液压缸计算
液压缸体内部压力计算公式

液压缸体内部压力计算公式液压系统是一种利用液体传递能量和控制工作机构的系统,其中液压缸是液压系统中的重要部件之一。
液压缸通过液压油的压力来产生线性运动,因此液压缸内部的压力是影响其工作性能的重要参数之一。
在液压系统中,计算液压缸内部压力是非常重要的,可以帮助工程师设计和选择合适的液压缸,保证系统的正常工作。
液压缸内部压力计算公式的推导。
液压缸内部的压力是由液压油的压力和活塞面积共同决定的。
假设液压缸的活塞面积为A,液压油的压力为P,液压缸内部的压力可以用以下公式表示:P = F/A。
其中P表示液压缸内部的压力,F表示液压缸所受到的力,A表示液压缸的活塞面积。
根据液压缸的工作原理可知,液压缸所受到的力F可以表示为:F = P × A。
将F代入液压缸内部压力的公式中,可以得到:P = (P × A) / A。
化简后可得到:P = P。
这个结果说明了液压缸内部的压力等于液压油的压力,这是由液压传动的工作原理决定的。
因此,液压缸内部压力计算公式可以简化为P = P。
液压缸内部压力计算公式的应用。
根据液压缸内部压力计算公式P = P,我们可以得出结论,液压缸内部的压力与液压油的压力成正比。
这意味着,如果液压油的压力增加,液压缸内部的压力也会增加;反之,如果液压油的压力减小,液压缸内部的压力也会减小。
在实际工程中,工程师可以根据液压缸的工作要求和系统的工作压力来选择合适的液压缸。
如果系统要求液压缸内部的压力较大,可以选择工作压力较高的液压油;如果系统要求液压缸内部的压力较小,可以选择工作压力较低的液压油。
此外,液压缸内部压力计算公式还可以用于设计和优化液压系统。
通过计算液压缸内部的压力,工程师可以确定液压缸的尺寸和工作压力,从而设计出满足系统要求的液压系统。
总结。
液压缸内部压力计算公式P = P是根据液压缸的工作原理推导出来的,它表明了液压缸内部的压力与液压油的压力成正比。
这个公式在液压系统的设计和选择中具有重要的应用价值,可以帮助工程师设计和选择合适的液压缸,保证系统的正常工作。
液压油缸缸径计算
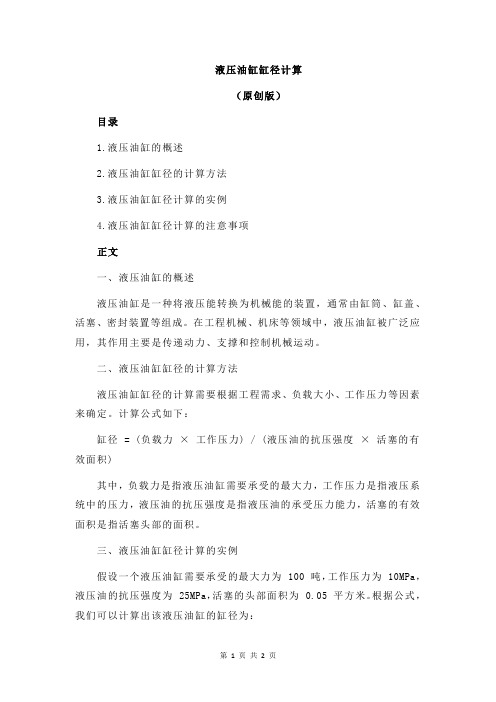
液压油缸缸径计算(原创版)目录1.液压油缸的概述2.液压油缸缸径的计算方法3.液压油缸缸径计算的实例4.液压油缸缸径计算的注意事项正文一、液压油缸的概述液压油缸是一种将液压能转换为机械能的装置,通常由缸筒、缸盖、活塞、密封装置等组成。
在工程机械、机床等领域中,液压油缸被广泛应用,其作用主要是传递动力、支撑和控制机械运动。
二、液压油缸缸径的计算方法液压油缸缸径的计算需要根据工程需求、负载大小、工作压力等因素来确定。
计算公式如下:缸径 = (负载力×工作压力) / (液压油的抗压强度×活塞的有效面积)其中,负载力是指液压油缸需要承受的最大力,工作压力是指液压系统中的压力,液压油的抗压强度是指液压油的承受压力能力,活塞的有效面积是指活塞头部的面积。
三、液压油缸缸径计算的实例假设一个液压油缸需要承受的最大力为 100 吨,工作压力为 10MPa,液压油的抗压强度为 25MPa,活塞的头部面积为 0.05 平方米。
根据公式,我们可以计算出该液压油缸的缸径为:缸径 = (100 × 10) / (25 × 0.05) = 400mm因此,该液压油缸的缸径应为 400mm。
四、液压油缸缸径计算的注意事项在计算液压油缸缸径时,需要注意以下几点:1.确保所选用的液压油符合工程需求,具有合适的抗压强度和粘度;2.考虑到液压系统的泄漏、热胀冷缩等因素,计算结果需要留有一定的余量;3.活塞的有效面积需要准确测量,以保证计算结果的准确性;4.在选择缸径时,还需要考虑到液压油缸的安装空间、成本等因素。
综上所述,液压油缸缸径的计算是一个复杂的过程,需要根据工程需求、负载大小、工作压力等多种因素来确定。
液压缸计算公式
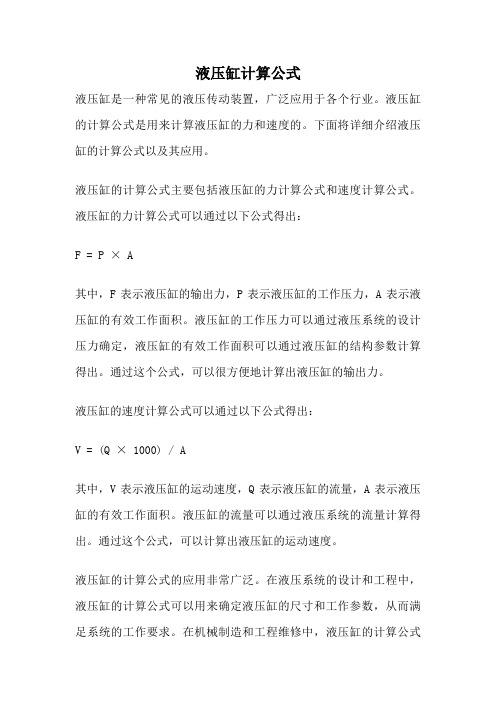
液压缸计算公式液压缸是一种常见的液压传动装置,广泛应用于各个行业。
液压缸的计算公式是用来计算液压缸的力和速度的。
下面将详细介绍液压缸的计算公式以及其应用。
液压缸的计算公式主要包括液压缸的力计算公式和速度计算公式。
液压缸的力计算公式可以通过以下公式得出:F = P × A其中,F表示液压缸的输出力,P表示液压缸的工作压力,A表示液压缸的有效工作面积。
液压缸的工作压力可以通过液压系统的设计压力确定,液压缸的有效工作面积可以通过液压缸的结构参数计算得出。
通过这个公式,可以很方便地计算出液压缸的输出力。
液压缸的速度计算公式可以通过以下公式得出:V = (Q × 1000) / A其中,V表示液压缸的运动速度,Q表示液压缸的流量,A表示液压缸的有效工作面积。
液压缸的流量可以通过液压系统的流量计算得出。
通过这个公式,可以计算出液压缸的运动速度。
液压缸的计算公式的应用非常广泛。
在液压系统的设计和工程中,液压缸的计算公式可以用来确定液压缸的尺寸和工作参数,从而满足系统的工作要求。
在机械制造和工程维修中,液压缸的计算公式可以用来评估液压缸的工作性能和故障排除。
液压缸的计算公式还可以用来优化液压系统的设计。
通过合理选择液压缸的尺寸和工作参数,可以提高液压系统的效率和稳定性。
同时,液压缸的计算公式也可以用来对液压系统进行性能测试和评估,为系统的优化提供依据。
液压缸的计算公式是液压系统设计和工程应用中的重要工具。
通过合理应用这些公式,可以方便地计算液压缸的力和速度,从而满足系统的工作要求。
液压缸的计算公式的应用范围广泛,对于液压系统的设计、制造和维修都具有重要意义。
希望本文的介绍对读者有所帮助。
液压缸计算

液压缸设计计算说明 系统压力为1p =25 MPa本系统中有顶弯缸、拉伸缸以及压弯缸。
以下为这三种液压缸的设计计算。
一、 顶弯缸 1 基本参数的确定(1)按推力F 计算缸筒内径D根据公式 3.5710D -=⨯ ① 其中,推力F=120KN系统压力1p =25 MPa带入①式,计算得D= 78.2mm ,圆整为D = 80 mm (2)活塞杆直径d 的确定确定活塞杆直径d 时,通常应先满足液压缸速度或速比的要求,然后再校核其结构强度和稳定性。
若速比为ϕ,则d = ② 取ϕ=1.6,带入②式,计算得d =48.9mm ,圆整为d =50mm8050D d ϕ===1.6 (3)最小导向长度H 的确定对一般的液压缸,最小导向长度H 应满足202L DH ≥+ ③ 其中,L 为液压缸行程,L=500mm带入③式,计算得H=65mm (4)活塞宽度B 的确定活塞宽度一般取(0.6~1.0)B D = ④ 得B=48mm~80mm ,取B=60mm (5)导向套滑动面长度A 的确定在D <80mm 时,取(0.6~1.0)A D = ⑤ D >80mm 时,取(0.6~1.0)A d = ⑥ 根据⑤式,得A=48mm~80mm ,取A=50mm (6)隔套长度C 的确定 根据公式2A BC H +=-⑦ 代入数据,解得C=10mm 2 结构强度计算与稳定校核 (1)缸筒外径缸筒内径确定后,有强度条件确定壁厚δ,然后求出缸筒外径D 1假设此液压缸为厚壁缸筒,则壁厚1]2D δ=⑧ 液压缸筒材料选用45号钢。
其抗拉强度为σb =600MPa 其中许用应力[]b nσσ=,n为安全系数,取n=5将数据带入⑧式,计算得δ=8.76mm故液压缸筒外径为D 1=D+2δ=97.52mm ,圆整后有 D 1=100mm ,缸筒壁厚δ=10mm (2)液压缸的稳定性和活塞杆强度验算按速比要求初步确定活塞杆直径后,还必须满足液压缸的稳定性及其强度要求。
液压缸的计算

(2)伸缩缸。
伸缩缸由两个或多个活塞缸套装而成,前一级活塞缸的活塞杆内孔是后一级活塞缸的缸筒,伸出时可获得很长的工作行程,缩回时可保持很小的结构尺寸,伸缩缸被广泛用于起重运输车辆上。
伸缩缸可以是如图4-10(a)所示的单作用式,也可以是如图4-10(b)所示的双作用式,前者靠外力回程,后者靠液压回程。
图4-10伸缩缸伸缩缸的外伸动作是逐级进行的。
首先是最大直径的缸筒以最低的油液压力开始外伸,当到达行程终点后,稍小直径的缸筒开始外伸,直径最小的末级最后伸出。
随着工作级数变大,外伸缸筒直径越来越小,工作油液压力随之升高,工作速度变快。
其值为:F i=p124iD(4-30)V1=4q/πD i2 (4-31) 式中的i指i级活塞缸。
图4-11齿轮缸(3)齿轮缸。
它由两个柱塞缸和一套齿条传动装置组成,如图4-11所示。
柱塞的移动经齿轮齿条传动装置变成齿轮的传动,用于实现工作部件的往复摆动或间歇进给运动。
二、液压缸的典型结构和组成1.液压缸的典型结构举例图4-12所示的是一个较常用的双作用单活塞杆液压缸。
它是由缸底20、缸筒10、缸盖兼导向套9、活塞11和活塞杆18组成。
缸筒一端与缸底焊接,另一端缸盖(导向套)与缸筒用卡键6、套5和弹簧挡圈4固定,以便拆装检修,两端设有油口A和B。
活塞11与活塞杆18利用卡键15、卡键帽16和弹簧挡圈17连在一起。
活塞与缸孔的密封采用的是一对Y形聚氨酯密封圈12,由于活塞与缸孔有一定间隙,采用由尼龙1010制成的耐磨环(又叫支承环)13定心导向。
杆18和活塞11的内孔由密封圈14密封。
较长的导向套9则可保证活塞杆不偏离中心,导向套外径由O形圈7密封,而其内孔则由Y形密封圈8和防尘圈3分别防止油外漏和灰尘带入缸内。
缸与杆端销孔与外界连接,销孔内有尼龙衬套抗磨。
图4-12双作用单活塞杆液压缸1—耳环2—螺母3—防尘圈4、17—弹簧挡圈5—套6、15—卡键7、14—O形密封圈8、12—Y形密封圈9—缸盖兼导向套10—缸筒11—活塞13—耐磨环16—卡键帽18—活塞杆19—衬套20—缸底如图4-13所示为一空心双活塞杆式液压缸的结构。
液压油缸推力计算公式

液压油缸推力计算公式
液压油缸推力计算公式是液压系统领域中非常重要的一种计算方法。
液压油缸是液压系统中的重要组成部分,负责将压力转化为力,推动机械设备运转,因此其推力大小的计算非常关键。
液压油缸推力计算公式的基本原理是根据液压油缸的几何尺寸和液压系统的工作压力,计算出液压油缸的理论推力大小。
液压油缸推力的大小受到多种因素的影响,如液压油缸的内径、活塞杆的直径、液压系统的工作压力等。
液压油缸推力计算公式的具体表达式如下:
F=π/4×D²×P
其中,F表示液压油缸的推力大小,单位为牛顿(N)或千克力(kgf);π为圆周率,约等于3.14;D为液压油缸的内径,单位为米(m)或毫米(mm);P为液压系统的工作压力,单位为帕斯卡(Pa)或巴(bar)。
由公式可以看出,液压油缸的推力大小与液压油缸的内径和液压系统的工作压力成正比,而与液压油缸的活塞杆直径无关。
因此,在设计液压系统时,需要根据液压油缸的推力需求和工作环境压力等因素,合理选择液压油缸的内径和液压系统的工作压力,以确保液压油缸的推力能够满足机械设备的需求。
需要注意的是,液压油缸的实际推力大小与其理论推力大小存在一定的误差。
这是由于液压油缸的摩擦力、密封性能、活塞杆的弯曲等因素的影响所导致的。
因此,在实际应用中,需要根据实际情况对液压油缸的推力进行调整和修正,以确保其能够正常工作。
液压油缸推力计算公式是液压系统设计和应用中非常重要的一种计算方法。
合理地应用该公式,可以有效地计算出液压油缸的理论推力大小,为机械设备的正常运行提供有力的支持。
液压缸的计算范文
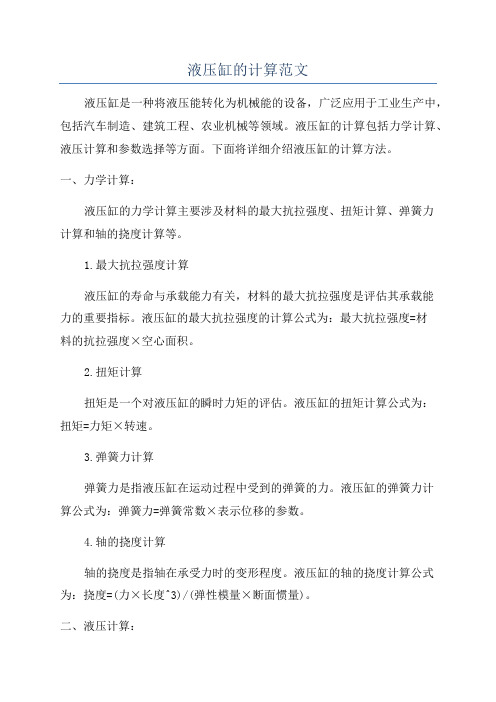
液压缸的计算范文液压缸是一种将液压能转化为机械能的设备,广泛应用于工业生产中,包括汽车制造、建筑工程、农业机械等领域。
液压缸的计算包括力学计算、液压计算和参数选择等方面。
下面将详细介绍液压缸的计算方法。
一、力学计算:液压缸的力学计算主要涉及材料的最大抗拉强度、扭矩计算、弹簧力计算和轴的挠度计算等。
1.最大抗拉强度计算液压缸的寿命与承载能力有关,材料的最大抗拉强度是评估其承载能力的重要指标。
液压缸的最大抗拉强度的计算公式为:最大抗拉强度=材料的抗拉强度×空心面积。
2.扭矩计算扭矩是一个对液压缸的瞬时力矩的评估。
液压缸的扭矩计算公式为:扭矩=力矩×转速。
3.弹簧力计算弹簧力是指液压缸在运动过程中受到的弹簧的力。
液压缸的弹簧力计算公式为:弹簧力=弹簧常数×表示位移的参数。
4.轴的挠度计算轴的挠度是指轴在承受力时的变形程度。
液压缸的轴的挠度计算公式为:挠度=(力×长度^3)/(弹性模量×断面惯量)。
二、液压计算:液压计算是液压缸设计中的重要过程,主要涉及液压缸的压力计算、液体流量计算和功率计算等。
1.压力计算液压缸的压力计算是指在给定的液体流量和缸的截面积下,计算液压缸所需的压力。
压力计算公式为:压力=力/面积。
2.流量计算液压缸的流量计算是指在给定的工作压力下,计算液压缸所需的液体流量。
流量计算公式为:流量=需要的液体流量/时间。
3.功率计算液压缸的功率计算是指在给定的压力和流量下,计算液压缸的功率。
功率计算公式为:功率=压力×流量。
三、参数选择:液压缸的参数选择是确保其正常工作的关键步骤,主要包括推力、速度、行程、缸筒直径和活塞杆直径等参数的选择。
1.推力的选择液压缸的推力是指在给定的工作条件下,液压缸所能提供的最大力。
推力的选择应满足工作条件所需的最小信号力。
2.速度的选择液压缸的速度是指液压缸的活塞在单位时间内的位移速度。
速度的选择应满足工作条件所需的最大速度。
液压缸基本参数的计算

b 2
(R
2 2
R
2 1
)(p 1
p2 )ηm
w
2πn
2q η v
b(R
2 2
R12 )
双叶片式 摆动角度一般小于150°。但在相同条件下,输出转矩是
单叶片摆动缸的两倍,输出角速度是单叶片缸的一半。
单叶片式 摆动角度较大,可达300°。
结构
五、组合式液压缸
1.串联液压缸
是由两个缸组成的串连液压缸。两个缸分别有自己的进油口、 出油口,缸筒固定在同一个活塞杆上。两个缸的进油口相连,出 油口也相连。串连液压缸的输出力是两个缸输出力的总和。
一、双活塞杆缸的计算 双活塞杆缸活塞两侧都有活塞杆伸出(动画)。
参数计算
v
q A
4q π(D2 d
2
)
F
π 4
(D2
d
2
)(p1
p2
)
双活塞杆缸根据安装方式不同又分为活塞杆固 定式和缸筒固定式两种。
当缸筒固定时,运动部件移动范围是活塞有效 行程的三倍;当活塞杆固定时,运动部件移动 范围是活塞有效行程的两倍 。
3.伸缩缸
由两个或多个活塞式缸套装而成。前一级活塞缸的活塞杆是 后一级活塞缸的缸筒。各级活塞依次伸出可获得很长的行程,当 依次缩回时缸的轴向尺寸很小。除双作用伸缩液压缸外,还有单 作用伸缩液压缸,它与双作用不同点是回程靠外力,而双作用靠 液压作用力。 动画4.2-4
双作用式伸缩缸
参数计算
Fi
P1
参数计算
单向运动时
双向运动时
v
4q πd 2
- 1、下载文档前请自行甄别文档内容的完整性,平台不提供额外的编辑、内容补充、找答案等附加服务。
- 2、"仅部分预览"的文档,不可在线预览部分如存在完整性等问题,可反馈申请退款(可完整预览的文档不适用该条件!)。
- 3、如文档侵犯您的权益,请联系客服反馈,我们会尽快为您处理(人工客服工作时间:9:00-18:30)。
液压缸设计计算说明
系统压力为1p =25 MPa
本系统中有顶弯缸、拉伸缸以及压弯缸。
以下为这三种液压缸的设计计算。
一、 顶弯缸
1 基本参数的确定
(1)按推力F 计算缸筒内径D
根据公式 3.5710D -=⨯ ① 其中,推力F=120KN
系统压力1p =25 MPa 带入①式,计算得D= 78.2mm ,圆整为D = 80 mm
(2)活塞杆直径d 的确定
确定活塞杆直径d 时,通常应先满足液压缸速度或速比的要求,然后再校核其结构强度和稳定性。
若速比为ϕ,则
d = ② 取ϕ=1.6,带入②式,计算得d =48.9mm ,圆整为d =50mm 8050
D d ϕ===1.6 (3)最小导向长度H 的确定
对一般的液压缸,最小导向长度H 应满足
202
L D H ≥+ ③ 其中,L 为液压缸行程,L=500mm
带入③式,计算得H=65mm
(4)活塞宽度B 的确定
活塞宽度一般取(0.6~1.0)B D = ④ 得B=48mm~80mm ,取B=60mm
(5)导向套滑动面长度A 的确定
在D <80mm 时,取(0.6~1.0)A D = ⑤ D >80mm 时,取(0.6~1.0)A d = ⑥ 根据⑤式,得A=48mm~80mm ,取A=50mm
(6)隔套长度C 的确定 根据公式2
A B C H +=- ⑦ 代入数据,解得C=10mm
2 结构强度计算与稳定校核
(1)缸筒外径
缸筒内径确定后,有强度条件确定壁厚δ,然后求出缸筒外径D 1
假设此液压缸为厚壁缸筒,则壁厚1]2D δ= ⑧ 液压缸筒材料选用45号钢。
其抗拉强度为σb =600MPa 其中许用应力[]b
n σσ=,n 为安全系数,取n=5
将数据带入⑧式,计算得δ=8.76mm
故液压缸筒外径为D 1=D+2δ=97.52mm ,圆整后有
D 1=100mm ,缸筒壁厚δ=10mm
(2)液压缸的稳定性和活塞杆强度验算
按速比要求初步确定活塞杆直径后,还必须满足液压缸的稳定性及其
强度要求。
由液压缸的固定形式,查表得,l/d <10,不需要进行稳定性验算。
l/d <10时,当活塞杆受纯压缩或纯拉伸时有
()
[]2214F d d σσπ=≤- ⑨ 式中,d 1为空心活塞杆内径,对实心杆,d 1=0
[σ]为活塞杆材料的许用应力,[]s n σσ=
,s σ为材料的屈服点,安
全系数n=1.4~2
活塞杆为实心杆,材料选用45号钢,s σ=335MPa ,安全系数取n=2,
将数据带入⑨式,计算得,σ=61.1155MPa ≤[]σ
强度满足要求。
3 液压缸其他结构的设计
(1)液压缸的密封
活塞杆与液压缸之间 活塞杆与液压缸之间为往复运动密封。
选用A 型液压缸活塞杆用防尘圈(FA50×58×5 GB/T 10708.3-1989)和活塞杆用高低唇Y 型橡胶密封圈(Y60×50×8 GB/T10708.1-1989) 活塞上的密封 活塞的密封选用活塞用高低唇Y 型橡胶密封圈(Y80×65×12.5 GB/T10708.1-1989)
端盖与缸体之间 液压缸选用法兰连接,端盖与缸体之间选用O 型橡胶密封圈(75×2.65 G GB/T 3452.1-1992)
(2)液压缸的缓冲装置
当活塞杆速度大于0.1m/s 时,需要设置缓冲装置。
该顶弯缸最大速度为0.08m/s ,不需要设置和缓冲装置。
二、拉伸缸
1 基本参数的确定
(1)按推力F计算缸筒内径D
将推力F=60KN,系统压力
p=25 MPa带入①式,计算得D=55.3mm
1
圆整为D=63mm
(2)活塞杆直径d的确定
取ϕ=1.8,带入②式,计算得d=42mm,圆整为d=45mm
(3)最小导向长度H的确定
此缸的行程L=250mm,带入③式,计算得H=44mm
(4)活塞宽度B的确定
根据公式④,有B=37.8mm~63mm,取B=40mm
(5)导向套滑动面长度A的确定
因为D=63mm≤80mm,故根据公式⑤,有A=37.8mm~63mm,取A=40mm
(6)隔套长度C的确定
将A、B、H带入公式⑦,计算得C=4mm
2 结构强度计算与稳定校核
(1)缸筒外径
假设此液压缸为厚壁缸筒,液压缸筒材料选用45号钢,抗拉强度为σ
=600MPa,安全系数取n=5。
将以上数据带入⑧式,计算得δ=6.90mm b
故液压缸筒外径为D1=D+2δ=76.8mm,圆整取
D1=80mm,缸筒壁厚δ=8.5mm
(2)液压缸的稳定性和活塞杆强度验算
由液压缸的固定形式,查表得,l/d<10,不需要进行稳定性验算。
活塞杆为实心杆,材料选用45号钢,
σ=335MPa,安全系数取n=2,
s
当活塞杆受纯压缩或纯拉伸时,根据公式⑨,代入数据,计算得
σ=37.7256MPa≤[]σ
强度满足要求。
3 液压缸其他结构的设计
(1)液压缸的密封
活塞杆与液压缸之间活塞杆与液压缸之间为往复运动密封。
选用A型液压缸活塞杆用防尘圈(FA45×53×5 GB/T 10708.3-1989)和活塞杆用高低唇Y型橡胶密封圈(Y55×45×8 GB/T10708.1-1989)
活塞上的密封活塞的密封选用活塞用高低唇Y型橡胶密封圈(Y63×53×8 GB/T10708.1-1989)
端盖与缸体之间液压缸选用法兰连接,端盖与缸体之间选用O型橡胶密封圈(58×2.65 G GB/T 3452.1-1992)
(2)液压缸的缓冲装置
当活塞杆速度大于0.1m/s时,需要设置缓冲装置。
该顶弯缸最大速度为0.045m/s,不需要设置和缓冲装置。
三、压弯缸
1 基本参数的确定
(1)按推力F计算缸筒内径D
将推力F=80KN,系统压力
p=25 MPa带入①式,计算得D=63.8mm
1
圆整为D=63mm
(2)活塞杆直径d 的确定
取ϕ=1.6,带入②式,计算得d =38.57mm ,圆整为d=40mm
(3)最小导向长度H 的确定
此缸的行程L=500mm ,带入③式,计算得H=56.5mm
(4)活塞宽度B 的确定
根据公式④,有B=37.8mm~63mm ,取B=40mm
(5)导向套滑动面长度A 的确定
因为D=63mm ≤80mm ,故根据公式⑤,有A=37.8mm~63mm ,取A=40mm
(6)隔套长度C 的确定
将A 、B 、H 带入公式⑦,计算得C=16.5mm
2 结构强度计算与稳定校核
(1)缸筒外径
假设此液压缸为厚壁缸筒,液压缸筒材料选用45号钢,抗拉强度为σb =600MPa ,安全系数取n=5。
将以上数据带入⑧式,计算得δ=6.90mm 故液压缸筒外径为D 1=D+2δ=76.8mm ,圆整取
D 1=80mm ,缸筒壁厚δ=8.5mm
(2)液压缸的稳定性和活塞杆强度验算
由液压缸的固定形式,查表得,l/d >10,需要进行稳定性验算。
对液压缸,其稳定条件为
K K
F F n ≤ ⑩
式中,F 为液压缸的最大推力,F=80KN
F K 为液压缸的临界力 n K 为稳定性安全系数,一般为2~4,取n K =4
将数据带入⑩式,计算得F K ≥320KN
又有柔度为l r μλ=
,其中r =,I 为活塞杆端面的最小惯性矩,4
64d I π=。
查表得,μ=0.5
故有λ=25
而45号钢的对应于屈服极限时的柔度值λs=4613352.568s a b σ--===49.07 λ<λs ,故为短粗杆,只需满足cr σ<s σ即可。
cr σ=K F A
==254.65MPa <335MPa 液压缸稳定性满足要求。
活塞杆为实心杆,材料选用45号钢,s σ=335MPa ,安全系数取n=2,
当活塞杆受纯压缩或纯拉伸时,根据公式⑨,代入数据,计算得 σ=63.6620MPa ≤[]σ
强度满足要求。
3 液压缸其他结构的设计
(1)液压缸的密封
活塞杆与液压缸之间 活塞杆与液压缸之间为往复运动密封。
选用A 型液压缸活塞杆用防尘圈(FA40×48×5 GB/T 10708.3-1989)和活塞杆用高低唇Y 型橡胶密封圈(Y50×40×8 GB/T10708.1-1989)
活塞上的密封活塞的密封选用活塞用高低唇Y型橡胶密封圈(Y63×53×8 GB/T10708.1-1989)
端盖与缸体之间液压缸选用法兰连接,端盖与缸体之间选用O型橡胶密封圈(58×2.65 G GB/T 3452.1-1992)
(2)液压缸的缓冲装置
当活塞杆速度大于0.1m/s时,需要设置缓冲装置。
该顶弯缸最大速度为0.08m/s,不需要设置和缓冲装置。