无损检测概论
《无损检测概论》课件

无损检测的工作原理和方法
无损检测的工作原理基于材料对不同类型能量的反射、散射、透射和吸收的 特性。常用的无损检测方法包括:发射、接收和分析能量信号。
常用无损检测技术介绍
超声波检测
通过发送超声波脉冲来探测 物体内部的缺陷,并根据接 收到的反射信号推断缺陷的 位置和性质。
磁粉检测
利用磁场和铁粉颗粒的磁性 相互作用,检测材料中的缺 陷和裂纹。
从高层次来看,无损检测是一种用于识别、评估和监测材料、结构和系统中 缺陷和性能问题的技术。它可以在不破坏原材料或构件的情况下,提供准确 的结果。
无损检测的分类及应用领域
• 无损检测根据检测方法的不同可以分为:视觉检测、渗透检测、超声波检测、磁性颗粒检测等。 • 无损检测在多个领域中都有广泛应用,包括:航空航天、汽车制造、核能行业等。
渗透检测
通过涂覆可渗透液体的表面, 然后观察渗透液是否被材料 中的缺陷吸收,来检测缺陷 的存在。来自无损检测的优势和局限性
1 优势
无损检测无需破坏材料,能够快速、准确地检测缺陷,提高生产效率和安全性。
2 局限性
无损检测技术对操作符要求高,并且在某些情况下可能无法探测到微小的或深埋的缺陷。
无损检测在工业中的应用案例
航空航天
无损检测在航空航天行业中广泛 应用,用于检测飞机结构、发动 机零件等的缺陷和疲劳损伤。
汽车制造
无损检测可用于检测汽车零部件 的质量和完整性,确保汽车在生 产过程中没有任何缺陷。
核能行业
无损检测可以帮助检测核能设施 内部的缺陷,确保其安全性和性 能。
总结及未来发展趋势
无损检测是一个重要的技术领域,为许多行业提供了关键的质量控制和安全 保障。随着科学技术的不断发展,无损检测技术将进一步提高准确性、效率 和实用性。
无损检测概论

安全生产是企业发展的基础,没有安全生产企
业就不可能健康成长;
文明生产是现代企业管理基本要求。
第六章 无损检测概论
7、 无损检测的HSE管理 HSE的概念:HSE是健康(Health)、安全 (Safety)和环境(Environment)管理体系的简称。
体系实质:事前风险分析,确定可能发生的危
险和后果,采取防范手段和措施防止危险发生,
RT、UT探测内部缺陷,MT、PT适用表面缺陷,ET适用 钢管、钢板等规则材料表面、近表面缺陷。AE实时监控。
第六章 无损检测概论
6.1.4 无损检测新技术 随着现代技术发展尤其是数字和计算机技术 发展,产生了许多无损检测新技术: 计算机射线照相(CR)、数字平板照相(DR)、 层析照相(CT);超声波增加了衍射时差( TOFD)检测、相控阵(PA)导波(GW);电 磁检测增加了漏磁检测(MEL)等。
以减少人员伤害、财产损失和环境污染的有效
管理手段。
第六章 无损检测概论
7、 无损检测人员考虑措施:
(1)严格学习并尊重各项安全制度,考核合格后上岗;
(2)检测前做好准备工作,做到三不伤害;
(3)上岗前戴好劳保防护; (4)做好检测前各项安全措施; (5)射线检测前做好防火,减少不必要照射; (6)根据检测方法制定安全措施。
性,必须在检测前,根据被检物体的材料,结构
,形状,尺寸可能产生的缺陷种类,在什么部位
,什么方向等种种情况进行分析,然后根据无损
检测方法各自的特点选择最适合的检测方法。只
有这样,检测方法的选择和应用才会正确和合理
Байду номын сангаас 第六章 无损检测概论
6.3.4 综合应用各种无损检测方法 在无损检测应用中,必须认识到任何一种无损检 测方法都不是万能的,都有各自的优缺点,因此
无损检测概论

射线检测 (Radiography Testing )简称RT
超声波检测(Ultrasonic Testing)简称UT 磁粉检测(Magnetic Testing)简称MT
渗透检测(Penetrant Testing)简称)简称PT
四、无损检测方法的选择
1.经济方面的考虑
首先要考虑的是进行必要的资本投入,并应详细评估 资金的回收情况。对于一个好的企业,在检测方法和 可靠性方面的投资,会收到相当的经济效益。
一般:
射线检测对体积型缺陷比较敏感;
超声波检测对面缺陷比较敏感; 磁粉检测只能用于铁磁性材料的检测; 渗透检测则用于表面开口缺陷的检测; 涡流检测对开口或近表面缺陷、磁性和非磁性的 导电材料都具有很好的适用性。
因此,无损检测技术广泛应于各种设备、压力容器、机械零部 件等的检测诊断,受到工业界的普遍重视。
二、无损检测技术的发展阶段
(一)无损检测技术发展的三个阶段
无损检查( Nondestructive Inspection, NDI)、 无损检测(Nondestructive Testing,NDT)、
2. 在役检测 使用无损检测技术对装臵在运行过程中进行监测,或者在检修 期进行检测,能及时发现影响其安全运行的隐患,防止事故。 这对于大型设备,如核反应堆、桥梁建筑、铁路车辆、压力容 器、输送管道、飞机、火箭等,具有重要的意义。 在役检测不仅可以及时发现隐患,更重要的是可以根据所发 现的早期缺陷及其发展程度(如疲劳裂纹的萌生与发展),在 确定其方位、形状、尺寸和性质等的基础上,对装臵能否继续 使用及其安全运行寿命进行评价。
(三)无损检测技术的特点
1.无损检测不会对构件造成任何损伤 无损检测是在不破坏构件的前提下,利用材料物理性质的变 化来判断构件内部和表面是否存在缺陷,不会对材料、工件和 设备造成任何损伤。
无损检测基础

5.再热裂纹
名称
特征
产生机理
防止措施
冷裂纹
a.成生于较低温度,且产生于焊后一段时间以后,故又称为延迟裂纹。 b.主要产生于热影响区,也有发生在焊缝区的。 c.冷裂纹可能是沿晶开裂,穿晶开裂或两者混合出现。 d.冷裂纹引起的构件破坏是典型的脆断。
1.坡口尺寸不合理; 2.坡口有污物; 3.多层焊时,层间清渣不彻底; 4.焊接线能量小; 5.焊缝散热太快,液态金属凝固过快; 6.焊条药皮,焊剂化学成分不合理,熔点过高,冶金反应不完全,脱渣性不好; 7.钨极惰性气体保护焊时,电源极性不当,电流密度大,钨极熔化脱落于熔池中。 8.手工焊时,焊条摆动不良,不利于熔渣上浮。
a.合金元素合杂质的影响碳元素以及硫、磷等杂质元素的增加,会扩大敏感温度区。使结晶裂纹的产生机会增多。 b.冷去速度的影响 冷却速度增大,一是使结晶偏析加重,二是使结晶温度区间增大,两者都会增加结晶裂纹的出现机会。 c.结晶应力与拘束力的影响 在脆性温度区内,金属的强度极低,焊接应力又使这部分金属受拉,当拉应力达到一定程度时,就会出现结晶裂纹。
a.再热裂纹的产生机理有多种解释,其中楔型开裂理论的解释如下:近缝区金属在高温热循环作用下,强化相碳化物(如碳化钛、碳化钒、碳化铌、碳化铬等)沉积在晶内的位错上,使晶内强化迁都大大高于晶界强化,尤其是当强化相弥散分别在晶粒内时,会阻碍晶粒内部的局部调整,又会阻碍晶粒的整体变形,这样由于应力松弛而带来的塑性变形就主要由晶界金属来承担,于是,晶界区金属会产生滑移,且在三晶粒交界处产生应力集中,就会产生裂纹,即所谓的楔型开裂。图2-30是楔型开裂的示意图。
无损检测概论.

无损检测概论一.无损检测基础知识1.无损检测的定义与分类(1)定义:在不损坏试件的前提下,以物理或化学方法为手段,借助先进的技术和设备器材,对试件的内部及表面的结构、性质、状态进行检查和测试的方法,以“NDT”英文缩写表示。
而用人的肉眼为手段称之为宏观检查,以英文“VT”表示。
1无损探伤:是无损检测早期阶段的名称,其涵义是探测和发现缺陷;2无损检测:是当前阶段的名称,其内涵不仅仅是探测缺陷,还包括探测试件的一些其他信息,例如结构、性质、状态等,并试图通过测试,掌握更多的信息;3无损评价:是将进入或目前正在进入的新阶段的名称,其内涵不仅仅是探测缺陷、探测试件的结构、性质、状态,还要求获取更全面、更深刻的、更准确的综合信息,例如缺陷的形状、尺寸、位置、取向、内含物、缺陷部位的金相组织、残余应力等,结合成像技术、自动化技术、计算机数据分析和处理等技术,与材料力学、断裂力学等知识综合应用,对试件或产品的质量和性能给出全面、准确的评价。
(2)分类:目前无损检测方法可分为射线检测(RT)、超声波检测(UT)、磁粉检测(MT)、渗透检测(PT)、涡流检测(ET)、声发射检测(AE)。
1、常用的无损检测方法:RT、UT、MT、PT是应用最广泛的探测缺陷的四大常规方法2、 RT、UT是用于探测试件内部缺陷的,RT是检测内部的体积壮缺陷,UT是检测内部的平面形缺陷。
3、 MT和PT、ET主要用于探测试件表面和近表面缺陷。
4、声发射主要用于探测试件在承载状态下的缺陷张口位移(活动)情况。
5、其他如激光、红外、微波、液晶等技术应用于无损检测。
2.无损检测的目的(1)保证产品质量:通过无损检测可以将原材料中的冶炼、轧制缺陷和制造中的工艺缺陷,如焊接缺陷等一些不允许存在的缺陷发现并予以消除而保证产品质量。
(2)保障使用安全:通过无损检测可以发现设备试件在使用中产生的缺陷,并予以消除而提高了设备在规定的使用条件下工作时的可靠性。
无损检测概论

A型脉冲反射式模拟超声波检测仪的主要组成部分是:同步电路、扫描电 路、发射电路、接受放大器电路、显示器和电源电路等。
仪器工作原理:同步电路产生触发脉冲同时加至扫描电路和发射电路, 扫描电路受触发开始工作,产生锯齿波扫描电压,加至示波管水平偏转 板,使电子束发生水平偏转,在荧光屏上产生一条水平扫描线。与此同 时,发射电路受触发产生高频脉冲,施加至探头,激励压电晶片振动, 在工件中产生超声波,超声波在工件中以一定方式和速度向前传播,遇 到缺陷或底面产生反射,返回探头时,又被压电晶片转变为电信号,经 接收放大和检波,加至示波管垂直偏转板上,使电子束发生垂直偏转, 在水平扫描线的相应位置上产生缺陷回波和底波。
无损检测概论
武进
无损检测(NDT):就是利用声、光、磁和电等特
性,在不损坏或不影响被检对象使用性能的前提下, 检测被检对象中是否存在缺陷或不均匀性,给出缺 陷大小、位置、性质和数量等信息,进而判定被检 对象所处技术状态(如合格与否、使用寿命等)的 所有技术手段的总称。无损检测方法很多(目视检 测、声发射、超声波衍射时差法等),并且随着科 学技术的不断发展,出现了红外等新的检测技术手 段,但根据美国国家宇航局调研分析,其认为可分 为六大类约70余种。但在实际应用中比较常用的, 也就是我们说的常规无损检测方法仍指为涡流检测、 磁粉(漏磁)检测、射线检测、渗透检测和超声检 测五种。
缺点:不适用于形状复杂的工件,而且只能检测导 电材料表面和近表面缺陷,缺陷深度一般不大于 5mm,涡流检测必须有高频信号存在,给信号处理带 来一定困难,容易引起信号相互干涉。检测结果也 易受到材料本身及检测仪器功能和检测条件等其它 因素干扰。
漏磁(磁粉)检测(MT)(MFT)法的简介
漏磁(磁粉)检测
无损检测技术概论

Hale Waihona Puke b) 声学方法:——超声检测; ——声发射检测 ; ——电磁声检测
添加标题
B超
添加标题
电磁方法:
表面方法:
——涡流检测 ; ——漏磁检测
——磁粉检测 ; ——渗透检测 ; ——目视检测
——泄漏检测 。
泄漏方法:
01
——红外热成像检测
红外方法:
02
无损检测NDT (Nondestructive Test)
X射线探伤机
用途:X射线探伤机适用于国防、造船、石油、化工、机械、航空航天和建筑等工业部门检查船体、管道、高压容器、锅炉、飞机、车辆和桥梁等材料、零部件加工焊接质量,内部缺陷以及各种轻金属、橡胶、陶瓷等加工的质量。
X射线探伤机
特点: X射线发生器体积小,阴极接地,风扇强迫冷却; 重量轻,携带方便,操作简单; 自动训练X射线发生器,查询曝光参数; 延时启动高压,保证操作者安全; 严格控制生产工艺,造型美观,结构合理。
射线探伤
射线探伤
P60
利用 X射线或γ射线在穿透被检物各部分时强度衰减的不同﹐检测被检物中缺陷的一种无损检测方法。 部分的厚度或密度因缺陷的存在而有所不同。当X射线或γ射线在穿透被检物时﹐射线被吸收的程度也将不同。若射线的原始强度为I 0﹐通过线吸收係数为μ 的材料至距离d后﹐强度因被吸收而衰减为I ﹐其关系为 d为物体的厚度,μ 称为材料对射线的吸收系数。如果物体的组织不均匀,或者内部有孔洞或夹杂,则物体各部分的吸收系数并不相同,因此检测到的各处的射线强度亦不相同。
当能量小于1.022 MeV 时,不产生这一效应,能量越大这一效应也越大。这一效应造成对入射线强度的减弱。所以用作探伤时,过分增加射线能量有时反而会减小穿透深度。因此一般经验是最大入射能量在30 MeV 以下。 总的吸收系数
《无损检测概述》课件
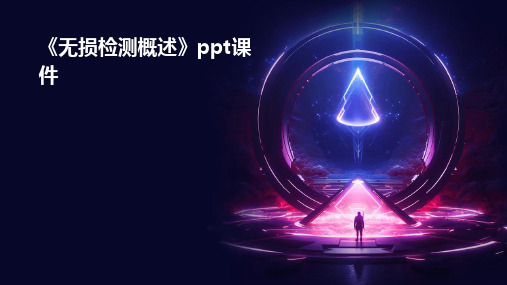
检测标准与规范
无损检测技术的标准与规范需要不断 完善,以确保检测结果的准确性和可 靠性。
检测人员素质
无损检测技术需要高素质的检测人员 ,以确保检测结果的准确性和可靠性 。
无损检测技术的未来发展方向
智能化
无损检测技术将向智能化方 向发展,通过引入人工智能 、机器学习等技术,提高检 测效率和准确性。
数字化
无损检测技术将向数字化方 向发展,通过引入数字化技 术,实现无损检测数据的数 字化存储、处理和传输。
集成化
无损检测技术将向集成化方 向发展,通过将多种无损检 测技术进行集成,实现更全 面、更准确的检测。
绿色环保
无损检测技术将向绿色环保 方向发展,通过采用环保材 料和绿色技术,降低对环境 的负面影响。
优点
对表面缺陷检测灵敏度高,可实现快 速在线检测。
缺点
仅适用于导电材料,对非导电材料不 适用。
渗透检测
原理
应用
利用渗透剂渗透到物体的表面裂纹中,通 过显像剂显示缺陷。
适用于检测非疏孔性材料的表面裂纹、气 孔等缺陷。
优点
对表面缺陷检测灵敏度高,操作简便。
缺点
需要使用化学试剂,对环境有一定影响。
CHAPTER
原理
利用磁粉的磁性,检测铁磁性 材料的表面和近表面缺陷。
应用
适用于检测钢铁、不锈钢等材 料的表面裂纹、折叠等缺陷。
优点
对表面缺陷检测灵敏度高。
缺点
仅适用于铁磁性材料,对非磁 性材料不适用。
涡流检测
原理
利用电磁感应原理,检测导电材料的 表面和近表面缺陷。
应用
适用于检测金属材料的表面裂纹、折 叠等缺陷。
02
磁粉检测技术细节
- 1、下载文档前请自行甄别文档内容的完整性,平台不提供额外的编辑、内容补充、找答案等附加服务。
- 2、"仅部分预览"的文档,不可在线预览部分如存在完整性等问题,可反馈申请退款(可完整预览的文档不适用该条件!)。
- 3、如文档侵犯您的权益,请联系客服反馈,我们会尽快为您处理(人工客服工作时间:9:00-18:30)。
●
 ̄  ̄ _  ̄  ̄  ̄
●
 ̄  ̄  ̄  ̄
夹渣
●
○
○
○
 ̄
 ̄
 ̄
 ̄  ̄
注:●很适用; ○适用; △有附加条件适用; ※不适用;  ̄不相关
检测方法和检测对象的适应性(二)
分类 检测对象 内部缺陷检测 方法 表面近表面缺陷检 测方法
RT
白点 表 表面裂纹 面 表面针孔 缺 折叠 断口白点 ○  ̄ ※ △ ※
无损检测技术发展 过程的三个阶段
• 无损探伤:(Non-distructive Inspection) 简称NDI
• 早期名称 • 探测和发现缺陷
• 无损检测:(Non- distructive Testing) 简称NDT
• 当前名称 • 不仅要探测发现缺陷,还包括探测试件的其 它信息,如结构、状态、性质
UT
○ △ ※  ̄ ※
MT
 ̄ ● △ ○ ●
PT
 ̄ ● ● ○ ●
ET
 ̄ ● △ ○  ̄
陷
分 类
注:●很适用; ○适用; △有附加条件适用; ※不适用;  ̄不相关
谢
谢
• 由于无损检测技术及其方法种类繁多,因此 有必要对其进行分类。教材附录15介绍了美 国国家咨询委员会无损检测评价委员会的分 类系统,它将无损检测技术划分为6大类,是 其中的一种分类方法。可以从总体上了解各 类方法的检测对象、适用范围、局限性等。
2.无损检测的目的
1)保证产品质量 • 借助仪器和器材,可以发现目视检查无法发 现的内外部宏观缺陷。
4)钢管中常见宏观缺陷及其产生原因 • 裂纹 由于产生原因不同而分为纵裂纹和横裂 纹 • 表面划伤 • 翘皮的折叠 表面可见并呈一定角度 • 夹杂和分层
5)钢棒和型材中常见宏观缺陷及其产生原因 • 内部缺陷 由于轧制作用,缺陷一般有延展性
• 表面缺陷 产生原因不同,形状不同,但均分 布在表面和近表面
5、无损检测方法的应用选择小结
• 锅炉压力容器制造过程中无损检测的应用、各 种无损检测方法与检测对象的适应性如下
• 锅炉压力容器制造过程中无损检测方法的选择 • 原材料检验 • 板材 • 锻件和棒材 UT UT、MT(PT)
• 管材 • 螺栓
UT(RT)、MT(PT) UT、MT(PT)
•
焊接检验
6)钢板中常见宏观缺陷及其产生原因 • 与锻件和型材中的缺陷基本类似,按其严重 程度可分为大、中、小三类缺陷
7)在用设备定检中常见宏观缺陷及其产生原因 • 在用设备定检中,除常发现因制造方式不同导致 的制造缺陷发展以致缺陷超标,还应注意设备因 运行而发生的运行缺陷。 • 疲劳裂纹 设备或部件承受交变载荷而引起的裂 纹,该类裂纹的断口一般有明显的呈同心圆状的 疲劳源并伴有脆性断口。 • 应力腐蚀裂纹 处于特定腐蚀介质中且受拉应力 作用下产生的裂纹 • 氢损伤 • 摩擦腐蚀 • 空化腐蚀
• 无损评价:(Non- distructiv Evaluation) 简称NDE • 新的发展阶段的名称 • 不仅要求发现缺陷,探测试件的结构、状态、 性质,还要求获取更全面、准确和综合的信 息,辅以成象技术、自动化技术、计算机数 据分析和处理技术等,与材料力学、断裂力 学等学科综合应用,以期对试件和产品的质 量和性能作出全面、准确的评价。
• 在产品制造过程中的适当环节正确地进行无 损检测,防止以后的工序浪费,减少返工, 降低废品率,从而降低制造成本。
3.无损检测的应用特点
1)要与破坏性检测相结合
• 由于无损检测具有的局限性,不是所有的需 要测试的项目和性能都能进行无损检测,这 种局限性可能来自方法本身,也可能来自被 测试对象的形状、位置等客观条件的不允许, 所以某些试验只能采用破坏性检验。
• 其它几种常用无损探伤方法
• 涡流检测(Eddy current Testing )简称ET • 声发射检测(Acoustic Emission)简称AE • 目视检测(Visual and Optical Testing) 简称 VT
• 泄漏检测(Leak Testing)简称LT
• 其它无损检测技术 • 随着现代科学技术的发展,激光、红外、微 波、液晶等技术都被应用于无损检测领域, 而传统的常规无损检测技术也因为现代科技 的发展,大大丰富了应用方法,如射线照相 就可细分为X射线、γ射线、中子射线、高能 X射线、射线实时照相、层析照相……等多种 方法。
4.缺陷的种类和产生原因
• 如前节所述,了解材料和焊缝中的缺陷种类 和产生原因,有助于正确选择无损检测方法, 制定合理的检测方案,从而取得正确的检测 结果。
1)钢焊缝中常见宏观缺陷及其产生原因(外 观缺陷略) • 气孔 由形状和产生原因分为不同种类 • 夹渣 由成份分为金属夹渣(夹杂)和非金属 夹渣 • 裂纹 由产生温度分为热裂纹和冷裂纹;由产 生原因分为再热裂纹、层状撕裂和应力腐蚀 裂纹等。 • 未焊透 • 未熔合 分为坡口未熔合和根部未熔合
– – – – – – – – – 坡口 清根部位 对接焊缝 角焊缝和T型焊缝 工卡具焊疤 爆炸复合层 坡焊复合层堆焊前 坡焊复合层堆焊后 水压试验后 UT、PT(MT) PT(MT) RT(UT)、MT(PT) UT(RT)、PT(MT) MT(PT) VT MT(PT) UT、PT MT
检测方法和检测对象的适应性(表一)
• 无损检测技术的产生和发展:借助于现代科学技术 发展的基础产生和发展。 • 射线照相法(RT)——X射线的发现(伦琴射线) • 超声波检测(UT)——二次大战中迅速发展的声纳 技术和雷达技术的基础上开发 • 磁粉检测(MT)——电磁学基础 • 渗透检测(PT)——物理化学的进展 • 涡流检测(ET)——电磁学(电磁感应) • ………… • 现代电子技术和计算机技术的发展和其它学科介入 无损检测领域,使无损检测技术如虎添翼,得到质 的飞跃。
无损检测概论
1.无损检测的定义和分类 2.无损检测的目的 3.无损检测的应用特点 4.缺陷的种类和产生原因 5. 无损检测方法的应用选择小结
1.无损检测的定义和分类
• 定义: • 通俗的定义:无损检测指在不损坏试件的前 提下,对试件进行检查和测试的方法。 • 亦称非破坏性检验。
• 现代无损检测的定义:在不破坏试件的前提 下,以物理或化学方法为手段,借助现代的 技术和设备器材,对试件内部及表面的结构、 性质、状态进行检查和测试的方法。
• 无损检测不需破坏试件就能完成检测过程, 可以对产品进行100%检验和逐件检验,为产 品质量提供有效保证。
2)保障使用安全 • 可以对在用设备和部件进行定期检验,保障 使用安全。
3)改进制造工艺
• 在产品工艺试验中,对工艺试样进行无损检 验,并根据检测结果改进制造工艺,确定理 想的制造工艺。
4)降低生产成本
2)正确选用无损检测的时机 • 必须根据无损检测的目的,正确选择无损检测 的时机,从而顺利地完成检测预定目的,正确评 价产品质量。
3)正确选用合理的无损检测方法 • 每种无损检测方法均具有局限性,不能适用 于所有工件和缺陷。为了提高检测结果的可 靠性,必须根据被检件的特点(材料、结构、 形状、尺寸,预计可能产生的缺陷种类、形 状、所处部位、取向……)选择适宜的检测 方法。 • 所谓适宜 ,即不是片面的追求最高的检测灵 敏度,而是在保证充分安全性的同时兼顾产 品的经济性,这样选择的检测方法才是正确、 合理的。
4)综合应用各种无损检测方法 • 每种无损检测方法均有其自身的优缺点,不能适 用于所有工件和缺陷。因此,在对某试件确定无 损检测方案时,只要可能,应尽量采用多种无损 检测方法,以保证方法间的互补,从而取得更多 的产品和缺陷信息 • 除应用无损检测方法获得产品信息外,还应充分 利用其它有关产品的材料、焊接、加工工艺及产 品结构等多方面的信息,综合判断。 • 这点对于大型和重要工件的无损检验尤为重要
分类 检测对象 内部缺陷检测方法 RT 试 件 分 类 锻件 铸件 压延件(管、板、型材 ※ ● ※ UT ● ○ ● 表面近表面缺陷检测方 法 MT ● ● ● PT ● ○ ○ ET △ △ ●
焊缝
内 部 缺 陷 分 类 裂纹 分层 疏松 气孔 缩孔 未焊透 未熔合
●
※ ※ ● ● ● △
●
● ○ ○ ○ ● ●
锅炉压力容器检验中常用的 无损检测方法
• 四大常规无损探伤方法: • 射线检测 (Radiography Testing)简称RT • 超声波检测(Ultrasonic Testing)简称UT
• 磁粉检测(Magnetig Testing)简称MT • 渗透检测(Penetrant Testing)简称PT
2)铸件中常见宏观缺陷及其产生原因 • 气孔 分为单个气孔和密集性气孔 • 夹渣和夹沙 • 冷隔 • 缩孔和疏松 • 裂纹 由于形成温度不同分为热裂纹和冷裂纹
3)锻件中常见宏观缺陷及其产生原因 • 缩孔和缩管 • 非金属夹杂物 • 夹砂 • 龟裂 • 锻造裂纹 产生原因较多,由于产生原因不同 形状和发生的部位也不同。 • 白点 氢致裂纹