schemes with a controllable flame are described, which employ the principle of large jets colliding with one another; three of these schemes have been implemented. A boiler with a steam capacity of 230 t/h has been retrofitted in accordance with one of these schemes (with an inverted furnace) . Tests of this boiler, during which air-dust mixture was fed at a velocity of 25–30 m/s from the boiler front using a high concentration dust system, showed that the temperature of gases at the outlet from the furnace had a fairly uniform distribution both along the furnace width and depth . A simple method of shifting the flame core over the furnace height was checked during the operation of this boiler, which consisted of changing the ratio of air flow rates through the front and rear nozzles;this allowed a shift to be made from running the furnace in adry-bottom mode to a slag-tap mode and vice Versace. A bottom-blast furnace scheme has received rather wide use in boilers equipped with different types of burners and mills. Boilers with steam capacities ranging from 50 to 1650 t/h with such an aerodynamic scheme of furnaces manufactured by ZiO and Bergomask have been installed at a few power stations in Russia and abroad . We have to point out that, so far as the efficiency of furnace process control is concerned, a combination of the following two aerodynamic schemes is of special interest: the inverted scheme and the bottom-blast one. The flow pattern and a calculation analysis of the furnace process in such a furnace during the combustion of lean coal are presented in [13].Below, two other techniques for controlling the furnace process are considered. Boilers with flame–stoker furnaces have gained acceptance in industrial power engineering, devices that can be regarded to certain degree as controllable ones owing to the presence of two zones in them . Very different kinds of fuel can be jointly combusted in these furnaces rather easily. An example of calculating such a furnace device is given in [2]. As for boilers of larger capacity, work on developingcontrollable two-zone furnaces is progressing slowly . The development of a furnace device using the so-called VIR technology (the transliterated abbreviation of the Russian introduction, innovation, and retrofitting) can be considered as holding promise in this respect. Those involved in bringing this technology to the state of industry standard encountered difficulties of an operational nature (the control of the process also presented certain difficulties). In our opinion, these difficulties are due to the fact that the distribution of fuel over fractions can be optimized to a limited extent and that the flow in the main furnace volume has a rather sluggish aerodynamic structure. It should also be noted that the device for firing the coarsest fractions of solid fuel in a spouting bed under the cold funnel is far from being technically perfect.Centrifugal dust concentrators have received acceptance for firing high-reactive coals in schemes employing pulverizing fans to optimize the distribution of fuel as to its flow rate and fractions. The design of one such device is schematically shown in [9]. Figure shows a distribution of fuel flow rates among four tiers of burners that is close to the optimum one. This distribution can be controlled if we furnish dust concentrators with a device with variable blades, a solution that has an adequate effect on the furnace process.。
锅炉系统毕业设计论文中英文资料对照外文翻译文献
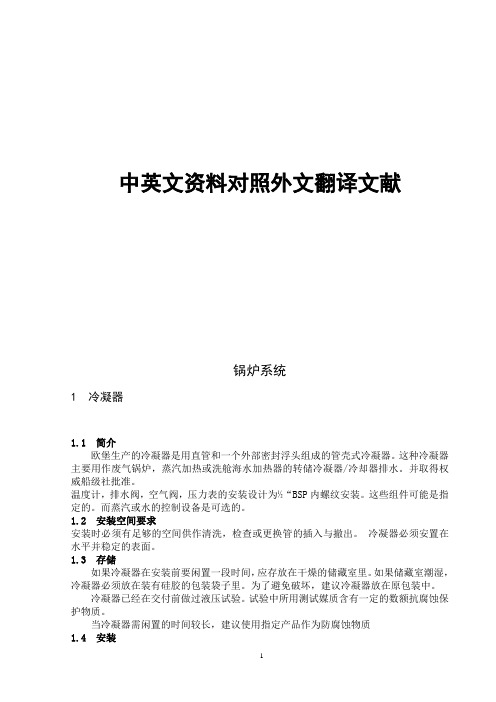
中英文资料对照外文翻译文献锅炉系统1 冷凝器1.1 简介欧堡生产的冷凝器是用直管和一个外部密封浮头组成的管壳式冷凝器。
这种冷凝器主要用作废气锅炉,蒸汽加热或洗舱海水加热器的转储冷凝器/冷却器排水。
并取得权威船级社批准。
温度计,排水阀,空气阀,压力表的安装设计为½“BSP内螺纹安装。
这些组件可能是指定的。
而蒸汽或水的控制设备是可选的。
1.2 安装空间要求安装时必须有足够的空间供作清洗,检查或更换管的插入与撤出。
冷凝器必须安置在水平并稳定的表面。
1.3 存储如果冷凝器在安装前要闲置一段时间,应存放在干燥的储藏室里。
如果储藏室潮湿,冷凝器必须放在装有硅胶的包装袋子里。
为了避免破坏,建议冷凝器放在原包装中。
冷凝器已经在交付前做过液压试验。
试验中所用测试媒质含有一定的数额抗腐蚀保护物质。
当冷凝器需闲置的时间较长,建议使用指定产品作为防腐蚀物质1.4 安装冷凝器设计为垂直或水平安装。
在水平安装的情况下,蒸汽喷嘴必须朝上,而冷凝水出口喷嘴朝下。
如果是垂直安装冷凝器,蒸汽入口和海水出口端必须朝上。
排水和空气排放阀必须安装在冷凝器在最低和最高点的中间线的位置。
任何选择性的控制设备必须根据具体指示安装。
步骤A:将冷凝器安装在水平平面上。
步骤B:钻基础固定螺栓孔。
步骤C:将螺栓放入孔中并拧紧。
连接冷凝器步骤D:移除所有的塞子和盲板,然后再连接冷凝器。
步骤E:在连接中确保没有杂质进入。
步骤F:管道连接起来,确保从管道和冷凝器之间没有强制力的产生。
1.5 调试启动前要确保所有连接都牢固地拧紧是很重要的。
同样重要的是,冷凝器和连接管道空气要彻底排出。
步骤A:如果装有安全阀,必须加以调整到最大设计压力或较低。
步骤B:法兰螺栓要拧紧。
拧紧法兰螺栓时始终使用扭矩扳手。
步骤C:运行一小时,停止冷凝器,并重新拧紧所有螺栓。
步骤D:启动阶段,冷凝器的两边都要排出空气,必须认真仔细的检查回路的泄漏。
1.6 性能冷凝器性能须附和传热计算表规定的要求。
外文翻译----燃气锅炉控制系统

附录2燃气锅炉控制系统锅炉燃烧系统是使燃料燃烧所产生的热量,适应蒸汽负荷的需要,同时还要保证经济燃烧和锅炉安全运行。
首先,要维持蒸汽母管的蒸汽压力不变,采用双交叉限幅控制,使锅炉系统无论在负荷上升或下降时都能满足“负荷增加时,先增加空气量,后增加燃料量;负荷减少时,先减少燃料量,后减少空气量”,以使锅炉燃烧持续保持在无黑烟状态;其次,保持锅炉燃烧的经济性,以达到最小的热量损失和最大的燃烧效率;最后,始终维持炉膛负压在一定范围内,以使燃烧工况、锅炉房工作条件、锅炉的维护及安全运行都最有利。
在工业锅炉燃烧过程中,用常规仪表进行控制,存在滞后、间歇调节、烟气中氧含量超过给定值、低负荷和烟气温度过低等问题。
采用PLC 对锅炉进行控制时,由于它的运算速度快、精度高、准确可靠,可适应复杂的、难于处理的控制系统。
因而,可以解决以上由常规仪表控制难以解决的问题。
负荷调节是以蒸汽压力为主调参数,蒸汽流量为前馈信号,并考虑鼓风量的影响而进行的复杂PID 串级调节;氧量调节通过氧量信号、蒸汽流量及鼓风量来调节炉排电机转速,控制给煤量;炉膛压力调节以炉膛压力为主调参数,鼓风量为前馈信号进行P I 调节,控制引风机转速; 在锅炉燃烧控制中,对蒸汽压力极高进行越限报警及联锁控制:即当蒸汽压力高于报警上限时,产生上限越限声光报警,当蒸汽压力高于报警上上限时,除进行越限声光报警外,PLC 发出联锁控制信号,强制鼓风电机、引风电机及炉排电机停机,锅炉紧急停炉,以保证安全生产。
系统硬件组成根据工艺特点及锅炉的位置分布,选择IPC 和PLC 组成基于IPC- PLC 的三级DCS 监控系统,整个控制系统的组成图。
用三台西门子S7- 300 系列PLC 分别控制三台锅炉,安装在中控室。
PLC 用西门子的Step7 软件进行硬件组态, 所有的PID 控制、联锁保护、开关量控制均在PLC 上实现。
三台PLC 通过以太网与上位工控机相连, 将现场采集的数据传给上位工控机, 并接收上位工控机的各种数据和控制命令。
锅炉专业英语中英文对照表(综合版)

boiler锅炉boiler unit锅炉机组stationary boiler固定式锅炉steam boiler/generator蒸汽锅炉utility boiler电站锅炉industrial boiler工业锅炉hot water boiler热水锅炉indoor boiler室内锅炉ourdoor boiler露天锅炉package boiler快装锅炉shop-assembled boiler组装锅炉field-assembled boilerfield-erected boilersupercritical pressure boiler超临界压力锅炉subcritical pressure boiler亚临界压力锅炉superhigh pressure boiler超高压锅炉high pressure boiler高压锅炉medium pressure boiler中压锅炉low pressure boiler低压锅炉natural circulation boiler自然循环锅炉forced circulation boiler强制循环锅炉assisted circulation boiler辅助循环锅炉controlled circulation boiler控制循环锅炉once-through boiler直流锅炉combined circulation boiler复合循环锅炉low circulation-ratio boiler低循环倍率锅炉solid-fuel fired boiler固体燃料锅炉liquid-fuel fired boiler液体燃料锅炉coal fired boiler燃煤锅炉oil fired boiler燃油锅炉gas fired boiler燃气锅炉multi-fuel fired boiler混烧锅炉boiler with dry-ash furnaceboiler with dry-bottom furnaceboiler with slag-tap furnaceboiler with wet-bottom furnacesupercharged boiler增压锅炉water tube boiler水管锅炉cross drum boiler横锅筒(汽包)锅炉longitudinal drum boiler纵锅筒(汽包)锅炉shell boiler锅壳锅炉horizontal boiler卧式锅壳锅炉vertical boiler立式锅炉stationary boiler of locomotive type固定式机车锅炉π-type boiler (two-pass boiler)π型锅炉box-type boiler箱型锅炉tower boiler 塔型锅炉散装锅炉固态排渣锅炉液态排渣锅炉D-type boilerD 型锅炉rated capacitynominal capacitymaximum continuous rating最大连续蒸发量rated heating capacity额定供热量nominal steam conditionnominal steam parameternominal steam pressure额定蒸汽压力nominal steam temperature额定蒸汽温度(nominal) hot water temperature热水温度feed water temperature给水温度return water temperature回水温度circulation circuitsteam generating circuitsteam purification蒸汽净化steam temperature control汽温调节feed water给水condensate凝结水make-up water补给水boiler water锅水;炉水boiling crisis沸腾换热恶化as-fired fuel炉前燃料fire bedfuel bedfire line最高火界additive添加剂flue gas dew point烟气露点boiler circulation水循环mechanical carry-overmoisture carry-overvaporous carry-over溶解携带water separation汽水分离steam washing蒸汽清洗stage evaporation分段蒸发pressurized firing压力燃烧negative-pressure firing负压燃烧grate firing火床燃烧suspension firing火室燃烧;悬浮燃烧tangential firing切向燃烧opposed firing对冲燃烧cyclone-furnace firing旋风燃烧fluidized-bed combustion沸腾燃烧gas recirculation烟气再循环natural draft自然通风mechanical draft机械通风balanced draft平衡通风forced draft 正压通风火床机械携带额定蒸发量额定蒸汽参数循环回路induced draft负压通风zone control分段送风pressure atomizationmechanical atomizationtwin-fluid atomization双流体雾化rotary-cup atomization旋杯雾化;转杯雾化direct leakageinfiltration leakagebypass leakageentrained leakageboiler proper锅炉本体heating surface受热面radiant heating surface辐射受热面convection heating surface对流受热面pressure part受压部件;受压元件cylindrical shell筒体head封头;端盖header集箱;联箱tube panel管屏up flow riser tube panel垂直上升管屏ribbon panel回带管屏spirally-wound tubes水平围绕管圈tube bundle管束gas passgas ductconvection pass对流烟道parallel gas passes并联烟道air duct风道arch拱furnace arch折焰角water-cooled hopper bottom冷灰斗wall with refractory liningrefractory beltsupporting tube悬吊管design pressure设计压力maximum allowable working pressure最高允许工作压力maximum allowable metal temperature最高许用壁温furnace enclosure design pressure炉膛设计压力heat input输入热量heat output锅炉有效利用热量fuel consumption燃料消耗量calculated fuel consumption计算燃料消耗量ash-retention efficiency排渣率load range at constant temperature(保持)额定汽温的负荷范围injection flow(rate)喷水量blowdown flow(rate)排污量theoretical air 理论空气量卫燃带压力雾化;机械雾化直接泄漏间接泄漏烟道excess air ratio过量空气系数hot air temperature热风温度exhaust gas temperature排烟温度theoretical combustion temperatureadiabatic temperaturefurnace outlet gas temperaturefurnace exit gas temperaturepressure drop汽水阻力draft losspressure dropstack draft自生通风压头available static head运动压头circulation ratio循环倍率circulation velocity循环水速steam quality by mass质量含汽率;干度mass velocity质量流速critical steam quality临界含汽率steam quality at minimum heat transfercoefficient最高壁温处含汽率furnace volume炉膛容积furnace volume heat release rateheat liberation rate in furnacefurnace cross-section heat release ratefurnace plan heat release rateburner zone wall heat release rate燃烧器区域炉壁热负荷furnace wall heat release rate炉壁热负荷furnace wall heat flux density炉壁热流密度critical heat flux density临界热流密度grate heat release rate炉排(面积)热负荷burner heat input燃烧器热功率ignition energy点火能量evaporation rate受热面蒸发率percentage of economizer evaporation省煤器沸腾率primary air一次风secondary air二次风tertiary air三次风imaginary circle假想切圆percentage of air space通风截面比fineness煤粉细度explosion mixture limits爆炸界限furnace炉膛;炉胆fire box火箱smoke box烟箱burner燃烧器tilting burner摆动式燃烧器igniter点火器oil atomizer 油雾化器理论燃烧温度炉膛出口烟气温度通风阻力炉膛容积热负荷炉膛截面积热负荷register调风器stabilizer稳燃器wind box风箱burner portburner quarlgrate炉排hand-fired grate手烧炉排stoker-fired gratemechanical stokertravelling grate stoker链条炉排chain grate stoker链带式炉排bar grate stoker横梁式炉排louvre stoker鳞片式炉排vibrating stoker振动炉排inclined reciprocating grate往复炉排spreader stoker抛煤机air compartment风室reinjection system飞灰复燃装置drum锅筒;汽包steam drum上锅筒water drum下锅筒shell锅壳drum internals锅筒内部装置;汽包内部装置steam washer清洗装置cyclone separator旋风分离器turbo separator轴流式分离器baffle plate缝隙挡板corrugated scrubber百叶窗分离器screen separator钢丝网分离器perforated distribution plate多孔板dry pipe集汽管evaporating heating surface蒸发受热面water-cooled wall水冷壁membrane wall膜式水冷壁division wall双面水冷壁anti-clinker box防焦箱gererating tube bankboiler convection tube bankboiler (slag) screen防渣管fire tube ;smoke tube烟管;火管mixer混合器superheater过热器radiant superheater辐射过热器wall superheater墙式过热器platen superheater屏式过热器convection surperheater对流过热器steam-cooled wall 包墙过热器燃烧器喷口机械炉排锅炉管束steam-cooled roof顶棚管过热器reheater再热器attemperatordesuperheatersurface type attemperatorsurface type desuperheaterspray type attemperatorspray type desuperheaterbifluxreheater superheater attemperatorbypass damper旁路挡板economizer省煤器steaming economizer沸腾式省煤器steel tube economizer钢管省煤器finned tube economizer鳍片管省煤器cast-iron gilled tube economizer铸铁省煤器air heater空气预热器tubular air heater管式空气预热器rotary air heaterregenerative air heater rotating-plate type regenerativeair heaterLjungstrom type air heaterstationary-plate type regenerativeair heaterrothemuhle type air heatersteam air heater暖风器boiler structure锅炉构架top-supported structure by beams支承式锅炉构架top-supported structure by hangers悬吊式锅炉构架buckstay刚性梁inner casing内护板outer casing外护板boiler steam and water circuit锅炉汽水系统boiler external piping锅炉范围内管道start-up system启动系统start-up flash tank启动分离器safety valve安全阀safety relief valve安全泄放阀water level indicator水位表injector注水器boiler setting炉墙soot blower吹灰器slag removal equipment除渣设备boiler efficiency锅炉效率;锅炉热效率boiler operating availability锅炉可用率boiler forced outage rate锅炉事故率feed water condition 给水品质汽-汽热交换器回转式空气预热器受热面回转式预热器风罩回转式预热器减温器面式减温器喷水减温器steam purity 蒸汽品质moisture in steam 蒸汽湿度boiler water concentration 锅水浓度;炉水浓度total dissolved salt 总含盐量total solid (matter)全固形物dissolved solid (matter)溶解固形物suspended solid (matter)悬浮物total hardness (总)硬度alkalinity 碱度heat loss 热损失heat loss due to exhaust gas 排烟热损失heat loss due to unburned gases 气体(化学)未完全燃烧热损失heat loss due to unburned carbon inrefuse 固体(机械)未完全燃烧热损失heat loss due to radiation 散热损失heat loss due to sensible heat in slag 灰渣物理热损失unburned combustible in flue dustunburned carbon in flue dust unburned combustible in slagunburned carbon in slag unburned combustible in sifting 漏煤可燃物含量dust loadingdust density load range of boiler 锅炉负荷调节范围turndown ratio 燃烧器调节比air leakage factor 漏风系数set pressure 整定压力start-to-discharge pressure 前泄压力popping pressure 起座压力reseating pressure 回座压力blowdown 回座压差discharge capacity 排放量;排汽能力boiler efficiency test 锅炉效率试验;锅炉热效率试验hydrostatic test 水压试验hydrostatic deformation test 验证性水压试验air leakage test 漏风试验pressure decay test 风压试验load test 负荷试验circulation test 水循环试验thermal chemical test 热化学试验sounding of tube by balls 通球试验safety valve operating test 安全阀校验flue gas analysis 烟气分析Orsat (gas analyser)奥氏(烟气)分析器suction pyrometer 抽气式热电偶(高温计)venturi pneumatic pyrometer 气力式高温计heat flux meter 热流计飞灰可燃物含量;飞灰含碳量炉渣可燃物含量;炉渣含碳量烟气含尘量start-up启动filling上水water level水位initial water level点火水位purge吹扫blowoff放水drain疏水blowdown排污raising pressure升压bringing a boiler onto the line 并汽start-up pressure启动压力start-up flow rate启动流量shutdownoutageout of service停用banking fire压火storage停炉保护chemical cleaning化学清洗boiling-out(碱)煮炉flushing冲管steam-line blowing 吹管passivating钝化drying-out烘炉flow stagnation停滞flow reversal倒流separation of two-phase fluid 汽水分层steam bindingsteam blanketingpriming汽水共腾foaming泡沫共腾external deposit烟气侧沉积物internal deposit汽水侧沉积物slagging结渣fouling积灰clogging堵灰pitting attack点状腐蚀ductile gouging延性腐蚀hydrogen damage 氢脆caustic embrittlement苛性脆化high temperature corrosion 高温腐蚀low temperature corrosion 低温腐蚀overheating超温;过热flashback回火blow off脱火loss of ignition熄火;灭火furnace explosion炉膛爆炸furnace implosion 炉膛内爆汽塞停炉furnace puff炉膛爆燃blow hole火口secondary combustion二次燃烧。
工业锅炉节能毕业论文中英文资料外文翻译文献

工业锅炉节能中英文资料外文翻译文献专业英文资料Boiler energy savingIndustrial boiler energy saving technology related to many, what is the most important increase industrial furnace thermal utilization ratio of pot namely, increasing the thermal efficiency of the industrial boiler. This section from burning, transportation line maintenance, new technology and new equipment and the application of the industrial boiler auxiliary equipment of energy saving, pot boiler water processing, etc and the industrial boiler room way of energy saving is discussed in this paper.1. The furnace of industrial boiler furnace arch arch is very important. The role is to make arch furnace chamber of the mixture of gases and radiation and hot gas organization flow, to make the fuel and ignition and combustion when. Sua and at present industrial boiler with the actual YongQiLiang rated load are often not with horse, the use of coal changes greatly, and often have large design coal poor vision, so in actual use, often to furnace necessary improvement in arch coal need to be comfortable.For transformation of the former furnace arch situation, the existing problem is: for the use of coal and coal than design poor miscellaneous, boiler flue gas temperature appear the chamber exports low (about 700℃), more than 200 ℃ design low. The new coal fire late, often appear fire bed broken fire, fire from about 0.6 ~ coal disc 1 cm, furnace combustion is not strong, ash high carbon content. According to the problems furnace arch structure, from improving the ignition of fuel conditions and raise the temperature of boiler furnace to reform.After improvement furnace arch, in actual shipped in from the observed, the transformation effect is good, people away from coal furnace fuel after disc 0.3 MRP on fire, fire bed combustion intense, flame full of degree good, strong rotation. Due to the lower arch before, after extended arch, the arch of the throat and mouth shape between into space from the original 2 cm or so down to 1 cm. To strengthen the disturbance of the air mixed, to form the airflow, strengthen the furnace combustion, improve the efficiency of the district and the whole arch before furnace temperature, make its reach to 1400℃ above, improved the ignition of fuel conditions. Coal in the ignition, of furnace temperature rise, make the carbon content and ash significantly less. The flue gas mixture and strengthen the hydrocyclone separation of flue gas carbon particles needed to fall in the fire bed and new fuel layer further burns out.2. The reasonable air supply and regulationIn the chain furnace, the furnace, the furnace of reciprocating vibration, according to the different characteristics of the combustion process, reasonable air supply, to promote the furnace combustion is very important. As in the chain furnace, along with fuel keep movement, which in turn happen on fire, burning, and burn the stage. Burning along the length direction is the stoker stages, zoning, so along the length direction along the air quantity is also different. The preheating zone along the head and tail burn stage, air requirements small; The burning along the middle stage, air requirements. According to this13characteristic, must use block supply air, to meet the needs of the burning. The current domestic production of the boiler although all are to consider this one characteristic, with the wind in subsection room, and equipped with air inlet adjustment. But according to the survey.3.The secondary airSecond wind to strengthen the air combustion is very effective. Second wind have the following function:(1) strengthen the furnace of air disturbance and mixed, make the furnace of oxygen and flammable gas mixture evenly, make chemical don't fully burning loss and the chamber excess air coefficient reducing. (2) secondary air in furnace flue gas vortex formed, on the one hand, extended the suspension fine coal grain in the chamber of a stroke, increase the fine particles suspended furnace in the residence time of, make it have a full time to burn, make not complete combustion heat loss; Another result of air separation of spiral effect, make coal dust grain and the grain re-blows rejection within, and reduce the small fly ash escape from the quantity, the mechanical incomplete combustion heat loss.英译汉14锅炉的节能工业锅炉的节能技术涉及多方面 , 最主要是提高工业锅炉的热能利用率 , 即提高工业锅炉的热效率。
热风炉控制系统中英文对照外文翻译文献

热风炉控制系统中英文对照外文翻译文献(文档含英文原文和中文翻译)译文:基于西门子PCS7的热风炉控制系统的设计本文介绍的方法利用西门子过程控制系统PCS7 V6.0控制加热炉。
描述了两者的配置控制系统软件和硬件,功能通过该系统,随着困难解决方案。
加热炉控制系统的配置双CPU冗余。
采用工业以太网,欧洲流行的PROFIBUS DP现场总线和分布式I / O减反射膜结构。
它采用ET200M I/O站的冗余。
带PROFIBUS-DP通信接口和节点具有双控制器的通信协议(CPU)。
一、介绍在生产过程中的热轧带钢,要求对来料板坯温度比较高;一般来说,应当是1 350℃左右。
的加热炉的加热程序的设备,如能满足连续可靠的要求生产只有在控制的温度和输出量有很好的协调。
加热炉采用可移动的步进梁移动冷板坯的出口侧的输入时,炉侧;钢板坯是移动的,它将被加热的喷嘴喷射炉气联合焦炭炉。
当板坯入炉炉体的末端,它首先会被加热到850℃左右在预热段,然后约1300℃在加热段;最后将进入热浸泡部分使板坯加热均匀滚动。
上述控制过程通常通过不断的PID (比例,积分和差分)。
S分别对各控制截面的顶部或侧壁分别收集实际温度在每节该炉和再采样值将被发送到PLC(可编程逻辑控制器)实现连续比例,积分和微分(PID控制)通过测量值之间的差异空气和煤气流量设定值;然后开度每段的喷枪将调整控制气体的流量,温度控制,然而,因为它不是关于气体的燃烧清楚,如果这采用的方法是,热利用效率介质的极低、能耗非常大。
在这里,一种改进的双交叉振幅限制全自动燃烧控制进行了介绍和其基本原理是进行控制燃烧的上部和下部各节在正常工作时间;如有必要,温度将上部调整信号可被视为套双交叉限幅控制和在下部前温度检测值可用于炉状态监测。
这一原则主从控制模式可以更好地协调在上燃烧和供热平衡段和下部的燃烧上、下段均匀;同时,它认为天然气的燃烧,起到了很好的作用节能。
在这个项目中,PCS7 V6.0由西门子将用于实现上述控制功能。
- 1、下载文档前请自行甄别文档内容的完整性,平台不提供额外的编辑、内容补充、找答案等附加服务。
- 2、"仅部分预览"的文档,不可在线预览部分如存在完整性等问题,可反馈申请退款(可完整预览的文档不适用该条件!)。
- 3、如文档侵犯您的权益,请联系客服反馈,我们会尽快为您处理(人工客服工作时间:9:00-18:30)。
中英文资料对照外文翻译文献锅炉系统1 冷凝器1.1 简介欧堡生产的冷凝器是用直管和一个外部密封浮头组成的管壳式冷凝器。
这种冷凝器主要用作废气锅炉,蒸汽加热或洗舱海水加热器的转储冷凝器/冷却器排水。
并取得权威船级社批准。
温度计,排水阀,空气阀,压力表的安装设计为½“BSP内螺纹安装。
这些组件可能是指定的。
而蒸汽或水的控制设备是可选的。
1.2 安装空间要求安装时必须有足够的空间供作清洗,检查或更换管的插入与撤出。
冷凝器必须安置在水平并稳定的表面。
1.3 存储如果冷凝器在安装前要闲置一段时间,应存放在干燥的储藏室里。
如果储藏室潮湿,冷凝器必须放在装有硅胶的包装袋子里。
为了避免破坏,建议冷凝器放在原包装中。
冷凝器已经在交付前做过液压试验。
试验中所用测试媒质含有一定的数额抗腐蚀保护物质。
当冷凝器需闲置的时间较长,建议使用指定产品作为防腐蚀物质1.4 安装冷凝器设计为垂直或水平安装。
在水平安装的情况下,蒸汽喷嘴必须朝上,而冷凝水出口喷嘴朝下。
如果是垂直安装冷凝器,蒸汽入口和海水出口端必须朝上。
排水和空气排放阀必须安装在冷凝器在最低和最高点的中间线的位置。
任何选择性的控制设备必须根据具体指示安装。
步骤A:将冷凝器安装在水平平面上。
步骤B:钻基础固定螺栓孔。
步骤C:将螺栓放入孔中并拧紧。
连接冷凝器步骤D:移除所有的塞子和盲板,然后再连接冷凝器。
步骤E:在连接中确保没有杂质进入。
步骤F:管道连接起来,确保从管道和冷凝器之间没有强制力的产生。
1.5 调试启动前要确保所有连接都牢固地拧紧是很重要的。
同样重要的是,冷凝器和连接管道空气要彻底排出。
步骤A:如果装有安全阀,必须加以调整到最大设计压力或较低。
步骤B:法兰螺栓要拧紧。
拧紧法兰螺栓时始终使用扭矩扳手。
步骤C:运行一小时,停止冷凝器,并重新拧紧所有螺栓。
步骤D:启动阶段,冷凝器的两边都要排出空气,必须认真仔细的检查回路的泄漏。
1.6 性能冷凝器性能须附和传热计算表规定的要求。
,保持指定的蒸汽压力特别重要,因为压力降低可能导致进口速度过大,将会使其产生噪音并损害冷凝器,而较低的压力下会降低热性能。
通常,有效评估冷凝器性能的方法是通过监测评估冷凝水出口温度或海水出口温度。
如果冷凝水温度过高或海水出口温度过低,要么是冷凝器需要清洗或操作参数不正确。
需要检查其工作条件,并采取适当的纠正行动,以使性能恢复所要求的水平。
1.7 在关闭期间的保护在关闭期间发生的腐蚀,主要是由于氧气的存在。
如果存在非蒸馏水,如碱性或海水在冷凝器中,就很容易发生腐蚀。
然而,即使在完全放空的情况下,冷凝器接触到残留的冷凝水仍然会造成腐蚀。
因此,当停止工作时,应当通过使用淡水冲洗海水端,并仔细在两端泄放以保护冷凝器,如果冷凝器需在一个较长时期的停止工作,尤其是在寒冷的冬季。
必须小心清空。
打开空气阀口并检查堵塞情况。
1.8 维护和清洁冷凝器应定期清理,每十二个月或当没有其他原因的情况下而输出下降的时候,应将内部的管子移出清洁。
步骤A:检查是否有水在收集箱或管子中。
步骤B:将内部管束取出后,用有压力的液体进行外部清洗步骤3:将管束的上盖移除后,使用酸性的液体从内部进行清洁,表面的杂质可以用软质尼龙刷去除。
但很重要的一点是进行机械清除时不要破坏管子的表面。
步骤D:安全阀必须每年都要检查其设置点是否正确。
1.9 拆卸和重装管束当需要将管束从冷凝器中取出时,必须拆除海水连接头,拆下蒸汽进口处的水箱,松下其他水箱的连接螺栓需要利用水箱中的顶升螺栓将水箱和管架连接用的紧固O形圈拉开。
在拉出管束前,应使用带状材料缠绕保护管架箱浮动端的表面。
由于管束和包装表面容易损伤,一定要轻拿轻放。
检查管束,水箱和外壳是否遭到破坏或过度磨损,进行必要的维修和清洗后,重新组装冷凝器。
在水箱浮动端的环槽中安装新的O形圈,并涂耐热硅润滑脂,使安装更容易,并可以增加垫材的使用寿命。
然后将管束装入管架中,在插入管束前,管架始终要用包装材料保护。
使抗冲击板块正对蒸汽喷嘴的冲击是十分重要的,不然可能会因为管子被过度侵蚀而发生故障。
安装末端水箱。
取下管架浮动端的包装带,轻轻地将浮动端水箱滑上。
这是极为重要的板块正面临冲击的蒸汽喷嘴,否则可能会失败,使用法兰螺栓确保无偏斜地固定水箱后,装上管子并锁紧螺丝。
垫片表面要清洁并防止损坏,每拆下一个接头都要更换新的垫片。
应当尽量使用原装垫片和垫圈,并保证安装牢固紧密。
需始终使用扭力扳手上紧法兰螺栓。
运行冷凝器一个小时,停止,然后上紧法兰螺栓。
对接头的紧密性进行压力实验。
在运行期间,对冷凝器进行小心的泄放,并对循环回路进行检查是否漏泄。
1.10 备件订货时请注明零件的冷凝器(在铭牌上)的序列号。
需要备件的进一步信息,请联系欧堡工业。
2 化学定量泵2.1 简介化学定量泵是由微处理器控制的电磁定量泵。
该泵能够准确显示液体化学品加药压力管道系统中的流量,并能进行容器的打开和关闭。
化学定量泵的主要组成部分包括操作面板,电源端,液源腔该泵的工作原理是液端定量膜由微处理器控制作动的电磁铁驱动,形成脉冲作用在化学液体上,这就引起吸口端,液体腔和排出端之间产生压力差。
这个压力差将引起吸口和出口的自动阀开启或关闭,从而供应化学液体。
泵的容量(供给速度)取决于行程长度和行程率。
冲程长度使用行程长度调节旋钮在0%和100%间调节。
最佳剂量是设置在30%和100%行程的长度。
行程率10%和100%之间使用的多功能开关进行步进调节,每级为10%。
但在外部模式中,行程率是由电信号控制的。
2.2 安全在安装,调试,运行,维护和修理期间必须始终应遵守遵循以下安全原则请注意,泵的设计不适合用于:(1)气体化学物质或悬浮固体和容易爆炸的危险场所。
(2)在紧急情况下的泵应立即关闭。
断开电源的电源线。
(3)在任何时候都应该能够方便地进行操作和管理。
附近不能有障碍(4)水泵和外围设备只有合格和有授权的维修人员才能对其进行维修和管理。
(5)当做有关泵的工作时,首先要断开电源(6)在做有关泵的工作前,必须泄放出口管路上的压力液体,放空液腔中的液体,并冲洗干净。
(7)务必阅读化学品安全数据。
(8)处理危险或未知的化学物质,务必穿上防护服时(9)如果排出管被封锁,切勿让定量泵运转,因为这可能会导致排出管道破裂。
2.3 安装2.3.1 一般安装化学定量泵通常预装在化工罐上。
因此该泵安装或更换的地方必须遵守以下安装注意事项:(1)化学定量泵必须位于一个环境温度在-10 C至+45之间,在非冷凝的情况下相对湿度不超过92%的环境中(2)泵的泵脚必须牢固地安装在牢固的基准座上,泵运行时不能震动(3)启动和运行时不得超过其最大允许压力。
这种泵的最大吸高为2 mmWC,最大工作压力为16巴。
例如由于化学物质供应系统的位置,导致运行压力超标的情况下,在出口端必须安装一个安全阀,多余的液体回到吸口(4)吸入和排出阀必须安装在垂直位置。
(5)其管子必须具备这样的要求,即如果需要,允许将泵和液腔拆开,在安装时不能产生应力和弯曲,所以只有原装的产品才能达到这种尺寸要求。
(6)吸入管应呈上升趋势并尽可能短以防止气泡的形成。
(7)由于在底部有化学品的沉淀和杂质,底阀的位置要高于它们的位置。
(8)连接到供应系统的出口管的止回阀必须上紧。
2.3.2 电气安装该泵是和主电源的连接通过主电源线。
如果泵连接到电源时与感应元件并联,必须对他们进行电器隔离,防止开关断开时产生的冲击造成损害。
2.4 操作这个化学定量泵的操作面板配有支持泵的设置和运作操作开关,接线端子,和指示器。
该泵可通过手动操作控制或外部控制。
如果泵仅需要手动操作模式时将不会提供可选的终端接到“外部控制”。
当泵需要是通过“外部控制”和/或“浮动开关”控制时,必须提供可选的终端外部控制。
“在化学品罐中装有测量液位的浮动开关,它能够提供液位信号到泵。
由于液位的变化需要安装两个浮动开关到接线端子。
同时泵也需要进一步安装故障监测继电器用于低水位报警。
以下为泵操作指令的完整描述。
如果化学计量泵包括零件或功能,不是用于定量供应系统,这些指令可以忽略。
2.5 泵的基本信息2.5.1 行程长度调节旋钮行程长度可以在0%和100通过调节冲程长度调节旋钮进行连续性的调节。
在技术上只有再现性在调整范围30%至100%可行。
2.5.2 多功能开关多功能开关用来选择操作模式和设置行程率。
下面的操作模式是供多功能开关选择的模式:停止。
外部。
手动(设置在10%的行程步进率)。
测试(自吸功能)。
(1)停止“停止”功能使泵电源未断开也可以停用。
(2)外部外部操作模式允许通过触点或者半导体的外部模式操纵设备单独调节其行程“暂停”功能,可以通过外部终端远程操作使泵停止。
(3)手动操作手动操作模式通过多功能开关对行程率进行10%的步进调整。
(4)测试“测试”功能检查泵的自吸的功能。
开关设置在测试位时,多功能开关“测试”是自动的。
2.5.3 LED指示灯运行和错误状态通过操作面板上的三个指示灯显示:绿色LED指示灯,操作显示:此LED点亮时排出行程被激活。
黄色的LED指示灯,报警指示灯:如果设备装有浮动开关,LED灯亮时,表明液面低于第一触发液面。
红色LED指示灯,故障指示灯:如果装有浮子开关,指示灯亮起来时说明液位测量发生故障。
它闪烁时表示未定义的运行状态2.6 保养.为确保化学定量泵工作安全和性能可靠,必须进行定期保养。
正常保养间隔为三个月。
这是根据其运行时间大约为30%时制定的。
但在使用比较频繁的情况下,保养周期应缩短。
进行以下维护工作:检查泵短期运行时进给率是否正确。
检查排气孔处的化学品是否渗流。
检查排出管与液源端连接是否牢固。
检查排出和吸入阀是否牢固地固定。
检查液源端尤其是排气孔处的水密性。
检查膜片是否损坏检查液源端的固定螺丝是否上紧。
检查泄放阀是否牢牢地固定到位。
检查泄放功能是否正常运行。
检查电气接线有没有破损。
Boiler System1 Condenser1.1 General descriptionAalborg Industries' MD condensers are of the shell and tube type with straight tubes and an externally sealed floating head. The MD condenser is primarily used as dump condenser/drain cooler for exhaust gas boilers, or as steam heated tank cleaning heater for sea water. The condensers are approved by major marine classification societies.Thermometers, drain valve, air valve, and pressure gauge can be fitted on designated ½" BSP threads. These components may be supplied on request. Control equipment for either steam or water is optional.1.2 Installation space requirementsWhen mounting the condenser sufficient space must be allowed for withdrawal of the tube insert for cleaning, inspection, or replacement purposes. The condenser must be placed on a level and stable surface.1.3 StorageIf the condenser must be stored prior to the installation, it should be in a dry storage room. If the storage room is damp, the condenser must be wrapped together with bags of silica gel. To avoid damages it is recommend that the condenser is stored in the original packing.The condenser has been hydrostatically tested before delivery. The used test medium contains a certain amount of corrosion protection .When the condenser is kept in storage for an extended period of time, it is recommend to use Castrol Rustilo Aqua 2 as protection against corrosion.1.4 installationThe condenser is designed for either vertical or horizontal installation. In case of horizontal installation the steam inlet nozzle must face upwards, and the condensate outlet nozzle face downwards.If the condenser is mounted vertically, the steam inlet and sea water outlet end must face upwards. Drain and air vent valves must be mounted according to the orientations of the condenser e.g. lowest and highest ½" thread position on the shell.Any optional control equipment must always be installed according to specific instructions.STEP A:Place the condenser on a level and plane surface.STEP B:Drill the holes for the foundation bolts.STEP C:Place the bolts into the holes and tighten up.Connecting the condenserSTEP D:Remove all plugs and blind flanges before connecting the condenser.STEP E:Ensure that no impurities are present in the connectionSTEP F:Set up the pipe connections and make sure that no forces from the piping are transferred to the condenser1.5 CommissioningBefore start-up it is important to make sure that all connections are securely tightened. It is equally important that the condenser and the connecting pipes are thoroughly air-vented.STEP A:If a safety valve is fitted it must be adjusted to maximum design pressure or lower.STEP B:Tighten all main flange bolts . Always use a torque wrench when tightening the flange bolts.STEP C:Operate the condenser for one hour, stop, and retighten all bolts .STEP D:Both sides of the condenser must be carefully vented and the circuits carefully inspected for leakage during the whole start-up period.1.6 PerformanceThe performance of the condenser is subject to the conditions specified in the heat transfer calculation sheet. It is particularly important that the steam pressure is maintained as specified, since lowering the pressure may cause excessive inlet velocity which may be both noisy and harmful to the condenser, as well as the lower pressure will decrease the thermal performance. Usually it will be sufficient to evaluate the performance of the condenser by monitoring the outlet temperature of either the condensate or the water outlet temperature . If the condensate temperature is too high or the sea water outlet temperature is too low, either the condenser needs cleaning or the operating parameters are incorrect. Check the operating conditions and take appropriate corrective action to bring the performance back to the required level.1.7 Conservation during shut down periodsCorrosion occurrences in shut down periods are mainly caused by oxygen. The corrosion occurs if non-distilled, alkaline or sea water remains in the condenser. However, even when fully emptied, the condenser is exposed to corrosion caused by water residues or condensation. Hence, when out of service, it should be protected against corrosion by flushing with fresh water on the sea water side and carefully draining of both sides.If the condenser is out of service for an extended period of time – in particular during winter seasons with frost – it must be carefully emptied. Open the air vent valve and check for clogging.1.8 Maintenance and cleaningThe condenser should be cleaned regularly by removing the tube insert everytwelve months or at any time there is a decrease in output not related to other causes.STEP A:Check if any deposits have collected in the water boxes or in/on the tubes.STEP B:Cleaning of the tube bundle from the outside is carried out after removing the tube insert using a liquid jetSTEP C:Cleaning of the tube bundle from the inside is carried out after removing the cover by flushing the tubes with e.g. citric acid. To remove scales or impurities a soft nylon brush can be used, but it is very important not to damage the tube surface during mechanical cleaning.STEP D:Once every year the safety valve must be checked for correct set point.1.9 Dismantling and reassembling of the tube bundleWhen the tube bundle must be pulled from the condenser, the sea water connections must be dismantled and the water boxes at the steam inlet removed. Loosen the bolts for the other water box and use the jacking bolts in the water box to pull the water box off the tight O-ring fitting with the tube sheet. Protect the floating end tube sheet packing surface with a wrap of tape before pulling the bundle. Handle the bundle and water boxes with care, since both tubes and packing surfaces can be damaged by impact.Inspect the tube bundle, water boxes and the shell for damage and excessive wear, make necessary repairs and cleaning and reassemble the condenser. Fit new O-rings to the floating end water box gasket grooves and grease with heat resistant silicone grease to ease the mounting and increase the gasket life time. Mount the bundle in the shell and remember to protect the packing surface of the tube sheet before inserting the bundle. It is extremely important that the impingement plate is facing the steam inlet nozzle, otherwise the tubes may fail prematurely due to erosion. Mount the fixed end water box. Remove the protective tape from the floating end tube sheet and gently slide the floating head water box on. Use the flange bolts to ensure a proper fitting without yawing of the water box. Set up the piping again and tighten all bolts.Gasket surfaces must be cleaned and protected against damage. New gaskets should be fitted every time a connection has been dismantled. To ensure a tight fit only original spares should be used when replacing the gaskets and O-rings.Always use a torque wrench when tightening the flange bolts.Operate the condenser for one hour, stop, and retighten all boltsA pressure test should be carried out to prove tight joints.Both sides of the condenser must be carefully vented and the circuits carefully inspected for leakage during the whole start-up period.1.10 Spare partsWhen ordering spare parts please state the serial number of the condenser (located on the nameplate). For spare parts and further information please contact Aalborg Industries.2 Chemical dosing pump2.1 GeneralThe chemical dosing pump is a microprocessor controlled solenoid metering pump. The pump offers highly accurate reproducible metering in the dosing of liquid chemicals in pressurised pipe systems, and into open and closed containers. The main components of the chemical dosing pump are the operating panel, power end, and liquid end..The working principle of the pump is that chemical feed occurs as a result of pulsed deflections of the dosing diaphragm within the liquid end, which causes pressure differentiation between the suction side, liquid end cavity, and discharge side. The pressure differentiation causes the suction and discharge self-acting valves to open and close, resulting in chemical feed. The dosing diaphragm is driven by an electromagnet, which is stimulated and controlled by a microprocessor.The pump capacity (feed rate) is determined by the stroke length and stroke rate. The stroke length is set between 0% and 100% using the stroke length adjustment knob. Optimum dosing reproducibility is achieved by setting the stroke length between 30% and 100%. The stroke rate adjustable in 10% steps between 0% and 100% using the multifunction switch. However, in "external" operating mode the stroke rate is controlled by electrical signals.2.2 SafetyThe following safety guide lines must always be observed during installation, commissioning, operation, maintenance, and repair:(1)Please note that the pump is not designed for:Use with gaseous chemicals or suspended solids and in explosion-hazardous locations.(2)In emergency cases the pump should be switched off immediately. Disconnect the power cable from the power supply.(3)The pump must be accessible at all times for both operation and servicing. Access must not be obstructed in any way.(4)The pumps and peripherals must be serviced and repaired by qualified and authorised persons only.(5)Before working on a pump always disconnect the mains power.(6)Before working on a pump always de-pressurise the discharge line, empty the liquid end, and rinse out.(7)Always read the chemical safety data.(8)Always wear protective clothing when handling hazardous or unknown chemicals.(9)Never allow the metering pump to operate if the discharge line is blocked, as this can result in a rupture of the discharge line.2.3 Installation2.3.1 general InstallationThe chemical dosing pump is normally pre-mounted a chemical tank. However, in case that the pump must be mounted elsewhere or replaced please observe the following general installation notes(1)The chemical dosing pump must be located in an environment with ambient temperature between -10︒C to +45︒C and a maximum permissible relative humidity of 92% non-condensing.(2)The pump must be mounted with the pump foot resting on a firm horizontal base. Ensure that it is fastened into place firmly, and will not vibrate in operation.(3)The maximum permissible priming and operating pressures must not be exceeded. For this type of pump the maximum priming lift is 2 mmWC and the maximum operating pressure is 16 barg. In case that the operating pressure is exceeded, e.g. due to the position of the chemical feed into the feed system, the discharge side must be provided with a relief valve. The surplus chemicals should be led back to the chemical tank.(4)Suction and discharge valves must be installed in a vertical position.(5)The tubing should be attached in such a way that it allows lateral detachment of the pump and liquid end, if necessary. The tubing must be free from stress and bends when fitted. Only original hoses with the correct dimensions should be used.(6)The suction tubing should be as short as possible and rising in order to prevent air bubbles forming.(7)The foot valve should be installed so that it hangs just above the bottom of the chemical tank. For chemicals with impurities or sedimentation at the bottom, the foot valve should be positioned well above this layer.(8)The check valve, which connects the discharge line to the feed water system, must be tightened properly.2.3.2 Electrical installationThe pump is connected to the mains power supply by using the mains lead. If the pump is connected to the mains in parallel with inductive power consumers (e.g. solenoid valves, motors) it must be electrically isolated. This prevents damage caused by induction and voltage surges when switching off. illustrates the power element of the pump.2.4 operationThe operation panel of the chemical dosing pump is equipped with operation knobs/switches, connection terminals, and indicators, which support the operation and setting of the pump.The pump can be operated through manual control or external control. If the pump is intended only to operate in manual mode it will not be provided with the optional terminal connection "external control" 。