垃圾发电炉膛温度计算模型说明
垃圾焚烧发电厂经济技术指标解释及计算公式
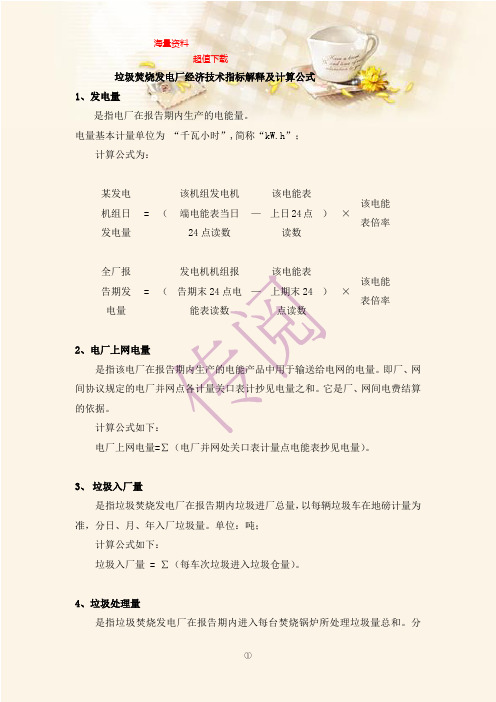
垃圾焚烧发电厂经济技术指标解释及计算公式1、发电量是指电厂在报告期内生产的电能量。
电量基本计量单位为“千瓦小时”,简称“kW.h”;计算公式为:某发电机组日发电量= (该机组发电机端电能表当日24点读数—该电能表上日24点读数)×该电能表倍率全厂报告期发电量= (发电机机组报告期末24点电能表读数—该电能表上期末24点读数)×该电能表倍率2、电厂上网电量是指该电厂在报告期内生产的电能产品中用于输送给电网的电量。
即厂、网间协议规定的电厂并网点各计量关口表计抄见电量之和。
它是厂、网间电费结算的依据。
计算公式如下:电厂上网电量=∑(电厂并网处关口表计量点电能表抄见电量)。
3、垃圾入厂量是指垃圾焚烧发电厂在报告期内垃圾进厂总量,以每辆垃圾车在地磅计量为准,分日、月、年入厂垃圾量。
单位:吨;计算公式如下:垃圾入厂量 = ∑(每车次垃圾进入垃圾仓量)。
4、垃圾处理量是指垃圾焚烧发电厂在报告期内进入每台焚烧锅炉所处理垃圾量总和。
分日、月、年入厂垃圾量,单位:吨;计算公式如下:垃圾处理量=∑(进入锅炉燃烧的垃圾量),以垃圾吊称重计量∑为准。
5、垃圾焚烧厂用电量是指垃圾焚烧发电厂在报告期内垃圾焚烧处理过程中所消耗的电量:专指从生活垃圾进厂计量开始到烟气达标排放,以及余热发电并网。
用以评价处理垃圾的直接电成本。
因不同厂的边界不一,为方便统一评价,不含原水取水用电、渗滤液处理厂用电、飞灰固化用电以及炉渣综合利用用电。
分班、日、月、年焚烧厂用电量。
单位:千瓦时、万千万时;计算公式如下:焚烧厂用电量=∑(所有厂用变电量总和+∑高压辅机电量)。
6、各子系统厂用电量(1)渗滤液处理厂用电量是指垃圾焚烧发电厂在报告期内处理渗滤液(指标达到国家排放标准)所消耗的电量。
单位:千瓦时;计算公式如下:渗滤液处理厂用电量=∑(渗滤液处理车间电量表读数差值×倍率)。
(2)飞灰固化厂用电量(同上)(3)炉渣综合利用厂用电量(同上)(4)取水厂用电量(同上)。
2s烟气DCS温度计算模型

300吨/天垃圾焚烧炉DCS温度计算模型
二〇一八年十二月
一、温度测点及炉膛结构图
(实际标高13670mm)
横截面S=17.34 m²
二、焚烧炉烟气量
省煤器漏风系数】【焚烧炉漏风系数】
Q N:烟囱进口烟气流量(m³N/h)
Q S:石灰浆流量(kg/h)(目前以常量1800kg/h计算)
查锅炉设计标准:焚烧炉本体(包括燃烧室)漏风系数0.05;
省煤器每级漏风系数0.02,共2级,漏风系数为0.04;
烟气净化系统及烟道漏风系数0.05。
三、烟气温度
T1 :第一层三个实测温度的平均值
T2 :第二层三个实测温度的平均值
T3 :第三层三个实测温度的平均值四、烟气流速
一通道内平均烟气温度(℃) :
一通道内平均烟气流速(m/s) :
五、烟气在一通道总停留时间(s)
六、烟气在≥850℃区间停留时间
烟气在850℃时所处的炉膛高度(m):
H850℃
烟气在≥850℃区间停留时间(s):
t850℃
七、烟气停留2s时DCS温度
烟气停留2S处高度H = 2 V (m)
采用插值法计算2S处DCS温度(℃)
T DCS
七、温度阶梯图
T0 H0 T1
T2 T3 H1 H2 H3 H T DCS
850℃H 850℃。
垃圾焚烧炉膛烟气温度计算模型的探讨——满足烟气850 ℃以上停留2 s 的监管要求

xy9: !"# '-fkzGq{'|}J
489:7 (m5+,~ ()* >?~ BCDE~ -f
;<=>?@,-&%
ABCDE@.
AFG?@/&&%0$!&1 !&!& &%2&&3$2&1
&'(@/&4/5$3/67489:;4<7=#>84!&!&4&%4&&5
&)%*+%%),- ,- ./0 123*+32.),- 4,503 ,6 73+0 82% 90:;0<2.+<0 )- =2%.0 (-*)-0<2.),- 7+<-2*0@400. ./0 >+;0<?)%),- @0A+)<0:0-.% ./2. ./0 73+0 82% >.2B% CD,?0 !"# 6,< E % !"# $%&'(&)* +&) ,-%.%)/0 1%&' $"23")4 *5 62%3%)7 8)92:;:%<2< 8)=%:').2)9 >:'"; ?'5 @9A5 62%3%)7 BCCCDE 05 62%3%)7 F-')7G2 H")(" 8)=%:').2)9&I J:'92K9%')
. LA2Kl-l)'I'R7(i?g'h5 @t9As5 6R2e%3%s)7er*vCeCCdD.C 45 M-&)7-&% !NM 8)=%:').2)9 ?'O @9A5 !-&)7-&% PC*QC4
垃圾焚烧发电炉排炉工艺设计参数计算方法
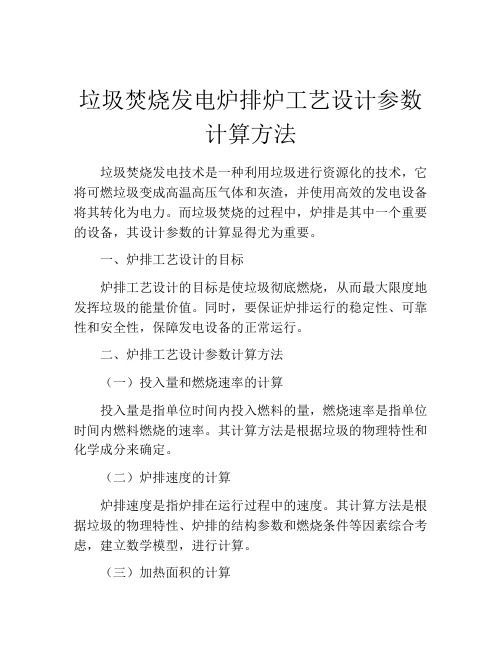
垃圾焚烧发电炉排炉工艺设计参数计算方法垃圾焚烧发电技术是一种利用垃圾进行资源化的技术,它将可燃垃圾变成高温高压气体和灰渣,并使用高效的发电设备将其转化为电力。
而垃圾焚烧的过程中,炉排是其中一个重要的设备,其设计参数的计算显得尤为重要。
一、炉排工艺设计的目标炉排工艺设计的目标是使垃圾彻底燃烧,从而最大限度地发挥垃圾的能量价值。
同时,要保证炉排运行的稳定性、可靠性和安全性,保障发电设备的正常运行。
二、炉排工艺设计参数计算方法(一)投入量和燃烧速率的计算投入量是指单位时间内投入燃料的量,燃烧速率是指单位时间内燃料燃烧的速率。
其计算方法是根据垃圾的物理特性和化学成分来确定。
(二)炉排速度的计算炉排速度是指炉排在运行过程中的速度。
其计算方法是根据垃圾的物理特性、炉排的结构参数和燃烧条件等因素综合考虑,建立数学模型,进行计算。
(三)加热面积的计算加热面积是指炉排运行过程中需要同时加热垃圾的表面积。
其计算方法是根据垃圾的物理特性,以及燃烧产物的热传递特性进行计算。
(四)气流分配的计算气流分配是指在炉排运行过程中,将所需的氧气和空气分配到适当的位置,以保证垃圾的充分燃烧和炉排的稳定运行。
其计算方法是根据炉排的结构参数和燃烧条件等因素进行计算。
(五)排渣量的计算排渣量是指单位时间内从炉排中排出的灰渣的量,其计算方法是根据垃圾的物理特性和燃烧条件等因素进行计算。
(六)氧化亚氮排放量的计算氧化亚氮排放量是指炉排运行过程中排放的氧化亚氮的量。
其计算方法是根据垃圾的物理特性和化学成分,以及燃烧产物的生成量和排放标准等因素进行计算。
三、炉排工艺设计参数的优化措施优化炉排工艺设计参数是提高垃圾焚烧发电技术效益的关键。
具体措施包括:(一)合理选择垃圾种类和粒度,以保证垃圾燃烧效果。
(二)设计合理的炉排结构和运行参数,以提高垃圾燃烧效率和发电效率。
(三)加强炉排内气流的调控,以保证垃圾的充分燃烧和炉排的稳定运行。
(四)控制炉排内的温度和压力,避免因过高的温度和压力而导致炉排故障。
生活垃圾焚烧发电厂设计参数与焚烧负荷变化的统计分析

生活垃圾焚烧发电厂设计参数与焚烧负荷变化的统计分析目录一、内容简述 (2)1.1 研究背景 (3)1.2 研究目的与意义 (4)1.3 研究内容与方法 (5)二、生活垃圾焚烧发电厂设计参数分析 (6)2.1 垃圾焚烧厂主要设计参数 (7)2.1.1 焚烧厂规模 (8)2.1.2 焚烧炉型选择 (9)2.1.3 烟气排放参数 (9)2.2 设计参数对焚烧效果的影响 (10)2.2.1 燃料种类与燃烧效率 (11)2.2.2 运行参数对燃烧过程的影响 (12)2.2.3 环境因素对焚烧效果的影响 (13)三、焚烧负荷变化对发电厂性能的影响 (14)3.1 焚烧负荷的定义与计算方法 (16)3.2 焚烧负荷变化对发电厂能效的影响 (17)3.3 焚烧负荷变化对烟气排放的影响 (18)3.4 焚烧负荷变化对垃圾热值利用的影响 (19)四、统计分析与模型建立 (20)4.1 统计分析方法的选择 (21)4.2 统计分析结果展示 (23)4.3 模型建立与验证 (24)4.4 模型在焚烧负荷变化中的应用 (26)五、结论与建议 (27)5.1 研究结论总结 (28)5.2 对焚烧发电厂设计的建议 (29)5.3 对焚烧负荷管理的建议 (30)一、内容简述随着城市化进程的加速,生活垃圾的产量逐年上升,焚烧发电作为一种高效、环保的处理方式,逐渐成为处理城市生活垃圾的重要手段。
本文旨在对生活垃圾焚烧发电厂的设计参数进行统计分析,并探讨焚烧负荷变化对其影响。
在设计阶段,焚烧发电厂的各项参数选择直接关系到其运营效率和经济效益。
通过对多个焚烧发电厂的实际运行数据进行分析,可以得出各参数间的相关性及对焚烧负荷的影响程度。
结合相关规范和标准,对焚烧厂的烟气排放、热能利用等关键指标进行设定,以确保焚烧发电厂的安全、稳定、高效运行。
焚烧负荷的变化受到多种因素的影响,包括垃圾成分、热值、气象条件等。
在运营过程中,通过调整焚烧参数,如氧气含量、燃烧温度、燃烧时间等,可以优化焚烧效果,提高垃圾的热能利用率。
化工废弃物焚烧炉炉排的设计计算

上部 高度 日: 算式 为 : 计
日 2 × ×r ( ㈩ )
q R
石
式中
B—— 焚烧 炉废 弃 物 的处理量 , g h k/ ; Q 处 理废 弃物 的低 位发 热量 ,J k ; k/ g
:
1
— —
6l
占 2
6 3
6 4
1
1 8 m , 见 炉 墙 7 W/ 可
… 。…
安 全 与 环 境 ,0 3 1 ( ) 1 . 2 0 ,6 5 :5
+ — — + — — + —— + — — + ——
o1 A1 A2 A3 A4 o2 / t
烧 。根 据层 燃 炉体 积 热 负 荷 q 的计 算 公 式 可
导 热 数
.
厚 度
mm
k ・ I -’ W ・m ~ ・ K 一 g l l
得 到炉膛 的体 积 = ̄ Q B
据 经 验 取 2 0 W/ 5k m 。
.et ,
a
-
00 q
2 2 3其 2. m ,
根 据废 弃物 的发 热量 和空 气过 剩 系
炉 内壁 和外 表 面 的对 流 换 热 系 数 , 别取 10 ( ・ 和 3 分 0 W/ I n K)
—
数 计算 得 到 ,
1 O 0 ̄ ; 0 C
6 m / g N k ;
5 W/(n K); . i ・
0 —— 下 部 炉 膛 出 口处 的烟 气 温 度 , = : 0
国家 环 境 保 护 总 局 规 划 与 财 务 司. 险 废 物 和 医 疗 危 废 物 处 置 设 施 建 设 规 划 [ . 京 : 境 科 学 出 版 M] 北 环
垃圾焚烧炉排炉二次风配风的CFD优化模拟

垃圾焚烧炉排炉二次风配风的CFD优化模拟垃圾焚烧炉是一种能够有效处理城市生活垃圾的设备。
在垃圾焚烧过程中,二次风和配风的合理调节对于炉内温度分布、燃烧效率和废气排放有着重要影响。
因此,利用计算流体力学(CFD)模拟技术对垃圾焚烧炉进行优化模拟是十分必要的。
首先,对垃圾焚烧炉进行CFD模拟需要建立合适的物理模型和数学模型。
物理模型应包括垃圾填充层、炉膛、烟道等主要结构,数学模型应包括质量守恒方程、能量守恒方程和动量守恒方程。
同时,还应考虑燃料的燃烧反应和烟气的混合与传导等细节。
其次,CFD模拟应着重优化排炉二次风和配风的调节。
排炉二次风的主要作用是加强燃烧过程,保证垃圾焚烧炉内足够的氧气供给,提高燃烧效率,降低废气排放。
配风的主要作用是调节炉内温度分布,防止炉内局部过热或过冷。
通过CFD模拟,可以合理设计二次风和配风的喷射位置、角度和流量,使其均匀分布在炉内,充分与燃烧垃圾接触,最大程度上发挥其功能。
在进行CFD模拟时,需要对炉内的物料特性和燃烧特性进行实验测试,并建立合适的物料模型和燃烧模型。
通过对实验数据的分析,可以确定物料和燃烧模型中的参数,从而提高模拟的准确性。
同时,还需要考虑炉内垃圾的湿度、粒径分布和混合物质等因素对燃烧过程的影响。
通过CFD模拟可以得到炉内温度分布、燃烧效率和废气排放等关键指标的数值计算结果。
通过对模拟结果的分析,可以优化炉内二次风和配风的调节,使其达到最佳状态。
例如,在炉膛顶部增设适当的二次风口可以增加上层的燃烧温度,改善燃烧效率;调节配风的流量和角度可以更好地控制炉内温度分布,避免过热或过冷带来的问题。
综上所述,利用CFD模拟技术对垃圾焚烧炉的排炉二次风和配风进行优化模拟是十分必要和重要的。
通过对垃圾焚烧炉内流场和温度场的分析,可以优化二次风和配风的调节,提高燃烧效率和废气排放质量。
这对于垃圾焚烧炉的改进和设计具有重要指导意义。
垃圾发电炉膛温度计算模型说明

垃圾发电炉膛温度计算模型说明一、简介我们目前上传的炉膛温度根据最新环保文件《生活垃圾焚烧监控(监测)联网传输技术要求(试行)》,是根据现场安装在顶棚的三支温度测点,再依据锅炉设计公司数学模型,具体公式:三只顶棚温度平均值*MIN[1.4,(K1-(实际负荷/锅炉设计负荷)*K2]*K3;其中系数K1,K2,K3有厂家的设计值,再来现场根据三种典型锅炉工况下进行修正,具体是在低层和高层同时经行测温,依据得到的多组数据计算出对应三种工况下的2S炉膛温度测量值,再反推相应工况下的K1,K2,K3系数,最后在取三轮试验的K1,K2,K3的平均值,最终作为修正后系数,带入公式,形成DCS计算的2S炉膛温度。
二、炉膛2S温度实际测量值(计算以#3炉的测温试验数值为例,具体可以参考附件表格)锅炉第一烟道相关参数宽度:7.65米深度3.42米level upper net measurement(高位置水平距离)=lBNBZ + Δl=32米level lower net measurement(低位置水平距离)=lBNBZ + ΔlBNBZ=25米level start 2s post combustion zone(2S燃烧区域开始距离)=lBNBZ=16.4米temperature gradient(温度梯度)=28.36 °C/mtraverage temperature upper level(高位置平均温度)=三只顶棚温度的测量值取平均值=914.0 °Caverage temperature lower level(低位置平均温度)=低位置的温度测量值取平均值=1112.5°C烟气流量(STP标况)=41864.2Nm³/h计算值如下:目标2S炉膛温度实际测量值,分成以下四步:1、Flue gas velocity(烟气流速)的计算=烟气流量(STP标况)*(273.15+C22)/273.15/(width*depth)/3600=2.240 m/s2、temperature start post combustion zone(2S燃烧区域开始温度:T0)T0= 低位置平均温度+(低位置距离-2S燃烧区域开始距离)*温度梯度=1112.5+(25-16.4)*28.36=1356°C3、middle Temperature combustion zone(燃烧区中间位置温度)Tm = (T0+850°C)/2=1103.1°C4、hight of 2s post combustion zone(2S燃烧区高度)=Δl + ΔlNBZ=烟气流速*2S=4.479 m5、2s temperature实际测量值(2S温度)=TNBZ=2S燃烧区域开始温度-2S燃烧区高度*温度梯度=1229.3°C6、我公司实际安装的为三支顶棚温度,他们的平均值:Troof(顶棚平均温度)=869.2 °C三、DCS炉膛温度计算公式:第一步:三只顶棚温度平均值*MIN[1.4,(K1-(试验负荷/锅炉设计负荷)*K2]*K3 公式说明:上面公式中需要确定三个系数值K1,K2,K3当(K1-(试验负荷/锅炉设计负荷)*K2)的数值如果大于1.4的情况,DCS炉膛温度等于顶棚温度平均值*1.4倍后再经行K3系数的修正。
- 1、下载文档前请自行甄别文档内容的完整性,平台不提供额外的编辑、内容补充、找答案等附加服务。
- 2、"仅部分预览"的文档,不可在线预览部分如存在完整性等问题,可反馈申请退款(可完整预览的文档不适用该条件!)。
- 3、如文档侵犯您的权益,请联系客服反馈,我们会尽快为您处理(人工客服工作时间:9:00-18:30)。
垃圾发电炉膛温度计算模型说明
一、简介
目前上传的炉膛温度根据最新环保文件《生活垃圾焚烧监控(监测)联网传输技术要求(试行)》,是根据现场安装在顶棚的三支温度测点,再依据锅炉设计公司德国巴高克提供的数学模型,具体公式:三只顶棚温度平均值*MIN[1.4,(K1-(实际负荷/锅炉设计负荷)*K2]*K3;其中系数K1,K2,K3有厂家的设计值,再来现场根据三种典型锅炉工况下进行修正,具体是在低层和高层同时经行测温,依据得到的多组数据计算出对应三种工况下的2S炉膛温度测量值,再反推相应工况下的K1,K2,K3系数,最后在取三轮试验的K1,K2,K3的平均值,最终作为修正后系数,带入公式,形成DCS计算的2S炉膛温度。
二、具体解释
炉膛2S温度实际测量值(计算以#3炉的测温试验数值为例,具体可以参考附件表格)
锅炉第一烟道相关参数(德国巴高克厂家提供)
宽度:7.65米深度3.42米
level upper net measurement
(高位置水平距离)=lBNBZ +
Δl=32米
level lower net measurement
(低位置水平距离)=lBNBZ +
ΔlBNBZ
=25米
level start 2s post
combustion zone(2S燃烧区域
开始距离)=lBNBZ
=16.4米
temperature gradient(温度梯
度)
=28.36 °C/mtr
average temperature upper
level(高位置平均温度)=三只
顶棚温度的测量值取平均值
=914.0 °C
average temperature lower
level(低位置平均温度)=低位
置的温度测量值取平均值
=1112.5°C
烟气流量 (STP标
况)=41864.2Nm³/h
计算值如下:目标2S炉膛温度实际测量值,分成以下四步:
1、Flue gas velocity(烟气流速)的计算
=烟气流量 (STP标况)*(273.15+C22)/273.15/(width*depth)/3600=2.240 m/s
2、temperature start post combustion zone(2S燃烧区域开始温度:T0)
T0= 低位置平均温度+(低位置距离-2S燃烧区域开始距离)*温度梯度
=1112.5+(25-16.4)*28.36=1356°C
3、middle Temperature combustion zone(燃烧区中间位置温度)
Tm = (T0+850°C)/2=1103.1°C
4、hight of 2s post combustion zone(2S燃烧区高度)
=Δl + ΔlNBZ=烟气流速*2S=4.479 m
5、2s temperature实际测量值(2S温度)
=TNBZ=2S燃烧区域开始温度-2S燃烧区高度*温度梯度=1229.3°C
6、我公司实际安装的为三支顶棚温度,他们的平均值:
Troof(顶棚平均温度)=869.2 °C
三、DCS炉膛温度计算公式:
第一步:三只顶棚温度平均值*MIN[1.4,(K1-(试验负荷/锅炉设计负荷)*K2]*K3
公式说明:上面公式中需要确定三个系数值K1,K2,K3
当(K1-(试验负荷/锅炉设计负荷)*K2)的数值如果大于1.4的情况,DCS炉膛温度等于顶棚温度平均值*1.4倍后再经行K3系数的修正。
默认的K值为K1=1.587;K2=0.267;K3=0.97(由德国巴高克提供,应该是试验数据所得,为设计值,反映顶棚温度在不同负荷下与2S炉膛温度的比例关系);
第二步:在现场根据三轮典型工况下的具体负荷值经行修正
第一轮试验负荷为45.6 t/h;所以K1-(负荷/48.8)*K2=1.587-45.6/48.8*0.267=1.338
第二轮试验负荷为42.0 t/h;所以K1-(负荷/48.8)*K2=1.587-42.0/48.8*0.267=1.357
第二轮试验负荷为49.6 t/h;所以K1-(负荷/48.8)*K2=1.587-42.0/48.8*0.267=1.316
所以对应三轮试验的炉膛温度计算值为:
根据上面的计算公式:三只顶棚温度平均值*MIN[1.4,(K1-(试验负荷/锅炉设计负荷)*K2]*k3 第一轮试验负荷为45.6 t/h,顶棚温度为869.2,2s温度计算值=869.2*1.338*0.97=1127.69
第二轮试验负荷为42.0t/h,顶棚温度为824.5,2s温度计算值=824.5*1.357*0.97=1085.44
第三轮试验负荷为49.6t/h,顶棚温度为869.1,2s温度计算值=869.1*1.316*0.97=1109.11
根据上面的第二章炉膛2S温度实际测量值分别为
第一轮试验负荷为45.6 t/h,顶棚温度为869.2,2s温度实际值=1229.40
第二轮试验负荷为42.0t/h,顶棚温度为824.5,2s温度实际值=1153.56
第三轮试验负荷为49.6t/h,顶棚温度为869.1,2s温度实际值=1137.70
第三步:根据三轮试验算出的2s温度实际值,反推出相对应的K1,K2,K3值
试验1Round1 K1=1.591 K2=0.21 K3=1.01408
试验2Round2 K1=1.581 K2=0.21 K3=0.99936
试验3Round3 K1=1.591 K2=0.21 K3=0.95027
再根据上面的数值取三组平均值,分别得出K1,K2,K3的平均值k1_avg=1.588,k2_avg=0.21,k3_avg=0.988,最终带入第一步中的公式(如下显示)
三只顶棚温度平均值*MIN[1.4,(K1-(试验负荷/锅炉设计负荷)*K2]*K3
到此2S炉膛温度计算完成
举例:二期#3炉2S炉膛温度具体公式为:
三只顶棚温度平均值*MIN[1.4,(1.588-(实际负荷/48.8)*0.21]*0.988。