喷漆车间喷漆生产工艺流程
喷漆车间喷漆生产工艺流程

喷漆车间喷漆生产工艺流程喷漆车间是汽车制造工艺中的一个重要环节,它负责对汽车进行喷涂,赋予汽车漂亮的外观和保护层。
以下是喷漆车间的喷漆生产工艺流程。
1. 表面处理:首先,对汽车的表面进行处理,包括去除油污、灰尘和杂质,以确保喷涂效果。
2. 研磨和填补:采用砂纸和研磨机对汽车表面进行研磨,使其平整光滑。
同时,进行填补工作,补充和修复汽车表面的凹陷和磕碰。
3. 喷底漆:使用底漆喷枪将底漆均匀地喷涂在汽车表面。
底漆能够修复表面的不平整,并提供良好的附着力,使上层涂料牢固。
4. 干燥和打磨:将喷涂的底漆进行烘干,通常使用烤箱进行加热。
之后,使用砂纸对底漆进行打磨,以获得平整的表面。
5. 上色:根据客户的要求,选择合适的涂料颜色,并使用喷枪将颜料均匀地喷涂在汽车表面。
以确保颜色的一致性和整体效果。
6. 清漆:在上色完成后,使用喷枪将清漆喷涂在汽车表面,以增加光泽度并提供保护层。
清漆还能增强涂饰的耐磨性和抗紫外线性能。
7. 干燥和抛光:将喷涂的漆料进行烘干,通常需要一段适当的时间来确保漆料彻底干燥。
之后,使用抛光工具对汽车表面进行抛光,以获得更好的光泽效果。
8. 质量检测:最后,对喷漆完成的汽车进行质量检测,包括颜色一致性、涂层的平整度以及表面的光泽度等等。
只有通过严格的质量检验,才能确保喷漆产品符合标准。
以上是喷漆车间的喷漆生产工艺流程。
通过精心的处理和专业的喷涂技术,喷漆车间能够为汽车提供美观且耐久的外观。
这不仅能提升车辆的价值,还能增加用户的满意度。
喷漆车间是汽车制造工艺中的一个重要环节,它负责对汽车进行喷涂,赋予汽车漂亮的外观和保护层。
喷漆生产工艺流程的每个环节都需要精确和细致的操作,以确保喷涂质量和效果达到最佳。
在表面处理阶段,首当其冲的是对汽车表面进行彻底的清洁。
这是非常关键的一步,因为表面的油污、灰尘和杂质会影响喷涂的附着力和外观效果。
常用的清洁方法包括使用洗车剂和清水清洗汽车表面,使用清洁剂去除顽固的污渍,并使用纤细的砂纸去除表面的瑕疵。
喷漆车间喷漆工艺流程
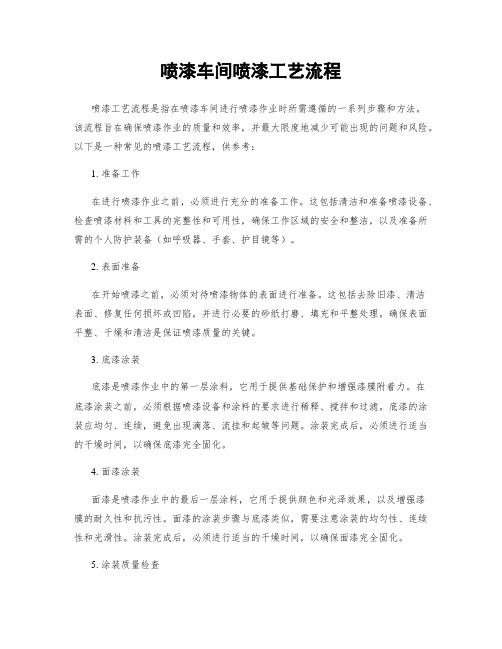
喷漆车间喷漆工艺流程喷漆工艺流程是指在喷漆车间进行喷漆作业时所需遵循的一系列步骤和方法。
该流程旨在确保喷漆作业的质量和效率,并最大限度地减少可能出现的问题和风险。
以下是一种常见的喷漆工艺流程,供参考:1. 准备工作在进行喷漆作业之前,必须进行充分的准备工作。
这包括清洁和准备喷漆设备、检查喷漆材料和工具的完整性和可用性,确保工作区域的安全和整洁,以及准备所需的个人防护装备(如呼吸器、手套、护目镜等)。
2. 表面准备在开始喷漆之前,必须对待喷漆物体的表面进行准备。
这包括去除旧漆、清洁表面、修复任何损坏或凹陷,并进行必要的砂纸打磨、填充和平整处理。
确保表面平整、干燥和清洁是保证喷漆质量的关键。
3. 底漆涂装底漆是喷漆作业中的第一层涂料,它用于提供基础保护和增强漆膜附着力。
在底漆涂装之前,必须根据喷漆设备和涂料的要求进行稀释、搅拌和过滤。
底漆的涂装应均匀、连续,避免出现滴落、流挂和起皱等问题。
涂装完成后,必须进行适当的干燥时间,以确保底漆完全固化。
4. 面漆涂装面漆是喷漆作业中的最后一层涂料,它用于提供颜色和光泽效果,以及增强漆膜的耐久性和抗污性。
面漆的涂装步骤与底漆类似,需要注意涂装的均匀性、连续性和光滑性。
涂装完成后,必须进行适当的干燥时间,以确保面漆完全固化。
5. 涂装质量检查在喷漆作业完成后,必须进行涂装质量检查。
这包括检查漆膜的平整度、光泽度和颜色一致性,检查是否存在漏涂、流挂、起皱、气泡和划痕等问题。
此外,还需要检查涂装表面是否光滑、无瑕疵,并与所需质量标准进行比对。
6. 清洁和维护在喷漆作业完成后,必须进行清洁和维护工作。
这包括清洁喷漆设备、工具和工作区域,以防止漆料和溶剂的积聚和污染。
此外,还需要定期检查和维护喷漆设备,确保其正常运行和安全使用。
以上是喷漆车间喷漆工艺流程的一般步骤和要求。
实际的工艺流程可能会根据不同的喷漆设备、涂料和作业要求而有所变化。
在进行喷漆作业时,务必遵循相关的安全操作规程和环境保护要求,以确保作业的安全性和可持续性。
喷漆车间喷漆工艺流程
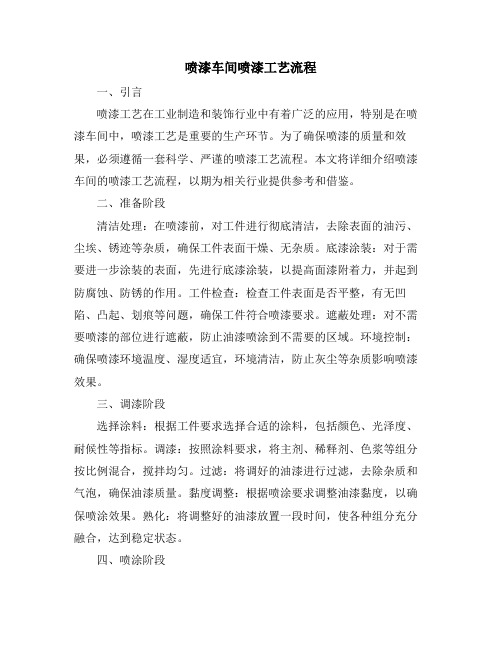
喷漆车间喷漆工艺流程
一、引言
喷漆工艺在工业制造和装饰行业中有着广泛的应用,特别是在喷漆车间中,喷漆工艺是重要的生产环节。
为了确保喷漆的质量和效果,必须遵循一套科学、严谨的喷漆工艺流程。
本文将详细介绍喷漆车间的喷漆工艺流程,以期为相关行业提供参考和借鉴。
二、准备阶段
清洁处理:在喷漆前,对工件进行彻底清洁,去除表面的油污、尘埃、锈迹等杂质,确保工件表面干燥、无杂质。
底漆涂装:对于需要进一步涂装的表面,先进行底漆涂装,以提高面漆附着力,并起到防腐蚀、防锈的作用。
工件检查:检查工件表面是否平整,有无凹陷、凸起、划痕等问题,确保工件符合喷漆要求。
遮蔽处理:对不需要喷漆的部位进行遮蔽,防止油漆喷涂到不需要的区域。
环境控制:确保喷漆环境温度、湿度适宜,环境清洁,防止灰尘等杂质影响喷漆效果。
三、调漆阶段
选择涂料:根据工件要求选择合适的涂料,包括颜色、光泽度、耐候性等指标。
调漆:按照涂料要求,将主剂、稀释剂、色浆等组分按比例混合,搅拌均匀。
过滤:将调好的油漆进行过滤,去除杂质和气泡,确保油漆质量。
黏度调整:根据喷涂要求调整油漆黏度,以确保喷涂效果。
熟化:将调整好的油漆放置一段时间,使各种组分充分融合,达到稳定状态。
四、喷涂阶段
喷枪选择:根据工件形状和涂装要求选择合适的喷枪,确保喷涂均匀、无滴漆。
喷涂设备检查:检查喷枪、气管、油泵等设备是否正常,确保喷涂过程顺利进行。
试喷:在正式喷涂前进行试喷,调整喷涂参数,确保效果符合要求。
面漆喷涂:将调整好的面漆进行喷涂,注意控制喷枪与工件的距离、角度和移动速度,确保涂层均匀、光滑。
喷漆车间喷漆工艺流程
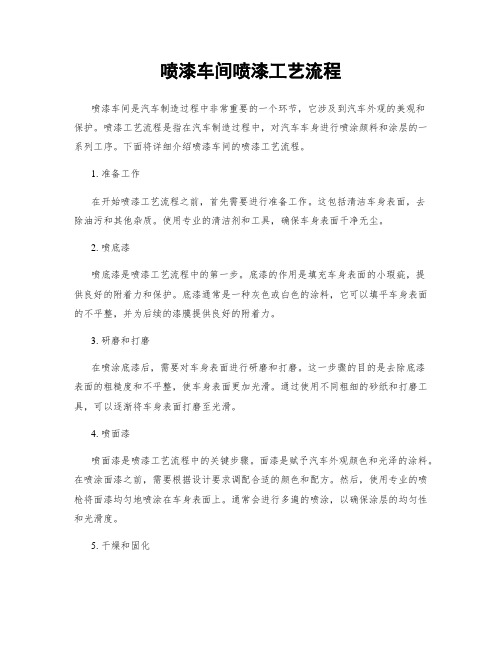
喷漆车间喷漆工艺流程喷漆车间是汽车制造过程中非常重要的一个环节,它涉及到汽车外观的美观和保护。
喷漆工艺流程是指在汽车制造过程中,对汽车车身进行喷涂颜料和涂层的一系列工序。
下面将详细介绍喷漆车间的喷漆工艺流程。
1. 准备工作在开始喷漆工艺流程之前,首先需要进行准备工作。
这包括清洁车身表面,去除油污和其他杂质。
使用专业的清洁剂和工具,确保车身表面干净无尘。
2. 喷底漆喷底漆是喷漆工艺流程中的第一步。
底漆的作用是填充车身表面的小瑕疵,提供良好的附着力和保护。
底漆通常是一种灰色或白色的涂料,它可以填平车身表面的不平整,并为后续的漆膜提供良好的附着力。
3. 研磨和打磨在喷涂底漆后,需要对车身表面进行研磨和打磨。
这一步骤的目的是去除底漆表面的粗糙度和不平整,使车身表面更加光滑。
通过使用不同粗细的砂纸和打磨工具,可以逐渐将车身表面打磨至光滑。
4. 喷面漆喷面漆是喷漆工艺流程中的关键步骤。
面漆是赋予汽车外观颜色和光泽的涂料。
在喷涂面漆之前,需要根据设计要求调配合适的颜色和配方。
然后,使用专业的喷枪将面漆均匀地喷涂在车身表面上。
通常会进行多遍的喷涂,以确保涂层的均匀性和光滑度。
5. 干燥和固化在喷涂完面漆后,需要进行干燥和固化的过程。
这一步骤的目的是使喷涂的漆膜干燥和固化,以确保其耐久性和质量。
干燥和固化的方法可以有多种,包括自然干燥、烘干室和紫外线固化等。
根据不同的喷漆工艺和涂料类型,选择合适的干燥和固化方法。
6. 抛光和润色在干燥和固化后,需要对喷涂的漆膜进行抛光和润色。
这一步骤的目的是使漆膜更加光滑和亮丽。
通过使用抛光机和专业的抛光剂,可以去除漆膜表面的细微瑕疵和划痕,使其达到更高的光泽度。
7. 检查和质量控制在完成喷漆工艺流程后,需要进行检查和质量控制。
这包括检查漆膜的均匀性、光泽度和颜色的一致性。
同时,还需要检查是否存在漆膜起泡、脱落或其他缺陷。
通过严格的质量控制,确保喷漆工艺达到预期的效果和质量标准。
喷漆车间喷漆工艺流程

喷漆车间喷漆工艺流程喷漆车间是汽车创造和修复过程中非常重要的一个环节。
喷漆工艺流程涉及到多个步骤和技术,下面将详细介绍一下标准的喷漆工艺流程。
1. 车辆准备阶段:在喷漆工艺流程开始之前,需要对车辆进行准备工作。
这包括清洁车辆表面,去除旧漆、油脂和灰尘等杂质。
同时,检查车辆表面是否有凹陷、划痕或者其他损坏,需要进行修复。
2. 面层准备:在喷漆之前,需要对车辆表面进行面层准备。
这包括填充和研磨。
首先,使用填充剂填充凹陷和划痕,使表面平整。
然后,使用砂纸和砂轮对填充的部份进行研磨,以确保表面光滑。
3. 底漆喷涂:底漆是喷漆工艺中的第一层涂料,用于保护车身并提供漆面附着力。
首先,需要将底漆与稀释剂混合,以达到适当的粘度。
然后,使用喷枪将底漆均匀地喷涂在车身上。
喷涂完成后,需要等待底漆干燥。
4. 中漆喷涂:中漆是喷漆工艺中的第二层涂料,用于提供颜色和外观效果。
中漆的选择根据客户要求和车辆类型来确定。
中漆的喷涂过程与底漆类似,需要将中漆与稀释剂混合,并使用喷枪均匀地喷涂在车身上。
5. 面漆喷涂:面漆是喷漆工艺中的最后一层涂料,用于提供光泽和保护。
面漆的选择也根据客户要求和车辆类型来确定。
面漆的喷涂过程与底漆和中漆类似,需要将面漆与稀释剂混合,并使用喷枪均匀地喷涂在车身上。
6. 干燥和抛光:喷涂完成后,需要等待涂层干燥。
干燥时间根据涂料类型和环境条件而定。
一旦涂层干燥,可以进行抛光工作。
抛光可以提高涂层的光泽度和平滑度,使车身外观更加完美。
7. 检验和质量控制:在喷漆工艺流程的最后阶段,需要对喷漆质量进行检验和控制。
检查涂层是否均匀、无气泡、无划痕和无色差。
同时,还需要检查涂层的附着力和耐久性。
如果发现任何问题,需要进行修复和调整。
以上是标准的喷漆工艺流程。
每一个步骤都需要专业的技术和经验,以确保喷漆质量和持久性。
喷漆车间通常配备先进的设备和工具,以提供高质量的喷漆服务。
喷漆车间喷漆工艺流程

喷漆车间喷漆工艺流程喷漆车间是汽车制造过程中不可或缺的一环,喷漆工艺流程是汽车外观涂装的重要步骤。
本文将详细介绍喷漆车间的喷漆工艺流程,包括准备工作、喷漆前处理、喷漆操作、烘干和质检等环节。
一、准备工作1. 确定喷漆车间的喷漆区域,确保环境干净、通风良好,并配备必要的安全设施。
2. 检查喷漆设备和工具的完好性,确保喷枪、喷漆机等设备能正常工作。
3. 准备所需的喷漆材料,包括底漆、面漆、清漆等,并按照配方准确称量。
二、喷漆前处理1. 清洁车身表面,去除油污、灰尘和其他杂质,以确保漆膜附着力。
2. 进行车身修复,包括填补凹陷、修复划痕等,使车身表面平整。
3. 进行打磨处理,使用砂纸、打磨机等工具,将车身表面磨光,去除旧漆和凸起的部分。
三、喷漆操作1. 应用底漆,使用喷枪均匀喷涂在车身表面,形成底漆层。
底漆能提高漆膜的附着力和耐候性。
2. 应用面漆,根据客户要求或标准配方,使用喷枪均匀喷涂在底漆层上,形成面漆层。
面漆决定了汽车的颜色和光泽。
3. 进行涂装控制,确保喷漆的厚度、均匀性和质量符合要求。
可使用涂厚测量仪、喷漆面板等工具进行检测和调整。
四、烘干1. 将喷漆完成的车辆送入烘干室,通过控制温度和湿度,加速漆膜的干燥和固化。
2. 烘干时间根据喷漆材料和环境条件而定,通常需要几小时到几天不等。
五、质检1. 对喷漆完成的车辆进行外观检查,包括颜色、光泽、涂层厚度等方面的评估。
2. 进行涂层附着力测试,使用剥离测试仪等工具,评估漆膜与车身的附着程度。
3. 检查漆膜的平整度和光洁度,排除可能存在的缺陷和瑕疵。
六、返修和维护1. 如果发现质量问题或不符合要求,需要进行返修和修复。
可以使用打磨、喷漆等方法进行修补。
2. 定期进行设备和工具的维护保养,确保其正常运行和使用寿命。
以上是喷漆车间的喷漆工艺流程的详细介绍。
在实际操作中,喷漆工艺流程可能会根据不同的汽车制造商、产品要求和工艺水平有所差异。
然而,严格按照标准的喷漆工艺流程进行操作,能够保证喷漆质量和外观效果的一致性,提高汽车的质量和市场竞争力。
喷涂的工艺流程(3篇)
一、前言喷涂是一种将涂料均匀涂覆在物体表面的工艺,广泛应用于汽车、建筑、家具、金属制品等行业。
喷涂工艺具有施工简便、涂层均匀、附着力强等优点,能够提高产品的外观质量和使用寿命。
本文将详细介绍喷涂工艺的流程,以供相关从业人员参考。
二、喷涂工艺流程1. 准备工作(1)材料准备:根据产品要求,选择合适的涂料、固化剂、稀释剂等材料。
涂料应符合国家相关标准,确保产品质量。
(2)设备准备:检查喷涂设备是否正常,包括喷枪、喷壶、搅拌器、空气压缩机等。
(3)场地准备:确保喷涂场地通风良好,无灰尘、油污等杂质,地面平整。
2. 喷涂前的表面处理(1)清洗:使用溶剂或水将物体表面的油污、灰尘、锈蚀等杂质清洗干净。
(2)打磨:对物体表面的凹凸不平、焊缝、焊点等部位进行打磨,提高涂层的附着力。
(3)磷化:对金属表面进行磷化处理,提高涂层的耐腐蚀性。
3. 喷涂作业(1)涂装前的准备工作:将涂料、固化剂、稀释剂按比例搅拌均匀,确保涂料均匀。
(2)喷涂方法:根据产品形状、尺寸和涂料特性选择合适的喷涂方法,如空气喷涂、高压无气喷涂等。
(3)喷涂参数:根据涂料特性、物体表面及环境温度等因素调整喷涂压力、喷枪距离、喷涂速度等参数。
(4)喷涂操作:手持喷枪,均匀地喷涂涂料,避免漏喷、流淌、堆积等现象。
(1)自然固化:将喷涂后的物体放置在通风、干燥的环境中,待涂料自然固化。
(2)加热固化:对需要快速固化的物体进行加热处理,提高固化速度。
5. 检查与修整(1)外观检查:检查涂层颜色、光泽、厚度、平整度等是否符合要求。
(2)附着力检查:使用专用仪器检测涂层与物体表面的附着力。
(3)修整:对不符合要求的涂层进行修整,如打磨、补涂等。
6. 包装与储存(1)包装:将完成喷涂的物体进行包装,防止涂层受到污染。
(2)储存:将包装好的物体存放在干燥、通风、避光的场所,避免阳光直射和潮湿。
三、喷涂工艺注意事项1. 涂料选择:根据产品要求、施工环境等因素选择合适的涂料。
喷漆车间喷漆工艺流程
喷漆车间喷漆工艺流程喷漆车间是一个专门进行汽车喷漆的工作区域,其工艺流程包括准备工作、喷涂准备、喷涂操作和喷涂后处理等步骤。
以下是喷漆车间喷漆工艺流程的详细描述:1. 准备工作在开始喷涂之前,需要对车间进行准备工作,包括清洁车间、准备喷漆设备和材料等。
首先,清洁车间的地面和墙壁,确保没有灰尘和杂质。
然后,检查喷涂设备,确保其正常工作并进行必要的维护。
最后,准备喷漆所需的材料,如底漆、面漆、稀释剂等。
2. 喷涂准备在进行喷涂之前,需要对车辆进行准备工作,包括清洁、遮盖和打磨等。
首先,清洁车辆的表面,去除油脂、污垢和旧漆。
然后,使用塑料薄膜或纸张覆盖车辆的非喷涂部分,以防止喷漆溅到其他区域。
最后,对需要喷涂的部位进行打磨,以获得光滑的表面。
3. 喷涂操作在进行喷涂操作时,需要按照一定的顺序和技术进行。
首先,使用底漆对车辆进行底涂,以提供良好的附着力和耐久性。
底漆需要均匀地喷涂在车辆表面上,并确保没有漏涂或滴涂。
然后,等待底漆干燥后,使用面漆进行面涂。
面漆需要均匀地喷涂在底漆上,并确保没有出现色差或涂层不均匀的情况。
在喷涂过程中,需要控制好喷涂距离和喷涂厚度,以获得理想的喷涂效果。
4. 喷涂后处理在喷涂完成后,需要进行喷涂后处理工作,以保证喷涂效果和质量。
首先,等待喷涂的漆面干燥,通常需要一定的时间。
然后,对喷涂的漆面进行检查,确保没有出现色差、气泡或涂层不均匀等问题。
如果有需要,可以进行修复和调整。
最后,对喷涂的车辆进行整理和清洁,以使其焕然一新。
总结:喷漆车间的喷漆工艺流程包括准备工作、喷涂准备、喷涂操作和喷涂后处理等步骤。
准备工作包括清洁车间、准备喷漆设备和材料。
喷涂准备包括清洁、遮盖和打磨车辆。
喷涂操作需要按照顺序和技术进行底涂和面涂。
喷涂后处理包括干燥、检查、修复和清洁车辆。
通过严格执行这些步骤,可以确保喷漆车间的喷涂工艺流程达到高质量和理想效果。
喷漆车间喷漆工艺流程
喷漆车间喷漆工艺流程一、工艺流程概述喷漆车间是汽车创造工厂中的重要环节,主要负责对汽车车身进行喷涂,以保护车身表面并提升外观质量。
喷漆工艺流程是一个复杂而精细的过程,包括准备工作、底漆喷涂、面漆喷涂和涂装后处理等环节。
二、准备工作1. 车身检查:检查车身表面是否有划痕、凹陷等瑕疵,如有需要进行修复。
2. 清洁车身:使用清洁剂和高压水枪清洗车身表面,去除尘土、油脂等污物。
3. 车身遮盖:使用塑料薄膜和胶带将车身上的玻璃、灯具等部件进行遮盖,以防止喷漆时的溅射。
三、底漆喷涂1. 底漆准备:将底漆倒入喷漆枪的喷漆杯中,并根据需要添加稀释剂和固化剂,搅拌均匀。
2. 底漆喷涂:将喷漆枪对准车身表面,以均匀的速度、距离和喷涂角度进行喷涂,保证底漆均匀覆盖整个车身。
3. 底漆干燥:将喷涂完的车身放入烤房中进行干燥,时间和温度根据底漆的要求进行控制。
四、面漆喷涂1. 面漆准备:将面漆倒入喷漆枪的喷漆杯中,并根据需要添加稀释剂和固化剂,搅拌均匀。
2. 面漆喷涂:将喷漆枪对准车身表面,以均匀的速度、距离和喷涂角度进行喷涂,保证面漆均匀覆盖整个车身。
3. 面漆干燥:将喷涂完的车身放入烤房中进行干燥,时间和温度根据面漆的要求进行控制。
五、涂装后处理1. 研磨抛光:使用研磨机和抛光机对车身进行研磨和抛光,以去除喷漆过程中产生的瑕疵温和泡。
2. 车身组装:将喷漆完的车身进行组装,包括安装玻璃、灯具、车标等部件。
3. 质量检验:对喷漆后的车身进行质量检验,检查漆面的平整度、光泽度和颜色是否符合要求。
4. 包装出库:将合格的车身进行包装,并送往下一个生产环节或者出库。
六、安全注意事项1. 喷漆车间应保持良好的通风系统,以排除喷漆过程中产生的有害气体和粉尘。
2. 喷漆工作人员应佩戴防护用品,如口罩、防护眼镜、防护服等,以保护自身安全。
3. 喷漆车间应设置灭火器和紧急停电装置,以应对突发情况。
4. 喷漆工作人员需严格遵守操作规程,禁止吸烟、明火和饮食等行为。
喷漆车间工艺流程
喷漆车间工艺流程喷漆车间工艺流程喷漆车间是汽车生产过程中非常关键的一个环节,它对车辆的外观质量和保护作用起着重要的作用。
下面将介绍一下喷漆车间的工艺流程。
首先,喷漆车间的准备工作非常重要。
在喷漆之前,首先需要准备好喷漆设备和材料。
喷漆设备包括喷漆枪、空压机、涂装设备以及喷漆室等。
而喷漆材料则包括底漆、面漆、清漆等。
这些设备和材料的准备需要根据车辆的类型和需求来确定。
接下来是喷漆车间的准备工作。
首先,需要对车辆进行彻底清洗,以确保车身的表面没有灰尘、沙尘等杂质。
然后,需要对车身进行研磨,以去除旧漆和划痕,使车身表面更加光滑。
在研磨过程中,需要使用不同粗细的砂纸,根据需要进行多次研磨,直到车身表面完全光滑。
准备工作完成后,就可以进行喷漆了。
首先是进行底漆的喷涂。
底漆是为了增强漆膜的附着力和防腐性能,它可以填平车身表面的不平整,并形成一层坚硬且光滑的底漆膜。
底漆一般需要进行两次涂装,第一次涂装时需要进行喷灰处理,以确保车身表面光滑无瑕疵;第二次涂装则是为了增强底漆膜的厚度和坚硬度。
完成底漆喷涂后,就可以进行面漆的喷涂了。
面漆是车身最外层的漆膜,它直接影响到车辆的颜色和光泽度。
喷涂面漆时,需要根据车辆的颜色要求和喷涂方式来选择相应的面漆。
喷涂面漆时,需要进行多次喷涂,每次喷涂后都需要进行10-15分钟的干燥时间。
而且在喷涂时,需要采取遮挡措施,以避免漆雾污染周围环境。
最后是清漆的涂装。
清漆是为了保护面漆,并增加其光亮度和光泽度。
清漆喷涂时,需要进行两次涂装,以增加清漆膜的厚度和光滑度。
在喷涂完清漆后,需要进行一段时间的干燥,以确保清漆膜完全固化。
整个喷漆车间的工艺流程就是这样,从准备工作到喷涂的不同环节,每一步都需要严格控制和细致操作。
只有如此,才能保证汽车喷漆工艺的质量和效果。
通过科学的工艺流程,能够使汽车外观更加美观、耐用,为消费者提供更好的驾驶体验。
- 1、下载文档前请自行甄别文档内容的完整性,平台不提供额外的编辑、内容补充、找答案等附加服务。
- 2、"仅部分预览"的文档,不可在线预览部分如存在完整性等问题,可反馈申请退款(可完整预览的文档不适用该条件!)。
- 3、如文档侵犯您的权益,请联系客服反馈,我们会尽快为您处理(人工客服工作时间:9:00-18:30)。
喷漆车间喷漆工艺流程一、除油1、去除黑色金属工件在生产过程中表面的油污,用槽浸法。
碱液清洗配方:氢氧化钠4%、磷酸钠4%、磷酸三钠4%、OP-10乳化液0.3%、温度90~95℃,处理时间5~8分钟。
处理后检查方法:水洗后用刷帚刷,目测油污是否去净。
2、去除有色金属工件表面的油污,用槽浸法。
采用KL-13型除油除锈添加剂处理(该添加剂为白色粉末),使用浓度:兑水比例2%,温度大于5℃(如加温处理速度加快),时间5~10分钟,槽液PH值:7。
3、塑料制品的表面除油,用槽浸法。
选用KL-16型脱腊除油粉,使用浓度:兑水比例5%,温度40~65℃,时间5~10分钟。
二、清洗(除油后用水清洗)三、除锈采用酸性除锈,去除钢铁表面的锈垢,用槽浸法。
酸洗除锈液配方:浓度31%的工业盐酸、缓蚀剂3%,温度:常温。
处理时间3~8分钟,处理后检查方法:水洗后目测是否有锈垢存在。
四、清洗(除锈后用水清洗)五、表调用于磷化前的表面处理,用槽浸法(表调剂为白色粉末)。
配槽液时按每1~3公斤/吨的用量慢慢添加,搅拌使其溶解。
表调剂的工作条件为PH值7.5~9.5,温度:常温,时间半分钟。
六、磷化用锌系磷化液使钢铁表面磷化,用槽浸法。
WF磷化剂分为:A剂——配槽剂,B剂——补加剂,C剂——促进剂。
1、槽液配制:槽内加水3/4体积,按每25~30公斤/吨的量加入A剂,然后再添加用热水溶解的氢氧化钠(按每0.7公斤/吨的用量),最后加水至工作液面确认酸度。
在即将开始磷化时,按每0.5~0.7公斤/吨的量加入C剂,搅拌均匀待用。
2、使用工艺参数:总酸度18~35点,游离酸度0.5~1.5点,促进剂2~3点,温度35~45℃,浸磷时间5~10分钟,检查方法:水洗、干燥后目测磷化膜应呈瓦灰色、结晶细致、无斑点、以及未磷化到的部位无氧化物等固体沉积物残留于表面,磷化后水洗应彻底,清洗后应迅速干燥。
3、磷化液管理:磷化液连续使用后总酸度上升可用水稀释,总酸度下降时,按每1.6公斤/吨补加B剂可上升1点。
游离酸度上升时按每0.4公斤/吨加入氢氧化钠可降游离酸度1点,游离酸度下降可按每6公斤/吨加入B剂,游离酸度可上升1点。
槽液温度过低或C 剂添加过多或B剂补加不足,游离酸度可能降到0.4点以下,出现这种情况时要按每0.9公斤/吨添加B剂,游离酸度上升0.1点,当C剂添加过多产生彩色膜时,可搅动或加热让其加快自然挥发。
七、清洗(磷化后用水清洗)八、干燥(磷化、清洗后使待喷漆工件干燥)九、喷涂喷涂前必须做好以下几项工作:①选择涂料的品种②检查涂料的性能③充分搅匀涂料④调整涂料粘度⑤涂料净化过滤⑥涂料颜色调整喷涂时应根据被喷工件选择合适的涂料以及适当的粘度,要根据涂料的种类、空气压力、喷嘴的大小以及被喷面的需要量来定。
①喷嘴口径为0.5mm~1.8mm②供给喷枪的空气压力一般为0.3~0.6Mpa③喷嘴与被喷面的距离一般以20~30cm为宜④喷出漆流的方向应尽量垂直于物体表面⑤操作时每一喷涂条带的边缘应当重叠在前一已喷好的条带边缘上(以重叠1/3为宜),喷枪的运动速度应保持均匀一致,不可时快时慢。
十、干燥1、一般ABS、PC等塑料自干漆烘烤温度为55~65℃,时间为30~35分钟。
2、烘干聚合型涂料,如氨基漆、丙稀酸漆、环氧树脂漆等,一般烘烤温度为130~140℃,(丙烯酸漆需静止放上10分钟再进行烘烤)时间30~35分钟。
十一、喷涂膜质量检查1、检查漆膜的干燥程度,目测或用刀片刮划检查漆膜的厚度。
用三菱铅笔划试硬度,应在3H左右。
2、检查漆膜的附着力,采用11号手术刀片进行划格试验。
试验时,将刀片平面垂直于试验表面,用力均匀,进度平稳,纵横垂直切割4条划痕至底材表面,形成9个小方格,每个小方格的面积为1mm2,用刷帚沿方格阵两对角线方向轻轻地往返5次,观察漆膜的脱落情况。
非破坏性的附着力测定方法:可用压敏胶的胶带,将它胶粘在漆膜表面,然后用手拉开以检查其附着力。
3、检查涂层的颜色、光泽和表面状态。
颜色和光泽目测应符合标准要求,用测光仪测定光泽。
检查漆面应无沾附砂料或灰尘,光色是否均匀,无皱纹、气泡、裂痕、胶皮、流挂、斑点、针孔、渗色或缩孔现象。
喷漆车间喷漆工艺流程一、除油1、去除黑色金属工件在生产过程中表面的油污,用槽浸法。
碱液清洗配方:氢氧化钠4%、磷酸钠4%、磷酸三钠4%、OP-10乳化液0.3%、温度90~95℃,处理时间5~8分钟。
处理后检查方法:水洗后用刷帚刷,目测油污是否去净。
2、去除有色金属工件表面的油污,用槽浸法。
采用KL-13型除油除锈添加剂处理(该添加剂为白色粉末),使用浓度:兑水比例2%,温度大于5℃(如加温处理速度加快),时间5~10分钟,槽液PH值:7。
3、塑料制品的表面除油,用槽浸法。
选用KL-16型脱腊除油粉,使用浓度:兑水比例5%,温度40~65℃,时间5~10分钟。
二、清洗(除油后用水清洗)三、除锈采用酸性除锈,去除钢铁表面的锈垢,用槽浸法。
酸洗除锈液配方:浓度31%的工业盐酸、缓蚀剂3%,温度:常温。
处理时间3~8分钟,处理后检查方法:水洗后目测是否有锈垢存在。
四、清洗(除锈后用水清洗)五、表调用于磷化前的表面处理,用槽浸法(表调剂为白色粉末)。
配槽液时按每1~3公斤/吨的用量慢慢添加,搅拌使其溶解。
表调剂的工作条件为PH值7.5~9.5,温度:常温,时间半分钟。
六、磷化用锌系磷化液使钢铁表面磷化,用槽浸法。
WF磷化剂分为:A剂——配槽剂,B剂——补加剂,C剂——促进剂。
1、槽液配制:槽内加水3/4体积,按每25~30公斤/吨的量加入A剂,然后再添加用热水溶解的氢氧化钠(按每0.7公斤/吨的用量),最后加水至工作液面确认酸度。
在即将开始磷化时,按每0.5~0.7公斤/吨的量加入C剂,搅拌均匀待用。
2、使用工艺参数:总酸度18~35点,游离酸度0.5~1.5点,促进剂2~3点,温度35~45℃,浸磷时间5~10分钟,检查方法:水洗、干燥后目测磷化膜应呈瓦灰色、结晶细致、无斑点、以及未磷化到的部位无氧化物等固体沉积物残留于表面,磷化后水洗应彻底,清洗后应迅速干燥。
3、磷化液管理:磷化液连续使用后总酸度上升可用水稀释,总酸度下降时,按每1.6公斤/吨补加B剂可上升1点。
游离酸度上升时按每0.4公斤/吨加入氢氧化钠可降游离酸度1点,游离酸度下降可按每6公斤/吨加入B剂,游离酸度可上升1点。
槽液温度过低或C 剂添加过多或B剂补加不足,游离酸度可能降到0.4点以下,出现这种情况时要按每0.9公斤/吨添加B剂,游离酸度上升0.1点,当C剂添加过多产生彩色膜时,可搅动或加热让其加快自然挥发。
七、清洗(磷化后用水清洗)八、干燥(磷化、清洗后使待喷漆工件干燥)九、喷涂喷涂前必须做好以下几项工作:①选择涂料的品种②检查涂料的性能③充分搅匀涂料④调整涂料粘度⑤涂料净化过滤⑥涂料颜色调整喷涂时应根据被喷工件选择合适的涂料以及适当的粘度,要根据涂料的种类、空气压力、喷嘴的大小以及被喷面的需要量来定。
①喷嘴口径为0.5mm~1.8mm②供给喷枪的空气压力一般为0.3~0.6Mpa③喷嘴与被喷面的距离一般以20~30cm为宜④喷出漆流的方向应尽量垂直于物体表面⑤操作时每一喷涂条带的边缘应当重叠在前一已喷好的条带边缘上(以重叠1/3为宜),喷枪的运动速度应保持均匀一致,不可时快时慢。
十、干燥1、一般ABS、PC等塑料自干漆烘烤温度为55~65℃,时间为30~35分钟。
2、烘干聚合型涂料,如氨基漆、丙稀酸漆、环氧树脂漆等,一般烘烤温度为130~140℃,(丙烯酸漆需静止放上10分钟再进行烘烤)时间30~35分钟。
十一、喷涂膜质量检查1、检查漆膜的干燥程度,目测或用刀片刮划检查漆膜的厚度。
用三菱铅笔划试硬度,应在3H左右。
2、检查漆膜的附着力,采用11号手术刀片进行划格试验。
试验时,将刀片平面垂直于试验表面,用力均匀,进度平稳,纵横垂直切割4条划痕至底材表面,形成9个小方格,每个小方格的面积为1mm2,用刷帚沿方格阵两对角线方向轻轻地往返5次,观察漆膜的脱落情况。
非破坏性的附着力测定方法:可用压敏胶的胶带,将它胶粘在漆膜表面,然后用手拉开以检查其附着力。
3、检查涂层的颜色、光泽和表面状态。
颜色和光泽目测应符合标准要求,用测光仪测定光泽。
检查漆面应无沾附砂料或灰尘,光色是否均匀,无皱纹、气泡、裂痕、胶皮、流挂、斑点、针孔、渗色或缩孔现象。
喷漆车间喷漆工艺流程一、除油1、去除黑色金属工件在生产过程中表面的油污,用槽浸法。
碱液清洗配方:氢氧化钠4%、磷酸钠4%、磷酸三钠4%、OP-10乳化液0.3%、温度90~95℃,处理时间5~8分钟。
处理后检查方法:水洗后用刷帚刷,目测油污是否去净。
2、去除有色金属工件表面的油污,用槽浸法。
采用KL-13型除油除锈添加剂处理(该添加剂为白色粉末),使用浓度:兑水比例2%,温度大于5℃(如加温处理速度加快),时间5~10分钟,槽液PH值:7。
3、塑料制品的表面除油,用槽浸法。
选用KL-16型脱腊除油粉,使用浓度:兑水比例5%,温度40~65℃,时间5~10分钟。
二、清洗(除油后用水清洗)三、除锈采用酸性除锈,去除钢铁表面的锈垢,用槽浸法。
酸洗除锈液配方:浓度31%的工业盐酸、缓蚀剂3%,温度:常温。
处理时间3~8分钟,处理后检查方法:水洗后目测是否有锈垢存在。
四、清洗(除锈后用水清洗)五、表调用于磷化前的表面处理,用槽浸法(表调剂为白色粉末)。
配槽液时按每1~3公斤/吨的用量慢慢添加,搅拌使其溶解。
表调剂的工作条件为PH值7.5~9.5,温度:常温,时间半分钟。
六、磷化用锌系磷化液使钢铁表面磷化,用槽浸法。
WF磷化剂分为:A剂——配槽剂,B剂——补加剂,C剂——促进剂。
1、槽液配制:槽内加水3/4体积,按每25~30公斤/吨的量加入A剂,然后再添加用热水溶解的氢氧化钠(按每0.7公斤/吨的用量),最后加水至工作液面确认酸度。
在即将开始磷化时,按每0.5~0.7公斤/吨的量加入C剂,搅拌均匀待用。
2、使用工艺参数:总酸度18~35点,游离酸度0.5~1.5点,促进剂2~3点,温度35~45℃,浸磷时间5~10分钟,检查方法:水洗、干燥后目测磷化膜应呈瓦灰色、结晶细致、无斑点、以及未磷化到的部位无氧化物等固体沉积物残留于表面,磷化后水洗应彻底,清洗后应迅速干燥。
3、磷化液管理:磷化液连续使用后总酸度上升可用水稀释,总酸度下降时,按每1.6公斤/吨补加B剂可上升1点。
游离酸度上升时按每0.4公斤/吨加入氢氧化钠可降游离酸度1点,游离酸度下降可按每6公斤/吨加入B剂,游离酸度可上升1点。
槽液温度过低或C。