油库阀门的常见故障及防治
分析炼油装置的阀门内漏及对策
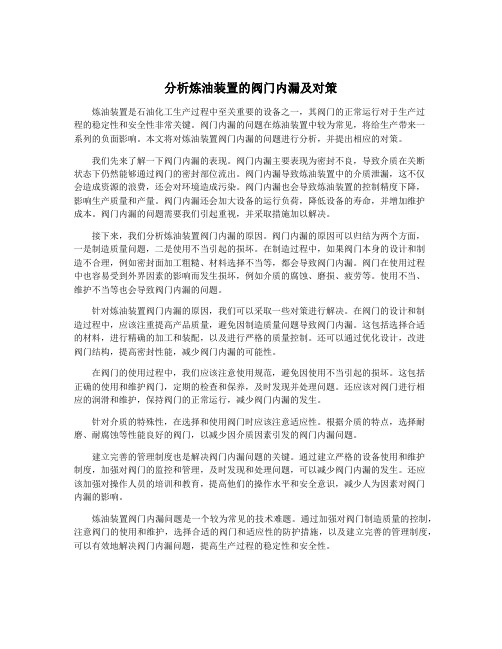
分析炼油装置的阀门内漏及对策炼油装置是石油化工生产过程中至关重要的设备之一,其阀门的正常运行对于生产过程的稳定性和安全性非常关键。
阀门内漏的问题在炼油装置中较为常见,将给生产带来一系列的负面影响。
本文将对炼油装置阀门内漏的问题进行分析,并提出相应的对策。
我们先来了解一下阀门内漏的表现。
阀门内漏主要表现为密封不良,导致介质在关断状态下仍然能够通过阀门的密封部位流出。
阀门内漏导致炼油装置中的介质泄漏,这不仅会造成资源的浪费,还会对环境造成污染。
阀门内漏也会导致炼油装置的控制精度下降,影响生产质量和产量。
阀门内漏还会加大设备的运行负荷,降低设备的寿命,并增加维护成本。
阀门内漏的问题需要我们引起重视,并采取措施加以解决。
接下来,我们分析炼油装置阀门内漏的原因。
阀门内漏的原因可以归结为两个方面,一是制造质量问题,二是使用不当引起的损坏。
在制造过程中,如果阀门本身的设计和制造不合理,例如密封面加工粗糙、材料选择不当等,都会导致阀门内漏。
阀门在使用过程中也容易受到外界因素的影响而发生损坏,例如介质的腐蚀、磨损、疲劳等。
使用不当、维护不当等也会导致阀门内漏的问题。
针对炼油装置阀门内漏的原因,我们可以采取一些对策进行解决。
在阀门的设计和制造过程中,应该注重提高产品质量,避免因制造质量问题导致阀门内漏。
这包括选择合适的材料,进行精确的加工和装配,以及进行严格的质量控制。
还可以通过优化设计,改进阀门结构,提高密封性能,减少阀门内漏的可能性。
在阀门的使用过程中,我们应该注意使用规范,避免因使用不当引起的损坏。
这包括正确的使用和维护阀门,定期的检查和保养,及时发现并处理问题。
还应该对阀门进行相应的润滑和维护,保持阀门的正常运行,减少阀门内漏的发生。
针对介质的特殊性,在选择和使用阀门时应该注意适应性。
根据介质的特点,选择耐磨、耐腐蚀等性能良好的阀门,以减少因介质因素引发的阀门内漏问题。
建立完善的管理制度也是解决阀门内漏问题的关键。
油库阀门故障的成因及排除方法

油库阀门故障的成因及排除方法本文分析了油庫阀门常见故障及其可能产生的原因,并根据这些因给出了排除故障的方法和一定的预防措施,为减少公司阀门故障的发生,降低事故发生率,提供一些参考意见。
关健词:阀门;故障分析;预防1 阀门设备的故障分析阀门设备在油库的各个系统中,使用数量多,使用次数频繁,在油库系统中发挥着巨大的作用。
油库阀门是否能够安全正常使用直接影响着油库系统的运行。
但是,油库阀门同样也是故障和事故多发的部位,因此,需要一些合理的措施进行预防。
加强油库阀门设备的管理是保证油库系统的安全运行和减少事故发生的关键所在。
1.1 阀门设备的设计安装问题①未合理选择阀门:不同的地区和环境应选择不同的阀门,例如,在严寒地区选用了铸铁类的阀门,又没有进行相应的保温措施,最后会因为油中的水结冰沉积在阀门中,胀裂阀门,导致损坏;②管路没有设置合理的泄压装置:在夏季,温度高,管内存油因为热膨胀而压力增高,没有泄压装置,有可能会胀裂阀门,或冲毁法兰垫片;③错误的阀门安装位置:在有横向位移的管道上,若阀门设置距离支座太近,当管道横向位移时,阀门很容易受损法兰容易破坏;④试压后水未放净,产生冻裂,或者试压操作不当,验收检查不够严格,使得垫片被水击坏。
1.2 在操作使用中导致的故障不当的操作,以及某些人为因素都会导致阀门的关闭不严,错开,未关的情况发生,造成“死油”段,当管路受到一定的憋压时,使得阀门损坏。
此外,如果在管路系统的试压和试漏之前没有按照规定进行吹扫焊渣和铁锈,则有可能导致密封面的划伤、冲蚀或者挤压;若杂质沉积在了阀门底部,又会造成阀门关闭不严的问题。
1.3维修和检查不到位①阀门没有按照规定要求进行定期的试压、清洗,维护和保养不够及时,会造成阀门的开关失灵或者关闭不严问题;②在冬季到来之前没有做任何的保温措施,也没有把阀门内的积水排除干净,造成阀门的冻裂情况;③在对阀门进行检查和维修时,必须按照国家规定在无压力状态进行,如果错误的带压进行操作,不仅会损坏阀门设备导致阀门故障,而且有可能导致跑油事故,造成不可挽回的损失。
闸阀常见的故障及解决办法
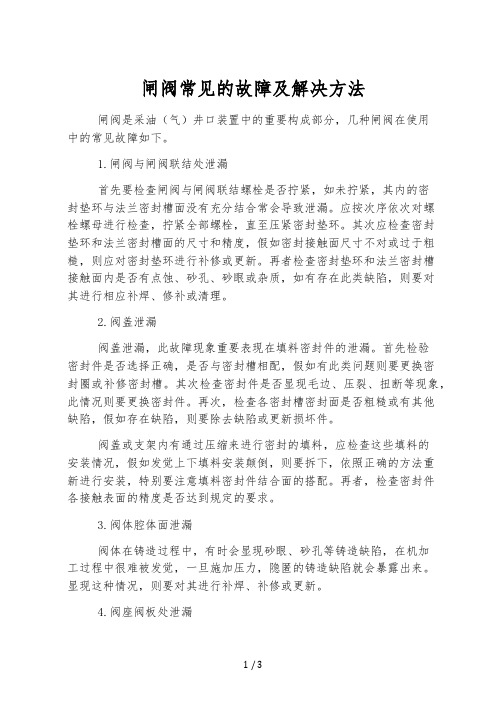
闸阀常见的故障及解决方法闸阀是采油(气)井口装置中的重要构成部分,几种闸阀在使用中的常见故障如下。
1.闸阀与闸阀联结处泄漏首先要检查闸阀与闸阀联结螺栓是否拧紧,如未拧紧,其内的密封垫环与法兰密封槽面没有充分结合常会导致泄漏。
应按次序依次对螺栓螺母进行检查,拧紧全部螺栓,直至压紧密封垫环。
其次应检查密封垫环和法兰密封槽面的尺寸和精度,假如密封接触面尺寸不对或过于粗糙,则应对密封垫环进行补修或更新。
再者检查密封垫环和法兰密封槽接触面内是否有点蚀、砂孔、砂眼或杂质,如有存在此类缺陷,则要对其进行相应补焊、修补或清理。
2.阀盖泄漏阀盖泄漏,此故障现象重要表现在填料密封件的泄漏。
首先检验密封件是否选择正确,是否与密封槽相配,假如有此类问题则要更换密封圈或补修密封槽。
其次检查密封件是否显现毛边、压裂、扭断等现象,此情况则要更换密封件。
再次,检查各密封槽密封面是否粗糙或有其他缺陷,假如存在缺陷,则要除去缺陷或更新损坏件。
阀盖或支架内有通过压缩来进行密封的填料,应检查这些填料的安装情况,假如发觉上下填料安装颠倒,则要拆下,依照正确的方法重新进行安装,特别要注意填料密封件结合面的搭配。
再者,检查密封件各接触表面的精度是否达到规定的要求。
3.阀体腔体面泄漏阀体在铸造过程中,有时会显现砂眼、砂孔等铸造缺陷,在机加工过程中很难被发觉,一旦施加压力,隐匿的铸造缺陷就会暴露出来。
显现这种情况,则要对其进行补焊、补修或更新。
4.阀座阀板处泄漏阀座阀板处泄漏,在安装或维护和修理闸阀当中是最为常见的现象。
一般可分两类:一类是密封面泄漏,另一类是密封圈根部泄漏。
首先应当检查阀座与阀板接触密封面的精度,此密封面至少要研磨,如发觉表面精度过于粗糙,则应当拆下重新进行研磨。
其次检查密封面是否存在点蚀、压痕、砂眼、裂纹等缺陷,显现此情况,则要对阀板或阀座进行更换。
对有压簧的阀座,应当检查压簧的弹性是符合要求,假如弹性减弱,则要更新压簧。
再者检查阀板与阀杆T形联结处是否过于松动,致使阀板在压紧的过程中显现斜度的情况,此情况则要拆下阀板,调整其到最佳尺寸。
炼油厂阀门故障修复及现场维护管理
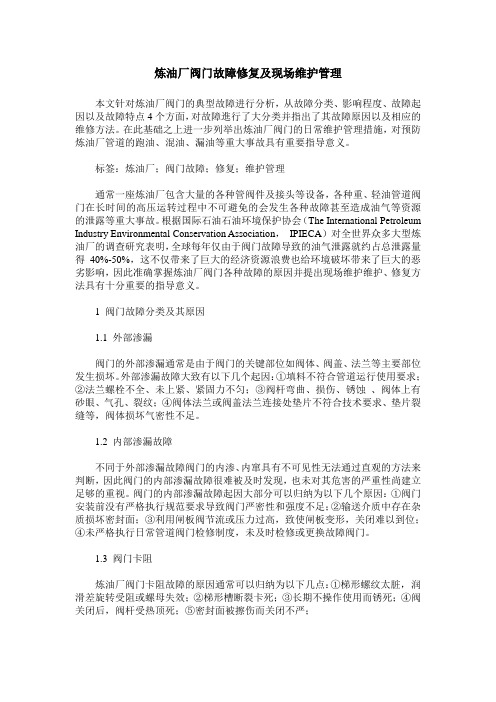
炼油厂阀门故障修复及现场维护管理本文针对炼油厂阀门的典型故障进行分析,从故障分类、影响程度、故障起因以及故障特点4个方面,对故障進行了大分类并指出了其故障原因以及相应的维修方法。
在此基础之上进一步列举出炼油厂阀门的日常维护管理措施,对预防炼油厂管道的跑油、混油、漏油等重大事故具有重要指导意义。
标签:炼油厂;阀门故障;修复;维护管理通常一座炼油厂包含大量的各种管阀件及接头等设备,各种重、轻油管道阀门在长时间的高压运转过程中不可避免的会发生各种故障甚至造成油气等资源的泄露等重大事故。
根据国际石油石油环境保护协会(The International Petroleum Industry Environmental Conservation Association,IPIECA)对全世界众多大型炼油厂的调查研究表明,全球每年仅由于阀门故障导致的油气泄露就约占总泄露量得40%-50%,这不仅带来了巨大的经济资源浪费也给环境破坏带来了巨大的恶劣影响,因此准确掌握炼油厂阀门各种故障的原因并提出现场维护维护、修复方法具有十分重要的指导意义。
1 阀门故障分类及其原因1.1 外部渗漏阀门的外部渗漏通常是由于阀门的关键部位如阀体、阀盖、法兰等主要部位发生损坏。
外部渗漏故障大致有以下几个起因:①填料不符合管道运行使用要求;②法兰螺栓不全、未上紧、紧固力不匀;③阀杆弯曲、损伤、锈蚀、阀体上有砂眼、气孔、裂纹;④阀体法兰或阀盖法兰连接处垫片不符合技术要求、垫片裂缝等,阀体损坏气密性不足。
1.2 内部渗漏故障不同于外部渗漏故障阀门的内渗、内窜具有不可见性无法通过直观的方法来判断,因此阀门的内部渗漏故障很难被及时发现,也未对其危害的严重性尚建立足够的重视。
阀门的内部渗漏故障起因大部分可以归纳为以下几个原因:①阀门安装前没有严格执行规范要求导致阀门严密性和强度不足;②输送介质中存在杂质损坏密封面;③利用闸板阀节流或压力过高,致使闸板变形,关闭难以到位;④未严格执行日常管道阀门检修制度,未及时检修或更换故障阀门。
分析炼油装置的阀门内漏及对策
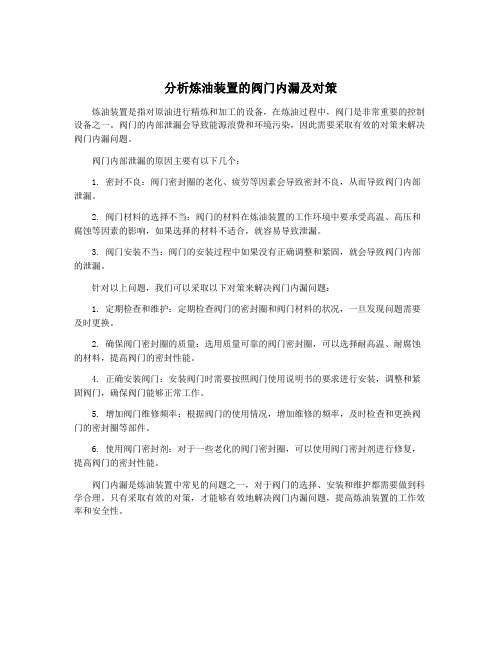
分析炼油装置的阀门内漏及对策
炼油装置是指对原油进行精炼和加工的设备,在炼油过程中,阀门是非常重要的控制设备之一。
阀门的内部泄漏会导致能源浪费和环境污染,因此需要采取有效的对策来解决阀门内漏问题。
阀门内部泄漏的原因主要有以下几个:
1. 密封不良:阀门密封圈的老化、疲劳等因素会导致密封不良,从而导致阀门内部泄漏。
2. 阀门材料的选择不当:阀门的材料在炼油装置的工作环境中要承受高温、高压和腐蚀等因素的影响,如果选择的材料不适合,就容易导致泄漏。
3. 阀门安装不当:阀门的安装过程中如果没有正确调整和紧固,就会导致阀门内部的泄漏。
针对以上问题,我们可以采取以下对策来解决阀门内漏问题:
1. 定期检查和维护:定期检查阀门的密封圈和阀门材料的状况,一旦发现问题需要及时更换。
2. 确保阀门密封圈的质量:选用质量可靠的阀门密封圈,可以选择耐高温、耐腐蚀的材料,提高阀门的密封性能。
4. 正确安装阀门:安装阀门时需要按照阀门使用说明书的要求进行安装,调整和紧固阀门,确保阀门能够正常工作。
5. 增加阀门维修频率:根据阀门的使用情况,增加维修的频率,及时检查和更换阀门的密封圈等部件。
6. 使用阀门密封剂:对于一些老化的阀门密封圈,可以使用阀门密封剂进行修复,提高阀门的密封性能。
阀门内漏是炼油装置中常见的问题之一,对于阀门的选择、安装和维护都需要做到科学合理。
只有采取有效的对策,才能够有效地解决阀门内漏问题,提高炼油装置的工作效率和安全性。
阀门常见故障及日常维护

1 阀门常见故障及主要成因阀门作为化工生产中的重要部件,在生产中发挥着重要作用。
比如在进行场内外原材料运输时,阀门的使用可以减少操作难度,为便捷施工生产带来益处。
另外,阀门的分段处理功能可以在管道出现故障时起到很好的控制作用,以减轻生产损失。
阀门依据其作用分为安全阀、减压阀等,比如常见的泄压阀具有控制液体压力的作用,在系统检测到压力过高或者自动检测出现过高压时,打开阀门进行液体泄压,可以控制流量和压力,在化工企业安全生产中起到十分重要的作用。
阀门在化工生产中经常处于危险位置,常有故障发生。
阀门经常出现的故障有:阀门主体泄漏,阀门失灵、失控,阀杆弯折、断裂,底座开裂等。
造成这些问题的主要原因与工作人员的疏忽有关,也与阀门的安装质量有很大关系。
1.1 阀门质量不合格和安装失误阀门在化工生产中的重要作用,决定了企业要对其质量严格把控。
化工生产用阀门质量一定要符合相关要求,选购时要进行严格测试,只有符合企业运行标准的阀门才能投入使用。
一些企业过于追求低成本,甚至出现选用劣质阀门的情况,这为阀门的后续使用环节埋下了隐患。
劣质阀门在使用过程中的表现大不如优质阀门,而且存在相当大的安全隐患。
除了选用高质量阀门以外,阀门安装时也需要格外注意,由于安装失误引起的阀门故障也时有发生。
1.2 操作不当引起的故障控制阀门的工作人员应具备优良的操作技术,以减少失误。
操作过程中,一些技术人员不能严格遵守操作规范,用力过猛致使操纵杆超过最大承受限度,而阀门的保护机制又不能在第一时间起到过力保护,导致阀门失灵。
1.3 阀门使用过频、维修不及时阀门等设备的用时都会有相应的限度,过高使用频率会加快阀门部件的受损程度以及老化速度,尤其是针对化工企业来说,原材料大多具有腐蚀性,给阀门的使用带来了更多的不确定性,也会缩短阀门的使用期限。
1.4 阀门主体安装失误阀门主体的安装焊接,需要有精良的焊接技术,减少因焊接质量带来的阀门故障。
在阀体补焊时,不良的焊接技术会造成阀体开裂、阀门主体与底座之间产生间隙,增加阀门故障概率。
2024年油库阀门的安全操作(3篇)
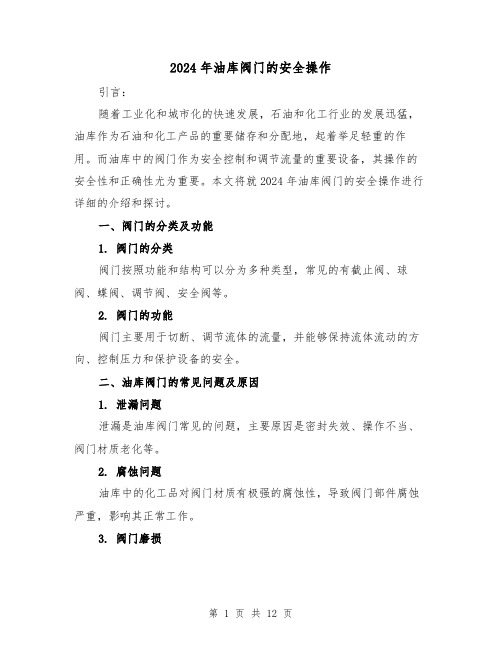
2024年油库阀门的安全操作引言:随着工业化和城市化的快速发展,石油和化工行业的发展迅猛,油库作为石油和化工产品的重要储存和分配地,起着举足轻重的作用。
而油库中的阀门作为安全控制和调节流量的重要设备,其操作的安全性和正确性尤为重要。
本文将就2024年油库阀门的安全操作进行详细的介绍和探讨。
一、阀门的分类及功能1. 阀门的分类阀门按照功能和结构可以分为多种类型,常见的有截止阀、球阀、蝶阀、调节阀、安全阀等。
2. 阀门的功能阀门主要用于切断、调节流体的流量,并能够保持流体流动的方向、控制压力和保护设备的安全。
二、油库阀门的常见问题及原因1. 泄漏问题泄漏是油库阀门常见的问题,主要原因是密封失效、操作不当、阀门材质老化等。
2. 腐蚀问题油库中的化工品对阀门材质有极强的腐蚀性,导致阀门部件腐蚀严重,影响其正常工作。
3. 阀门磨损由于油库中的介质流速高、工作时间长,阀门的磨损程度较大,容易导致漏气、渗漏等问题。
三、油库阀门的安全操作规范1. 定期检查和维护油库阀门应定期进行检查和维护,特别是对于容易发生泄漏和腐蚀问题的部位,如阀杆、密封面等,要定期检查、清洁和更换。
2. 操作前的准备工作在操作阀门之前,必须做好以下准备工作:①确认阀门位置和状态;②确认阀门所处的介质、压力以及温度;③确认阀门周围环境是否安全。
3. 操作规范在操作阀门时,应按照以下规范进行:①操作人员要熟悉阀门的位置和工作原理,并佩戴个人防护装备;②在操作之前,要进行必要的准备工作,如卸除管道压力、排空介质等;③操作过程中,要慢慢开关阀门,避免突然关闭或打开,以免引发压力波动、介质喷溅等危险;④操作完毕后,要检查阀门是否关闭严密,防止漏气和泄漏。
4. 建立管理制度对于油库阀门的安全操作,必须建立相应的管理制度,包括培训操作人员的技能和安全知识、制定符合实际情况的操作规范和操作流程等,通过严格的管理确保油库阀门的安全操作。
四、2024年油库阀门安全操作的应用现状与挑战1. 应用现状目前,已经有一些石油和化工企业对于油库阀门的安全操作进行了一些研究和实践,并通过培训操作人员、完善操作规范等方式,提高了油库阀门的安全性和可靠性。
闸阀常见故障和预防措施

书山有路勤为径,学海无涯苦作舟
闸阀常见故障和预防措施
闸阀是采油(气)井口装置中的主要构成部分,几种闸阀在使用中的常见故障如下。
1、闸阀与闸阀联结处泄漏
首先要检查闸阀与闸阀联结螺栓是否拧紧,如未拧紧,其内的密封垫环与法兰密封槽面没有充分结合常会导致泄漏。
应按顺序依次对螺栓螺母进行检查,拧紧全部螺栓,直至压紧密封垫环。
其次应检查密封垫环和法兰密封槽面的尺寸和精度,假如密封接触面尺寸不对或过于粗糙,则应对密封垫环进行补修或更新。
再者检查密封垫环和法兰密封槽接触面内是否有点蚀、砂孔、砂眼或杂质,如有存在此类缺陷,则要对其进行相应补焊、修补或清理。
2、阀盖泄漏
阀盖泄漏,此故障现象主要表现在填料密封件的泄漏。
首先检验密封件是否选择正确,是否与密封槽相配,假如有此类问题则要更换密封圈或补修密封槽。
其次检查密封件是否出现毛边、压裂、扭断等现象,此情况则要更换密封件。
再次,检查各密封槽密封面是否粗糙或有其他缺陷,假如存在缺陷,则要消除缺陷或更新损坏件。
阀盖或支架内有通过压缩来进行密封的填料,应检查这些填料的安装情况,假如发现上下填料安装颠倒,则要拆下,按照正确的方法重新进行安装,特别要注意填料密封件结合面的配合。
再者,检查密封件各接触表面的精度是否达到规定的要求。
3、阀体腔体面泄漏
阀体在铸造过程中,有时会出现砂眼、砂孔等铸造缺陷,在机加工过程。
- 1、下载文档前请自行甄别文档内容的完整性,平台不提供额外的编辑、内容补充、找答案等附加服务。
- 2、"仅部分预览"的文档,不可在线预览部分如存在完整性等问题,可反馈申请退款(可完整预览的文档不适用该条件!)。
- 3、如文档侵犯您的权益,请联系客服反馈,我们会尽快为您处理(人工客服工作时间:9:00-18:30)。
油库阀门的常见故障及防治集团公司文件内部编码:(TTT-UUTT-MMYB-URTTY-ITTLTY-油库阀门的常见故障及防治1.阀体和阀盖的常见故障是什么?这些故障产生的原因是什么?应采取什么防治措施来避免这些故障?阀体和阀盖的常见故障不外乎以下几种:一是破损;二是出现砂眼;三是发生老化或腐蚀破坏。
产生这些故障的原因可能是以下几方面。
①阀体和阀盖产生破损的原因主要是由于设计不良,如安全系数小、结构不合理,内应力集中;或者是由于制造质量差,如厚薄不均、材质不匀;或者是由于焊接质量差,如焊缝过脆,内应力过大等;或者由于安装不当,位置偏斜扭曲;或者由于阀门选用不当,与工况不相适应;或者由于水击压力过高;或者由于维护不周,冬季保温不好被冻裂;或者由于受强大外力破坏。
②砂眼产生的原因主要是由于制造质量差所致。
③腐蚀或老化产生的原因主要是由于制造质量差,或者由于防腐及维护不力,更换维修不及时所致。
针对这些故障,可以采取以下的预防措施。
①破坏的防治措施有:应按国家标准设计,严格遵守操作规程、工艺进行加工制造,建立完善的质量保证体系;焊接时应严格按焊接工艺和操作规程施焊,并应认真检查和探伤;安装时应使阀门受力均匀,防止法兰有错口和张口现象;选用阀门应按实际工况正确选择;管路系统应设防止水击超压措施;加强阀门维护,冬季做好保温措施;超过使用期限的阀门应有防振措施,操作应平稳,一旦发现疲劳缺陷应及时更换。
②砂眼的预防措施有:阀门制造过程中应严格遵守加工工艺和操作规程办事,建立完善的质保体系,出厂前应认真做强度试验。
③腐蚀老化的预防措施有:提高制造质量,根除制造缺陷;加强防腐措施;增强阀门维护,及时维修或更换。
相应地,对这些常见故障也可以采取如下的治理方法:阀体和阀盖发生破损、砂眼、腐蚀老化故障时,应停车卸压修理;按科学堵漏方法进行堵漏;根据实际情况进行修复或更换破损件或更换阀门。
2.填料的常见故障是什么?这些故障产生的原因是什么?应采取什么防治措施来避免这些故障?填料的常见故障主要有:施加在填料上的预紧力过小、紧固件失灵、阀杆密封面损坏和填料失效四种。
产生这些故障的原因可能有以下几方面。
①填料上的预紧力过小有以下几种原因:填料不足,或因装填数量不足,或因磨损、老化和装填不当;或因无预紧间隙;或因压套歪斜、直径偏大压在填料函上;或因螺纹乱扣、锈蚀、混入杂质,使螺纹拧紧时受阻。
②紧固件失灵的原因是:制造质量差,如压盖、压套螺母、螺栓、耳子等零件产生断裂;或由于振动使之松弛;或由于腐蚀损坏;或由于操作不当,如用力不均匀,用力过猛过大,损坏了紧固件;或由于维修不力。
③阀杆密封面损坏的原因有:制造缺陷所致,如硬度过低,存有裂纹、剥落、阀杆不圆、阀杆弯曲不直;或因阀杆受到腐蚀,密封面出现凹坑、剥落现象;或因安装不正,使阀杆过早损坏;或因维修不及时。
④填料失灵的原因有:选材不当,所用填料与工况不适应;组装不正确,如填料搭配不当、安装不正、搭头不合、上紧下松,甚至缺少垫料;系统操作不稳,温度和压力波动大,造成填料泄漏;填料老化、磨损、波纹管破损而失效;填料质量差,如填料松散、有毛头、干涸、断头、杂质等缺陷。
针对这些故障,可以采取以下的预防措施。
①预紧力过小的预防措施:按规定填装足量的填料,更换过期填料,正确装配填料,防止上紧下松和多圈缠绕现象;压套压人填料函的深度应为其高度的1/4—1/3,并且压套螺母和压盖螺栓的螺纹应有相应的预紧高度;装填料前,将压套放人填料函内检查其配合间隙是否符合要求,装配时应正确防止压套偏斜,防止填料露在外面,并检查压套端面是否压到填料函内;经常检查和清扫螺栓、螺母,拧紧螺栓螺母时,应涂敷少许石墨粉或防锈剂。
②防止紧固件失灵的措施有:提高制造质量;做好设备和管道的防振工作,加强巡回检查和日常维护保养工作;紧固零件时应对称均匀,紧固或松动前应仔细检查,涂以一定除锈剂或少许石墨粉;按时维修,对不符合技术要求的紧固件应及时更换。
③防止阀杆密封面损坏的措施:提高阀杆制造质量;加强阀杆防腐措施;安装时应使阀杆与其螺母、压盖、填料函同心;装置管道检修时,对阀杆进行修理或更换。
④防止填料失效的措施有:按工况正确选用填料;按技术要求组装填料,应事先预制填料,一圈一圈错开搭分别压紧,防止多层缠绕、一次压紧等现象,操作时应平稳,防止系统温度压力过大波动;按要求更换填料;使用时应认真检查填料的品种、规格、型号、厂家、出厂时间和质地好坏,不符合要求的不能使用。
相应地,对这些常见故障也可以采取如下的治理方法。
①预紧力过小时的治理方法是:关闭阀门或启用密封后,修理好零件,添加填料,调整预紧力和预紧间隙;若阀门不能关闭时,上密封失效的情况下可采用阀门的机械堵漏法或粘接堵漏法或注剂堵漏法进行堵漏;当压套搁浅时,应找出搁浅原因,对症下药,若因压套毛刺或直径过大引起,应用锉力修整至正常为止;若因螺纹抗进,可用除锈剂或煤油清洗干净,然后用什锦锉修整螺纹至其松紧适当为止。
②紧固件失灵的治理方法是:关闭阀门后,确认填料不会因内压往外移动时,按正常方法修复紧固件;若阀门不能关闭时,可以用改换密封法或带压粘接(注剂)修复紧固件;若为一般紧固件松动和损坏,可直接修理和拧紧紧固件即可。
③阀杆密封面损坏的治理方法是:若为轻微损坏可用抛光法消除;若密封面损坏至泄漏,需关闭阀门或启用上密封后,进行研磨或局部镀层修复;若密封面损坏难以修复时,可用带压更换阀门法给予解决。
④填料失灵的治理方法是:关闭阀门或启用上密封后,更换填料或用适当的阀门堵漏方法进行堵漏,或用其他方法更换填料或者更换阀门。
3.垫片的常见故障是什么?这些故障产生的原因是什么?应采取什么防治措施来避免这些故障?垫片的常见故障有预紧力不够、紧固件失灵、静密封面缺陷、法兰损坏、垫片失效等五种。
产生这些故障的原因可能有以下几种。
(1)产生预紧力不够的原因凹面深度大于凸面高度;垫片太薄;无预紧间隙或预紧间隙太小,无法压紧垫片;螺纹因锈蚀,或混入杂质,或规格不一,使螺纹拧紧时受阻或者松紧不一,疑是压紧,实为未压紧;法兰搁浅,没有压紧垫片;法兰歪斜。
(2)发生紧固件失灵的原因制造质量差,紧固件有裂纹、滑丝等缺陷;因振动而松弛;或因腐蚀损坏;或因用力不当;或因维护不及时,未及时更换。
(3)产生静密封面缺陷的原因制造缺陷存有气孔、夹渣、裂纹、凹坑、表面不平;或因腐蚀损坏;或因受外力冲撞压伤。
(4)法兰损坏的原因制造质量差,存有裂纹、气孔、厚度不够等缺陷;或因紧固力过大所致;或因装配不正所致。
(5)垫片失效的原因垫片质量差,如老化、不平、脱皮、粗糙;或因选用不当与工况不符;或因安装不正,如装偏、压伤、垫片过大或过小;或因操作不力,温度和压力波动过大,水击压力超限;或因垫片老化损坏所致。
针对这些故障,可以采取以下的预防措施。
(1)预防预紧力不够的措施垫片安装前应检查凸凹面尺寸,若凹面深度大于凸面高度,应修复到规定尺寸,一般凹面深度等于凸面高度,按公称压力和通径选用垫片的厚度;安装垫片后,法兰间或压紧螺母的螺纹应有一定预紧间隙,以备使用时进一步压紧垫片;经常检查和清扫螺栓、螺母;安装时注意螺栓螺母规格型号一致性;拧紧螺栓螺母时,应涂敷少许石墨或除锈剂;安装垫片前,应认真检查法兰静密封面各部尺寸并事先将两法兰装合一下,然后正式安装,若发现两法兰间隙过大,应检查是否搁浅;安装应正确,要防止垫片装偏,法兰局部搁浅;拧紧螺栓时应对称轮流均匀,法兰间隙一致。
(2)防止静密封面出现缺陷的措施提高产品铸造和金属加工质量,严格验收制度,做好试压工作;搞好防腐工作,防止垫片和介质对静密封面的腐蚀;选用的垫片硬度应低于静密封面硬度,安装垫片时防止异物压伤静密封面。
(3)预防法兰损坏的措施提高制造质量,严把产品的强度试验关;用力应均匀一致,切忌用力过猛过大,特别是铸铁和非金属阀门;阀门组装及阀门安装在设备或管道上时应正确,防止装偏强扭等现象。
(4)预防垫片失效的措施严格按技术要求检验垫片质量,不用过期和不合格的垫片;按照工况条件选用垫片,充分考虑温度与压力间的制约关系;严格按规定制作垫片,装好垫片,并试压合格;操作应平稳,防止温度压力的波动,操作阀门和其他设备应防止水击的产生,应有防水击设施;按时更换垫片。
垫片初漏应及时处理,以防垫片冲坏;金属垫片重用时,应进行退火和修复后使用;非金属垫片禁止重复使用。
相应地,对这些常见故障也可以采取如下的治理方法。
(1)预紧力不够的治理方法清除螺纹上污物,用煤油、石墨、除锈剂减少螺纹处阻力,然后从泄漏处慢慢地拧紧螺栓,对称、均匀、逐步向两边螺栓拧紧,至垫片不泄漏;采用焊接、强压胶等方法堵漏;采用适当的方法更换垫片或修复法兰。
(2)紧固件失灵的治理方法卸压停车更换紧固件;用G形工具卡住失灵的紧固件处,然后更换紧固件;松动的凝固件若完好时,可按正确的拧紧方法拧紧紧固件;采用适当的方法堵漏。
(3)静密封面缺陷的治理方法卸压停车修理静密封面;向静密封面内注胶堵漏;采用合适的堵漏方法堵漏或更换阀门。
(4)法兰损坏的治理方法卸压停车更换阀门;或采用带压粘接堵漏或注剂堵漏法进行修复。
(5)垫片失效的治理方法采用适当方法更换垫片;或向失效垫片内侧注入堵漏胶;或采用适当方法更换阀门。
4.密封面的常见故障是什么?这些故障产生的原因是什么?应采取什么防治措施来避免这些故障?密封面的常见故障有密封面不密合、损坏、混入异物、松脱、启闭件脱离、泄漏等。
产生这些故障的原因有以下几方面。
(1)发生密封面损坏的主要原因密封面不平或者角度不对、不圆、不能形成密合线;密封面材质不当或未按工况选用阀门,使用中产生腐蚀、冲蚀、磨损等;密封面加工时质量差,如堆焊和热处理时没按操作规程办事,造成硬度低、易磨损,或因合金元素烧损而被腐蚀,或因内应力过大而产生裂纹;进行表面处理时产生剥落或因研磨过量,失去原有性能;或因将截断阀作调节阀、减压阀使用,密封面被冲蚀;操作中关闭件已达到全关闭位置,仍继续施加大力关闭,密封面遭到破坏、挤压变形。
(2)密封面混入异物的主要原因不常开启或不常关闭的密封面上易沾积异物;或因设备和管道有锈垢、焊渣等卡在密封面上;或因介质有硬粒物嵌在密封面上。
(3)密封圈松脱的主要原因密封面碾压不严;或因密封面焊接不良;或因密封圈连接螺纹、螺钉、压圈等紧固件松动或脱落;或因密封面与阀体连接面不密合或被腐蚀等。
(4)启闭件脱落的原因由于操作不良,启闭件超过上、下死点还继续开关,造成连接处损坏断裂;或者由于关闭件与阀杆连接形式选用不当,易腐蚀、磨损而脱落。
(5)系统造成密封面泄漏的原因由于水击压力超限,将密封面损坏;或由于系统内温度和压力波动过大,导致密封面泄漏;或由于设备管道振动,造成关闭件松动而发生泄漏。