无损检测的概述
公共基础知识无损检测技术基础知识概述
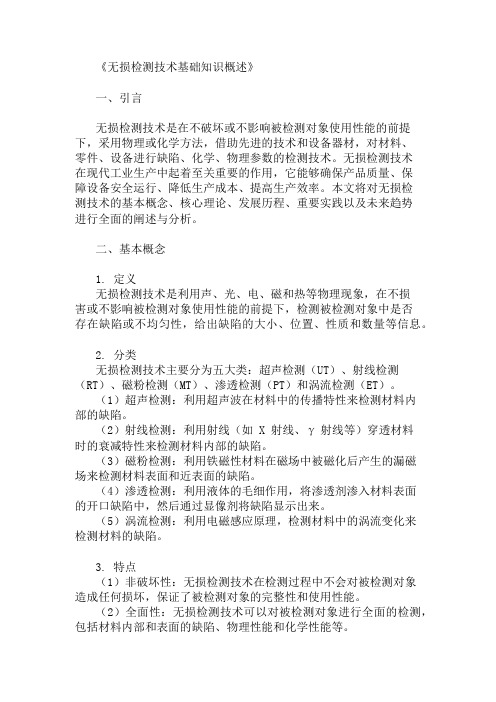
《无损检测技术基础知识概述》一、引言无损检测技术是在不破坏或不影响被检测对象使用性能的前提下,采用物理或化学方法,借助先进的技术和设备器材,对材料、零件、设备进行缺陷、化学、物理参数的检测技术。
无损检测技术在现代工业生产中起着至关重要的作用,它能够确保产品质量、保障设备安全运行、降低生产成本、提高生产效率。
本文将对无损检测技术的基本概念、核心理论、发展历程、重要实践以及未来趋势进行全面的阐述与分析。
二、基本概念1. 定义无损检测技术是利用声、光、电、磁和热等物理现象,在不损害或不影响被检测对象使用性能的前提下,检测被检测对象中是否存在缺陷或不均匀性,给出缺陷的大小、位置、性质和数量等信息。
2. 分类无损检测技术主要分为五大类:超声检测(UT)、射线检测(RT)、磁粉检测(MT)、渗透检测(PT)和涡流检测(ET)。
(1)超声检测:利用超声波在材料中的传播特性来检测材料内部的缺陷。
(2)射线检测:利用射线(如 X 射线、γ射线等)穿透材料时的衰减特性来检测材料内部的缺陷。
(3)磁粉检测:利用铁磁性材料在磁场中被磁化后产生的漏磁场来检测材料表面和近表面的缺陷。
(4)渗透检测:利用液体的毛细作用,将渗透剂渗入材料表面的开口缺陷中,然后通过显像剂将缺陷显示出来。
(5)涡流检测:利用电磁感应原理,检测材料中的涡流变化来检测材料的缺陷。
3. 特点(1)非破坏性:无损检测技术在检测过程中不会对被检测对象造成任何损坏,保证了被检测对象的完整性和使用性能。
(2)全面性:无损检测技术可以对被检测对象进行全面的检测,包括材料内部和表面的缺陷、物理性能和化学性能等。
(3)可靠性:无损检测技术采用先进的技术和设备器材,检测结果准确可靠,可以为产品质量和设备安全运行提供有力的保障。
(4)高效性:无损检测技术检测速度快、效率高,可以大大提高生产效率和降低生产成本。
三、核心理论1. 超声检测理论超声检测是利用超声波在材料中的传播特性来检测材料内部的缺陷。
无损检测概论

射线检测 (Radiography Testing )简称RT
超声波检测(Ultrasonic Testing)简称UT 磁粉检测(Magnetic Testing)简称MT
渗透检测(Penetrant Testing)简称)简称PT
四、无损检测方法的选择
1.经济方面的考虑
首先要考虑的是进行必要的资本投入,并应详细评估 资金的回收情况。对于一个好的企业,在检测方法和 可靠性方面的投资,会收到相当的经济效益。
一般:
射线检测对体积型缺陷比较敏感;
超声波检测对面缺陷比较敏感; 磁粉检测只能用于铁磁性材料的检测; 渗透检测则用于表面开口缺陷的检测; 涡流检测对开口或近表面缺陷、磁性和非磁性的 导电材料都具有很好的适用性。
因此,无损检测技术广泛应于各种设备、压力容器、机械零部 件等的检测诊断,受到工业界的普遍重视。
二、无损检测技术的发展阶段
(一)无损检测技术发展的三个阶段
无损检查( Nondestructive Inspection, NDI)、 无损检测(Nondestructive Testing,NDT)、
2. 在役检测 使用无损检测技术对装臵在运行过程中进行监测,或者在检修 期进行检测,能及时发现影响其安全运行的隐患,防止事故。 这对于大型设备,如核反应堆、桥梁建筑、铁路车辆、压力容 器、输送管道、飞机、火箭等,具有重要的意义。 在役检测不仅可以及时发现隐患,更重要的是可以根据所发 现的早期缺陷及其发展程度(如疲劳裂纹的萌生与发展),在 确定其方位、形状、尺寸和性质等的基础上,对装臵能否继续 使用及其安全运行寿命进行评价。
(三)无损检测技术的特点
1.无损检测不会对构件造成任何损伤 无损检测是在不破坏构件的前提下,利用材料物理性质的变 化来判断构件内部和表面是否存在缺陷,不会对材料、工件和 设备造成任何损伤。
无损检测

/ examination、evaluation (美国) A、语言习惯不同; B、含义也略有不同。 个人理解:所有无损检测方法均是利用被检件的不连续性,
郑州华电金源管道有限公司
2、常用方法介绍
• 2.1 射线检测(RT) • 2.1.1原理 • 射线检测是指用X射线或伽玛射线来检测材料和工件、并
以射线照相胶片作为记录介质和显示方法的一种无损检测 方法。射线照相检测是利用X射线和伽玛射线的众多特性 (如感光),通过观察射线照相胶片上的有关X射线或伽 玛射线在被检材料或工件中发生的衰减变化,来判定被检 材料和工件的内部是否存在缺陷,从而在不破坏或不损害 被检材料和工件的情况下,评估其性能的符合性。
程;
• 按现行的规范、标准、技术条件,解释和评定检测结果; • 若被认证机构授权,可受理资格鉴定考试; • 可实施或监督所有 1 级和 II 级人员的工作。
持有 III 级证书人员应:
郑州华电金源管道有限公司
Zhengzhou Huadian-Jinyuan Piping Co,.Ltd.
1.无损检测概述
郑州华电金源管道有限公司
Zhengzhou Huadian-Jinyuan Piping Co,.Ltd.
2、常用方法介绍
• 磁粉能检测近表面缺陷,而渗透智能检测出在表面开口的
缺陷;
• 磁粉需借助电源,而渗透可不受水电限制。
郑州华电金源管道有限公司
Zhengzhou Huadian-Jinyuan Piping Co,.Ltd.
2、常用方法介绍
• 2.6MT、PT对比 • 相同: • 均适用于检测工件表面缺陷; • 均能检出各种性质缺陷; • 操作简单,缺陷显示直观,较容易判断; • 均对环境光线有要求,大于1000Lux; • 不同: • 磁粉只适用铁磁性材料,渗透则不适用于多孔疏松型材料; • 磁粉相对灵敏度较渗透高;
无损检测技术

(5)ES线又称Acm线,是碳在奥氏体中的溶解度曲线。即L→Fe3CⅡ。
(6)GS线又称A3线,
(7)GP线奥氏体向铁素体转变的终了线。
(8)PSK水平线共析线(727℃),又称A1线。
(9)PQ线碳在铁素体中的溶解度曲线。
无损检测相关知识
--钢的分类和命名
无损检测相关知识
--焊接缺陷的种类和产生原因
1.外观缺陷
(1)咬边:咬边是指沿着焊趾,在母材部分形成的凹陷或沟槽.
产生咬边的主要原因是电弧热量太
高,即电流太大,运条速度太小。焊
条与工件间角度不正确,摆动不合
理,电弧过长,焊接次序不合理等也
会造成咬边.
(2)焊瘤: 焊缝中的液态金属流到加热不足未熔化的母材上或从焊缝
性。
无损检测相关知识
--铁碳合金基本组织
铁素体: 碳在α-Fe中形成的间隙固溶体称为铁素体( α-Fe 体心立方
晶格),用符号F表示。碳在α-Fe中的溶解度很低,因此,铁
素体的机械性能与纯铁相近,其强度、硬度较低,但具有良
好的塑性、韧性。
奥氏体:碳在γ-Fe中形成的间隙固溶体称为奥氏体( γ-Fe 面心立方晶
b.弹簧钢
c.轴承钢
(3) 工具钢:a.碳素工具钢;b.合金工具钢;c.高速工具钢。
(4) 特殊性能钢:a.不锈耐酸钢;b.耐热钢:包括抗氧化钢、热强钢、气阀钢;c.电热合金
钢;d.耐磨钢;e.低温用钢;f.电工用钢。
(5) 专业用钢——如桥梁用钢、船舶用钢、锅炉用钢、压力容器用钢、农机用钢等。
声发射检测(AE)等。
无损检测概述
无损检测核准规则项目代码
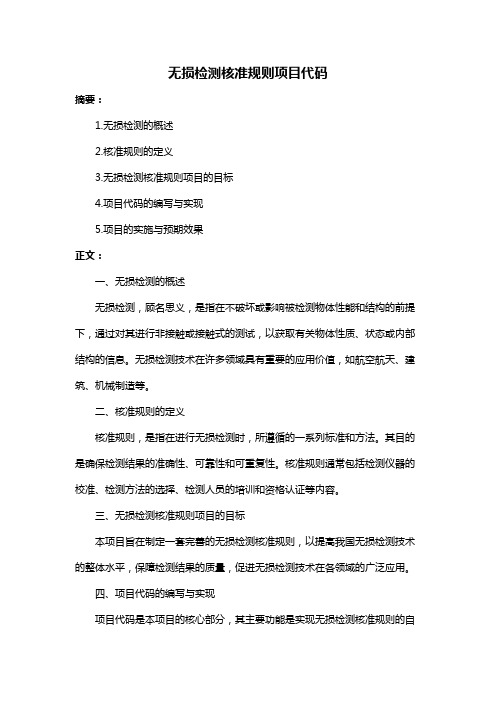
无损检测核准规则项目代码摘要:1.无损检测的概述2.核准规则的定义3.无损检测核准规则项目的目标4.项目代码的编写与实现5.项目的实施与预期效果正文:一、无损检测的概述无损检测,顾名思义,是指在不破坏或影响被检测物体性能和结构的前提下,通过对其进行非接触或接触式的测试,以获取有关物体性质、状态或内部结构的信息。
无损检测技术在许多领域具有重要的应用价值,如航空航天、建筑、机械制造等。
二、核准规则的定义核准规则,是指在进行无损检测时,所遵循的一系列标准和方法。
其目的是确保检测结果的准确性、可靠性和可重复性。
核准规则通常包括检测仪器的校准、检测方法的选择、检测人员的培训和资格认证等内容。
三、无损检测核准规则项目的目标本项目旨在制定一套完善的无损检测核准规则,以提高我国无损检测技术的整体水平,保障检测结果的质量,促进无损检测技术在各领域的广泛应用。
四、项目代码的编写与实现项目代码是本项目的核心部分,其主要功能是实现无损检测核准规则的自动化处理。
项目代码分为以下几个模块:1.数据采集模块:负责从各种无损检测设备中获取检测数据,并将其转化为统一的数据格式。
2.数据处理模块:对采集到的数据进行预处理、分析和存储,以满足后续核准规则的执行需求。
3.规则引擎模块:根据预先设定的核准规则,对数据进行匹配和判断,生成检测结果。
4.结果输出模块:将检测结果以可视化的形式展示给用户,以便用户进行分析和判断。
五、项目的实施与预期效果本项目将在实际的无损检测场景中进行实施,以验证其有效性和可行性。
预期项目实施后,将带来以下效果:1.提高无损检测的准确性和可靠性,降低误检率和漏检率。
2.提高检测效率,降低检测成本。
《无损检测》课件

电力工业
无损检测在电力工业中用于发 电机组、变压器等设备的检测
。
02
无损检测技术分类
超声检测
总结词
通过高频声波显示材料内部结构的无损检测方法。
详细描述
超声检测利用高频声波在材料中传播的特性,通过接收和分析反射回来的声波 信号,可以检测出材料内部的缺陷、裂纹、气孔等问题,广泛应用于金属、非 金属、复合材料等多种材料的检测。
案例二:压力容器的射线检测
总结词
射线检测是一种常用的无损检测方法,对于压力容器 的内部结构和材料特性进行全面检测,以确保其安全 可靠。
详细描述
压力容器是一种广泛应用于石油、化工、制药等领域的 设备,其安全性至关重要。由于压力容器的使用环境和 内部介质具有高温、高压、腐蚀等特点,容易产生裂纹 、气孔、夹渣等缺陷。为了确保压力容器的安全运行, 必须对其进行无损检测。射线检测是一种常用的无损检 测方法,通过X射线或γ射线的穿透和成像技术,可以 清晰地显示出容器内部的缺陷和结构,为压力容器的安 全评估和维修提供有力支持。
确定需要检测的物品或部位, 了解其材料、结构和使用情况
。
收集相关信息
收集有关检测物品的历史、制 造工艺、使用环境等方面的信 息。
选择合适的检测方法
根据目标和信息,选择最合适 的无损检测方法。
准备检测设备和器材
确保所需的仪器、探头、试剂 等齐全且性能良好。
检测操作
设置检测参数
根据实际情况,调整仪器参数,确保准确性 和可靠性。
案例三:高铁轮对的磁粉检测
总结词
高铁轮对是高铁列车运行的关键部件,其质量和安全 性至关重要。磁粉检测是一种有效的无损检测方法, 可以对轮对的表面和近表面缺陷进行全面检测。
无损检测概述

5、渗透检测(PT)
6、涡流检测(ET)
7、声发射 AE
二、非常规无损检测方法
关于无损检测培训与无损检测人员资质认证 为什么要做无损检测培训
国内无损检测培训情况
中国培训体系
通过国内的相关学会获得NDT对应资质
国际无损检测培训情况
国际上常见的无损检测培训体系
3、超声波检测(UT)
1、超声波检测的定义:通过超声波与试件相互作用,就反射、透 无损检测设备
射和散射的波进行研究,对试件进行宏观缺陷检测、几何特性测量、组织结构和力学性能变化的检测和表征,并进而对其特定应用性进行评价的技术。 2、超声波工作的原理:主要是基于超声波在试件中的传播特性。 a.声源产生超声波,采用一定的方式使超声波进入试件; b.超声波在试件中传播并与试件材料以及其中的缺陷相互作用,使其传播方向或特征被改变; c.改变后的超声波通过检测设备被接收,并可对其进行处理和分析; d.根据接收的超声波的特征,评估试件本身及其内部是否存在缺陷及缺陷的特性。 3、超声波检测的优点: a.适用于金属、非金属和复合材料等多种制件的无损检测; b.穿透能力强,可对较大厚度范围内的试件内部缺陷进行检测。如对金属材料,可检测厚度为1~2mm的薄壁管材和板材,也可检测几米长的钢锻件; c.缺陷定位较准确; d.对面积型缺陷的检出率较高; e.灵敏度高,可检测试件内部尺寸很小的缺陷; f.检测成本低、速度快,设备轻便,对人体及环境无害,现场使用较方便。 4、超声波检测的局限性: a.对试件中的缺陷进行精确的定性、定量仍须作深入研究; b.对具有复杂形状或不规则外形的试件进行超声检测有困难; c.缺陷的位置、取向和形状对检测结果有一定影响; d.材质、晶粒度等对检测有较大影响; e.以常用的手工A型脉冲反射法检测时结果显示不直观,且检测结果无直接见证记录。 5、超声检测的适用范围: a.从检测对象的材料来说,可用于金属、非金属和复合材料; b.从检测对象的制造工艺来说,可用于锻件、铸件、焊接件、胶结件等; c.从检测对象的形状来说,可用于板材、棒材、管材等; d.从检测对象的尺寸来说,厚度可小至1mm,也可大至几米; e.从缺陷部位来说,既可以是表面缺陷,也可以是内部缺陷。
2023年无损检测考规

2023年无损检测考规摘要:一、前言二、无损检测概述三、2023年无损检测考规变化1.考试科目与内容调整2.考试形式与时间变化3.考试合格标准与证书颁发四、应对策略与建议1.考生备考注意事项2.培训机构教学调整五、总结正文:一、前言随着我国工程技术水平的不断提高,无损检测技术在各个领域的应用越来越广泛。
为了保证无损检测人才的质量,我国对无损检测从业人员的考核标准也在不断完善。
本文将为您介绍2023年无损检测考规的相关内容。
二、无损检测概述无损检测(Non-Destructive Testing,简称NDT)是指在不破坏或不影响被检测对象使用性能的前提下,利用各种物理现象或物理特性对材料、构件或设备进行缺陷、性质、状态等检查和评价的方法。
无损检测技术包括超声波、射线、磁粉、渗透等多种方法,广泛应用于航空、航天、石油、化工、电力、铁路等行业。
三、2023年无损检测考规变化1.考试科目与内容调整为了适应无损检测技术的发展和实际应用需求,2023年无损检测考试科目进行了调整。
例如,将新增某些新兴检测方法,如激光超声波、声发射等;同时,对传统检测方法的内容进行优化和更新。
2.考试形式与时间变化2023年无损检测考试将采用计算机辅助考试(CBT)形式,取代传统的纸质试卷考试。
考试时间也将相应缩短,以提高考试效率。
3.考试合格标准与证书颁发2023年无损检测考试合格标准将更加严格,以提高行业整体素质。
考试合格后,考生将获得由中国无损检测学会或其他指定机构颁发的无损检测专业技能证书。
四、应对策略与建议1.考生备考注意事项针对考试科目的调整,考生应关注最新的考试大纲,了解新增内容;针对考试形式的改变,考生需熟悉计算机辅助考试的操作流程,提前做好心理准备。
2.培训机构教学调整无损检测培训机构应关注考规的变化,及时更新教学内容,调整教学计划,以提高培训质量。
五、总结2023年无损检测考规的变化对考生和培训机构提出了新的要求。
- 1、下载文档前请自行甄别文档内容的完整性,平台不提供额外的编辑、内容补充、找答案等附加服务。
- 2、"仅部分预览"的文档,不可在线预览部分如存在完整性等问题,可反馈申请退款(可完整预览的文档不适用该条件!)。
- 3、如文档侵犯您的权益,请联系客服反馈,我们会尽快为您处理(人工客服工作时间:9:00-18:30)。
第一章无损检测概述1.1无损检测目的1.2无损检测范围1.3常用的无损检测办法1.3.1射线检测(RT)1.3.2渗透检测(PT)1.3.3磁粉检测(MT)1.3.4超声检测(UT)1.3.5涡流检测(ET)第一章无损检测概述无损检测是指在不损伤和破坏材料、机器和结构物的情况下,对它们的物理性质、机械性能以及内部结构等进行检测的一种方法,是探测其内部或外表的缺陷(伤痕)的现代检验技术。
所以,无损检测技术是提高产品质量,促进技术进步不可缺少的手段。
1.1无损检测的目的:(1)确保工件或设备质量,保证设备安全运行用无损检测来保证产品质量,使之在规定的使用条件下,在预期的使用寿命内,产品的部分或整体都不会发生破损,从而防止设备和人身事故。
这就是无损检测最重要的目的之一。
(2)改进制造工艺.无损检测不仅要把工件中的缺陷检测出来,而且应该帮助其改进制造工艺。
例如,焊接某种压力容器,为了确定焊接规范,可以根据预定的焊接规范制成试样,然后用射线照相检查试样焊缝,随后根据检测结果,修正焊接规范,最后确定能够达到质量要求的焊接规范。
(3)降低制造成本通过无损检测可以达到降低制造成本的目的。
例如,焊接某容器,不是把整个容器焊完后才无损检测,而是在焊接完工前的中间工序先进行无损检测,提前发现不合格的缺陷,及时进行修补。
这样就可以避免在容器焊完后,由于出现缺陷而整个容器不合格,从而节约了原材料和工时费,达到降低制造成本的目的。
1.2无损检测的范围(1)组合件的内部结构或内部组成情况的检查(2)材料、铸锻件和焊中缺陷缝的检查a、质量评定b、寿命评定(3)材料和机器的计量检测通过定量的测定材料和机器的变形量或腐蚀量来确定能不能继续使用。
例如,用超声波测厚仪来测定容器的腐蚀量,通过射线照相来测定原子反应堆用过的燃料棒的变形量、喷气发动机叶片的变形量等。
(4)材质的无损检测无损检测可以用来验证材料品种是否正确,是否按规定进行处理,例如,可采用电磁感应法来进行材质混料的分选和材料热处理状态的判别。
(5)表面处理层的厚度测定确定各种表面层的深度和厚度。
例如,用电磁感应检测法可以测定渗碳淬火层的深度和镀层的厚度。
(6)应变测试1.3常用的无损检测办法1.3.1射线检测(RT)射线检测(探伤)有X射线、γ射线和中子射线等检测方法。
它是利用各种射线源对材料的透射性能及不同材料的射线的衰减程度的不同,使底片感光成黑度不同的图像来观察的。
射线检测用来检测产品的气孔、夹渣、铸造孔洞等立体缺陷。
当裂纹方向与射线平行时就能被检查出来。
1、基本原理利用射线通过物质时的衰减规律,即当射线通过物质时,由于射线与物质的相互作用发生吸收和散射而衰减。
其衰减程度,则根据其被通过部位的材质、厚度和存在缺陷的性质不同而异。
2、应用优点是检测结果可作为档案资料长期保存,检测图像较直观,对缺陷尺寸和性质判断比较容易。
缺点是当裂纹面与射线近于垂直时就很难检查出来,对工件中平面型缺陷(裂纹未熔合等缺陷)也具有一定的检测灵敏度,但与其它常用的无损检测技术相比,对微小裂纹的检测灵敏度较低,并且生产成本高于其它无损检测技术,其检验周期也较其它无损检测技术长,并且射线对人体有害,需要有防护设备。
3、主要方法照相法荧光屏直接观察法1.3.2渗透检测(PT)液体渗透检测是—种检查工件或材料表面缺陷的—种方法,它不受材料磁性的限制,比磁粉探伤的应用范围更加广泛。
应用于各种金属、非金属、磁性、非磁性材料及零件的表面缺陷的检查。
可以说,除表面多孔性材料以外,几乎一切材料的表面开口缺陷都可以应用此方法获得满意的检测结果。
1、基本原理利用黄绿色的荧光渗透液或红色的着色渗透液对窄狭缝隙良好的渗透性,经过渗透清洗、显示处理以后显示放大了的探伤显示痕迹,用目视法来观察,对缺陷的性质和尺寸做出适当的评价。
2、应用优点是应用广泛,原理简明易懂,检查经济,设备简单,显示缺陷直观,并可以同时显示各个不同方向的各类缺陷。
对大型工件和不规则零件的检查以及现场机件的抢修检查,更能显示其特殊的优点。
但渗透探伤对埋藏于表皮层以下的缺陷是无能为力的。
缺点是只能检查开口暴露于表面的缺陷,另外还有操作工序繁杂等。
3、步骤第一步:将被探工件浸涂具有高度渗透能力的渗透液,由于液体的润湿作用和毛细现象,渗透液便渗入工件表面缺陷中第二步:将工件缺陷以外的多余渗透液清洗干净第三步:涂一层亲和吸附力很强的白色显像剂,将渗入裂缝中的渗透液吸出来第四步:在白色涂层上显示出缺陷的形状和位置的鲜明图案,从而达到了无损检疵的目的。
1.3.3磁粉检测(MT)1、基本原理当材料或工件被磁化后,若在工件表面或近表面存在裂纹、冷隔等缺陷,便会在该处形成一漏磁场。
此漏磁场将吸引、聚集检测过程中施加的磁粉,而形成缺陷显示。
因此,磁粉检测首先是对被检工件加外磁场进行磁化.外加磁场的获得一般有两种方法:一种是由可以产生大电流(几百安培至上万安培)的磁力探伤机直接给被检工件通大电流而产生磁场;另一种是把被检工件放在螺旋管线圈产生的磁场中,或是放在电磁铁产生的磁场中使工件磁化。
工件被磁化后,在工件表面上均匀喷洒微颗粒的磁粉(磁粉平均粒度为5~10μm),一般用四氧化三铁或三氧化二铁作为磁粉。
如果被检工件没有缺陷,则磁粉在工件表面均匀分布。
当工件上有缺陷时,由于缺陷(如裂纹、气孔、非金属夹杂物等)内含有空气或非金属,其磁导率远远小于工件的磁导率;由于磁阻的变化,位于工件表面或近表面的缺陷处产生漏磁场,形成一个小磁极,如图3.1所示。
磁粉将被小磁极所吸引,缺陷处由于堆积比较多的磁粉而被显示出来,形成肉眼可以看到的缺陷图像。
为了使磁粉图像便于观察,可以采用与被检工件表面有较大反衬颜色的磁粉。
常用的磁粉有黑色、红色和白色。
为了提高检测灵敏度,还可以采用荧光磁粉,在紫外线照射下使之更容易观察到工件中缺陷的存在。
2、应用用于检测铁磁性材料和工件(包括铁、镍、钻等)表面上或近表面的裂纹以及其它缺陷。
对表面缺陷最灵敏,对表面以下的缺陷随埋藏深度的增加检测灵敏度迅速下降。
采用磁粉检测方法检测磁性材料的表面缺陷,比采用超声波或射线检测的灵敏度高,而且操作简便、结果可靠、价格便宜。
因此它被广泛用于磁性材料表面和近表面缺陷的检测。
对于非磁性材料如有色金属、奥氏体不锈钢、非金属材料等不能采用磁粉检测方法。
但当铁磁性材料上的非磁性涂层厚度不超过50μm时,对磁粉检测的灵敏度影响很小。
3、方法a、湿法磁悬液应采用软管浇淋或浸渍法施加于试件,使整个被检表面被完全覆盖。
采用连续法时,磁化电流应在施加磁悬液之前或从磁悬液中取出之前接通(如果检测采用浸渍法),并保持1/5~1/2 s,直至试件被磁悬液覆盖,磁悬液覆盖膜足以产生良好的磁痕。
采用剩磁法时,试件应通过施加电流至少1/5s的方法来磁化。
此后,切断磁化电流,采用软管浇淋或浸渍法施加磁悬液。
对于浸渍法,试件应仔细地从磁悬液中取出,以免冲掉磁痕。
对于剩磁荧光磁粉检验法,如觉得有必要保证缺陷的磁痕有效,则试件可放在用于制备磁悬液的载液中仔细清洗。
b、干法磁粉应直接喷撒在被检区域,并除去过量的磁粉。
轻轻地振动试件,使其获得较为均匀的磁粉分布。
应注意避免使用过量的磁粉,不然会影响缺陷的有效显示。
对于连续法,磁化电流应恰好在施加磁粉前接通,并应在其后的吹风、轻敲或振动中,保持接通。
对于剩磁法,试件应先磁化,在切断磁化电流之后,再按上述方法施加磁粉。
1.3.4超声检测(UT)1.原理和类型超声波探伤主要是通过测量信号往返于缺陷的渡越时间,来确定缺陷和表面间的距离;测量回波信号的幅度和发射换能器的位置,来确定缺陷的大小和方位。
这就是通常所说的脉冲反射法或A扫描法。
此外,还有B扫描和C扫描等方法。
B扫描可以显示工件内部缺陷的纵截面图形。
C扫描可以显示工件内部缺陷的横剖面图形。
1、应用超声波检测是工业无损检测中应用最为广泛的一种方法。
就无损探伤而言,超声波法适用于各种尺寸的锻件、轧制件、焊缝和某些铸件,无论是钢铁、有色金属和非金属,都可以采用超声波法进行检验。
各种机械零件、结构件、电站设备、船体、锅炉、压力容器和化工容器、非金属材料等,都可以用超声波进行有效的检测。
有的采用手动方式,有的可采用自动化方式。
就物理性能检测而言,用超声波法可以无损检测厚度、材料硬度、淬硬层深度、晶粒度、液位和流量、残余应力和胶接强度等。
2、方法接触法:就是探头与工件表面之间经一层薄的耦合剂直接接触进行探伤的方法。
耦合剂主要起传递超声波能量作用。
液浸法:就是将探头与工件全部浸入液体,或探头与工件之间局部充以液体进行探伤的方法。
液体一般用水,故又称水浸法。
探头不直接与工件接触,因而易于实现自动化检测,也适用于检测表面粗糙的工件。
1.3.5涡流检测(ET)涡流检测工业上无损检测的方法之一。
给一个线圈通入交流电,在一定条件下通过的电流是不变的。
如果把线圈靠近被测工件,像船在水中那样,工件内会感应出涡流,受涡流影响,线圈电流会发生变化。
由于涡流的大小随工件内有没有缺陷而不同,所以线圈电流变化的大小能反映有无缺陷。
原理:将通有交流电的线圈置于待测的金属板上或套在待测的金属管外(见图)。
这时线圈内及其附近将产生交变磁场,使试件中产生呈旋涡状的感应交变电流,称为涡流。
涡流的分布和大小,除与线圈的形状和尺寸、交流电流的大小和频率等有关外,还取决于试件的电导率、磁导率、形状和尺寸、与线圈的距离以及表面有无裂纹缺陷等。
因而,在保持其他因素相对不变的条件下,用一探测线圈测量涡流所引起的磁场变化,可推知试件中涡流的大小和相位变化,进而获得有关电导率、缺陷、材质状况和其他物理量(如形状、尺寸等)的变化或缺陷存在等信息。
但由于涡流是交变电流,具有集肤效应,所检测到的信息仅能反映试件表面或近表面处的情况。
特点:1、对于金属管、棒、线材的检测,不需要接触,也无需要耦合介质。
所以检测速度高,易于实现自动化检测,特别适合在线普检。
2、对于表面缺陷的探测灵敏度很高,且在一定范围内具有良好的线性指示,可对大小不同缺陷进行评价,所以可以用作质量管理与控制。
3、影响涡流的因素很多,如裂纹、材质、尺寸、形状及电导率和磁导率等。
采用特定脾电路进行处理,可筛选出某一因素而抑制其他因素,由此有可能对上述某单独影响因素进行有效的检测。
4、由于检查时不需接触工件又不用耦合介质,所以可进行高温下的检测。
由于探头可伸入到远处作业,所以可对工件的狭窄区域及深孔壁(包括管壁)等进行检测。
5、由于采用电信号显示,所以可存储、再现及进行数据比较和处理。
6、涡流探伤的对象必须是导电材料,且由于电磁感应的原因,只适用于检测金属表面缺陷,不适用检测金属材料深层的内部缺陷。
7、金属表面感应的涡流的渗透深度随频率而异,激励频率高时金属表面涡流密度大,随着激励频率的降低,涡流渗透深度增加,但表面涡流密度下降,所以探伤深度与表面伤检测灵敏度是相互矛盾的,很难两全。