三牙轮钻头工艺流程
江汉三牙轮钻头使用说明
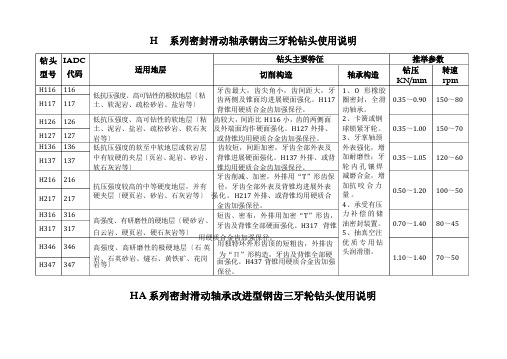
钻头IADC H系列密封滑动轴承钢齿三牙轮钻头使用说明钻头主要特征推举参数型号代码适用地层切削构造轴承构造钻压转速KN/mm rpm 低抗压强度、高可钻性的极软地层〔粘土、软泥岩、疏松砂岩、盐岩等〕牙齿最大,齿尖角小,齿间距大,牙齿两侧及锥面均进展硬面强化。
H117背锥用硬质合金齿加强保径。
1、O 形橡胶圈密封,全滑动轴承。
0.35~0.90 150~80低抗压强度、高可钻性的软地层〔粘齿较大,间距比H116 小,齿的两侧面土、泥岩、盐岩、疏松砂岩、软石灰及外端面均作硬面强化。
H127 外排、岩等〕或背锥均用硬质合金齿加强保径。
低抗压强度的软至中软地层或软岩层齿较短,间距加密,牙齿全部外表及中有较硬的夹层〔页岩、泥岩、砂岩、背锥进展硬面强化。
H137 外排、或背软石灰岩等〕锥均用硬质合金齿加强保径。
牙齿削减、加密,外排用“T”形齿保抗压强度较高的中等硬度地层,并有径,牙齿全部外表及背锥均进展外表硬夹层〔硬页岩、砂岩、石灰岩等〕强化。
H217 外排、或背锥均用硬质合金齿加强保径。
短齿、密布,外排用加密“T”形齿,高强度、有研磨性的硬地层〔硬砂岩、牙齿及背锥全部硬面强化。
H317 背锥白云岩、硬页岩、硬石灰岩等〕用硬质合金齿加强保径。
高强度、高研磨性的极硬地层〔石英用独特环外形齿顶的短粗齿,外排齿岩、石英砂岩、燧石、黄铁矿、花岗为“Π”形构造,牙齿及背锥全部硬面强化。
H437 背锥用硬质合金齿加强岩等〕2 、卡簧或钢球锁紧牙轮。
3 、牙掌轴颈外表强化,增加耐磨性;牙轮内孔镶焊减磨合金,增加抗咬合力量。
4 、承受有压力补偿的储油密封装置。
5 、抽真空注优质专用钻头润滑脂。
0.35~1.00 150~700.35~1.05 120~600.50~1.20 100~500.70~1.40 80~451.10~1.40 70~50保径。
HA 系列密封滑动轴承改进型钢齿三牙轮钻头使用说明H116 116H117 117 H126 126H127 127 H136 136H137 137 H216 216 H217 217 H316 316 H317 317 H346 346 H347 347适用地层钻头主要特征切削构造轴承构造推举参数 钻压 转速 KN/mm rpmHA137 137低抗压强度、高可钻性的极软地层 〔粘土、软泥岩、疏松砂岩、盐岩等〕低抗压强度、高可钻性的软地层 〔粘土、泥岩、盐岩、疏松砂岩、软石灰岩等〕低抗压强度的软至中软地层或软 岩层中有较硬的夹层〔页岩、泥岩、 牙齿最大,齿尖角小,齿间距大,牙齿两侧及锥面均进展硬面强化。
三牙轮钻头工作原理
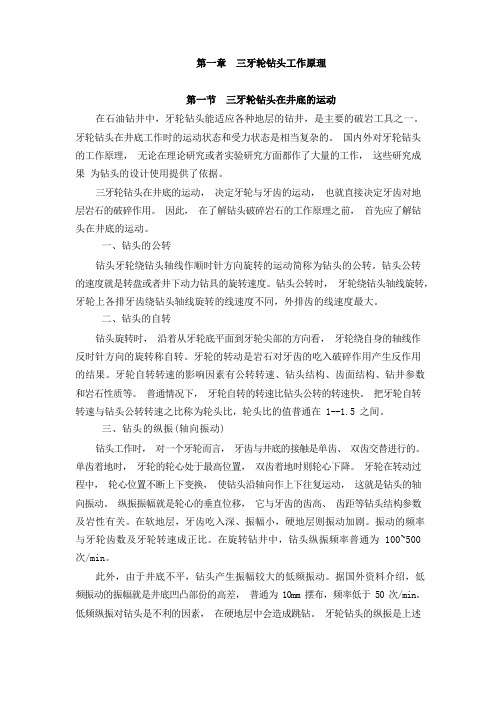
在石油钻井中,牙轮钻头能适应各种地层的钻井,是主要的破岩工具之一。
牙轮钻头在井底工作时的运动状态和受力状态是相当复杂的。
国内外对牙轮钻头的工作原理,无论在理论研究或者实验研究方面都作了大量的工作,这些研究成果为钻头的设计使用提供了依据。
三牙轮钻头在井底的运动,决定牙轮与牙齿的运动,也就直接决定牙齿对地层岩石的破碎作用。
因此,在了解钻头破碎岩石的工作原理之前,首先应了解钻头在井底的运动。
一、钻头的公转钻头牙轮绕钻头轴线作顺时针方向旋转的运动简称为钻头的公转。
钻头公转的速度就是转盘或者井下动力钻具的旋转速度。
钻头公转时,牙轮绕钻头轴线旋转,牙轮上各排牙齿绕钻头轴线旋转的线速度不同,外排齿的线速度最大。
二、钻头的自转钻头旋转时,沿着从牙轮底平面到牙轮尖部的方向看,牙轮绕自身的轴线作反时针方向的旋转称自转。
牙轮的转动是岩石对牙齿的吃入破碎作用产生反作用的结果。
牙轮自转转速的影响因素有公转转速、钻头结构、齿面结构、钻井参数和岩石性质等。
普通情况下,牙轮自转的转速比钻头公转的转速快。
把牙轮自转转速与钻头公转转速之比称为轮头比,轮头比的值普通在 1--1.5 之间。
三、钻头的纵振(轴向振动)钻头工作时,对一个牙轮而言,牙齿与井底的接触是单齿、双齿交替进行的。
单齿着地时,牙轮的轮心处于最高位置,双齿着地时则轮心下降。
牙轮在转动过程中,轮心位置不断上下变换,使钻头沿轴向作上下往复运动,这就是钻头的轴向振动。
纵振振幅就是轮心的垂直位移,它与牙齿的齿高、齿距等钻头结构参数及岩性有关。
在软地层,牙齿吃入深、振幅小,硬地层则振动加剧。
振动的频率与牙轮齿数及牙轮转速成正比。
在旋转钻井中,钻头纵振频率普通为 100~500 次/min。
此外,由于井底不平,钻头产生振幅较大的低频振动。
据国外资料介绍,低频振动的振幅就是井底凹凸部份的高差,普通为 10mm 摆布,频率低于 50 次/min。
低频纵振对钻头是不利的因素,在硬地层中会造成跳钻。
三牙轮钻头生产工艺

三牙轮钻头生产工艺1. 引言三牙轮钻头是一种常用的工业切削工具,主要用于金属加工领域。
它的高质量和高效率使得它成为许多企业的首选。
本文将介绍三牙轮钻头的生产工艺,包括原材料选取、工艺流程、设备与工具以及质检方法。
2. 原材料选取2.1 刀片材料三牙轮钻头的刀片材料一般选用高速钢或硬质合金。
高速钢具有良好的热稳定性和切削性能,适用于中等强度的金属材料。
硬质合金则具有更好的刚性和耐磨性,适用于较硬的材料加工。
2.2 刀柄材料刀柄材料通常选用优质的工具钢或高速钢,以确保刀柄的强度和稳定性。
3. 生产工艺流程三牙轮钻头的生产工艺一般包括以下步骤:3.1 材料切割与成型首先,将所选材料切割成适当的尺寸。
对于刀片材料,可以使用切割机、剪切机或锯床进行切割。
对于刀柄材料,可以使用车床进行加工成适当的形状。
3.2 钻孔加工接下来,将刀柄和刀片进行组装,并使用数控机床进行钻孔加工。
钻孔的直径和深度需要根据具体需求进行调整。
3.3 热处理完成钻孔加工后,需要对整体进行热处理。
热处理的目的是提高材料的硬度和强度,以确保刀具在使用时有较长的使用寿命。
3.4 刃磨与修磨经过热处理的刀具可能存在一些不规则或磨损的刃口。
因此,需要进行刃磨和修磨的过程,以确保刀具的切削性能。
刃磨和修磨的具体步骤和参数需要根据不同的刀具类型和规格进行调整。
3.5 表面处理为了提高刀具的表面质量和耐腐蚀性,需要对刀具进行表面处理。
常用的表面处理方法包括镀镍、硬铬、氮化等。
3.6 质检与包装最后,在生产完成后,需要对刀具进行质量检查。
常用的检验方法包括外观检查、尺寸测量、硬度测试等。
通过质检合格后,进行包装和标记,以待发货和销售。
4. 设备与工具生产三牙轮钻头所需的设备与工具主要包括:•切割机、剪切机或锯床•数控机床(钻孔加工)•热处理设备•刃磨和修磨工具•表面处理设备(镀镍、硬铬、氮化)•质检设备(外观检查、尺寸测量、硬度测试)5. 质检方法为确保三牙轮钻头的质量,需要进行质量检测。
三牙轮钻头工作原理
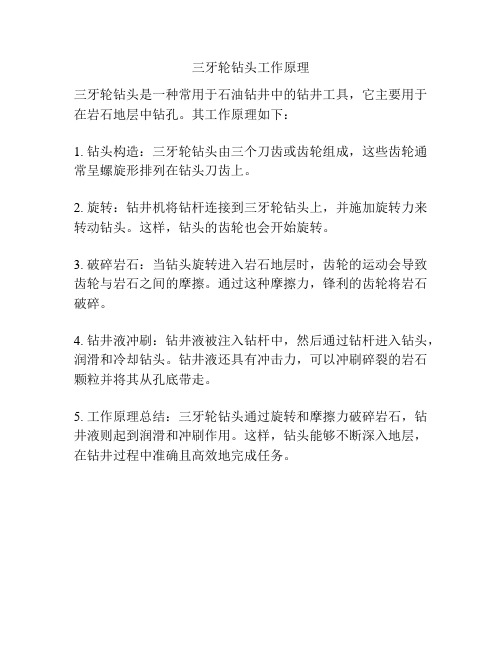
三牙轮钻头工作原理
三牙轮钻头是一种常用于石油钻井中的钻井工具,它主要用于在岩石地层中钻孔。
其工作原理如下:
1. 钻头构造:三牙轮钻头由三个刀齿或齿轮组成,这些齿轮通常呈螺旋形排列在钻头刀齿上。
2. 旋转:钻井机将钻杆连接到三牙轮钻头上,并施加旋转力来转动钻头。
这样,钻头的齿轮也会开始旋转。
3. 破碎岩石:当钻头旋转进入岩石地层时,齿轮的运动会导致齿轮与岩石之间的摩擦。
通过这种摩擦力,锋利的齿轮将岩石破碎。
4. 钻井液冲刷:钻井液被注入钻杆中,然后通过钻杆进入钻头,润滑和冷却钻头。
钻井液还具有冲击力,可以冲刷碎裂的岩石颗粒并将其从孔底带走。
5. 工作原理总结:三牙轮钻头通过旋转和摩擦力破碎岩石,钻井液则起到润滑和冲刷作用。
这样,钻头能够不断深入地层,在钻井过程中准确且高效地完成任务。
三牙轮钻头

三牙轮钻头是应用最广泛的钻井钻头()之一,具有适应地层广,机械钻速高的特点。
三牙轮钻头由切削结构、轴承结构、锁紧元件、储油密封装置、喷嘴装置等二十多种零部件组成。
三牙轮钻头的分类1、轴承类型:滚动轴承和滑动轴承2、密封类型:橡胶密封和金属密封3、按牙齿的固定方式分为:镶齿(硬质合金齿)三牙轮钻头和铣齿(钢齿)三牙轮钻头三牙轮钻头的工作原理牙轮钻头在钻压和钻柱旋转的作用下,牙齿压碎并吃入岩石,同时产生一定的滑动而剪切岩石。
当牙轮在井底滚动时,牙轮上的牙齿依次冲击、压入地层,这个作用可以将井底岩石压碎一部分,同时靠牙轮滑动带来的剪切作用削掉牙齿间残留的另一部分岩石,使井底岩石全面破碎,井眼得以延伸。
[1]产品优势石油钻井和地质钻探中应用最多的还是牙轮钻头。
牙轮钻头在旋转时具有冲击、压碎和剪切破碎地层岩石的作用,所以,牙轮钻头能够适应软、中、硬的各种地层。
特别是在喷射式牙轮钻头和长喷嘴牙轮钻头出现后,牙轮钻头的钻井速度大大提高,是牙轮钻头发展史上的一次重大革命。
牙轮钻头按牙齿类型可分为铣齿(钢齿)牙轮钻头、镶齿(牙轮上镶装硬质合金齿)牙轮钻头;按牙轮数目可分为单牙轮、双牙轮、三牙轮和多牙轮钻头。
目前,国内外使用最多、最普遍的是三牙轮钻头。
在石油、勘探以及各种钻探行业中牙轮钻头是不可缺少的重要部分,但是牙轮钻头对一些钻探行业来说价格实在太高,这就促使一些钻探行业对二手牙轮钻头产生了很大兴趣,其价格低,质量可靠(在石油钻探中只使用了其寿命的1/3),为钻探行业降低了大量成本,所以二手牙轮钻头已经成为一些钻探行业中的一重要部分.FJ517G三牙轮钻头所属分类钻井,勘探,石油,钻头,钻井配件产品名称215.9mm金属密封江汉镶齿三牙轮钻头产品型号FJ517G结构特点1、采用浮动轴承结构,浮动元件由高强度、高弹性、高耐温性、高耐磨性特点的新材料制成,表面经固体润滑剂处理。
在降低轴承副相对线速度的同时,减少摩擦面温升,能有效提高高钻压或高转速钻井工艺条件下的轴承寿命和轴承可靠性。
三牙轮钻头

三牙轮钻头、钻爪热处理工艺一、20CrMo热处理1、渗碳温度930℃,在强渗后进行扩散渗碳。
其计算公式为:式中,δCD总渗碳层深度,τ为时间(h),T为绝对温度(K)。
T=930℃时,A(T)=0.647。
在930℃时,要得到δCD=2.6mm,则需要渗碳总时间(t T):=16.16h,强渗期时间由下式计算:其中C为扩散期的表面碳势;C0为零件原始成分的含碳量;C1为渗碳期的表面碳势。
若强渗期碳势为1.2,扩散期碳势为0.85,渗层厚度2.6mm,强渗期时间(tc)为6.8h。
扩散期时间T D由下式计算:t D=t T-tc若强渗期碳势为1.2,扩散期碳势为0.85,渗层厚度2.6mm,扩散期时间(tc)为9.36h。
应根据实际生产条件在保证渗层深度的前提下,可适当的缩短时间,增加时间,参考工艺如下:2、淬火、回火20CrMo的合适淬火温度在(820~840)℃范围内。
实践证明,选用这温度范围是较合适的。
工艺曲线参照原工艺。
二、20Cr2Ni4热处理20Cr2Ni4属高强度合金渗碳钢。
一般渗碳工艺:920℃渗碳,渗后680℃回火,820℃淬火,180℃回火。
强渗、扩散后随炉降温至850~860℃,出炉转入缓冷坑冷却至小于或等于300度,出炉空冷。
淬火工艺:第一次淬火的温度为880~900度,目的是细化心部组织,并消除表层的网状渗碳体。
第一次淬火的冷却空冷(正火),目的防止网状碳化物析出,减少淬火变形。
第二次淬火温度为800-820℃。
目的是改善表层组织得到细小颗粒状碳化物加隐晶或细针状马氏体组织,以保证硬度和耐磨性要求。
*其他零件工艺*如果零件尺寸大,碳势高,渗层深,也可以提高渗碳温度,如NNCF41104160Y 背衬轴承外圈外径为520mm,内径为362 mm,根据用户要求,该轴承经渗碳热处理后要达到如下技术要求:成品套圈表面硬度要求为57~60HRC,表面含碳量达到1.3%,有效渗碳层深度大于5.0 mm。
三牙轮钻头生产工艺
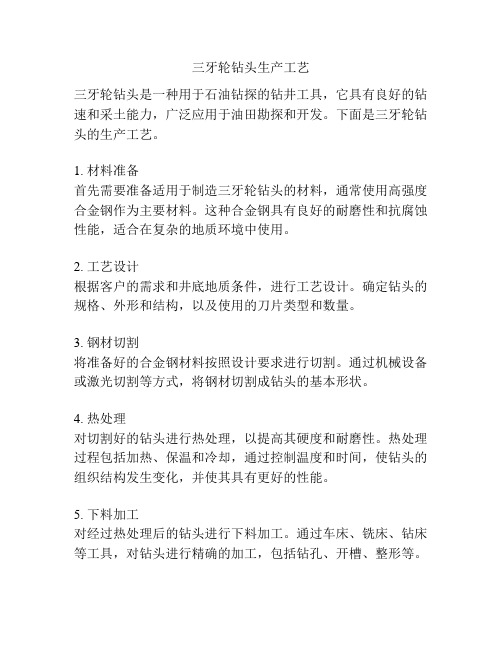
三牙轮钻头生产工艺三牙轮钻头是一种用于石油钻探的钻井工具,它具有良好的钻速和采土能力,广泛应用于油田勘探和开发。
下面是三牙轮钻头的生产工艺。
1. 材料准备首先需要准备适用于制造三牙轮钻头的材料,通常使用高强度合金钢作为主要材料。
这种合金钢具有良好的耐磨性和抗腐蚀性能,适合在复杂的地质环境中使用。
2. 工艺设计根据客户的需求和井底地质条件,进行工艺设计。
确定钻头的规格、外形和结构,以及使用的刀片类型和数量。
3. 钢材切割将准备好的合金钢材料按照设计要求进行切割。
通过机械设备或激光切割等方式,将钢材切割成钻头的基本形状。
4. 热处理对切割好的钻头进行热处理,以提高其硬度和耐磨性。
热处理过程包括加热、保温和冷却,通过控制温度和时间,使钻头的组织结构发生变化,并使其具有更好的性能。
5. 下料加工对经过热处理后的钻头进行下料加工。
通过车床、铣床、钻床等工具,对钻头进行精确的加工,包括钻孔、开槽、整形等。
6. 刀片装配将精加工好的钻头与刀片进行装配。
刀片通常采用硬质合金材料,通过焊接或夹持的方式与钻头连接。
确保刀片与钻头的连接牢固,并使刀片的形状和角度符合要求。
7. 表面处理对装配好的钻头进行表面处理,以提高其耐腐蚀性能和外观质量。
可以采用喷涂、镀铬等方式进行表面处理,以增加钻头的耐用性和美观度。
8. 检测和质量控制对制造好的三牙轮钻头进行检测,包括外观检查、尺寸检测、硬度测试等。
通过检测,排除不合格品,并保证产品质量。
9. 包装和出厂对检测合格的钻头进行包装,并准备出厂。
包装通常采用木箱、塑料袋等方式,以确保产品的安全运输和储存。
以上是三牙轮钻头的生产工艺概述,具体的生产过程中可能还会涉及其他技术和步骤。
在整个生产过程中,需要严格控制各个环节的质量,确保生产出高性能、高质量的三牙轮钻头。
常见汽车级机床用零件机加热处理工艺路线
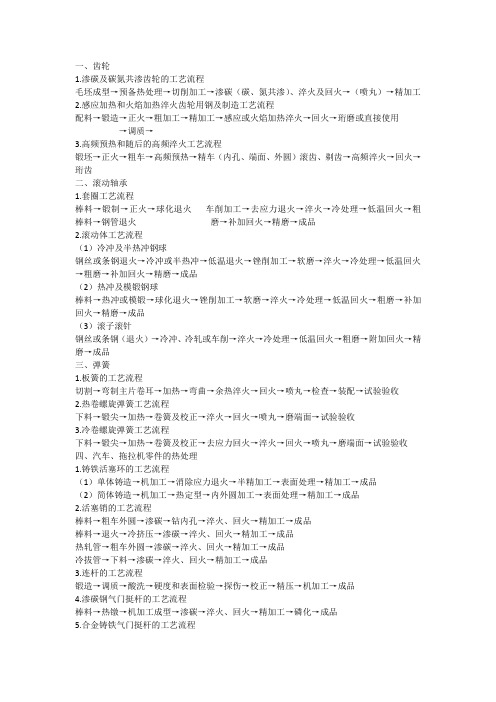
一、齿轮1.渗碳及碳氮共渗齿轮的工艺流程毛坯成型→预备热处理→切削加工→渗碳(碳、氮共渗)、淬火及回火→(喷丸)→精加工2.感应加热和火焰加热淬火齿轮用钢及制造工艺流程配料→锻造→正火→粗加工→精加工→感应或火焰加热淬火→回火→珩磨或直接使用→调质→3.高频预热和随后的高频淬火工艺流程锻坯→正火→粗车→高频预热→精车(内孔、端面、外圆)滚齿、剃齿→高频淬火→回火→珩齿二、滚动轴承1.套圈工艺流程棒料→锻制→正火→球化退火车削加工→去应力退火→淬火→冷处理→低温回火→粗棒料→钢管退火磨→补加回火→精磨→成品2.滚动体工艺流程(1)冷冲及半热冲钢球钢丝或条钢退火→冷冲或半热冲→低温退火→锉削加工→软磨→淬火→冷处理→低温回火→粗磨→补加回火→精磨→成品(2)热冲及模锻钢球棒料→热冲或模锻→球化退火→锉削加工→软磨→淬火→冷处理→低温回火→粗磨→补加回火→精磨→成品(3)滚子滚针钢丝或条钢(退火)→冷冲、冷轧或车削→淬火→冷处理→低温回火→粗磨→附加回火→精磨→成品三、弹簧1.板簧的工艺流程切割→弯制主片卷耳→加热→弯曲→余热淬火→回火→喷丸→检查→装配→试验验收2.热卷螺旋弹簧工艺流程下料→锻尖→加热→卷簧及校正→淬火→回火→喷丸→磨端面→试验验收3.冷卷螺旋弹簧工艺流程下料→锻尖→加热→卷簧及校正→去应力回火→淬火→回火→喷丸→磨端面→试验验收四、汽车、拖拉机零件的热处理1.铸铁活塞环的工艺流程(1)单体铸造→机加工→消除应力退火→半精加工→表面处理→精加工→成品(2)简体铸造→机加工→热定型→内外圆加工→表面处理→精加工→成品2.活塞销的工艺流程棒料→粗车外圆→渗碳→钻内孔→淬火、回火→精加工→成品棒料→退火→冷挤压→渗碳→淬火、回火→精加工→成品热轧管→粗车外圆→渗碳→淬火、回火→精加工→成品冷拔管→下料→渗碳→淬火、回火→精加工→成品3.连杆的工艺流程锻造→调质→酸洗→硬度和表面检验→探伤→校正→精压→机加工→成品4.渗碳钢气门挺杆的工艺流程棒料→热镦→机加工成型→渗碳→淬火、回火→精加工→磷化→成品5.合金铸铁气门挺杆的工艺流程合金铸铁整体铸造(间接端部冷激)→机械加工→淬火、回火→精加工→表面处理→成品合金铸铁整体铸造(端部冷激)→机械加工→消除应力退火→精加工→表面处理→成品钢制杆体→堆焊端部(冷激)→回火→精加工→成品钢制杆体→对焊→热处理→精加工→表面处理→成品6.马氏体型耐热钢排气阀的工艺流程马氏体耐热钢棒料→锻造成型→调质→校直→机加工→尾部淬火→抛光→成品7.半马氏体半奥氏体型耐热钢(Gr13Ni7Si2)排气阀的工艺流程棒料→顶锻→精压→热处理→精加工→成品8.奥氏体耐热钢排气阀的工艺流程棒料→顶锻→精压→阀面和尾部堆焊耐热合金→热处理→杆部滚压或软氮化→精加工→成品9.半轴调质的工艺流程合金结构钢棒料→锻造成形→正火或退火→机械加工→调质→校直→精加工→成品10.半轴的表面淬火的工艺流程棒料→锻造成形→预先热处理→校直→机械加工→表面淬火→校直→精加工→成品11.柱塞副和喷油嘴偶件的工艺流程热扎退火棒料→自动机加工成型→热处理→精加工→时效→成品12.拖拉机履带板(1)40SiMn2履带板的热处理热轧成形→下料→机加工→热处理→成品(2)ZGMn13履带板的热处理铸造成型→热处理→成品五、金属切削机床零件的热处理1.机床导轨(1)MM7125平面磨床立柱镶钢导轨锻造→正火→机加工→消除应力退火→机加工→淬火→回火→磨(2)M9025工具曲线磨床镶钢导轨锻造→退火→机加工→淬火→回火→磨(3)S788轴承磨床镶钢导轨机加工→消除应力退火→机加工→渗碳→淬火→回火→磨→时效(4)MZ208轴承磨床镶钢导轨锻造→退火→机加工→消除应力退火→机加工→淬火→冰冷处理→回火→磨→时效2.机床主轴(1)CA6104车窗主轴(45钢)下料→粗加工→正火→机加工→高频淬火→回火→磨(2)T68、T611镗床的镗杆及MGB132磨床的主轴(35CrMoAlA钢)下料→粗车→调质→精车→消除应力处理→粗磨→渗氮→粗磨(3)SGC630精密丝杠车床主轴(12CrNi3A)锻造→正火→机加工→渗碳→正火→校直→消除应力→机加工→头部淬火→颈部淬火→回火→磨→时效(4)X62W万能升降台铣床主轴(球墨铸铁QT60-2)铸造→机加工→淬火→回火(5)M1040无心磨床主轴(球墨铸铁QT60-2)铸造→机加工→正火→机加工3.丝杠(1)7级或7级精度一下的一般丝杠(45钢)下料→正火或调质→校直→消除应力处理→机加工(2)6级或6级以上精密不淬硬丝杠(T10或T12钢)球化退火→机加工→消除应力处理→机加工→时效→精加工(3)中大型精密淬硬丝杠(CrWMn)锻造→球化退火→机加工→消除应力→机加工→消除应力→机加工→淬火、回火→冰冷处理→回火→探伤→机加工→时效→精加工→时效→精加工(4)中小型精密淬硬丝杠(9Mn2V)锻造→球化退火→机加工→消除应力→机加工→淬硬淬火→回火→冰冷处理→回火、探伤→机加工→时效→精加工→时效→精加工(5)滚珠丝杠(GCr15,GCr15SiMn)4.弹簧卡头(1)卧式多轴自动车床夹料卡头(9SiCr)锻造→退火→机加工→淬火→回火→机加工→磨开口→胀大定型(2)卧式多轴自动车床送料卡头(T8A钢)锻造→退火→机加工→淬火→回火→磨(3)仪表机床小型专用卡头(60Si2)退火→机加工→淬火→回火→磨(4)磨阀辨机床专用卡头(65Mn)锻造→正火→高温→回火→机加工→淬火→回火→机加工5.摩擦片(1)X62W万能升降台铣床摩擦片(A3)机加工→渗碳→淬火→回火→机加工→回火(2)DLMO电磁离合器摩擦片(65Mn)冲片→淬火→回火→磨(3)电磁离合器摩擦片(6SiMnV)锻造→退火→切片→淬火→回火→磨6.FW250万能分度头主轴(45)锻造→正火→机加工→淬火→回火→机加工7.万能分度头蜗杆(20Cr)正火→机加工→渗碳→机加工→淬火→回火→机加工8.三爪卡盘卡爪(45)正火→机加工→淬火→回火→高频淬火→回火→法蓝→磨加工9.三爪卡盘丝(45)锻造→正火→机加工→淬火→回火→法蓝→磨六、活塞1.20CrMnMo钢制活塞的热处理锻造→正火→检验→机加工→渗碳→检验→正火→淬火→清洗→回火→检验→喷砂→磨削2.钒钢活塞的热处理下料→锻造→检验→预先淬火→球化退火→检验→机加工→淬火→回火→检验→磨削七、凿岩机钎尾锻造→退火→检验→渗碳→检验→淬火→回火→清洗→检验→磨削。
- 1、下载文档前请自行甄别文档内容的完整性,平台不提供额外的编辑、内容补充、找答案等附加服务。
- 2、"仅部分预览"的文档,不可在线预览部分如存在完整性等问题,可反馈申请退款(可完整预览的文档不适用该条件!)。
- 3、如文档侵犯您的权益,请联系客服反馈,我们会尽快为您处理(人工客服工作时间:9:00-18:30)。
2、牙轮主要加工工艺流程:
①模锻—②钻中心孔—③车外表面—④粗车内孔—⑤止推面钻孔、镶铜合金(堆焊内孔止推面)—⑥热处理—⑦喷砂—⑧钻齿孔—⑨压齿—⑩精车内孔—⑪装牙轮底部垫块—⑫装镶套。
装配及焊接工艺要点如下:
(1)装滚柱前先涂润滑脂可以使滚柱粘在牙轮上,便于装配;
(2)滚珠塞销顶部的外形应与滚珠外形一致,以便于装配后滚珠滚动;
(3)焊牙轮钻底部焊缝和焊牙轮钻侧面焊缝工序完成后,使用水进行冷却,水不可接触焊缝。
(4)对比空气润滑,油润滑的牙轮钻对密封的要求更高,牙轮处O型圈的材料和密封效果很重要,应保证润滑脂不能泄露。
牙掌加工工艺流程中重要工序工艺要点如下:
(1)牙掌加工工件为锻件,锻件质量和材料很重要,牙掌材料选用8620。为方便以后焊接,在锻造时需在锻件上预留坡口;
(2)结合销孔是连接三片牙掌的定位孔,同时也是加工中用来定位端面和牙轮小轴位置的重要基准,在加工时要保证其位置准确;
(3)车牙轮小轴时,采用V型夹具,借助结合销孔定位;
(4)在堆焊牙轮小轴上端面工序中使用Co6材料,堆焊止推面使用Co190材料;
(5)牙轮小轴与滚珠、滚柱及牙轮配合形成轴承,且小轴上端面和小轴止推面为牙掌与牙轮接触的主要受力面,牙轮小轴的精度要求很高。为保证小轴加工精度,磨小轴上端面工序完成后,小轴上端面将作为基准,磨小轴止推面,同时应严格保证上端面与止推面的距离。
(5)工序⑰—⑲可在一台车床加工完成。
(5)工序②—④、⑩可在车床上加工完成,工序⑧需在一台加工中心上完成。
3、牙轮装配及车螺纹主要工艺流程:
①清洗、烘干—②在牙轮内孔涂润滑脂,装滚柱—③牙轮轴涂润滑脂—④装牙轮—⑤填滚珠—⑥塞滚珠塞销—⑦焊塞销—⑧装定位销—⑨组合三片牙掌—⑩用卡环夹紧—⑪卡规测牙轮直径,调直径—⑫焊牙轮钻底部焊缝—⑬冷却—⑭去夹环,焊牙轮钻侧面焊缝—⑮冷却—⑯退火—⑰车螺纹外锥、车掉牙掌上端面工艺孔—⑱车螺纹—⑲车内孔挡圈槽—⑳焊平定位槽和焊储油孔螺钉— 打标— 喷漆— 装水孔喷嘴、弹性挡圈。
三牙轮钻头工艺流程
1、牙掌主要加工工艺流程:
①模锻—②铣平上端面—③钻定位孔(在上端面钻两个工艺孔)—④铣120°面—⑤钻结合销孔—⑥车小轴—⑦车止推面堆焊槽、钻车小轴上端面堆焊孔—⑧铣轴颈储油面—⑨铣止推面油槽—⑩钻轴颈油孔—⑪钻扩泥浆孔—⑫钻注油孔—⑬钻肩部储油孔—⑭钻掌背齿孔—⑮铣定位槽(用于加工螺纹)—⑯钻滚珠塞销孔—⑰堆焊掌背碳化钨—⑱堆焊小轴上端面、止推面及上部外圆面—⑲热处理—⑳喷砂— 压齿— 磨小轴上端面— 磨小轴止推面— 焊油管。
牙轮加工工艺要点如下:
(1)牙轮加工工件为锻件,锻件底部平整便于钻中心孔进行定位。牙轮材料选用9315;
(2)车牙轮外表面时,牙轮外表面的槽道可以做的深一些,之后再进行堆焊填补,堆焊材料中可加入球粒合金;
(3)压齿后牙轮的形状会有变化,为保证牙轮内孔精度,需在压齿后夹持牙轮外圆,再精车牙轮内孔。
(4)牙轮底部垫块虽然在表面有锯齿பைடு நூலகம்但牙轮上与其配合的孔不需要加工齿痕;