宽厚板生产线工艺流程.
宽厚板生产工艺设计

宽厚板生产工艺设计摘要本文对中厚板目前在我国的发展状况形式及中厚板轧制过程中的轧制规程、轧制方法及道次的确定进行阐述,并且对中厚板在轧制中的工艺、参数、设备,进行了进一步说明。
关键词:中厚板 ;轧钢工艺;轧钢设备Design of the production process of heavy plateAbstractIn this paper, plate current form of development in China and in the process of plate rolling schedule, rolling method and passes the determination to elaborate, and on the plate in the rolling process, parameters, equipment, further instructions.Key words: plate; steelrolling process; steelrolling equipment目录第1章绪论.......................................... 错误!未定义书签。
1.1国内中厚板生产简介................................... 错误!未定义书签。
1.2国外中厚板轧机的发展................................. 错误!未定义书签。
1.3中厚板生产的进步 (4)1.3.1生产技术方面的进步 (4)1.3.2装备方面的进步........................................................................... 错误!未定义书签。
1.4我国中厚板发展的不足................................. 错误!未定义书签。
宽厚板的加热、轧制和冷却技术

2一 0 取样贯 2 一扮线装! 2 一 1 2 冷娇机
图 3 德 国迪林根厚板厂工艺图
本也开始建立了发m优势。之后, 一些新工艺技 术、 控制系统和装备得到了开发与应用, 其中宽厚 板轧制新技术主要有 1高尺寸精度轧制技术。如r ) 射线测厚仪、 立 辊轧边机、 A 液压 WC系统、 工作辊移动( S + WR ) 强力弯辊( B 、 WR )成对交叉辊轧机(C 和连续可 P) 变凸度轧机(V ) 皮 C C等一术的应用, 提高了厚板尺寸 控制精度; 2平面形状控制伎术。如 M S ) A 平面形状控制 法、 狗骨轧制法及T P F 技术在日 芬兰、 本、 英国、 瑞 典等宽厚板轧机上得列了应用; 3控轧控冷技术。T C 工艺已成为宽厚板 ) MP 生产的主导工艺, 采用此技术生产的钢板已占3% 0 - 0 其板坯加热溢度为90 1 I, 5%, 5 一1 C 出炉温 5 0 度低于常规 轧制, 但混差小于 3'。此外, 0 C 宽厚板 生产品种多、 用途广、 现格大, 因而国外宽厚板生产 已 经普遍由 计算机进行 设定、 控制。
1 . x . 15 7 2 4
千叶厚板厂
全箱式炉型
8 3 0 3 . x . 5
加古川厚 h ’ / v
炉型
9 0 1 1 0 7 15 1
‘ ik声波探伤(/) _ 一 J 一 o A V_
热矫直、标记轧制批号 一 卜 一一
成检w 、扎,板志试打- , 品查 面尺 . 标 样印一 a r 品
L卜 部 查 试 打 冷 _外 松 、 样 印
一争 人工超声波探伤 ( , 供货状态) 一 1 一
最终检查伏 面、板形尺寸和标心
- il线装置 一 , - t ,
宝钢宽厚板切割生产线

宝钢宽厚板切割生产线1. 项目简介宝钢宽厚板工程是宝钢“十五”计划重点项目。
工程分两期建设,一期建设一架四辊可逆精轧机,一架立辊轧机,轧制最大宽度4.8米,长25米,厚150毫米,年产140万吨宽厚板。
二期增建一架粗轧机,生产规模扩展到180万吨,最大轧制厚度可达400毫米。
产品以船用板及管线板为主,同时还生产建筑、锅炉容器、模具等国内紧缺钢板品种,专用板约占90%左右。
作为我国第一套特宽幅现代化宽厚板轧机生产线,该工程的建设将改变我国5米级造船用板,大口径、长距离、高钢级、抗硫化氢管线用板长期依赖进口的状况。
该生产线由板坯接收跨、板坯跨、加热炉区、主轧跨、主电室、磨辊间、冷床跨、剪切跨、中转跨、热处理跨、涂漆跨以及末端成品跨等组成。
经过连铸、精轧、热矫直、超声波探伤、火焰切割、热处理、喷印等工序形成最终宽厚板产品,工艺图如下图所示。
宽厚板生产工艺流程图火焰切割系统作为宽厚板生产线的一个重要工序,主要用于大于50mm厚带温(最高温度350℃)钢板的定尺切割(切头、切尾、横向及纵向切割、废边切割)和取样切割,以及特殊尺寸钢板的切割,切割出来的成品可以直接满足用户订货的尺寸要求并直接在钢板上冲打产品信息。
该项目功能需求新颖、难度大,在国内首创,国外也仅有日本有类似系统。
而且相比日本的类似系统,宝钢还提出了废边切割、双工位切割等需求,此外该系统还解决了对于钢板的轮廓扫描和定位、热钢板切割过程中钢板尺寸变化的温度补偿等高难度技术问题。
该宽厚板生产线的上位监控系统除了对切割过程进行自动化监控外,还集成了大量特殊的算法和独特的功能,易控(INSPEC)软件由于具有强大的二次编程能力,可以把常规的监控功能与使用高级语言开发的软件功能模块无缝集成到一起,因此选用了易控(INSPEC)软件作为系统的开发平台。
2.系统构成该宽厚板切割系统采用分层设计,整个控制系统由L3管理系统、CCC中心计算机系统、NC控制计算机系统、底层运动控制单元等构成。
宽厚板轧制工艺

展宽轧制有纵向展宽轧制、横向展宽轧制和角轧展宽 轧制三种。横向展宽轧制是目前厚板厂普遍使用的方
式。
2013-7-11 4
宽厚板轧制工艺
3)精轧(Final Rolling)阶段
精轧轧制的目的
质量控制
轧制延伸
通过板形控制、厚度控制、性能控制及表 面质量控制等手段生产出板厚精度高、同板差 小、平坦度好及具有良好的综合性能的钢板。
控轧轧制(TMR)
控制轧制手段
成份:Nb、V、Ti等碳氮化物生成元素是发挥控制轧制 效果的重要元素。 加热:采用通过低温加热,初期粒径变小,也是实现细
粒化的方法。
轧制:未再结晶区域的强压下,两相区的轧制是目前控 制轧制最有效的手段。
2013-7-11 13
宽厚板轧制工艺
控轧轧制(TMR)
单机架多块钢轧制工艺
11
宽厚板轧制工艺
控轧轧制(TMR)
第三阶段:(γ +α )两相区的 轧制(<Ar3) 如在两相共存区进一步轧制,
未相变的奥氏体晶粒更加伸长,
在晶粒内形成形变带。另一方面, 已经相变完成的铁素体晶粒中因
冷加工会形成位错密度高的亚晶
粒。其结果变成真正的晶粒细化。
2013-7-11
12
宽厚板轧制工艺
宽厚板轧制工艺
宽厚板轧制工艺
-轧线工艺
制作:胡贤磊
时间:2008年3月
2013-7-11
1
宽厚板轧制工艺
厚板轧制特点
厚板轧制的特点是尺寸规格繁多、轧制 中要求有展宽轧制。
厚板轧制过程一般分为以下三个阶段。
成形轧制、展宽轧制、精轧轧制
2013-7-11
2
宽厚板轧制工艺
宽厚板轧制工艺

4/9/2020
9
控轧轧制(TMR)
➢ 第一阶段:再结晶区轧制 (≥950℃) 经高温加热晶粒变粗的奥 氏体随着反复 轧制-再结晶 而逐步变细。再结晶及其以 后的晶粒成长是短时间发生 的,未见明显的微细化。在 再结晶温度领域的下限附近 的强化轧制,由于因轧制引 起的再结晶晶粒细化而使奥 氏体晶粒明显变化。
宽厚板轧制工艺
12
控轧轧制(TMR)
➢控制轧制手段
宽厚板轧制工艺
成份:Nb、V、Ti等碳氮化物生成元素是发挥控制轧制 效果的重要元素。
加热:采用通过低温加热,初期粒径变小,也是实现细 粒化的方法。
轧制:未再结晶区域的强压下,两相区的轧制是目前控 制轧制最有效的手段。
4/9/2020
13
控轧轧制(TMR)
宽厚板轧制工艺
宽厚板轧制工艺
-轧线工艺
制作:胡贤磊 时间:2008年3月
4/9/2020
1
宽厚板轧制工艺
厚板轧制特点
厚板轧制的特点是尺寸规格繁多、轧制 中要求有展宽轧制。
厚板轧制过程一般分为以下三个阶段。
成形轧制、展宽轧制、精轧轧制
4/9/2020
2
宽厚板轧制工艺
1) 成形轧制(Sizing Rolling)阶段
4/9/2020
5
厚板轧制过程示意图
宽厚板轧制工艺
4/9/2020
6
控轧控冷(TMCP) 技术
➢TMCP材特点:
宽厚板轧制工艺
强度、韧性、可焊性的统一;
降低成本、提高加工性能。
4/9/2020
7
控轧控冷(TMCP) 技术
宽厚板轧制工艺
➢控轧轧制(TMR)
固溶强化: 添加C,Mn,Si,Ni 等合金元素;
宽厚板工艺流程

宽厚板工艺流程宽厚板工艺流程宽厚板是一种广泛应用于建筑、电力、汽车和机械制造等行业的金属材料。
在其生产过程中,需要经历多个工艺流程来保证产品质量和性能。
首先,原材料准备是宽厚板生产的第一步。
通常使用的原材料包括钢坯和钢带。
这些原材料需要经过检验和筛选,以确保其符合生产标准和要求。
接下来是钢坯预处理。
钢坯通常需要经过切割、破碎和清洗等处理工艺,以去除表面氧化物、气孔和杂质,并为后续的加工做好准备。
然后是热轧工艺。
热轧是宽厚板生产的核心工艺之一。
在这个过程中,钢坯经过预热和热轧机械压制,在高温下经过多次加热和轧制,最终形成所需的宽厚板。
热轧工艺可以改变钢材的结构和性能,提高其机械强度和塑性。
紧接着是冷轧工艺。
冷轧是在宽厚板热轧之后的一个重要工艺。
在这个过程中,宽厚板通过冷轧机进行冷压,以进一步提高板材的表面精度和尺寸稳定性。
冷轧工艺可以提高宽厚板的表面质量,使其适用于更高要求的应用领域。
然后是退火处理。
退火是一种热处理工艺,将宽厚板加热到一定温度并保持一段时间,然后缓慢冷却。
退火可以改变宽厚板的组织结构,提高其机械强度和塑性,并减轻因冷加工导致的内应力和组织不均匀问题。
最后是表面处理工艺。
宽厚板通常需要进行涂层、喷漆或镀锌等表面处理,以提高其耐腐蚀性和装饰性。
这些工艺可以保护宽厚板的表面,延长其使用寿命。
综上所述,宽厚板的工艺流程包括原材料准备、钢坯预处理、热轧、冷轧、退火处理和表面处理等多个环节。
每个工艺环节都有各自的目的和要求,必须严格按照工艺流程进行执行,以保证宽厚板的质量和性能。
只有通过科学合理的工艺流程,才能生产出符合市场需求的高质量宽厚板产品。
莱钢4300mm宽厚板生产线工艺技术特点
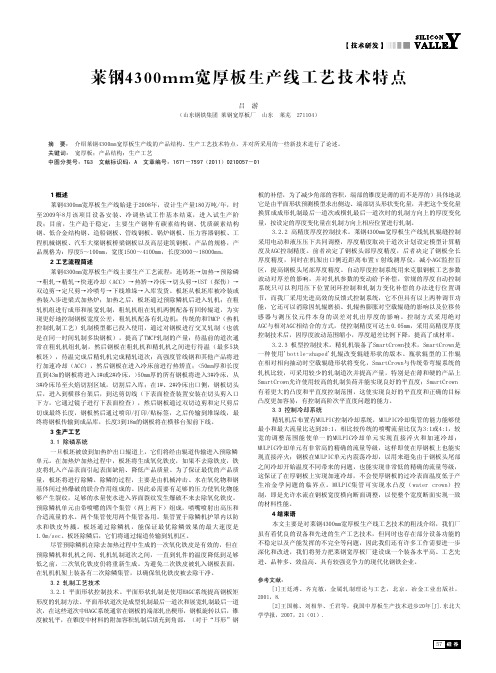
莱钢4300mm宽厚板生产线工艺技术特点吕游(山东钢铁集团 莱钢宽厚板厂山东莱芜 271104)摘 要:介绍莱钢4300mm宽厚板生产线的产品结构、生产工艺技术特点,并对所采用的一些新技术进行了论述。
关键词:宽厚板;产品结构;生产工艺中图分类号:TG3 文献标识码:A 文章编号:1671-7597(2011)0210057-011 概述板的补偿,为了减少角部的容积,端部的锥度是薄的而不是厚的)具体地说它是由平面形状预测模型求出侧边、端部切头形状变化量,并把这个变化量莱钢4300mm宽厚板生产线始建于2008年,设计生产量180万吨/年,时换算成成形轧制最后一道次或横轧最后一道次时的轧制方向上的厚度变化至2009年8月该项目设备安装、冷调热试工作基本结束,进入试生产阶量,按设定的厚度变化量在轧制方向上相应位置进行轧制。
段;目前,生产趋于稳定,主要生产钢种有碳素结构钢、优质碳素结构3.2.2 高精度厚度控制技术。
莱钢4300mm宽厚板生产线轧机辊缝控制钢、低合金结构钢、造船钢板、管线钢板、锅炉钢板、压力容器钢板、工采用电动和液压压下共同调整,厚度精度取决于道次计划设定模型计算精程机械钢板、汽车大梁钢板桥梁钢板以及高层建筑钢板,产品的规格,产度及AGC控制精度。
前者决定了钢板头部厚度精度,后者决定了钢板全长品规格为:厚度5~100mm,宽度1500~4100mm,长度3000~18000mm。
厚度精度,同时在机架出口侧近距离布置γ射线测厚仪,减小AGC监控盲2 工艺流程简述区,提高钢板头尾部厚度精度。
自动厚度控制系统用来克服钢板工艺参数莱钢4300mm宽厚板生产线主要生产工艺流程:连铸坯→加热→预除磷波动对厚差的影响,并对轧机参数的变动给予补偿,常规的厚度自动控制→粗轧→精轧→快速冷却(ACC)→热矫→冷床→切头剪→UST(探伤)→系统只可以利用压下位置闭环控制和轧制力变化补偿的办法进行位置调双边剪→定尺剪→冷喷号→下线堆垛→入库发货。
厚板工艺流程

厚板工艺流程
厚板工艺流程主要包括以下步骤:
1. 板材切割:根据设计要求将原始的金属板材切割成所需的形状和尺寸。
常用的切割方法有火焰切割、等离子切割、激光切割等。
切割完成后,板材需要进行校平和清理的处理,以确保下一步工艺的顺利进行。
2. 预弯处理:通过预弯操作,将板材的边缘折弯成所需的角度。
这一步骤主要是通过专用的边缘卷辊进行,使板材在弯角处加强性能,并为下一步的成型做好准备。
3. 成型轧制:消除板坯表面的影响和提高宽度控制的精度,沿板坯长度方向或斜向进行1~4道轧制,把坯料轧至所要求的厚度。
4. 展宽轧制:为达到轧制成品规格所要求的宽度,板坯转90°、沿板宽方向轧制。
5. 精轧:展宽轧制后再转90°,转回原坯料长度方向,轧制到成品板厚度。
6. 探伤检测:根据钢板质量要求,用超声波进行不同深度的探伤,对焊管用板的四个板边要全面进行探伤。
7. 涂层处理:如果需要防锈,可使用抛丸涂层法。
抛丸去除氧化铁皮后,再涂层防锈,涂层后应快干。
8. 其他处理:根据成品交货状态的不同,可能需要进行热处理、抛丸或涂漆等处理。
请注意,厚板的生产工艺流程根据每个厂的生产线布置情况、车间内物流的走向以及其主要产品品种和交货状态的不同而具有其各自的特点。
如需了解更多信息,建议咨询专业人士。
- 1、下载文档前请自行甄别文档内容的完整性,平台不提供额外的编辑、内容补充、找答案等附加服务。
- 2、"仅部分预览"的文档,不可在线预览部分如存在完整性等问题,可反馈申请退款(可完整预览的文档不适用该条件!)。
- 3、如文档侵犯您的权益,请联系客服反馈,我们会尽快为您处理(人工客服工作时间:9:00-18:30)。
关键特点: • 高效的板坯除鳞设备,可根据板坯厚度不同进行调整 • 粗轧机进出口侧的旋转辊道将用于产品宽度的展宽。 • 采用控制轧制和热机轧制工艺生产高性能的钢板(如管线钢板、高强度船板和 优质结构钢板)。 • 液压自动厚度控制 (AGC) 缸具有高精度和快速动态响应特性,该缸的特性能 够进行平面形状轧制。。 • VAI 平面形状轧制和AGC 系统,与VAI 的2 级模型相结合能保证成材率和钢 板的矩形化最优。 • VAI 的2 级模型通过保证精确预报宽展和实现正确宽度的轧边道次计算来使成 材率最优。2 级模型也能计算头尾需要的短行程和需要的钢板板体的修正。 • 实现绝对辊缝控制、头尾短行程控制和板身修正控制的VAI 技术控制系统 (TCS)。 • 提高凸度和平直度控制、提高产量和轧宽轧薄能力的VAI SmartCrown 系 统。 • 钢板平直度控制的工作辊弯辊系统 (WRB)。 • 使用电动机械宽度调整和短行程液压缸进行立辊辊缝调整的轧边机,轧边机附 着在粗轧机机座上,具有保证钢板头尾宽度最优的高速短行程能力。VAI 有很 多液压轧边机的参考。 • 绝对的立辊辊缝测量, VAI自动化技术不需要轧边机的测压元件并且使宽度公 差更好。
宽厚板生产线工艺流程
轧钢车间职工培训
1 2018/11/27
主要培训内容 一 介绍生产线工艺流程 二 轧钢车间工作范围 三 车间各工种职责介绍
2 2018/11/27
工艺流程介绍
工艺流程 车间布置图() 产品介绍
3 2018/11/27
12 2018/11/27
其他信息
其他培训活动 列出相关的书籍、文章及电子文档 顾问服务及其他资源
13 2018/11/27
5 2018/11/27
MULPIC 加速钢板冷却系统提供了高可控性的、精确的加速冷 却能力。这个系统的特点是具有非常高的流量调节比,允许广 泛厚度范围的钢板的控制冷却和工艺需要。这个系统也设计了 直接淬火(DQ)功能。 热矫直机具有覆盖很大厚度和宽度范围的矫直能力的技术水平。 2个主冷床和第三个厚板冷床允许全部范围的钢板进行有效冷却, 同时为下游工序提供了缓冲能力。 在1#剪切线,一台机械滚切式双切边剪达到切边最小化、切边 质量和成品宽度精确、剪切厚度最大到50mm的水平。 将来建造第二条剪切线后,生产能力达到180万吨。 机械定尺剪具有为精确定尺的和保证整条剪切线高产能的剪切 速度而采用的较高剪切力设计。 钢板的标志和打印通过高性能设备的联合操作进行。 钢板堆垛装置去进行成品钢板的预堆垛,以便转移到成品发货 区。 冷矫直机能够为有特殊的高精度要求的最终用户提高钢板的平 直度。 整条生产线的工艺仪表和仪器为VAI的自动化系统提供需要的 数据,以控制和优化完善钢板的生产。
6 2018/11/27来自连铸坯规格7 2018/11/27
产品尺寸
8 2018/11/27
9 2018/11/27
二 轧钢车间工作范围
三个区域-轧钢,精整,生产准备 各区域具体分工,职工职责 各区域间的衔接联系
10 2018/11/27
11 2018/11/27
总结
回顾所学的内容 指出应用所学内容的方法 要求得到培训反馈信息