铸造工艺学课件第一章
合集下载
第一章铸造工艺基础

1-3铸造内应力、变形和裂纹
• 铸造内应力:铸件的固态收缩受到阻碍而引起的内应力。 • 残余内应力:一直保持到室温的铸造内应力 • 临时内应力:在冷却过程中暂存的铸造内应力 • 铸造内应力是铸件产生变形和裂纹的基本原因 • 按内应力产生原因不同分为热应力和机械应力 一、铸造内应力的形成 • 介绍热应力和机械应力的产生 1.热应力: • 1)定义:由于铸件的壁厚不均,各部分冷却速度不同,各部分收缩 不一致引起的内应力。 • 2)金属应力状态改变:(金属自高温至室温) • 金属在再结晶温度以上处于塑性状态,在再结晶温度以下处于弹性状 态,再结晶温度是分界点 • 塑性状态降温 弹性状态 • 弹性状态升温 塑性状态
流动性
二、浇注条件 • 1.浇注温度: “决定性”影响 浇温升高充型能力越强 • 实践中可利用此规律对薄壁铸件或流动性较差的合金可适当提高浇温, 提高充型能力 • 浇温也不宜过高,否则易产生缩孔、缩松等缺陷 • 2.充型压力 • 合金受压越大充型能力越强 三、铸型填充条件 • 1.铸型材料: • 铸型导热系数和比热容升高,合金充型能力下降 • 2.铸型温度: • 铸型温度升高减缓冷却速度,充型能力升高 • 3.铸型中气体: • 铸型中气体阻碍液体合金的充型,应减少之.
三、铸件的裂纹与防止 • 铸造内应力超过材料强度极限时产生裂纹 1.热裂 • (1)定义:在高温下形成的裂纹 • (2)形状特征:缝隙宽、形状曲折、缝内呈氧化色 • (3)形成原因:合金完全凝固前固态收缩已开始,晶粒间存在液体, 强度、塑性低 • (4)分布:一般分布在应力集中部位 • (5)主要影响因素:合金性质、铸型阻力 • (6)防止方法①使铸件结构合理②改善铸型和型芯的退让性③减少 浇、冒口对铸件收缩的机械阻碍④内浇口设置符合同时凝固原则⑤减 少合金中有害杂质含量。 2.冷裂 • (1)含义:在低温下形成的裂纹 • (2)形状特征:裂纹细小,呈连续直线状,缝内呈轻微氧化色 • (3)分布:常出现在形状复杂工件的受拉伸部分
第一章铸造工艺基础38页PPT

缩孔易出现的部位
缩松的形成 P43
原因:铸件最后凝固的收缩未能得到补足,或者结晶温度范围宽的合 金呈糊状凝固,凝固区域 较宽,液、固两相共存,树枝晶发达,枝 晶骨架将合金液分割开的小液体区难以得到补缩所致。
定向凝固
定向凝固的缺点和应用: 缺点——铸件成本高,加大铸造内应力(易变形、开裂)。 应用——体收缩大的合金,如铸钢、铝青铜和铝硅合金等。
二、铸件的变形与防止: P46
对于厚薄不均匀、截面不对称等铸件,内部 会产生变形来达到平衡。受拉伸的部分会产生压 缩变形,受压缩的部分会会产生拉伸变形。
框形铸件变形
T形梁铸钢件变形
铸件的变形
有的铸件虽无明显的变形,但经切削加工后, 破坏了铸造应力的平衡,产生变形甚至裂纹。
圆柱体铸件加工后的变形
表面被加工 掉一层后
砂型 砂型 砂型 砂型
铸钢 C=0.4%
砂型 砂型
铝硅合金(铝硅明)
金属型(300℃)
镁合金(含Al及Zn)
砂型
锡青铜(Sn=10%,Zn=2%)
砂型
硅黄铜(Si=1.5~4.5%)
砂型
1300 1300 1300 1300 1600 1640 680~720 700 1040 1100
1800 1300 1000 600 100 200 700~800 400~600 420 1000
1. 各种成形方法的原理、特点及适用范围; 2. 各种零件的结构工艺性; 3. 常用工程材料的性能特点
第一章
铸造工艺基础
铸 造 生 产 过 程
P37
铸造优点:
1)易制造形状复杂制件
– 液态金属流动性→复杂外
形
– 型芯 →复杂内腔
铸造工艺图ppt课件

可编辑课件PPT
19
设
计
要
点
铸造工艺 方案的确定
工艺参数 的确定
浇注系统 和冒口
铸造工艺 图的绘制
铸造工艺设计包括:
Ø选择铸造方法或造型方法
Ø铸件的浇注位置和分型面位置,型芯和芯头结构;
Ø加工余量、收缩率和拔模斜度等工艺参数;
Ø浇注系统、冒口和冷铁的布置等;
Ø将所确定的工艺方案用文字和铸造工艺符号在零件图
可编辑课件PPT
25
1.2 铸造工艺图概述
可编辑课件PPT
26
浇注位置,分型面,分模面,活块,本模的类型和 分型负数,加工余量,拔模斜度,不铸孔和沟槽, 砂芯个数和形状,芯头形式、尺寸和间隙,分盒面, 芯盒的填砂(射砂)方向,砂芯负数,砂型的出气孔, 砂芯出气方向、起吊方向,下芯顺序,芯撑的位置、 数目和规格,工艺补正量,反变形量,非加工壁厚 的负余量,浇口和冒口的形状和尺寸,冷铁形状和 个数,收缩筋(割筋)和拉筋形状、尺寸和数量,和 铸件同时铸造的试样,铸造收缩率等
21
1.1. 3 设计的内容和程序
选择铸造方法或造型方法 铸件的浇注位置和分型面位置,型芯和芯头结构; 加工余量、收缩率和拔模斜度等工艺参数; 浇注系统、冒口和冷铁的布置等; 将所确定的工艺方案用文字和铸造工艺符号在零件图上表示出 来,绘制铸造工艺图。
工作程序:审图—初步方案—讨论—确定—设计—
会签—修改—生效。
可编辑课件PPT
7
四羊方尊 高58.3厘米;重 34公斤。1938年湖南 省宁乡县出土。商代 方尊的代表。 铜尊盛行于商代和 西周时期,是一种饮 酒用具。这件四羊方 尊是现存商代青铜方 尊中最大的一件,是 国家特级文物。 被认为是中国青 铜铸造史上最杰出的 作品之一 。
第一章铸造用砂铸造工艺学
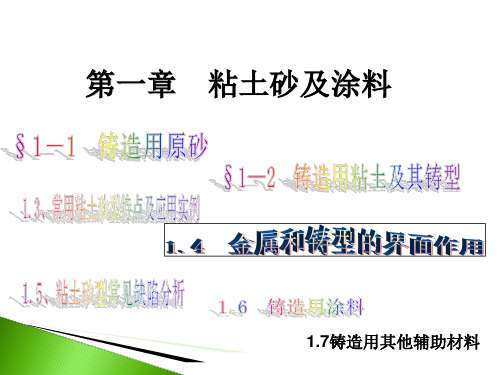
序号
1 2
3
4 5
6
7 8 9
1 0
1 1
底盘
3 1. 筛孔尺 寸(mm) . 7 3 0 5
美国筛 号 6 1 2
0. 8 5 0
2 0 0. 8 4 1
0 . 6 0 0
0. 4 2 5
0. 3 0 0
5 0 0. 2 9 7
0 . 2 1 2
0 . 1 5 0
0. 1 0 6
0. 0 7 5
橄榄石砂(olivine sand) 矿物组成及化学成分:[(Mg,Fe)2SiO4]是由含Mg2SiO4高的 橄榄石制成。见图。铸造用橄榄石常含有5-10%的铁橄榄石。 性能:熔点1600-1760 ℃ 、热膨胀率比石英小而且均匀(见图12-10),不易发生夹砂类缺陷。烧结点低1200℃,但不为金属润 湿,具有化学惰性。与钢液接触形成致密层防止粘砂。同时,由 于无晶型转变,热膨胀率低,故不易产生夹砂类缺陷。 规格:根据中国造型公司企业标准XQ/ZQS-4-86,按物理化学性 能分两级,按粒度分两组(见表)。生产中通过破碎、细磨、分 级、水洗。 应用:用于高锰钢铸件可防止铸件粘砂,也可防止对人体的危害。
3.镁砂(magnesite) 主要成分 主要成分为MgO,(菱镁矿)MgCO2→MgO+CO2。 菱镁矿高温煅烧(1500-1650℃)使MgO重结晶、烧 结、破碎、分选。
性能:熔点高、蓄热系数高(是石英砂的一倍半)、 热膨胀率比石英小,无相变引起的体积膨胀、化学 性能稳定,不与MnO、FeO反应,用于锰钢可防止 粘砂。 规格:见表,按MgO的含量,有两种规格。
表1-6不同耐火材料的蓄热系数和铸件在型壳中的凝固时间
耐火材料 名称 型壳的初 蓄热系数 凝固 始温度 (J/(m2•℃•s1/ 时间 2) 20 1115.2 54 20 836.4 100. 8
铸造工艺学ppt综述

第三篇
第一章铸造工艺设计概论
铸南
造昌
➢设计概念、依据、内容及程序
工大
艺学
学机 C电
➢工艺设计与经济、环境的关系
A工
I程
课学
件院
EXIT
§1-1 工艺设计的概念、依据、内容及程序
一、概念
铸造工艺设计:就是根据铸造零件的结构特点、技术要求、 生产批量和生产条件等,确定铸造方案和工艺参数,绘制铸造工 艺图,编制工艺卡等技术文件的过程。
名 称
工艺符号和表示方法
用红色线表示,在任一端画 分 “<”符号
模
分
线
型
用红色线表示
线
分
型
分
模线Βιβλιοθήκη 铸造工艺符号及表示方法名 称
工艺符号和表示方法
用红色线表示,在加工符号
附近标注加工余量数值
凡带斜度的加工余量应标注
斜度 机 械 加 工 余 量
名 称
工艺符号和表示方法
芯 用蓝色线表示,并标注斜度 头 和间隙数值。 有两个以上型芯 斜 时,用数字“1#”“2#”等标注 度 与 芯 头 间 隙
铸造工艺设计的一般内容
项 目
内
容
用途及应用范围
在零件图上,用标准(JB2435-78)规定的
用于制造模样、模
铸 造 工
红、蓝色符号表示出:浇注位置和分型面、
板、芯盒等工艺装备, 也是设计这些金属模具
加工余量、铸造收缩率(说明)、起模斜度、 的依据,还是生产准备
艺 模样的反变形量、分型负数、工艺补正量、 和铸件验收的根据
◆ 铸造工艺设计中要注意节约能源。如采用湿型铸造比干型 铸造节省燃料消耗,也可采用自硬砂型取代普通干砂型等。
第一章铸造工艺设计概论
铸南
造昌
➢设计概念、依据、内容及程序
工大
艺学
学机 C电
➢工艺设计与经济、环境的关系
A工
I程
课学
件院
EXIT
§1-1 工艺设计的概念、依据、内容及程序
一、概念
铸造工艺设计:就是根据铸造零件的结构特点、技术要求、 生产批量和生产条件等,确定铸造方案和工艺参数,绘制铸造工 艺图,编制工艺卡等技术文件的过程。
名 称
工艺符号和表示方法
用红色线表示,在任一端画 分 “<”符号
模
分
线
型
用红色线表示
线
分
型
分
模线Βιβλιοθήκη 铸造工艺符号及表示方法名 称
工艺符号和表示方法
用红色线表示,在加工符号
附近标注加工余量数值
凡带斜度的加工余量应标注
斜度 机 械 加 工 余 量
名 称
工艺符号和表示方法
芯 用蓝色线表示,并标注斜度 头 和间隙数值。 有两个以上型芯 斜 时,用数字“1#”“2#”等标注 度 与 芯 头 间 隙
铸造工艺设计的一般内容
项 目
内
容
用途及应用范围
在零件图上,用标准(JB2435-78)规定的
用于制造模样、模
铸 造 工
红、蓝色符号表示出:浇注位置和分型面、
板、芯盒等工艺装备, 也是设计这些金属模具
加工余量、铸造收缩率(说明)、起模斜度、 的依据,还是生产准备
艺 模样的反变形量、分型负数、工艺补正量、 和铸件验收的根据
◆ 铸造工艺设计中要注意节约能源。如采用湿型铸造比干型 铸造节省燃料消耗,也可采用自硬砂型取代普通干砂型等。
铸造工艺学课件第一章

有机物燃烧,化合物分 解,产生大量气体,又 叫“发气区”,有可能 导致气孔。
图1-5 浇注后某一瞬间砂型水分的分布
I-完全烘干区;II-水分饱和凝聚区;III-水分不饱和凝聚区;
IV-正常区
铸造工艺学
第1章 金属与铸型的相互作用
3.湿分迁移导致铸型湿度与温度变化
干燥区厚度与铸件尺 寸,浇注温度、浇注后 时间有关;
铸造工艺学
第1章 金属与铸型的相互作用
图1-7 石英的同质异构变化
纵向转变为同类转变,即在同一类型晶型中,在高低温晶型
间发生的转变,这种转变不必断开和重新键合硅氧键,只需将
原来骨架上的硅氧四面体稍作扭动,作一些位移,即可完成。
这种转变需要的能量低,速度也较快,故称为快转变,又称位
移转变。
铸造工艺学
(2)吸附水 一般指黏土胶团中的外吸附层和扩散层中的水。它被吸 附在黏土质点表面上,而不进入晶格中,吸附水与黏土质点的结合不 像矿物组成水那样牢固。
(3)自由水 一般指远离黏土质点而机械混入的水。
铸造工艺学
第1章 金属与铸型的相互作用
黏土加热到100℃以上就失去全部自由水。随着水 分的去除,黏土质点相互靠近,出现收缩。
铸造工艺学
第1章 金属与铸型的相互作用
图1-6 硅氧四面体和β石英四面体的连接 (a)硅氧四面体 (b) β石英四面体的连接
铸造工艺学
第1章 金属与铸型的相互作用
图1-7 石英的同质异构变化
横向的转变为同级转变,即在不同类型晶型间发生转变, 这种转变必须使硅氧骨架中Si-O-Si键断开后重新键合,转变过 程需很大能量,速度也慢,又叫慢转变,亦称重建转变。
第1章 金属与铸型的相互作用
在浇注时,铸型被加热的时间较短,整个铸型的温度也
铸造工艺学第1章

2.粘砂
粘砂是铸钢、铸铁件生产中常见的铸造缺陷之一。根据 将砂层粘结在铸件表面的粘结物质的性质,粘砂可分为机械 粘砂即金属渗入到砂粒间空隙,将砂粒固定在铸件表面;化 学粘砂即金屑或金屑氧化物和造型材料形成化合物,将砂层 枯结在铸件表面。
或多角形的天然石英砂,粒度最好均匀分布在相邻四个筛号 上,每个筛号上的停留量都在10~35%之间。
铸铁件湿型砂普遍采用粘结性能较好的膨润土。
2.煤粉的作用原理及应用
(1)煤粉受热燃烧产生大量的还原性气体,防止铁水被氧化, 减少或防止金属氧化物与造型材料发生化学反应。 (2)煤粉在高温液态金属热作用下产生大量的气体,使金属 与铸型材料之间和砂粒孔隙中的气体压力猛增,有效地防止 液态金属的渗入。 (3)煤粉受热软化,结焦变成胶质体,堵塞或减少砂粒的孔 隙,使液态金属难以渗入。 (4)煤粉中的挥发分在400℃以上的还原性气氛下裂解成光 亮碳,它是一种微晶碳或不定型石墨,不被铁水及其他氧化 物所润湿,有效隔绝了金属与铸型界面发生反应。 (5)煤粉加热到一定温度的,干馏出煤焦油成为具有可塑性 的胶质体,使型砂的塑性、退让性增加,减少型砂因受热膨 胀而产生的内应力,有利于防止铸件产生夹砂等缺陷。
2.铸型的水分迁移
湿型被金属液急剧加热时,
砂型中的水分会从高温的表 面层向低温的里层迁移。由 于水分迁移的结果,在湿型 中出现四个区域,如图1-13 所示,第一区域——干燥区 (a区);第二区域——水分 饱和凝聚区(b区);第三区 域——过渡区(c区),也叫 水分不饱和凝聚区;第四区 域——正常区(d区),它是 从铸型温度为室温至砂箱壁 处。
3.铸钢件湿型砂
铸钢件湿型砂的含水量应严格控制,一般为4~5%左右, 面砂的透气性应大于100,背砂的透气性应在180~200以上, 湿压强度应大于55kPa,铸型的表面硬度应在80~90左右。手 工造型时型砂的紧实率控制在50~55%。
1铸造-铸造工艺基础.ppt-铸造

防止措施:
(1)铸件壁厚要尽量均匀,并使之
形状对称。 (2)尽量采用同时凝固原则。 (3)反变形法。 (4)时效处理。
三、铸件的裂纹与防止
1、热裂:高温下形成的裂纹。 形状特征:缝隙宽、形状曲折、缝内呈 氧化色。 主要影响因素: 合金性质 凝固时期受到阻碍
⑵ 冷裂:低温下形成的裂纹。 形状特征:裂纹细小、呈连续直线 状,有时缝内呈轻微氧化色。
灰铸铁、硅黄铜流
动性最好; 铸钢流动性最差。 影响合金流动性的 主要因素:化学成分
二、浇注条件
1、浇注温度 2、充型压力
三、铸型填充条件
1、铸型材料:导热系数、比热容
2、铸型温度
3、铸型中气体 4、铸件结构
第二节 铸件的凝固与收缩
一、铸件的凝固方式
逐层凝固方式:纯金属或共晶合金 糊状凝固方式:合金的结晶温度范围宽 中间凝固方式:介于上述二者之间。
三、铸件中的缩孔与缩松
1. 缩孔和缩松的形成
缩孔:集中在铸件上部或最后凝固部位容积较大的孔洞.
缩松:分散在铸件某区域内的细小缩孔。
宏观缩松 显微缩松
逐层凝固合金:缩孔倾向大; 糊状凝固合金:缩松倾向大。
2、 缩孔和缩松的防止
顺序凝固(定向凝固)原则: 在铸件上可能出现缩孔的厚 大部位通过安放冒口等工 艺措施,使铸件远离冒口 的部位先凝固,而后是靠 近冒口的部位凝固,最后 才是冒口本身的凝固。
⑴ 热应力:由于铸件
壁厚不均匀、各部分冷却速度 不同,以至在同一时期内铸件 各部分收缩不一致而引起的。
1杆:拉应力
2杆:压应力:
温 度 (℃) 浇口
同时凝固温度曲线铸件源自冷铁 ⅢⅠ Ⅱ 距离
铸件实现同时凝固示意图
- 1、下载文档前请自行甄别文档内容的完整性,平台不提供额外的编辑、内容补充、找答案等附加服务。
- 2、"仅部分预览"的文档,不可在线预览部分如存在完整性等问题,可反馈申请退款(可完整预览的文档不适用该条件!)。
- 3、如文档侵犯您的权益,请联系客服反馈,我们会尽快为您处理(人工客服工作时间:9:00-18:30)。
有机物燃烧,化合物分 解,产生大量气体,又 叫“发气区”,有可能 导致气孔。
图1-5 浇注后某一瞬间砂型水分的分布
I-完全烘干区;II-水分饱和凝聚区;III-水分不饱和凝聚区;
IV-正常区
铸造工艺学
第1章 金属与铸型的相互作用
3.湿分迁移导致铸型湿度与温度变化
干燥区厚度与铸件尺 寸,浇注温度、浇注后 时间有关;
有机物质燃烧或升华;化合物分解(如硼酸受热后,经过
几次脱水,最后分解为硼酐);石英砂粒的同质异构转变;
型壁的膨胀与收缩;型壁强度的变化等。
在机械作用下,液体金属对铸型冲击、冲刷,使型
腔胀大,砂芯变形等。
在化学和物理化学作用下,金属的氧化与燃烧;铸
型材料与金属或金属氧化物化学反应、黏结,造型材料
发气等。 这些伴生现象
不利情况下
使铸件产生各类缺陷!!!
铸造工艺学
第1章 金属与铸型的相互作用
1.2 金属与铸型的热作用 1.2.1 金属对铸型的加热及铸件的冷却
研究在不同时间内铸型各 点温度变化的情况,以及铸 型在不同时间内所吸收的热 量,其方法有解析计算法、 模拟法(电模拟和水力模拟)和 实验法等。
图1-2铸型的加热与铸件的冷却曲线 1-铸件; 2-铸型。
第四区域—正常区。
铸造工艺学
第1章 金属与铸型的相互作用
4.根据湿分迁移的理论,在铸型工艺方面应注意以下几个问题:
(1)扎通气孔
深度应透过水分凝聚区,即快到模型表面,又要防止扎坏 模型的工作表面,通气孔直径5~8mm。
(2)采用面砂和背砂
面砂采用含水量少、强度高、颗粒较细的型砂,背砂采 用颗粒较粗、透气性较好的型砂。
图1-1 型砂结构示意图 1-原砂2-黏结剂 3-附加物 4-孔隙
铸造工艺学
第1章 金属与铸型的相互作用
砂型是一种微孔-多孔隙体系,或者 毛细管-多孔隙体系。
液体金属在浇注、凝固、冷却过程中 会和铸型发生热的、机械的、化学和物 理化学的相互作用。
图1-1 型砂结构示意图 1-原砂2-黏结剂 3-附加物 4-孔隙
铸造工艺学
第1章 金属与铸型的相互作用
图1-6 硅氧四面体和β石英四面体的连接 (a)硅氧四面体 (b) β石英四面体的连接
铸造工艺学
第1章 金属与铸型的相互作用
图1-7 石英的同质异构变化
横向的转变为同级转变,即在不同类型晶型间发生转变, 这种转变必须使硅氧骨架中Si-O-Si键断开后重新键合,转变过 程需很大能量,速度也慢,又叫慢转变,亦称重建转变。
第1章 金属与铸型的相互作用
在浇注时,铸型被加热的时间较短,整个铸型的温度也
不高,同时又缺乏矿化剂。因此,由α石英转变为α鳞石英
和α方石英是难以进行的。
对铸造生产来说,必须考虑的是在573℃,由β石英转
变为α石英时的体积膨胀问题,它是快转变。一旦加入到
573℃,相变立即发生,同时伴有体积膨胀,体积膨胀为
铸造工艺学
第1章 金属与铸型的相互作用
1.2.4 夹砂
夹砂又叫包砂、结疤和鼠尾等,是铸件常见的一类表面缺 陷,特别是用湿型铸造厚(1)夹砂结疤:它是金属液进入裂纹 把拱起的砂型表层包在铸件内,就 成为夹砂结疤;它的特点是:在铸 件表面上有局部凸出的形状不规则 的金属瘤状或片状物,在它的下面 有一层型砂。如图1-8 (a)所示。
0.82%。
虽然这时的体积膨胀不到1%,但由于这个转变是突然
产生的,因此,它将影响铸件的尺寸精度,并可能使铸件
产生夹砂、胀砂等缺陷。
铸造工艺学
第1章 金属与铸型的相互作用
2.黏土的干缩
水分在黏土中的存在形式有以下几种: (1)矿物组成水 包括结构水、结晶水和晶层水等三种。结构水是以 H+和OH-离子的形式存在于矿物的结晶格架的一定位置上,它有一定 的数量。结晶水是以水分子H2O的形式存在于矿物结晶格架的一定位 置上,也有一定的数量。晶层水是以水分子H2O的形式存在于晶层之 间,其数量不定。
5-25.2mm;6-50.8mm;7-101.6,mm
图1-4 湿型受热时温度变化曲线
从图中可看出: (1)浇注后,铸型内表面温度迅速地接近液体金属的温度, 但此时,铸型其它部分仍然处于相当低的温度。
铸造工艺学
第1章 金属与铸型的相互作用
图1-3干型的加热曲线 1-型面;2-2.7mm;3-6.5mm;4-13.3mm
铸造工艺学
第1章 金属与铸型的相互作用
总的来看,型砂在加热时的膨胀可分为两个阶段。 当石英砂的膨胀能被黏土的收缩所抵消,或者说当 石英砂粒间的相互移动的阻力小于砂型外部的阻力时, 仅减少砂粒之间的空隙,并不引起铸型尺寸的变化,这 个阶段称为显微膨胀。 当砂粒间的间隙难以减小,或者砂粒间的相互移动 的阻力大于砂型外部的阻力时,将引起铸型尺寸发生变 化,这个阶段称为宏观膨胀。铸件的很多缺陷,如裂纹、 夹砂和尺寸不符等主要是由型砂的宏观膨胀造成的。
铸造工艺学
第1章 金属与铸型的相互作用
1.解析计算法
铸件与铸型的热交换是属于不稳定的导热问题。 因此,运用解析计算法研究铸型温度场时,一般作了下列 的假设: (1)铸型与铸件的接触面是一个平面; (2)铸型与铸件在界面上的温度是相同的; (3)铸型与铸件平面都是无限大的,即只考虑一维方向的热 传导;
第1 章 金属与铸型的相互作用
第1章 金属与铸型的相互作用
1.1 概述
普通型砂是由原砂、黏土和水等按 一定比例混制成的。
原砂是型砂的骨架,黏土是黏结剂, 它被水润湿后,在砂粒表面形成一层黏 土薄膜,把松散的砂粒黏结在一起,使 型砂具有一定的工艺性能。在被黏土膜 包围的砂粒之间,有一定的孔隙,它使 型砂具有一定的透气性。
一般铝镁合金铸件, 浇注1分钟后,干燥区 厚度约3~6mm。
特点是“三高一少”,
即温度高、强度高、水
图1-5 浇注后某一瞬间砂型水分的分布
蒸汽压高,水分少。
I-完全烘干区;II-水分饱和凝聚区;III-水分不饱和凝聚区; IV-正常区
铸造工艺学
第1章 金属与铸型的相互作用
第二区域—水分饱和凝聚区。 温度100℃区域 蒸发界面 型内的水分蒸腾或蒸发在干 燥区和本区的界面上发生, 此界面称为蒸发界面。
铸造工艺学
第1章 金属与铸型的相互作用
1.解析计算法
铸件与铸型的热交换是属于不稳定的导热问题。 因此,运用解析计算法研究铸型温度场时,一般作了下列 的假设: (4)在整个过程中,铸型材料的各热物理参数不随温度变化; (5)不论在铸件或铸型中都不发生吸热及放热反应; (6)浇注时,液体金属对型腔中空气的加热以及因对流热传 导造成的热量损失,不予考虑。
水分饱和凝聚区的扩大
含水量约10~15%,为正常水分的2~3倍,出现自由水;热湿拉 强度比常温抗拉强度低得多(正常区的1/3~1/10),
铸造工艺学
第1章 金属与铸型的相互作用
第二区域—水分饱和凝 聚区。 砂型容易产生表层与里 层脱离的现象,产生夹 砂缺陷。
凝聚的水容易堵塞孔隙, 导致排气不畅,易产生 气孔
当浇注时,铸型被迅速加热,加热的程度随着距型 腔表面远近而不同,表面层温度高,里层温度低,水分 及水蒸气除部分变成蒸汽从冒口、冒气孔逸出外,其余 大部分都向铸型里层迁移。
铸造工艺学
第1章 金属与铸型的相互作用
3.湿分迁移导致铸型湿度与温度变化
第一区域—干燥区, 又叫完全烘干区。
型腔表面至100℃处, T>100 ℃;水分蒸发较 多:全部自由水、大部 分吸附水和部分结构水;
铸造工艺学
第1章 金属与铸型的相互作用
这三方面的作用是紧密联系、互相促进的。其中热作 用是其它两方面作用的基础,且它们的作用是随热作用的 剧烈程度而变化的,如果金属对铸型的加热越剧烈,则其 它两方面的作用就越严重。
还会在铸型中产生各种伴生现象。
铸造工艺学
第1章 金属与铸型的相互作用
在热作用下,型腔表面层的水分向铸型里层迁移;
5-25.2mm;6-50.8mm;7-101.6,mm
图1-4 湿型受热时温度变化曲线
(3)干型表面层的温度比湿型高。
铸造工艺学
第1章 金属与铸型的相互作用
1.2.2 铸型湿分的迁移和强度变化
1.湿分迁移: 湿分是水分和水蒸汽的总称。湿分迁移是指铸型中
水分和水蒸汽从型腔表面层向铸型内部迁移的现象。 2.湿分迁移的方向:
(3)在铸造大型铸件肘,可采用干型或表面干型
先将铸型于350~400℃进行烘干,可使干强度比湿强度提
高5~10倍,透气率提高50%。
铸造工艺学
第1章 金属与铸型的相互作用
1.2.3 铸型体积的变化 1.原砂的膨胀
受热后,原砂的体积将发生膨胀。其原因主要有两个 方面: 一是因温度升高而产生热膨胀,为受热均匀膨胀; 二是因温度升高发生相变(β石英发生同质异构变化)而产 生的体积膨胀。
图1-8 夹砂的形成 (a) 夹砂;(b)鼠尾
铸造工艺学
1.2.4 夹砂
第1章 金属与铸型的相互作用
夹砂又叫包砂、结疤和鼠尾等,是铸件常见的一类表面缺 陷,特别是用湿型铸造厚大的平板类铸件时,更常出现。一 般将夹砂分两种形式。
(2)鼠尾:型腔下表面层在金属液热 作用下发生翘起,特点是:在铸件 表面上出现浅的方向性凹槽或不规 则的折痕,无金属瘤状物,形状似 老鼠尾巴,故称鼠尾,通常沿下型 内浇口正前方产生,如图1-8 (b)所 示。
由于晶体结构的差异,高岭石和蒙脱石的含水形式、 数量有较大差异。其收缩的特点也大不一样。
高岭石在低温加热时因脱水较少,收缩并不显著, 在400~700℃失去结构水,体积出现收缩。
铸造工艺学
第1章 金属与铸型的相互作用
蒙脱石在低温加热时脱水多,收缩显著。 尤其是在100~200℃左右肘,失去了大量的吸附水和晶 层水,因此产生了显著的收缩。 继续加热到550~750℃左右,失去结构水,而这时的体 积变化并不最显著。 蒙脱石与高岭石在加热过程中,其体积变化有明显的不 同。高岭石的主要收缩发生在较高的温度范围;而蒙脱 石的主要收缩则发生在较低的温度(100~200℃)范围内。