毕业设计-搅拌反应釜设计(普通夹套)
设计一台夹套传热式带有搅拌装置的反应釜

公称直径 DN/mm 曲边高度 h1/mm
1100
275
1200
300
1300
325
直边高度 h2/mm
25 40 500 25 40 50 25 40 50
内表面积 A/mm² 容积 V/m³
1.3980 1.4499 1.4844 1.6652 1.7117 1.7494 1.9340 1.9953 2.0361
换热器要求满足 5.筒体和上封头的连接采用甲型平焊法兰连接选取凹凸密封面法兰
1.131
H1=1.101m, 于是
i= Hi =1.101/1.200=0.9175≈1 Di
圆整后的 H1=1200mm,圆整后的实际容积 V=V1m×H1+V 封=1.6117m³
4.夹套几何尺寸的计算:
夹套内径:D2=D1+100=1300mm
选择操作容积为 1m³
装料系数:
η= 操作容积= 1 =0.67 【8】 全容积 1.5
夹套高 H2 计算:
H2= V V封 = 0.67 1.5 0.2545 =0.6635m 【9】
V 1m
1.131
夹套所包围的罐体的表面积,一定要大于工艺要求的传热面积 F
F 封+F 筒≥F 【10】
其中 F 筒=H2×F1m ,已知:F1m=3.77 ㎡
F 封+F 筒=1.6652+0.6635×3.77=4.1665>3
筒体的连接常焊接成封闭结构,夹套内径 D2 可根据筒体内径 D1,
夹套下封头型式同罐体封头,其直径 D2 与夹套筒体相同。
表 2 夹套直径 D2【4】
D1
500~600
700~1800
2000~3000
12立方米搅拌装置(反应釜)设计毕业设计[管理资料]
![12立方米搅拌装置(反应釜)设计毕业设计[管理资料]](https://img.taocdn.com/s3/m/265b7b179b89680202d825b7.png)
摘要带搅拌的夹套反应釜是化学、医药及食品等工业中常用的典型反应设备之一。
它是一种在一定压力和温度下,借助搅拌器将一定容积的两种(或多种)液体以及液体或气体物料混匀,促进其反应的设备。
一台带搅拌的夹套反应釜。
它主要由搅拌容器、搅拌装置、传动装置、轴封装置、支座、人孔、工艺接管和一些附件组成。
本文主要介绍的时一种推进式夹套反应釜设计,包括整体结构设计、强度校核以及一些工艺设计。
夹套反应釜分罐体和夹套两部分,主要有封头和筒体组成,多为中、低压压力容器;搅拌装置有搅拌器和搅拌轴组成,其形式通常由工艺而定;传动装置主要有电动机、减速器、联轴器和传动轴等组成;轴封装置一般采用机械密封或填料密封;它们与支座、人孔、工艺接管等附件一起,构成完整的夹套反应釜。
关键词:反应釜、筒体设计、夹套设计、法兰、接管、焊缝、开孔补强reactor designAbstractA stirred jacketed reactor is the chemical, pharmaceutical and food industries in the typical reaction to one of the devices used. It is a certain pressure and temperature, by means of a stirrer to a volume of two (or more) of liquid and the liquid or gas,Body material mix, promoting the reaction of the device.A jacketed stirred reactor. It mainly consists of mixing vessel, a stirring device, transmission device, the shaft sealing device, bearing, manholes, pipe connection and some accessories.This paper describes time-jacketed reactor one kind push design, including the overall structural design, strength check, and some process design. Jacketed reactor tank and a jacket of two parts, the main composition and the cylinder head, mostly in low pressure vessel; stirring means with a stirrer and the stirring shaft, whose form is usually determined by the process and; transmission main motor, reducer, couplings and drive shafts and other components; seal device commonly used mechanical seal or packing seal; them with support, manholes, and other accessories takeover process, together constitute a complete jacketed reactor.Keywords: reactor、cylinder design、jacket design、flange、receivership、welds, opening reinforcement引言反应釜的广义理解即有物理或化学反应的不锈钢容器,根据不同的工艺条件需求进行容器的结构设计与参数配置,设计条件、过程、检验及制造、验收需依据相关技术标准,以实现工艺要求的加热、蒸发、冷却及低高速的混配反应功能。
搅拌反应釜的釜体设计及夹套设计解读

搅拌反应釜的釜体设计及夹套设计2.1 概述夹套式反应釜的釜体是由封头、筒体和夹套三部分组成。
封头有椭圆形封头和锥形封头等形式。
上、下封头与筒体常为焊接。
2.2 釜体材料的选择根据工艺参数及操作条件(见附录2)确定封头、筒体及夹套的材料。
此设计的釜体材料选用0Cr18Ni9与夹套材料选用Q235-B ,热轧钢板,其性能与用途见表2-1。
表2-1 Q235-B 性能与用途由工艺参数及操作条件和表2-1可知,0Cr18Ni9和Q235—B 材料能够满足任务书中的设计温度、设计压力。
在操作条件下,Q235—B 能使设备安全运转,并且不会因腐蚀而对介质产生污染,而且相对与其他钢号价格便宜,所以本设计釜体材料选用0Cr18Ni9与夹套材料采用Q235-B ,热轧钢板。
2.3 封头的选择搅拌反应釜顶盖在受压状态下操作常选用椭圆形封头,本设计采用椭圆形标准封头,直边高度mm h 45= ,其内径取与筒体内径相同的尺寸。
椭圆形封头是由半个椭圆球体和一个圆柱体组成,由于椭圆部分径线曲率平滑连续,封头中的应力分布不均匀。
对于2=ba 得标准形封头,封头与直边的连接处的不连续应力较小,可不予考虑。
椭圆形封头的结构特性比较好。
2.4 釜体几何尺寸的确定釜体的几何尺寸是指筒体的内径i D 和高度H 。
釜体的几何尺寸首先要满足化工工艺的要求。
对于带搅拌器的反应釜来说,容积V 为主要决定参数。
2.4.1 确定筒体的内径由于搅拌功率与搅拌器直径的五次方成正比,而搅拌器直径往往需随釜体直径的增加而增大。
因此,在同样的容积下筒体的直径太大是不适宜的。
对于发酵类物料的反应釜,为使通入的空气能与发酵液充分接触,需要有一定的液位高度,筒体的高度不宜太矮。
因此,要选择适宜的长泾比(iD H )。
根据釜体长径比对搅拌功率、传热的影响以及物料特性对筒体长径比的要求,又由实践经验,针对一般反应釜,液—液相物料,iD H取值在1.7-2.3之间,并且考虑还要在封头上端布置机座和传动装置,因此,取i D H=2.3。
搅拌反应釜课程设计
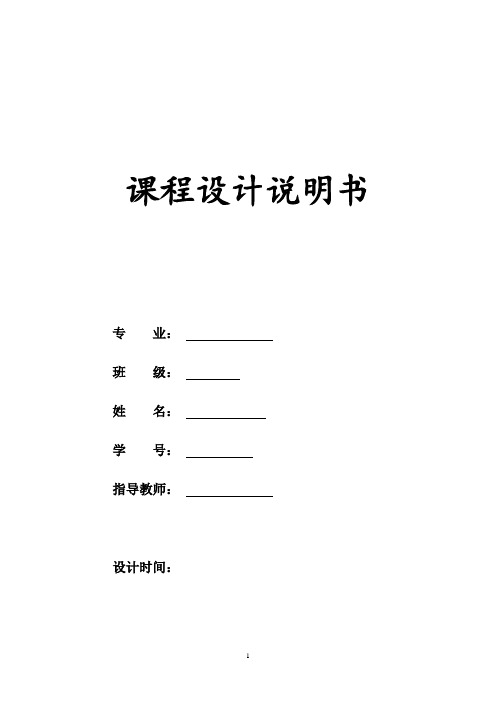
课程设计说明书专业:班级:姓名:学号:指导教师:设计时间:要求与说明一、学生采用本报告完成课程设计总结。
二、要求文字(一律用计算机)填写,工整、清晰。
所附设备安装用计算机绘图画出。
三、本报告填写完成后,交指导老师批阅,并由学院统一存档。
目录一、设计任务书 (5)二、设计方案简介 (6)1.1罐体几何尺寸计算 (7)1.1.1确定筒体内径 (7)1.1.2确定封头尺寸 (8)1.1.3确定筒体高度 (9)1.2夹套几何计算 (10)1.2.1夹套内径 (10)1.2.2夹套高度计算 (10)1.2.3传热面积的计算 (10)1.3夹套反应釜的强度计算 (11)1.3.1强度计算的原则及依据 (11)1.3.2按内压对筒体和封头进行强度计算 (12)1.3.2.1压力计算 (12)1.3.2.2罐体及夹套厚度计算 (12)1.3.3按外压对筒体和封头进行稳定性校核 (14)1.3.4水压试验校核 (16)(二)、搅拌传动系统 (16)2.1进行传动系统方案设计 (17)2.2作带传动设计计算 (17)2.2.1计算设计功率Pc (17)2.2.2选择V形带型号 (17)2.2.3选取小带轮及大带轮 (17)2.2.4验算带速V (18)2.2.5确定中心距 (18) (18)2.2.6 验算小带轮包角12.2.7确定带的根数Z (18)2.2.8确定初拉力Q (19)2.3搅拌器设计 (19)2.4搅拌轴的设计及强度校核 (19)2.5选择轴承 (20)2.6选择联轴器 (20)2.7选择轴封型式 (21)(三)、设计机架结构 (21)(四)、凸缘法兰及安装底盖 (22)4.1凸缘法兰 (22)4.2安装底盖 (23)(五)、支座形式 (23)5.1 支座的选型 (23)5.2支座载荷的校核计算 (25)(六)、容器附件 (26)6.1手孔和人孔 (26)6.2设备接口 (27)6.2.1接管与管法兰 (27)6.3视镜 (28)四、设计结果汇总 (31)五、参考资料 (33)六、后记 (35)七、设计说明书评定 (36)八、答辩过程评定 (36)一、设计任务书设计题目:夹套反应釜的设计设计条件:设计参数及要求设计参数及要求简图容器内夹套内工作压力/MPa 0.18 0.25设计压力/MPa 0.2 0.3工作温度/℃100 130设计温度/℃<120 <150介质染料及有机溶剂水蒸气全容积/m3 2.5操作容积/ m3 2.0传热面积/ m2>3腐蚀情况微弱推荐材料Q345R或Q245R搅拌器型式浆式200搅拌轴转速/(r/min)轴功率/kW 4工艺接管表符号公称尺寸连接面形式A 25 PL/RF 蒸汽入口B 65 PL/RF 进料口C1,2100 - 视镜D 25 PL/RF 温度计管口E 25 PL/RF 压缩空气入口F 40 PL/RF 放料口G 25 PL/RF 冷凝水出口设备安装场合室内二、设计方案简介三、工艺计算及主要设备计算(一)、罐体和夹套的结构设计夹套式反应釜是由罐体和夹套两大部分组成的。
反应釜毕业设计-

反应釜设计的有关内容一、设计条件及设计内容分析由设计条件单可知,设计的反应釜体积为1.03m ;搅拌轴的转速为200/min r ,轴的功率为4kw;搅拌桨的形式为推进式;装置上设有5个工艺接管、2个视镜、4个耳式支座、1个温度计管口。
反应釜设计的内容主要有:(1) 釜体的强度、刚度、稳定性计算和结构设计; (2) 夹套的的强度、刚度计算和结构设计; (3) 设计釜体的法兰联接结构、选择接管、管法兰; (4) 人孔的选型及补强计算; (5) 支座选型及验算; (6) 视镜的选型;(7) 焊缝的结构与尺寸设计; (8) 电机、减速器的选型;(9) 搅拌轴及框式搅拌桨的尺寸设计; (10)选择联轴器; (11)设计机架结构及尺寸; (12)设计底盖结构及尺寸; (13)选择轴封形式;(14)绘总装配图及搅拌轴零件图等。
第一章 反应釜釜体的设计1.1 釜体DN 、PN 的确定 1.1.1 釜体DN 的确定将釜体视为筒体,取L/D=1.1 由V=(π/4)L D i 2,L=1.1i D 则=Di 31.140.1π⨯⨯,m Di 0.1=,圆整mm Di 1000= 由[]1314页表16-1查得釜体的mm DN 1000= 1.1.2釜体PN 的确定由设计说明书知釜体的设计压力PN =0.2MPa 1.2 釜体筒体壁厚的设计 1.2.1设计参数的确定设计压力p1:p1=0.2MPa ;液柱静压力 p1H=10^(-6)×1.0×10^3×10×1.1=0.011MPa 计算压力p1c : p1c=p1+p1H=0.2+0.011=0.211MPa ; 设计温度t1: <100℃ ; 焊缝系数Φ: Φ=0.85许用应力[]t σ:根据材料Q235-B 、设计温度<100℃,由参考文献知[]t σ=113MPa ;钢板负偏差1C :1C =0.6mm (GB6654-96); 腐蚀裕量2C :2C =3.0mm 。
搅拌反应釜设计毕业设计

搅拌反应釜设计毕业设计搅拌反应釜设计毕业设计搅拌反应釜是化工工业中常用的设备之一,广泛应用于化学反应、溶解、混合等过程。
在进行搅拌反应釜的设计时,需要考虑多个因素,包括反应物料的性质、反应温度、反应时间等。
本文将探讨搅拌反应釜设计的相关问题,以及如何优化设计方案。
一、反应物料的性质在进行搅拌反应釜设计时,首先要了解反应物料的性质。
不同的物料具有不同的反应性质,包括反应速率、反应热、反应产物等。
这些性质将直接影响到反应釜的设计参数,如搅拌速度、搅拌形式、加热方式等。
因此,在设计过程中要充分考虑反应物料的性质,以确保反应能够顺利进行。
二、反应温度的控制反应温度是搅拌反应釜设计中的重要参数之一。
不同的反应需要不同的温度条件,有些反应需要高温条件进行,而有些则需要低温条件。
因此,在设计反应釜时,要根据反应的要求选择合适的加热方式和温度控制系统。
同时,还需要考虑到反应过程中可能产生的热量,以确保反应温度能够稳定控制在预定范围内。
三、反应时间的控制反应时间是搅拌反应釜设计中的另一个重要参数。
不同的反应需要不同的反应时间,有些反应需要较长的时间才能达到预期的反应程度,而有些则只需要短暂的反应时间。
在设计反应釜时,要根据反应的要求选择合适的搅拌速度和反应时间控制系统。
同时,还需要考虑到反应过程中可能发生的反应速率变化,以确保反应时间能够准确控制。
四、反应釜的结构设计搅拌反应釜的结构设计也是设计过程中的关键环节。
反应釜的结构应该能够满足反应物料的搅拌需求,并且具有良好的密封性和耐腐蚀性。
在设计过程中,要考虑到反应釜的容积、搅拌器的形式和尺寸、进出料口的位置和尺寸等因素。
同时,还需要根据反应釜的使用环境选择合适的材料,以确保反应釜的安全可靠运行。
五、搅拌反应釜设计的优化方案为了提高搅拌反应釜的效率和性能,可以采取一些优化方案。
首先,可以通过改变搅拌器的形式和尺寸来提高搅拌效果。
其次,可以采用多级搅拌器或多层搅拌器来增加搅拌强度。
搅拌反应釜的釜体设计及夹套设计

搅拌反应釜的釜体设计及夹套设计2.1 概述夹套式反应釜的釜体是由封头、筒体和夹套三部分组成。
封头有椭圆形封头和锥形封头等形式。
上、下封头与筒体常为焊接。
2.2 釜体材料的选择根据工艺参数及操作条件(见附录2)确定封头、筒体及夹套的材料。
此设计的釜体材料选用0Cr18Ni9与夹套材料选用Q235-B ,热轧钢板,其性能与用途见表2-1。
表2-1 Q235-B 性能与用途由工艺参数及操作条件和表2-1可知,0Cr18Ni9和Q235—B 材料能够满足任务书中的设计温度、设计压力。
在操作条件下,Q235—B 能使设备安全运转,并且不会因腐蚀而对介质产生污染,而且相对与其他钢号价格便宜,所以本设计釜体材料选用0Cr18Ni9与夹套材料采用Q235-B ,热轧钢板。
2.3 封头的选择搅拌反应釜顶盖在受压状态下操作常选用椭圆形封头,本设计采用椭圆形标准封头,直边高度mm h 45= ,其内径取与筒体内径相同的尺寸。
椭圆形封头是由半个椭圆球体和一个圆柱体组成,由于椭圆部分径线曲率平滑连续,封头中的应力分布不均匀。
对于2=ba 得标准形封头,封头与直边的连接处的不连续应力较小,可不予考虑。
椭圆形封头的结构特性比较好。
2.4 釜体几何尺寸的确定釜体的几何尺寸是指筒体的内径i D 和高度H 。
釜体的几何尺寸首先要满足化工工艺的要求。
对于带搅拌器的反应釜来说,容积V 为主要决定参数。
2.4.1 确定筒体的内径由于搅拌功率与搅拌器直径的五次方成正比,而搅拌器直径往往需随釜体直径的增加而增大。
因此,在同样的容积下筒体的直径太大是不适宜的。
对于发酵类物料的反应釜,为使通入的空气能与发酵液充分接触,需要有一定的液位高度,筒体的高度不宜太矮。
因此,要选择适宜的长泾比(iD H )。
根据釜体长径比对搅拌功率、传热的影响以及物料特性对筒体长径比的要求,又由实践经验,针对一般反应釜,液—液相物料,iD H取值在1.7-2.3之间,并且考虑还要在封头上端布置机座和传动装置,因此,取i D H=2.3。
大学毕业设计-—2.4立方米搅拌反应釜设计
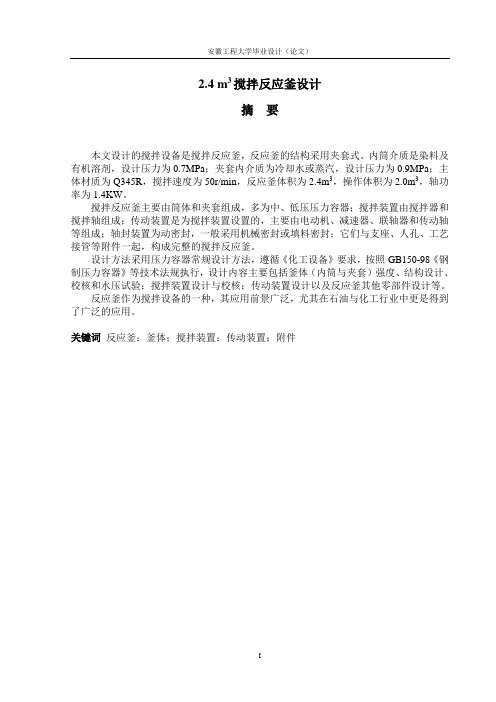
2.4 m3搅拌反应釜设计摘要本文设计的搅拌设备是搅拌反应釜,反应釜的结构采用夹套式。
内筒介质是染料及有机溶剂,设计压力为0.7MPa;夹套内介质为冷却水或蒸汽,设计压力为0.9MPa;主体材质为Q345R,搅拌速度为50r/min,反应釜体积为2.4m3,操作体积为2.0m3,轴功率为1.4KW。
搅拌反应釜主要由筒体和夹套组成,多为中、低压压力容器;搅拌装置由搅拌器和搅拌轴组成;传动装置是为搅拌装置设置的,主要由电动机、减速器、联轴器和传动轴等组成;轴封装置为动密封,一般采用机械密封或填料密封;它们与支座、人孔、工艺接管等附件一起,构成完整的搅拌反应釜。
设计方法采用压力容器常规设计方法,遵循《化工设备》要求,按照GB150-98《钢制压力容器》等技术法规执行,设计内容主要包括釜体(内筒与夹套)强度、结构设计、校核和水压试验;搅拌装置设计与校核;传动装置设计以及反应釜其他零部件设计等。
反应釜作为搅拌设备的一种,其应用前景广泛,尤其在石油与化工行业中更是得到了广泛的应用。
关键词反应釜;釜体;搅拌装置;传动装置;附件IAbstractThis design of mixing equipment is stirred tank reactor with jacket. Inner tube is a dye and an organic solvent medium and the design pressure is 0.7Mpa.jacket cooling medium is water or steam and the design pressure ois 0.9MPa; The main material is Q345R, stirring speed is 50r/min, reactor volume is 2.4m3, operating volume is 2.0m3 and shaft power is 1.4KW。
- 1、下载文档前请自行甄别文档内容的完整性,平台不提供额外的编辑、内容补充、找答案等附加服务。
- 2、"仅部分预览"的文档,不可在线预览部分如存在完整性等问题,可反馈申请退款(可完整预览的文档不适用该条件!)。
- 3、如文档侵犯您的权益,请联系客服反馈,我们会尽快为您处理(人工客服工作时间:9:00-18:30)。
乳化液泵站设计•专业:机械工程及自动化
导师:姜虹学生:
斯郎旺加
一.课题研究背景及意义•1.课题研究背景
•乳化液泵站的技术是随着煤矿机械化的发展而迅速发展起来的。
•早在70年代初,随着我国TZ-1型全工作面液压支架的研制成功,我国自行设计®公称压力为10MPa,公称流量为10OL/min的RB100/100行乳化液泵同时研制成功,从此我国煤矿生产有了第一套液压支架和第一套乳化液泵站。
之后,不同型号的乳化液泵站,喷雾泵站,注水泵站又陆续被研制出来,并得到了推广和应用。
•我国乳化If泵站从低压10 Mpa,小流量100L/min起步,压力逐步提高到20 Mpa,31.5 Mpa,和35Mpa,流量分别提高到110L/min,125 L/min,现已提高到200 L/min,甚至更大的流量。
定流量的乳化液泵站技术的发展带动了自动变量乳化液泵的研究,也提出了分级卸载式乳化液泵站。
乳化液泵站产品的发展,带动了喷雾泵站和注水泵站的发展,掘进机用喷雾泵的研制也取得了进展。
为了提高乳化液泵及泵站元件、喷雾泵站及元件、注水泵及元件的产品质量,推进乳化液泵站的技术水平提高,相关部门起草了一系列的标准、规范档,为乳化液泵站试验装置的研制和使用提供了科学的技术依据。
,面调力支回脏的些牵及靠在、乳要
一作、
压压站心中某机以是站产以重
之工架的液泵的作在煤,都泵生所常
备采移给是液体动,采顶,液常。
■
设综、供站化人架外、斤等
化正泵着
要。
溜站泵乳像史作达千柱乳面液起 主置推泵液向好而。
工马移支,作化产
的装现液化及就,中液压推压见工乳生
面换实化乳液站住相力液与液可证为全
作转能乳,供泵液液压链定体此保分安
工量并是说架液压化的紧固单由是部的
煤能,都以支化高乳给的的的。
,心面
采的板,所压乳着的供机机用的位核作
化能顶作。
液么送站站送载护作地其工
械压撑动果向那输泵泵输转支工的而采 机液支等结把,架到液板式前液要,综
合为够滑的们话支回化刮桥超压重备对
综变能防作我的压流乳曲、处高分设,
是转以、动果管液路靠弯顶口的十键坏
义站能所护顶如血向管架可斤出给有关好
意泵械之侧斤。
作
地液支,千下供占的的
宄液机架、千源比断
回压面紧、站面率能 %
化把支壁种力道不从液
作张上泵作产性。
题乳种压护各动管源又除
工的面液工生泵用课一液、使的的源液采
•正是由于泵站是综合机械化采煤工作面的主要装备之一,重要的动力源,相关技术,装备的发展源头等诸多方面的原因,对泵站的研究,改进成功提高综采装备质量的关键
一步。
•我们通过乳化液泵站的研究,加深了对综合机械化采煤;作面各环节的认识,培养了进行综合分析和提高解决实际问题的能力;巩固,扩大,深化所学的知识。
.设计的主要计算
齿轮的设计计算齿轮轴的校核计算曲轴的设计计算
连杆和连杆螺栓的设计计算
滑块销的设计计算柱塞与泵头的设计计算吸、排液阀得设计计算及箱体强度计算
轴瓦和滚动轴承的核验计算
齿轮的设计计算
齿轮属于该泵传动系统中的主要承载零件之一,本设计采用由一对齿轮构成的乳化液泵减速箱,电动机驱动,经一级齿轮减速带动曲轴旋转。
为使结构紧凑,工作中无轴向分力,遙择童齿圆tt齿轮彳专云ii。
由于泵转速较高,且齿轮箱局部发热较严重,因而需
要齿轮有较高的强度和齿面硬度。
故选择齿轮轴材料
38CrMoAIA,调质处理,氮化处理,Hv》850,相当于HRC>65;非齿面约HB229;大齿轮为400,齿面氮化处理,HRC48-55;HB为241〜286,取为250o用这些材料及热处理
方法能得到强度高、韧性好,齿面硬的齿轮。
本设计以接触疲劳强度设计,以弯曲疲劳强度校核。
齿
轮的设计计算
•1.以接触疲劳强度设计计算•初步计算•校核
计算•确定主要传
动尺寸
•2.齿根弯曲疲劳强度验算
齿轮轴的校核计算
•齿轮轴主要受齿轮的轴向力,轴承的支反力和联轴器传递过来的扭矩,有必要对其进行校核。
•1.齿轮轴受的力矩
•齿轮轴选用38OM0AIA材料,胚料锻造,其后进行调质处理,表面离子氮化,,氮化层深0.3mm
•2.齿轮轴的强度校核
•按许用弯曲应力和疲劳强度验算
由于齿轮轴受力较小,两支撑跨度乂诙小,故无须进行静强度核刚度校核。
曲轴的设计计算
曲轴为乳化液泵的主要承载构件,它的设计合理与否,直接影响着整个泵的运行情况。
目前,
大多数乳化液泵采用三曲拐整体结构的曲轴,为保证曲轴有足够的强度和刚度,其内部不钻孔,曲柄做成圆盘形。
曲轴颈与曲柄圆盘处用圆角光滑过渡,以免引起过大的应力集中。
本设计曲轴选用40Cr圆钢材调质处理,表面
离子氮化。
以使其具有较高的强度和表面硬度,从而提高其表面耐磨性,延长使用寿命。
曲轴三曲柄成120。
分布,使得动平衡良好,也使得流量脉动M小。
•1.曲柄滑块机构的受力分析
•2.曲轴的设计计算
•3.曲轴强度计算
•乳化液泵曲轴三曲拐互错12Q;,三个柱塞交替工作,每个柱塞的吸、排液行程各180°,曲柄
销工作时,有时是两个曲柄销同时承受压力,一个
曲柄销处于柱塞的吸液行程,不承受压力。
有时是
一个曲柄销承受压力,两个曲柄销处于柱塞的吸液
行程,不承受压力。
因而曲轴是在对称循环交变应
力下工作的。
设计曲轴时,应根据两个曲柄销同时
承受最大压力情况进行计算。
•两个曲柄销同时受力又有三种情况,即曲柄销I、II; II、III;或I、III同时受力。
计算支撑反力时,应按靠近支撑的两个曲柄销同时受力来处理。
这时所求的支反力为最大值。
显然,这时曲轴所受的弯矩也最大。
连杆和连杆螺栓的设计计算
连杆为曲轴和滑块的中间连接件,它由连杆体和连杆盖两部分组成。
连杆大端与曲轴连接,小端通过滑块与柱塞连接。
选用工字型截面连杆,
它悬裒奄同样强度条件下,运动质量小、毛还可铸造等优点。
连杆小端轴承采用整体的青铜轴套,使小端结构简化。
大端轴承为双金属轴瓦。
小端采用滑块 _马滑块连接。
该连杆采用大端定位,在大端轴瓦两端面与曲柄销的配合端面之间采用较小的间隙(0.2〜0.5 mm),而在小端轴套端面与滑块配合端面之间取较大的间隙(2〜5 mm)。
• MRB—100/31.5型乳化液泵连杆选用QT40-10铸造成型,毛坯去毛刺后作喷丸处理,以消除铸造应力,并提高其机械设计性能。
1 .连杆基本尺寸的确定
2.连杆强度校核
3.连杆杆体的稳定性计算
4.连杆端盖的强度校核
5.连杆小端的强度校核
6.连杆螺栓的计算
羽表4.16螺栓校核
滑块销的设计计算
• 滑块销用来连接连杆与滑块,其受力情
况与连大端盖相似。
滑块销一般为空心圆柱型
•f块销的直径可按柱塞承受的最大压力P 确定
•确定基本尺寸
柱塞与泵头的设计计算
•本设计柱塞选用38CrMoAIA合金材料,调质热处理,HB约为229,表面氮化HV850,氮化层深c0.3mm
•柱塞强度的校核
•柱塞稳定性校核
•泵头的强度计算
吸、排液阀得设计计算及箱
体强度计算
•本乳化液泵采用三翼式锥形阀,采用1Cr13不锈钢材,调质热处理,HB=187〜217。
;为便于加工、使用和维修,进、排液阀采用通用结构。
阀口通流面积阀
芯
阀的最大开启高度
吸、排液阀弹簧阀
座比压验算
吸、排液阀弹簧的自振频率验算泵缸及阀的性能验算箱体强度计算
轴瓦和滚动轴承的核验计算
•连杆轴瓦的核验计算
•连杆小头衬套校核
•小齿轮轴轴承的验算
•曲轴轴承的验算
•本设计遵循一般机械设计步骤:搜集资料;开题;结构方案的设计确定;计算、绘草图并校核;画图;修改;最后完成毕业设计。
其中计算、绘草图是关键步骤。
•在计算绘草图中遵循一边绘草图,一边计算校核的原则。
从主要参数确定算起,到传动零件校核,最后到单向阀的计算。
中间对设计的原理进行了介绍。
• MRB—100/31.5型乳化液泵与配套乳化液箱组成乳化液泵站,为矿井下煤层综合机械化釆煤液压支架提供动力源。
泵站一般由两台泵组成,平时一台工作,一台检修,需大流量时两台泵可以同时开启。
•在毕业设计的半年多的时间里,我得到了老师、、同学的热情帮助,在这里,我向他们表示最衷心的感谢。
•首先,要感谢我的毕业设计导师〜老师,〜老师在做毕业设计时经常督促我,帮助我。
我的基础本来就打的不好,再加上这门设计有很多地方都是计算的,在这种情况下老师耐心的帮助我,在此我非常感谢我能选到这么善解人意,宽宏大量的老师。
谢谢。