冲裁模设计过程实例一
冲裁模设计实例1

冲裁模设计实例1零件图如下:图2-1 零件零件名称:托板,大批量生产材料:08F钢板 t=2mm2.1 冲裁件的工艺性分析冲裁零件的工艺性是指零件对冲压加工工艺的适应性,即加工过程的难易程度。
良好的加工工艺性是指在满足使用要求的前提下能够用最经济实用的方法将零件给冲压出来。
而级进模由于多工位因素大的存在必须从冲裁件的基准、结构形式、尺寸公差、表面精度、材料性能、模具的工作强度等方面进行分析冲裁件的工艺性。
本设计的冲裁件为托板,其加工的工艺性分析如下:冲件为08F钢板,是优质的碳素结构钢,具有良好的冲压性能;冲裁件结构简单但有90度尖角,为了提高模具寿命故改为R1的工艺圆角,零件图上未标注尺寸偏差,属未标注公差,可按IT14级确定工件尺寸的公差。
经查公差表,各尺寸公差58074.0-,38062.0-,052.0-,044.0-,1422.022.0+-,1722.022.0+-,φ5.3 3.00+为:2.2 确定工艺方案及模具结构形式在冲压工艺方案确定后,模具结构形式的确定也相当重要,因为他直接关系到冲压过程的生产效率、冲压件的质量、尺寸精度、及其模具的寿命。
由上面的分析可知冲裁件尺寸要求不高,尺寸不大形状结构简单,但生产量大,根据材料较厚的特点,为保证孔位精度,冲模有较高的生产率,实行工序集中的工艺方案,采用导正钉进行定位、刚性卸料装置、自然卸料方式的级进模结构形式。
级进模是指在依次排列不同工步的凸模下连续送进坯料,使得压力机的一次行程中在模具的不同部位同时完成数道工序的模具。
级进模可以减少模具和设备的数量,提高生产率,而且容易实现自动化。
但是比简单模具结构复杂、制造麻烦。
成本相对较高。
表2-2冲压批量图批量项目单件小批中批大批大量大件<1 1-2 2-20 20-300 >300中件<1 1-5 5-50 50-1000 >1000小件<1 1-10 10-100 100-5000 >5000模具形式简易模简单模连续模、复合模连续模、复合模连续模、复合模组合模组合模简单模简单模简单模简易模半自动模半自动模设备形式通用压力机通用压力机高速压力机机械高速压力机自动机专用压力机与自动机自动和半自动通用压力机注:表内数字为每年班产量的概略数值(千件)第3章:模具设计计算3.1排样、计算条料宽度及其确定步距在纯冲裁类级进模排样设计时原则上为先冲导正孔和间距精度要求较高的孔。
冲裁实例
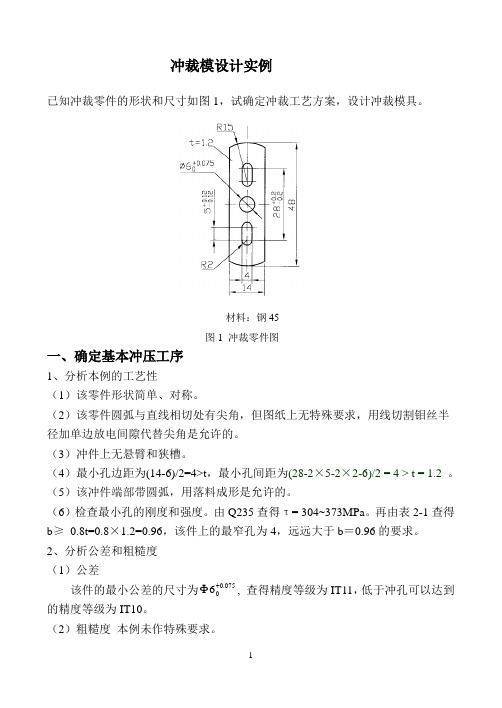
冲裁模设计实例已知冲裁零件的形状和尺寸如图1,试确定冲裁工艺方案,设计冲裁模具。
材料:钢45 图1 冲裁零件图一、确定基本冲压工序1、分析本例的工艺性(1)该零件形状简单、对称。
(2)该零件圆弧与直线相切处有尖角,但图纸上无特殊要求,用线切割钼丝半径加单边放电间隙代替尖角是允许的。
(3)冲件上无悬臂和狭槽。
(4)最小孔边距为(14-6)/2=4>t ,最小孔间距为(28-2×5-2×2-6)/2 = 4 > t = 1.2 。
(5)该冲件端部带圆弧,用落料成形是允许的。
(6)检查最小孔的刚度和强度。
由Q235查得τ= 304~373MPa 。
再由表2-1查得b ≥ 0.8t=0.8×1.2=0.96,该件上的最窄孔为4,远远大于b =0.96的要求。
2、分析公差和粗糙度 (1)公差该件的最小公差的尺寸为075.006+Φ, 查得精度等级为IT11,低于冲孔可以达到的精度等级为IT10。
(2)粗糙度 本例未作特殊要求。
3、被冲材料为Q235,冲裁性能很好。
根据以上分析,本例的冲裁工艺性好。
4、确定基本冲压工序由图1可知,该件外形为落料,内形为冲孔,冲孔有一圆孔和两长圆形孔。
二、确定冲裁工艺方案1、确定冲裁工艺方案:就是确定工序顺序和工序组合。
方案一:先落料、后分三次冲孔,采用四付单工序模方案二:先落料、后同时冲三孔,采用二付单工序模方案三:先冲孔、后落料,采用级进模冲裁方案四:先冲孔、后切断,采用少废料级进模冲裁方案五:同时冲孔、落料,采用复合工序模方案一和方案二的模具结构简单,生产率低,既不能满足产量要求又不经济;方案四最大的特点是省料,但冲件精度低,若按长度方向送进零件尺寸可以保证但料窄,送料步距大,不方便;若按宽度方向送进,冲件圆弧与直边吻接不好。
方案五冲件精度高但操作不方便,生产率不高;方案三既能满足冲件精度要求,模具数量少,操作方便,生产率高,若采用侧刃定距还便于实现自动送料。
2018-冲裁模设计范例-word范文 (13页)

本文部分内容来自网络整理,本司不为其真实性负责,如有异议或侵权请及时联系,本司将立即删除!== 本文为word格式,下载后可方便编辑和修改! ==冲裁模设计范例篇一:冲裁模设计实例3. 排样设计篇二:一个垫片的冲裁模设计范例冲裁模零件简图:如图1所示.名称:垫圈材料:Q235钢材料厚度:2mm 生产批量:大批量要求设计此工件的冲裁模。
图1 零件图一. 冲压件工艺分析该零件形状简单、对称,是由圆弧和直线组成的.由表2-10、2-11查得,冲裁件内外所能达到的经济精度为IT14,孔中心与边缘距离尺寸公差为±0.2mm.将以上精度与零件简图中所标注的尺寸公差相比较,可认为该零件的精度要求能够在冲裁加工中得到保证.其它尺寸标注、生产批量等情况,也均符合冲裁的工艺要求,故决定采用利用导正销进行定位、刚性卸料装置、自然漏料方式的冲孔落料模进行加工.方案一采用复合模加工。
复合模的特点是生产率高,冲裁件的内孔与外缘的相对位置精度高,冲模的轮廓尺寸较小。
但复合模结构复杂,制造精度要求高,成本高。
复合模主要用于生产批量大、精度要求高的冲裁件。
方案二采用级进模加工。
级进模比单工序模生产率高,减少了模具和设备的数量,工件精度较高,便于操作和实现生产自动化。
对于特别复杂或孔边距较小的冲压件,用简单模或复合模冲制有困难时,可用级进模逐步冲出。
但级进模轮廓尺寸较大,制造较复杂,成本较高,一般适用于大批量生产小型冲压件。
比较方案一与方案二,对于所给零件,由于两小孔比较接近边缘,复合模冲裁零件时受到壁厚的限制,模具结构与强度方面相对较难实现和保证,所以根据零件性质故采用级进模加工。
二. 模具设计计算1.排样、计算条料宽度及确定步距采用单排方案,如图3-2。
由表2-18确定搭边值,根据零件形状两式件间按矩形取搭边值取搭边值。
,侧边则进距:条料宽度:查表2-19图3-22.计算冲压力该模具采用钢性卸料和下出料方式 1)落料力查表8-72)冲孔力中心孔:2个小孔:3)冲裁时的推件力查表2-37取表2-38,序号1的凹模刃口形式,故,则个为避免各凸模冲裁力的最大值同时出现,且考虑到凸模相距很近时避免小直径凸模由于承受材料流动挤压力作用而产生倾斜或折断故把三冲孔凸模设计成阶梯凸模如图3-3图3-3则最大冲压力:3.确定模具压力中心如图3-4,根据图形分析,因为工件图形对称,故落料时F落的压力中心在上O1;冲孔时F孔1、F孔2的压力中心在O2上。
冲裁模的设计步骤及实例
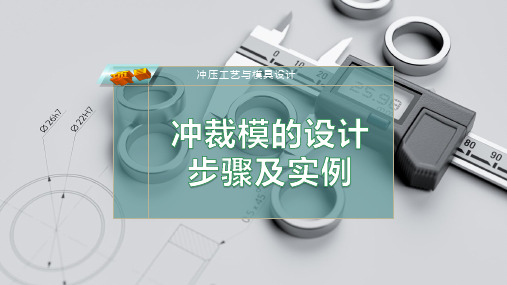
压力机闭合高度与模具闭合高度的关系 M— 1—床身; 2—滑块
冲裁模的设计步骤及实例
1.1 冲裁模的设计步骤
模具总装配图的一般布置情况
Hale Waihona Puke 冲裁模的设计步骤及实例1.2 冲裁模的设计实例
1.冲压件工艺性分析 2.冲压工艺方案确定 3.主要设计计算
4.模具总体设计 5.模具主要零部件的设计 6.模具装配图
冲压工艺与模具设计
冲压工艺与模具设计
冲裁模的设计步骤及实例
1.1 冲裁模的设计步骤
1.冲裁件工艺性分析。 2.确定冲裁工艺方案。 3.选择模具的结构形式。 4.进行必要的工艺计算。 5.选择并确定模具主要零部件的结构与尺寸。 6.选择压力机的型号或验算已选的压力机。 7.绘制模具总装配图及零件图。
冲裁模的设计步骤及实例
冲裁模的设计步骤及实例
1—顶杆; 2、4、13—垫板; 3—凸模固定板; 5—凸模; 6—推件块; 7—落料凹模; 8—导料销; 9—卸料板; 10—推杆; 11—凸凹模; 12—凸凹模固定板; 14—上模座; 15—模柄; 16— 17—橡胶; 18—卸料螺钉; 19—挡料销; 20—下模座
落料冲孔复合模总装配图
冲裁工艺与模具设计-冲裁模设计步骤及实例
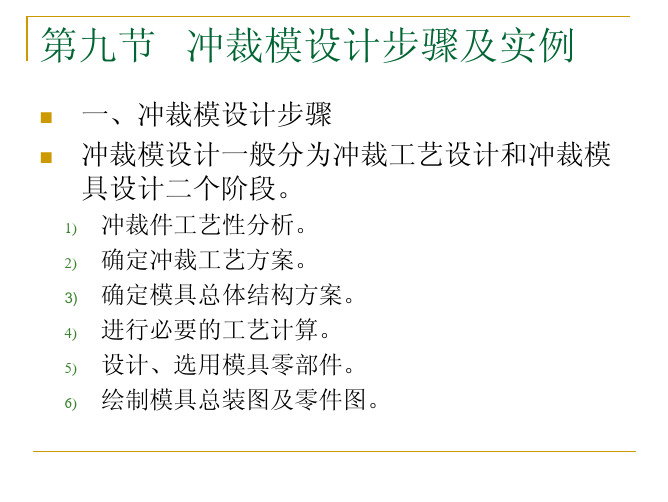
高模具寿命,建议将所有90°清角改为R=1的圆角。 3. 尺寸精度:零件图上所有尺寸均未标注公差,属自由尺寸,可
按IT14级确定工件尺寸的公差。经查公差表,各尺寸公差为: 58-0.74、38-0.62、30-0.52、16-0.44、14±0.22、17±0.22、
Ф3.5+0.3 结论:可以冲裁
《冲压工艺及模具设计》
第2(章1冲)裁模具工类艺型及冲裁模设计
模具类型主要是指单工序模、复合模、级进模三种。有些单件试 制或小批量生产的情况下,也采用简易模或组合模。
模具类型应根据生产批量、冲件形状与尺寸、冲件质量要求、材 料性质与厚度、冲压设备与制模条件、操作与安全等因素确定。
(2)操作与定位方式
△ ------条料下料时的下偏差值 C -------条料与导料板之间的间隙
《冲压工艺及模具设计》
第2章 冲裁工艺及冲裁模设计
表 2.5.3剪料公差△及条料与导料板之间隙δ(mm)
《冲压工艺及模具设计》
第2章 冲裁工艺及冲裁模设计
2.计算总冲压力 由于冲模采用刚性卸料装置和自然漏料方式,故
总的冲压力为: P总冲压力=P冲裁力+P推件力 P冲裁力=P1+P2 式中 P1--------落料时的冲裁力
《冲压工艺及模具设计》
第2章 冲裁工艺及冲裁模设计
冲裁模设计要点及设计实例
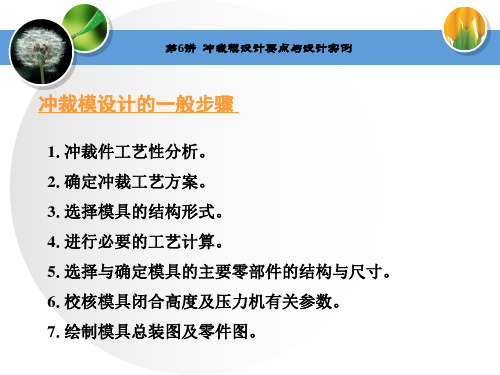
第6讲 冲裁模设计要点与设计实例 讲
七、绘制模具总装图和零件图
1.绘制模具总装图 .绘制模具总装图 应清楚表达各零件之间的装配关系以及固定连接方式。 1)主视图 ) 剖视图,闭合状态,闭合高度尺寸,条料和工件剖切面涂 视图, 状态,
红/黑
2)俯视图 ) 部分,未见部分可用虚线表示, 俯视可见部分,未见部分可用虚线表示,平面轮廓尺寸, 图中排样图轮廓线用双点划线表示。 表示。 侧视图、局部视图和仰视图 3)侧视图、局部视图和仰视图 一般不要求,必要画时出, 一般不要求,必要画时出,宜少勿多。
因冲裁力不大, 因冲裁力不大,压力中心偏 移坐标原点O较小,为了便于模 移坐标原点 较小, 较小 具的加工和装配, 具的加工和装配,模具中心仍 选在坐标原点O。若选用 选在坐标原点 。若选用J23-25 冲床, 点仍在压力机模柄孔投 冲床,C点仍在压力机模柄孔投 影面积范围内,满足要求。 影面积范围内,满足要求。
起粗定距的活动挡料销、 起粗定距的活动挡料销、弹簧和螺 塞选用标准件,规格为 × 。 塞选用标准件,规格为8×16。
φ8mm导正销 导正销
第6讲 冲裁模设计要点与设计实例 讲
(3)导料板的设计 ) (4)卸料部件的设计 ) ① 卸料板的设计 ②卸料螺钉的选用 (5)模架及其它零部件设计 )
第6讲 冲裁模设计要点与设计实例 讲
第6讲 冲裁模设计要点与设计实例 讲
五、模具的主要零部件设计
模具主要零件的结构设计,就是确定工作零件、 模具主要零件的结构设计,就是确定工作零件、定位零 件、卸料和出件零件、导向零件以及连接与固定零件的结构 卸料和出件零件、
形式和固定方法。
在设计时, 在设计时,要考虑到零部件的加工工艺性和装配工艺性。
冲裁模设计过程实例(一)
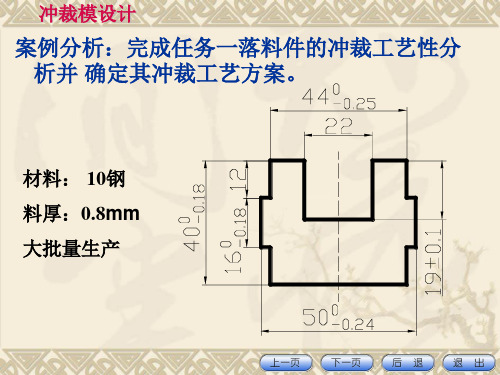
总个数为:
1500 43.6
1000 51.5
34
19
646
➢ 裁成宽53.6mm、长1500mm的条料,则一张板材能出的零件
总个数为:
1000 53.6
1500 41.5
18
36
648
➢ 裁成宽53.6mm、长1000mm的条料,则一张板材能出的零件
总个数为:
1500 53.6
凹模外壁间的距离均满足最小距离要求。
冲裁模设计
凸模与固定板结构
冲裁模设计
任务一凹模结构设计(P579)
冲裁模设计
案例分析:任务一模架及连接固定件的设计
凹模外形尺寸为110mm×100mm, 后侧导柱模架规格为: 上模座125mm×100mm×30mm, 下模座125mm×100mm×35mm, 导柱22mm×130mm, 导套22mm×80mm×28mm。 初选压力机为J23—16。压入式模柄规格A30×73。 垫板外形尺寸同凹模周界,厚度取8mm。 凸模固定板外形尺寸也为凹模周界尺寸,厚度取27mm。 根据模具尺寸,选M8的螺钉和φ8的销钉,卸料螺钉也为M8。
C2 19 0.025 mm
技术要求:凸模刃口按凹模实际刃口尺寸配作,以0.0720.104mm的间隙与凹模配制。
冲裁模设计
e)弹性元件选用与计算
材料较薄,料厚为0.8mm,采用弹性卸料装置,橡胶尺寸计算
如下:
(1)确定橡胶垫自由高度
H 0 (3.5 ~ 4)H工
H 工 h工作 h修磨 t 1mm (5 ~ 10)mm
a)
现选用1500mm×1000mm的钢板,则需计算采用 不同的裁剪方式时,每张板料能出的零件总个数。
冲裁模设计
模具毕业设计实例冲裁模设计举例

冲裁模设计举例图2.69所示零件为电视机安装架下板展开坯料,材料为1Cr 13,厚度mm t 3=,未注圆角半径mm R 1=,中批量生产,确定产品的冲裁工艺方案并完成模具设计。
图2.69 零件图1. 冲裁件工艺性分析零件的加工涉及冲孔和落料两道工序。
除孔中心尺寸公差为±0.1mm 和孔径尺寸公差为+0.2mm 外,其余尺寸均为未注公差,查表2.4可知,冲裁件内外形的达到的经济精度为IT12~IT14级。
符合冲裁的工艺要求。
查表2.2可知,一般冲孔模冲压该种材料的最小孔径为d ≥1.0t ,t =3mm,因而孔径ø8mm 符合工艺要求。
由图可知,最小孔边距为:d =4mm ,大于材料厚度3mm ,符合冲裁要求。
2. 确定冲裁工艺方案及模具结构形式该冲裁件对内孔之间和内孔与外缘之间有较高的位置精度的要求,生产批量较大,为保证孔的位置精度和较高的生产效率,采用冲孔落料复合冲裁的工艺方案,且一次冲压成形。
模具结构采用固定挡料销和导料销对工件进行定位、弹性卸料、下方出料方式的倒装式复合冲裁模结构形式。
3. 模具设计与计算(1)排样设计排样设计主要确定排样形式、条料进距、条料宽度、材料利用率和绘制排样图。
1)排样方式的确定。
根据冲裁件的结构特点,排样方式可选择为:直排。
2)送料进距的确定。
查表2.7,工件间最小工艺搭边值为mm 2.2,可取mm a 31=。
最小工艺边距搭边值为mm 5.2,取mm a 3=。
送料进距确定为mm h 44.199=。
3)条料宽度的确定。
按照无侧压装置的条料宽度计算公式,查表2.8、表2.9确定条料与导料销的间隙和条料宽度偏差分别为mm mm b 0.1,0.10=∆=。
()()0100093132862-∆-∆-=+⨯+=++=b a L B4)材料利用率的确定。
%08.91%10044.1999344.19686=⨯⨯⨯==Bh A η 4)绘制排样图。
- 1、下载文档前请自行甄别文档内容的完整性,平台不提供额外的编辑、内容补充、找答案等附加服务。
- 2、"仅部分预览"的文档,不可在线预览部分如存在完整性等问题,可反馈申请退款(可完整预览的文档不适用该条件!)。
- 3、如文档侵犯您的权益,请联系客服反馈,我们会尽快为您处理(人工客服工作时间:9:00-18:30)。
➢ 裁成宽43.6mm、长1000mm的条料,则一张板材能出的零件
总个数为:
145.3600150.150034 19646
➢ 裁成宽53.6mm、长150数为:
150.3600145.150018 36648
➢ 裁成宽53.6mm、长1000mm的条料,则一张板材能出的零件
y7 20 y8 10.5 y9 1
l2 12
8
y2 14
7
5 9
3
1
2
6
4
冲裁模设计
代入公式计算得:
x0 0
n
li yi
y0
i1 n
li
i1
22(20)221212(134) 31(98)11111mm
0.08mm
冲裁模设计
d) 凸凹模刃口尺寸计算,已知材料为08钢, 料厚0.8mm。
冲裁模设计
c)压力中心的计算
零件左右对称,只需计算压力中心纵坐标。建立坐标系,并 将零件右半部分图形分解为9条直线,则每段直线的长度及中点 的纵坐标分别为:
l1 22
l3 3
l4 16 l5 3
l6 12
l7 11 l8 19 l9 11
y1 20
y3 8
y4 0
y5 8
y6 14
冲裁模设计
(3)确定橡胶垫的平面尺寸,外形为矩形,中间开有矩形孔以 避让凸模。避让孔尺寸为45mm×55mm,外形暂定一边长为 110mm,则另一边长为
b1104555A
b72604555mm89mm 110
(4)校核橡胶垫的自由高度 H0 36 0.65
a 11055
高径比在0.5~1.5之间,所以选用的橡胶垫规格合理。 橡胶的装模高度约为0.85×36mm=30.6mm,取整装模高度为 30 mm。卸料板外形尺寸同凹模外形尺寸110mm×100mm, 厚度取8mm,并用四个卸料螺钉将其和橡胶固定于上模。
总个数为:
155.3600140.150027 24648
冲裁模设计
经比较第3、4种裁剪方法的材料利用率最高。考虑工人操作方 便,选用第4种裁剪方式,即裁为宽53.6mm、长1000mm的条 料。其具体排样图如下图所示。
冲裁模设计
b)计算冲裁力,卸料力:F=KLtť=1.3*224*0.8*300=69888N, F推件力=F*0.06=4193N, 初选压力机为J23—16
冲件图
凹模磨损示意图
冲裁模设计 说明:因零件较薄凹模计算采用配做法。落料件应先计算凹
模。(见中国模具设计大典P211表7.2-4 标准公差数值(摘自G B/T
1800.3—1998))
1. 磨损后刃口尺寸变大的有: 4400.24mm、4000.18mm 、1600.18mm 、 5000.24mm ,
2. 冲裁工艺方案的确定
一套简单落料模 3. 选择模具的结构形式
采用单工序模具
冲裁模设计
模具结构:单工序落料模 材料料厚:0.8mm 卸料装置:弹性卸料 定位零件:固定挡料销和导料销
冲裁模设计
任务二装配图
1-下模座 2-销钉 3-凹模 4-导料销 5-橡胶 6-导套 7-凸模固定板 8-上模座 9-卸料螺钉 10-模柄 11-横销 12-防转销 13-螺钉 14-垫板 15-凸模 16-导柱 17-卸料版18-螺钉 19-挡料销
精度等级都为IT12,所以X取0.75。代入公式得:
A 1 (4 4 0 .7 0 5 .2)0 0 4 .2/4 4 4.8 3 0 0 .0 2 m 6 m A 2 (4 0 .7 0 5 .1 )0 0 8 .1/4 8 3.8 9 0 0 .0 7 m 5 m
A 3 ( 1 6 0 .7 0 5 .1)0 0 8 .1/4 8 1.8 5 0 0 .0 7 m 5 m
如下:
(1)确定橡胶垫自由高度
H 0 ( 3.5~4) H 工
H工 h工作 h修磨 t 1mm (5 ~10)mm
H0 36mm
(0.81 7.2)mm
9mm
(2)确定橡胶垫的横截面积
查得橡胶垫预压量在10%~15%时的单位压力为0.5Mpa,
AFX/ p
A363N0726m0m 2 0.5MPa
A 4 ( 5 0 .7 0 5 .2)0 0 4 .2/4 4 4.8 9 0 0 .0 2 m 6 m
冲裁模设计
2. 磨损后刃口尺寸变小的有:2200.52mm,
精度等级为IT14,X取0.5。则
B j ( B m X iΔ n ) 0 /4 ( 2 0 2 .5 0 .5 ) 0 0 .1 2 3 2 .2 0 2 0 .1 6 m 3
冲裁模设计
4.工艺计算: 1)确定排样方式
根据零件形状分析其应采用单直排的排样方式,排 样方式有如下两种。
a)
现选用1500mm×1000mm的钢板,则需计算采用 不同的裁剪方式时,每张板料能出的零件总个数。
冲裁模设计
➢ 裁成宽43.6mm、长1500mm的条料,则一张板材能出的零件
总个数为:
140.3600155.150022 29638
冲裁模设计
5.模具主要零部件的结构设计
(1)凸模:直通式凸模,横销吊装固定。
(2)凹模:外形为矩形,直刃口高度为5mm,4个M8 螺钉和2个φ8销钉。 凹模高度:H K 0 . 3 b 5 3 m 0 1 . 5 m m 6 1 m m 7 凹模壁厚:C ( 1 .5 ~ 2 )H 1 .8 1m 7 3 m m 0m 凹模的总长:L (5 0 2 3)m 0 m 1m 10m 凹模的宽度:B (4 0 2 3)m 0 m 1m 00m 经检查螺孔与销孔间,螺孔、销孔与凹模刃口、
3. 磨损尺寸不变的有:120.22mm 、190.1mm ,则有: C1120.05m 5 m C2 190.02m 5 m
技术要求:凸模刃口按凹模实际刃口尺寸配作,以0.0720.104mm的间隙与凹模配制。
冲裁模设计
e)弹性元件选用与计算
材料较薄,料厚为0.8mm,采用弹性卸料装置,橡胶尺寸计算
冲裁模设计过程实例一
冲裁模设计
1. 冲裁工艺性分析
(1)材料分析 10钢为优质碳素结构钢,具有较好的冲裁成形性能。
(2)结构分析 零件结构简单,左右对称; 外形有多处尖角,建议过渡圆角值为R0.25mm。 零件结构满足冲裁要求。
(3)精度分析 5个尺寸,查表属于IT12,2个未注公差按IT14取值。 普通冲裁满足零件的精度要求。