煤制尿素工艺技术方案
煤化工装置尿素生产过程节能降耗的分析

煤化工装置尿素生产过程节能降耗的分析随着社会的发展和经济的快速增长,对能源的需求日益增加。
在这种情况下,能源的节约和高效利用成为了人们关注的焦点。
煤化工装置尿素生产过程是一个消耗能源较大的过程,因此在节能降耗方面具有一定的挑战性。
本文将从几个方面进行分析,探讨煤化工装置尿素生产过程节能降耗的技术途径及其可行性。
我们来分析目前煤化工装置尿素生产过程中存在的能源消耗情况。
煤化工装置尿素生产过程主要包括合成氨、尿素合成和尿素颗粒化三个步骤。
合成氨过程中主要能源消耗体现在天然气的蒸汽重整制氢和氮气的制氮,尿素合成过程中主要能源消耗体现在合成氨和二氧化碳的消耗,尿素颗粒化过程中主要能源消耗体现在旋流器和离心机耗能。
煤化工装置尿素生产过程中的能源消耗主要集中在原料气的消耗和设备耗能上。
针对煤化工装置尿素生产过程中存在的能源消耗情况,我们可以从以下几个方面来探讨节能降耗的技术途径。
可以通过优化合成氨工艺来降低原料气的消耗。
采用先进的蒸汽重整技术和新型的氮气制备技术,可以提高合成氨过程的能源利用效率,降低原料气的消耗。
可以通过改进尿素合成工艺来降低合成氨和二氧化碳的消耗。
采用高效的催化剂和优化的反应条件,可以提高尿素合成过程的能源利用效率,降低合成氨和二氧化碳的消耗。
可以通过更新和优化尿素颗粒化设备来降低能耗。
采用新型的旋流器和离心机,可以提高尿素颗粒化过程的能源利用效率,降低设备耗能。
在探讨节能降耗的技术途径之后,我们可以分析一下这些技术途径的可行性。
从技术上来看,这些技术途径已经在一些煤化工装置尿素生产过程中得到了应用,并取得了良好的效果。
一些尿素生产企业采用了先进的合成氨工艺和尿素合成工艺,实现了原料气的节约和能耗的降低。
从经济上来看,这些技术途径的投资成本较高,但是在长期运行中可以获得较好的经济效益。
通过技术改造和设备更新,可以降低能源消耗,提高产品质量,降低生产成本,从而增强企业的竞争力。
煤化工装置尿素生产过程节能降耗的技术途径主要包括优化合成氨工艺、改进尿素合成工艺和更新尿素颗粒化设备。
化肥厂生产过程及工艺流程
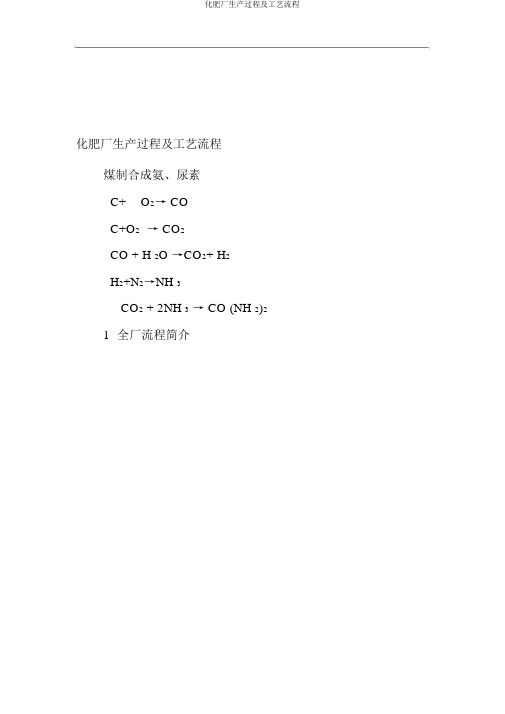
化肥厂生产过程及工艺流程化肥厂生产过程及工艺流程煤制合成氨、尿素C+ O2→ COC+O2→ CO2CO + H 2O →CO2+ H2H2+N2→NH 3CO2 + 2NH 3→ CO (NH 2)21全厂流程简介化肥厂生产过程及工艺流程煤蒸汽供热站蒸气空气N 2N2空分硫回收S煤低温液氮洗煤气化合成压缩备煤变换甲醇洗氨尿素合成CO2煤制合成氨、尿素流程简图尿素2过程工艺描绘(1)水煤浆气化制合成气装置由水煤浆制备工序来的水煤浆送入煤浆槽储藏待用。
浓度约为 63%的水煤浆经过煤浆给料泵加压输送到气化炉顶部工艺烧嘴,并与空分装置来的纯氧分别进入气化炉在 (G),约 1400℃工艺条件下,水煤浆与纯氧进行部分氧化反响,生成粗合成气。
反响后的粗合成气和溶渣进入气化炉下部的激冷室。
在激冷室中,粗合成气经冷却、清洗,将粗合成气中的大多数碳黑洗去,并和粗渣分开。
出激冷室的粗合成气直接进入文丘里清洗器和碳洗塔进一步清洗,除掉粗合成气中残留的碳黑,而后将水蒸汽/干气比约~的合成气送至变换工序。
溶渣被激冷室底部经过破渣机进入锁斗,按期排入渣池,渣池设有捞渣机将粗渣捞出,装车运往园区免烧砖项目。
渣池中含细渣的灰水经过渣池泵送至真空闪蒸器。
碳洗塔的液位经过控制进入塔内的灰水量来保持,碳洗塔内的黑水分两股排出,一股黑水去高压闪蒸器;另一股由灰水循环泵送至气化炉也进入高压闪蒸器,黑水经减压,闪蒸出黑水中溶解的气体并经过变换冷凝液加热器回收闪蒸汽的热量,经过高压闪蒸分别器,闪蒸出的气体至变换或火炬,水送入脱氧水槽。
(2)净化妆置a.变换变换工序主要反响式为:COS+H2O—— CO2+H2S+QCO+H2O—— CO2+H2+Q由气化送来粗煤气经煤气水分别器分别掉少许的冷凝液及尘埃后,经中温换热器温度高升至 250℃,进第一中温变换炉。
第一中温变换炉分上、下两段,炉内装有两段三层耐硫变换触媒,层间配有煤气激冷管线调温,出第一中温变换炉变换气CO 含量为 24% (干),温度为 420℃左右。
煤制尿素

汽提法
﹛
2.二氧化碳汽提法 3.氨汽提法
生产工艺: • 氨和二氧化碳在合成塔内,一次反应只有 55%~72%转化为尿素(以CO2计),从合成 塔出来的物料是含有氨和甲铵的尿素溶液。 在进行尿素溶液后加工之前,必须将氨和 甲铵分离出去。甲铵分解成氨和二氧化碳 是尿素合成反应中式(1)的逆反应,是强吸热 反应,用加热、减压和气提等手段能促进 这个反应的进行。围绕着如何回收处理从 合成塔里出来的反应混合物料,发展了尿 素的多种生产工艺。
氨的合成
• 合成反应的压力高、低各有利弊:压力高, 压缩功高,但有利于反应平衡,设备相对 小;压力低,压缩功相对低,设备相对大。 本工程按31.4MPa氨合成设计,并设后置 式废热锅炉热回收系统。具有塔阻力小, 氨净值高,使用寿命长,操作简单稳定、 投资少的特点。 • return
甲醇精馏(略)
改良ADA法
• 优点:溶液性能稳 定, • 优点:技术经济指 标较好, • 优点:溶液无毒, • 优点:对碳钢无腐 蚀作用 • 缺点:易堵塔,即 脱硫塔内单质硫易 沉降在填料或设备 上
栲胶法
• 原料易得,脱硫液无毒,活性好,脱硫性 能稳定, • 脱硫效率及气体净化度较高,不堵塔, • 并可用自吸入空气喷射氧化使溶液再生, 具有投资省、效果好、操作方便。 • 在气柜后、压缩机一段入口前采用栲胶脱 硫。
一、合成氨
主线:造气→脱硫 →变换 →脱硫 →脱碳→精脱硫→合成氨→ 合成 尿素 支线:甲醇 →精甲醇 氢氨回收
ቤተ መጻሕፍቲ ባይዱ 造气
• 本工程以无烟煤为原料,,选用空气常压固定床间歇气化 法,并采用成熟的自动加焦及炉况寻优技术来生产合成氨。 自动加焦技术利用机电控制使原料煤通过自动加焦机均匀 地进人造气炉中,由此达到稳定炉温、提高制气时间、减 少煤耗的目的;炉况寻优即随时监视炉内操作情况,并优 化调节的技术。这两项新技术的运用,可使造气炉的产气 量在原料消耗及设备不变的情况下,提高15%。同时,再 使用“过热蒸汽制气”、“入炉蒸汽流量自动调节”、 “人炉蒸汽压力微机控制”、“余热集中回收”等有效的 节能降耗措施,提高单炉产气量,降低生产成本,使生产 运行平稳,安全可靠。
年产20万吨尿素生产工艺设计
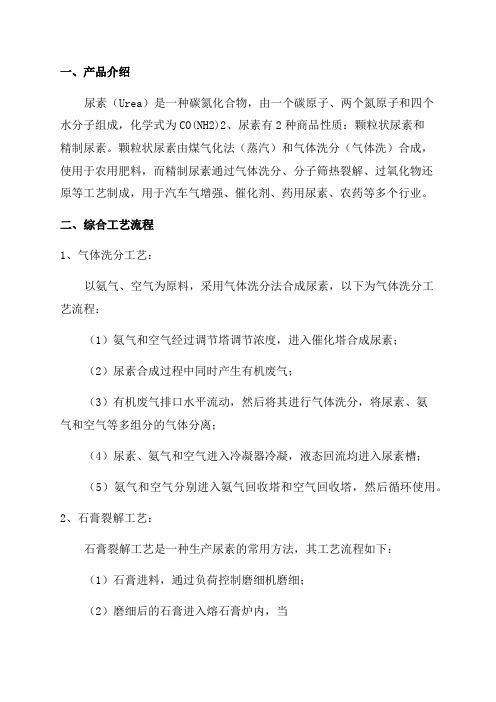
一、产品介绍
尿素(Urea)是一种碳氮化合物,由一个碳原子、两个氮原子和四个
水分子组成,化学式为CO(NH2)2、尿素有2种商品性质:颗粒状尿素和
精制尿素。
颗粒状尿素由煤气化法(蒸汽)和气体洗分(气体洗)合成,
使用于农用肥料,而精制尿素通过气体洗分、分子筛热裂解、过氧化物还
原等工艺制成,用于汽车气增强、催化剂、药用尿素、农药等多个行业。
二、综合工艺流程
1、气体洗分工艺:
以氨气、空气为原料,采用气体洗分法合成尿素,以下为气体洗分工
艺流程:
(1)氨气和空气经过调节塔调节浓度,进入催化塔合成尿素;
(2)尿素合成过程中同时产生有机废气;
(3)有机废气排口水平流动,然后将其进行气体洗分,将尿素、氨
气和空气等多组分的气体分离;
(4)尿素、氨气和空气进入冷凝器冷凝,液态回流均进入尿素槽;
(5)氨气和空气分别进入氨气回收塔和空气回收塔,然后循环使用。
2、石膏裂解工艺:
石膏裂解工艺是一种生产尿素的常用方法,其工艺流程如下:
(1)石膏进料,通过负荷控制磨细机磨细;
(2)磨细后的石膏进入熔石膏炉内,当。
褐煤生产尿素工艺流程

褐煤生产尿素工艺流程褐煤生产尿素的工艺流程一般包括以下几个步骤:褐煤破碎、褐煤浸出、氨合成、尿素合成和尿素精制。
首先,褐煤破碎。
将原料褐煤经过破碎设备进行破碎,使其变为适合后续处理的颗粒状物料。
破碎后的褐煤颗粒大小一般为几毫米到几厘米不等。
接着,褐煤浸出。
将破碎后的褐煤与溶剂进行接触,使其中的有机质溶解到溶剂中,形成褐煤提取浆料。
溶剂一般为脱去硫醇的煤油或石油醚。
褐煤提取浆料经过分离设备分离出溶解在溶剂中的有机质,得到褐煤提取液。
然后,氨合成。
将褐煤提取液与氨气在合成反应器中进行反应,得到氨基氨甲酸褐煤。
首先,将褐煤提取液混合物加入反应器中,然后逐渐加入氨气并加热,反应温度一般在130℃-160℃之间。
经过一系列的化学反应,褐煤提取液中的有机质与氨气反应生成氨基氨甲酸褐煤。
接下来,尿素合成。
将氨基氨甲酸褐煤与二氧化碳在尿素合成反应器中进行反应,得到尿素。
首先,将氨基氨甲酸褐煤与二氧化碳以一定的比例混合后加入反应器中,然后加热至高温(一般为150℃-180℃),持续一段时间进行反应。
在高温下,氨基氨甲酸褐煤与二氧化碳发生缩合反应,生成尿素。
最后,尿素精制。
将合成得到的尿素溶液经过蒸发、冷却、结晶等工艺步骤进行精制处理,得到纯净的尿素。
首先,将尿素溶液进行蒸发,除去其中的水分,使其浓缩。
然后,在一定的温度下进行冷却,促使尿素结晶。
最后,通过过滤等操作将尿素晶体分离出来,得到纯净的尿素产品。
综上所述,褐煤生产尿素的工艺流程主要包括褐煤破碎、褐煤浸出、氨合成、尿素合成和尿素精制等步骤。
这个工艺流程能够将褐煤转化为高附加值的化肥产品,实现资源的有效利用和循环利用,具有较高的经济效益和环境效益。
煤制尼龙6生产工艺流程

煤制尼龙6生产工艺流程
煤制尿素是一种重要的煤化工工艺,主要步骤如下:
1. 煤气化: 将煤在高温高压下气化,生成一氧化碳和氢气的混合气体。
2. 转化反应: 通过催化剂作用,将一氧化碳与水蒸汽进行转化反应,生成氢气和二氧化碳。
3. 二氧化碳除去: 用溶液将产物气中的二氧化碳吸收掉,留下富氢气体。
4. 氨合成: 以富氢气为原料,通过氨合成反应生产氨。
5. 尿素合成: 将氨与二氧化碳在高温高压下合成尿素。
6. 尿素浓缩: 采用真空蒸发或结晶等方法浓缩尿素溶液。
7. 尿素粉体化: 将浓缩的尿素溶液通过喷雾干燥或压滤等方式制备尿素粉体产品。
尿素是重要的基本化工原料,可以用于生产尼龙6树脂、医药中间体、肥料等产品。
尼龙6树脂是通过尿素与己內酰胺开环缩合聚合而制得。
国内尿素合成工艺研究

科技专论国内尿素合成工艺研究山西潞安煤基合成油有限公司(山西长治) 崔保命【摘 要】介绍了用于尿素合成的水溶液全循环法、二氧化碳汽提法、氨汽提法的工艺及其流程特点、适用范围,并从几方面对其进行了比较与分析。
【关键词】尿素合成;工艺水溶液全循环法;二氧化碳汽提法;氨汽提法;比较分析尿素是固体氮肥中含氮量最高的肥料,其发展速度已超过了其他氮肥品种。
我国尿素装置主要有水溶液全循环法、二氧化碳汽提法和氨汽提法三种生产工艺。
本文在此简要进行分析。
一、三种尿素合成工艺技术及优缺点1.水溶液全循环法1.1水溶液全循环法工艺特点及优缺点该法合成塔操作压力19.6MPa,温度188℃,NH 3/CO 2分子比为4.0,CO 2转化率约64%。
出合成塔溶液经中、低压分解,二段蒸发造粒得尿素产品。
由于中压分解压力低,分解气的热量除在一段蒸发加热器下段回收少部分冷凝热外,其余大部分热量由于冷凝温度低,只有用冷却水移走。
因此该法蒸汽消耗高,每吨尿素耗蒸汽约1.7吨。
该法无高压分解回收流程,为此高压设备少,投资费用低,但公用工程总体水平消耗较高,且装置规模较小。
近年来,国内的中、小尿素装置进行了一系列技改,从降低蒸汽消耗方面做了大量努力,取得了一定的效果,使蒸汽消耗有所下降。
2. 二氧化碳汽提法2.1二氧化碳汽提法的工艺特点及优缺点二氧化碳汽提法的特点是在最佳氨碳比的条件下,使合成压力降到最低。
同时,在合成压力下进行CO 2汽提和冷凝,产生的冷凝热可副产蒸汽作为蒸汽喷射器的动力蒸汽及系统保温。
2.2二氧化碳汽提法工艺优缺点汽提法工艺的出现,突破了传统水溶液全循环法的未反应物回收方式,使尿素生产的辅助能耗大幅度降低。
二氧化碳汽提法克服了传统水溶液全循环工艺的一些缺点,同时减少了设备,简化了流程。
另外,池式冷凝器与传统的降膜式冷凝器比较,合成塔容积减少了40%;因而减少了尿素装置框架的高度;同时增大了传热系数及传热温差,减少了传热面积;增大了操作弹性。
煤制尿素工艺流程
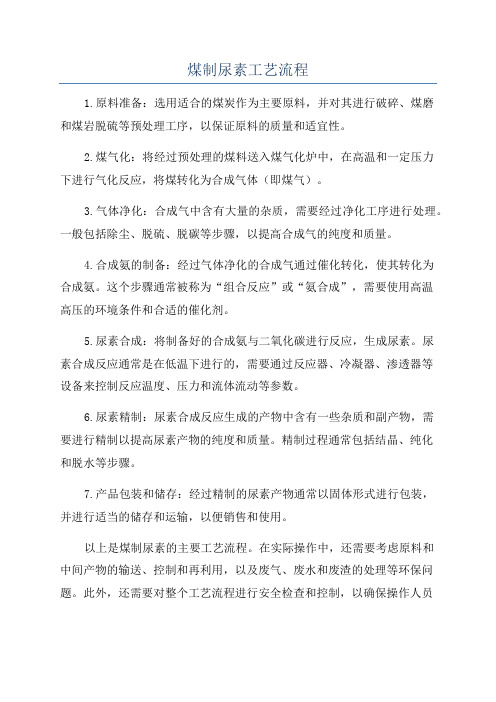
煤制尿素工艺流程
1.原料准备:选用适合的煤炭作为主要原料,并对其进行破碎、煤磨
和煤岩脱硫等预处理工序,以保证原料的质量和适宜性。
2.煤气化:将经过预处理的煤料送入煤气化炉中,在高温和一定压力
下进行气化反应,将煤转化为合成气体(即煤气)。
3.气体净化:合成气中含有大量的杂质,需要经过净化工序进行处理。
一般包括除尘、脱硫、脱碳等步骤,以提高合成气的纯度和质量。
4.合成氨的制备:经过气体净化的合成气通过催化转化,使其转化为
合成氨。
这个步骤通常被称为“组合反应”或“氨合成”,需要使用高温
高压的环境条件和合适的催化剂。
5.尿素合成:将制备好的合成氨与二氧化碳进行反应,生成尿素。
尿
素合成反应通常是在低温下进行的,需要通过反应器、冷凝器、渗透器等
设备来控制反应温度、压力和流体流动等参数。
6.尿素精制:尿素合成反应生成的产物中含有一些杂质和副产物,需
要进行精制以提高尿素产物的纯度和质量。
精制过程通常包括结晶、纯化
和脱水等步骤。
7.产品包装和储存:经过精制的尿素产物通常以固体形式进行包装,
并进行适当的储存和运输,以便销售和使用。
以上是煤制尿素的主要工艺流程。
在实际操作中,还需要考虑原料和
中间产物的输送、控制和再利用,以及废气、废水和废渣的处理等环保问题。
此外,还需要对整个工艺流程进行安全检查和控制,以确保操作人员
及设备的安全。
煤制尿素工艺的技术和经济指标也是关键的研究和改进对象,涉及到原料利用率、能耗、产品质量和成本等方面的考虑。
- 1、下载文档前请自行甄别文档内容的完整性,平台不提供额外的编辑、内容补充、找答案等附加服务。
- 2、"仅部分预览"的文档,不可在线预览部分如存在完整性等问题,可反馈申请退款(可完整预览的文档不适用该条件!)。
- 3、如文档侵犯您的权益,请联系客服反馈,我们会尽快为您处理(人工客服工作时间:9:00-18:30)。
煤制尿素工艺技术目前,世界上最具有竞争性的尿素合成工艺是荷兰Stamicarbon公司的CO2汽提工艺、意大利Snamprogetti公司的NH3汽提工艺和日本东洋公司的ACES工艺。
它们在世界上建厂数量为:CO2汽提工艺115套,氨汽提工艺80套,ACES工艺9套。
1980以后建厂的工艺以氨汽提工艺居多。
近年来,CO2汽提工艺有很大的发展,Stamicarbon与Sandvik公司合作,推出了一种耐腐蚀性能更优异的专门双相钢材料——Safurex (Stamicarbon A4-18005型BE.06),该材料可以在无氧情况下,能耐高温甲铵液的腐蚀,在中国宁夏用新的CO2汽提工艺成功的改造了NH3汽提工艺,使装置增产50%。
(一)国外尿素技术工艺概况1、CO2汽提工艺该工艺由荷兰Stamicarbon公司于1964年开始中间试验,1967年建成第一套工业装置。
该工艺在70年代初期发展迅速,目前己在世界范围内承建200多套尿素装置,总能力大约为50 Mt/a,占世界尿素总能力的45%,设计能力范围在70~3250t/d。
我国也己有18套大型装置在运行,最大的单系列是中海油富岛化学有限公司的2700t/d。
该工艺包括原料压缩、尿素合成及未反应物的高压分解和回收、未反应物的低压分解和回收、尿液浓缩与造粒、工艺冷凝液处理等工序。
该工艺用CO2作汽提剂,在与合成等压条件下将合成塔出料在汽提塔内加热汽提,使未转化的大部分甲铵分解成CO2和NH3蒸出,分解及汽化所需的热量由2.45MPa蒸汽供给。
汽提塔出汽在高压冷凝器内生成甲铵冷凝液,冷凝反应所放出的热量副产低压蒸汽,供低压分解、尿液蒸发使用,汽提塔出液减压后进入精馏塔,将残余甲铵和氨进一步加热分解并蒸出,然后经真空闪蒸,两段真空蒸发浓缩至99.7%的尿液送造粒塔造粒,或者直接用一段蒸发的96%尿液去生产大颗粒尿素。
2、NH3汽提工艺NH3汽提工艺由意大利Snamprogetti公司于1967年试验成功并获得专利。
1970年第一套工业装置建成。
最近5年来,世界新增尿素能力70%采用Snamprogetti技术。
80年代,我国也引进了大中型氨汽提法尿素生产装置。
该工艺基本与二氧化碳汽提法一样。
只是提高了合成塔的NH3/CO2摩尔比,使进入汽提塔的合成液中游离氨量增大,以达到自汽提效果。
该工艺包括原料压缩、尿素合成及未反应物的高压分解和回收、过剩氨经冷凝成液氨返回系统、尿液浓缩与造粒、工艺冷凝液处理等工序。
该工艺在与合成等压条件下将合成塔出料在汽提塔内加热自汽提,使未转化的大部分甲铵分解成CO2和NH3蒸出,分解及汽化所需的热量由2.45MPa蒸汽供给。
汽提塔出汽在高压冷凝器内生成甲铵冷凝液,冷凝反应所放出的热量副产低压蒸汽,供低压分解、尿液蒸发使用,汽提塔出液减压后进入中、低压分解系统,将残余甲铵和氨进一步加热分解并蒸出,然后经真空闪蒸,两段真空蒸发浓缩至99.7%的尿液送造粒塔造粒,或者直接用一段蒸发的96%尿液去生产大颗粒尿素。
中压分解气体去冷凝吸收,将过剩氨分离出来返回合成系统。
3、ACES工艺ACES工艺是日本东洋工程公司(TEC )开发的节能节资型尿素生产新工艺。
它是将CO2汽提工艺的高汽提效率与全循环工艺的高单程转化率有机结合起来的一种新工艺。
合成塔内氨/碳比高达4.0,可基本上忽略腐蚀问题,在190℃与17.1 MPa的操作条件下,合成转化率达到68%,大大减少了汽提塔用于分解和分离未反应物所需的中压蒸汽量,使其成为当今工业化尿素工艺中能耗最低的工艺。
其设备选材也有独到之处,主要高、中压设备都采用TEC参与开发的双相不锈钢(DP-3),能很好的解决设备的腐蚀问题。
其缺点是高压圈内设备台数较多,操作、控制比较复杂,高压圈内物料循环靠设备的位差来实现,工艺框架较高,增加了一次性土建费用,设备的操作、维修也不方便。
90年代我国先后引进了2套ACES装置。
该工艺包括原料压缩、尿素合成及未反应物的高压分解和回收、未反应物的中、低压分解和回收、尿液浓缩与造粒、工艺冷凝液处理等工序。
该工艺用CO2作汽提剂,在与合成等压条件下将合成塔出料在汽提塔内加热汽提,使未转化的大部分甲铵分解成CO2和NH3蒸出,分解及汽化所需的热量由2.45MPa蒸汽供给。
汽提塔出汽在高压冷凝器内生成甲铵冷凝液,冷凝反应所放出的热量一部分副产低压蒸汽,供低压分解、尿液蒸发使用,一部分用于加热汽提后的尿液,汽提塔出液减压后进入中、低压分解系统,将残余甲铵和氨进一步加热分解并蒸出,然后经真空闪蒸,两段真空蒸发浓缩至99.7%的尿液送造粒塔造粒,或者直接用一段蒸发的96%尿液去生产大颗粒尿素。
该工艺无过剩氨回收系统。
除上述三种尿素工艺外,世界上典型的尿素工艺还有意大利蒙特爱迪生公司的等压双汽提工艺(简称IDR法)、美国UTI的热循环工艺以及瑞士卡萨利(Casale)公司的HEC尿素技术。
它们都比较适合现有尿素装置的技术改造。
(二)国内尿素工艺技术概况我国尿素工业的发展始于1957年,在上海化工研究院(以下简称上海院)氮肥室进行尿素生产的理论研究和试验工作。
1958年在南京永利宁厂筹建我国第一套半循环工艺的中试装置(年产3000t),每生产1t尿素排放的尾汽氨量为650 kg左右,1965年2月在中试装置上完成了高效半循环的试验,但每生产1t尿素尚有尾汽氨量约176 kg。
同年12月上海院在日产2t的实验装置上完成了水溶液全循环的工艺研究和试验工作,为我国自行设计水溶液全循环工艺尿素装置提供了详细充实的技术数据。
1967年上海院在试验装置上采用变换汽汽提制取尿素工艺取得成功,开创了我国中压联尿的新工艺,并由国内设计院完成工程设计及施工图。
1974年和1975年分别在延安东风化肥厂、天津永红化肥厂、江苏六合化肥厂建成年产1万t的中压联尿装置并投入化工试车。
1960年我国引进前苏联的年产1万t的不循环法尿素装置在太原化肥厂投入生产。
1962年南京永利宁厂半循环装置通过国家鉴定,由国内设计的2套年产4万t的半循环装置先后在上海吴径化工厂和浙江巨州化工厂相继投产。
1966年我国引进荷兰Stamicarbon公司的2套8万t/a水溶液全循环工艺装置在沪州天然汽化工厂投产。
利用上海院水溶液全循环工艺技术数据并借鉴进口装置自行设计、设备自制的年产11万t尿素装置于1966年11月在石家庄化肥厂投入生产,标志着我国尿素工业发展进入一个新的阶段。
70年代初至80年代初,我国建成8-11万t/a的中型尿素装置35套。
同时我国又引进了荷兰Stamicarbon公司70年代先进工艺CO2汽提法大型尿素装置13套和日本三井东压公司的东洋高压全循环改良C法2套,每套年生产能力为50-52万吨。
80年代初化四院与荷兰凯洛格-大陆公司联合设计日产1740t的CO2汽提法尿素装置,设备大部分由国内自行制造,第一套装置于1984年9月在浙江镇海石化总厂投产成功,第二套装置于1986年在新疆乌鲁木齐石油化工厂投产,第三套装置于1988年7月在宁夏化工厂投产,表明我国己具有自行设计、制造大型尿素装置的能力,并赶上国外先进技术水平。
80年代末第一套52万吨/年NH3汽提引进装置在河南中原大化建成投产,90年代初引进的5套年产13万t氨汽提工艺的中型尿素装置先后在河北宣化、北京化工实验厂、河南洛阳、山西原平、陕西宝鸡建成投产。
90年代中期又引进意大利Snamprogetti公司的十几套大中型氨汽提工艺装置和一套日本TEC公司ACES法大型尿素装置,四川泸天化引进意大利IDR双汽提工艺改造原2套水溶液全循环工艺装置。
1986年我国尿素工业发展又掀起了一个新的阶段,即众多小氮肥厂改产尿素的技术改造,使小氮肥厂的技术进步和技术革新发生了质的变化。
相继有100多家小氮肥厂利用水溶液全循环法进行碳铵改尿素。
水溶液全循环工艺虽属60年代技术水平,但由于我国尿素工艺研究和工业生产发展过程中均以该工艺为主,因此积累了工艺设计、设备制造、操作技术和生产管理的丰富经验,为小氮肥厂改产尿素提供了丰富技术,使小尿素装置投产以后即能稳定运行。
小尿素装置发展迅速,是适合我国国情的,充分发挥了原小氮肥厂的优势。
我国现有小尿素装置159套,其中水溶液全循环工艺151套。
目前,部分小尿素装置的生产能力己达6-10万t/a,正向13-20万t/a中型装置发展。
中型装置目前有48套,其中水溶液全循环工艺39套,氨汽提工艺5套,CO2汽提工艺2套,IDR工艺2套。
中型装置尿素产量占全国尿素产量的17%。
随着大、小型尿素装置的兴建,中型装置的产量比例相对减少。
大型装置己建29套,其中氨汽提工艺8套,CO2汽提工艺18套,改良“C'法2套,ACES工艺1套,其生产能力占我国尿素总产量的40%。
以水溶液全循环工艺为主的中、小型装置有192套,占全国尿素装置总产量的81.7%,其生产的尿素量占全国尿素总产量的57%。
此外,CO2汽提工艺占27%,氨汽提工艺占13.5%,其它工艺占2.5%。
(三)工艺技术方案比较从国内外尿素技术进展来看,适合大型尿素装置建设的技术只有荷兰Stamicarbon公司的CO2汽提工艺、意大利Snamprogetti公司的NH3汽提工艺和日本东洋公司的ACES工艺。
它们也是在世界上建厂数最多的工艺,代表当今尿素技术的发展方向。
下面就上述三种工艺技术作一比较。
表1-16三种工艺的主要工艺指标的比较(来源于日产900吨尿素的报价)从上表可以看出,三种工艺的吨尿素消耗指标基本相同。
三种尿素的工艺特点如下:1、CO2汽提工艺(1)流程简单。
由于合成工段汽提效率很高,减小了下游工序的复杂程度。
Stamicarbon的CO2汽提工艺是目前唯一工业化的只有单一低压回收工序的尿素生产工艺。
因为流程简单,所以带来许多好处,如操作方便,投资省,可靠性强,运转率高,维修费用低等。
(2)高压圈工艺在优化理论指导下运行。
合成压力采用最低平衡压力、氨/碳比采用最低共沸组成时的氨/碳比(2.95)、操作压力为13.6 MPa、温度为180-183℃、冷凝温度为167℃、汽提温度约190℃、汽提效率为80%以上,这些参数都比较温和,因而采用316L或25-22-2CrNiMo材料即可达到材质耐强腐蚀性的要求,设备制造和维修都比较方便。
(3)电耗低。
因为CO2汽提工艺操作压力比其他汽提工艺都低,因而高压氨泵、高压甲铵泵的功耗也低。
另外,由于汽提效率高且没有中压回收工段,没有单独的液氨需要循环回收,甲铵液的循环量也少,因而进一步降低了循环氨、甲铵所必须的功耗。
(4)采用池式冷凝器。
采用池式高压甲铵冷凝器是Stamicarbon对其尿素工艺的最新改进。