水泥厂工艺设计概况修订稿
日产4000吨水泥熟料工厂设计
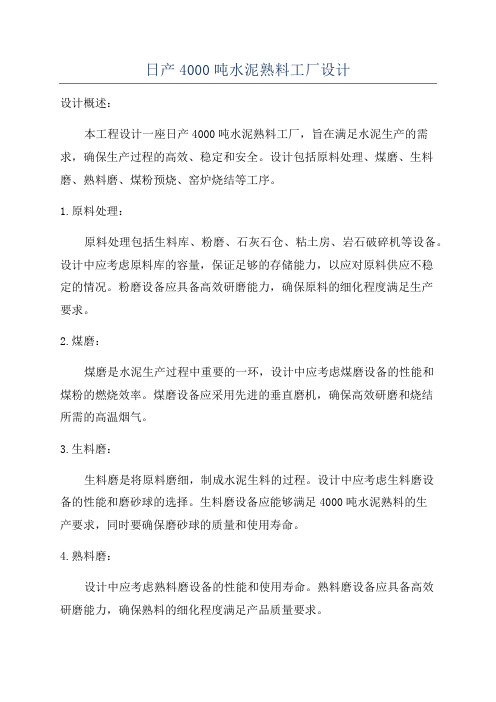
日产4000吨水泥熟料工厂设计设计概述:本工程设计一座日产4000吨水泥熟料工厂,旨在满足水泥生产的需求,确保生产过程的高效、稳定和安全。
设计包括原料处理、煤磨、生料磨、熟料磨、煤粉预烧、窑炉烧结等工序。
1.原料处理:原料处理包括生料库、粉磨、石灰石仓、粘土房、岩石破碎机等设备。
设计中应考虑原料库的容量,保证足够的存储能力,以应对原料供应不稳定的情况。
粉磨设备应具备高效研磨能力,确保原料的细化程度满足生产要求。
2.煤磨:煤磨是水泥生产过程中重要的一环,设计中应考虑煤磨设备的性能和煤粉的燃烧效率。
煤磨设备应采用先进的垂直磨机,确保高效研磨和烧结所需的高温烟气。
3.生料磨:生料磨是将原料磨细,制成水泥生料的过程。
设计中应考虑生料磨设备的性能和磨砂球的选择。
生料磨设备应能够满足4000吨水泥熟料的生产要求,同时要确保磨砂球的质量和使用寿命。
4.熟料磨:设计中应考虑熟料磨设备的性能和使用寿命。
熟料磨设备应具备高效研磨能力,确保熟料的细化程度满足产品质量要求。
5.煤粉预烧:煤粉预烧是水泥熟料工厂的重要工序。
在设计中应考虑煤粉预烧设备的性能和热能利用率。
煤粉预烧设备应能够稳定地完成预烧过程,并满足熟料窑炉的需求。
6.窑炉烧结:窑炉烧结是将熟料烧结成水泥的关键过程。
设计中应考虑窑炉的尺寸、结构和热能利用率。
窑炉应具备高温下的稳定运行能力,并确保高质量的烧结过程。
7.环保设施:在设计中应考虑环保设施的设置,确保工厂的环境保护和资源利用。
环保设施包括粉尘收集装置、烟气治理装置等,以达到国家和地方的环保标准。
8.自动化控制系统:工厂的自动化控制系统应实现全生产线的自动控制和监测。
通过PLC、DCS等自动化设备,实现工厂的高效运行和可持续发展。
总结:以上是一座日产4000吨水泥熟料工厂设计的简要概述。
设计中需要考虑原料处理、煤磨、生料磨、熟料磨、煤粉预烧、窑炉烧结等工序,并配置相应的设备和环保措施。
通过合理的设计和高效的设备,确保生产过程的稳定、高效和安全,提高产品质量和工厂的竞争力。
水泥制品生产工艺改善与控制技术研究

水泥制品生产工艺改善与控制技术研究一、水泥制品生产工艺改善的必要性水泥制品作为基础建材,在国民经济中占有重要地位。
随着经济发展和人民生活水平提高,对建筑美观度和品质的需求也逐渐增强。
传统的水泥制品生产工艺已经无法满足新时代的要求,因此需要对其生产工艺进行改进和优化,以提高水泥制品的质量和生产效率。
二、水泥制品生产工艺改善的途径1. 原材料的优化选择水泥制品生产中,原材料的质量和配比是影响产品质量的重要原因。
因此,对原材料进行优化选择,选择高品质的天然石材或工业废渣作为原材料,严格控制配比,能够有效提高产品质量和减少生产成本。
2. 精细加工及工艺流程的优化在水泥制品生产中,通过优化工艺流程和提高加工精度来改善产品质量。
例如,在制管过程中,采用高效的管机设备和专业的数控加工系统,使管子的强度和尺寸精度得到提高,从而提高产品的质量。
3. 先进设备的应用随着科技的发展,水泥制品生产设备也得到了不断的更新换代。
先进设备的应用,能够实现自动化生产,并且能够大幅降低操作成本和提高产品质量。
三、水泥制品生产控制技术1. 温度控制技术水泥制品加工过程中,粘土需要在特定的温度下进行加工。
因此,掌握温度控制技术可以有效提高产品的质量。
在定制水泥制品加工中,为了适应不同的加工条件,需要对温度控制系统进行调整。
控制系统需要身体热胀冷缩等温度变化,维持粘土在合适的温度下进行加工。
2. 湿度控制技术水泥制品生产过程中,湿度的控制也是一个非常关键的环节。
如果湿度过高或过低,都会影响产品的质量。
因此,掌握湿度控制技术,控制加工环境的湿度保持在正常范围内,也是非常重要的。
3. 产品质量检测技术产品质量检测技术是保障产品质量的重要手段。
通过建立科学规范的质量检测流程,对制品进行严格的检测,确保产品符合国家和行业标准。
四、结论随着经济发展和技术创新,水泥制品生产工艺和控制技术也在不断升级。
通过对原材料的优化选择、精细加工和工艺流程的优化及先进设备的应用,能够提高产品的质量和生产效率。
水泥生产工艺的设计【整理精品范本】
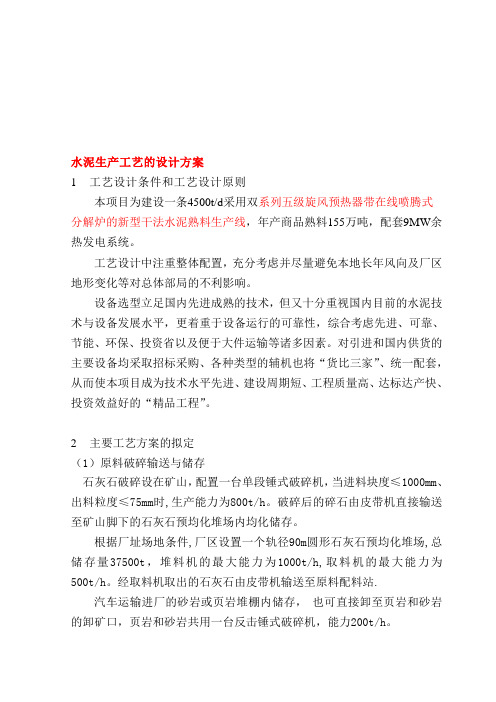
水泥生产工艺的设计方案1 工艺设计条件和工艺设计原则本项目为建设一条4500t/d采用双系列五级旋风预热器带在线喷腾式分解炉的新型干法水泥熟料生产线,年产商品熟料155万吨,配套9MW余热发电系统。
工艺设计中注重整体配置,充分考虑并尽量避免本地长年风向及厂区地形变化等对总体部局的不利影响。
设备选型立足国内先进成熟的技术,但又十分重视国内目前的水泥技术与设备发展水平,更着重于设备运行的可靠性,综合考虑先进、可靠、节能、环保、投资省以及便于大件运输等诸多因素。
对引进和国内供货的主要设备均采取招标采购、各种类型的辅机也将“货比三家”、统一配套,从而使本项目成为技术水平先进、建设周期短、工程质量高、达标达产快、投资效益好的“精品工程”。
2 主要工艺方案的拟定(1)原料破碎输送与储存石灰石破碎设在矿山,配置一台单段锤式破碎机,当进料块度≤1000mm、出料粒度≤75mm时,生产能力为800t/h。
破碎后的碎石由皮带机直接输送至矿山脚下的石灰石预均化堆场内均化储存。
根据厂址场地条件,厂区设置一个轨径90m圆形石灰石预均化堆场,总储存量37500t,堆料机的最大能力为1000t/h,取料机的最大能力为500t/h。
经取料机取出的石灰石由皮带机输送至原料配料站.汽车运输进厂的砂岩或页岩堆棚内储存,也可直接卸至页岩和砂岩的卸矿口,页岩和砂岩共用一台反击锤式破碎机,能力200t/h。
钢渣或铁矿石尾矿进厂粒度≤40mm,无需破碎。
破碎后的页岩和砂岩由胶带输送机送至辅助原料长型预均化堆场,侧式悬臂堆料机的堆料能力400t/h(与原煤共用一台堆料机),侧式刮板取料机的能力110t/h。
进厂钢渣或铁矿石尾矿堆于堆棚内储存,铲车取料后由皮带机直接送至原料配料站。
原料配料站设石灰石、页岩、砂岩及铁矿石尾矿或钢渣四个仓。
(2)原煤卸车输送与储存进厂原煤堆于原煤堆棚内储存,铲车取料送入原煤预均化堆场的进料皮带机。
原煤和辅助原料共用一台堆料机。
水泥工艺设计

水泥工艺设计一、前期准备1.1 原材料采购水泥生产的原材料主要包括石灰石、粘土、铁矿石和煤等。
在采购原材料时,要注重品质、价格和供货周期等方面的考虑。
1.2 设备采购水泥生产需要使用各种设备,如球磨机、旋转窑、冷却机等。
在采购设备时,要根据生产规模和技术要求进行选择。
1.3 土地选址和环评审批水泥生产需要选取适宜的土地,并进行环境影响评价审批,以确保生产过程对环境的影响最小化。
二、原材料处理2.1 石灰石的处理将采集到的石灰石送入颚式破碎机进行初步粉碎,再送入圆锥式细碎机进行细碎,最后通过振动筛分离出所需颗粒大小的物料。
2.2 粘土的处理将采集到的粘土送入圆盘式制粒机进行制粒,然后送入回转窑干燥,并通过振动筛分离出所需颗粒大小的物料。
2.3 铁矿石的处理将采集到的铁矿石送入颚式破碎机进行初步粉碎,再送入圆锥式细碎机进行细碎,最后通过振动筛分离出所需颗粒大小的物料。
2.4 煤的处理将采集到的煤送入颚式破碎机进行初步粉碎,然后送入球磨机进行细碎,并通过振动筛分离出所需颗粒大小的物料。
三、生产流程3.1 原材料预处理将经过处理后的原材料按一定比例混合,并送入球磨机进行混合和细碎。
3.2 烧成过程将已经混合好的原材料送入旋转窑中,在高温下进行反应,形成水泥熟料。
在旋转窑出口处,通过冷却机对水泥熟料进行冷却。
3.3 粉末制备将冷却后的水泥熟料送入球磨机中进行细碎,最终得到所需颗粒大小的水泥粉末。
3.4 包装和储存将制备好的水泥粉末包装成袋或散装,并存放在干燥通风的仓库中。
四、环保措施4.1 烟气处理在旋转窑出口处设置烟气处理设备,将烟气中的二氧化硫等污染物进行吸收和净化。
4.2 垃圾处理生产过程中产生的垃圾要进行分类处理,有机垃圾进行堆肥处理,非有机垃圾送入垃圾焚烧设备进行焚烧。
4.3 水资源利用对生产过程中产生的废水进行回收和利用,减少对水资源的浪费。
五、安全措施5.1 设备维护定期对生产设备进行检查和维护,确保设备运行正常。
水泥生产工艺改进与优化
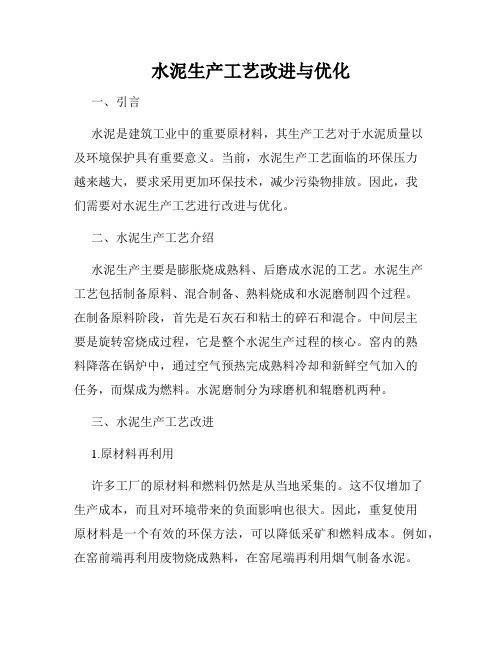
水泥生产工艺改进与优化一、引言水泥是建筑工业中的重要原材料,其生产工艺对于水泥质量以及环境保护具有重要意义。
当前,水泥生产工艺面临的环保压力越来越大,要求采用更加环保技术,减少污染物排放。
因此,我们需要对水泥生产工艺进行改进与优化。
二、水泥生产工艺介绍水泥生产主要是膨胀烧成熟料、后磨成水泥的工艺。
水泥生产工艺包括制备原料、混合制备、熟料烧成和水泥磨制四个过程。
在制备原料阶段,首先是石灰石和粘土的碎石和混合。
中间层主要是旋转窑烧成过程,它是整个水泥生产过程的核心。
窑内的熟料降落在锅炉中,通过空气预热完成熟料冷却和新鲜空气加入的任务,而煤成为燃料。
水泥磨制分为球磨机和辊磨机两种。
三、水泥生产工艺改进1.原材料再利用许多工厂的原材料和燃料仍然是从当地采集的。
这不仅增加了生产成本,而且对环境带来的负面影响也很大。
因此,重复使用原材料是一个有效的环保方法,可以降低采矿和燃料成本。
例如,在窑前端再利用废物烧成熟料,在窑尾端再利用烟气制备水泥。
2.新型窑壁结构熟料反应的核心区域在旋转窑内,其周围是一个多孔的熟料层,这是热反应的主要场所。
因此,窑壁对熟料的热传递和物料运动至关重要,窑壁的设计结构可以改进传热和物料运动,提高熟料反应的质量和效率。
3.煤粉喷吹技术燃料是水泥生产中的一个重要因素。
传统的燃烧技术采用浮动煤粉,其不仅能降低环境质量,而且燃烧效率也不尽如人意。
因此,煤粉喷吹代替浮动煤粉,能有效改善环境问题,并且可以提高燃烧效率。
四、水泥生产工艺优化1.降低能耗水泥生产中能耗较大,其中约90%的能量都用于熟料的烧成。
因此,优化窑炉操作和减少浪费燃料能有效降低能耗,从而达到减轻污染物排放并提高经济效益的目的。
2.减少污染物排放烟气处理是水泥工厂中的重要问题之一。
减少烟气排放,防止水泥厂对周围环境造成污染是水泥生产中必须重视的问题。
可以采取建立废气处理系统和循环利用废气中的热能等方法,减少污染物排放和提高水泥质量。
水泥厂工艺设计概论
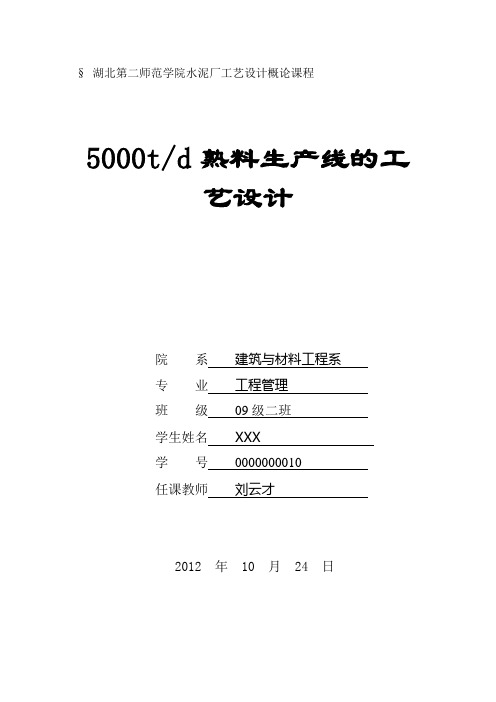
§湖北第二师范学院水泥厂工艺设计概论课程5000t/d熟料生产线的工艺设计院系建筑与材料工程系专业工程管理班级09级二班学生姓名XXX学号**********任课教师刘云才2012 年 10 月 24 日5000t/d熟料生产线的工艺设计专业工程管理学生XXX学号0000000010摘要:本文以5000t/d水泥熟料生产线为对象,从原材料、燃料的选择开始,对水泥熟料生产线的生产工艺进行了详细的介绍,并在文中给出了工艺平衡计算和水泥厂生产线的平面图。
关键词:物料平衡;热耗;物料均化;预分解窑Abstract:Based on the 5000 t/d cement clinker production line for object, begin with raw materials, fuel choice, production process to cement clinker production line were introduced in detail, and in this paper presents the process balance calculation and cement production line of the plan.Key words:Material balance; heat rate; Material homogenization; Precalcining kiln目录1 前言 (3)2 原材料、燃料的选择 (3)2.1 生料 (3)2.2 燃料 (3)2.3 水泥 (4)3 配方 (4)4 生产工艺 (4)4.1 生产线选择 (4)4.2 热耗 (4)4.3 生产线布置 (4)4.4 水泥原料、燃料所采用的预均化措施 (5)4.5 生料、水泥的均化与贮存措施 (5)4.5.1 均化 (5)4.5.2 贮存 (5)4.6 环境保护、节能降耗措施 (5)4.6.1 环境保护 (5)4.6.2 节能降耗 (5)4.7 电力、运输措施 (6)5 工艺平衡设计 (6)5.1 1吨熟料的生料需要量 (6)5.2 1吨熟料需要的原材料 (6)5.3 1吨熟料需煤量、熟料热耗 (6)5.4 1吨熟料制成水泥需要的石膏、粉煤灰 (6)5.5 物料平衡表 (6)5.6 各个工艺环节的储存量 (7)5.7 设备选型与库房类型 (7)5.7.1 设备选型 (7)5.7.2 库房类型 (8)5.8 总图布置 (10)6 结语 (10)参考文献 (11)1 前言水泥是国民经济的基础材料,在日常生活中随处可见,水泥工业是重化工工业,它的特点是对矿产资源的依存性大,物料储运量多,能量消耗高,在设计工作中对这些问题必须予以足够的认识。
水泥制品的生产工艺改进
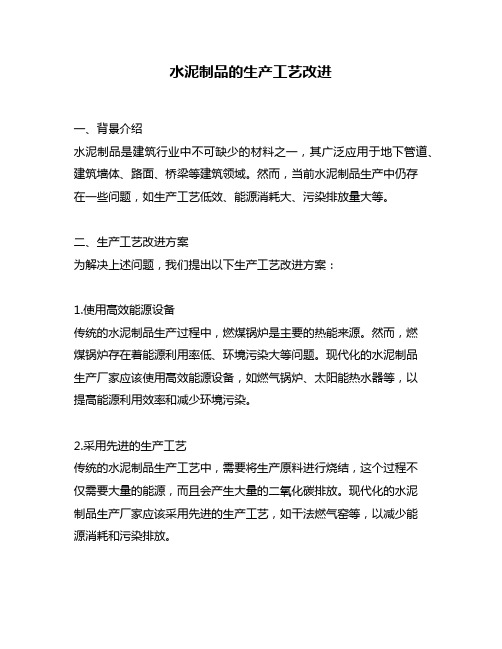
水泥制品的生产工艺改进一、背景介绍水泥制品是建筑行业中不可缺少的材料之一,其广泛应用于地下管道、建筑墙体、路面、桥梁等建筑领域。
然而,当前水泥制品生产中仍存在一些问题,如生产工艺低效、能源消耗大、污染排放量大等。
二、生产工艺改进方案为解决上述问题,我们提出以下生产工艺改进方案:1.使用高效能源设备传统的水泥制品生产过程中,燃煤锅炉是主要的热能来源。
然而,燃煤锅炉存在着能源利用率低、环境污染大等问题。
现代化的水泥制品生产厂家应该使用高效能源设备,如燃气锅炉、太阳能热水器等,以提高能源利用效率和减少环境污染。
2.采用先进的生产工艺传统的水泥制品生产工艺中,需要将生产原料进行烧结,这个过程不仅需要大量的能源,而且会产生大量的二氧化碳排放。
现代化的水泥制品生产厂家应该采用先进的生产工艺,如干法燃气窑等,以减少能源消耗和污染排放。
3.使用高效的热轧设备在水泥制品生产过程中,需要对原材料进行热轧处理。
传统的热轧设备存在着能源消耗大、工艺复杂等问题。
现代化的水泥制品生产厂家应该使用高效的热轧设备,如电热炉、感应炉等,以提高生产效率和减少能源消耗。
4.采用智能化控制系统传统的水泥制品生产过程中,需要大量的人力进行操作和监测。
现代化的水泥制品生产厂家应该采用智能化控制系统,以实现生产过程的自动化、智能化,提高生产效率和质量。
5.使用环保原材料传统的水泥制品生产过程中,主要使用的是石灰石、粘土等原材料。
这些原材料存在着开采成本高、污染排放量大等问题。
现代化的水泥制品生产厂家应该使用环保原材料,如废弃物、废旧钢材等,以减少对环境的影响。
三、实施效果评估通过实施上述生产工艺改进方案,可以达到以下效果:1.减少能源消耗采用高效能源设备、先进的生产工艺和高效的热轧设备可以减少能源消耗,降低生产成本。
2.减少污染排放采用先进的生产工艺、智能化控制系统和环保原材料可以减少污染排放,提高企业形象。
3.提高生产效率采用智能化控制系统和高效的热轧设备可以提高生产效率,增加企业盈利。
水泥厂设计范文
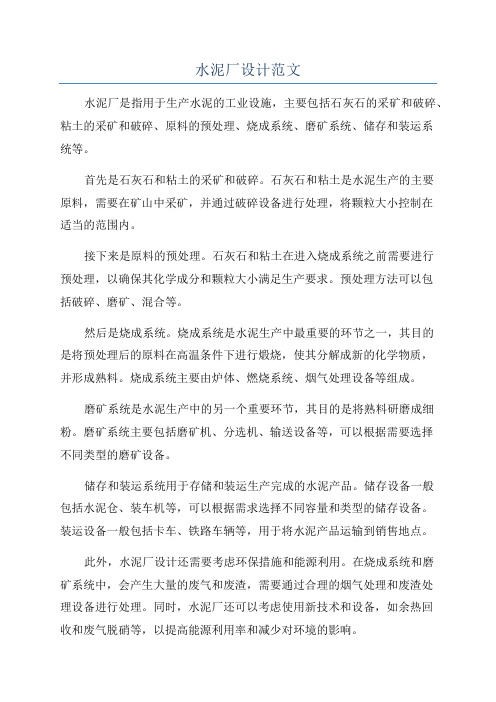
水泥厂设计范文水泥厂是指用于生产水泥的工业设施,主要包括石灰石的采矿和破碎、粘土的采矿和破碎、原料的预处理、烧成系统、磨矿系统、储存和装运系统等。
首先是石灰石和粘土的采矿和破碎。
石灰石和粘土是水泥生产的主要原料,需要在矿山中采矿,并通过破碎设备进行处理,将颗粒大小控制在适当的范围内。
接下来是原料的预处理。
石灰石和粘土在进入烧成系统之前需要进行预处理,以确保其化学成分和颗粒大小满足生产要求。
预处理方法可以包括破碎、磨矿、混合等。
然后是烧成系统。
烧成系统是水泥生产中最重要的环节之一,其目的是将预处理后的原料在高温条件下进行煅烧,使其分解成新的化学物质,并形成熟料。
烧成系统主要由炉体、燃烧系统、烟气处理设备等组成。
磨矿系统是水泥生产中的另一个重要环节,其目的是将熟料研磨成细粉。
磨矿系统主要包括磨矿机、分选机、输送设备等,可以根据需要选择不同类型的磨矿设备。
储存和装运系统用于存储和装运生产完成的水泥产品。
储存设备一般包括水泥仓、装车机等,可以根据需求选择不同容量和类型的储存设备。
装运设备一般包括卡车、铁路车辆等,用于将水泥产品运输到销售地点。
此外,水泥厂设计还需要考虑环保措施和能源利用。
在烧成系统和磨矿系统中,会产生大量的废气和废渣,需要通过合理的烟气处理和废渣处理设备进行处理。
同时,水泥厂还可以考虑使用新技术和设备,如余热回收和废气脱硝等,以提高能源利用率和减少对环境的影响。
总之,水泥厂设计需要综合考虑原料的采矿和破碎、预处理、烧成系统、磨矿系统、储存和装运系统等各个环节,同时还需要考虑环保和能源利用等因素,以确保水泥生产的高效性和可靠性。
- 1、下载文档前请自行甄别文档内容的完整性,平台不提供额外的编辑、内容补充、找答案等附加服务。
- 2、"仅部分预览"的文档,不可在线预览部分如存在完整性等问题,可反馈申请退款(可完整预览的文档不适用该条件!)。
- 3、如文档侵犯您的权益,请联系客服反馈,我们会尽快为您处理(人工客服工作时间:9:00-18:30)。
水泥厂工艺设计概况 WEIHUA system office room 【WEIHUA 16H-WEIHUA WEIHUA8Q8-上图为水泥厂工艺流程水泥厂主要的生产车间包含:物料的破碎(石灰石、黏土、砂岩、页岩、铁矿石、原煤、石膏等),熟料储存,熟料散装,煤粉制备,原、燃料储存或预均化,混合材及石膏的储存,原料配料站,水泥配料站,原料粉磨及废气处理,水泥粉磨,水泥储存,生料均化库,水泥散装、包装及发运,生料入窑,压缩空气站,烧成窑尾,化验室,中央控制室,烧成窑中,矿渣微粉粉磨系统,烧成窑头等。
物料的破碎在水泥生产中,大部分的物料都需要先经过破碎,如石灰石、粘土、砂岩、粉砂岩、铁矿石、煤、熟料、石膏、混合材等等,破碎的目的是为后续的粉磨、输送、储存等工序创造良好条件。
水泥厂破碎车间一般设有石灰石破碎、辅助原料破碎车间。
原煤破碎、石膏破碎等根据具体工厂来料情况决定是否设置。
水泥厂中破碎量最大的物料是石灰石,每生产1吨熟料大约需要石灰石~吨左右。
破碎机选用:常用于石灰石破碎的破碎机种类有:锤式破碎机、反击式破碎机、颚式破碎机、旋回式破碎机、园锥式破碎机等,锤式破碎机、反击式破碎机一段破碎即可满足要求,颚式破碎机、旋回式破碎机用于二段破碎的一级破碎,圆锥破用于二段破碎的二级破碎。
粘土破碎采用齿辊破碎机、冲击式破碎机等。
砂岩、粉砂岩破碎采用反击式破碎机,也有采用颚式破碎机、锤式破碎机等。
原煤破碎采用环锤式破碎机、立轴式破碎机、颚式破碎机等。
石膏破碎采用锤式破碎机、颚式破碎机等。
物料的储存水泥厂是连续运行的工厂,为了避免外部运输的不均衡、设备能力之间的不平衡、上下工序间生产班制的不同,质量检验的要求以及由于其它原因造成物料供应的中断,保证工厂正常地进行生产,要求各种原材料、燃料、半成品、成品在工厂内部都要有一定的储存量。
某物料的储存量所能满足工厂生产需要的天数,称为该物料的储存期。
物料的储存方式:露天堆场:未破碎的大块的石灰石、石膏等。
简易堆棚:辅助原料、原煤、石膏、混合材等。
联合储库:辅助原料、原煤、石膏、混合材等。
圆库(仓) :含水量小的小块状、颗粒状、粉状等非粘性物料,如碎石灰石、粉煤灰、干矿渣(粉) 、熟料、水泥等。
预均化堆场:石灰石、辅助原料、原煤等。
物料的均化生料化学成分的均齐性,不仅直接影响熟料的质量,而且对窑的产量、热耗、运转周期、耐火材料的寿命等都有较大的影响,这些影响对现代大型干法回转窑尤其敏感。
为了保证窑的稳产高产,必须进行生料的均化,减少入窑生料的化学成分波动,保证入窑生料化学成分的稳定。
由于水泥厂是以天然矿物作为原料,随着矿山开采层位、开采地段的不同,原料的成分波动在所难免,除应注意选择合理开采方案,尽量减少进厂原料成分波动以外,在要求配制成分稳定的生料方面,当然又不能苛求于矿山。
因此,还应对原料、生料采取有效的均化措施以满足生产要求。
原料的预均化原料的预均化是在堆料和取料过程中在预均化堆场内实现的。
水泥厂根据原料成分波动情况一般对石灰石、硅质原料(粘土、砂岩等)、燃料(煤)分别进行预均化。
也有厂将石灰石与粘土混合预均化的。
预均化堆场的型式常用的预均化堆场有长形预均化堆场、圆形预均化堆场。
长形预均化堆场:长形预均化堆场设置两个堆料区,一个区堆料,另一个区取料,两区交替使用。
长形预均化堆场具有扩建方便的优点。
长形预均化堆场(桥取)用于石灰石、原煤。
长形预均化堆场(侧取)用于辅助原料、原煤。
圆形预均化堆场:只有一个料堆,连续堆料和取料。
同等储量的条件下,圆形堆场占地面积小,设备的费用和维护费用均较低。
但由于有出料隧道,当地下水位较高时也有其不利之处,另外,无法扩建。
圆形预均化堆场的均化效果不如长形预均化堆场。
2500t/d直径为60000。
2500t/d、3200t/d、 5000t/d直径为80000。
5000t/d、6000t/d直径为90000。
6000t/d、 10000t/d直径为110000。
生料的均化出磨的生料其化学成分总难免有波动,必须经过均化以至调整,才能满足入窑生料控制指标的要求,一般入窑生料碳酸钙含量的标准偏差控制在±%。
新型干法水泥生产线都采用连续均化库系统。
其优点是流程简单、操作管理方便、便于自动控制等。
常用的生料均化库型式有:MF库、IBAU库、CP库、CF库等。
常用生料均化库的规格:2500t/d、3200t/d:Ф16 X 48m,储量:7000t。
5000t/d、6000t/d :Ф20 X 64m,储量:17600t。
6000t/d、7000t/d :Ф X 66m,储量:20000t。
10000t/d: 2 ?- Ф20X 64m,储量:2 × 17600t。
常用熟料库的规格:Ф15 X 36 m,储量:7500t。
Ф18 X 40 m,储量:10000t。
Ф22 X 50 m,储量:20000t。
Ф32 X 28m,储量:25000t。
Ф45 X 38m,储量:50000t。
Ф60 X 41m,储量:100000t。
常用水泥库的规格及储量:Ф12 X 30 m,储量:3500t。
Ф15 X 35 m,储量:6500t。
Ф18 X 45m,储量:10000t。
Ф22 X 60 m,储量:20000t。
物料的粉磨水泥工厂是能源消耗大户,而物料在粉磨过程中要消耗大量的电能。
在水泥生产过程中,磨制生料、制备煤粉和制成水泥,都要进行粉磨作业。
用煤作燃料的水泥厂,每生产一吨水泥需要粉磨的物料量约~吨。
在全厂生产用电中,由于采用的粉磨设备的不同,电耗也不同,一般而言,生料粉磨电耗为16~22kWh/t ,煤磨电耗为30~35 kWh/t,水泥电耗为30~40kWh/t。
全厂粉磨电耗占全部电耗的60%以上。
因此,合理的选择粉磨流程和设备,保证粉磨产品的质量并降低粉磨电耗,对于水泥厂的生产有着重要的意义。
随着现代干法窑规格的日益扩大,单台窑的产量已达到10000t/d以上,与窑配套的磨机规格也在朝着大型化方向发展,原料磨的台时产量已达到500t/h 以上,水泥磨的台时产量已达到250t/h 以上。
另外,磨机也在朝着节能方向发展,现在,在大中型水泥厂,原料粉磨越来越多地采用了辊式磨(立磨)和辊压机终粉磨系统,煤磨根据煤质情况尽可能地选用立磨系统,水泥粉磨系统则越来越多地采用了辊压机、辊式磨等节能的粉磨系统。
新型干法水泥厂目前有朝全厂无球化方向发展趋势。
即原料磨采用立磨或辊压机终粉磨、煤磨采用立磨、水泥磨采用立磨终粉磨。
辊压机终粉磨用于水泥粉磨的很少,主要是由于成品的颗粒形状及级配与球磨机有区别,影响水泥的性能。
原料粉磨新型干法水泥生产线中,原料粉磨常用以下几种粉磨流程:辊式磨、中卸磨、辊压机终粉磨。
辊式磨(立磨):在2500t/d以上规模的生产线中,原料磨采用辊式磨的占绝对的多数。
主要优点是:体积小、占地面积小、噪声低、利用废气余热处理湿原料能力好、烘干物料水分大,台时产量大、入磨物料粒度大,而最大的优点在于粉磨电耗低(比管磨系统低6kWh/t生料)。
它的缺点是对磨琢性物料和金属夹杂物较敏感,磨辊及磨盘易磨损,不很适应研磨硬质物料等。
辊式磨的电耗一般在16~20 kWh/t生料。
球磨机(管磨):常用的球磨机系统有风扫磨、中卸磨及尾卸磨等。
常用于2500t/d及以下规模。
2500t/d规模以上用管磨系统的不多。
球磨机系统具有投资低、对原料的适应性强、生产可靠、运转率高产品细度均匀等优点。
缺点是流程复杂,电耗高。
风扫磨的电耗一般在20~24 kWh/t生料,中卸磨的电耗一般在19~22 kWh/t生料。
辊压机终粉磨系统:辊压机终粉磨系统近几年在国内水泥厂使用的越来越多,7000t/d等水泥厂均采用辊压机终粉磨系统。
优点是节能,电耗12~14kWh/t-生料,比立磨系统低。
缺点是设备运转率有待提高,此外,系统烘干能力不如立磨系统。
几种原料粉磨系统对原料的适用范围粉磨系统:原料的物理特性适用范围。
中卸磨:水分宜<6%,易磨性及磨蚀性均不限。
辊式磨:水分宜<8%,易磨性中等,磨蚀性正常。
辊压机终粉磨:水分宜<5%,易磨性及磨蚀性均不限。
原料粉磨系统入磨物料的粒度要求原料粉磨系统入磨物料的粒度要求应根据采用的原料磨的类型和系统确定:钢球磨系统(包括中卸磨、尾卸磨、风扫磨等)入磨物料粒度应≤25mm;辊式磨系统宜为≤75mm;辊压机系统的入磨物料粒度宜为≤50mm。
原料粉磨系统的选择原料粉磨系统的选择主要考虑下列因素:原料的物理特性,如入磨物料的粒度、水分、易磨性等;系统的产量要求;节能;操作及自控水平;系统的可靠性及运转率;投资和生产成本。
煤粉制备煤粉制备所用的设备,目前大都采用烘干风扫磨及辊式磨系统。
现代干法水泥窑的热耗与窑的规格有关,产量越高热耗越低,一般在730 ~ 850 kcal/kg-熟料。
折算到标煤为107 ~ 121kg/t-熟料。
相当于电耗~ kWh/t熟料。
煤粉制备系统的电耗对水泥的总电耗影响不是很大。
烟煤和无烟煤无烟煤和含煤矸石较多的烟煤不适合采用立磨粉磨。
无烟煤挥发份低(小于5%) ,热值一般较高,可达到23450 ~ 27885kJ/kg。
由于挥发份低,煤粉着火温度高,燃烬时间长。
烟煤着火温度410 ~430℃,燃烧延续时间约10min,在600~650℃燃烬。
无烟煤着火温度550℃,燃烧延续时间约14min,在850℃燃烬。
粉磨烟煤和无烟煤在细度也有区别:烟煤煤粉细度为88μm筛筛余8%~15%,无烟煤煤粉细度为88μm筛筛余3%~5%。
随着煤粉细度的变化,无烟煤着火温度和燃烬温度的变化幅度比烟煤大,这主要是无烟煤中挥发份低、固定碳含量高的缘故。
无烟煤的热量主要来自固定碳,无烟煤的着火温度和燃烧时间主要取决于固定碳的燃烧性能。
固定碳是固体颗粒,结构致密,与烟煤中较多的可烟气体(挥发份)相比,其燃点较高,燃烧速度慢。
煤粉细度的改变主要是改变了固定碳的粒度,使燃烧面积发生变化。
水泥粉磨水泥粉磨流程:水泥粉磨系统流程种类较多,目前常用的有以下几种流程:①管磨开流;②管磨圈流;③辊压机开流+管磨开流;④辊压机圈流+管磨开流;⑤辊压机开流+管磨圈流;⑥辊压机圈流+管磨圈流;⑦辊式磨终粉磨等。
目前常用的水泥粉磨流程有:辊压机圈流+管磨开流、辊压机圈流+管磨圈流系统。
立磨预粉磨系统国内水泥厂用的不多、立磨终粉磨系统也不多,但是未来发展的趋势。
圈流水泥粉磨系统的优点:与开流水泥磨相比,圈流水泥磨具有如下优点:有利于降低水泥温度,防止石膏脱水;调节水泥细度方便;小于45微米的细粉较多,有利于提高28天的水泥强度;粉磨电耗低一些。
辊压机+管磨水泥粉磨系统的优点:与管磨圈流水泥磨相比,具有如下优点:产量高,电耗低。