表面粗糙度概念及测量方法
表面粗糙度的测量方法

环境振动和噪声会影响测量结果的准确性,应采取措施减小或消除这些因素的 影响。
测量误差的来源与控制
误差来源分析
表面粗糙度的测量误差可能来源于测 量设备、被测表面、操作人员和环境 条件等多个方面。
误差控制措施
为减小测量误差,应对各个方面的误 差源进行分析和控制,如提高操作人 员的技能水平、加强设备维护和校准 等。
触针法
总结词
利用触针接触表面并测量其微观不平度的度测量方法之一。它通过将一个微小的触针置于 待测表面上,利用传感器记录触针在表面上的起伏变化,从而测量表面的微观不 平度。该方法精度高,适应性强,但可能会对表面造成轻微划痕。
印模法
总结词
通过复制表面微观形貌并进行分析的方法。
表面粗糙度的测量方法
目录 CONTENT
• 表面粗糙度概述 • 接触式测量方法 • 非接触式测量方法 • 测量方法的选用与注意事项
01
表面粗糙度概述
定义与重要性
定义
表面粗糙度是指物体表面微观不 平度的程度,通常是指在加工过 程中留下的痕迹。
重要性
表面粗糙度对物体的使用性能和 寿命有着重要影响,如耐磨性、 抗腐蚀性、接触刚度等。
光学显微镜法
总结词
利用光学显微镜观察表面形貌来测量表 面粗糙度
VS
详细描述
光学显微镜法是利用光学显微镜观察表面 形貌,通过观察到的表面形貌特征来测量 表面粗糙度的一种非接触式测量方法。通 过调整显微镜的放大倍数和焦距,可以观 察到不同尺度下的表面形貌特征,从而测 量表面粗糙度的大小。
扫描隧道显微镜法
糙度值增大。
工件材料
工件材料的硬度、韧性 等物理性质对表面粗糙
度有影响。
粗糙度检测方法及评定【干货技巧】
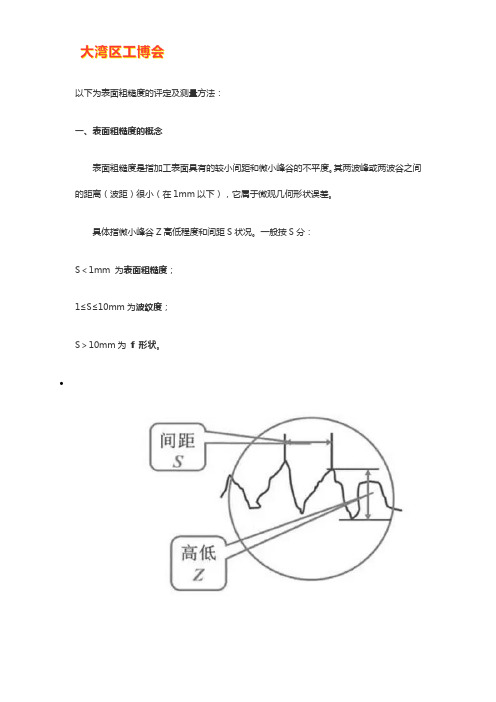
以下为表面粗糙度的评定及测量方法:一、表面粗糙度的概念表面粗糙度是指加工表面具有的较小间距和微小峰谷的不平度。
其两波峰或两波谷之间的距离(波距)很小(在1mm以下),它属于微观几何形状误差。
具体指微小峰谷Z高低程度和间距S状况。
一般按S分:S<1mm 为表面粗糙度;1≤S≤10mm为波纹度;S>10mm为f 形状。
•二、VDI3400、Ra、Rmax对照表国家标准规定常用三个指标来评定表面粗糙度(单位为μm):轮廓的平均算术偏差Ra、不平度平均高度Rz和最大高度Ry。
在实际生产中多用Ra指标。
轮廓的最大微观高度偏差Ry在日本等国常用Rmax符号来表示,欧美常用VDI指标。
下面为VDI3400、Ra、Rmax 对照表。
三、表面粗糙度形成因素表面粗糙度一般是由所采用的加工方法和其他因素所形成的,例如加工过程中刀具与零件表面间的摩擦、切屑分离时表面层金属的塑性变形以及工艺系统中的高频振动、电加工的放电凹坑等。
由于加工方法和工件材料的不同,被加工表面留下痕迹的深浅、疏密、形状和纹理都有差别。
四、表面粗糙度对零件的影响主要表现影响耐磨性。
表面越粗糙,配合表面间的有效接触面积越小,压强越大,摩擦阻力越大,磨损就越快。
影响配合的稳定性。
对间隙配合来说,表面越粗糙,就越易磨损,使工作过程中间隙逐渐增大;对过盈配合来说,由于装配时将微观凸峰挤平,减小了实际有效过盈,降低了连接强度。
影响疲劳强度。
粗糙零件的表面存在较大的波谷,它们像尖角缺口和裂纹一样,对应力集中很敏感,从而影响零件的疲劳强度。
影响耐腐蚀性。
粗糙的零件表面,易使腐蚀性气体或液体通过表面的微观凹谷渗入到金属内层,造成表面腐蚀。
影响密封性。
粗糙的表面之间无法严密地贴合,气体或液体通过接触面间的缝隙渗漏。
影响接触刚度。
接触刚度是零件结合面在外力作用下,抵抗接触变形的能力。
机器的刚度在很大程度上取决于各零件之间的接触刚度。
影响测量精度。
零件被测表面和测量工具测量面的表面粗糙度都会直接影响测量的精度,尤其是在精密测量时。
表面粗糙度的测量方法1

y
i 1
5
pi
y vi
i 1
5
5
在取样长度内,也可从平行于轮廓中线m的任意一根线算起, 计算被测轮廓的五个最高点(峰)到五个最低点(谷)之间 的平均距离
Rz
(h2 h4 ...h10 ) (h1 h3 ...h9 ) = 5
3.轮廓最大高度
在取样长度内,轮廓峰顶线和轮廓谷底线之间的距离 (图4-3)。
实际工作中,对加工表面粗糙度的评 定可归纳为如下四种方式。
1.与表面粗糙度标准样板比较的方法
表面粗糙度样板:按各种加工方法做成的不同几何形状的 一套标准表面样块,用来与被测的表面 相比较。
表面粗糙度样板
测量方法:
目测法:Ra值2.5-80m的表面;
用5~10倍放大镜比较:Ra值0.32-2.5m的表面;
(2)算术平均中线: 在取样长度范围内,划分实际轮廓为上、下两部分, 且使上下两部分面积相等的线。
轮廓的算术平均中线
二、评定参数及数值:
对评定参数的基本要求:
(1)正确、充分反映表面微观几何形状特征;
(2)具有定量的结果; (3)测量方便。
国标从水平和高度两方向各规定了三个评定参数:三个基本 参数(水平),三个附加的评定参数(高度)
图4-5 光切原理
2.测量仪器原理及定度
(1)原理 光切显微镜的光路原理如图4-6所示。用测微目镜量出a、 a’的距离N,即可求出峰谷间的高度。
图4-6 光切显微镜光路
由于物镜分辨率及景深的限制,光切法测量范围一般为:
Rz= (80~0.8)m(旧国标3~9)。
表面粗糙度的测量方法
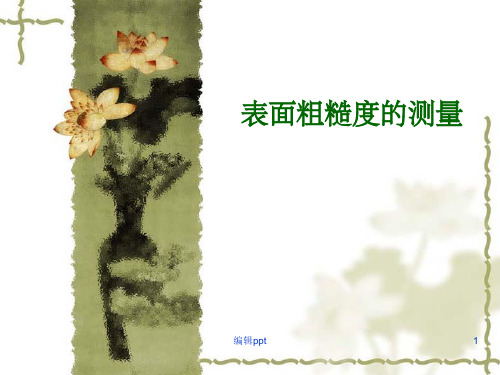
编辑ppt
1
第一节表面粗糙度的评定参数
主要内容:
1、主要术语及定义
取样长度L
评定长度L
n
轮廓中线m
2、6个评定参数
3个基本、3个附加
3、一般规定
重点: 3个基本评定参数
编辑ppt
2
一.主要术语及定义
1.实际轮廓:平面与实际表面相交所得的轮廓线。
按照相截方向的不同,它又可分为横向实际轮廓和纵向实 际轮廓。在评定或测量表面粗糙度时,除非特别指明,通 常均指横向实际轮廓,即与加工纹理方向垂直的截面上的 轮廓。
编辑ppt
17
取得表面测量信号以后,亦可用人工进行计算处理给出结果。
编辑ppt
18
❖ 15.2 表面粗糙度测量的基本原则
❖
(1)测量方向
❖
按现行标准所定义的各种粗糙度评定参数,是基于轮廓法确定数值,
是在被测表面的法向截面上的实际轮廓上进行测量的结果。由于垂直于
被测表面的法向截面存在各种不同的测量方向.试验表明,大多数的切
削加工表面,在横向轮廓上测得的粗糙度数值比较大,只是有的该铣加
工和个别端铣加工表面,在纵向轮廓上会有较大的数值。 如果在被测表
面上难以确定加工纹理方向,以及某些加工纹理紊乱或不存在固定方向
的表面,应分别在多个方向上测量,以获取最大参故值为结果.或取其
峰谷高度的最大值,计算一个区域的测量结果。
❖
编辑ppt
❖ 15.1 测量方法综述
❖ 对加工表面质量的评定,除了用视觉和触觉进行定性地比较检验的方 法以外,并逐步实现了用数值确定表面粗糙度参数值的定量测量。从本 世纪30年代陆续提出了测量粗糙度的方法原理和仪器以来,已发展了一 系列利用光学、机械、电气原理的表面粗糙度专用测量仪器,其基本结 构模式如图9—7所示。
表面粗糙度和表面光洁度

表面粗糙度和表面光洁度表面粗糙度和表面光洁度是表征物体表面质量的两个重要指标。
它们直接影响着物体的外观、触感以及物体与周围环境的相互作用。
本文将从不同角度解释和探讨表面粗糙度和表面光洁度的概念、测量方法以及对物体性能的影响。
一、表面粗糙度的概念和测量方法表面粗糙度是指物体表面不平整的程度。
在我们的日常生活中,我们可以通过肉眼观察或触摸来感知物体的表面粗糙度。
然而,为了更加准确地描述和测量表面粗糙度,科学家们提出了一系列量化指标和测量方法。
常用的表面粗糙度指标包括Ra(平均粗糙度)、Rz(平均最大峰谷高度)等。
这些指标可以通过光学仪器、扫描仪和原子力显微镜等设备进行测量。
其中,原子力显微镜是一种非常精确的测量工具,它可以在纳米级别测量表面的高度差异。
表面粗糙度的测量方法通常可以分为两类:接触法和光学法。
接触法是通过表面测高仪等设备直接接触物体表面来测量表面的高度差异。
光学法则是利用光的反射、散射等特性来测量表面的粗糙度。
这两种方法各有优缺点,根据不同的应用场景和要求选择合适的测量方法。
二、表面光洁度的概念和测量方法表面光洁度是指物体表面的反射能力,也可以理解为表面的光滑程度。
一般来说,光洁度越高,物体表面的反射能力越强,外观越亮丽。
表面光洁度的测量方法主要有两种:视觉法和光学法。
视觉法是通过肉眼观察物体表面的光洁度,比较主观。
光学法则是利用光的反射、透射等特性来测量表面的光洁度。
常用的测量设备包括光泽仪、反光度计等。
三、表面粗糙度和表面光洁度对物体性能的影响表面粗糙度和表面光洁度对物体的性能有着重要的影响。
首先,它们影响着物体的摩擦特性。
当表面粗糙度增加时,物体与其他物体之间的摩擦力也会增加。
此外,表面粗糙度还对物体的润滑性能、磨损寿命等方面有着重要的影响。
表面粗糙度和表面光洁度还影响着物体的光学性能。
对于光学元件来说,表面光洁度是一个非常重要的指标。
如果表面存在较大的粗糙度或缺陷,会导致光的散射、吸收等现象,降低光学元件的传输效率。
机械制造中的机械加工表面粗糙度工作原理

机械制造中的机械加工表面粗糙度工作原理机械加工是指通过削、切、磨等工艺将工件原有形状进行改变以满足一定尺寸、形状和粗糙度要求的加工方法。
在机械制造过程中,机械加工表面粗糙度的控制是十分重要的,它直接影响到零件的功能和使用寿命。
本文将介绍机械加工表面粗糙度的工作原理。
一、表面粗糙度的概念表面粗糙度是指工件表面上凹凸不平的程度,通常用Ra(平均粗糙度)来表示。
在机械加工中,我们常常要求工件表面光洁度高、粗糙度小,以确保零件的密封性、运动性和装配性能。
二、机械加工表面粗糙度的影响因素机械加工表面粗糙度受到多种因素的影响,主要包括以下几个方面:1.切削参数:切削速度、进给量、切削深度等切削参数直接影响到工件表面的质量。
一般来说,切削速度越大、进给量越小、切削深度越小,工件表面的粗糙度就越小。
2.切削工具状况:切削工具的磨损情况对工件表面质量有重要影响。
切削工具磨损过度会导致切削力增大、表面粗糙度加大。
所以,及时更换和修磨切削工具能够有效控制表面粗糙度。
3.工件材料:工件材料的硬度、韧性等性质会影响机械加工的精度和表面质量。
例如,硬度较高的材料可能导致切削刀具的磨损,从而影响表面的粗糙度。
4.切削方式:不同的切削方式,如车削、铣削、磨削等,对工件表面粗糙度的影响也有所不同。
三、机械加工表面粗糙度的控制方法为了能够控制机械加工表面的粗糙度,在实际操作中可以采取以下措施:1.选择合适的工艺参数:根据工件材料、形状和要求,合理选择切削速度、进给量、切削深度等参数,以获得较小的粗糙度。
2.使用高质量的切削工具:选择具有良好刚性和耐磨性的切削工具,并保持其锋利度,以便实现更好的切削效果。
3.优化切削方式:根据工件的特点,选择合适的切削方式。
有时候,可以采用一些先进的切削方式,如超声波切削、电火花加工等,以改善表面粗糙度。
4.后续加工工艺:有时候,机械加工的表面粗糙度无法满足要求,可以考虑通过后续加工工艺来改善。
例如,研磨、抛光等方法可以使工件表面更加光滑。
粗糙度测量标准
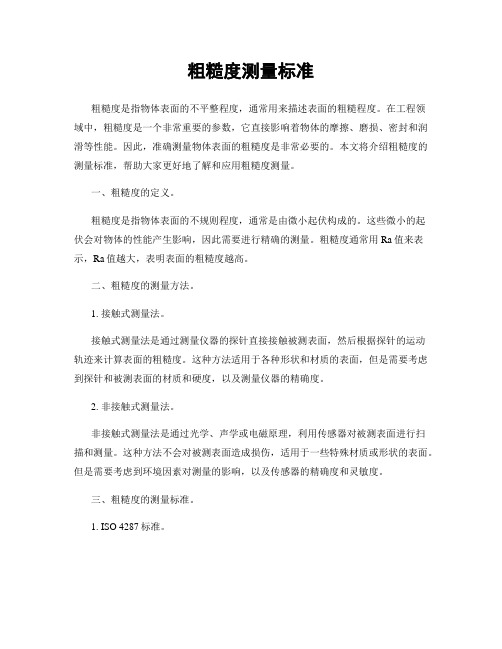
粗糙度测量标准粗糙度是指物体表面的不平整程度,通常用来描述表面的粗糙程度。
在工程领域中,粗糙度是一个非常重要的参数,它直接影响着物体的摩擦、磨损、密封和润滑等性能。
因此,准确测量物体表面的粗糙度是非常必要的。
本文将介绍粗糙度的测量标准,帮助大家更好地了解和应用粗糙度测量。
一、粗糙度的定义。
粗糙度是指物体表面的不规则程度,通常是由微小起伏构成的。
这些微小的起伏会对物体的性能产生影响,因此需要进行精确的测量。
粗糙度通常用Ra值来表示,Ra值越大,表明表面的粗糙度越高。
二、粗糙度的测量方法。
1. 接触式测量法。
接触式测量法是通过测量仪器的探针直接接触被测表面,然后根据探针的运动轨迹来计算表面的粗糙度。
这种方法适用于各种形状和材质的表面,但是需要考虑到探针和被测表面的材质和硬度,以及测量仪器的精确度。
2. 非接触式测量法。
非接触式测量法是通过光学、声学或电磁原理,利用传感器对被测表面进行扫描和测量。
这种方法不会对被测表面造成损伤,适用于一些特殊材质或形状的表面。
但是需要考虑到环境因素对测量的影响,以及传感器的精确度和灵敏度。
三、粗糙度的测量标准。
1. ISO 4287标准。
ISO 4287标准是国际上公认的粗糙度测量标准,它规定了粗糙度测量的方法和参数。
根据ISO 4287标准,粗糙度的测量应该包括三个参数,Ra、Rz和Rmax。
这些参数可以全面地描述表面的粗糙度特征,对于工程应用非常有价值。
2. ANSI标准。
ANSI标准是美国国家标准协会制定的粗糙度测量标准,它与ISO 4287标准类似,也是通过Ra、Rz和Rmax等参数来描述表面的粗糙度。
但是与ISO 4287标准相比,ANSI标准在参数的计算方法和测量范围上有所不同,需要根据实际情况进行选择和应用。
四、粗糙度测量的应用。
粗糙度测量在工程领域有着广泛的应用,主要包括以下几个方面:1. 材料加工。
在材料加工过程中,粗糙度测量可以帮助工程师更好地控制加工质量,提高加工效率和产品性能。
机械加工表面粗糙度解释及测量

較低的光潔度對于盡快加工零件和盡量減 少輔助工作量有明顯的經濟效益。何況 在某些用途中﹐一定的粗糙性可以提高 零件的功能﹐有些零件甚至明確規定了 最大和最小粗糙度的值。舉例來說﹐具 有一定粗糙度的表面常常可以增加漆層 或其它涂敷層的黏附性。
有些多功能零件要求很復雜的表面﹐才能 最好地發揮作用。比如發動機的汽缸內 壁必須足夠光滑﹐以便為活塞環提供良 好的密封表面﹐利于壓縮﹐並防止漏氣 。同時﹐表面上還必須具有尺寸﹑數量 和分布都合適的凹點﹐為的是保持潤滑 油。
Ry(ISO,JIS)
全粗糙度高度(最大高度)---Ry(ISO,JIS); Ry=(Peakmax-Valleymin)sampling
length
Ry(DIN)
全粗糙度高度(最大高度)--Ry(DIN); 在各取樣長度內, 求出各Zi, 而在各 Zi中最大值稱為Ry(DIN)=Rmax;
•Rmax對零件表面的劃傷﹑毛刺之類的缺 陷非常敏感﹐很適合于檢驗這樣的狀態 。然而﹐由于生產過程中的個別劃痕或 毛刺往往不具有代表性﹐所以Rmax不適 于監控工序的穩定性
.(Rmax)
Rq
粗糙度幾何(平方)平均值 (Root mean square roughness, Rq)
下圖所示, Rq=(1/N Σyi2)1/2
Rt
最大高度---Rt, 由全體評價長度算出, Rp 和Rv之和. Rt=(PeakmaxValleymin)assessment length
b. Shoe/Skid VS Skidless type stylus 之用法不同: 如圖所示
Shoe/Skid type:滑動器半徑比波峰間隔 (Sm)大很多,使其運動幾乎成一直線。 若Sm過大則可用Shoe來支撐。優點易 於歸零.
- 1、下载文档前请自行甄别文档内容的完整性,平台不提供额外的编辑、内容补充、找答案等附加服务。
- 2、"仅部分预览"的文档,不可在线预览部分如存在完整性等问题,可反馈申请退款(可完整预览的文档不适用该条件!)。
- 3、如文档侵犯您的权益,请联系客服反馈,我们会尽快为您处理(人工客服工作时间:9:00-18:30)。
其余 25
φ φ M φ
★ 在不同方向的
表面上标注时,代
3.2
号中的数字及符号
的方向必须按图中
的规定标注。
★ 代号中的数字
方向应与 尺寸数 字的方向 一致。
3.2
★ 符号的尖端必 须从材料 外指向 表面。
30° 3.2
3.2 3.2
30° 3.2
★ 当零件所有表面都有 相同表面粗糙度要求时, 可在图样右上角统一标注 代号。
表面粗糙度概念 及测量方法
表面粗糙度
一、表面粗糙度的基本概念
表示零件表面具有较小间距和峰谷所组成的微观几何形 状特性,称为表面粗糙度。
表面粗糙度对零件的配合性质、耐磨性、强度、抗腐性 密封性、外观要求等影响很大,因此,零件表面的粗糙度的 要求也有不同。一般说来,凡零件上有配合要求或有相对运 动的表面,表面粗糙度参数值要小。
六、表面粗糙度的常用测量方法
➢比较法:将被测表面和表面粗糙度样 板直接进行比较,多用于车间,评定 表面粗糙度值较大的工件。
➢光切法:利用光切原理,用双管显微 镜测量。 常用于测量Rz为0.5~60μm。
➢干涉法:利用光波干涉原理,用干涉 显微镜测量。可测量Rz和Ry值。
➢感触法:
同一零件上,工作表面比非工作表面粗糙度值 小;摩擦表面比非摩擦表面要小;受循环载荷的表 面要小;配合要求高、联接要求可靠、受重载的表 面粗糙度值都应小;同一精度,小尺寸比大尺寸、 轴比孔的表面粗糙度值要小。
2.参数的选用:首选主要评定参数1—2个,在常用 尺寸段内,选用Ra。附加评定参数必须与主要评定 参数连用。常用数值范围内,Ra=0.025—6.3, Rz=0.1—25μm,优先选用Ra.
二、评定表面粗糙度的参数
★ 轮廓算术平均偏差——Ra ★ 微观不平度十点高度——Ry ★ 轮廓最大高度——Rz 优先选用轮廓算术平均偏差Ra
三、表面粗糙度的代号(符)号及其标注
1、表面粗糙度的符号ba1 Nhomakorabeaa2
C(f)
ed
a1、a2——粗糙度高度参数代号及其数 值( μm );
b——加工要求、镀覆、表面处理或其它 说明等;
四、表面粗糙度代号在图样上的标注
★ 在同一图样上每一表面只注一次粗糙度代号,且应注 在可见轮廓线、尺寸界线、引出线或它们的延长线上,并 尽可能靠近有关尺寸线。
★ 当零件的大部分表面具有相同的粗糙度要求时,对其
中使用最多的一种,代(符)号,可统一注在图纸的右上
角。加注 “其余”二字。 例如:
C×45ο
注写Ra时,只写数值; 注写Rz、Ry时,应同时注出Rz、 Ry和数值。
只注一个值时,表示为上限值;注两个值时,表示为 上限值和下限值。
例如:
3.2 用任何方法获得的表面, Ra的上限值为3.2m。
3.2 1.6 用去除材料的方法获得的表面, Ra的上限值为3.2m,
下限值为1.6m。
Ry3.2 用任何方法获得的表面, Ry的上限值为3.2m。
基本符号加一小圆,表示表面是用不去除材料方法获得。 如铸、锻、冲压变形、热轧、冷轧、粉未冶金等,或者是用 于保持原供应状况的表面(包括保持上道工序的状况)。
在上述三个符号的长边上均可加一横线;用于标注有关参 数和说明。
在上述三个符号上均可加一小圆,表示所有表面具有相 同的表面粗糙度要求。
2、表面粗糙度参数: 表面粗糙度参数的单位是m。
c——样长度(mm)或波纹度( μm ); d——加工纹理方向符号; e——加工余量(mm) f——粗糙度间距参数值(mm)或轮廓支
承长度率。
符号
意 义及说 明
基本符号,表示表面可用任何方法获得。当不加注粗糙度 参数值或有关说明时,仅适用于简化代号标注。
基本符号加一短划,表示表面是用去除材料的方法获得。 如车、铣、磨、剪切、抛光、腐蚀、电火花加工、气割等。
★ 对不连续的同一表面, 可用细实线相连,其表 面粗糙度代号可注一次。
★ 零件上连续要素 及重复要素(孔、槽、 齿等)的表面,其表 面粗糙度代号只注一 次。
3.2
抛光 12.5 1.6
五、表面粗糙度的选用(GB/T1031——1995)
1.原则:首先应满足零件表面的功能要求,同时还应 顾及工艺的经济性。即:在满足零件表面功能要求 的前提下,尽量选取较大的参数值。