焦化行业工艺流程图
煤炭焦化过程及工艺流程

煤碳焦化厂生产工艺及流程一、焦系统工艺流程图煤塔→振动给料机→捣固装煤车→荒煤气→上升管→桥管→集气管→吸气管→气液分离器→回收分厂↑→ 焦炉→罩式拦焦车→熄焦车→熄焦塔→凉焦台→焦1皮带→↑ ↘↓推焦车↘↑ ↓ ↓消烟除尘车→除尘通风机→ 烟囱→焦3皮带→焦4皮带→单层振动筛→焦5皮带→分料器→焦6皮带↓ ↓ ↓↓可逆输送机↓ ↓ ↓中焦焦仓←25~40㎜级←双层振动筛焦8皮带大焦焦仓↙↓ ↓小焦焦仓←10~25㎜级<10㎜级→焦沫仓>40㎜级大焦焦场→汽车外运二、鼓冷系统工艺流程从焦炉来的荒煤气、氨水、焦油首先在气液分离器进行气液分离,分离出的粗煤气分别进入循环池;分离下来的焦油、氨水和焦油渣一起进入进入机械化氨水澄清槽。
离开气液分离器的煤气进入横管式初冷器,初冷器分上、下两段,在初冷器上段,用循环水间接冷却煤气冷却至45℃,再经下段制冷水间接冷却,使煤气进一步降温至22℃,冷却后的煤气进入旋流板捕雾器,最后进入煤气鼓风机进行加压,加压后煤气进入电捕焦油器,捕集焦油雾滴后的煤气,送往脱硫及硫回收工段。
送往用户使用。
初冷器的煤气冷凝液分别由初冷器上、下段流出,分别经初冷水封槽进入上、下段冷凝液循环槽,由冷凝液循环泵送至初冷器上、下段喷淋,吸收净化煤气中的奈;苯;酚等,多余部分下段冷凝液循环泵外排气液分离器前荒煤气管上或焦油氨水机械分离槽内。
由气液分离器来的氨水焦油混合液自流入机械化氨水澄清槽,在槽内经重力分离作用,上层为储藏的的氨水,连续满流至循环氨水槽后,经循环氨水泵加压后,送焦炉桥底部水管处喷洒冷却荒煤气。
多余的氨水去剩余氨水槽,用剩余氨水泵送至脱硫工段进行蒸氨。
中部为焦油,经焦油液位调节器连续压入焦油中间槽,当达到一定液位时,用焦油泵将其送至焦油槽,焦油需外售时,用焦油泵送往装车台装车外售。
焦油渣则沉淀于澄清槽底部,经链条刮板机连续刮出槽外。
定期送往煤场掺混炼焦。
三、循环水流程由循环水池来的循环水经循环水泵加压后分别供给横管初冷器一段、风机冷却器、预冷塔换热器装置,氨水废水强制冷却器、氨酚冷却凝缩器,粗苯冷凝冷却器,一段油水换热器、空压站。
焦化行业工艺流程图

关键词:焦化行业烧结行业矿冶行业解决方案1。
焦化行业工艺流程焦化行业工艺流程如图1.焦炉煤气(贫煤气或高炉煤气)从焦炉底孔吹入燃烧室燃烧(焦炉煤气下喷,高炉煤气混合煤气侧喷),对相邻炭化室进行加热,并采用交换机进行分时段送气切换;将粒度为〈3mm的配合煤料经加煤车送入1000℃左右炭化室进行隔绝空气加热,入炉煤在相邻燃烧室高温加热下,经高温干馏结焦形成焦炭,推焦机将成熟的焦炭从炭化室中推出,经过拦焦车,落到熄焦车的车箱中,熄焦车将炽热的焦炭(约1000℃左右)拉到熄焦塔下,用水喷洒熄焦,使红焦熄灭,温度降到300℃左右,同时控制焦炭水分在5±2%的范围内,熄完焦后,熄焦车将焦炭拉走并放至晾焦台上,再经皮带运走,干熄焦则由电机车将灼热焦炭运往干熄焦炉,用氮气置换热能,经锅炉换热,带汽轮机发电,冷却后的焦炭由旋转密封阀排除,由皮带运出;高温干馏出来的约700℃左右的荒煤气,进入上升管,经桥管氨水喷嘴连续不断地喷洒热氨水(75℃左右),使荒煤气迅速冷却至80~100℃,并与其他炭化室的荒煤气汇集一起经集气管排吸气管、气液分离器、初冷器、鼓风机加压、经产品回收工段净化后送给用户,另外还有煤焦油及苯等副产品。
2. 焦化行业控制方案a。
顺序控制方案主要为设备顺序控制,用于实现整个机组中各主要设备的监视操作、顺序启停和联锁保护等功能.焦炉加热系统换向工艺:焦炉煤气加热换向都要经历3个基本过程即:关煤气-空气与废气进行交换—开煤气;两次换向时间间隔根据加热制度、煤气种类、格子砖的清洁程度等具体情况而定;焦炉公用一个煤气总管时,为防止煤气压力变化幅度太大,影响焦炉正常加热,故几座焦炉不能同时加热,一般需相隔5min以上。
b。
联锁控制方案在焦化行业中主要的设备联锁有鼓风机联锁,油泵联锁,电捕箱联锁等,具体的联锁方案如图2所示。
c。
模拟量控制方案主要是完成整个机组的参数控制,将所有需要调整的模拟量参数稳定在运行所需要的范围内,减轻操作员的劳动强度,从而实现系统的自动控制。
焦化厂详细工艺流程

共八十三页
前
言
马鞍山钢铁股份有 限公司是一个拥有烧结、 焦化、轧钢、动力等机 构。年产200万吨综合 生产能力 的 (shēnɡ chǎn nénɡ lì) 特大型钢铁联合企业。 该企业初创于50年代, 60年代被盛誉为“江 南一枝花”。
共八十三页
1、焦化厂工艺(gōngyì) 简介
区分。
共八十三页
1.5 我国煤的分类(fēn lèi)
分类指标: (1)干燥无灰基挥发分Vdaf;
(2)粘结指数G (3)胶质层最大厚度y (4)奥亚膨胀度b。
煤类的划分(huà fēn)和编码 种类煤用两位阿拉伯数码表示。十位数系按煤的挥发分分组,无烟煤为0,
烟煤为1~4,褐煤为5。个位数,无烟煤类为1~3,表示煤化程度; 烟煤类为1~6,表示粘结性;褐煤类为1~2,表示煤化程度。
21pa大部分送总厂作为燃气使用另一部分送到石灰作业区作为石灰窑用燃料我厂气柜为浮顶式气柜有效高度为212m安全高度为718m煤气来自洗脱苯煤气去总厂煤气去石灰气柜经煤压机气柜加压站流程图初冷器气液分离器电捕焦油器鼓风机脱硫塔饱和器终冷塔气柜煤气来自焦炉液相去机槽气相冷凝液去机槽净煤气外送去总厂煤气去石灰回炉煤气去管式炉煤气总流程图洗苯塔第5部分炼焦主要产物和产品5炼焦主要产物和产品吨煤干基可以生产
共八十三页
第2 部分
备煤工艺
共八十三页
备煤工艺(gōngyì)
备煤:对进厂的洗精煤进行处理,以达到炼焦要求,通常把原料煤 在炼焦前进行的工艺处理过程称为备煤工艺过程。这个过程是在 备煤作业区来进行完成的。主要经过堆放、配合、粉碎、调湿、 除杂等一系列过程使之达到炼焦要求之后,通过皮带被输送到煤 塔供炼焦作业区使用。
焦化厂工艺流程文字叙述及流程图

备煤炼焦所用精煤,一方面由外部购入,另一方面由原煤经洗煤后所得,洗精煤由皮带机送入精煤场。
精煤经受煤坑下的电子自动配料称将四种煤按相应的比例送到带式输送机上除铁后,进入可逆反击锤式粉碎机粉碎后(小于3mm占90%以上),经带式输送机送至焦炉煤塔内供炼焦用。
炼焦装煤推焦车在煤塔下取煤,捣固成煤饼后,按作业计划从机侧推入炭化室内。
煤饼在炭化室内经过一个结焦周期的高温干馏,炼成焦炭并产生荒煤气。
炭化室内的煤饼结焦成熟后,由装煤推焦机推出并通过拦焦机的导焦栅送入熄焦车内。
熄焦车由电机牵引至熄焦塔熄焦。
熄焦后的焦炭卸至凉焦台,冷却后送往筛焦楼进行筛分和外运。
煤在干馏过程中产生的荒煤气汇集到炭化室的顶部空间,经上升管、桥管进入集气管。
700℃的荒煤气在桥管内经过氨水喷洒后温度降至85℃左右,煤气和冷凝下来的焦油氨水一起经吸煤气管道送入煤气回收车间进行煤气净化及焦油回收。
焦炉加热燃用的净化煤气经预热器预热至45℃左右进入地下室,通过下喷管把煤气送入燃烧室立火道,燃烧后的废气经烟道、烟囱排入大气。
冷鼓由焦炉送来的80-83℃的荒煤气,沿吸煤气管道入气液分离器。
经气液分离后,煤气进入初冷器进行两段间接冷却;上段用32℃循环水冷却煤气,下段用16-18℃低温水冷却煤气,使煤气冷却至22℃,然后经捕雾器入电捕焦油器除去悬浮的焦油雾后进入鼓风机,煤气由鼓风机加压送至脱硫工段。
在初冷器下段用含有一定量焦油、氨水的混合液进行喷洒,以防止初冷器冷却水管外壁积萘,提高煤气冷却效果。
由气液分离器分离出的焦油氨水混合液自流入机械化氨水澄清槽,进行氨水、焦油和焦油渣的分离。
分离后的氨水自流入循环氨水中间槽,用泵送到焦炉集气管喷洒冷却荒煤气,多余的氨水(即剩余氨水)送入剩余氨水槽,焦油自流入焦油中间槽,然后用泵将焦油送至焦油贮槽,静置脱水后外售,分离出的焦油渣定期用车送至煤场掺入精煤中炼焦。
脱硫来自冷鼓工段的粗煤气进入脱硫塔下部与塔顶喷淋下来的脱硫液逆流接触洗涤后,煤气经捕雾段除去雾滴后全部送至硫铵工段。
焦化厂生产工序及工艺流程图

焦化厂生产工序及工艺流程焦化厂的生产车间由备煤筛焦车间、炼焦车间、煤气净化车间及相配套的公用工程组成。
产品焦炭和副产品煤焦油、硫膏、硫铵、粗苯等外售。
焦炉煤气经净化后,部分返回焦炉和化产系统作为燃料气,剩余煤气全部外供发电用燃料气。
焦化厂主要生产工序包括:备煤,炼焦、熄焦,筛贮焦,冷鼓、电捕、脱硫及硫回收、蒸氨、硫铵、洗脱苯等工序。
洗精煤—备配煤—炼焦—熄焦—筛贮焦—煤气净化及化产回收—煤气外送。
生产工序如下图所示:外供燃料气1. 备配煤工序备配煤是焦化工程的第一道工序,主要是负责洗精煤的贮运、配煤、粉碎、输送,为焦炉提供合格原料。
备配煤工序主要由储煤场及地下配煤槽、粉碎机楼和胶带机通廊及转运站等组成。
2. 炼焦、熄焦工序炼焦、熄焦是焦化工程的第二步工序,也是最核心的工艺,主要负责将合格的配合精煤采用高温干馏工艺炼成焦炭,并采用湿法熄焦工艺将焦炭熄火降温。
炼焦过程副产荒煤气。
焦化厂炼焦、熄焦工序包括1#、2#焦炉、煤塔、间台、端台、炉门修理站、推焦杆及煤槽底板更换站、装煤出焦除尘地面站、熄焦系统、熄焦塔、晾焦台、粉焦沉淀池、熄焦泵房、烟囱及相应配套焦炉机械。
3. 筛贮焦工序筛贮焦是焦化工程的第三步工序,筛贮焦工序主要负责将炼焦工序熄火的焦炭进行筛分、输送、储存。
焦炭筛分为>35mm、35-15mm、<15mm三个级别外售。
4. 冷凝鼓风工序冷凝鼓风工序的主要任务是对来自焦炉的荒煤气进行冷凝冷却、加压,脱除煤气中的萘及焦油雾,焦油与氨水的分离贮存及焦油、循环氨水、剩余氨水的输送等。
5. 脱硫及硫回收工序脱硫及硫回收工序的任务是将来自冷凝鼓风工序焦炉煤气中所含各种硫化物和氰化物脱除,使煤气中的硫化氢含量脱至200mg/Nm3以下送出。
浮选出的硫泡沫经熔硫釜连续熔硫,副产硫磺外售。
6. 蒸氨工序蒸氨工序的任务是将冷鼓来的剩余氨水在蒸氨塔中用蒸汽蒸出,蒸出的氨汽经氨分缩器冷却,冷凝下来的液体入蒸氨塔顶作回流,未冷凝的氨汽用循环水冷凝成浓氨水送脱硫工序作为脱硫补充液。
焦化车间各工段工艺图

各种警示标识、告知卡、公告栏等的制作
4.03
危害治理费用
粉尘、噪声的治理改造
100.74
职业卫生评价费
职业卫生预评价/控制效果评价
22.5
应急救援设施费用
呼吸器、防毒面具、应急灯、防毒口罩、急救箱、应急通讯和交通设施
15.47
个人防护用品
预防粉尘、程
表14职业卫生专项经费调查表
项目
内容
经费(万元)
备注
防尘设施
除尘器/除尘设施
90.73
防毒设施
报警仪、巡检时的监护仪及其他设施
1.08
高温降温
接触危害补贴、防暑降温药品、其他
8.33
职业卫生培训、教育
上岗前、在岗期间培训和宣传培训资料
5.46
职业健康体检
体检费用
10.7
图5-2备煤工艺流程图
图5-3炼焦工艺流程图
图5-4炼焦工艺流程图
图5-5筛焦工艺流程图
图5-6熄焦和筛焦工艺流程图
图5-7化产工艺流程
图5-7-1冷鼓工艺流程图
图5-7-2冷鼓水处理工艺流程图
图5-8脱硫工艺流程图
图5-9硫胺工艺流程图
图5-10粗苯工艺流程
图5-11生化工艺流程图
图5-12锅炉工艺流程
合计
267.29
焦化厂工艺流程文字叙述及流程图
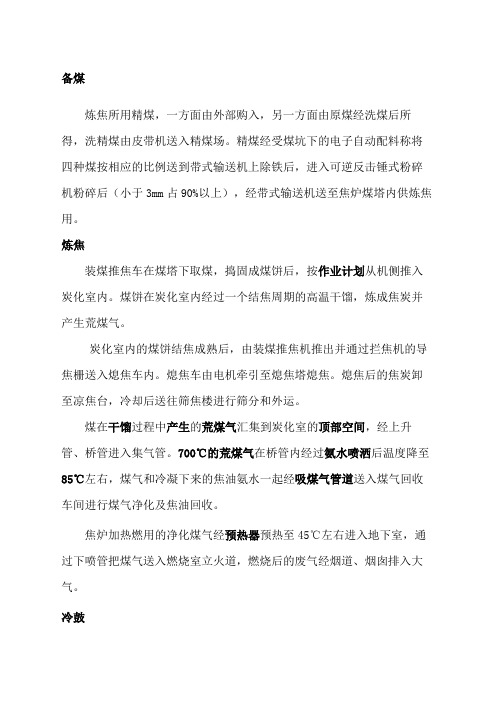
备煤炼焦所用精煤,一方面由外部购入,另一方面由原煤经洗煤后所得,洗精煤由皮带机送入精煤场。
精煤经受煤坑下的电子自动配料称将四种煤按相应的比例送到带式输送机上除铁后,进入可逆反击锤式粉碎机粉碎后(小于3mm占90%以上),经带式输送机送至焦炉煤塔内供炼焦用。
炼焦装煤推焦车在煤塔下取煤,捣固成煤饼后,按作业计划从机侧推入炭化室内。
煤饼在炭化室内经过一个结焦周期的高温干馏,炼成焦炭并产生荒煤气。
炭化室内的煤饼结焦成熟后,由装煤推焦机推出并通过拦焦机的导焦栅送入熄焦车内。
熄焦车由电机牵引至熄焦塔熄焦。
熄焦后的焦炭卸至凉焦台,冷却后送往筛焦楼进行筛分和外运。
煤在干馏过程中产生的荒煤气汇集到炭化室的顶部空间,经上升管、桥管进入集气管。
700℃的荒煤气在桥管内经过氨水喷洒后温度降至85℃左右,煤气和冷凝下来的焦油氨水一起经吸煤气管道送入煤气回收车间进行煤气净化及焦油回收。
焦炉加热燃用的净化煤气经预热器预热至45℃左右进入地下室,通过下喷管把煤气送入燃烧室立火道,燃烧后的废气经烟道、烟囱排入大气。
冷鼓由焦炉送来的80-83℃的荒煤气,沿吸煤气管道入气液分离器。
经气液分离后,煤气进入初冷器进行两段间接冷却;上段用32℃循环水冷却煤气,下段用16-18℃低温水冷却煤气,使煤气冷却至22℃,然后经捕雾器入电捕焦油器除去悬浮的焦油雾后进入鼓风机,煤气由鼓风机加压送至脱硫工段。
在初冷器下段用含有一定量焦油、氨水的混合液进行喷洒,以防止初冷器冷却水管外壁积萘,提高煤气冷却效果。
由气液分离器分离出的焦油氨水混合液自流入机械化氨水澄清槽,进行氨水、焦油和焦油渣的分离。
分离后的氨水自流入循环氨水中间槽,用泵送到焦炉集气管喷洒冷却荒煤气,多余的氨水(即剩余氨水)送入剩余氨水槽,焦油自流入焦油中间槽,然后用泵将焦油送至焦油贮槽,静置脱水后外售,分离出的焦油渣定期用车送至煤场掺入精煤中炼焦。
脱硫来自冷鼓工段的粗煤气进入脱硫塔下部与塔顶喷淋下来的脱硫液逆流接触洗涤后,煤气经捕雾段除去雾滴后全部送至硫铵工段。
2024版年度焦化厂详细工艺流程课件PPT共63张大纲
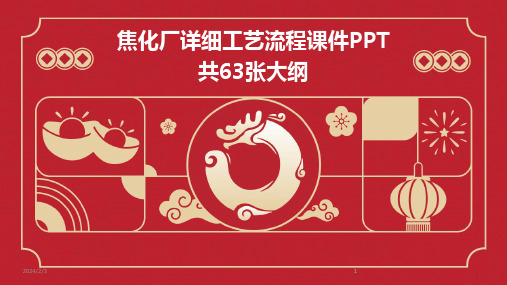
2024/2/3
14
2024/2/3
04
工艺流程详解
CHAPTER
15
原料进入生产线前准备工作
原料验收
检查原料质量、数量及规格,确 保符合生产要求。
2024/2/3
原料储存
将原料分类储存,避免混杂和污染。
原料预处理
根据生产需要对原料进行破碎、筛 分、混合等预处理操作。
16
各阶段反应过程描述及控制要点
资源利用指标
包括水资源利用率、固体废弃物利用率等,反映焦化厂资源利用情况。
经济效益指标
包括节能减排项目投资回报率、内部收益率等,反映焦化厂节能减排的经济效益。
2024/2/3
30
08
2024/2/3
总结回顾与未来展望
CHAPTER
31
本次课程重点内容总结
焦化厂工艺流程概述
介绍了焦化厂的基本工艺流程,包括原料煤的预处理、炼焦、煤气 净化、化产品回收等环节。
提高了安全生产和环保意识,认 识到焦化厂生产过程中的风险点
和防控措施。
通过实际案例分析和讨论,加深 了对理论知识的理解和掌握。
2024/2/3
33
行业发展趋势预测
焦化行业将继续向大型化、集约化方 向发展,提高产业集中度和竞争力。
新能源和可再生能源的快速发展将对 焦化行业产生一定影响,焦化厂需要 积极应对市场变化,调整产品结构和 产业布局。
2024/2/3
石油焦
辅助原料,具有高碳、低 硫、高热值等特点,可提 高焦炭质量。
生物质
可再生原料,具有低碳、 低硫、环保等特点,但热 值较低。
8
原料预处理方法与技术
煤炭破碎与筛分
将大块煤炭破碎成合适 粒度,筛分出杂质,提
- 1、下载文档前请自行甄别文档内容的完整性,平台不提供额外的编辑、内容补充、找答案等附加服务。
- 2、"仅部分预览"的文档,不可在线预览部分如存在完整性等问题,可反馈申请退款(可完整预览的文档不适用该条件!)。
- 3、如文档侵犯您的权益,请联系客服反馈,我们会尽快为您处理(人工客服工作时间:9:00-18:30)。
关键词:焦化行业烧结行业矿冶行业解决方案
焦化行业工艺流程1.
焦从焦炉底孔吹入燃烧室燃烧(焦炉煤气(贫煤气或高炉煤气)焦化行业工艺流程如图1。
,对相邻炭化室进行加热,并采用交换机进行分时段炉煤气下喷,高炉煤气混合煤气侧喷)℃左右炭化室进行隔绝空气加热,1000<3mm送气切换;将粒度为的配合煤料经加煤车送入推焦机将成熟的焦炭从炭化室经高温干馏结焦形成焦炭,入炉煤在相邻燃烧室高温加热下,拉到熄)1000℃左右(中推出,经过拦焦车,落到熄焦车的车箱中,熄焦车将炽热的焦炭约%的5±2℃左右,同时控制焦炭水分在焦塔下,用水喷洒熄焦,使红焦熄灭,温度降到300再经皮带运走,干熄焦则由电机车范围内,熄完焦后,熄焦车将焦炭拉走并放至晾焦台上,冷却后的焦炭由将灼热焦炭运往干熄焦炉,用氮气置换热能,经锅炉换热,带汽轮机发电,℃左右的荒煤气,进入上升管,经桥700旋转密封阀排除,由皮带运出;高温干馏出来的约并与其他℃,~,使荒煤气迅速冷却至80100)(75管氨水喷嘴连续不断地喷洒热氨水℃左右经产品回炭化室的荒煤气汇集一起经集气管排吸气管、气液分离器、初冷器、鼓风机加压、收工段净化后送给用户,另外还有煤焦油及苯等副产品。
焦化行业控制方案2.
a. 顺序控制方案
主要为设备顺序控制,用于实现整个机组中各主要设备的监视操作、顺序启停和联锁保护等功能。
焦炉加热系统换向工艺:焦炉煤气加热换向都要经历3个基本过程即:关煤气—空气与废气进行交换—开煤气;两次换向时间间隔根据加热制度、煤气种类、格子砖的清洁程度等具体情况而定;焦炉公用一个煤气总管时,为防止煤气压力变化幅度太大,影响焦炉正常加热,故几座焦炉不能同时加热,一般需相隔5min以上。
b. 联锁控制方案
在焦化行业中主要的设备联锁有鼓风机联锁,油泵联锁,电捕箱联锁等,具体的联锁方案如图2所示。
c. 模拟量控制方案
主要是完成整个机组的参数控制,将所有需要调整的模拟量参数稳定在运行所需要的范围内,减轻操作员的劳动强度,从而实现系统的自动控制。
(1)入初冷器煤气总管压力控制:通过调节鼓风机转速或煤气系统大循环翻板阀调节。
压力设定值通过集气管压力修正。
(2)集气管压力控制:常规的PID调节方法,调节作用较强易引起超调,并容易破坏其他炉和吸力系统的平衡,相互影响相互干扰,导致整个系统控制不能达到要求;调节作用较弱则在装煤结束和用气量发生变化后达到平衡时间较长;同时采用变PID的控制方法效果也不佳,超调和振荡依然不能很好克服。
为了解决上述问题,我们采用了变PID和模糊控制器相结合的方案,使用结果证明,该方案能较好地克服装煤结束后气压突变的状况。
方案的主要原理是根据状态和趋势在偏差较大和变化趋势较快的情况下采用模糊控制器快速输出,根据集气管压力变化自动调节荒煤气管道上的翻板开度,从而稳定集器管压力。
根据状态和趋势在偏差较小和变化趋势较慢的情况下根据控制器判断选择控制器的PID参数来微调。
(3)初冷器吸入压力自动控制:目的是保证煤气吸力稳定,从而保证集气管压力稳定,进一步保证鼓风机后续工段的压力稳定。
针对不同形式的鼓风机,该控制可通过调节鼓风机转速,或控制风机旁路(大循环)等方法来实现。
压力信号可取自初冷器入口,引入DCS,由DCS输出4~20mA信号完成自动控制。
当多炉共用一总管时,鼓风机吸入压力的设定值,通过集气管压力测量,去自动修正,把压力控制在适合集气管调节的范围内。
作为修正的多个集气管压力,可由人工手动选择。
当采用鼓风机调速时,通过设定的鼓风机吸入压力值,调节鼓风机转速。
如采用离心风机,须考虑喘振和共振控制范围较小。
(4)分烟道压力控制:目的是保证烟道的吸力稳定,达到合理的空气过剩系数,从而减少热损失,提高热效率。
根据分烟道压力变化自动调节烟道翻板的开度,稳定分烟道压力。
燃烧控制系统采用以加热煤气量作为前馈参数调节烟道吸力的方案,需考虑到废气含氧量受诸多方面因素影响。
(5)气液分离器液位控制:目的是防止冷凝液溢槽。
冷凝液含有轻质焦油和氨水,一旦该控制通过调节至初冷器前荒煤气管道上的调很难用常规方法清除。
溢出会造成环境污染,
节阀来实现。
(6)主煤气流量控制:目的是将焦炉温度控制在1250~1350℃。
根据主煤气流量变化自动调节主煤气管道上的翻板开度,稳定主煤气流量,保证焦炉温度。
在炼焦煤性质稳定的情况下,加热温度的变化会对炼焦化学产品的质量和产率产生影响。
在煤气性质稳定的前提下,通过控制燃烧室煤气流量来保证焦炉加热。
加热系统控制采用前馈控制结合炉温修正的方案,即将影响焦炉加热的主要因素如加热煤气特性、配合煤的特性和焦炉操作等纳入流量控制模块。
二烧结行业自控解决方案
随着我国冶金工业技术的迅速发展,要求冶金企业在技术装备水平方面有较大的突破,目前
DCS在烧结行业的应用已经比较成熟,许多采用DCS的企业在投产后都显示出较好的经济效益。
浙江中控技术有限公司烧结行业解决方案已在国内多家矿冶企业得到了成功应用,为矿冶行业用户带来了显著的社会与经济效益。
1. 烧结行业工艺简介
烧结是在铁矿粉中配入适量的熔剂和燃料,在烧结机上点火燃烧,通过燃烧的高温作用产生一定量的液相,把其他未溶化的烧结料颗粒粘结起来,冷却后成为多孔块状烧结矿。
其工艺流程为:铁矿粉、燃料、熔剂和其他料种按一定比例混和后加到热返矿上,再和二次配煤粉混和,配好的原料按一定配比加水,送给料槽,再到烧结机,点火后烧结矿在台车上烧结,烟气由抽风机自上而下抽走,烧结终了的烧结块由机尾落下,破碎后经筛分和冷却,筛上物送到料仓或高炉,筛下物作为返矿和铺底料重新烧结。
2. 烧结行业控制方案
烧结工艺过程的控制系统主要包括以下几部分:
(1)自动配料控制(定比值控制):精确配料在整个烧结控制中及其重要,它是烧结质量好坏的前提。
配料自动控制包括精矿、硅砂、石灰石、生石灰、粉焦、反矿等控制。
(2)混合料湿度控制(前馈—反馈控制):包括一次混合加水控制、二次混合加水控制等。
(3)混合料料仓料位控制(进出料平衡):先计算入料量与排出量之间重量收支的偏差值,当计算偏差超过一定范围时,原料仪表调节器输出信号,改变各配料仓的排料量,使其料位处于动态平衡。
(4)铺底料料仓料位控制:使铺底料料仓的进料量与排料量平衡。
根据烧结机的速度变化来改
变铺底料带式输送机的速度作为前馈控制,由铺底料料仓设定的料位与料位传感器实测料位值的偏差经调节器的PID运算进行反馈控制。
烧结料层厚度控制:对于中小型烧结机,其厚度可以不进行横向控制,纵向控制式(5)
通过调节圆辊速度来实现,并设有手动主闸门做粗调用。
对于大型烧结机,由于台车宽,其料层厚度控制由横向均匀布料控制和纵向层厚控制两部分组成。
(6)烧结点火装置燃烧控制:通过调节点火装置煤气供给量和煤气—空气比值实现。
点火装置
燃烧控制有炉内温度控制及点火强度控制两种方式。
(7)煤气总管压力控制(单回路):送到烧结厂来的煤气压力通常是不稳定的,因而难以保证烧结点火及燃烧控制系统的正常运行。
为此在煤气总管设置一个单回路压力自动控制系统。
(8)安全信号控制系统:有煤气低压信号和自动切断系统等。
(9)工艺设备电气运转控制:根据设备之间的关系划分成若干相对独立的系统,实现每个系统
内设备之间的顺序启动、同时启动、顺序停止、同时停止、事故停止、机旁运转、设备单启单停等。
三结束语
浙江中控技术有限公司以工业自动化国家工程研究中心、工业控制技术国家重点实验室的科研积累为技术支撑,长期致力于工业自动化领域的技术研发和产业化。
目前已经形成完备的产品体系,具有为用户提供完整的工业自动化整体解决方案的能力。
公司在矿冶控制领域多年耕耘并取得了大量的成功应用案例,我们期待为矿冶行业更多的用户提供最优秀的整体解决方案与最完善的服务。