两种润滑油调合工艺技术的对比
润滑油调和工艺详解--罐式调和

润滑油调和工艺详解--罐式调和1.润滑油调合工艺类型常见的润滑油调合工艺,一般分两种基本类型:罐式调合和管道调合。
不同的调合工艺具有独特的特点和适用不同的场合。
2.罐式调合罐式调合是将基础油和添加剂按比例直接送入调合罐,经过搅拌后,即为成品油。
罐式调合系统主要包括成品罐、混合装置、加热系统、散装和桶状添加剂的加入装置、计量设备、机泵和管线等基础设施及过程控制系统。
一些系统中抽桶装置的应用避免了桶装添加剂加入时各种杂质对产品质量的影响,也减少了添加剂对环境的污染;一些桶抽取装置具有清洗功能,将添加剂残留损耗降低到最低限度。
润滑油过滤,润滑油过滤设备,润滑油过滤器,润滑油过滤机,润滑油过滤袋,润滑油粘度,润滑油检测,润滑油生产工艺,润滑油润滑油过滤,润滑油过滤设备,润滑油过滤器,润滑油过滤机,润滑油过滤袋,润滑油粘度,润滑油检测,润滑油生产工艺,润滑油罐式调合工艺分为机械搅拌方式调合、泵循环方式调合、气动脉冲混合方式调合。
所使用的调合罐一般是带有加热系统和混合装置的金属罐(最好是不锈钢和搪瓷的)2.1机械搅拌调合使用机械搅拌混合是油罐调合的常用方法,适用于相对小批量的润滑油成品油的调合。
被调合物料是在搅拌器的作用下,形成主体对流和涡流扩散传质、分子扩散传质,使全部物料性质达到均一。
搅拌调合的效率,取决于搅拌器的设计及其安装。
润滑油成品油调合常用的搅拌方式主要有侧向伸入式搅拌及立式中心式搅拌两大类。
见下图⑴侧向伸入式搅拌⑵立式中心式搅拌图2-1润滑油调合常用搅拌方式⑴罐侧壁伸入式搅拌调合:搅拌器由罐侧壁伸入罐内,每个罐可装一个或几个,搅拌器的叶轮是船用推进式螺旋桨型。
影响搅拌调合所需功率的几个因素:①罐的容积与高径比:高径比越大,静压头越大所需总功率也越大;②介质粘度:介质粘度越大,流动阻力越大,所需功率相应增大;③搅拌时间:连续搅拌时间越短,搅拌所需功率越大;④搅拌运行方式:据有关资料记载:以两组分为例,两组分同时进罐,边进边搅,全润滑油过滤,润滑油过滤设备,润滑油过滤器,润滑油过滤机,润滑油过滤袋,润滑油粘度,润滑油检测,润滑油生产工艺,润滑油部进罐后继续搅拌,这种方式单位容积所需动力最小。
培训教程-润滑油调和工艺课件.ppt

到油品生产中,以先进的控制方式来操纵润滑油调和的整 个生产过程。按事先设定好的脉冲频率,延时和压力等参 数,通过现场一整套特殊的控制装置和安装在调和罐内的 集气盘,产生动力强大的大气泡。大气泡产生以后,自下 而上,自上而下地搅动油品,使油品中的各种组份在极短 的时间内被均匀地混合,从而达到合格产品质量。
润滑油调和工艺
管道调和:就是将两种或两种以 上组分油或添加剂,按规定比例 同时送入总管和管道混合器,达 到混合均匀的调和方法。管道调 和又分为简单管道调和和自动管 道调和。在调和过程中,各组分 的比例和质量标准完全由自动化 仪表和计算机检测、控制和自动 操作的称管道自动调和。用常规 控制仪表,人工操作掌握调和比 例的,直接经一条管线混和均匀 进入成品罐的属半自动调和或简 单管道调和。
v.
润滑油调和工艺
一、间隙调和
1、机械搅拌调和 被调和物料是在搅拌器的作用下,形成主体对流和涡
流扩散传质、分子扩散传质,使全部物料性质达到均一。 罐内物料在搅拌器转动时产生两个方向的运动;一是沿搅 拌器的轴线方向的向前运动,当受到罐壁或罐底的阻挡时, 改变其运动方向,经多次变向后,最终形成近似圆周的循 环流动;二是沿搅拌器浆叶的旋转方向形成的圆周运动, 使物料翻滚,最终达到混合均匀的目的。
v.
泵循环喷嘴搅拌调和
射流混合器 这种混 合器由容器、射流元件 和循环泵等组成(图4 [射流混合器和流 型] )。液体的高速射 流穿过低速的液体时, 一方面推动前方的液体 运动,一方面在界面上 产生高剪切力,从而形 成大量旋涡,进一步将 周围液体卷入射流中, 从而得到混合。
v.
静态混合器调和
v.
两种不同润滑油加氢工艺流程对比

一致ꎬ故对这两种润滑油加氢工艺流程做对比分析意义很大ꎻ
为了表述直观ꎬ在对比分析过程中ꎬ将“ 加氢处理” 称为“ 一
段加氢” ꎬ“ 异构脱蜡→补充精” 称为“ 二段加氢” ꎮ
1 两种润滑油加氢工艺流程介绍
1. 1 第一种润滑油加氢工艺流程 反应部分
configuration of main equipmentꎬenergy consumption of plant and difficulty of production operation. The results showed that: The
first process has fewer main equipment and lower energy consumptionꎻThe second process is relatively independent and flexibleꎬ
环氢压缩机分液罐ꎬ8 - 一段循环氢压缩机ꎬ9 - 新氢压缩机ꎬ10 - 一段热低压分离器ꎬ11 - 一段冷低压分离器ꎬ12 - 低压汽提塔进料加热炉ꎬ13 - 低压
14 - 二段热低压分离器ꎬ15 - 二段冷低压分离器ꎬ16 - 循环氢脱硫系统ꎬ17 - 开工电加热器ꎮ
图 1 第一种润滑油加氢工艺反应部分流程
收稿日期:2019 - 10 - 08
作者简介:艾 明(1981—) ꎬ大学本科ꎬ工程师ꎬ2005 年毕业于武汉化工学院ꎬ研究方向:从事油品化工工程设计及油品加氢装
Key words: lubricating oilꎻhydrogenation processꎻequipment configurationꎻenergy consumption of plantꎻproduction operation
工业润滑油调和优化方案
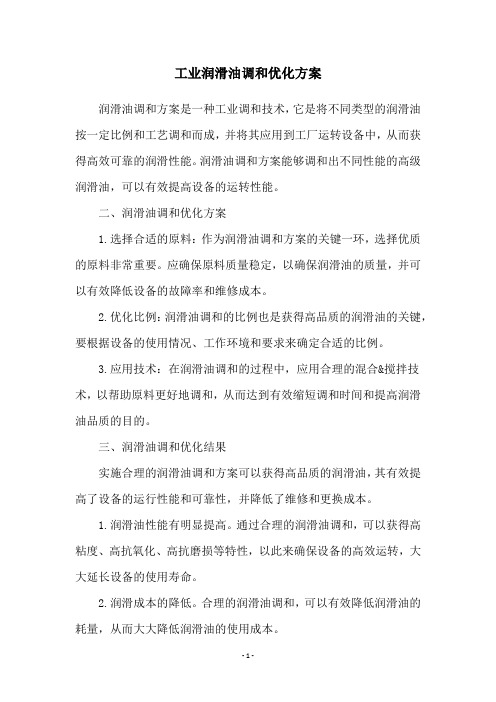
工业润滑油调和优化方案
润滑油调和方案是一种工业调和技术,它是将不同类型的润滑油按一定比例和工艺调和而成,并将其应用到工厂运转设备中,从而获得高效可靠的润滑性能。
润滑油调和方案能够调和出不同性能的高级润滑油,可以有效提高设备的运转性能。
二、润滑油调和优化方案
1.选择合适的原料:作为润滑油调和方案的关键一环,选择优质的原料非常重要。
应确保原料质量稳定,以确保润滑油的质量,并可以有效降低设备的故障率和维修成本。
2.优化比例:润滑油调和的比例也是获得高品质的润滑油的关键,要根据设备的使用情况、工作环境和要求来确定合适的比例。
3.应用技术:在润滑油调和的过程中,应用合理的混合&搅拌技术,以帮助原料更好地调和,从而达到有效缩短调和时间和提高润滑油品质的目的。
三、润滑油调和优化结果
实施合理的润滑油调和方案可以获得高品质的润滑油,其有效提高了设备的运行性能和可靠性,并降低了维修和更换成本。
1.润滑油性能有明显提高。
通过合理的润滑油调和,可以获得高粘度、高抗氧化、高抗磨损等特性,以此来确保设备的高效运转,大大延长设备的使用寿命。
2.润滑成本的降低。
合理的润滑油调和,可以有效降低润滑油的耗量,从而大大降低润滑油的使用成本。
3.使用润滑油更安全、更可靠。
润滑油调和方案对润滑油性能进行了优化,使得润滑油不仅能提供高效的润滑性能,而且安全可靠,能够有效抑制设备的故障率。
四、总结
润滑油调和方案是一项重要的工业应用技术,它能够有效提高设备的运转性能,降低设备的维修和更换成本,并能帮助企业节省大量的投资。
正确使用此类方案,能有效提高企业的效益,是企业可持续发展的重要因素。
润滑油基础油的生产工艺优化选择
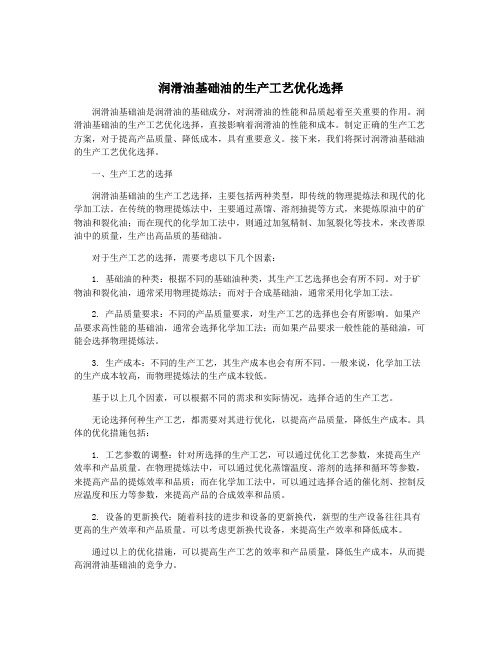
润滑油基础油的生产工艺优化选择润滑油基础油是润滑油的基础成分,对润滑油的性能和品质起着至关重要的作用。
润滑油基础油的生产工艺优化选择,直接影响着润滑油的性能和成本。
制定正确的生产工艺方案,对于提高产品质量、降低成本,具有重要意义。
接下来,我们将探讨润滑油基础油的生产工艺优化选择。
一、生产工艺的选择润滑油基础油的生产工艺选择,主要包括两种类型,即传统的物理提炼法和现代的化学加工法。
在传统的物理提炼法中,主要通过蒸馏、溶剂抽提等方式,来提炼原油中的矿物油和裂化油;而在现代的化学加工法中,则通过加氢精制、加氢裂化等技术,来改善原油中的质量,生产出高品质的基础油。
对于生产工艺的选择,需要考虑以下几个因素:1. 基础油的种类:根据不同的基础油种类,其生产工艺选择也会有所不同。
对于矿物油和裂化油,通常采用物理提炼法;而对于合成基础油,通常采用化学加工法。
2. 产品质量要求:不同的产品质量要求,对生产工艺的选择也会有所影响。
如果产品要求高性能的基础油,通常会选择化学加工法;而如果产品要求一般性能的基础油,可能会选择物理提炼法。
3. 生产成本:不同的生产工艺,其生产成本也会有所不同。
一般来说,化学加工法的生产成本较高,而物理提炼法的生产成本较低。
基于以上几个因素,可以根据不同的需求和实际情况,选择合适的生产工艺。
无论选择何种生产工艺,都需要对其进行优化,以提高产品质量,降低生产成本。
具体的优化措施包括:1. 工艺参数的调整:针对所选择的生产工艺,可以通过优化工艺参数,来提高生产效率和产品质量。
在物理提炼法中,可以通过优化蒸馏温度、溶剂的选择和循环等参数,来提高产品的提炼效率和品质;而在化学加工法中,可以通过选择合适的催化剂、控制反应温度和压力等参数,来提高产品的合成效率和品质。
2. 设备的更新换代:随着科技的进步和设备的更新换代,新型的生产设备往往具有更高的生产效率和产品质量。
可以考虑更新换代设备,来提高生产效率和降低成本。
润滑油基础油的生产工艺优化选择
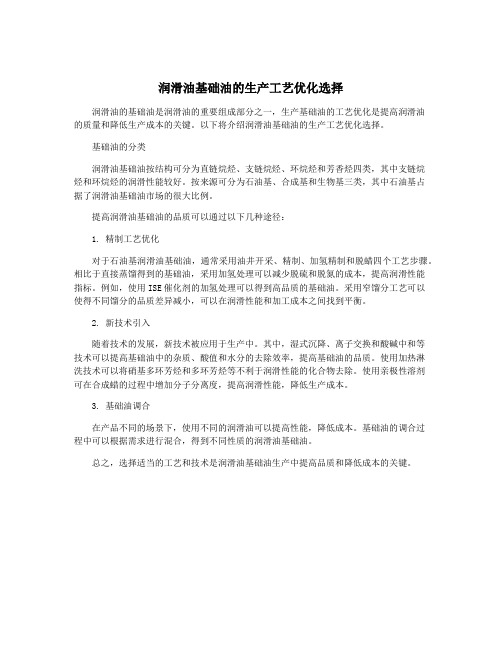
润滑油基础油的生产工艺优化选择
润滑油的基础油是润滑油的重要组成部分之一,生产基础油的工艺优化是提高润滑油
的质量和降低生产成本的关键。
以下将介绍润滑油基础油的生产工艺优化选择。
基础油的分类
润滑油基础油按结构可分为直链烷烃、支链烷烃、环烷烃和芳香烃四类,其中支链烷
烃和环烷烃的润滑性能较好。
按来源可分为石油基、合成基和生物基三类,其中石油基占
据了润滑油基础油市场的很大比例。
提高润滑油基础油的品质可以通过以下几种途径:
1. 精制工艺优化
对于石油基润滑油基础油,通常采用油井开采、精制、加氢精制和脱蜡四个工艺步骤。
相比于直接蒸馏得到的基础油,采用加氢处理可以减少脱硫和脱氮的成本,提高润滑性能
指标。
例如,使用ISE催化剂的加氢处理可以得到高品质的基础油。
采用窄馏分工艺可以
使得不同馏分的品质差异减小,可以在润滑性能和加工成本之间找到平衡。
2. 新技术引入
随着技术的发展,新技术被应用于生产中。
其中,湿式沉降、离子交换和酸碱中和等
技术可以提高基础油中的杂质、酸值和水分的去除效率,提高基础油的品质。
使用加热淋
洗技术可以将硝基多环芳烃和多环芳烃等不利于润滑性能的化合物去除。
使用亲极性溶剂
可在合成蜡的过程中增加分子分离度,提高润滑性能,降低生产成本。
3. 基础油调合
在产品不同的场景下,使用不同的润滑油可以提高性能,降低成本。
基础油的调合过
程中可以根据需求进行混合,得到不同性质的润滑油基础油。
总之,选择适当的工艺和技术是润滑油基础油生产中提高品质和降低成本的关键。
浅析润滑油调合的先进工艺与应用
浅析润滑油调合的先进工艺与应用摘要:本文主要对国内润滑油调节的先进工艺进行了简单的分析,并且对润滑油调节应用进行了阐述。
关键词:润滑油调和;先进工艺;应用前言:随着我国经济的不断发展,我国的各大市场竞争极其激烈,对于润滑油市场也是如此,一个润滑油厂,可以调合很多种润滑油,并且这些厂家既可以做到小批量生产,同时也能够大批量的批发,可以满足消费者的各种需求,对于润滑油的调合,主要是利用一种自动调合系统,这个系统主要包括在线管道调合应用、自动批量调合以及同步计量调合,可以适应各种润滑油的批量生产。
一、润滑油调合的先进工艺1.1在线管道调合系统在线管道调合系统主要分为两个部分,分别是调合站以及计算机管理系统,调合站主要有四个到九个通道,并且这些通道主要适合一定的比例范围组分,最大的通道主要是基础油,最小的通道主要适用于桶装添加剂,每一个调合通道都会设置一些空气干燥器、温度传感器以及各种控制阀等。
在进行操作时,系统可以实现高精确的配比度,同时也可以实现成品油质量的优化控制。
在线管道调合系统的主要特点是生产速度快,并且调合的过程是全自动调合,系统具有很强的生产效率,该系统的生产量不能够低于50立方米。
调合时,管道内部不能够存在杂质,必须要保证清洁。
对于一些低比例的添加剂,必须要先将其稀释成母液。
1.2自动批量调合系统自动调合系统主要有两种类型,第一种是将所有的基础油以及散装添加剂在调合釜的顶部管道,利用质量流量计对各个组分进行计量,使其能够进入调合釜。
第二种则是将各个组分依次进入称重罐。
主控系统通过调合量进行相应的计算,最后,将所有的组分利用称重罐送入一个加热控制的调合釜。
在调合之后,将这些调合的部分送入储存罐。
主要的工作步骤,首先是进料,将所有的基础油以及调合剂送入调合釜,工作人员将固体添加剂灌入,其次,在规定的温度向,进行搅拌,使其均匀,并且在调合之后,将物料送入一个储罐,然后,将调合釜利用基础油进行清洗,将清洗之后的油送入到成品储罐。
调和技术
随着能源枯竭这一问题的日益突出,作为炼油行业末端的润滑油产业,高效生产、节能降耗将成为实现可持续发展的必然之路,面临巨大的压力,许多润滑油企业通过技术改造,优化物流,精益生产来降低消耗,消化成本上升对企业生产经营的影响,因此大批先进的润滑油生产工艺及其装置被引入现今的润滑油生产中来,其中SMB、ABB以及ILB是现代润滑油调合过程较为先进的调合生产工艺,现将这三种工艺的应用情况进行阐述。
同步计量自动调合SMB(Simultaneous Metering Blender),在大批量润滑油生产过程中具有效率高、能耗低以及计量准确的优势;自动批量调合ABB(Automatic Batch Blender)适应于批量小、原料种类多、原料加入精度要求高特点下的小批量生产;在线调合ILB(In Line Blender)适合在原料质量水平稳定、产品分析周期短、批量大状况下的快速生产。
1、同步计量自动调合技术(SMB)同步计量自动调合,目前国际上ABB和FMC公司的润滑油调合技术较为成熟,也为国际石油公司在中国的润滑油生产厂所普遍使用,无论是ABB还是FMC其装置的主要组成大同小异,调合单元主要包括:计量回路(计量通道)、给料系统、调合母管。
若以一个具有4计量通道的SMB系统,可最多同时进行4种组分的注入的SMB系统举例,一次调合280吨某润滑油产品的过程。
整个调合生产过程包括:调合设备启动、注料、原料切换、管线清洗及冲扫以及储罐油品脉冲搅拌,整个生产周期所需时间为315min,而注完料的储罐油品脉冲搅拌时间只有100min,为对比SMB调合工艺与原采用加剂槽配母液,泵循环传统调合生产工艺两者的效率,将同样的生产计划采用加剂槽配母液,泵循环传统调合工艺进行生产,采用调合完毕后储罐三点测粘度的方法,判定油品是否混合均匀。
对比传统工艺和SMB装置工艺生产同品种280吨产品所需时间,SMB装置的时间大大综合。
SMB调合工艺在大批量的油品调合生产中较传统的加剂槽配母液,泵循环传统调合工艺可将生产周期缩短60%,其投料精度也远远高于传统计量方式。
浅析润滑油调和工艺技术的研究
浅析润滑油调和工艺技术的研究作者:闫雪梅来源:《城市建设理论研究》2013年第31期【摘要】随着汽车工业和机械工业的发展,对于高品质润滑油的需求量不断增加,单用炼油厂直接分离得到的润滑油基础油已经不能生产负荷高品质润滑油规格标准要求要求的润滑油产品,也就无法满足各类机械设备的润滑要求,所以各类润滑油产品加快了升级改造的步伐。
这也促使了润滑油调和技术和工艺的不断完善,不断的推出新产品。
为此,本文主要针对润滑油调和工艺技术进行了分析,旨在提高我国润滑油的质量和调和油产品的使用。
【关键词】润滑油,调和油,调和工艺,技术中图分类号:TE65文献标识码:A随着工业润滑油向着长寿命、节能、环保方向的发展,对于润滑油的抗氧化性、氧化安定性、粘度指数和挥发性等性能提出了新的要求。
而目前机械设备、汽车制造、钢铁工业等对高品质润滑油的需求不是采用传统方式直接分离得到的润滑油基础油所能达到的,所以对润滑油实现在加工生产是必然的。
为了实现高品质润滑油的生产,润滑油生产厂家一般根据润滑油产品的特定和性质,选择一种或者多种润滑油基础油,在加入多种添加剂,在特定的调和设备中经过一定的调和工艺进行加工,从而得到合格的润滑油产品—调和油。
尽管润滑油在调和的过程中多为物理的调和过程,并不存在化学反应,但是为了更好是现实对高品质润滑油的要求,润滑油调和工艺也处于不断完善过程中。
润滑油的调和工艺在我国的炼厂中,润滑油调和的工艺主要分为罐式调和管道调和两种方式,不同的润滑油调和方式有不同的特点和使用情况。
1.1润滑油的罐式调和润滑油的罐式调和工艺是将需要进行调和的基础油、添加剂等根据一定的调和比例,分别放入调和罐中,在助泵循环的作用下,经过电动搅拌等方式,将调和罐中的基础油和添加剂均匀混合成调和油。
罐式调和的工艺和设备相对比较简便,易操作,装置的投资比较少,适用于生产小批量和组分多的调和油,同时对于非流动体状态添加剂的润滑油产品的调和也同样适用。
润滑油调和工艺详解-- 管道调和
润滑油过滤,润滑油过滤设备,润滑油过滤器,润滑油过滤机,润滑油过滤袋,润滑油粘度,润滑油检测,润滑油生产工艺,润滑油润滑油调和工艺详解--管道调和1.润滑油调合工艺类型常见的润滑油调合工艺,一般分两种基本类型:罐式调合和管道调合。
不同的调合工艺具有独特的特点和适用不同的场合。
管道调合是将润滑油配方中的基础油、添加剂组分,按照计算好的比例,同时送入总管和混合器,经过均匀混合后即为成品油,其理化指标和使用性能即可达到技术要求,可以直接灌装或送入储罐。
管道调合通过实时在线调整管道泵的转速,以使得各条管道中原料油的流量进行动态地调整,以达到预设定的比例,保证最优的调合精度。
另外一种管道调合,也是通过管道加入添加剂,经过管道上流量计计量,但需要在调合罐中混合均匀方为成品油。
见下图。
润滑油调合广泛应用计算机自动控制技术和在线分析仪表,具有自动化程度高、调合质量好、计量精度高及品种调换灵活等特点。
图2:管道调合示意图润滑油过滤,润滑油过滤设备,润滑油过滤器,润滑油过滤机,润滑油过滤袋,润滑油粘度,润滑油检测,润滑油生产工艺,润滑油2.管道调合2.1.管道调合系统的构成管道调合也称连续调合。
调合系统由主控计算机控制,计算机中可预先输入配方,操作人员只需输入产品名称和调合量,计算机自动计算、控制各组分的投料量,动态画面可以显示整个操作过程中各部分的运行状态,通过色彩变化显示物流方向和设备起用情况,可对现场的设备、阀门进行监控和连锁停泵,对油罐高液位和设备故障报警,还可打印报表。
这些也是自动调合系统的共同特点。
管道调合装置的一般构成:①储罐:基础油罐、添加剂罐、调合罐/成品油罐②组分通道:每个通道包括配料泵、计量表、过滤器、排气罐、温度传感器、止回阀、压力调节阀等。
组分通道的配备需要综合考虑原料种类、配方组分结构和配比、总体产品结构、预计产量等因素。
通道口径和泵的排量由装置的调合能力和组分的配比决定。
③集合管、混合器和脱水器:各组分通道与总管相连,各组分按规定比例汇集到集合管;进入混合器混合均匀;脱水器将油中的微量水脱出,一般为真空脱水器。
- 1、下载文档前请自行甄别文档内容的完整性,平台不提供额外的编辑、内容补充、找答案等附加服务。
- 2、"仅部分预览"的文档,不可在线预览部分如存在完整性等问题,可反馈申请退款(可完整预览的文档不适用该条件!)。
- 3、如文档侵犯您的权益,请联系客服反馈,我们会尽快为您处理(人工客服工作时间:9:00-18:30)。
两种润滑油调合工艺技术的对比
1.润滑油调合工艺类型
常见的润滑油调合工艺,一般分两种基本类型:罐式调合和管道调合。
不同的调合工艺具有独特的特点和适用不同的场合。
罐式调合是将基础油和添加剂按比例直接送入调合罐,经过搅拌后,即为成品油。
罐式调合系统主要包括成品罐、混合装置、加热系统、散装和桶状添加剂的加入装置、计量设备、机泵和管线等基础设施及过程控制系统。
一些系统中抽桶装置的应用避免了桶装添加剂加入时各种杂质对产品质量的影响,也减少了添加剂对环境的污染;一些桶抽取装置具有清洗功能,将添加剂残留损耗降低到最低限度。
管道调合是将润滑油配方中的基础油、添加剂组分,按照计算好的比例,同时送入总管和混合器,经过均匀混合后即为成品油,其理化指标和使用性能即可达到技术要求,可以直接灌装或送入储罐。
2.罐式调合和管道调合两种调合工艺的比较
罐式调合是把定量的各调合组分依次加入到调合罐中,加料过程中不需要控制组分的流量,只需确定各组分最后的数量。
还可以随时补加某种不足的组分,直至产品完全符合规格标准。
这种调合方法,工艺和设备均比较简单,不需要精密的流量计和高度可靠的自动控制手段,也不需要在线的质量检测手段。
因此,建设此种调合装置所需投资少,易于实现。
此种调合装置的生产能力受调合罐大小的限制,只要选择合适的调合罐,就可以满足一定生产能力的要求,但劳动强度大。
新型自动批量调合的自动化程度高,计量精确,合格率高,适合不同客户的特殊需求,以及新产品的试生产的需要。
管道调合是把全部调合组分以正确的比例同时送入调合装置进行调合,从管道的出口即得到质量符合规格要求的最终产品。
这种调合方法需要有满足混合要求的连续混合器,润滑油过滤,润滑油过滤设备,润滑油过滤器,润滑油过滤机,润滑油过滤袋,润滑油粘度,润滑油检测,润滑油生产工艺,润滑油
润滑油过滤,润滑油过滤设备,润滑油过滤器,润滑油过滤机,润滑油过滤袋,润滑油粘度,润滑油检测,润滑油生产工艺,润滑油需要有能够精确计量、控制各组分流量的计量设备和控制手段,还要有在线质量分析仪表和计算机控制系统。
需要设备和过程控制具有高度的稳定性。
所以连续调合可以实现优化控制,合理利用资源,减少不必要的质量过剩,从而降低成本。
连续调合顾名思义是连续进行的,其生产能力取决于组分罐和成品罐容量的大小。
综上所述,罐式调合适合批量小、组分多的,具有特殊工艺要求或特殊产品特性的油品调合,在产品品种多、缺少计算机技术装备的条件下更能发挥其作用。
而生产规模大、品种和组分数较少,又有足够的吞吐储罐容量和资金能力时,管道调合则更有其优势。
批量调合一般情况下,设备简单,投资较少;管道调合相对投资较大。
具体应用中,需作具体的可行性研究,根据经济、技术分析而确定。
润滑油调和灌装工艺流程图
润滑油过滤,润滑油过滤设备,润滑油过滤器,润滑油过滤机,润滑油过滤袋,润滑油粘度,润滑油检测,润滑油生产工艺,润滑油润滑油过滤解决方案-卓品科技应用工艺点过滤精度过滤效率过滤目的推荐过滤形式
泵前管道过滤器75/100um 公称过滤精度去除大颗粒杂质保护后端的泵
卓品T 型管道过
滤器包装前精细过滤1/5/0.5u m 90%以上过滤效率管道杂质,添加剂带入的杂质,空气中的灰尘等卓品Bag-Well 高效率过滤袋
包装前精细过滤5/10/1um 90%以上过滤效率管道杂质,添加剂带入的杂质,空气中的灰尘等卓品C2B-Well 芯式滤袋。