煤制烯烃工艺及催化剂的选择
煤制烯烃 历史沿革
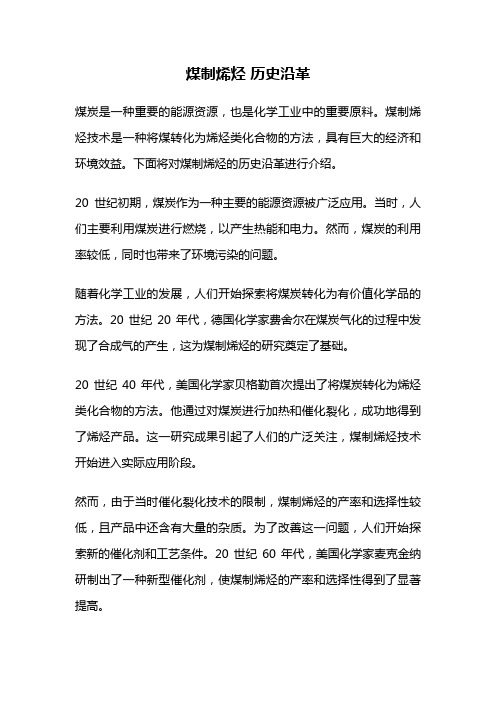
煤制烯烃历史沿革煤炭是一种重要的能源资源,也是化学工业中的重要原料。
煤制烯烃技术是一种将煤转化为烯烃类化合物的方法,具有巨大的经济和环境效益。
下面将对煤制烯烃的历史沿革进行介绍。
20世纪初期,煤炭作为一种主要的能源资源被广泛应用。
当时,人们主要利用煤炭进行燃烧,以产生热能和电力。
然而,煤炭的利用率较低,同时也带来了环境污染的问题。
随着化学工业的发展,人们开始探索将煤炭转化为有价值化学品的方法。
20世纪20年代,德国化学家费舍尔在煤炭气化的过程中发现了合成气的产生,这为煤制烯烃的研究奠定了基础。
20世纪40年代,美国化学家贝格勒首次提出了将煤炭转化为烯烃类化合物的方法。
他通过对煤炭进行加热和催化裂化,成功地得到了烯烃产品。
这一研究成果引起了人们的广泛关注,煤制烯烃技术开始进入实际应用阶段。
然而,由于当时催化裂化技术的限制,煤制烯烃的产率和选择性较低,且产品中还含有大量的杂质。
为了改善这一问题,人们开始探索新的催化剂和工艺条件。
20世纪60年代,美国化学家麦克金纳研制出了一种新型催化剂,使煤制烯烃的产率和选择性得到了显著提高。
随着科学技术的不断发展,煤制烯烃的研究取得了新的突破。
20世纪70年代,美国和苏联相继建立了大型的煤制烯烃生产装置,并开始商业化生产煤制烯烃产品。
这标志着煤制烯烃技术进入了一个新的阶段。
在20世纪80年代和90年代,煤制烯烃技术得到了进一步的改进和完善。
新型催化剂的研制和工艺条件的优化,使得煤制烯烃的产率和选择性进一步提高。
同时,人们对煤制烯烃的反应机理和催化剂的作用机理也有了更深入的认识。
随着21世纪的到来,煤制烯烃技术得到了广泛应用和推广。
煤制烯烃产品被广泛用于塑料、橡胶、化纤、涂料等化工领域,为国民经济的发展做出了重要贡献。
同时,煤制烯烃技术也得到了进一步的创新和发展,如采用新型催化剂、改进反应工艺等,以提高产率、选择性和产品质量。
总结来看,煤制烯烃的历史沿革经历了从初期的探索研究到实际应用的过程。
60 万吨年MTO(煤制烯烃)分厂设计

第1 章总论1.1 项目概况本项目为60 万吨/年MTO(煤制烯烃)分厂设计,原料采用煤化工企业总厂生产的甲醇,借助类似催化裂化装置的流化床反应形式,生产以乙烯、丙烯为主的低碳烯烃。
在反应温度500~550摄氏度,压力为0.1~0.15MPa,催化剂P-ZSM-5条件下,甲醇转化率为100%,C2-C4烯烃的选择性高达86%。
工艺流程简单、可靠、投资少、能耗低、对进料组成变化适应性强。
1.2 设计依据国家相关的法律法规要求可行性研究报告以及设计计划任务现有的MTO工艺技术以及化工工程设计相关规定1.3 工艺特点MTO工艺采用优点很多的流化床反应器。
部分待生催化剂经过用空气烧焦的连续再生,可以保持催化剂活性和产品组成不听。
工业规模生产的催化剂已经通过示范试验,选择性、长期稳定性和抗磨性都符合要求。
流化床反应器还具有调节操作条件和较好回收反应热的灵活性。
这种反应器早已广泛用于炼油厂的催化裂化装置特别是催化剂再生。
反应器的操作条件可以根据目的产品的需要进行调节。
压力通常决定于机械设计的考虑,较低的甲醇分压有利于得到较高的轻烯烃特别是乙烯的选择性。
因此,采用粗甲醇(通常可以含有20%左右水)作原料,可以得到某些产率优势。
温度是一个重要的控制参数,较高的温度有利于得到较高的乙烯收率。
MTO工艺提供一种把具有低成本优势的原料(天然气或煤)转化为高附加值低级烃乙烯和丙烯产品的途径。
甲醇制烯烃工艺的主要产品是乙烯(C2H4)、丙烯(C3H6),传统上乙烯和丙烯的来源主要是石油烃类蒸汽裂解,其原料主要是石脑油。
随着煤经合成气生产甲醇的技术日臻成熟,甲醇是低附加值的化工产品,另外受金融风暴的影响,国际甲醇价格下跌,开发甲醇下游产品使煤经由甲醇制取低碳烯烃成为备受关注的一条生产路线1.4 产品方案本项目主要产品为乙烯(C2H4)、丙烯(C3H6),并副产一定量丁烯(C4H8),以及C5+区地处交通便利位置,有较好的市场前景。
煤制烯烃过程技术经济分析与生命周期评价

煤制烯烃过程技术经济分析与生命周期评价一、本文概述本文旨在全面深入地探讨煤制烯烃过程的技术经济分析和生命周期评价。
煤制烯烃作为一种重要的化工过程,其经济性和环境影响对于化工行业的可持续发展具有重要意义。
本文首先概述了煤制烯烃过程的基本原理和工艺流程,随后从技术经济角度分析了该过程的成本效益,包括原料成本、能源消耗、设备投资以及运营维护等方面。
在此基础上,本文进一步进行了生命周期评价,全面评估了煤制烯烃过程从原料开采到产品废弃整个生命周期内的环境影响,包括能源消耗、温室气体排放、水资源消耗以及废弃物产生等。
通过本文的研究,旨在为煤制烯烃过程的优化和可持续发展提供理论依据和实践指导。
二、煤制烯烃技术概述煤制烯烃(CTL,Coal to Olefins)是一种将煤炭转化为烯烃的化学过程,主要目标是从非石油资源生产重要的化工原料,如乙烯和丙烯。
随着全球对可再生能源和可持续发展的日益关注,以及石油资源的日益枯竭,CTL技术已成为化学工业的重要发展方向。
煤制烯烃的过程主要包括煤气化、合成气制备、甲醇合成和甲醇制烯烃(MTO)或甲醇制丙烯(MTP)等步骤。
煤炭通过气化反应生成合成气(一氧化碳和氢气的混合物)。
然后,合成气经过催化转化生成甲醇。
甲醇再进一步转化为烯烃。
煤制烯烃技术的优势在于可以利用丰富的煤炭资源,实现化工原料的多元化和本地化生产,减少对进口石油的依赖。
煤炭的价格相对稳定,有助于降低生产成本并增强产业竞争力。
然而,该技术也面临一些挑战,如煤炭气化过程中产生的二氧化碳排放问题,以及煤制烯烃过程中较高的能耗和水耗等。
为了应对这些挑战,研究者们正在开发更加高效、环保的煤制烯烃技术。
例如,通过改进气化工艺、提高催化剂活性、优化反应条件等手段,以降低能耗和减少排放。
随着新技术的不断发展,未来煤制烯烃技术有望实现更高效、更环保的生产过程。
煤制烯烃技术是一种具有潜力的化工生产方法,它不仅可以利用丰富的煤炭资源生产重要的化工原料,还有助于减少对石油资源的依赖和降低生产成本。
煤制烯烃的主要工艺流程

煤制烯烃的主要工艺流程
煤制烯烃是利用煤作为原料,通过化学反应将煤转化为烯烃产品的过程。
其主要工艺流程包括:
1. 煤气化:将煤在高温、高压和缺氧条件下分解成气体,主要产物为一氧化碳、氢气和少量甲烷等。
这是煤制烯烃的前置工艺。
2. 合成气制备:将煤气化产物中的一氧化碳和氢气按照一定比例混合,经过催化剂反应生成合成气。
合成气中一氧化碳和氢气的比例对后续烯烃产物的性质和产率具有重要影响。
3. 合成烯烃:将合成气通过合成反应器,经过催化剂催化作用,生成烯烃。
常用的催化剂有Fischer-Tropsch催化剂、ZSM-5分子筛催化剂等。
4. 烯烃分离:将合成的烯烃产品从反应器中分离出来,通过蒸馏、萃取等工艺进行提纯和分离。
5. 烯烃后处理:对分离出来的烯烃产品进行后续处理,如裂解、加氢、氧化等,以提高其纯度和改善其物化性能,以满足工业应用要求。
总体而言,煤制烯烃的工艺流程相对复杂,但其具有原料来源广泛、生产成本低廉、产品种类丰富等优点,具有广泛的应用前景。
- 1 -。
煤制烯烃示范工程项目主要污染治理工艺优选方案

煤制烯烃示范工程项目主要污染治理工艺优选方案煤制烯烃示范工程是指利用燃煤等方式生产烯烃的工程项目。
煤制烯烃生产过程中,会产生大量的废水、废气和固体废弃物,对环境造成严重影响。
因此,提出合理的污染治理工艺优选方案,对于减少污染物的排放,保护环境具有重要意义。
1.废水治理方案:煤制烯烃过程中产生的废水含有大量的有机污染物和重金属离子,直接排放会对水体造成严重污染。
首先,应引入预处理工艺,包括中性化调节、悬浮物去除、沉淀去除、生化处理等,以降低污染物的浓度。
然后,采用活性炭吸附、高级氧化等技术进行进一步处理,去除难降解的有机污染物和重金属离子。
最后,通过深度处理和消毒等工艺,确保废水达到国家排放标准。
2.废气治理方案:煤制烯烃生产过程中,产生的废气中主要含有一氧化碳、二氧化碳、硫化氢、苯等有机物和氮氧化物等污染物。
首先,应通过合理的工艺设计,减少废气的产生,如合理配气、优化反应条件等。
然后,采用干法除尘、湿法脱硝、脱硫和脱氨等技术,去除废气中的颗粒物、有机物和气态污染物。
最后,采用催化催化剂进行脱催化,降低氮氧化物的排放浓度。
最终,通过排气口监测,确保废气的排放符合国家标准。
3.固体废弃物治理方案:煤制烯烃生产过程中所产生的固体废弃物主要包括煤渣、催化剂和催化剂废料等。
首先,应采用分类和预处理的方式,对固体废弃物进行处理。
其中,煤渣可经过煤渣固化处理,生成水泥煤矸石,用于水泥加工。
催化剂可经过高温焚烧还原,回收金属成分,降低废料的处理量。
对于催化剂废料,可以通过化学还原和稳定化等方法进行处理,减少对环境的影响。
同时,还应建立固体废弃物的监测系统,确保废弃物的处置合规,对环境没有二次污染。
4.排放监测方案:煤制烯烃示范工程项目应建立完善的排放监测系统,对废水、废气和固体废弃物的排放进行监测和记录。
监测系统应包括在线监测和周期采样监测两种方式,以确保数据的准确性。
同时,还应加强对监测数据的分析和评估,及时发现问题,并采取相应的纠正措施。
煤制烯烃生产流程原理和发展趋势
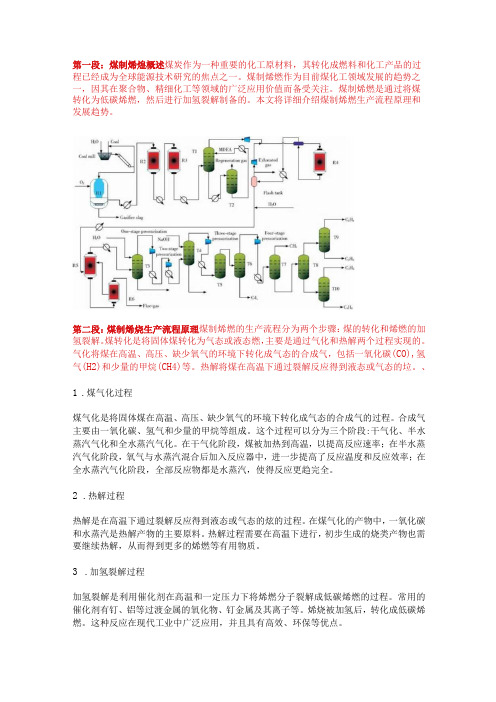
第一段:煤制烯煌概述煤炭作为一种重要的化工原材料,其转化成燃料和化工产品的过程已经成为全球能源技术研究的焦点之一。
煤制烯燃作为目前煤化工领域发展的趋势之一,因其在聚合物、精细化工等领域的广泛应用价值而备受关注。
煤制烯燃是通过将煤转化为低碳烯燃,然后进行加氢裂解制备的。
本文将详细介绍煤制烯燃生产流程原理和发展趋势。
第二段:煤制烯烧生产流程原理煤制烯燃的生产流程分为两个步骤:煤的转化和烯燃的加氢裂解。
煤转化是将固体煤转化为气态或液态燃,主要是通过气化和热解两个过程实现的。
气化将煤在高温、高压、缺少氧气的环境下转化成气态的合成气,包括一氧化碳(CO),氢气(H2)和少量的甲烷(CH4)等。
热解将煤在高温下通过裂解反应得到液态或气态的垃。
、1.煤气化过程煤气化是将固体煤在高温、高压、缺少氧气的环境下转化成气态的合成气的过程。
合成气主要由一氧化碳、氢气和少量的甲烷等组成。
这个过程可以分为三个阶段:干气化、半水蒸汽气化和全水蒸汽气化。
在干气化阶段,煤被加热到高温,以提高反应速率;在半水蒸汽气化阶段,氧气与水蒸汽混合后加入反应器中,进一步提高了反应温度和反应效率;在全水蒸汽气化阶段,全部反应物都是水蒸汽,使得反应更趋完全。
2.热解过程热解是在高温下通过裂解反应得到液态或气态的炫的过程。
在煤气化的产物中,一氧化碳和水蒸汽是热解产物的主要原料。
热解过程需要在高温下进行,初步生成的烧类产物也需要继续热解,从而得到更多的烯燃等有用物质。
3.加氢裂解过程加氢裂解是利用催化剂在高温和一定压力下将烯燃分子裂解成低碳烯燃的过程。
常用的催化剂有钉、铝等过渡金属的氧化物、钉金属及其离子等。
烯烧被加氢后,转化成低碳烯燃。
这种反应在现代工业中广泛应用,并且具有高效、环保等优点。
总的来说,煤制烯燃生产流程涉及多个步骤,其中包括煤气化、热解和加氢裂解等关键的原理。
通过这些步骤的协同作用,煤可以转化为烯崎,从而实现对煤资源的高效利用和化石能源的替代,具有广阔的应用前景和巨大的经济价值。
2024年煤制烯烃工艺市场分析现状
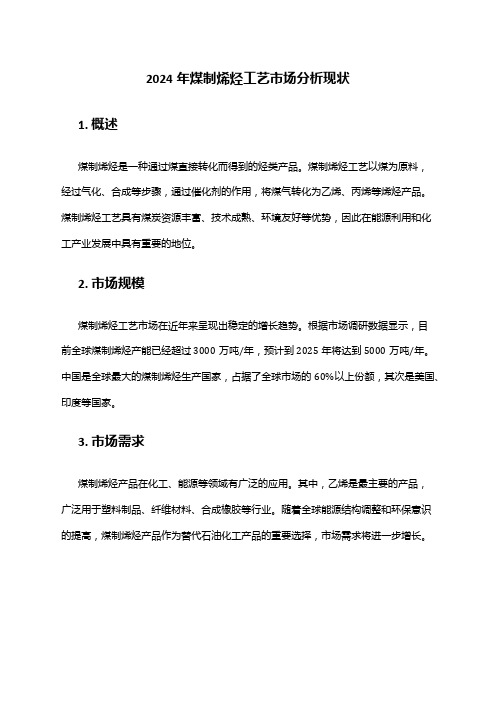
2024年煤制烯烃工艺市场分析现状1. 概述煤制烯烃是一种通过煤直接转化而得到的烃类产品。
煤制烯烃工艺以煤为原料,经过气化、合成等步骤,通过催化剂的作用,将煤气转化为乙烯、丙烯等烯烃产品。
煤制烯烃工艺具有煤炭资源丰富、技术成熟、环境友好等优势,因此在能源利用和化工产业发展中具有重要的地位。
2. 市场规模煤制烯烃工艺市场在近年来呈现出稳定的增长趋势。
根据市场调研数据显示,目前全球煤制烯烃产能已经超过3000万吨/年,预计到2025年将达到5000万吨/年。
中国是全球最大的煤制烯烃生产国家,占据了全球市场的60%以上份额,其次是美国、印度等国家。
3. 市场需求煤制烯烃产品在化工、能源等领域有广泛的应用。
其中,乙烯是最主要的产品,广泛用于塑料制品、纤维材料、合成橡胶等行业。
随着全球能源结构调整和环保意识的提高,煤制烯烃产品作为替代石油化工产品的重要选择,市场需求将进一步增长。
4. 技术发展煤制烯烃工艺技术经过多年的发展已经相对成熟。
目前主要的煤制烯烃工艺包括间接液化、直接煤制烯烃等方法。
其中,直接煤制烯烃工艺具有工艺简单、能耗低等优势,在工业应用中得到了广泛应用和推广。
5. 市场竞争目前,全球煤制烯烃工艺市场上存在着一定的竞争。
主要的竞争企业包括中国石化、山西焦煤集团、美国Exxon Mobil等。
这些企业在煤制烯烃工艺技术和产能方面具有较高的竞争力,通过技术创新和扩大生产规模来提高市场份额。
6. 市场前景未来,煤制烯烃工艺市场仍然具有较好的发展前景。
首先,煤炭资源丰富,提供了坚实的原料基础;其次,煤制烯烃工艺成本较低,具有一定的竞争优势;此外,煤制烯烃产品可以替代石油化工产品,符合环保要求,将受到政策支持和市场认可。
7. 结论煤制烯烃工艺市场具有较大的潜力和发展空间。
在国家资源战略和环保意识的推动下,煤制烯烃工艺将继续发挥重要作用,推动能源转型和化工产业升级。
然而,市场竞争也日益激烈,企业需要不断进行技术创新和产能扩大,提高市场竞争力。
煤质烯烃的工艺技术

煤质烯烃的工艺技术煤质烯烃是指从煤炭中提取出来的烯烃类化合物,具有重要的工业应用价值。
煤质烯烃的工艺技术主要包括煤液化和煤气化两种方法。
1. 煤液化技术煤液化是将煤炭在高温高压下通过催化剂或溶剂作用,将煤中的有机物质转化为液体产品的过程。
煤液化技术可分为直接液化和间接液化两种方法。
直接液化是指将煤炭与溶剂和催化剂混合后,在高温高压下进行反应,通过催化剂的作用将煤转化为液体产品。
在直接液化过程中,溶剂可起到催化剂的作用,帮助提高反应速率和产物收率。
间接液化是指先将煤炭气化生成合成气,再通过催化剂的作用进行反应生成液体产品。
煤液化技术的关键步骤包括煤炭粉碎、石油溶剂提取和催化剂添加等。
煤炭粉碎可以增加煤与溶剂催化剂的接触面积,有利于反应进行。
溶剂的选择对于反应速率和产物性质有重要影响,通常选择具有较高活性和选择性的溶剂。
催化剂的选择和添加方式也会影响反应的进行和产物的性质。
2. 煤气化技术煤气化是指将煤炭在高温下与气化剂(通常为氧气和水蒸气)反应,生成合成气的过程。
合成气主要包括一氧化碳和氢气,可以用作燃料或化工原料。
煤气化技术可分为固定床气化、流化床气化和床层气化等方法。
固定床气化是最传统的煤气化技术,将煤炭放置在反应器中,通过控制气化剂的供气量和反应条件,使煤炭与气化剂反应生成合成气。
流化床气化是指将煤炭破碎成较小的颗粒,通过气流作用使其悬浮在反应器中,与气化剂反应生成合成气。
床层气化是将煤炭放置在床层中,通过控制气化剂的上下供气或其他传质方式使煤炭与气化剂充分接触反应,生成合成气。
煤气化技术的关键步骤包括煤炭预处理、气化剂准备和气化反应等。
煤炭预处理主要包括煤炭粉碎和煤炭干燥,以提高煤与气化剂的接触面积和反应速率。
气化剂的准备包括氧气和水蒸气的供应和净化。
气化反应的温度和压力及气化剂的供气量等条件对反应进行和产物分布有重要影响。
总之,煤质烯烃的工艺技术主要包括煤液化和煤气化两种方法。
煤液化通过催化剂或溶剂作用,将煤中的有机物质转化为液体产品。
- 1、下载文档前请自行甄别文档内容的完整性,平台不提供额外的编辑、内容补充、找答案等附加服务。
- 2、"仅部分预览"的文档,不可在线预览部分如存在完整性等问题,可反馈申请退款(可完整预览的文档不适用该条件!)。
- 3、如文档侵犯您的权益,请联系客服反馈,我们会尽快为您处理(人工客服工作时间:9:00-18:30)。
煤制烯烃的工艺及催化剂的选择煤制烯烃即煤基甲醇制烯烃,是指以煤为原料合成甲醇后再通过甲醇制取乙烯、丙烯等烯烃的技术。
煤经甲醇制烯烃工艺主要由煤气化制合成气、合成气制取甲醇、甲醇制烯烃三项技术组成。
1、煤气化制合成气1.1 煤气化工艺煤气化是指煤与气化剂在一定的温度、压力等条件下发生反应而转化为煤气的工艺过程,且一般是指煤的完全气化,即将煤中的有机质最大限度地转变为有用的气态产品,而气化后的残留物只是灰渣。
几种煤气化工艺技术性能综合比较见表1。
表1 不同气化工艺技术性能比较1.1.1煤浆制备由煤运系统送来的原料煤干基(<25mm)或焦送至煤贮斗,经称重给料机控制输送量送入棒磨机,加入一定量的水,物料在棒磨机中进行湿法磨煤。
为了控制煤浆粘度及保持煤浆的稳定性加入添加剂,为了调整煤浆的PH值,加入碱液。
出棒磨机的煤浆浓度约65%,排入磨煤机出口槽,经出口槽泵加压后送至气化工段煤浆槽。
煤浆制备首先要将煤焦磨细,再制备成约65%的煤浆。
磨煤采用湿法,可防止粉尘飞扬,环境好。
用于煤浆气化的磨机现在有两种,棒磨机与球磨机;棒磨机与球磨机相比,棒磨机磨出的煤浆粒度均匀,筛下物少。
煤浆制备能力需和气化炉相匹配,本项目拟选用三台棒磨机,单台磨机处理干煤量43~53t/h,可满足60万t/a甲醇的需要。
为了降低煤浆粘度,使煤浆具有良好的流动性,需加入添加剂,初步选择木质磺酸类添加剂。
煤浆气化需调整浆的PH值在6~8,可用稀氨水或碱液,稀氨水易挥发出氨,氨气对人体有害,污染空气,故本项目拟采用碱液调整煤浆的PH值,碱液初步采用42%的浓度。
为了节约水源,净化排出的含少量甲醇的废水及甲醇精馏废水均可作为磨浆水。
1.1.2 气化在本工段,煤浆与氧进行部分氧化反应制得粗合成气。
煤浆由煤浆槽经煤浆加压泵加压后连同空分送来的高压氧通过烧咀进入气化炉,在气化炉中煤浆与氧发生如下主要反应:CmHnSr+m/2O2—→mCO+(n/2-r)H2+rH2SCO+H2O—→H2+CO2反应在6.5MPa(G)、1350~1400℃下进行。
气化反应在气化炉反应段瞬间完成,生成CO、H2、CO2、H2O和少量CH4、H2S等气体。
离开气化炉反应段的热气体和熔渣进入激冷室水浴,被水淬冷后温度降低并被水蒸汽饱和后出气化炉;气体经文丘里洗涤器、碳洗塔洗涤除尘冷却后送至变换工段。
气化炉反应中生成的熔渣进入激冷室水浴后被分离出来,排入锁斗,定时排入渣池,由扒渣机捞出后装车外运。
气化炉及碳洗塔等排出的洗涤水(称为黑水)送往灰水处理。
1.2 煤气化催化剂的选择煤的催化气化是在煤的固体状态下进行的,催化剂与煤的粉粒按照一定的比例均匀地混合在一起,煤表面分布的催化剂通过侵蚀开槽作用,使煤与气化剂更好地接触并加快气化反应。
与传统的煤气化相比,煤的催化气化可以明显降低反应温度,提高反应速率, 改善煤气组成, 增加煤气产率。
一般而言, 可用于煤气化反应的催化剂主要是以碱金属和碱土金属为主的金属氧化物、金属氢氧化物、盐类以及铁、钴、镍等过渡金属元素的化合物。
不同类型的催化剂适用于不同的气化剂, 不同催化剂对不同气化反应的催化活性也各不相同。
适于催化C- H2O 反应的催化剂主要是钾、钠、钙、铁、镍的化合物, 适于催化C- CO2、 C- O2 的催化剂主要是钾、钠、钙的化合物,适于催化C- H2反应的催化剂主要是铁、镍的化合物。
其中碱金属、碱土金属和铁系金属催化剂的主要性质比较见表 2。
表2 碱金属、碱土金属和铁系催化剂的主要性质比较根据研究过的催化剂的组成可将催化剂分为3类:单体金属盐或氧化物催化剂;复合催化剂;可弃催化剂,包括煤中的矿物质、工业废液、废碱等。
不同金属化合物对煤气化反应具有不同的催化作用机理。
1.2.1 单体金属盐催化剂通常认为, 芳香碳氢化合物很难与氧离子或者氢氧离子进行反应, 碱金属盐的存在可能会通过与碳原子部分成键而使煤焦表面碳骨架电荷发生迁移,改变了煤焦表面碳原子的电子云分布,削弱了碳一碳键的结合强度, 增强了碳一氧键的键合力,使煤焦表面具有了更强的反应活性点, 使气化反应更易于进行。
钙和铁化合物的催化作用,更多的学者则趋向于认为钙和铁直接参与了反应, 而不像碱金属盐那样通过改变焦样表面的能量分布起到催化作用, 它们的催化作用可以用氧化和还原循环反应来表述。
目前研究得最多的单体催化剂是K2CO3,用 K2CO3 作为催化剂, 成本低, 制备方法简单, 稳定性也较好。
K2 CO3也是目前唯一一种工业应用的煤催化气化催化剂。
对于单体催化剂, 关键在于催化剂的回收和重复利用。
在使用 K2CO3 作为催化剂的 Exxon 法中, 由于一部分钾与煤灰中硅酸铝反应,故仅用水洗法只能回收 60 % ~ 80 %。
1.2.2 复合催化剂复合催化剂的催化效果明显优于单体催化剂的催化效果。
其中三元催化剂的催化效果最好,这是由于三元催化剂呈液态, 而二元催化剂和单体催化剂 K2 CO3为固态。
催化剂以液态存在, 其流动性好,更容易扩散到反应体系,煤炭的活性点相应增加, 因此活性就相对较高。
复合催化剂选择性好, 反应温度较低, 熔点较低。
催化剂熔点越低,其催化活性越高。
这是由于熔点越低,在气化温度下流动性越好,越容易扩散到反应体系且活性点增加。
众多研究表明复合催化剂的工业化前景较好, 但是催化剂回收重复利用是其经济性生产的关键。
1.2.3 可弃性催化剂可弃催化剂是指一种经工业催化应用后无须回收而直接废弃的催化剂。
煤催化气化的可弃催化剂主要包括生物质灰、工业废碱液、工业废固碱、硫铁矿渣、转炉赤泥等。
廉价及高效催化剂的来源是煤催化气化的研究热点。
可弃催化剂作为一种加速煤气化反应的有效与廉价催化剂, 逐渐引起研究者的注意。
可弃催化剂在煤气化后不必回收,从而省去催化剂回收环节。
可以作为煤气化催化剂的工业废料很多, 有效物质的含量不尽相同,催化效率差异很大。
包括锯末、农作物秸秆、稻壳等在内的生物质也对煤气化有催化作用, 因此, 也可以用生物质作为催化剂进行煤催化气化研究。
一旦催化效率研究得到突破, 可弃催化剂将为煤催化气化的工业化创造良好的条件。
1.3 变换在本工段将气体中的CO部分变换成H2。
本工段的化学反应为变换反应,以下列方程式表示:CO+H2O—→H2+CO2由气化碳洗塔来的粗水煤气经气液分离器分离掉气体夹带的水分后,进入气体过滤器除去杂质,然后分成两股,一部分(约为54%)进入原料气预热器与变换气换热至305℃左右进入变换炉,与自身携带的水蒸汽在耐硫变换催化剂作用下进行变换反应,出变换炉的高温气体经蒸汽过热器与甲醇合成及变换副产的中压蒸汽换热、过热中压蒸汽,自身温度降低后在原料气预热器与进变换的粗水煤气换热,温度约335℃进入中压蒸汽发生器,副产4.0MPa蒸汽,温度降至270℃之后,进入低压蒸汽发生器温度降至180℃,然后进入脱盐水加热器、水冷却器最终冷却到40℃进入低温甲醇洗1#吸收系统。
另一部分未变换的粗水煤气,进入低压蒸汽发生器使温度降至180℃,副产0.7MPa 的低压蒸汽,然后进入脱盐水加热器回收热量,最后在水冷却器用水冷却至40℃,送入低温甲醇洗2#吸收系统。
气液分离器分离出来的高温工艺冷凝液送气化工段碳洗塔。
气液分离器分离出来的低温冷凝液经汽提塔用高压闪蒸气和中压蒸汽汽提出溶解在水中的CO2、H2S、NH3后送洗涤塔给料罐回收利用;汽提产生的酸性气体送往火炬。
1.4 低温甲醇洗本工段采用低温甲醇洗工艺脱除变换气中CO2、全部硫化物、其它杂质和H2O。
2、合成气制甲醇2.1 甲醇合成经甲醇洗脱硫脱碳净化后的产生合成气压力约为 5.6MPa,与甲醇合成循环气混合,经甲醇合成循环气压缩机增压至6.5MPa,然后进入冷管式反应器(气冷反应器)冷管预热到235℃,进入管壳式反应器(水冷反应器)进行甲醇合成,CO、CO2和H2在Cu-Zn催化剂作用下,合成粗甲醇,出管壳式反应器的反应气温度约为240℃,然后进入气冷反应器壳侧继续进行甲醇合成反应,同时预热冷管内的工艺气体,气冷反应器壳侧气体出口温度为250℃,再经低压蒸汽发生器,锅炉给水加热器、空气冷却器、水冷器冷却后到40℃,进入甲醇分离器,从分离器上部出来的未反应气体进入循环气压缩机压缩,返回到甲醇合成回路。
一部分循环气作为弛放气排出系统以调节合成循环圈内的惰性气体含量,合成弛放气送至膜回收装置,回收氢气,产生的富氢气经压缩机压缩后作为甲醇合成原料气;膜回收尾气送至甲醇蒸汽加热炉过热甲醇合成反应器副产的中压饱和蒸汽(2.5MPa),将中压蒸汽过热到400℃。
粗甲醇从甲醇分离器底部排出,经甲醇膨胀槽减压释放出溶解气后送往甲醇精馏工段。
系统弛放气及甲醇膨胀槽产生的膨胀气混合送往工厂锅炉燃料系统。
甲醇合成水冷反应器副产中压蒸汽经变换过热后送工厂中压蒸汽管网。
2.2 甲醇精馏从甲醇合成膨胀槽来的粗甲醇进入精馏系统。
精馏系统由预精馏塔、加压塔、常压塔组成。
预精馏塔塔底出来的富甲醇液经加压至0.8MPa、80℃,进入加压塔下部,加压塔塔顶气体经冷凝后,一部分作为回流,一部分作为产品甲醇送入贮存系统。
由加压塔底出来的甲醇溶液自流入常压塔下塔进一步蒸馏,常压塔顶出来的回流液一部分回流,一部分作为精甲醇经泵送入贮存系统。
常压塔底的含甲醇的废水送入磨煤工段作为磨煤用水。
在常压塔下部设有侧线采出,采出甲醇、乙醇和水的混合物,由汽提塔进料泵送入汽提塔,汽提塔塔顶液体产品部分回流,其余部分作为产品送至精甲醇中间槽或送至粗甲醇贮槽。
汽提塔下部设有侧线采出,采出部分异丁基油和少量乙醇,混合进入异丁基油贮槽。
汽提塔塔底排出的废水,含少量甲醇,进入沉淀池,分离出杂醇和水,废水由废水泵送至废水处理装置。
中间罐区:甲醇精馏工序临时停车时,甲醇合成工序生产的粗甲醇,进入粗甲醇贮罐中贮存。
甲醇精馏工序恢复生产时,粗甲醇经粗甲醇泵升压后送往甲醇精馏工序。
甲醇精馏工序生产的精甲醇,进入甲醇计量罐中。
经检验合格的精甲醇用精甲醇泵升压送往成品罐区甲醇贮罐中贮存待售。
2.3空分装置本装置工艺为分子筛净化空气、空气增压、氧气和氮气内压缩流程,带中压空气增压透平膨胀机,采用规整填料分馏塔,全精馏制氩工艺。
原料空气自吸入口吸入,经自洁式空气过滤器除去灰尘及其它机械杂质。
过滤后的空气进入离心式空压机经压缩机压缩到约0.57MPa(A),然后进入空气冷却塔冷却。
冷却水为经水冷塔冷却后的水。
空气自下而上穿过空气冷却塔,在冷却的同时,又得到清洗。
经空冷塔冷却后的空气进入切换使用的分子筛纯化器空气中的二氧化碳、碳氢化合物和水分被吸附。
分子筛纯化器为两只切换使用,其中一只工作时,另一只再生。
纯化器的切换周期约为4小时,定时自动切换。