液压缸设计计算公式
液压油缸设计计算公式

液压油缸的主要设计技术参数一、液压油缸的主要技术参数:1.油缸直径;油缸缸径,内径尺寸。
2. 进出口直径及螺纹参数3.活塞杆直径;4.油缸压力;油缸工作压力,计算的时候经常是用试验压力,低于16MPa乘以,高于16乘以5.油缸行程;6.是否有缓冲;根据工况情况定,活塞杆伸出收缩如果冲击大一般都要缓冲的。
7.油缸的安装方式;达到要求性能的油缸即为好,频繁出现故障的油缸即为坏。
应该说是合格与不合格吧好和合格还是有区别的。
二、液压油缸结构性能参数包括:1.液压缸的直径;2.活塞杆的直径;3.速度及速比;4.工作压力等。
液压缸产品种类很多,衡量一个油缸的性能好坏主要出厂前做的各项试验指标,油缸的工作性能主要表现在以下几个方面:1.最低启动压力:是指液压缸在无负载状态下的最低工作压力,它是反映液压缸零件制造和装配精度以及密封摩擦力大小的综合指标;2.最低稳定速度:是指液压缸在满负荷运动时没有爬行现象的最低运动速度,它没有统一指标,承担不同工作的液压缸,对最低稳定速度要求也不相同。
3.内部泄漏:液压缸内部泄漏会降低容积效率,加剧油液的温升,影响液压缸的定位精度,使液压缸不能准确地、稳定地停在缸的某一位置,也因此它是液压缸的主要指标之。
液压油缸常用计算公式液压油缸常用计算公式项目公式符号意义液压油缸面积 (cm 2 ) A =πD 2 /4 D :液压缸有效活塞直径 (cm) 液压油缸速度 (m/min) V = Q / A Q :流量 (l / min)液压油缸需要的流量(l/min) Q=V×A/10=A×S/10tV :速度 (m/min)S :液压缸行程 (m)t :时间 (min)液压油缸出力 (kgf)F = p × AF = (p × A) -(p×A)p :压力 (kgf /cm 2 )非标液压、机电、试验、工控设备开发研制。
液压缸无杆腔面积A=*40*40/ (平方米)=(平方米)泵的理论流量Q=排量*转速=32*1430/1000000 (立方米/分)=(立方米/分)液压缸运动速度约为V=*Q/A= m/min所用时间约为T=缸的行程/速度=L/V==8 (秒) 上面的计算是在系统正常工作状态时计算的,如果溢流阀的安全压力调得较低,负载过大,液压缸的速度就没有上面计算的大,时间T就会增大. 楼主应把系统工作状态说得更清楚一些.其实这是个很简单的问题:你先求出油缸的体积,会求吧,等于:4021238立方毫米;然后再求出泵的每分钟流量,需按实际计算,效率取92%(国家标准),得出流量为:32X1430X1000X92%=立方毫米;两数一除就得出时间:分钟,也就是秒,至于管道什么流速什么的东西根本不要考虑,影响比较少.油缸主要尺寸的确定方法1.油缸的主要尺寸油缸的主要尺寸包括:缸筒内径、活塞缸直径、缸筒长度以及缸筒壁厚等。
液压缸计算公式
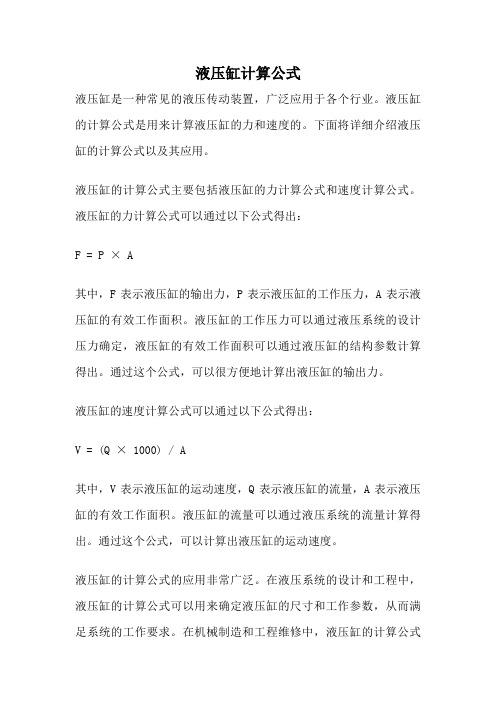
液压缸计算公式液压缸是一种常见的液压传动装置,广泛应用于各个行业。
液压缸的计算公式是用来计算液压缸的力和速度的。
下面将详细介绍液压缸的计算公式以及其应用。
液压缸的计算公式主要包括液压缸的力计算公式和速度计算公式。
液压缸的力计算公式可以通过以下公式得出:F = P × A其中,F表示液压缸的输出力,P表示液压缸的工作压力,A表示液压缸的有效工作面积。
液压缸的工作压力可以通过液压系统的设计压力确定,液压缸的有效工作面积可以通过液压缸的结构参数计算得出。
通过这个公式,可以很方便地计算出液压缸的输出力。
液压缸的速度计算公式可以通过以下公式得出:V = (Q × 1000) / A其中,V表示液压缸的运动速度,Q表示液压缸的流量,A表示液压缸的有效工作面积。
液压缸的流量可以通过液压系统的流量计算得出。
通过这个公式,可以计算出液压缸的运动速度。
液压缸的计算公式的应用非常广泛。
在液压系统的设计和工程中,液压缸的计算公式可以用来确定液压缸的尺寸和工作参数,从而满足系统的工作要求。
在机械制造和工程维修中,液压缸的计算公式可以用来评估液压缸的工作性能和故障排除。
液压缸的计算公式还可以用来优化液压系统的设计。
通过合理选择液压缸的尺寸和工作参数,可以提高液压系统的效率和稳定性。
同时,液压缸的计算公式也可以用来对液压系统进行性能测试和评估,为系统的优化提供依据。
液压缸的计算公式是液压系统设计和工程应用中的重要工具。
通过合理应用这些公式,可以方便地计算液压缸的力和速度,从而满足系统的工作要求。
液压缸的计算公式的应用范围广泛,对于液压系统的设计、制造和维修都具有重要意义。
希望本文的介绍对读者有所帮助。
液压油缸设计计算公式
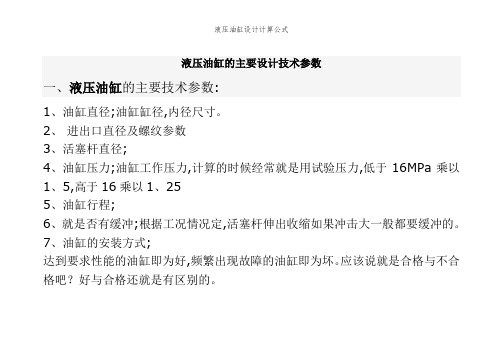
液压油缸的主要设计技术参数一、液压油缸的主要技术参数:1、油缸直径;油缸缸径,内径尺寸。
2、进出口直径及螺纹参数3、活塞杆直径;4、油缸压力;油缸工作压力,计算的时候经常就是用试验压力,低于16MPa乘以1、5,高于16乘以1、255、油缸行程;6、就是否有缓冲;根据工况情况定,活塞杆伸出收缩如果冲击大一般都要缓冲的。
7、油缸的安装方式;达到要求性能的油缸即为好,频繁出现故障的油缸即为坏。
应该说就是合格与不合格吧?好与合格还就是有区别的。
二、液压油缸结构性能参数包括:1、液压缸的直径;2、活塞杆的直径;3、速度及速比;4、工作压力等。
液压缸产品种类很多,衡量一个油缸的性能好坏主要出厂前做的各项试验指标,油缸的工作性能主要表现在以下几个方面:1、最低启动压力:就是指液压缸在无负载状态下的最低工作压力,它就是反映液压缸零件制造与装配精度以及密封摩擦力大小的综合指标;2、最低稳定速度:就是指液压缸在满负荷运动时没有爬行现象的最低运动速度,它没有统一指标,承担不同工作的液压缸,对最低稳定速度要求也不相同。
3、内部泄漏:液压缸内部泄漏会降低容积效率,加剧油液的温升,影响液压缸的定位精度,使液压缸不能准确地、稳定地停在缸的某一位置,也因此它就是液压缸的主要指标之。
液压油缸常用计算公式液压油缸常用计算公式项目公式符号意义液压油缸面积(cm 2 ) A =πD 2 /4 D :液压缸有效活塞直径(cm)液压油缸速度(m/min) V = Q / A Q :流量(l / min)液压油缸需要的流量(l/min) Q=V×A/10=A×S/10tV :速度(m/min)S :液压缸行程(m)t :时间(min)液压油缸出力(kgf) F = p × AF = (p × A) -(p×A)( 有背压存在时)p :压力(kgf /cm 2 )泵或马达流量(l/min) Q = q × n / 1000 q :泵或马达的几何排量(cc/rev) n :转速( rpm )泵或马达转速(rpm) n = Q / q ×1000 Q :流量(l / min) 泵或马达扭矩(N、m) T = q × p / 20π非标液压、机电、试验、工控设备开发研制。
液压油缸推力计算公式

液压油缸推力计算公式
液压油缸推力计算公式是液压系统领域中非常重要的一种计算方法。
液压油缸是液压系统中的重要组成部分,负责将压力转化为力,推动机械设备运转,因此其推力大小的计算非常关键。
液压油缸推力计算公式的基本原理是根据液压油缸的几何尺寸和液压系统的工作压力,计算出液压油缸的理论推力大小。
液压油缸推力的大小受到多种因素的影响,如液压油缸的内径、活塞杆的直径、液压系统的工作压力等。
液压油缸推力计算公式的具体表达式如下:
F=π/4×D²×P
其中,F表示液压油缸的推力大小,单位为牛顿(N)或千克力(kgf);π为圆周率,约等于3.14;D为液压油缸的内径,单位为米(m)或毫米(mm);P为液压系统的工作压力,单位为帕斯卡(Pa)或巴(bar)。
由公式可以看出,液压油缸的推力大小与液压油缸的内径和液压系统的工作压力成正比,而与液压油缸的活塞杆直径无关。
因此,在设计液压系统时,需要根据液压油缸的推力需求和工作环境压力等因素,合理选择液压油缸的内径和液压系统的工作压力,以确保液压油缸的推力能够满足机械设备的需求。
需要注意的是,液压油缸的实际推力大小与其理论推力大小存在一定的误差。
这是由于液压油缸的摩擦力、密封性能、活塞杆的弯曲等因素的影响所导致的。
因此,在实际应用中,需要根据实际情况对液压油缸的推力进行调整和修正,以确保其能够正常工作。
液压油缸推力计算公式是液压系统设计和应用中非常重要的一种计算方法。
合理地应用该公式,可以有效地计算出液压油缸的理论推力大小,为机械设备的正常运行提供有力的支持。
液压缸设计计算公式
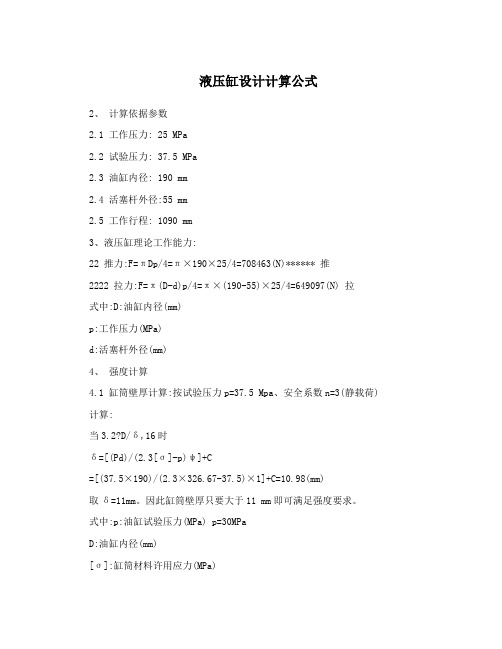
液压缸设计计算公式2、计算依据参数2.1 工作压力: 25 MPa2.2 试验压力: 37.5 MPa2.3 油缸内径: 190 mm2.4 活塞杆外径:55 mm2.5 工作行程: 1090 mm3、液压缸理论工作能力:22 推力:F=πDp/4=π×190×25/4=708463(N)****** 推2222 拉力:F=π(D-d)p/4=π×(190-55)×25/4=649097(N) 拉式中:D:油缸内径(mm)p:工作压力(MPa)d:活塞杆外径(mm)4、强度计算4.1 缸筒壁厚计算:按试验压力p=37.5 Mpa、安全系数n=3(静载荷) 计算:当3.2?D/δ,16时δ=[(Pd)/(2.3[σ]-p)ψ]+C=[(37.5×190)/(2.3×326.67-37.5)×1]+C=10.98(mm)取δ=11mm。
因此缸筒壁厚只要大于11 mm即可满足强度要求。
式中:p:油缸试验压力(MPa) p=30MPaD:油缸内径(mm)[σ]:缸筒材料许用应力(MPa)[σ] =σ/n=980/3=326.67(M Pa) bσ:缸筒材料的抗拉强度(MPa) b查手册:27SiMn的σ=980MPa bn:取安全系数n=3(静载荷)ψ:强度系数(当为无缝钢管时ψ=1)C:计入壁厚公差及腐蚀的附加厚度(一般应将壁厚圆整至标准厚度值)4.4 活塞杆螺纹连接强度计算活塞杆试验最大拉力:22 P=π(D-d)p/422 =π×(190-55)×37.5/4=973646(N)活塞杆危险断面处的拉应力:2 σ =P/ [π×d/4] 12 =973646/[π×45.2/4]=607.1(MPa)式中:P:活塞杆试验最大拉力(N)D:油缸内径(mm)d:活塞杆外径(mm)d:活塞杆危险断面处直径,初选是活塞杆O型圈沟槽1 (mm)σ:活塞杆材料屈服强度(MPa) s查手册 42CrMo钢调质,取σ=930MPa sn:安全系数,取n=1.5因为σ ?[σ]=620MPa,所以螺纹强度能够满足要求。
液压缸的计算范文
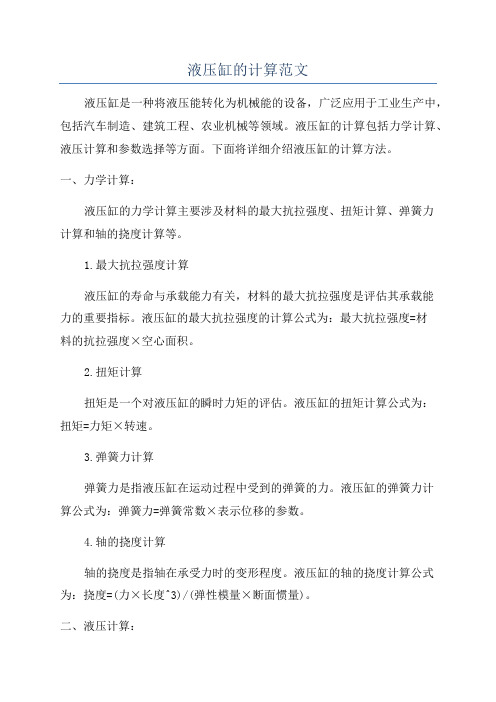
液压缸的计算范文液压缸是一种将液压能转化为机械能的设备,广泛应用于工业生产中,包括汽车制造、建筑工程、农业机械等领域。
液压缸的计算包括力学计算、液压计算和参数选择等方面。
下面将详细介绍液压缸的计算方法。
一、力学计算:液压缸的力学计算主要涉及材料的最大抗拉强度、扭矩计算、弹簧力计算和轴的挠度计算等。
1.最大抗拉强度计算液压缸的寿命与承载能力有关,材料的最大抗拉强度是评估其承载能力的重要指标。
液压缸的最大抗拉强度的计算公式为:最大抗拉强度=材料的抗拉强度×空心面积。
2.扭矩计算扭矩是一个对液压缸的瞬时力矩的评估。
液压缸的扭矩计算公式为:扭矩=力矩×转速。
3.弹簧力计算弹簧力是指液压缸在运动过程中受到的弹簧的力。
液压缸的弹簧力计算公式为:弹簧力=弹簧常数×表示位移的参数。
4.轴的挠度计算轴的挠度是指轴在承受力时的变形程度。
液压缸的轴的挠度计算公式为:挠度=(力×长度^3)/(弹性模量×断面惯量)。
二、液压计算:液压计算是液压缸设计中的重要过程,主要涉及液压缸的压力计算、液体流量计算和功率计算等。
1.压力计算液压缸的压力计算是指在给定的液体流量和缸的截面积下,计算液压缸所需的压力。
压力计算公式为:压力=力/面积。
2.流量计算液压缸的流量计算是指在给定的工作压力下,计算液压缸所需的液体流量。
流量计算公式为:流量=需要的液体流量/时间。
3.功率计算液压缸的功率计算是指在给定的压力和流量下,计算液压缸的功率。
功率计算公式为:功率=压力×流量。
三、参数选择:液压缸的参数选择是确保其正常工作的关键步骤,主要包括推力、速度、行程、缸筒直径和活塞杆直径等参数的选择。
1.推力的选择液压缸的推力是指在给定的工作条件下,液压缸所能提供的最大力。
推力的选择应满足工作条件所需的最小信号力。
2.速度的选择液压缸的速度是指液压缸的活塞在单位时间内的位移速度。
速度的选择应满足工作条件所需的最大速度。
液压缸出力计算
液压缸出力计算液压缸是液压系统中常用的执行元件之一,它能够将液压能转化为机械能,实现线性运动或产生力。
液压缸出力的计算是液压系统设计过程中的重要环节之一,它涉及到液压缸的工作压力、活塞面积和力的计算等多个因素。
液压缸的出力主要受到工作压力的影响。
工作压力是指液压系统中液体传递的压力,通常以帕斯卡(Pa)为单位。
在液压缸中,工作压力作用在活塞上,通过活塞面积来传递力。
液压缸的活塞面积是指活塞面积的大小,通常以平方米(m²)为单位。
活塞面积越大,液压缸的出力就越大。
液压缸的出力计算公式为:出力 = 工作压力× 活塞面积其中,出力以牛顿(N)为单位。
这个公式表明,液压缸的出力与工作压力和活塞面积的乘积有关。
因此,在液压系统设计中,需要根据实际需求确定液压缸的工作压力和活塞面积,从而计算出液压缸的出力。
在实际应用中,液压缸的出力计算需要考虑多个因素。
首先是工作压力的确定,工作压力应根据液压系统的需求以及液压缸的承受能力来确定。
其次是活塞面积的确定,活塞面积可以通过液压缸的几何参数来计算,例如活塞直径和活塞杆直径等。
最后,根据出力计算公式即可得到液压缸的出力。
液压缸的出力计算对于液压系统设计和工程实施具有重要意义。
根据液压缸的出力计算结果,可以选择合适的液压缸型号和规格,确保液压系统能够满足工作需求。
同时,出力计算还可以用于评估液压缸的性能和可靠性,为系统的设计和优化提供依据。
在实际工程中,液压缸的出力计算需要综合考虑多个因素,例如液压缸的摩擦损失、密封件的摩擦力、液体的黏性等。
这些因素都会对液压缸的出力产生影响,需要在计算中予以考虑。
此外,液压缸的出力还受到系统压力损失和液体温度变化等因素的影响,这些因素也需要在实际计算中进行修正。
液压缸的出力计算是液压系统设计中的重要环节,它涉及到工作压力、活塞面积和力的计算等多个因素。
通过合理计算液压缸的出力,可以确保液压系统能够满足工作需求,并评估液压缸的性能和可靠性。
液压设计计算知识(2)
液压设计计算知识(2)9.液压缸缸筒设计项目计算公式说明缸筒内径当液压缸的理论作用力F(包括推力F1、拉力F2)及供油压力P为已知时则无活塞杆侧的缸筒内径:D=√(4F1/πP)·10-3(m)有活塞杆侧为:D =√[(4F2/πP·106)+d2](m)液压缸的理论作用力F按下式计算:F =F0/ψηt (N)当Q v及υ为已知时,则缸筒的内径D(未考虑容积效率ηv)按无活塞杆侧为:D =√(4Q v/πυ1)(m)按有活塞杆侧为:D =√[(4Q v/πυ2)+d2](m)最后将选择所求值的最大者,圆整到标准值。
d—活塞杆直径(m)P—供油压力(MPa)F0—活塞杆上和实际作用力(N)ψ—负载率一般取ψ=0.5~0.7ηt —液压缸的总效率υ1υ2—活塞杆伸出缩回速度 (m/min)Q v—液压缸的体积供油量(假定两侧供油量相同则Q v1=Q v2)(m3/s)缸筒壁厚缸筒壁厚为:δ= δ0+c1+c2关于δ0的值,可按下列情况分别进行计算当δ/D的比值小于等于0.08时,可用薄壁缸筒的实用计算式:δ0>P m a x D/2σP(m)当δ/D的比值等于0.08~0.3时,可用实用公式:δ0≥P m a x D/(2.3σP-3P m a x) (m)当δ/D的比值大于等于0.3时,可用实用公式:δ0≥D/2·√{[(σP+0.4P m a x)/(σP-3P m a x)]-1} (m)δ0≥D/2·√{[σP/(σP-√3P m a x)]-1} (m)δ0—为缸筒材料强度要求的最小值(m)c1—缸筒外径公差余量(m)c2—腐蚀余量(m)P m a x—缸筒内最高工作压力(MPa)σP—缸筒材料的许用应力(MPa)σP=σb/nσb—缸筒材料的抗拉强度(MPa)n—安全系数通常取5;最好按下表选取:材料名称静载荷交变载荷冲击载荷不对称对称钢锻铁3 5 8 12缸筒壁厚验算对最终采用的缸筒壁厚应作四方面的验算:①额定工作压力P n应低于一定极限值,以保证工作安全:P n≤0.35σs(D12-D2)/D12 (MPa)②同时额定工作压力也应与完全塑性变形压力有一定的比例范围,以免发生塑性变形:P n≤(0.35~0.42)P rL③验算缸筒径变形ΔD应处在允许范围内:ΔD=(DP r/E)·[(D12+D2)/(D12-D2)+γ](m)④缸筒的爆裂压力:P r=2.3σb/lg(D1/D) (MPa)P r L—缸筒发生完全塑性变形的压力(MPa)P r L≤2.3σb/lg(D1/D)σs—缸筒材料的屈服强度(MPa)P r—缸筒耐压试验压力(MPa)P m a x—缸筒内最高工作压力(MPa)E—液筒材料的弹性模数(MPa)γ—缸筒材料的泊松比,对钢材γ= 0.3缸底厚度缸筒底部为平面时,其厚度δ1可按照四周嵌住的圆盘强度公式进行近似的计算:δ1=0.433D2√(P/σp) (m)缸筒底部为拱形时[底部拱形圆大弧圆R≥0.8D,筒与底的圆角r≥(1/8)D]其厚度用下式计算:δ1=PD0β/(4σp) (m)δ1—缸底厚(m)D0—缸底外径 (m)P—缸内最大工作压力(MPa)σp—缸底材料许用应力(MPa)D2—计算厚度外径(m)β—系数当拱形高与D0之比为0.2~0.3时,取β=1.6~2.5缸头法兰厚度h=√4F b/[π(r a-d L)σp]×10-3 (m)如不考虑螺孔(d L),则为:h=√4F b/(πr aσp)×10-3 (m)F—法兰在缸筒最大内压下所承受的轴向压力 (N)r a—法兰外圆半径(m)b—螺孔中心到缸筒外径距离(m)d L—螺孔孔径(m)缸筒螺纹连接缸筒与端部用螺纹连接时,缸筒螺纹的强度计算如下:螺纹处的拉应力:σ=4KF10-6/π(d12-D2) (N/mm2)螺纹处的剪应力:τ=K1KF d010-6/0.2(d13-D3) (N/mm2)合成应力:σn=√(σ3+τ3)≤σp许用应力:σp=σs/n0(σs缸筒材料的屈服极限N/mm2)(n0安全系数,取1.2~2.5)F—缸筒端部承受的最大推力(N)D—缸筒内径(m)d0—螺纹外径(m)d1—螺纹底径(m)K—拧紧螺纹的系数,不变载荷取1.25~1.5,变载荷取2.5~4K1—螺纹连接的摩擦因数,K1=0.07~0.2平均值取K1=0.12Z—螺栓拉杆的数量缸法兰螺栓缸筒与端部用法兰或拉杆连接时,螺栓或拉杆的强度计算如下:螺纹处的拉应力:σ=4KF10-6/πd12Z (MPa)螺纹处的剪应力:τ=K1KF d010-6/0.2d13Z (MPa)合成应力:σn=√(σ3+τ3)≈1.3σ≤σp缸筒与端部焊接缸筒与端部用焊接连接时,其焊缝应力计算如下:σ=4F10-6/π(D12-d12)η≤σb/n(MPa)F—缸筒端部承受的最大推力(N)D1—缸筒外径(m)d1—螺焊缝底径(m)η—焊接效率,取η=0.7σb—焊条材料的抗拉强度(MPa)n—安全系数,参照缸筒壁的系数选取10.活塞的设计结构根据活塞密封装置形式来选用活塞结构形式(密封装置则按工作条件选定)通常分为整体活塞和组合活塞两类,前者是在活塞圆周上开沟槽,结构简单,但安装密封圈时容易拉伤和扭伤。
液压缸设计计算
总体计算第一部分压力1、油液作用在单位面积上的压强F?P PaA式中:N F——作用在活塞上的载荷,2m——活塞的有效工作面积,A从上式可知,压力值的建立是载荷的存在而产生的。
在同一个活塞的有效工作面积上,油液克服载荷所需要的压力就越大。
换句话说,如果活塞的有效工作面积一定,载荷越大,压力越大,活塞产生的作用力就越大。
是指液压缸能用以长期工作的压力。
额定压力(公称压力) PN,P,也是动态实验压力,是液压缸在瞬间所能承受的极限压力。
通最高允许压力max P5?1.P常规定为:。
MPa max P即在此压力下不出现变形、耐压实验压力是检验液压缸质量时需承受的实验压力,,r PN51.?P。
MPa 裂缝或破裂。
通常规定为:r。
液压缸压力等级见表1MPa单位液压缸压力等级表1~8 >8~16 >2.5 >2.516~32 >32 0压力范围~超高压低压中高压中压高压别级2、流量单位时间内油液通过缸筒有效截面的体积:V?Q L/mint?3?10At??V23??10D?Q?A?则由于 L/minL 4对于单活塞杆液压缸:?23?10Q??D当活塞杆伸出时4?223?10)?d(?QD?当活塞杆缩回时4式中:;L——液压缸活塞一次行程中所消耗的油液体积,V.min;t——液压缸活塞一次行程所需的时间,;mD——液压缸缸径,;d——活塞杆直径,m 。
——活塞运动速度,m/min?速比3、液压缸活塞往复运动时的速度之比:2vD2???22vd?D1式中:;——活塞杆的伸出速度,m/min v1;——活塞杆的缩回速度,m/min v2;——液压缸缸径,mD 。
——活塞杆直径,md以计算速比主要是为了确定活塞杆的直径和是否设置缓冲装置。
速比不宜过大或过小,免产生过大的背压或造成因活塞杆太细导致稳定性不好。
液压缸的理论推力和拉力4、?66210p?DAp?10??F N活塞杆伸出时的理推力:114?662210d10??)(Dp???Fp F N活塞杆缩回时的理论拉力:224式中:2m;——活塞无杆腔有效面积,A12m;——活塞有杆腔有效面积,A2;——工作压力,PMPa ;D——液压缸缸径,m 。
液压机油缸设计计算公式
液压机油缸设计计算公式
1.计算油缸内径
油缸内径的计算一般可以根据工作压力、输出力和油液作用面积来确定。
常用的计算公式如下:
S=F/P
其中,S为油液作用面积,F为输出力,P为工作压力。
2.计算油缸工作压力
油缸的工作压力可以根据系统所需的输出力和油缸的有效面积来计算。
常用的计算公式如下:
P=F/S
其中,P为工作压力,F为输出力,S为油缸的有效面积。
3.计算油缸的输出力
油缸的输出力可以根据工作压力和油缸的有效面积来计算。
常用的计
算公式如下:
F=P*S
其中,F为输出力,P为工作压力,S为油缸的有效面积。
4.计算油缸的速度
油缸的速度可以根据流量和油缸的有效截面积来计算。
常用的计算公
式如下:
Q=A*V
其中,Q为流量,A为油缸的有效截面积,V为油缸的速度。
除了以上的计算公式外,液压机油缸的设计还需要考虑油缸的结构形式、工作环境、密封性能、轴向稳定性等因素,这些因素会直接影响油缸的性能和使用寿命。
因此,设计液压机油缸时需要综合考虑以上因素,并根据具体的应用要求进行合理的选择和优化。
综上所述,液压机油缸设计计算公式是制定液压机油缸尺寸和参数的重要依据,通过合理的计算和选择,可以确保液压机油缸的性能和使用寿命,从而实现液压系统的稳定运行和高效工作。