软氮化原理浅析.
硬氮化、软氮化

硬氮化和软氮化工艺等方面的比较我在外工作多年,在工作中经常会遇到客户送来的产品需要氮化处理。
但当我们问到是氮化或软氮化时,他们就不知到了。
因为他们都是机械设计方面的技术人员,对热处理知识了解的不是太多。
所以,我们就得耐心的给他们讲解氮化和软氮化的区别和性能,包括生产成本等等。
所以,有必要将氮化和软氮化的工艺特点及主要应用范围进行了整理,供机械设计方面的工程技术人员在产品设计过程中参考。
一、硬氮化和软氮化方法、特点及主要应用范围。
二、国家标准对软氮化和硬氮化工艺方面的要求:1、GB/T18177-2000《钢的气体渗氮》(硬氮化)根据不同的渗层有多种工艺供选择。
2、⑴JB/T4155-1999《气体氮碳共渗》(软氮化)一般只有一个工艺范围供选择,常用的共渗温度为540-570℃,保温2-4H,处理过程要注意炉温波动及渗剂的加入量;工件进炉后,排气速度宜快,升温速度要控制,必要时可采取预热措施。
⑵对表面色泽有要求的工件,在升温阶段及共渗后冷却过程中,必须在渗氮气氛或其它保护气氛中进行。
三、检测方面:1、GB/T18177-2000《钢的气体渗氮》中检验方法中规定:⑴裂纹、开裂等可用肉眼判别,也可采用磁粉或渗透探伤等方法鉴别。
⑵表面硬度检验:根据产品要求以及渗层深度采用不同的负荷。
⑶渗层脆性检验:共5级,一般零件1-3级合格,重要零件1-2级合格。
⑷渗氮层疏松检验:共5级,一般零件1-3级合格,重要零件1-2级合格。
⑸渗氮扩散层中氮化物检验:共5级,一般零件1-3级合格,重要零件1-2级合格。
2、JB/T4155-1999《气体氮碳共渗》(软氮化)中检验方法中规定:⑴表面硬度及渗层深度见下表气体氮碳共渗后的表面硬度和渗层深度⑵化合物疏松层是其必检项目。
共5级,一般零件1-3级合格,重要零件1-2级合格。
四、软氮化和硬氮化之间的比较:1、渗层组织:软氮化后的渗层组织与气体氮化相似,由化合物层和扩散层组成。
汽车排气阀软氮化工艺研究
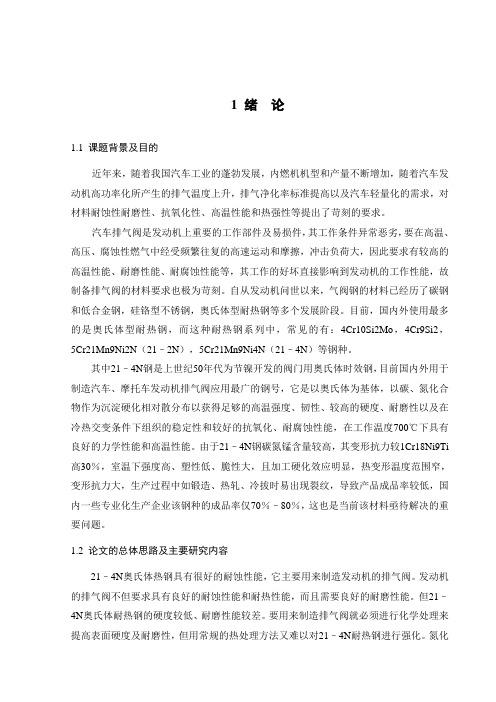
1绪论1.1 课题背景及目的近年来,随着我国汽车工业的蓬勃发展,内燃机机型和产量不断增加,随着汽车发动机高功率化所产生的排气温度上升,排气净化率标准提高以及汽车轻量化的需求,对材料耐蚀性耐磨性、抗氧化性、高温性能和热强性等提出了苛刻的要求。
汽车排气阀是发动机上重要的工作部件及易损件,其工作条件异常恶劣,要在高温、高压、腐蚀性燃气中经受频繁往复的高速运动和摩擦,冲击负荷大,因此要求有较高的高温性能、耐磨性能、耐腐蚀性能等,其工作的好坏直接影响到发动机的工作性能,故制备排气阀的材料要求也极为苛刻。
自从发动机问世以来,气阀钢的材料已经历了碳钢和低合金钢,硅铬型不锈钢,奥氏体型耐热钢等多个发展阶段。
目前,国内外使用最多的是奥氏体型耐热钢,而这种耐热钢系列中,常见的有:4Cr10Si2Mo,4Cr9Si2,5Cr21Mn9Ni2N(21–2N),5Cr21Mn9Ni4N(21–4N)等钢种。
其中21–4N钢是上世纪50年代为节镍开发的阀门用奥氏体时效钢,目前国内外用于制造汽车、摩托车发动机排气阀应用最广的钢号,它是以奥氏体为基体,以碳、氮化合物作为沉淀硬化相对散分布以获得足够的高温强度、韧性、较高的硬度、耐磨性以及在冷热交变条件下组织的稳定性和较好的抗氧化、耐腐蚀性能,在工作温度700℃下具有良好的力学性能和高温性能。
由于21–4N钢碳氮锰含量较高,其变形抗力较1Cr18Ni9Ti 高30%,室温下强度高、塑性低、脆性大,且加工硬化效应明显,热变形温度范围窄,变形抗力大,生产过程中如锻造、热轧、冷拔时易出现裂纹,导致产品成品率较低,国内一些专业化生产企业该钢种的成品率仅70%–80%,这也是当前该材料亟待解决的重要问题。
1.2 论文的总体思路及主要研究内容21–4N奥氏体热钢具有很好的耐蚀性能,它主要用来制造发动机的排气阀。
发动机的排气阀不但要求具有良好的耐蚀性能和耐热性能,而且需要良好的耐磨性能。
但21–4N奥氏体耐热钢的硬度较低、耐磨性能较差。
软氮化处理综述
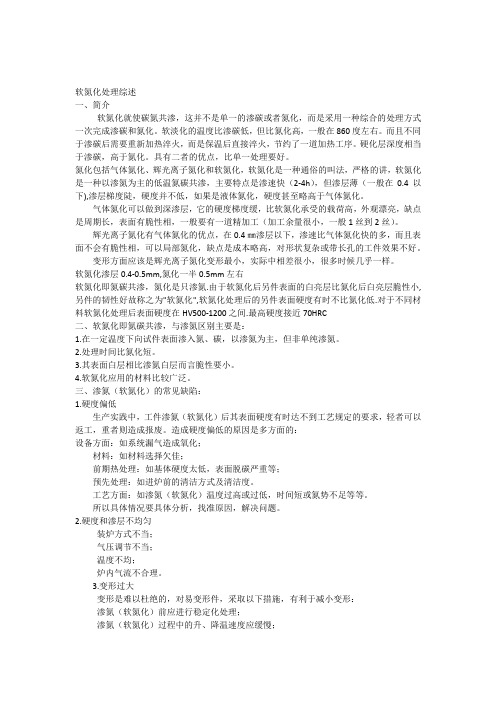
软氮化处理综述一、简介软氮化就使碳氮共渗,这并不是单一的渗碳或者氮化,而是采用一种综合的处理方式一次完成渗碳和氮化。
软淡化的温度比渗碳低,但比氮化高,一般在860度左右。
而且不同于渗碳后需要重新加热淬火,而是保温后直接淬火,节约了一道加热工序。
硬化层深度相当于渗碳,高于氮化。
具有二者的优点,比单一处理要好。
氮化包括气体氮化、辉光离子氮化和软氮化,软氮化是一种通俗的叫法,严格的讲,软氮化是一种以渗氮为主的低温氮碳共渗,主要特点是渗速快(2-4h),但渗层薄(一般在0.4以下),渗层梯度陡,硬度并不低,如果是液体氮化,硬度甚至略高于气体氮化。
气体氮化可以做到深渗层,它的硬度梯度缓,比软氮化承受的载荷高,外观漂亮,缺点是周期长,表面有脆性相,一般要有一道精加工(加工余量很小,一般1丝到2丝)。
辉光离子氮化有气体氮化的优点,在0.4㎜渗层以下,渗速比气体氮化快的多,而且表面不会有脆性相,可以局部氮化,缺点是成本略高,对形状复杂或带长孔的工件效果不好。
变形方面应该是辉光离子氮化变形最小,实际中相差很小,很多时候几乎一样。
软氮化渗层0.4-0.5mm,氮化一半0.5mm左右软氮化即氮碳共渗,氮化是只渗氮.由于软氮化后另件表面的白亮层比氮化后白亮层脆性小,另件的韧性好故称之为"软氮化",软氮化处理后的另件表面硬度有时不比氮化低.对于不同材料软氮化处理后表面硬度在HV500-1200之间.最高硬度接近70HRC二、软氮化即氮碳共渗,与渗氮区别主要是:1.在一定温度下向试件表面渗入氮、碳,以渗氮为主,但非单纯渗氮。
2.处理时间比氮化短。
3.其表面白层相比渗氮白层而言脆性要小。
4.软氮化应用的材料比较广泛。
三、渗氮(软氮化)的常见缺陷:1.硬度偏低生产实践中,工件渗氮(软氮化)后其表面硬度有时达不到工艺规定的要求,轻者可以返工,重者则造成报废。
造成硬度偏低的原因是多方面的:设备方面:如系统漏气造成氧化;材料:如材料选择欠佳;前期热处理:如基体硬度太低,表面脱碳严重等;预先处理:如进炉前的清洁方式及清洁度。
软氮化原理
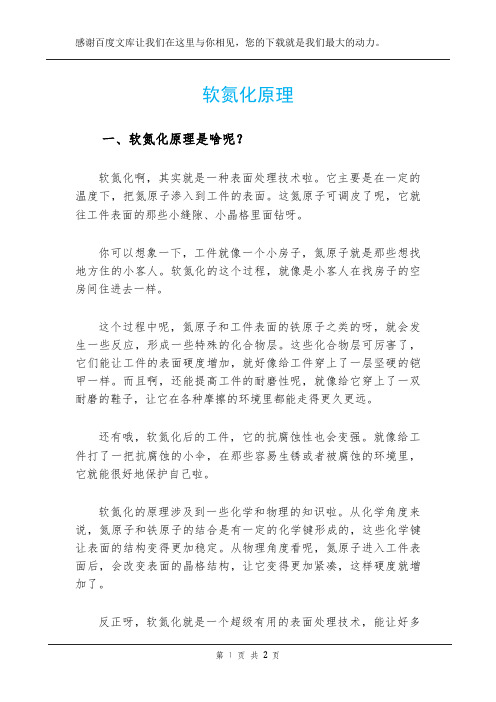
软氮化原理
一、软氮化原理是啥呢?
软氮化啊,其实就是一种表面处理技术啦。
它主要是在一定的温度下,把氮原子渗入到工件的表面。
这氮原子可调皮了呢,它就往工件表面的那些小缝隙、小晶格里面钻呀。
你可以想象一下,工件就像一个小房子,氮原子就是那些想找地方住的小客人。
软氮化的这个过程,就像是小客人在找房子的空房间住进去一样。
这个过程中呢,氮原子和工件表面的铁原子之类的呀,就会发生一些反应,形成一些特殊的化合物层。
这些化合物层可厉害了,它们能让工件的表面硬度增加,就好像给工件穿上了一层坚硬的铠甲一样。
而且啊,还能提高工件的耐磨性呢,就像给它穿上了一双耐磨的鞋子,让它在各种摩擦的环境里都能走得更久更远。
还有哦,软氮化后的工件,它的抗腐蚀性也会变强。
就像给工件打了一把抗腐蚀的小伞,在那些容易生锈或者被腐蚀的环境里,它就能很好地保护自己啦。
软氮化的原理涉及到一些化学和物理的知识啦。
从化学角度来说,氮原子和铁原子的结合是有一定的化学键形成的,这些化学键让表面的结构变得更加稳定。
从物理角度看呢,氮原子进入工件表面后,会改变表面的晶格结构,让它变得更加紧凑,这样硬度就增加了。
反正呀,软氮化就是一个超级有用的表面处理技术,能让好多
工件变得更厉害、更耐用呢。
碳氮共渗浅析
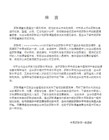
碳氮共渗与氮碳共渗其实没有什么区别,热处理一般的都通称为碳氮共渗。
只是碳氮共渗又分为:1.高温碳氮共渗,以渗碳为主,加热到奥氏体化,渗层深。
2.中温碳氮共渗,以渗碳为主,加热到奥氏体化,但温度比高温碳氮共渗低,渗层较浅,又叫氰化
3.低温碳氮共渗,以渗氮为主,加热到共析线以下,组织不发生相变,变形很小,又叫软氮化。
但我认为如果在0.5mm以内时,一次离子渗就可以达到,可以根据零件实际需要对渗层深度进行修正,这样即可以节约成本又可以满足使用需要。
碳氮共渗(carbonitrided)与氮碳共渗(nitrocarburized)的区别:
1、 碳氮共渗carbonitriding :在奥氏体状态下,同时将碳、氮渗入钢件表层,并渗碳为主的化学热处理工艺。
气体软氮化(碳氮共渗)温度常用560-570℃,因该温度下氮化层硬度值最高。氮化时间常为2-3小时,因为超过2.5小时,随时间延长,氮化层深度增加很慢。 可以看出碳氮共渗的温度最高,其组织由ε相、γ相和含氮的渗碳体Fe3(C,N)所组成,所以热应力和组织应力都较前两者大,再者渗层薄,所以不能承受重载。但这种处理也有优点,由于软氮化层不存在脆性ξ相,故氮化层硬而具有一定的韧性,不容易剥落。
4.碳氮共渗热处理的工艺温度低,一般淬火后的变形也小.
影视版主 2009-03-03 06:48
渗碳与碳氮共渗是有区别的:
渗碳一般都用880~940度,而碳氮共渗使用的温度比较低,一般在800~860度.
ummvixf 2009-03-03 06:49
2楼的说的不完全,对一些有安全要求的产品来说,选择渗碳更好点.其实两种工艺各有各的优点,具体要根据零件的服役条件及性能要求而选择.
软氮化工艺在我国工业中的应用及发展前景

软氮化工艺在我国工业中的应用及发展前景奚道鑫济南钢铁集团有限公司250101摘要:阐述软氮化的工艺原理,分析它赋予被处理零件的高的耐蚀性、耐磨性、抗疲劳性、抗咬合、抗擦伤性等的机理,并对目前软氮化工艺作一个细致的划分和归纳,对其在我国各个领域的应用作进一步的研究和展望。
关键词:软氮化、耐蚀性、耐磨性、硬度、表面粗糙度Tufftride craft in our country industry applicationand prospects for developmentXi DaoxinJigang Group Co.,Ltd. 250101Abstract: Soft nitride process principle of its parts to be dealt with high corrosion resistance, abrasion resistance, anti-fatigue, anti-bite, scratch resistance, and so the mechanism and process for the current soft nitride the delineation of a detailed and summarized, in their various fields of application in China for further studies and forecasts.Key words: soft nitride, corrosion resistance, wear resistance, hardness, surface roughness软氮化工艺起源于西德,实质上是以渗氮为主的低温碳氮共渗,钢的氮原子渗及的同时,还有少量的碳原子渗入,其处理结果与一般气体氮相比,渗层硬度低,脆性较小,故称为软氮化。
由于它能明显缩短氮化的周期,并使氮化工艺不受钢种的限制,并且经过软氮化工艺获得的渗层组织硬度较高,且耐磨性和抗疲劳性、抗咬合性都较好。
软氮化的‘白亮层’

软氮化的‘白亮层’作者:hezj钢的氮碳共渗(软氮化)中,获得厚度不到一根头发粗、薄薄如纸的白亮层,隐藏着许多的秘密。
一方面在工程上获得广泛应用,也留下许多谜团。
下面仅就这个问题说说个人的一些看法。
一,白亮层的优缺点及其应用1,渗氮和铁素体氮碳共渗时,对碳素钢而言,钢表面有一层化合物层,相结构为γ,、ε、ε+γ,三种基本形式;奥氏体氮碳共渗快冷时,临近化合物层下面还有一层含氮碳奥氏体的淬火层,相结构为M+A。
这种两种属性不同表面层,在弱酸性溶液中短时间浸蚀时抗蚀能力优于普通钢的基体组织,金相组织检查时,基体组织腐蚀出来后,仍然保持着为白色或灰白色,故称为‘白亮层’。
2,化合物白亮层,具有较高的硬度和良好的热硬性、较好的抗大气和淡水腐蚀性能和较低的摩擦系数。
含氮碳奥氏体淬火层具有中等硬度(可时效硬化)、耐磨性和耐蚀性(淬火态)都优于化合物层,其塑性也较高。
两种白亮层都有同样的问题,其内部的相结构不同,性能上而有所差别。
3,白亮层也有不足之处,单簿、脆性较大、怕酸、抗蚀性有限。
在应用上,选择有所侧重,通常按三个方面,即高耐磨性与抗疲劳性;较高抗蚀性与耐磨性;良好的滑动摩擦与减摩性。
同时要与钢牌号的选择相结合,优化组合达到工程上的不同要求。
所以,不要以为白亮层的优点是万能的,通用的,不讲条件的。
学以致用,掌握此门技术只是第一步,用好则是一种艺术。
4,化合物白亮层在通常渗氮的合金钢工件上,是否有利,要看使用条件。
对于局部承载力很大的零件,白亮层是有害的东西。
由于容易压碎而剥落,碎片将加速零件表面的磨损、划伤,使零件过早失效,还有可能散落到其他组件上造成事故。
尤其是高可靠性的精密机械,对化合物白亮层的厚度有严格的限制,甚至要求完全没有白亮层。
这时,扩散层(内氮化层)才是设计所需要的。
近代兴起的可控氮化技术,就是针对这个问题发展起来的。
可控氮化技术可以做到3~5μm以下(单相γ,),乃至无化合物层。
这是渗氮技术上的重大突破。
汽车曲轴的软氮化技术
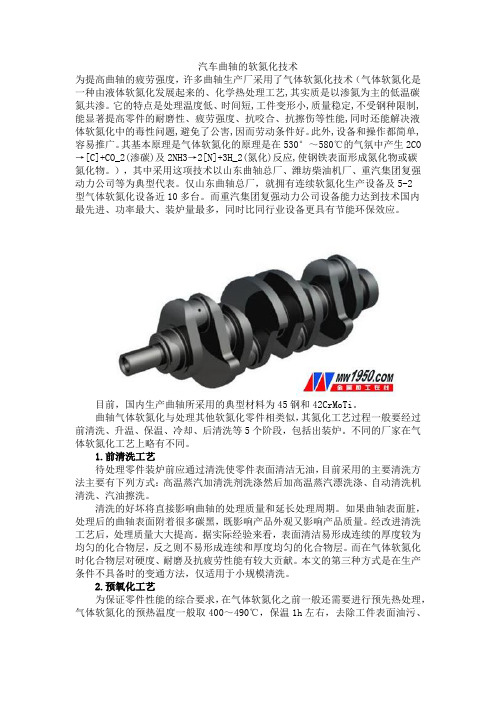
汽车曲轴的软氮化技术为提高曲轴的疲劳强度,许多曲轴生产厂采用了气体软氮化技术(气体软氮化是一种由液体软氮化发展起来的、化学热处理工艺,其实质是以渗氮为主的低温碳氮共渗。
它的特点是处理温度低、时间短,工件变形小,质量稳定,不受钢种限制,能显著提高零件的耐磨性、疲劳强度、抗咬合、抗擦伤等性能,同时还能解决液体软氮化中的毒性问题,避免了公害,因而劳动条件好。
此外,设备和操作都简单,容易推广。
其基本原理是气体软氮化的原理是在530°~580℃的气氛中产生2CO →[C]+CO_2(渗碳)及2NH3→2[N]+3H_2(氮化)反应,使钢铁表面形成氮化物或碳氮化物。
),其中采用这项技术以山东曲轴总厂、潍坊柴油机厂、重汽集团复强动力公司等为典型代表。
仅山东曲轴总厂,就拥有连续软氮化生产设备及5-2型气体软氮化设备近10多台。
而重汽集团复强动力公司设备能力达到技术国内最先进、功率最大、装炉量最多,同时比同行业设备更具有节能环保效应。
目前,国内生产曲轴所采用的典型材料为45钢和42CrMoTi。
曲轴气体软氮化与处理其他软氮化零件相类似,其氮化工艺过程一般要经过前清洗、升温、保温、冷却、后清洗等5个阶段,包括出装炉。
不同的厂家在气体软氮化工艺上略有不同。
1.前清洗工艺待处理零件装炉前应通过清洗使零件表面清洁无油,目前采用的主要清洗方法主要有下列方式:高温蒸汽加清洗剂洗涤然后加高温蒸汽漂洗涤、自动清洗机清洗、汽油擦洗。
清洗的好坏将直接影响曲轴的处理质量和延长处理周期。
如果曲轴表面脏,处理后的曲轴表面附着很多碳黑,既影响产品外观又影响产品质量。
经改进清洗工艺后,处理质量大大提高。
据实际经验来看,表面清洁易形成连续的厚度较为均匀的化合物层,反之则不易形成连续和厚度均匀的化合物层。
而在气体软氮化时化合物层对硬度、耐磨及抗疲劳性能有较大贡献。
本文的第三种方式是在生产条件不具备时的变通方法,仅适用于小规模清洗。
2.预氧化工艺为保证零件性能的综合要求,在气体软氮化之前一般还需要进行预先热处理,气体软氮化的预热温度一般取400~490℃,保温1h左右,去除工件表面油污、油脂,并在表面形成一层氧化物,使(合金)氮化物缓慢形成,使深层更加均匀。
- 1、下载文档前请自行甄别文档内容的完整性,平台不提供额外的编辑、内容补充、找答案等附加服务。
- 2、"仅部分预览"的文档,不可在线预览部分如存在完整性等问题,可反馈申请退款(可完整预览的文档不适用该条件!)。
- 3、如文档侵犯您的权益,请联系客服反馈,我们会尽快为您处理(人工客服工作时间:9:00-18:30)。
CO2+H2→CO+H2O (Fe4N,Fe2~3N)
CO+H2→[C]+H2O
渗氮层的组织 Fe-N系可形成五种相:α相 氮在α –Fe中的间隙固溶体,也称含氮铁素体,
体心立方点阵。590℃时,氮在α –Fe 中的溶解度最大,氮的质量分数约为0.1%, 随温度下降, α相 缓慢析出γ’相。
4、渗氮零件常见缺陷及防止措施 表2、渗氮零件常见缺陷及防止措施
缺陷内容 渗氮层硬 度低或硬 度不均匀 产生原因 防止措施
渗氮温度偏高;工件未洗净,经常校验仪表、热电偶,防止温控 表面有油污;调质硬度低; 器失灵;洗净油污;降低回火温度, 材料组织不均匀;密封不良、提高调质硬度,调整预备热处理工 炉盖等处漏气;装炉不当, 艺,更换石棉垫,加强密封、合理 气氛循环不良 装炉,保证气流畅通。
9
3、气体渗氮 气体渗氮一般使用无水氨气(氨+氮)作为供氮介质。整个渗氮过程可 分为分解、吸附及扩散三个过程,即氨的分解、钢件表面吸收氮原子、氮 原子从表面向里扩散。 影响渗氮因素很多,如温度、时间、压力、介质成分以及零件钢材成 分和组织等。只有合理地控制这些因素,才能获得满意的渗氮效果。为了 不影响零件调质后的心部强度,渗氮温度一般比调质时的回火温度低40~ 70℃。 随渗氮温度的升高,氮原子的扩散速度显著增大,同时也加快了渗层 对活性氮原子的吸收过程,因此渗层深度增加。但温度过高,会使变形增 大,心部强度下降。 渗氮时,保温时间决定了氮原子的渗入深度。随着时间的延长,渗氮 层深度不断增加,并呈抛物线规律变化。即开始时增加速度快,随着时间 的延长,渗层深度的增加越来越慢。
化合物层 氮浓度低,化合物层偏薄, 氨分解率不宜过高,冷速适当调 不致密, 冷却速度太慢,氮化物分 整,入炉前应除尽锈斑 抗蚀性差 解造成疏松层偏厚,零件 锈斑未除尽
13
3
5、热处理原理简介 热处理原理就是研究钢在加热和冷却过程中的组织和性能转变的 规律,五大转变(等温转变、回火转变、珠光体转变、贝氏体转变、 马氏体转变)四把火(淬火、正火、回火、退火)。
温度 温度 保温 加热 冷却
最基本的处理工艺曲线
时间
4
6、热处理分类 金属热处理工艺大体可分为整体热处理、表面热处理和化学热处理 三大类。根据加热介质、加热温度和冷却方法的不同,每一大类又可区 分为若干不同的热处理工艺。同一种金属采用不同的热处理工艺,可获 得不同的组织,从而具有不同的性能。 整体热处理是对工件整体加热,然后以适当的速度冷却,获得需要 的金相组织,以改变其整体力学性能的金属热处理工艺。钢铁整体热处 理大致有退火、正火、淬火和回火四种基本工艺。 表面热处理是以很大的功率密度对工件整体或局部加热,将工件一 定厚度的表面层加热到临界点以上,用淬火剂急冷,使表层组织转变为 马氏体,具有高的硬度、耐磨性、疲劳强度,而心部仍保持淬火前的组 织。 化学热处理是将金属或合金工件置于一定温度的活性介质中保温, 使一种或几种元素渗入它的表层,以改变其化学成分、组织和性能的热 处理工艺。
软氮化原理浅析
目录
一、 热处理的概述
二、化学热处理简介
三、氮化
一、热处理的概述
1、热处理概念 热处理是指对固态金属或合金采用适当方式加热、保温和冷却,以获 得所需要的组织结构与性能的工艺方法。 • 改善钢的性能,主要有两条途径: • 一是合金化 • 二是热处理
1
2、热处理特点: 热处理区别于其
11
γ相 氮在γ –Fe中的间隙固溶体,也称含氮奥氏体,面心立方点阵,存在 于共析温度590℃以上,缓冷时发生γ相 共析转变,生成共析组织(а+γ’); 如果快冷,则形成含氮马氏体。 γ’相 以Fe4-N为基体的固溶体,在680℃以下稳定存在。680℃以上转变 为ε相。 ε相 以Fe3-N为基体的固溶体,随温度降低, ε相 不断析出γ’相 。ξ相 为斜方晶格的间隙化合物,分子式为Fe2-N ,温度高于490 ℃ , ξ相 转 变为ε相 。 因此,渗氮层组织由表及里为: ε→ ε + γ’ → γ’ → γ’ +а→а,如果表面 氮质量分数达到11%左右,则ε相 可能转变为ξ相 。因ε、 γ’、 ξ相抗蚀性 很强,在金相显微镜下为白亮层。
6
表1:常用的化学热处理方法及其作用
热处理方法
渗碳及碳氮共渗 渗氮及氮碳共渗 渗硫 硫氮及硫氮碳共渗 渗硼 渗硅 渗锌 渗铝 渗铬 渗钒
渗入元素
C或C、N N或N、C S
作用
提高工件的耐磨性、硬度及疲劳强度 提高工件的表面硬度、耐磨性、抗咬合能力及抗腐蚀能力 提高工件的减磨性和抗咬合能力
S、N或S、N、 提高工件的耐磨性、减磨性及抗疲劳、抗咬合能力 C B Si Zn AL Cr V 提高工件的表面硬度,提高耐磨性、抗腐蚀能力及红硬性 提高工件的表面硬度、提高抗腐蚀、抗氧化能力 提高工件抗大气腐蚀能力 提高工件抗高温氧化、抗含硫介质腐蚀能力 提高工件抗高温氧化、抗腐蚀能力及耐磨性 提高工件的表面硬度,提高耐磨性、抗咬合能力
10
氨分解率是指某一温度下,分解出来的氮和氢的混合气体占炉气总体 积的百分比。若氨分解率过低,大量的氨来不及分解,提供活性氮原子的 概率小,不仅渗氮速度低,而且还造成浪费。若分解率过高,炉气中几乎 全部由分子态的N2和H2组成,所提供的活性氮原子也极少,同时大量的H2 吸附中工件表面也将阻碍氮的渗入。 氨分解率取决于渗氮温度、氨气流量、炉内压力、零件表面积及有无催 化剂等因素。在渗氮过程中,常采用调节氨流量的方法控制氨分解率。 渗氮过程
渗氮层 厚度浅
装炉不当,零件未经调 提高氨分解率,合理装炉,保 质处理,零件考得太近, 证零件留有5mm以上的空隙, 气氛循环不良 通过调质处理使基体组织形成 致密的回火素氏体 表面出现ξ相(Fe2N) 提高氨分解率,或降低氨的流 量,通过退氨处理使ξ相→ε相 (Fe2~3N)
渗氮层 脆性大
12
表面氧化 冷却时供氨不足,炉内负 色 压而吸入空气、炉门密封 不良、氨中含水过多,出 炉温度过高。 渗氮形成 网状、脉 状或鱼骨 状氮化物 渗氮温度太高、原始组织 晶粒粗大,零件有尖角、 锐边,表面脱碳严重,加 工粗糙度高,液氮含水量 太高、气氛氮势过高
8
2、渗氮的特点 渗氮就是在一定温度下(一般在AC1温度下)使活性氮原子渗入工件表面 的化学热处理工艺。特点如下: ⑴、高硬度和高耐磨性 渗氮后零件表面硬度可以达到950~1200HV,而 且到600℃仍可维持相当高的硬度。这显然是渗碳淬火处理达不到的。由 于硬度高,耐磨性也很好。 ⑵、较高的疲劳强度 渗氮后的表面产生了较大的残余压应力,能部分 抵消疲劳载荷下产生的拉应力,延缓疲劳破坏过程,使疲劳强度显著提 高。 ⑶、良好的抗咬合性能及抗蚀性 渗氮后的零件中短时间缺乏润滑或过 热的条件下,不容易发生卡死或擦伤损坏,具有良好的抗咬合性能。并 且能抵抗大气、自来水、弱碱性溶液等的腐蚀,具有良好的抗蚀性。 ⑷、变形小 渗氮温度低,一般为480~580 ℃,升降温速度又很慢,处 理过程心部无组织转变,仍保持调质状态的组织,所以渗氮后的零件变 形小。 渗氮的缺点是工艺过程较长,如获得1mm深的渗碳层,渗碳处理仅要6~ 9h,而获得0.5mm渗氮层,渗氮处理需要40~50h.其次,渗层也较薄,不 能承受太大的接触压力。
适当增大氨流量,保持炉内正压, 改进密封措施,出炉温度控制在 200℃以下。 降低并控制温度、降低调质时的 淬火温度,改进设计,尽量避免 尖角、锐边,调质处理的淬火工 序应在保护气氛炉中进行,或表 面脱碳层在机加时能完全切除。 渗氮前的磨削加工后期的进给量 减少,降低表面粗糙度,控制氨 分解率,勿使氮势过高
他加工工艺如铸造、压力加工等
的特点是只通过改变工件的组织 来改变性能,而不改变其形状。 铸造 3、热处理适用范围:只适用于 固态下发生相变的材料,不发
生固态相变的材料不能用热处
理强化。 轧制
2
4、热处理的作用 热处理是机械制造工艺中不可缺少的 组成部分,它是充分发挥金属材料的潜 力,改善零件加工工艺性能,提高材料 的使用性能,延长零件使用寿命的有效 手段, 根据加热、冷却方式的不同分为 退火、正火、淬火、回火、渗碳、渗氮 及感应加热淬火等多种热处理工艺,由 于热处理工艺不同,零件所获得的组织 结构也就不同,那么零件的性能也就不 同。因此,热处理在机械制造行业中被 广泛地应用,例如,汽车行业需要进行 热处理的零件占70%~80%;机床行业 占60% ~70%;轴承及各种模具则高达 100%.
硼铝共渗
铬铝共渗 铬铝硅共渗
B、AL
Cr、AL Cr、AL、Si
提高工件的耐磨性、抗腐蚀及抗高温氧化能力,表面脆性及抗剥落 能力优于渗硼
具有比单独渗铬或渗铝更优等耐热性能 提高工件的高温性能
7
三、氮化
氮化处理又称为扩散渗氮。气体渗氮在1923年左右,由德国人Fry首 度研究发展并加以工业化。由于经本法处理的制品具有优异的耐磨性、 耐疲劳性、耐蚀性及耐高温,其应用范围逐渐扩大。例如钻头、螺丝 攻、挤压模、锻压模、螺杆、连杆、曲轴、及齿轮凸轮等均有使用。 常见有液体渗氮、气体渗氮、离子渗氮。 我司曲轴氮化属于气体渗氮。 1、软氮化工艺参数的选择 氮化温度 Fe—N二元合金的共析温度为590℃,超过该温度界限, 会发生α→γ相变。而Fe—C—N三元合金的共析点是565 ℃(约 0.35%C,1.8%N),接近这个温度,氮在α—Fe中的溶解度最大, 所以一般认为软氮化温度以570℃最为合适。
5
二、化学热处理简介
化学热处理是将金属或合金工件置于一定温度的活性介质中保温,使一种或 几种元素渗入它的表层,以改变其化学成分、组织和性能的热处理工艺。发司 曲轴的氮化就是化学热处理。作用主要有两个方面:一是强化表面,如渗碳、 氮化、碳氮共渗、渗硼、硫氮共渗等,可以提高工件等表面等疲劳强度、硬度 和耐磨性;二是改善表面的物理、化学性能,如渗铝等,可以提高工件表面等 抗腐蚀能力、抗氧化能力。 根据钢中元素与渗入元素相互作用形成的相结构,化学热处理可分为两大类。 第一类为渗入元素在基体金属中富化但未超过固溶度,形成金属固溶体,如渗 碳(固溶扩散或纯扩散)。第二类为反应扩散,其一是扩散元素富化超过固溶 体与钢中元素形成有序相(金属间化合物),如渗氮;其二是渗入元素在溶质 元素晶格中的固溶度非常小,以致使两种元素相互作用形成化合物,如渗硼。 化学热处理通常由渗剂中的物理化学过程,渗入元素的活性物质或活性原子 被工件表面吸附和吸收,渗入原子在工件(金属)中扩散和化学反应三个基本 过程组成。