最新回转窑生产线工艺流程图
水泥厂回转窑工艺流程
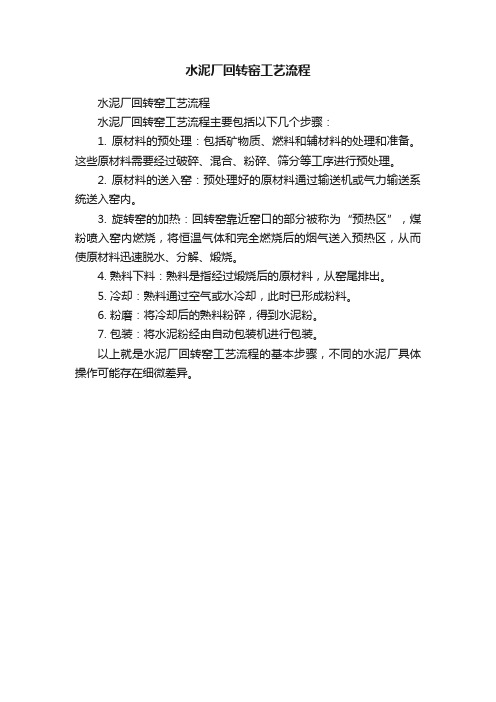
水泥厂回转窑工艺流程
水泥厂回转窑工艺流程
水泥厂回转窑工艺流程主要包括以下几个步骤:
1. 原材料的预处理:包括矿物质、燃料和辅材料的处理和准备。
这些原材料需要经过破碎、混合、粉碎、筛分等工序进行预处理。
2. 原材料的送入窑:预处理好的原材料通过输送机或气力输送系统送入窑内。
3. 旋转窑的加热:回转窑靠近窑口的部分被称为“预热区”,煤粉喷入窑内燃烧,将恒温气体和完全燃烧后的烟气送入预热区,从而使原材料迅速脱水、分解、煅烧。
4. 熟料下料:熟料是指经过煅烧后的原材料,从窑尾排出。
5. 冷却:熟料通过空气或水冷却,此时已形成粉料。
6. 粉磨:将冷却后的熟料粉碎,得到水泥粉。
7. 包装:将水泥粉经由自动包装机进行包装。
以上就是水泥厂回转窑工艺流程的基本步骤,不同的水泥厂具体操作可能存在细微差异。
回转窑安装施工方案

3回转窑安装施工方案3。
1概 述3。
1。
1该工程主要有3组托轮组和传动装置,窑尾密封装置,窑头罩等设备安装。
3。
1.2该工程施工工期短(4个月),施工场地窄小,有多重交叉作业,这些对施工增加了困难。
为此,在设备进场停放组装时必须按照《设备进场堆放组装布置图》进行。
3。
1。
3工程质量等级:优良。
3。
2施工工艺安装流程图:3。
2。
1基础检查及验收:3。
2.1。
1根据基础施工单位提供的基础交工资料,会同建设单位现场代表,复核基础标高及纵、横中心线是否符合设计要求,基础沉降是否稳定,基础在施工时应埋设有中心标板及测基础沉降的测点钢筋。
3.2.1.2根据设备实物对照过的设计图纸,检查设备基础的外型尺寸,砼标号(用回弹仪检测)标高中心线等是否符合要求:⑴基础外型尺寸允许误差±30mm;⑵基础平面标高允许误差+5mm或—15mm;⑶基础放线各中心线间距离允许误差1mm,并在各中心标板上做出明显的标记;⑷地脚螺栓孔的中心位置允许误差10mm,孔深允许误差 + 20mm;⑸基础表面及地脚螺栓孔的混凝土碎料及木板、积水等脏物必须清除干净;⑹基础在二次灌浆前必须凿出麻面.3。
2。
2设备开箱检查验收:3。
2。
2.1设备开箱检查验收应由建设单位和安装单位指派专人负责进行.3。
2。
2。
2根据设备的装配图和装箱单详细对设备型号、规格、数量、质量、外观、合格证、材质证明书等进行检查验收,并及时做好检查记录,双方签字.3.2.2。
3对设备内部部件一时难以检查到的,在安装、清洗和装配过程中如发现有变形、损坏、缺件和不符合图纸要求等情况,应及时通知建设单位解决处理。
3.2。
2。
4设备经检查验收合格后,要妥善保管,不得使其变形、损坏、锈蚀、错乱或丢失.3.2。
2。
5设备检查的方法及要求:⑴托轮组检查A、底座平面无扭曲,螺栓孔间距应符合设计要求;B、两托轮在底座之间的纵横中心线必须按图调整正确,检查两个托轮各部尺寸是否一致;比如托轮直径、轴承中心高度,装配后的串动量;要求两托轮的顶面必须在同一平面上.托轮表面应光滑,无碰伤和缺陷;C、检查托轮轴承座与环面接触情况及轴承与轴颈接触情况。
新型干法回转窑水泥生产工艺流程简述

新型干法回转窑水泥生产工艺流程简述一、水泥生产原燃材料及配料生产硅酸盐水泥的主要原料为石灰质原料和粘土质原料,有时还要根据燃料品质和水泥品种,掺加校正原料以补充某些成分的不足,还可利用废渣作为水泥的原料或混合材料生产。
(一)主要原料:1、石灰质原料:以碳酸钙为主要成份的原料,,是水泥熟料中CaO的主要来源。
如石灰石、白垩、石灰质泥灰岩、贝壳等。
一吨熟料约需1.2吨左右石灰质原料,在生料中约占75-78%。
2、粘土质原料:含碱和碱土的铝硅酸盐,主要成份为SiO2,其次为AL2O3,少量Fe2O3,是水泥熟料中SiO2、AL2O3的主要来源。
粘土质原料主要有黄土、粘土、页岩、泥岩、粉砂岩及河泥等。
一吨熟料约需0.2-0.3吨粘土质原料,在生料中约占11-17%。
(二)辅助原料;1、校正原料:(1)铁质校正原料:补充生料中Fe2O3的不足,主要为硫铁矿渣和铅矿渣等。
一吨熟料约需0.05吨。
(2)硅质校正原料:补充生料中SiO2的不足,主要有砂岩等,2、缓凝剂:以天然石膏和磷石膏为主。
掺加量3-5%。
3、工业废渣的利用:(1)赤泥:烧结法生产氧化铝排出的赤色废渣,以CaO、SiO2为主。
掺加石灰质原料可配制成生料。
(2)电石渣:以CaO为主。
可替代部分石灰石生产水泥。
(3)煤矸石:以SiO、AL2O3为主。
可替代粘土生产水泥。
(4)粉煤灰:以SiO、AL2O3为主。
可替代粘土配制生料,也可作混合材料。
(5)石煤:以SiO、AL2O3为主。
可作为粘土质原料,也可作燃料。
4、燃料:烟煤,用于熟料煅烧。
二、生产工艺流程:水泥生产的工艺流程简称为两磨一烧:两磨是指生料粉磨和水泥粉磨。
烧是指水泥熟料的煅烧。
1、生料粉磨:将制备好的主要原料(即石灰质原料75-78%、粘土质原料16-20%,铁质原料3-5%、)按照一定比例配比输入生料磨进行粉磨,磨制成符合要求的细粉,称为生料粉,然后再通过输送设备输入生料库存放均化。
回转窑施工方案

回转窑施工技术方案一、概述回转窑是水泥厂生产工艺中最关键的设备。
强大的热工负荷及连续生产的工作制度,对安装质量的要求十分严格,其安装质量的优劣,直接关系到全厂生产工艺线能否正常运行,因此施工中应采用先进的施工方法和检测手段,严格控制每一道工序的施工质量。
1.1回转窑主要组成部分支承装置、筒体、传动装置、液压挡轮装置、窑尾密封装置、窑头密封罩及润滑液压系统等。
1.回转窑规格和性能型式:干法生产预分解窑规格:φ4×60m斜度:3.5%支承座:3产量:2500T/D窑转速:用主传动时调速范围:0.396~3.96 r/min用辅助传动时:8.2 r/h传动型式:单传动传动电动机:减速器:挡轮型式:液压挡轮窑头密封型式:钢片密封窑头冷却方式:风冷窑尾密封型式:气缸压紧端面密封二、施工程序2.1回转窑施工工序流程图5、施工准备及设备出库检查组织施工人员熟悉图纸、安装说明书等技术资料,做好技术安装交底工作;了解设备到货及设备存放位置等现场情况;准备施工机具及材料,接通施工电源;根据设备到货清单检查其外观、规格、尺寸、数量及质量情况。
检查底座有无变形,实测底座螺丝孔间距及底座外形尺寸;每组托轮、球面瓦、轴承座组合成一体检查,重点检查托轮直径和轴承的中心高;检查轮带及套轮带处窑体的尺寸。
注意轮带内径与筒体上垫板处直径需留有窑筒体热膨胀值;检查窑筒体,测量每节窑筒体的实际长度和两轮带的中心距离以及窑筒体的总长度,并以此尺寸对窑进行基础放线,测量时最好选择无太阳直射时,或是早晨进行,并要求测量用盘尺在1kg/m的拉力下进行。
测量筒体的椭圆度等,检查筒体是否有马蹄口现象;检查大齿圈的齿形齿距(尤其是两个半圆接口处的齿距)、齿顶圆直径,检查大齿圈接口处的偏差,测量大齿圈的内径应与筒体外径加弹簧板的高度尺寸之和相等或稍大3—5mm,检查大齿圈的齿面是否有砂眼、裂纹等缺陷。
检查注意事项批:详细检查安装标记,没有标记的要通过检查做出标记,以便根据标记进行安装。
回转窑工艺、操作要求及推荐参数
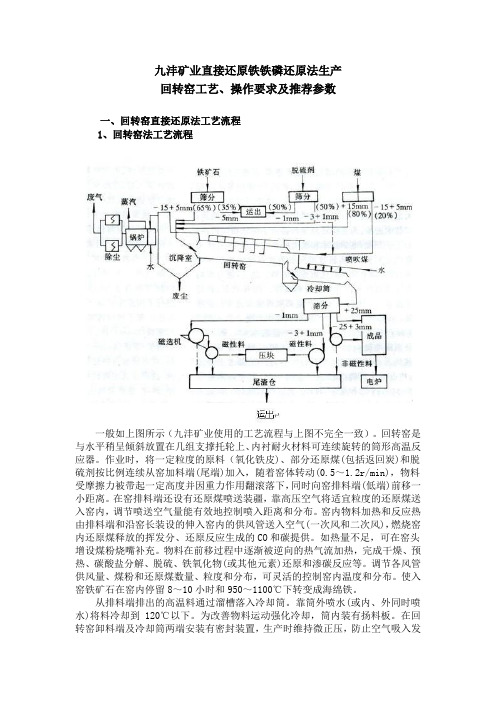
九沣矿业直接还原铁铁磷还原法生产回转窑工艺、操作要求及推荐参数一、回转窑直接还原法工艺流程1、回转窑法工艺流程一般如上图所示(九沣矿业使用的工艺流程与上图不完全一致)。
回转窑是与水平稍呈倾斜放置在几组支撑托轮上、内衬耐火材料可连续旋转的筒形高温反应器。
作业时,将一定粒度的原料(氧化铁皮)、部分还原煤(包括返回炭)和脱硫剂按比例连续从窑加料端(尾端)加入,随着窑体转动(0.5~1.2r/min),物料受摩擦力被带起一定高度并因重力作用翻滚落下,同时向窑排料端(低端)前移一小距离。
在窑排料端还设有还原煤喷送装疆,靠高压空气将适宜粒度的还原煤送入窑内,调节喷送空气量能有效地控制喷入距离和分布。
窑内物料加热和反应热由排料端和沿窑长装设的伸入窑内的供风管送入空气(一次风和二次风),燃烧窑内还原煤释放的挥发分、还原反应生成的CO和碳提供。
如热量不足,可在窑头增设煤粉烧嘴补充。
物料在前移过程中逐渐被逆向的热气流加热,完成干燥、预热、碳酸盐分解、脱硫、铁氧化物(或其他元素)还原和渗碳反应等。
调节各风管供风量、煤粉和还原煤数量、粒度和分布,可灵活的控制窑内温度和分布。
使入窑铁矿石在窑内停留8~10小时和950~1100℃下转变成海绵铁。
从排料端排出的高温料通过溜槽落入冷却筒。
靠筒外喷水(或内、外同时喷水)将料冷却到120℃以下。
为改善物料运动强化冷却,筒内装有扬料板。
在回转窑卸料端及冷却筒两端安装有密封装置,生产时维持微正压,防止空气吸入发生再氧化。
冷却后的物料经筛分分级、磁选分离得出磁性颗粒料(直接还原铁)、磁性粉料、非磁性颗粒料和非磁性粉。
非磁性颗粒料含较高固定碳,可作还原剂重新利用。
二、回转窑设备组成回转窑设备主要由筒体、滚圈、支承装置、传动装置、窑头罩、密封装置、集尘室、燃烧装置及热烟室等部分构成,详见上图。
(1)筒体。
回转窑的筒体由钢板卷成,从铆接已发展为全部焊接。
筒体应具有足够的刚度和强度,以保证在安装和运转中轴线的直线性和截面的圆度。
《回转窑安装规范》(参考Word)
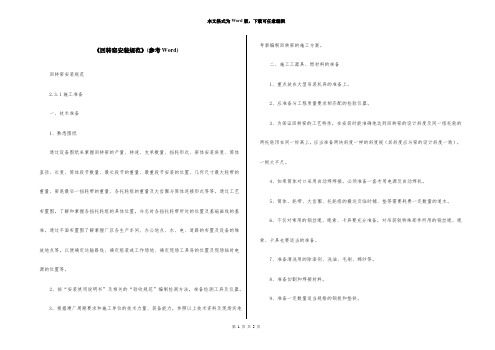
《回转窑安装规范》(参考Word)回转窑安装规范2.3.1施工准备一、技术准备1、熟悉图纸通过设备图纸来掌握回转窑的产量、转速、支承数量、挡轮形式、窑体安装斜度、筒体直径、长度、筒体段节数量、最长段节的重量、最重段节安装的位置、几何尺寸最大轮带的重量、窑尾最后一挡轮带的重量、各托轮组的重量及大齿圈与筒体连接形式等等。
通过工艺布置图,了解和掌握各挡托轮组的具体位置,冷态时各挡托轮带所处的位置及基础画线的基准。
通过平面布置图了解掌握厂区各生产车间、办公地点、水、电、道路的布置及设备的堆放地点等,以便确定运输路线、确定组装或工作场地、确定现场工具房的位置及现场临时电源的位置等。
2、按“安装使用说明书”及相关的“验收规范”编制检测方法,准备检测工具及仪器。
3、根据建厂周期要求和施工单位的技术力量、装备能力,参照以上技术资料及现场实地考察编制回转窑的施工方案。
二、施工工器具、燃材料的准备1、重点放在大型吊装机具的准备上。
2、应准备与工程质量要求相匹配的检验仪器。
3、为保证回转窑的工艺特性,在安装时能准确地达到回转窑的设计斜度及同一组托轮的两托轮顶在同一标高上,应当准备两块斜度一样的斜度规(其斜度应与窑的设计斜度一致),一根大平尺。
4、如果筒体对口采用自动焊焊接,必须准备一套专用电源及自动焊机。
5、筒体、轮带、大齿圈、托轮组的搬运及临时铺、垫等需要耗费一定数量的道木。
6、不仅对常用的钢丝绳、绳索、卡具要充分准备,对吊装较特殊部件所用的钢丝绳、绳索、卡具也要适当的准备。
7、准备清洗用的除漆剂、洗油、毛刷、棉纱等,8、准备切割和焊接材料。
9、准备一定数量适当规格的钢板和垫铁。
2.3.2回转窑施工工艺特点及安装工艺过程回转窑形大体重,其筒体较长,一般采用两档或多档支承。
回转窑的安装涉及到:起重运输、安装钳工工艺、铆工工艺、焊接工艺、管道工艺及砌筑工程等,使回转窑的安装形成了如下特点:1、安装技术要求较高,高精度的量具、仪器和检测工具广泛应用,要求操有较高的技术水平。
回转窑工艺流程
回转窑工艺流程回转窑是一种重要的烧结装置,广泛应用于建筑材料、冶金、化工等行业中。
它是一种连续式的烧结装置,通过回转窑可以将粉状原料逐渐转变为烧结物,并在高温下完成烧结过程。
回转窑工艺流程主要包括原料准备、进料、预热、烧结和冷却五个步骤。
首先,原料准备。
在回转窑工艺中,原料的选择和准备是非常重要的一步。
根据产品的需求,选择合适的原料,并按照一定的比例进行混合。
这些原料通常包括石灰石、粘土、煤粉等。
接下来是进料环节。
将混合好的原料送入回转窑的进料口,并根据需要的产量和烧结时间调整进料的速度和流量。
进料过程需要保持稳定,确保原料的均匀供给。
然后是预热阶段。
在回转窑中,原料需要经过一定的预热过程,将其温度升至适宜的烧结温度。
预热过程是通过高温燃烧气体和窑壁的传导来完成的。
预热的目的是为了使原料中的水分和挥发性成分迅速蒸发,减少烧结过程中的能耗。
接下来是烧结阶段。
在回转窑中,原料逐渐进入高温区域,进行烧结过程。
在高温下,原料中的成分发生化学反应,形成烧结物。
烧结过程中,需要控制好温度和时间,以保证烧结物的质量和稳定性。
最后是冷却阶段。
烧结完成后,烧结物需要在回转窑中进行冷却,使其温度降至室温以下。
冷却过程通常采用气流循环或水冷方式进行。
冷却的目的是为了降低烧结物的温度,使其达到需要的硬度和强度,并便于后续加工和运输。
回转窑工艺流程中,温度、时间、进料速度等参数的控制非常重要。
合理的工艺参数可以提高生产效率,降低能耗,并保证产品的质量和稳定性。
在实际应用中,还需要根据不同的原料和产品要求进行工艺优化,以达到最佳的效果。
总的来说,回转窑工艺流程是一个连续、稳定的过程,通过预热、烧结和冷却等步骤,将原料逐渐转变为烧结物。
合理的工艺参数和优化的工艺流程可以提高生产效率和产品质量,并减少能耗和环境污染。
回转窑工艺在工业生产中具有重要的应用价值,为多个行业的发展做出了贡献。
回转窑工艺、操作要求及推荐参数
九沣矿业直接还原铁铁磷还原法生产回转窑工艺、操作要求及推荐参数一、回转窑直接还原法工艺流程1、回转窑法工艺流程一般如上图所示(九沣矿业使用的工艺流程与上图不完全一致)。
回转窑是与水平稍呈倾斜放置在几组支撑托轮上、内衬耐火材料可连续旋转的筒形高温反应器。
作业时,将一定粒度的原料(氧化铁皮)、部分还原煤(包括返回炭)和脱硫剂按比例连续从窑加料端(尾端)加入,随着窑体转动(0.5~1.2r/min),物料受摩擦力被带起一定高度并因重力作用翻滚落下,同时向窑排料端(低端)前移一小距离。
在窑排料端还设有还原煤喷送装疆,靠高压空气将适宜粒度的还原煤送入窑内,调节喷送空气量能有效地控制喷入距离和分布。
窑内物料加热和反应热由排料端和沿窑长装设的伸入窑内的供风管送入空气(一次风和二次风),燃烧窑内还原煤释放的挥发分、还原反应生成的CO和碳提供。
如热量不足,可在窑头增设煤粉烧嘴补充。
物料在前移过程中逐渐被逆向的热气流加热,完成干燥、预热、碳酸盐分解、脱硫、铁氧化物(或其他元素)还原和渗碳反应等。
调节各风管供风量、煤粉和还原煤数量、粒度和分布,可灵活的控制窑内温度和分布。
使入窑铁矿石在窑内停留8~10小时和950~1100℃下转变成海绵铁。
从排料端排出的高温料通过溜槽落入冷却筒。
靠筒外喷水(或内、外同时喷水)将料冷却到120℃以下。
为改善物料运动强化冷却,筒内装有扬料板。
在回转窑卸料端及冷却筒两端安装有密封装置,生产时维持微正压,防止空气吸入发生再氧化。
冷却后的物料经筛分分级、磁选分离得出磁性颗粒料(直接还原铁)、磁性粉料、非磁性颗粒料和非磁性粉。
非磁性颗粒料含较高固定碳,可作还原剂重新利用。
二、回转窑设备组成回转窑设备主要由筒体、滚圈、支承装置、传动装置、窑头罩、密封装置、集尘室、燃烧装置及热烟室等部分构成,详见上图。
(1)筒体。
回转窑的筒体由钢板卷成,从铆接已发展为全部焊接。
筒体应具有足够的刚度和强度,以保证在安装和运转中轴线的直线性和截面的圆度。
碳酸锂回转窑生产工艺流程和技术特点详解
碳酸锂回转窑生产工艺流程和技术特点详解目录1.序言 (1)2.碳酸锂回转窑生产工艺流程图原理 (2)3.碳酸锂回转窑生产工艺流程图详解 (3)3. 1.前述 (3)1.2.碳酸锂生产工艺流程 (4)1.2.1.1.碳酸锂生产工艺流程——硫酸法生产工艺流程介绍: (4)1.2.2.碳酸锂生产工艺流程——锂辉石与硫酸盐混合烧结法生产工艺流程介绍: (4)1.2.3.碳酸锂生产工艺流程——碳酸钠加压浸出法生产工艺流程介绍: (5)1.2.4.碳酸锂生产工艺流程——氯化焙烧法生产工艺流程介绍: (5)1.3.碳酸锂生产工艺流程一一石灰石焙烧法生产工艺流程介绍: (5)1.4.碳酸锂生产工艺流程工作原理 (6)1.5.碳酸锂生产工艺流程技术特点 (7)4.碳酸锂的主要生产工艺设备 (8)5.碳酸锂回转窑生产工艺流程车间配置 (8)6.碳酸锂回转窑生产工艺流程技术特点 (8)7.碳酸锂焙烧回转窑焙烧锂矿石的优点如下 (8)1.序言碳酸锂[U转窑以锂辉石为原料生产碳酸锂,工业上比较成熟的工艺是硫酸法生产工艺流程。
此工艺的基本原理是在于硫酸与锂辉石在250~300°C下发生置换反应,生成硫酸锂。
这一反应只能发生于结构较为疏松的锂辉石,先将选矿获得的锂辉石精矿,在碳酸锂回转窑中高温焙烧,冷却后与足量的硫酸混合, 送入250℃酸化碳酸锂回转窑中进行硫酸焙烧。
冷却后水浸,加石灰石控制PH 值,得到含10%左右的粗锂液,用石灰调PH至11,加碳酸钠除钙、镁、铁、铝等杂质。
清液蒸发称含20左右的硫酸锂净化液,加入碳酸钠沉淀成碳酸锂。
离心脱水,得到碳酸锂产品,回收率在90%左右。
硫酸法生产碳酸锂收率较高, 将锂辉石与硫酸盐混合烧结生产,在一定温度下混合烧结,经一系列物理、化学反应后,所配入的硫酸盐中的金属元素,将矿石中锂置换生成可溶性的硫酸盐,主要杂质则生成难溶于水的化合物,然后将烧结后的熟料浸出分离,锂离子进入溶液,经净化、浓缩、沉淀后得到碳酸锂产品。
回转窑操作法
危险废物焚烧装置岗位操作法编写:吕忠希审阅:杨淑堂青岛新天地固体废物综合处置有限公司2008年2月目录一、主控室 (1)1、岗位任务 (1)2、工艺流程 (1)(1)工艺流程简述 (1)(2)工艺流程框图 (2)3、主要操作指标 (2)4、管理范围及主要设备 (3)(1)管理范围 (3)(2)主要设备 (3)5、开、停车操作程序 (4)(1)系统开车前的准备与检查 (4)(2)开车 (4)(3)停车 (5)(4)停车后的重新启动 (8)6、正常操作要点 (8)7、注意问题 (9)二、锅炉岗位 (10)1、岗位任务 (10)2、工艺流程图 (10)(1)锅炉系统 (10)(2)压缩空气系统 (10)(3)废液输送系统 (11)3、主要操作指标 (11)4、管理范围及主要设备 (11)(1)管理范围 (11)(2)主要设备 (11)5、安全操作 (12)(1)锅炉系统 (12)(2)空压机系统 (14)(3)废液输送系统 (15)三、尾气处理岗位 (16)1、岗位任务 (16)2、工艺流程 (16)(1)工艺流程简述 (16)(2)工艺流程图 (17)3、主要操作指标 (17)4、管理范围及主要设备 (17)(1)管理范围 (17)(2)主要设备 (17)5、开车前的准备 (18)6、开车的条件与程序 (19)7、注意问题 (19)四、破碎输送岗位 (20)1、岗位任务 (20)2、工艺流程图 (20)3、管理范围及主要设备 (20)(1)管理范围 (20)(2)主要设备 (20)4、注意问题 (21)5、箱废上料岗位 (21)(1)岗位任务 (21)(2)管理范围及主要设备 (22)(3)开车前的检查 (22)(4)运行 (22)(5)注意问题 (22)五、行车岗位 (22)1、岗位任务 (22)2、工艺流程 (22)3、管理范围及主要设备 (23)(1)管理范围 (23)(2)主要设备 (23)4、链板输送机 (23)(1)开车前的检查 (23)(2)开车: (23)(3)注意问题: (23)5、行车岗位安全操作规程 (23)附录:泵故障诊断方法 (25)一、主控室1、岗位任务负责焚烧系统的运行操作控制;指挥各岗位的开停车和运行操作;完成危险废物焚烧和尾气的净化处理,达到如下要求:(1)焚烧工况稳定,废物焚烧彻底,焚烧效率、残渣热灼减率等指标合格。