对几种新型纺纱的分析比较及其应用发展前景的看法(新).docx
纺纱新技术发展现状及趋势

纺纱新技术发展现状及趋势一、目录1.纺纱技术概述2.纺纱新技术的发展现状3.纺纱新技术的趋势4.结论二、纺纱技术概述纺纱技术是纺织工业的基础,其发展历程经历了多个阶段。
从最早的手工纺织到现代的自动化和智能制造,纺纱技术不断进步,以满足人们对纺织品质量和性能的需求。
在此过程中,新技术不断涌现,为纺纱技术的发展注入了新的活力。
三、纺纱新技术的发展现状1.自动化和智能化纺纱技术随着工业自动化和人工智能技术的不断发展,越来越多的自动化和智能化设备被应用于纺纱生产中。
例如,自动络筒机、自动接头机、智能纺纱机器人等,这些设备的应用大大提高了生产效率和质量。
2.精细化纺纱技术随着消费者对纺织品品质要求的提高,精细化纺纱技术逐渐成为纺纱技术发展的趋势。
精细化纺纱技术包括细纱、超细纱、微米纱等,其特点是纱线结构更加紧密、均匀,具有更好的柔软度和舒适性。
3.功能化纺纱技术功能化纺纱技术是指通过特殊工艺和材料,使纱线具有某种特殊功能。
例如,抗菌、抗静电、防水等。
这些功能化纺纱技术的应用拓宽了纺织品的应用领域,满足了不同消费者的需求。
四、纺纱新技术的趋势1.数字化和智能化趋势随着人工智能和大数据技术的发展,数字化和智能化将成为纺纱新技术的重要趋势。
通过引入人工智能技术,可以实现纺纱生产过程的自动化和智能化,提高生产效率和产品质量。
同时,通过大数据技术对生产数据进行分析和处理,可以实现生产过程的优化和管理。
2.绿色环保趋势随着环保意识的提高,绿色环保将成为未来纺纱新技术的重要趋势。
通过使用环保材料和节能减排技术,降低纺纱生产过程中的环境污染和资源浪费。
同时,推广循环经济模式,实现纺织废料的再生利用,提高资源利用效率。
纺纱行业的发展趋势与前景
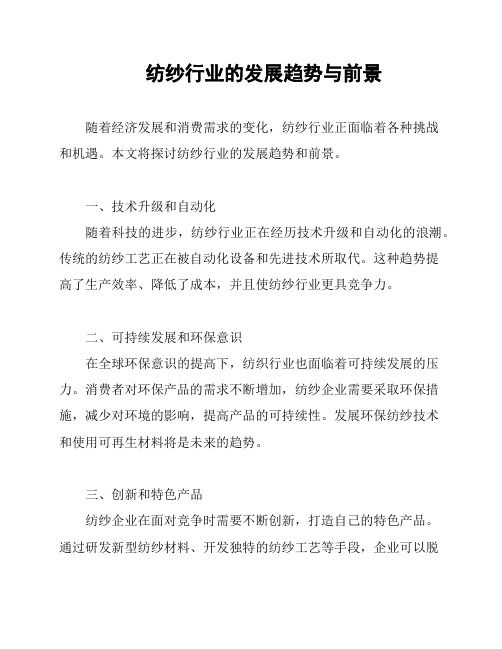
纺纱行业的发展趋势与前景
随着经济发展和消费需求的变化,纺纱行业正面临着各种挑战
和机遇。
本文将探讨纺纱行业的发展趋势和前景。
一、技术升级和自动化
随着科技的进步,纺纱行业正在经历技术升级和自动化的浪潮。
传统的纺纱工艺正在被自动化设备和先进技术所取代。
这种趋势提
高了生产效率、降低了成本,并且使纺纱行业更具竞争力。
二、可持续发展和环保意识
在全球环保意识的提高下,纺织行业也面临着可持续发展的压力。
消费者对环保产品的需求不断增加,纺纱企业需要采取环保措施,减少对环境的影响,提高产品的可持续性。
发展环保纺纱技术
和使用可再生材料将是未来的趋势。
三、创新和特色产品
纺纱企业在面对竞争时需要不断创新,打造自己的特色产品。
通过研发新型纺纱材料、开发独特的纺纱工艺等手段,企业可以脱
颖而出,满足消费者对个性化和高品质产品的需求。
同时,纺纱企
业也应关注市场需求变化,及时调整产品结构和市场定位。
四、市场国际化和跨界合作
随着全球市场的开放和竞争的加剧,纺纱企业需要加强国际化
发展和跨界合作。
拓展海外市场、参与国际贸易合作、实施国际化
战略等举措有助于增加企业的市场份额和竞争力。
总结起来,纺纱行业面临着技术升级、可持续发展、创新和国
际化等多重趋势。
通过抓住机遇、适应变化,纺纱企业可以实现持
续增长和发展。
然而,要实现这些目标,企业需要制定合适的策略,不断提高自身的竞争力和创新能力。
以上仅为个人观点,具体发展趋势还需结合市场实际情况进行
深入研究和分析。
纺织面料的发展趋势与新材料技术的应用

纺织面料的发展趋势与新材料技术的应用
1.前言
随着科技的进步和人们生活水平的不断提高,纺织面料的发展也逐渐进入了一个崭新的阶段。
在这个大背景下,新材料技术的应用变得尤为重要,这不仅可以提高面料的品质和性能,还可以为纺织行业注入新的活力和动力。
2.纤维素智能面料
纤维素智能面料是一种新型的面料,它是由纤维素制成的,其表面上涂有一层具有特殊功能的涂层。
这种面料可以根据环境和使用需求自动调节吸湿和透气的性能,让人们在各种场合下都能穿着舒适。
3.碳纤维面料
碳纤维是一种具有轻质高强、耐磨耐腐蚀等优异性能的新型材料,可以应用于各种领域,包括纺织行业。
碳纤维面料由碳纤维和合成纤维混合制成,具有极高的强度和坚韧性,可以用于制造高端服饰等。
4.仿生纤维面料
仿生纤维面料可以模仿生物体的功能特性,例如人体的机械性能、热传递性能、吸附和分离等特性。
这种面料的应用领域非常广泛,包括高端内衣、运动装备、医疗用品等。
5.光感纤维面料
光感纤维面料是一种具有高科技含量的新型面料,其特点是通过纤维中搭载的与光线交互的芯片和传感器,实现灯光控制、数据采集等功能。
这种面料在舞蹈、演出等领域有着广泛的应用前景。
6.结论
新材料技术的应用为纺织面料的发展带来了新的机遇和挑战,各种新型面料的出现不仅可以提高面料的品质和性能,还可以满足人们不断增长的需求。
未来,随着科技的不断进步和创新,纺织面料的发展前景将更加广阔。
2024年新型纺织纤维市场前景分析
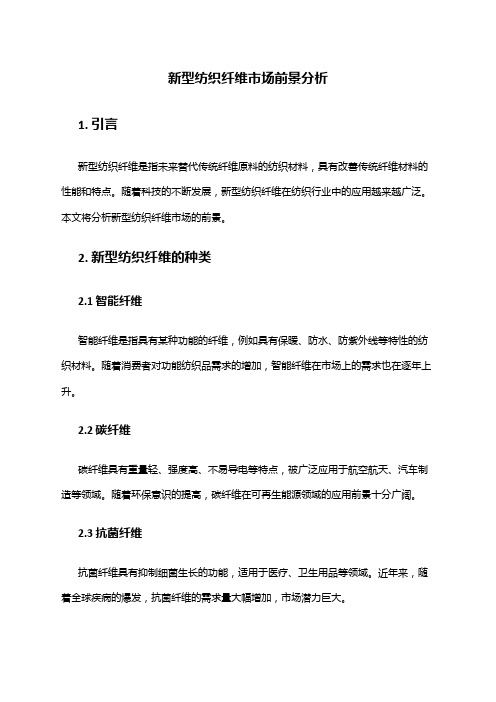
新型纺织纤维市场前景分析1. 引言新型纺织纤维是指未来替代传统纤维原料的纺织材料,具有改善传统纤维材料的性能和特点。
随着科技的不断发展,新型纺织纤维在纺织行业中的应用越来越广泛。
本文将分析新型纺织纤维市场的前景。
2. 新型纺织纤维的种类2.1 智能纤维智能纤维是指具有某种功能的纤维,例如具有保暖、防水、防紫外线等特性的纺织材料。
随着消费者对功能纺织品需求的增加,智能纤维在市场上的需求也在逐年上升。
2.2 碳纤维碳纤维具有重量轻、强度高、不易导电等特点,被广泛应用于航空航天、汽车制造等领域。
随着环保意识的提高,碳纤维在可再生能源领域的应用前景十分广阔。
2.3 抗菌纤维抗菌纤维具有抑制细菌生长的功能,适用于医疗、卫生用品等领域。
近年来,随着全球疾病的爆发,抗菌纤维的需求量大幅增加,市场潜力巨大。
3. 新型纺织纤维市场的发展趋势3.1 技术创新驱动市场增长随着科技的进步,新型纺织纤维的研发和生产技术不断更新。
技术创新带来的新产品和新应用不断涌现,推动了新型纺织纤维市场的增长。
3.2 消费者需求变化引领市场发展消费者对纺织品的需求不再局限于传统的功能和样式,更注重环保性、舒适度和健康性等方面。
新型纺织纤维能够满足消费者的需求,因此市场需求持续增长。
4. 新型纺织纤维市场前景4.1 市场规模持续扩大新型纺织纤维市场规模在不断扩大,预计未来几年将保持稳定增长。
随着国民经济的发展和人民生活水平的提高,对高品质、环保和多功能性纺织品的需求将进一步增加。
4.2 区域市场发展不平衡由于不同地区的经济发展水平和消费习惯的差异,新型纺织纤维市场在不同区域的发展也存在差异。
一些发达地区的市场发展较为成熟,而一些欠发达地区的市场仍然具有较大的发展潜力。
4.3 竞争加剧,创新驱动增长随着新型纺织纤维市场的潜力逐渐被发现,越来越多的企业涌入这个市场竞争。
在激烈的竞争中,只有不断创新,提高产品质量和技术含量,才能在市场中占据一席之地。
新型纺纱技术范文

新型纺纱技术范文随着科技的不断发展,纺织行业也在不断进步和创新。
新型纺纱技术的出现,为纺织品的生产提供了更高效、更节能、更环保的方法。
下面将介绍几种新型纺纱技术。
一、无纺布纺纱技术无纺布是一种新型的纺织品制造材料,它是通过纤维材料的单根纤维或纤维的网状物重新组装制成,而不经过纺纱和织造的传统纺织工艺。
与传统纺织品相比,无纺布具有较好的透气性、柔软性、防水性和抗菌性能。
无纺布纺纱技术主要包括干法纺、湿法纺和熔喷纺。
1.干法纺:干法纺是指将纤维原料通过风力或机械力使其悬浮在空气中,再经过静电或压力作用形成网状结构,然后通过加热或涂覆等工艺使其定型。
这种纺纱技术具有操作简便、生产效率高、成本低的特点。
2.湿法纺:湿法纺是将纤维原料加入到溶剂或溶液中,经过溶解、混合和过滤等处理后,通过喷细流的方式使纤维得以凝聚成片状纺丝。
湿法纺纱技术具有纤维均匀、纺丝速度快、纱线质量稳定的特点。
3.熔喷纺:熔喷纺是将熔融的纤维原料从微细孔喷射出来,经过凝结和拉伸等过程形成纤维丝,然后通过集束、冷却和拉伸等工艺使其定型。
熔喷纺纱技术具有纺纱速度快、成本低、纤维之间的结合力强的特点。
二、空气动力纺纱技术空气动力纺纱技术是一种通过高速气流将纤维原料进行纺丝的技术。
空气动力纺纱技术具有操作简单、纺纱速度快、纤维短节短的特点,适用于生产短纤维纱线和造粒丝等纤维产品。
通过调节气流速度和纤维原料的喷射角度,可以控制纺丝过程中纤维的拉伸和取向。
三、湿旋杯纺纱技术湿旋杯纺纱技术是一种通过旋转的杯状结构将纤维原料沉积在杯底的纺纱技术。
湿旋杯纺纱技术具有纺纱速度快、纤维稳定性高的特点,适用于生产高强度和高弹性的纤维纱线。
湿旋杯纺纱技术的关键是通过旋转底部的孔洞使纤维原料被拉伸和拉断,形成纤维丝。
四、气流喷射纺纱技术气流喷射纺纱技术是一种通过高速气流将纤维原料进行纺丝的技术。
气流喷射纺纱技术具有纺纱速度快、纤维耐磨性强的特点,适用于生产耐磨性和耐拉伸性要求较高的纤维纱线。
纺纱新技术发展现状及趋势

纺纱新技术发展现状及趋势摘要探讨纺纱新技术的发展现状及趋势。
分析了近年来环锭纺纱新技术和新型纺纱新技术的发展现状,综述了环锭纺、转杯纺和喷气涡流纺在纺纱方法、自动化智能化以及器材与专件等方面的进展,展望了纺纱新技术在全流程连续化、短流程、节能降耗、提高纺纱速度等方面的发展趋势,介绍了梳并联、细纱自动接头、超大牵伸、节能集聚纺、多级气圈、双分梳转杯纺和离心纺等新技术,并给出了对未来纺纱技术的预期。
认为:加强纺纱理论研究是纺纱新技术发展的基础,多学科特别是信息学科与纺纱结合将为纺织行业进步提供强大动力,螺旋式发展模式是纺纱新技术进步的特征。
关键词纺纱新技术;环锭纺;新型纺纱;智能化;短流程;节能纺纱活动伴随着人类文明的推进而发展。
回顾纺纱技术的发展历程,离不开开松、梳理、牵伸和加捻四大原理,目前纺纱技术也基本没有完全突破这些原理,只是在实现方式上有所区别或者在细节方面有所丰富。
从动力驱动和控制技术的角度来看,由于蒸汽机、电动机、变频技术和伺服电机等的应用,极大提高了纺纱效率和成纱质量的稳定性。
当前的纺纱产业界,环锭纺仍占主导地位,而转杯纺和喷气涡流纺也得到了迅速发展,成为新型纺纱中的主力军。
环锭纺的发展出现了集聚纺、低扭矩纺、全聚纺、聚纤纺、赛络纺和数码纺等,而新型纺纱技术中出现了静电纺、转杯纺、摩擦纺、喷气涡流纺、自捻纺和离心纺等新方法。
本文分别就环锭纺纱与新型纺纱两种体系来分析近年来纺纱新技术的进展,并展望未来的发展趋势。
1纺纱新技术的进展1.1环锭纺纱新技术的发展现状迄今为止,环锭纺依然是纺纱技术应用的主体,其优点和不足均非常明显。
环锭纺的优势体现在成纱结构合理、适纺号数范围广等方面,尤其是在特细号纱领域。
其缺点是工序长、纺纱速度受限、卷装尺寸受限、用工相对较多。
以下从3方面阐述环锭纺新技术的发展。
1.1.1环锭纺的改良技术近年来,集聚纺、低扭矩纺(假捻纺)、柔洁纺、复合纺和数码纺等技术的涌现和应用,使环锭纺纱技术得以进步与改良,成纱质量得到提高与改善。
新型纺纱1范文
新型纺纱1范文新型纺纱1范文新型纺纱技术在纺织行业中有着重要的应用。
它采用了先进的纺纱设备和工艺,通过改进纺纱的工艺流程和提高纺纱设备的性能,实现了纺纱过程中的高效率、高品质和低成本。
这种纺纱技术不仅能够满足人们对纺织品的不断提高的需求,而且还能够实现生产效益的最大化和资源的高效利用。
以下将对现代纺纱技术进行详细介绍。
首先,新型纺纱技术利用了先进的纺纱设备,如自动化纺机、智能化纺纱机等。
这些设备能够实现自动化操作,减少了人工干预,提高了生产效率。
同时,智能化设备还能够通过传感器和控制系统实时监测生产过程的各项参数,并进行自动调整,以确保纺纱的质量稳定。
此外,新型纺纱设备还具有高速度和低噪音的优点,使得纺纱过程更加快速和安静。
其次,新型纺纱技术改进了纺纱的工艺流程,提高了纺纱的效率和质量。
传统纺纱工艺中,纱线需要经过多次的拉伸和加热处理,以达到理想的纺纱效果。
而新型纺纱技术通过优化前处理和拉伸工艺,减少了纺纱过程中的中间环节,从而缩短了纺纱的周期和降低了消耗。
同时,新型纺纱技术还能够在纺纱过程中加入特殊的添加剂,改善纱线的柔软度和强度,并降低纺纱过程中的摩擦和磨损,以提高纺纱的质量。
再次,新型纺纱技术还利用了先进的纺纱材料,如高强度短纤维、空心纤维和特殊纤维等。
这些纺纱材料具有较高的强度和柔软度,能够满足人们对纺织品的不同需求。
同时,新型纺纱材料还具有较好的吸湿性和透气性,能够提高纺织品的舒适度和抗菌性。
此外,新型纺纱材料还具有较好的抗老化性能和耐磨损性能,能够延长纺织品的使用寿命。
最后,新型纺纱技术还注重环保和节能。
传统纺纱技术中,纺织品生产过程中会产生大量的废水、废气和废液等,对环境造成极大的污染。
而新型纺纱技术通过改进纺纱工艺和采用环保材料,减少了纺织品生产过程中的废物排放,并且能够将废物进行回收和再利用。
此外,新型纺纱技术还能够通过节能纺纱设备和优化能源利用,减少了能源的消耗,降低了生产成本。
(完整版)主要新型纺纱的比较
主要新型纺纱的比较1、成纱原理:转杯纺依靠调整回转的纺杯,将纱尾贴紧在纺杯内壁聚槽内,而头端为引纱罗拉握持并连续输出加捻成纱。
喷气纺靠两只喷嘴喷射相反方向的回旋气流,对由牵伸装置输出的须条先加捻后解捻,表面纤维形成包缠成纱。
摩擦纺一般用两只同向回转的摩擦元件,对其楔形区的纤维施加摩擦力偶,使纤维束滚动而加捻成纱。
2、成纱截面中纤维根数不同:喷气纱中最少纤维根数略高于环锭纱,可纺中低线密度纱;摩擦纺和转杯纺中的最少纤维根数较多。
3、对纤维性能要求不同:影响转杯纱强力的主要因素是纤维的强力和线密度,摩擦纱则是纤维的摩擦因数和强力。
4、纺纱速度和成纱线密度:环锭纺的可纺线密度覆盖面最广,但产量太低,各种新型纺纱的纺纱速度都比环锭纺高,但可纺线密度有局限性5、新型特点:新型纺纱取消了锭子、筒管、钢领、钢丝圈等加捻卷绕元件,并将加捻和卷绕作用分开完成,具有产量高,细纱机的产量取决于锭子的速度,而锭速的提高,一方面受钢丝圈速度的限制,另一方面受气圈张力的限制;卷装大,环锭细纱机上增大卷装的途径是增加筒管长度和加大钢领直径,但筒管加长则气圈高度加长,钢领加大则钢丝圈线速度增大,这些都会导致断头增多,而新型纺纱方法将加捻和卷绕分开进行,可直接纺成筒子纱;工艺流程短,新型纺纱采用条子喂入,直接纺成筒子纱,省去粗纱、络筒两道工序。
转杯纺1、原理:纺杯高速旋转,纺杯内便产生离心力,离心力可使从分流腔转移到纺杯内的棉纤维产生凝聚而成为须条,须条被加捻后便成为纱条。
2、工艺过程:条子从条筒中引出送入喂给罗拉,喂给罗拉与喂给板将条子向前输送,经分梳辊分梳成单纤维,被补风口和引纱管的气流吸入纺纱杯,沿纺纱杯壁滑入凝聚槽形成凝聚须条,由于纺纱杯高速回转产生的离心力使引纱纱尾贴附于凝聚槽面而与须条连接,并被纺纱杯摩擦握持而加捻成纱。
3、转杯纱结构与性能:转杯纱由纱芯与外包缠纤维两部分组成,内层的纱芯比较紧密,外层的包缠纤维结构松散;环锭纱没有纱芯,纤维在纱中大多呈螺旋线排列。
2024年纺纱行业市场分析及投资前景预测
投资风险评估:投资者需关注政策法规、原材料价格波动、汇率变 化等因素对纺纱行业的影响,合理规避投资风险。
PART 04
纺纱行业政策环境分析
18
政策环境对行业的影响
政策支持:促进纺纱行业的技术 创新和产业升级
贸易政策:影响纺纱行业的出口 和国际竞争力
添加标题
添加标题
添加标题
添加标题
环保政策:推动纺纱行业绿色发 展,加速淘汰落后产能
环保政策风险:随着环保意识的提高,国家对纺织行业的环保要求越来 越严格,企业需加大环保投入,可能会增加生产成本。
汇率风险:纺纱行业出口型企业面临汇率波动的风险,需关注国际经济 形势和汇率走势,采取有效的汇率风险管理措施。
投资策略建议
关注纺纱行业的技术创新和产品升级 深入研究纺纱行业的市场需求和竞争格局 投资纺纱行业的优质企业和品牌 关注纺纱行业的政策支持和市场环境变化
YOUR LOGO
2024年纺纱行 业市场分析及投 资前景预测
XX,A CLICK TO UNLIMITED POSSIBILITES
汇报人:XX
目录
01 纺 纱 行 业 概 述
02
2024年纺纱行业市场分 析
03 纺 纱 行 业 投 资 前 景 预 测
04 纺 纱 行 业 政 策 环 境 分 析
发展趋势:随着环保要求的提高 和技术的不断进步,纺纱行业正 在向绿色、智能、高效的方向发 展。
PART 02
2024年纺纱行业市场分 析
8
市场需求分析
2024年纺纱行业市场需求将保持稳定增长,主要得益于纺织品需求的不断扩大和消费升级的推动。
随着全球经济的逐步复苏,国际市场需求也将逐步回暖,为纺纱行业提供了更广阔的市场空间。
纺纱智能化的技术进步与未来发展趋势
纺纱智能化的技术进步与未来发展趋势纺纱智能化是指利用现代科技手段,将纺纱过程中的各个环节与设备进行信息化、自动化、智能化改造,以提高生产效率、节省能源、降低成本、提高产品质量。
目前,纺纱智能化技术正在取得突破性进展,并且在未来有着广阔的发展前景。
首先,纺纱智能化技术在生产效率方面的进步是显而易见的。
传统的纺纱过程中,需要大量的人工操作,生产效率低下。
而纺纱智能化技术的应用使得生产过程中的各个环节实现了自动化操作,大大提高了生产效率。
例如,智能化的纺纱机器人能够自动进行纱线排列、纺纱和清洗等工作,不仅提高了生产速度,还严格控制了产品质量。
其次,纺纱智能化技术的进步对能源的节约具有积极意义。
纺纱过程中的能源消耗主要包括电力、燃气和水资源等。
通过引入智能化控制系统,可以实现对能源的精确控制,减少浪费,提高能源利用率。
例如,智能化的纺纱设备能够根据实际需要进行自动调节,降低能源的消耗,实现绿色生产。
此外,纺纱智能化技术还能够提高产品质量。
传统的纺纱过程中,由于操作人员技术水平的限制,产品质量往往难以保证。
而智能化技术能够实现对生产环节的实时监控和控制,使得产品质量更加稳定和可靠。
例如,智能化的在线检测系统能够实时对纺纱过程中的参数进行监测和调整,以保证纱线的精度和强度。
未来,纺纱智能化技术的发展趋势将主要体现在以下几个方面:一是智能化设备和系统的更加先进和完善。
随着信息技术的不断发展,智能化设备和系统将会越来越先进和智能化。
例如,纺纱机器人将逐渐实现全自动生产,能够更好地适应多品种、小批量的生产需求。
同时,智能化控制系统将会更加强大和精确,能够实时调节和优化生产过程,提高生产效率和产品质量。
二是纺纱智能化技术与大数据、云计算等新兴技术的融合。
大数据和云计算等新兴技术的应用能够实现对纺纱过程中的大量数据进行收集、分析和处理,为纺纱生产决策提供有力支持。
例如,通过对纺纱过程中的数据进行挖掘和分析,可以提高设备的运维效率,降低故障率,延长设备寿命。
- 1、下载文档前请自行甄别文档内容的完整性,平台不提供额外的编辑、内容补充、找答案等附加服务。
- 2、"仅部分预览"的文档,不可在线预览部分如存在完整性等问题,可反馈申请退款(可完整预览的文档不适用该条件!)。
- 3、如文档侵犯您的权益,请联系客服反馈,我们会尽快为您处理(人工客服工作时间:9:00-18:30)。
.对几种新型纺纱的分析比较及其应用发展前景的看法东华大学周慈念本文所讲的新型纺纱是指成纱原理与成纱的主要机构以及其成纱结构(指单纱结构)不同于传统环锭纺纱的新型纺纱方法。
而基本原理与环锭纺相同的集聚纺,和与纺制类似股线或缆绳结构的赛罗纺与索罗纺、以及化纤长丝与细纱交捻的赛罗菲纺等纺纱技术就不属此围。
即使符合以上条件但实践证明受技术关键所制约而没有发展应用前景的静电纺纱、涡流纺纱(涡流管凝聚加捻)也不在其。
自上世纪六十年代以来,以转杯纺纱为代表的各种纺纱新技术开始面世。
其中到目前为止已被广泛应用或已局部应用、或有应用发展前景的新型纺纱主要有转杯纺纱、喷气纺纱、喷气涡流纺纱和摩擦纺纱等。
本文就以上几种新型纺纱技术的特点、应用围和今后发展前景做些分析比较,谈谈个人的看法与大家一起探讨。
通过分析探讨必将有利于我国纺机制造企业与纺织生产企业正确决策其今后技术、设备和产品开发的方向。
由于转杯纺纱已比较广泛应用于生产,以及全国会议上国外企业都已进行了较多的技术交流。
喷气纺纱也通过国外企业与学者的报告,大家都有所了解,在这里就不多做赘述,只做相互比较之用。
对喷气涡流纺纱由于国尚未有MVS 这种机型的机器引进,过去国虽然也有涡流纺纱研究与生产如天津纺织研究所已形成过中试车间,还有上棉三十一厂等开发应用过。
但其机构、原理、成纱品质、应用围就不可与现在的MVS 机同日而语。
所以对MVS 这种喷气涡流纺纱就须在文中略加介绍并作些分析比较。
另外对过去已引进过并已有国产化设备的摩擦纺纱技术也多作些介绍。
因为它在这十多年中已被大家所忽视,但我认为它有它的特点与它的应用围,是有一定发展前景的,完全可以在新型纺纱发展应用中占有一席之地的。
一、纺纱原理与机构1. l 转杯纺纱转杯纺纱是属于自由端纺纱原理。
纤维条从喂入到加捻点之间必须是不连续的,否则就是假捻加不上捻度成不了纱。
就无法实现高速与大卷装目的。
它是依靠喂给与分梳机构实现纤维条分离成不连续的纤维流,又通过气流将纤维流输送到转杯实现纤维与气流的分离。
纤维再集合成连续须条,籍转杯回转而加捻成纱。
由于纤维在抵达转杯并在其壁上加速向下滑移,对纤维的伸直度有一定的改善,同时在引出纱条时又要承受转杯的惯性离心力,所以有一定的纺纱力,才使成纱强力有一定的保证并带来一些成纱结构上的特点。
1. 2 喷气纺纱喷气纺纱是非自由端纺纱原理即是连续纺纱。
但又要达到成纱加捻和卷绕作用与机构分开实现高速与大卷装这一新型纺纱共同的目的。
其关键是如何使纱条获得捻度和强力。
该成纱的捻度是整个纱条还是部分纤维加捻,这是喷气纺纱方法给我们提供了对成纱捻度新的启示和认识。
其他新型纺纱大都是整个纱条获得捻度或分层获得捻度。
而喷气纺纱主要是头端离开罗拉钳口而尾端尚被握持的这部分所谓“头端自由纤维”依靠喷嘴的旋转气流被包缠到纱芯上获得“包缠捻度”而成纱。
采用二级喷嘴主要是利用第二级喷嘴与第一级喷嘴气流旋转方向相反且旋转速度(退捻力矩更强)较大的作用。
使被第一级喷嘴作用下初始包缠的纤维在通过第二级喷嘴后在退捻方向与初始包缠方向一致的情况下包缠更紧,因而成纱强度就更提高了。
1. 3 喷气涡流纺纱本人认为喷气涡流纺纱原理主要是喂入纤维与加捻点结合在一起而获得真捻的一种新的纺纱方法。
根据获得真捻的原理和方法可以有三种:l、喂入端喂入纤维与加捻点结合在一起而加捻成纱方法,MVS 纺纱基本上属于此方法。
2、喂入端与加捻点之间须条是断裂成纤维流,而纤维再凝聚到加捻点然后加捻成纱的方法,即我们所称的自由端纺纱方法。
3、加捻点与卷绕端结合在一起的加捻成纱方法,即传统的环锭纺纱方法。
由于至目前为止,国尚未引进 MVS 设备,因此不能清楚了解该喷嘴加捻的具体装置机构。
现仅根据其在美国申请的专利上的机构介绍,作些纺纱原理上分析。
该装置的机构主要特点我认为是须条喂入喷嘴的装置,见图 1 右部分。
图1 喷气涡流纺纱喷嘴装置示意图此乃带有斜面又偏转一角度并在中心有一针状物的喂入部件,这是关键部分。
因为进入喷嘴后须条依靠压缩空气切向涡流将此须条加捻时,则捻度受阻(一是针状物作用,二是偏转产生捻陷作用)就不易向前罗拉钳口传递,就不会造成假捻区。
同时须条与针状物接触在向下引出时有摩擦阻力,对纱条加捻力及纤维伸直有利,也即对成纱强力有利。
由于毕竟须条边缘纤维会受气流影响可能有少量纤维随加捻而包缠在纱体上。
图中空心锭(空气轴承压缩空气传动)机构。
据介绍此空心锭可转也可不转。
那么它起什么作用呢?我认为一是起引导管作用。
二是它的头端组成加捻区气室,同时对纱条有一定附加摩擦力矩作用。
对所纺不同纤维因其摩擦系数大小不同,引纱力也会因此而不同。
那么其转与不转也可以起一个调节力作用。
总的我认为此装置的关键作用是前面的喂入部件。
使喂入端纤维进入加捻点而成为真捻纺纱。
以上只是我个人的分析,正确的结论还须通过科学实验来认证。
今后有条件的话,可以用光学玻璃与有机玻璃结合按实际喷嘴装置机构仿制,进行有色纤维纺纱试验,然后采用高速摄影方法拍摄纺纱动态过程。
再用慢速放映结合照片观察那么就可对其纺纱原理做出正确的结论。
在这里我想提出一个问题与大家探讨,那就是不同纤维例如化纤纯纺与棉的纯纺或其混纺,由于化纤纤维长度与棉纤维的整齐度不同,此装置的加捻点与牵伸装置的前罗拉钳口之间隔距是否要做些调节?否则纱条加捻后,成纱强度即纱体外包缠纤维数量的多少是否会受影响?从村田公司资料上介绍的几个成纱样品上看,纺纯棉主要还是精梳纱及混纺纱,我认为装置对纤维长度与整齐度还是有一定要求的。
1. 4 摩擦纺纱摩擦纺纱首先是由Ernst Fehrer 博士创立于1953 年的 FEHRER公司所发明研制和生产的一种属自由端纺纱原理的新型纺纱方法。
该设备命名为 DREF系列的摩擦纺纱机。
至目前为止已生产了 DREF2、 DREF3 和 DREF2000 型这三种机型。
后两种机型可纺包芯纱和一些花色纱。
但这些花色纱在原理上已属包缠纺纱。
该纺纱头由 4 个部分组成:喂入机构、开松机构、凝聚加捻尘笼和卷统部分。
见图2。
图 2 摩擦(尘笼)纺示意图该方法特点是一对起凝聚与加捻作用的尘笼(打成上千万小孔的滚筒),尘笼装有针对一对尘笼楔形部分的吸嘴。
依靠外界风机在此处产生负压,使开松后向下输出的纤维流在该处沿尘笼轴向凝聚(留下纤维,分离气流)同时籍同向旋转的尘笼表面与须条表面产生的摩擦力矩将凝聚须条加上捻度而成纱。
如果是在尘笼楔形握持线上通过长丝或纱线,那么凝聚的纤维就包在外面成为包芯纱。
另外还可加装超喂装置和加装由计算机控制的牵伸装置间歇或快慢变速地喂给包覆纤维,由此可纺成起圈、结子、竹节等花色纱。
至于英国制造的Master-spinning摩擦纺纱机,由于原理相同,机构略有不同,它希望能够纺较细的纱,看来要达到这个目标是比较难实现的。
所以至目前还未见有新的报导和机器展出或生产应用。
二、适纺原料与纱支和速度以上几种新型纺纱适纺的原料和纱支及纺纱速度围可见表1。
纱支与纺纱速度的比较可见图 3。
表 1 几种新型纺纱的比较名称转杯纺纱喷气纺纱喷气涡流纺纱摩擦纺纱适纺原料天然纤维涤棉混纺涤/粘、纯棉可纺所有天然、人造、再生和人造纤维涤纶 100%及其他化纤/棉特种纤维再生纤维化纤纤维长度44纤维长度10~15 mm 及以上纤维的混纺纤维长度51mm mm 以下纤维长度 10~60mm以下适纺纱支170~10tex29~7.25tex29~10tex DREF2 型 100-3952tex (Ne3.5~60)(Ne20~80)(Ne20~60)(Nm0.25~10)FS2/92 国产机 (Nm0.25~15)DREF3 型 33.3~166.6tex包芯纱450)400ni350M V S m/m300(度250速200M J S 纱纺150DERFOE-Rotor1005005101520253035404550556065707580(Ne)0.2515纱支(Nm)图 3 几种纺纱方法的适纺纱支和速度三、成纱结构与特性3. l 转杯纱与尘笼纱结构同属自由端纺纱原理的转杯纺纱与摩擦(尘笼)纺纱其成纱结构基本是相同的。
用相同原料的条子分别纺成转杯纱与尘笼纱,并通过浸没描迹法观察示踪纤维在成纱中的几何排列形态,根据不同形态加以分类,其结果如表 2 所示。
表 2各类示踪纤维的根数百分率纤维类别尘笼纱转杯纱棉 67%涤 33%棉 67%涤 33%圆锥形螺旋线纤维0.65 1.97 2.34 3.23圆柱形螺旋线纤维 3.27 1.3214.0216.77属前打圈或前弯勾9.158.557.027.743.92 3.294.09 3.23于中打圈或中屈曲圈后弯钩 3.27 3.959.3614.19锥5.8814.47 4.68 1.94形前、后弯勾或前、后打圈、前弯钩,中打圈或中屈曲8.50 6.58 1.75 1.29圆柱后弯钩,中打圈或中屈曲 3.27 1.32 2.92 1.94形前、后弯钩,中打圈 4.58 3.95 1.170.65螺旋前端卷缠,后端正常转移 3.27 1.32 1.75 1.29线后端卷缠,前端正常转移 1.3108.19 2.58,但前卷缠,中打圈或中屈曲 1.31 1.320 2.58头前卷缠,中打圈或中屈曲,后弯钩00.6600、尾前卷缠,后弯钩000.58 1.29端前弯钩,后卷缠00.66 2.340有各前弯钩,中卷缠00 2.340种中卷缠00 1.750缺陷前、后卷缠0.650.66 2.340.65的前、后卷缠,中打圈0.650.6600纤维合计45.7647.3950.2839.37前对折 3.27 2.63 3.51 6.45不后对折0 1.97 2.92 3.87规纠缠(整理卷缠)纤维32.6831.5810.5310.97则外包或包缠纤维7.197.8916.3719.35纤维平直纤维7.19 5.2600合计50.3349.3333.3340.64从表中可见,对成纱强力起主要作用的圆锥形螺旋线纤维和圆柱形螺旋线纤维,转杯纱都多于尘笼纱,而对折、平直、纠缠、打圈等不规则纤维转杯纱则少于尘笼纱。
(与转杯纱相比,尘笼纱表面没有包缠纤维而存在着一定数量没有转移的平直纤维)所以尘笼纱的强力比转杯纱低。
从成纱捻度分析,两种纱都是捻度分层结构,即成纱截面各层捻度是不相同的;总的是外层捻度少而向层逐渐增多,呈外松紧的结构。
分析以上两种自由端纺纱方法的成纱结构,为什么尘笼纱中不规则纤维多,强力较低,主要是凝聚机构不同而造成的。
转杯纺虽然使分离的纤维要保持定向伸直凝聚也难,但至少在转杯滑移到凝聚槽并以凝聚槽的线速度运动,相比输送气流中的纤维速度还是加速的。