热平衡计算电阻炉
箱式电阻炉课程设计完整版
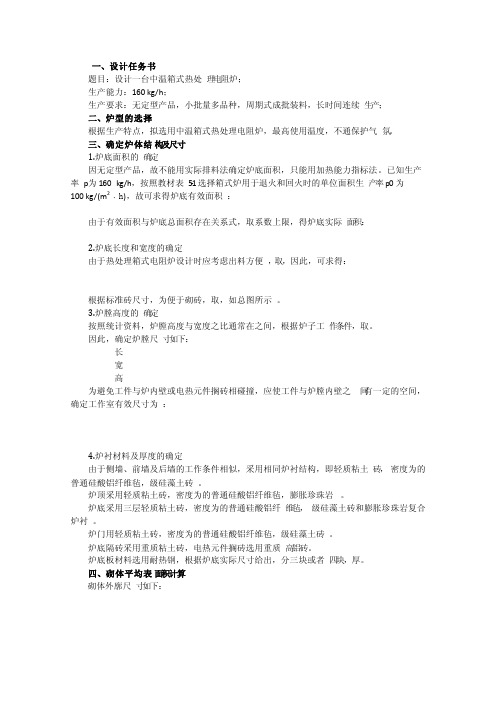
一、设计任务书题目:设计一台中温箱式热处理电阻炉;生产能力:160 kg/h;生产要求:无定型产品,小批量多品种,周期式成批装料,长时间连续生产;二、炉型的选择根据生产特点,拟选用中温箱式热处理电阻炉,最高使用温度,不通保护气氛。
三、确定炉体结构及尺寸1.炉底面积的确定因无定型产品,故不能用实际排料法确定炉底面积,只能用加热能力指标法。
已知生产率p为160kg/h,按照教材表5-1选择箱式炉用于退火和回火时的单位面积生产率p0为100 kg/(m2﹒h),故可求得炉底有效面积:由于有效面积与炉底总面积存在关系式,取系数上限,得炉底实际面积:2.炉底长度和宽度的确定由于热处理箱式电阻炉设计时应考虑出料方便,取,因此,可求得:根据标准砖尺寸,为便于砌砖,取,如总图所示。
3.炉膛高度的确定按照统计资料,炉膛高度与宽度之比通常在之间,根据炉子工作条件,取。
因此,确定炉膛尺寸如下:长宽高为避免工件与炉内壁或电热元件搁砖相碰撞,应使工件与炉膛内壁之间有一定的空间,确定工作室有效尺寸为:4.炉衬材料及厚度的确定由于侧墙、前墙及后墙的工作条件相似,采用相同炉衬结构,即轻质粘土砖,密度为的普通硅酸铝纤维毡,级硅藻土砖。
炉顶采用轻质粘土砖,密度为的普通硅酸铝纤维毡,膨胀珍珠岩。
炉底采用三层轻质粘土砖,密度为的普通硅酸铝纤维毡,级硅藻土砖和膨胀珍珠岩复合炉衬。
炉门用轻质粘土砖,密度为的普通硅酸铝纤维毡,级硅藻土砖。
炉底隔砖采用重质粘土砖,电热元件搁砖选用重质高铝砖。
炉底板材料选用耐热钢,根据炉底实际尺寸给出,分三块或者四块,厚。
四、砌体平均表面积计算砌体外廓尺寸如下:试中——拱顶高度,此炉子采用60°标准拱顶,取拱弧半径,则f可由求得f=131.052。
计算机控制技术课程设计-电阻炉温度控制系统设计
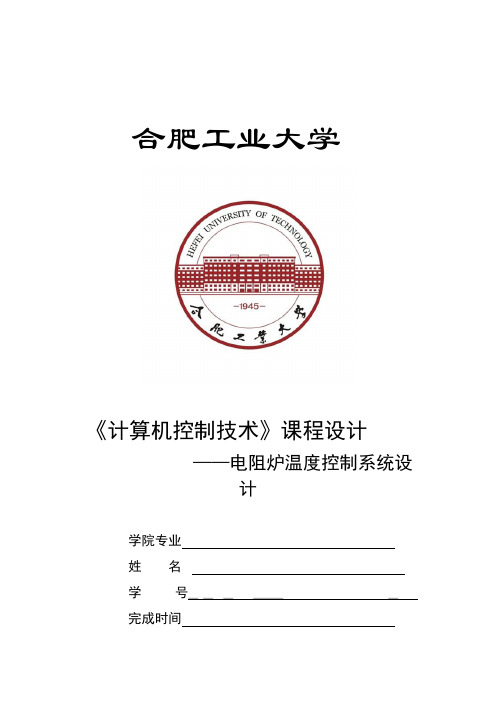
合肥工业大学《计算机控制技术》课程设计——电阻炉温度控制系统设计学院专业姓名学号_______ ________ _完成时间摘要:电阻炉的类型根据其热量产生的方式不同,可分为间接加热式和直接加热式两大类。
间接加热式电阻炉,就是在炉子内部有专用的电阻材料制作的加热元件,电流通过加热元件时产生热量,再通过热的传导、对流、辐射而使放置在炉中的炉料被加热。
直接加热式电阻炉,是将电源直接接在所需加热的材料上,让强大的电流直接流过所需加热的材料,使材料本身发热从而达到加热的效果。
工业电阻炉,大部分采用间接加热式,只有一小部分采用直接加热式。
由于电阻炉具有热效率高、热量损失小、加热方式简单、温度场分布均匀、环保等优点,应用十分广泛.关键词:炉温控制;高效率;加热一、总体方案设计本次课程设计主要就是使用计算机以及相应的部件组成电阻炉炉温的自动控制系统,从而使系统达到工艺要求的性能指标。
1、设计内容及要求电阻加热炉用于合金钢产品热力特性实验,电加热炉用电炉丝提供功率,使其在预定的时间内将炉内温度稳定到给定的温度值。
在本控制对象电阻加热炉功率为8KW,有220V交流电源供电,采用双向可控硅进行控制。
2、工艺要求及要求实现的基本功能本系统中所选用的加热炉为间接加热式电阻炉,控制要求为采用一台主机控制8个同样规格的电阻炉温度;电炉额定功率为20 kW;)恒温正常工作温度为1000℃,控温精度为±1%;电阻炉温度按预定的规律变化,超调量应尽可能小,且具有良好的稳定性;具有温度、曲线自动显示和打印功能,显示精度为±1℃;具有报警、参数设定、温度曲线修改设置等功能。
3、控制系统整体设计电阻炉温度计算机控制系统主要由主机、温度检测装置、A/D转换器、执行机构及辅助电路组成.系统中主机可以选用工业控制计算机、单片微型计算机或可编程序控制器中的一种作为控制器,再根据系统控制要求,选择一种合理的控制算法对电阻炉温度进行控制。
电阻炉炉温自动控制系统
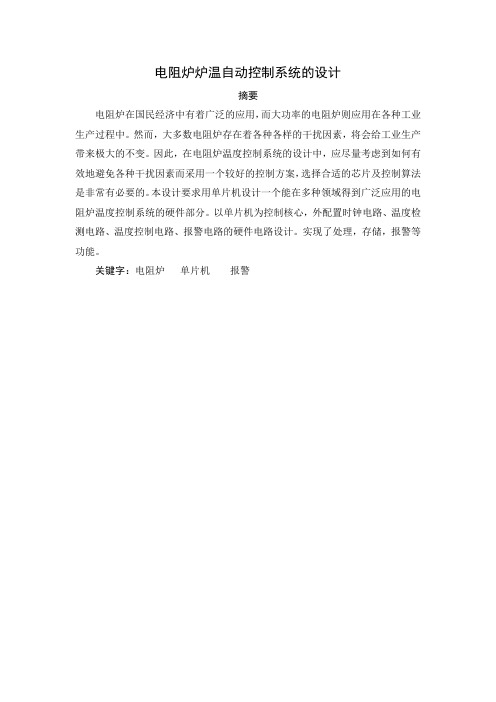
电阻炉以电为热源,通过电热元件将能转化为热能,在炉内对金属进行加热。电阻炉和火焰比,热效率高,可达50%-80%,热工制度容易控制,劳动条件好,炉体寿命长,炉温均匀,适用于要求较严的工件加热。电阻炉的功率是根据电阻炉的热平衡原则确定的,通过热平衡计算,可以比较精确的计算出电炉的功率。电炉所需的功率应包括炉子蓄热,工件加热需要热量、工件保温需要的热量、气氛裂解所需的热量,热损失等。其中炉子蓄热由电炉的规格、构造和主要尺寸、炉衬厚度,材料导热系数决定。电阻炉是热处理生产中应用最广的加热设备,通过不知在炉内的加热元件将电能转化为热能并记住辐射与对流的传热方式加热工件。
电阻炉功率的计算
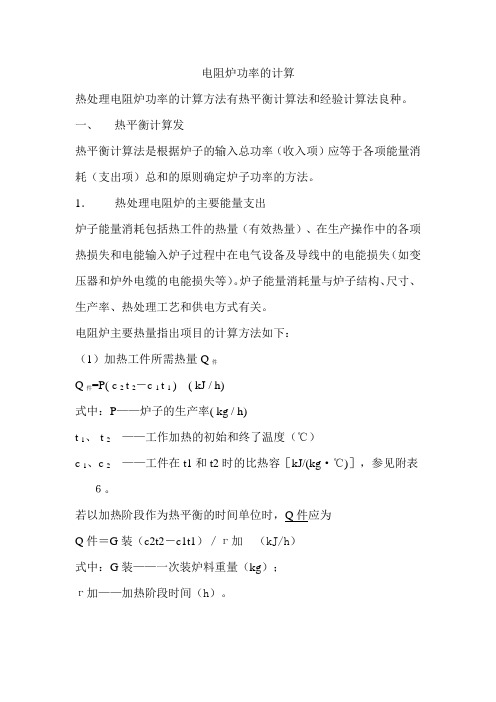
电阻炉功率的计算热处理电阻炉功率的计算方法有热平衡计算法和经验计算法良种。
一、热平衡计算发热平衡计算法是根据炉子的输入总功率(收入项)应等于各项能量消耗(支出项)总和的原则确定炉子功率的方法。
1.热处理电阻炉的主要能量支出炉子能量消耗包括热工件的热量(有效热量)、在生产操作中的各项热损失和电能输入炉子过程中在电气设备及导线中的电能损失(如变压器和炉外电缆的电能损失等)。
炉子能量消耗量与炉子结构、尺寸、生产率、热处理工艺和供电方式有关。
电阻炉主要热量指出项目的计算方法如下:(1)加热工件所需热量Q件Q件=P( c 2 t 2-c 1 t 1 ) ( kJ / h)式中:P——炉子的生产率( kg / h)t 1、t 2——工作加热的初始和终了温度(℃)c 1、c 2——工件在t1和t2时的比热容[kJ/(kg·℃)],参见附表6。
若以加热阶段作为热平衡的时间单位时,Q件应为Q件=G装(c2t2-c1t1)/г加(kJ/h)式中:G装——一次装炉料重量(kg);г加——加热阶段时间(h)。
(2)加热辅助构件(料筐、工夹具、支承架、炉底板及料盘)所需热量Q辅Q辅=P辅(c2t2-c1t1)(kJ/h)式中:P辅——每小时加热辅助构件的重量(kg/h);t1、t2——辅助构件加热的初始和终了温度(℃);c1、c2——辅助构件在t1和t2时比热容[kJ/(kg·℃);(3)加热控制气体所需热量Q控Q=V控c控(t2-t1)(kJ/h)式中:V控——控制气体的用量(m3/h);t1、t2——控制气体入炉前温度和工作温度(℃);c控——控制气体在t1~t2温度范围内的平均比热容[kJ/(m3·℃)] (4)通过炉衬的散热损失Q散在炉处于稳定态传热时,通过双层炉衬的散热损失为式中:tg、ta——炉气和炉外空气温度(℃),对电阻炉可以认为tg 近似等于炉内壁温度或炉温;啊s1、s2——第一层和第二层炉衬的厚度(m);λ1、λ2——第一层和第二层炉衬的导热率[W/(m2·℃)]ɑ∑2——炉体外壳对周围空气的综合传热系数[W/(m2·℃)](见附表2);F散——炉体的平均散热面积(m2);3.6——时间系数。
热处理电阻炉设计
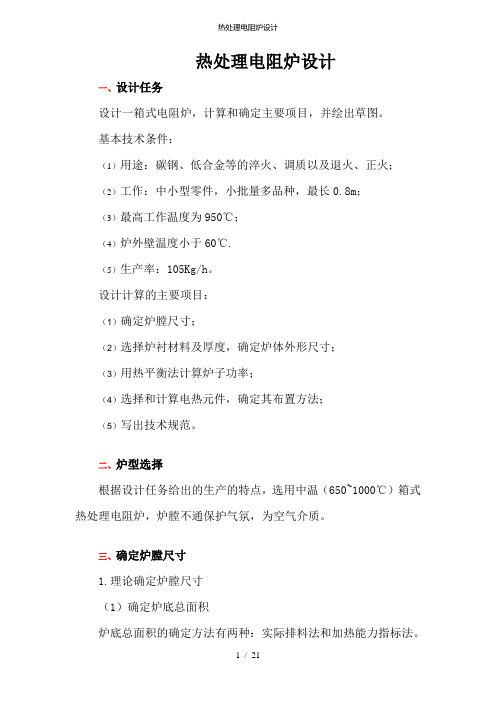
热处理电阻炉设计一、设计任务设计一箱式电阻炉,计算和确定主要项目,并绘出草图。
基本技术条件:(1)用途:碳钢、低合金等的淬火、调质以及退火、正火;(2)工作:中小型零件,小批量多品种,最长0.8m;(3)最高工作温度为950℃;(4)炉外壁温度小于60℃.(5)生产率:105Kg/h。
设计计算的主要项目:(1)确定炉膛尺寸;(2)选择炉衬材料及厚度,确定炉体外形尺寸;(3)用热平衡法计算炉子功率;(4)选择和计算电热元件,确定其布置方法;(5)写出技术规范。
二、炉型选择根据设计任务给出的生产的特点,选用中温(650~1000℃)箱式热处理电阻炉,炉膛不通保护气氛,为空气介质。
三、确定炉膛尺寸1.理论确定炉膛尺寸(1)确定炉底总面积炉底总面积的确定方法有两种:实际排料法和加热能力指标法。
本设计用加热能力指标法来确定炉底面积。
已知炉子生产效率P=105Kg/h 。
按教材表5-1选择适用于淬火、正火的一般箱式炉,其单位炉底面积生产率P 0=100~120Kg/(m 2·h )。
因此,炉子的炉底有效面积(即可以摆放工件的实际面积)F 1可按下式计算:2011105105m P P F ===通常炉底有效面积和炉底总面积之比值在0.75~0.85之间选择。
炉子小取值小值;炉子大取值大值。
本设计取中值0.8,则炉底总面积F 为:2125.18.018.0m F F ===(2)确定炉膛的长度和宽度炉底长度和宽度之比B L在3/2~2之间选择。
考虑到炉子使用时装、出料的方便,本设计取2=BL,则炉子炉底长度和宽度分别为:m F L 581.15.025.15.0===m L B 791.02581.12===(3)确定炉膛高度 炉膛高度和宽度之比BH在0.5~0.9之间选择,大炉子取小值,小炉子取大值。
本设计取中值0.7,则炉膛高度为:m B H 554.0791.07.07.0=⨯==2.确定实际炉膛尺寸为方便砌筑炉子,需要根据标准砖尺寸(230×113×65mm ),并考虑砌缝宽度(砌砖时两块砖之间的宽度2mm ),上下砖体应互相错开以及在炉底方面布置电热元件等要求,进一步确定炉膛尺寸。
第8章锅炉热平衡计算

23
第八章 结束!
有关参数。
反平衡试验的特点(与正平衡相反)
(书p.157)
(1)测量的数据比较多; (2)对工况稳定的要求相对比较低; (3)不但知道效率η,而且知道各项热损失qi的 大小;(对分析如何提高效率有利) (4)不需要测量燃料量B。
本章小结
1. 2. 3.
4. 5. 6. 7. 8.
锅炉的输入热量。 锅炉的各项热损失。 锅炉的主要热损失及其影响因素;如何降低各主要热损 失? 最佳过量空气系数。 锅炉的有效利用热量。 锅炉燃料消耗量和计算燃料消耗量。 正平衡和反平衡的概念、应用 锅炉正平衡和反平衡的效率及其测量。
G fa
fa BAar
100 C fa
, Gsl
sl BAar
100 C sl
;
( fa sl 1)
Qc 32700 kJ kg
C fa C sl fa Q4 327Aar sl 100 C fa 100 C sl
对于煤粉炉,机械未完全燃烧热损失
Q4 Q4fa
sl Q4
c Qc (G c Gsl ) fa
B
Qc C fa Csl ( G fa Gsl ) B 100 100
灰平衡:B
100 C fa Aar 100 Csl G fa Gsl 100 100 100 100 C fa 100 Csl 1 G fa Gsl BAar BAar
空气
雾化蒸汽
炉
炉墙向环境的散热Q5 其它热损失Q6
Q1
Q5
Qf
Q2
Q4
fa
Q3
Q4
sl
电阻炉电量估算
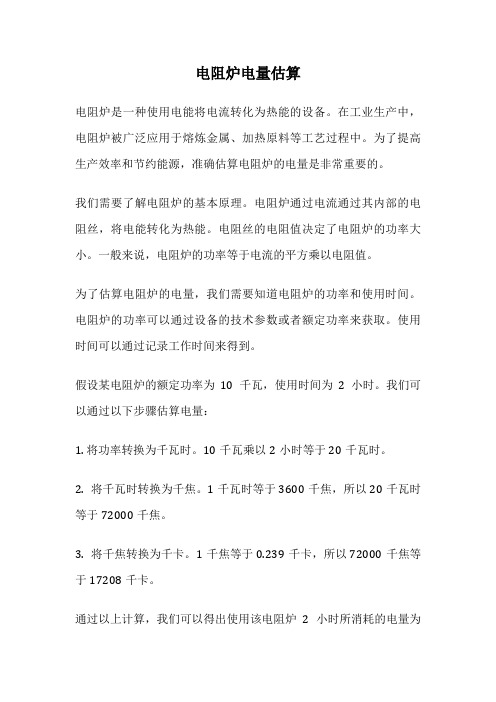
电阻炉电量估算电阻炉是一种使用电能将电流转化为热能的设备。
在工业生产中,电阻炉被广泛应用于熔炼金属、加热原料等工艺过程中。
为了提高生产效率和节约能源,准确估算电阻炉的电量是非常重要的。
我们需要了解电阻炉的基本原理。
电阻炉通过电流通过其内部的电阻丝,将电能转化为热能。
电阻丝的电阻值决定了电阻炉的功率大小。
一般来说,电阻炉的功率等于电流的平方乘以电阻值。
为了估算电阻炉的电量,我们需要知道电阻炉的功率和使用时间。
电阻炉的功率可以通过设备的技术参数或者额定功率来获取。
使用时间可以通过记录工作时间来得到。
假设某电阻炉的额定功率为10千瓦,使用时间为2小时。
我们可以通过以下步骤估算电量:1. 将功率转换为千瓦时。
10千瓦乘以2小时等于20千瓦时。
2. 将千瓦时转换为千焦。
1千瓦时等于3600千焦,所以20千瓦时等于72000千焦。
3. 将千焦转换为千卡。
1千焦等于0.239千卡,所以72000千焦等于17208千卡。
通过以上计算,我们可以得出使用该电阻炉2小时所消耗的电量为20千瓦时、72000千焦或17208千卡。
当然,这只是一个简单的估算方法。
实际情况中,可能需要考虑更多的因素,如电阻丝的损耗、电压的波动等。
因此,在实际使用中,我们建议根据电阻炉的具体情况和工作要求,结合实际监测数据进行更准确的电量估算。
电阻炉的电量估算是一个重要的工作,它可以帮助我们合理安排生产计划、节约能源和控制成本。
通过了解电阻炉的基本原理和使用时间,我们可以通过简单的计算方法来估算电阻炉的电量,并根据实际情况进行相应的调整和优化。
4章 炉子热平衡和燃料消耗量的计算(44-50)
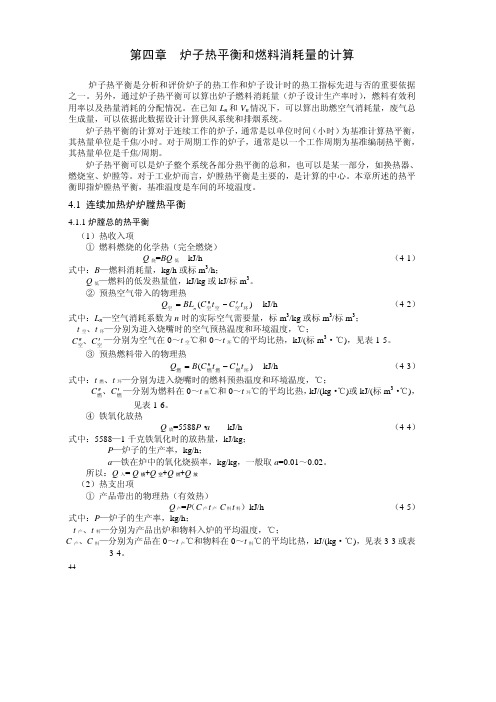
φ —炉门的遮蔽系数,一般取φ =0.5~0.8。
(b) 经开启炉门的溢出炉气热损失
Q溢 = V0ϕ (t气C气′′ − C气′ t环 ) kJ/h
(4-18)
式中:V0—单位时间内的炉气溢出量,标 m3/h;
t 气—溢出的炉气温度,℃;
C气′′ 、C气′ —分别为炉气在 0~t 气℃和 0~t 环℃的平均比热,kJ/(标 m3·℃),见表 1-5。
第四章 炉子热平衡和燃料消耗量的计算
炉子热平衡是分析和评价炉子的热工作和炉子设计时的热工指标先进与否的重要依据 之一。另外,通过炉子热平衡可以算出炉子燃料消耗量(炉子设计生产率时),燃料有效利 用率以及热量消耗的分配情况。在已知 Ln 和 Vn 情况下,可以算出助燃空气消耗量,废气总 生成量,可以依据此数据设计计算供风系统和排烟系统。
C燃′′ 、C燃′ —分别为燃料在 0~t 燃℃和 0~t 环℃的平均比热,kJ/(kg·℃)或 kJ/(标 m3·℃),
见表 1-6。
④ 铁氧化放热
Q 放=5588P·a kJ/h 式中:5588—1 千克铁氧化时的放热量,kJ/kg;
P—炉子的生产率,kg/h; a—铁在炉中的氧化烧损率,kg/kg,一般取 a=0.01~0.02。 所以:Q 入= Q 烧+Q 空+Q 燃+Q 放 (2)热支出项 ① 产品带出的物理热(有效热)
② 单位热耗:
标 m3(kg)/t
(4-24)
47
b′′ = 1000BQ低 kJ/t P
③ 单位标准热耗:
b′′ = b′ = 1000B Q低 29308 29308P
(3)炉子热效率:
kgce/t
η1
=
Q产 BQ低
- 1、下载文档前请自行甄别文档内容的完整性,平台不提供额外的编辑、内容补充、找答案等附加服务。
- 2、"仅部分预览"的文档,不可在线预览部分如存在完整性等问题,可反馈申请退款(可完整预览的文档不适用该条件!)。
- 3、如文档侵犯您的权益,请联系客服反馈,我们会尽快为您处理(人工客服工作时间:9:00-18:30)。
2.
5862.167887 27.5 161209.6169 0.708 9.1 0 5664000 1500 0.708 9.1 0 106200 6234670.843 623.4670843 7250.92219 1.05 7613.4683 654.6404385 8755.488545 752.8365043
16.5m× 5m× 5.5m台车式电阻炉热平衡计算书
1. 工艺条件和要求:
1.1炉膛尺寸: 长 宽 高 1.2当量工艺温度: tN 工件出炉温度 工件进炉温度 1.3升温速度: ℃/h 升温时间τ (h) 保温时间 1.4最大装载量: P (kg) 1.5炉体材料 容重Kg/m3 厚度S 1.6炉底材料 容重Kg/m3 厚度mm m m m
2.
950.6621505 319 303261.226 728 0.984992 0.25004 0.001903062 22.57908141 10.5
3. 升温期炉底热损失
3.1定性温度: tD ℃ 3.2导热系数: 3.3热容量 3.4导温系数(热扩散系数) 3.6热阻综合系数(热惰性系数) 3.6墙外表散热系数:
kcal/ m .h
kcal/Kg℃ m /h
2
.℃
0.226901 0.256785015 0.004016466 3.580258491 10.5 3.654983707 4.627568852 0.9
kcal/ m2..h0.5.℃
kcal/ m .h m2 kcal/ h ℃ kcal/m.h.℃ kcal/ Kg℃ m2 /h kcal/ m2..h0.5.℃
16.5m× 5m× 5.5m台车式电阻炉热平衡计算书
3.7傅立叶准数 3.8毕欧准数 3.9传热指数: (查图、表) 3.10升温末期炉墙单位热损失 3.11炉底表面积: 3.12升温末期炉墙总热损失 0.108236634 0.009593987 0.88
kcal/ m .h m2 kcal/ h kcal/ Kg℃
2. 0.5
2. 升温期炉墙热损失
2.1定性温度: tD ℃ 2.2导热系数: 2.3热容量 2.4导温系数(热扩散系数) 2.6热阻综合系数热惰性系数) 2.6墙外表散热系数: 2.7傅立叶准数 2.8毕欧准数 2.9传热指数: (查图、表) 2.10升温末期炉墙单位热损失 2.11炉膛内表面积: 2.12升温末期炉墙总热损失
4.工件吸热
4.1工件比热容 4.2升温时间 保温时间 4.3工件吸热量
kcal/ h
kg
5.炉底板及导流罩吸热
5.1材料重量kg 5.1材料比热容 5.2升温时间 保温时间 5.3材料吸热量:
kcal/ Kg℃
h h
6.升温末期总热需要量
kcal/ h kcal/ h 104kcal/ h
7.其他热量损失系数: 8. 总加热安装功率 9.安装功率放15%的余量
kw kw kw
104kcal/ h
kw
10 kcal/ h
4
10.加热时间简易计算
钢材重量 钢材平均比热容 钢材受热面积 综合给热系数 加热开始钢材温度 加热终了钢材温度 炉温 加热时间 80000 0.708 82.5 100 20 910 920 8.588320374
单位
结果
16.5m× 5m× 5.5m (长× 宽× 高) 16.5 5 5.5 910
℃
℃ ℃ ℃ ℃/h (h) h (kg)
25 0 100 9.1 0 80000 硅酸铝耐火纤维毡、毯(压缩后) 3 220 Kg/m mm 100 耐火粘土砖(面砖) ℃ 2070 (kcal/m.h.℃) 400 m2 /h 910