600t回转窑工艺流程图
600t活性石灰回转窑生产线工艺简介及技术特点

・
R R EF ACT I OR ES & U ME
0 t2 1 c. 0 1
Vo . 6 No5 1 3 .
6 0 活性石灰 回转窑生产线 0t 工艺简介及 技术特点
刘 波 苏国富 刘 拓 于仲仁 ( 沈阳水泥机械有限公 司,沈 阳 104 ) 11 1
料 的筛 选 。筛 分后 ≤ 1mm 的石 灰石 会 直接 落 入 振 5 动 筛 下 的 碎 石仓 中 。考 虑 到 原 料 的合 理 利 用 ,碎 石贮 仓 中 的小 颗粒 石灰 石 不用二 次破 碎 直接 被业 主
用 作 脱硫 剂 的 原料 。 1 — 0 m 的颗 粒 经 斗 式 提 升 56m
i t r d ci n nop o u t . o Ke r s Ac ie l y wo d : t me; Roa y k l P o e s Co v i tr i n; r c s ; mmiso i g sinn
1 工 业 2 6 0 (・ ) 活性 石 灰 回 x 0 td 转窑 生 产线 项 目由 沈 阳水 泥机 械 有 限公 司 总f_ f ̄ r g. , 中 冶焦 耐 工程 技 术 有 限公 司 负 责 整 个 工 程 的工 艺 设 计 。工 程 地 点 位 于 新 疆 石 灰 石 工 业 园 区 。 由于
磨 ,而 细 粉在 气 流 的 带 动下 进 人袋 式 收 尘器 收尘 , 达 到 粉 气分 离 的 目的 。 出选 粉 机 的气 体 ,经 收 尘
净 化 后 由排 风机 排 出 。 一 部 分 废 气 鼓 人 磨 煤 机 循 ’ 环 使 用 ,另 一 部 分 废 气 通 过 烟 囱排 人 大 气 中 。 由
表 l 焙 烧 系统 设 备 参 数
回转窑工艺技术操作规程学习资料

回转窑工艺技术操作规程学习资料第一部分:工艺原理1.回转窑的结构和工作原理1.1回转窑的结构1.2回转窑的工作原理第二部分:操作前准备2.1检查设备2.1.1检查回转窑设备是否处于正常状态2.1.2检查燃料供应系统和热交换器2.2清理回转窑设备2.2.1清理窑壁及窑内杂物2.2.2清理窑内的堵塞物2.3安全措施2.3.1穿戴必要的个人防护装备2.3.2切勿进行无关操作第三部分:操作步骤3.1开启回转窑设备3.1.1先启动预热设备,使设备达到适宜温度3.1.2启动空气供应系统3.1.3启动供料系统3.2调整回转窑设备3.2.1调整翻板板位3.2.2调整回转窑的转速3.3控制燃烧系统3.3.1准确调整燃烧系统的供气量和燃料供给量3.3.2应监测燃烧风鼓风机、鼓风机并保持其在正常工作范围内3.3.3定时调整燃煤窑温3.4调整进料速率3.4.1根据生产需要调整进料速率3.4.2避免进料过快或过慢3.5窑尾温度调节3.5.1根据生产需要调整窑尾温度3.5.2保持窑尾温度在稳定范围内第四部分:注意事项4.1注意炉渣的排放4.1.1根据窑尾温度和物料状态合理安排炉渣的排放时间4.1.2防止炉渣的过早排放引发事故4.2注意传动部件的润滑4.2.1定期对传动部件进行润滑4.2.2注意润滑油的质量和使用寿命4.3注意设备的维修和保养4.3.1定期对回转窑设备进行检查和维修4.3.2注意设备的保养和清洁4.4注意安全操作4.4.1确保操作人员拥有相关许可证和经验4.4.2遵循相关的安全操作规程第五部分:故障处理5.1窑转速过快或过慢5.1.1检查传动系统是否正常5.1.2检查润滑系统是否正常5.2窑温过高或过低5.2.1调整燃烧系统的燃料供给量和燃烧风量5.2.2检查窑内的热交换器和冷却系统是否正常5.3物料堵塞5.3.1添加解堵剂5.3.2清理回转窑设备内的堵塞物以上是回转窑工艺技术操作规程学习资料的概要,更详细的内容可以根据实际需求和操作要求进行进一步补充和完善。
第三部分 回转窑
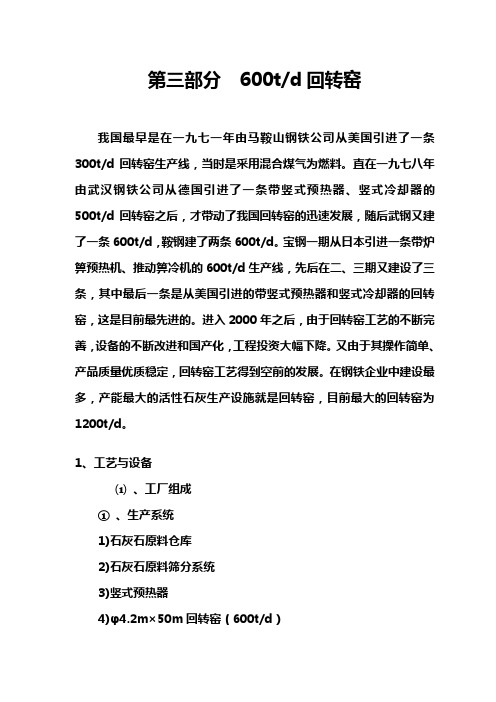
第三部分 600t/d回转窑我国最早是在一九七一年由马鞍山钢铁公司从美国引进了一条300t/d回转窑生产线,当时是采用混合煤气为燃料。
直在一九七八年由武汉钢铁公司从德国引进了一条带竖式预热器、竖式冷却器的500t/d 回转窑之后,才带动了我国回转窑的迅速发展,随后武钢又建了一条600t/d,鞍钢建了两条600t/d。
宝钢一期从日本引进一条带炉箅预热机、推动箅冷机的600t/d生产线,先后在二、三期又建设了三条,其中最后一条是从美国引进的带竖式预热器和竖式冷却器的回转窑,这是目前最先进的。
进入2000年之后,由于回转窑工艺的不断完善,设备的不断改进和国产化,工程投资大幅下降。
又由于其操作简单、产品质量优质稳定,回转窑工艺得到空前的发展。
在钢铁企业中建设最多,产能最大的活性石灰生产设施就是回转窑,目前最大的回转窑为1200t/d。
1、工艺与设备⑴、工厂组成①、生产系统1)石灰石原料仓库2)石灰石原料筛分系统3)竖式预热器4)φ4.2m×50m回转窑(600t/d)5)竖式冷却器6)煤气混合站7)回转窑烟气除尘净化及排烟系统8)控制站及操作室9)石灰成品筛分、贮存运输及计量系统②、公用及辅助生产系统1) 空气压缩站2) 中央变配电所、液压站③、行政生活设施1)综合楼包括办公室、化验室等生活设施⑵、工艺流程合格粒度的石灰石(20~50mm)由自卸汽车直接运至石灰石原料仓库贮存。
贮存量按7天考虑。
石灰石由2台5t抓斗桥式起重机加到石灰石受料槽,经过振动给料机、带式输送机送到筛分楼。
经过筛分,筛上料采用带式输送机经过皮带秤计量后送入竖式预热器顶部的受料仓中。
受料仓中的物料经加料管送入预热器内的环形通道,石灰石在环形通道内缓慢下移,并经1000~1100℃的窑尾烟气预热到900℃左右,废气进入窑尾废气处理系统,部分分解的石灰石经预热器上的液压推杆推动,通过加料室进入到600t/d烧混合煤气的回转窑内进行煅烧。
流程图——水泥厂主要生产工艺流程

水泥厂主要生产工艺流程水泥生产过程主要分为三个阶段,即生料制备、熟料烧成和水泥粉磨(俗称“两磨一烧”)。
其生产工艺总流程示意见图3-1。
采用五级旋风预热及窑外分解的新型干法水泥的生产工艺流程说明如下:(1)石灰石破碎及储存由自备汽车从矿山运来的石灰石经生产能力为500-600t/h的PCF2022单段锤式破碎机破碎后,进入φ80m的圆形预均化堆场中均化,圆形预均化堆场储量23100t,储期8.6d。
(2)粘土、铁粉储存粘土、铁粉分别由汽车运进厂内的堆栅储存,粘土的储量是5600吨储期11.2d;铁粉的储量是1600吨,储期13.1d。
储存在堆栅的粘土、铁粉由铲车送入斗式提升机,经斗式提升机分别送入2-φ5×10m的钢板库中储存,储量分别为200吨、250吨。
(3)原煤的储存原煤进厂后堆放在一30×160m的堆栅中,储量5000吨,储存期16.8天。
原煤经预破碎后,由皮带机、斗式提升机送到煤粉制备车间的原煤仓。
(4)生料制备出预均化堆场的石灰石经皮带机送入一座φ8×20m配料库,粘土、铁粉通过共用提升机各自进入一座φ5×10m 的钢板配料库。
出配料库的三种原料经电子皮带秤计量,并由QCS系统进行控制。
配制后的混合的混合料经由皮带输送机送入HRM3400立式磨内,在磨机入口处设有锁风阀。
出磨生料经连续取样器取样,并经多元素分析仪分析,分析结果输入配料计算机与标准值进行比较,计算后发出修改指令,重新调整各物料的喂料量,使配料保持在精度±2%的范围内。
含综合水分约3.5%左右的物料由锁风喂料机喂入磨内,同时从磨机底部抽入热风。
经磨辊碾磨过的物料在风环处被高速气流带起,经分离器分离后,粗物料落回磨内继续被碾压,细粉随气流出磨,经收尘器收下即为成品。
从窟尾预热器引来的320℃左右的高温废气,分成二路:一路经多管冷却器、混合室至窑尾袋收尘器;一路进出料磨作为烘干介质,出生料磨的废气由磨房主排风机引入混合室与从高温风机过来的废气混合后进入窑尾收尘器,净化后排入大气。
回转窑工艺、操作要求及推荐参数
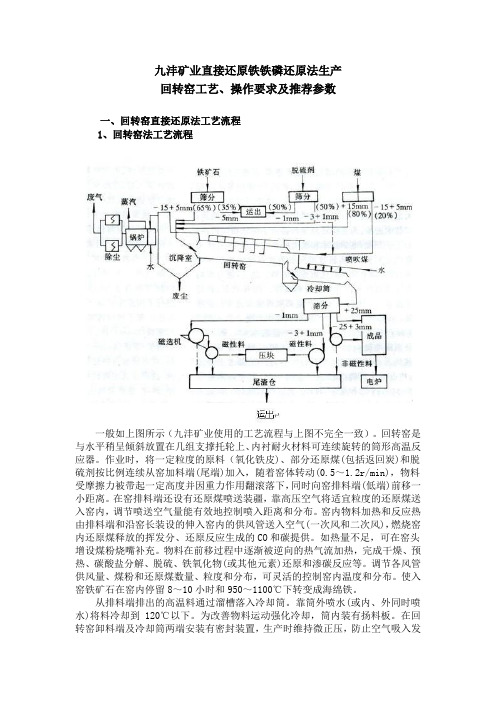
九沣矿业直接还原铁铁磷还原法生产回转窑工艺、操作要求及推荐参数一、回转窑直接还原法工艺流程1、回转窑法工艺流程一般如上图所示(九沣矿业使用的工艺流程与上图不完全一致)。
回转窑是与水平稍呈倾斜放置在几组支撑托轮上、内衬耐火材料可连续旋转的筒形高温反应器。
作业时,将一定粒度的原料(氧化铁皮)、部分还原煤(包括返回炭)和脱硫剂按比例连续从窑加料端(尾端)加入,随着窑体转动(0.5~1.2r/min),物料受摩擦力被带起一定高度并因重力作用翻滚落下,同时向窑排料端(低端)前移一小距离。
在窑排料端还设有还原煤喷送装疆,靠高压空气将适宜粒度的还原煤送入窑内,调节喷送空气量能有效地控制喷入距离和分布。
窑内物料加热和反应热由排料端和沿窑长装设的伸入窑内的供风管送入空气(一次风和二次风),燃烧窑内还原煤释放的挥发分、还原反应生成的CO和碳提供。
如热量不足,可在窑头增设煤粉烧嘴补充。
物料在前移过程中逐渐被逆向的热气流加热,完成干燥、预热、碳酸盐分解、脱硫、铁氧化物(或其他元素)还原和渗碳反应等。
调节各风管供风量、煤粉和还原煤数量、粒度和分布,可灵活的控制窑内温度和分布。
使入窑铁矿石在窑内停留8~10小时和950~1100℃下转变成海绵铁。
从排料端排出的高温料通过溜槽落入冷却筒。
靠筒外喷水(或内、外同时喷水)将料冷却到120℃以下。
为改善物料运动强化冷却,筒内装有扬料板。
在回转窑卸料端及冷却筒两端安装有密封装置,生产时维持微正压,防止空气吸入发生再氧化。
冷却后的物料经筛分分级、磁选分离得出磁性颗粒料(直接还原铁)、磁性粉料、非磁性颗粒料和非磁性粉。
非磁性颗粒料含较高固定碳,可作还原剂重新利用。
二、回转窑设备组成回转窑设备主要由筒体、滚圈、支承装置、传动装置、窑头罩、密封装置、集尘室、燃烧装置及热烟室等部分构成,详见上图。
(1)筒体。
回转窑的筒体由钢板卷成,从铆接已发展为全部焊接。
筒体应具有足够的刚度和强度,以保证在安装和运转中轴线的直线性和截面的圆度。
回转窑工艺、操作要求及推荐参数
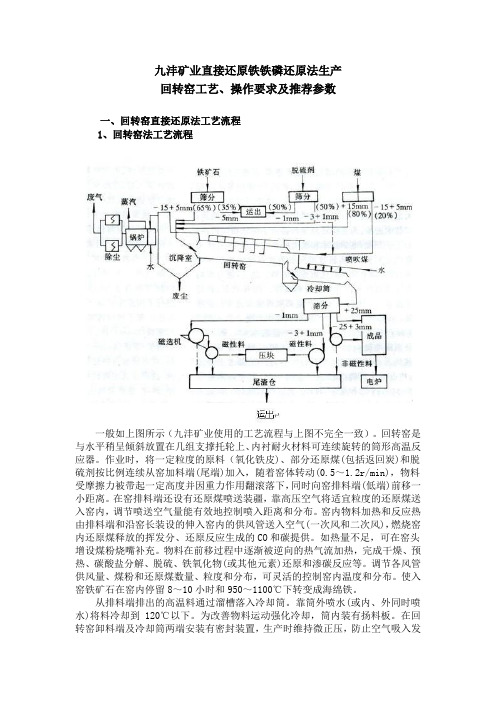
九沣矿业直接还原铁铁磷还原法生产回转窑工艺、操作要求及推荐参数一、回转窑直接还原法工艺流程1、回转窑法工艺流程一般如上图所示(九沣矿业使用的工艺流程与上图不完全一致)。
回转窑是与水平稍呈倾斜放置在几组支撑托轮上、内衬耐火材料可连续旋转的筒形高温反应器。
作业时,将一定粒度的原料(氧化铁皮)、部分还原煤(包括返回炭)和脱硫剂按比例连续从窑加料端(尾端)加入,随着窑体转动(0.5~1.2r/min),物料受摩擦力被带起一定高度并因重力作用翻滚落下,同时向窑排料端(低端)前移一小距离。
在窑排料端还设有还原煤喷送装疆,靠高压空气将适宜粒度的还原煤送入窑内,调节喷送空气量能有效地控制喷入距离和分布。
窑内物料加热和反应热由排料端和沿窑长装设的伸入窑内的供风管送入空气(一次风和二次风),燃烧窑内还原煤释放的挥发分、还原反应生成的CO和碳提供。
如热量不足,可在窑头增设煤粉烧嘴补充。
物料在前移过程中逐渐被逆向的热气流加热,完成干燥、预热、碳酸盐分解、脱硫、铁氧化物(或其他元素)还原和渗碳反应等。
调节各风管供风量、煤粉和还原煤数量、粒度和分布,可灵活的控制窑内温度和分布。
使入窑铁矿石在窑内停留8~10小时和950~1100℃下转变成海绵铁。
从排料端排出的高温料通过溜槽落入冷却筒。
靠筒外喷水(或内、外同时喷水)将料冷却到120℃以下。
为改善物料运动强化冷却,筒内装有扬料板。
在回转窑卸料端及冷却筒两端安装有密封装置,生产时维持微正压,防止空气吸入发生再氧化。
冷却后的物料经筛分分级、磁选分离得出磁性颗粒料(直接还原铁)、磁性粉料、非磁性颗粒料和非磁性粉。
非磁性颗粒料含较高固定碳,可作还原剂重新利用。
二、回转窑设备组成回转窑设备主要由筒体、滚圈、支承装置、传动装置、窑头罩、密封装置、集尘室、燃烧装置及热烟室等部分构成,详见上图。
(1)筒体。
回转窑的筒体由钢板卷成,从铆接已发展为全部焊接。
筒体应具有足够的刚度和强度,以保证在安装和运转中轴线的直线性和截面的圆度。
回转窑生产直接还原铁工艺(网络收集)图文并茂详解 一、二、三.
直接还原铁生产工艺——回转窑(一)2011-05-30 15:00来源:我的钢铁网试用手机平台回转窑直接还原法是以连续转动的回转窑作反应器,以固体碳作还原剂,通过固相还原反应把铁矿石炼成铁的直接还原炼铁方法。
回转窑直接还原是在950~1100℃进行的固相碳还原反应,窑内料层薄,有相当大的自由空间,气流能不受阻碍的自由逸出,窑尾温度较高,有利于含铁多元共生矿实现选择性还原和气化温度低的元素和氧化物以气态排出,然后加以回收,实现资源综合利用。
由于还原温度较低,矿石中的脉石都保留在产品里,未能充分渗碳。
由于还原失氧形成大量微气孔,产品的微观类似海绵,故也称海绵铁。
原料要求铁矿石(包括氧化球团矿、还原与燃烧用煤和脱硫剂是煤基回转窑直接还原生产的主要原料,是直接还原生产的物质基础。
原料的质量不仅对直接还原的生产效率、产品质量和能源消耗等技术经济指标有直接影响,还决定着直接还原工艺的成败。
因此,做好原料选择和加工准备是直接还原生产十分重要的基础工作,是能否生产出直接还原铁的关键。
一含铁原料的选用用于回转窑直接还原生产的含铁原料可以是天然铁矿石(即块矿,也可以是氧化球团。
决定含铁原料质量的主要因素是:化学成分、物理性质和冶金性能。
适宜于回转窑直接还原生产的铁矿石必须:含铁量高、脉石含量少、有害杂质少、化学成分稳定、粒度适宜,并且具有良好的还原性及一定的强度。
化学成分1.含铁量与脉石含铁原料以铁氧化物为主,还含有SiO2Al2O3、CaO、MgO等成分。
在回转窑还原过程中,所发生的主要化学变化是在固态下脱除含铁原料中的氧,而不能脱除脉石成分和其他杂质。
因此选用的含铁原料必须是含铁量高、脉石含量低。
通常要求含铁量在66%以上,脉石总量小于8%。
CaO与MgO通常在矿石中含量不多,在炼钢过程中不是有害成分,对回转窑工艺也没有大的影响。
一般要求原料中CaO<2.5%,Mgo<1.5%。
保留在直接还原铁中的酸性脉石SiO2和Al2O3导至炼钢电耗增高,生产率下降,渣量和各种材料消耗增加、炉衬寿命缩短。
钢铁行业回转窑工艺流程
钢铁行业回转窑工艺流程
钢铁行业是现代工业中不可或缺的一环,而回转窑工艺是钢铁生产中的一个重要环节。
下面详细介绍一下回转窑工艺的流程。
一、生料处理
生料处理是回转窑工艺中的第一步,是指将石灰石、石膏、粘土等生料进行预处理。
这一步操作的目的是使生料符合生产要求。
二、窑尾单点烧成
窑尾单点烧成是指将预处理好的生料放入窑尾,通过点火使其燃烧。
这一步操作可以提高窑内温度,增加产量。
三、窑头预热
窑头预热是指将燃烧的窑尾烟气通过窑头进行预热,使新鲜生料在进入窑内之前就达到一定温度,从而提高生料的反应性。
四、烧成过程
烧成过程是整个回转窑工艺的核心部分,也是钢铁生产中最重要的一环。
在烧成过程中,生料在高温下发生化学反应,产生熟料,从而获得钢铁生产主体原料。
烧成过程需要控制窑内的温度、风速、氧气含
量等,以确保生产出的熟料符合质量要求。
五、冷却过程
冷却过程是将烧成好的熟料通过辊式烧结机进行快速冷却的过程,目
的是使其具备足够的强度和韧性。
六、物料破碎
物料破碎是指将冷却好的熟料进行碎石,从而使其符合生产要求。
七、熟料运输
熟料运输是将碎好的熟料通过输送带或卡车等工具运输到下一道工序
进行处理。
通过以上步骤,回转窑工艺可以将生料转化为钢铁生产的主体原料,
确保钢铁生产的质量和产量,是钢铁行业中不可或缺的生产工艺之一。
回转窑操作法
危险废物焚烧装置岗位操作法编写:吕忠希审阅:杨淑堂青岛新天地固体废物综合处置有限公司2008年2月目录一、主控室 (1)1、岗位任务 (1)2、工艺流程 (1)(1)工艺流程简述 (1)(2)工艺流程框图 (2)3、主要操作指标 (2)4、管理范围及主要设备 (3)(1)管理范围 (3)(2)主要设备 (3)5、开、停车操作程序 (4)(1)系统开车前的准备与检查 (4)(2)开车 (4)(3)停车 (5)(4)停车后的重新启动 (8)6、正常操作要点 (8)7、注意问题 (9)二、锅炉岗位 (10)1、岗位任务 (10)2、工艺流程图 (10)(1)锅炉系统 (10)(2)压缩空气系统 (10)(3)废液输送系统 (11)3、主要操作指标 (11)4、管理范围及主要设备 (11)(1)管理范围 (11)(2)主要设备 (11)5、安全操作 (12)(1)锅炉系统 (12)(2)空压机系统 (14)(3)废液输送系统 (15)三、尾气处理岗位 (16)1、岗位任务 (16)2、工艺流程 (16)(1)工艺流程简述 (16)(2)工艺流程图 (17)3、主要操作指标 (17)4、管理范围及主要设备 (17)(1)管理范围 (17)(2)主要设备 (17)5、开车前的准备 (18)6、开车的条件与程序 (19)7、注意问题 (19)四、破碎输送岗位 (20)1、岗位任务 (20)2、工艺流程图 (20)3、管理范围及主要设备 (20)(1)管理范围 (20)(2)主要设备 (20)4、注意问题 (21)5、箱废上料岗位 (21)(1)岗位任务 (21)(2)管理范围及主要设备 (22)(3)开车前的检查 (22)(4)运行 (22)(5)注意问题 (22)五、行车岗位 (22)1、岗位任务 (22)2、工艺流程 (22)3、管理范围及主要设备 (23)(1)管理范围 (23)(2)主要设备 (23)4、链板输送机 (23)(1)开车前的检查 (23)(2)开车: (23)(3)注意问题: (23)5、行车岗位安全操作规程 (23)附录:泵故障诊断方法 (25)一、主控室1、岗位任务负责焚烧系统的运行操作控制;指挥各岗位的开停车和运行操作;完成危险废物焚烧和尾气的净化处理,达到如下要求:(1)焚烧工况稳定,废物焚烧彻底,焚烧效率、残渣热灼减率等指标合格。
回转窑的操作知识
挂窑皮的影响因素4.1 生料化学成分所谓挂窑皮就是液相凝固到耐火砖表面的过程。
因此熟料烧成液相量的多少液相粘度的高低直接影响到窑皮的形成,而生料化学成分直接影响液相量及其粘度。
以前湿法窑,人们主张挂窑皮期间的生料硅酸率适当偏低一些,而饱和比适当偏高一些。
但对于预分解窑,目前窑头都使用三风道或四风道燃烧器,回转窑正常运行时,一次风量少,二次风温度又很高。
因此煤粉燃烧速度、火焰温度远高于湿法窑。
如果降低硅酸率,液相量相应增加,物料容易烧流,挂上的窑皮不吃火容易脱落。
所以一般都主张挂窑皮的生料应与正常生料成分相同为好。
4.2 烧成温度和火焰控制挂好烧成带窑皮的主要因素除有一定的液相量和液相粘度以外,还要有适当的温度,气流、物料和耐火砖之间要有一定的温差。
一般应控制在正常生产时的烧成温度。
掌握熟料结粒细小而均齐,不烧大块更不能烧流,严禁跑生料。
升重控制在正常生产指标内。
要保持烧成温度稳定、窑速稳定、火焰形状完整、顺畅。
这样挂出的窑皮厚薄一致、平整、均匀、坚固。
4.3 喂料量和窑速为了使窑皮挂得坚固、均匀、平整,稳定窑内热工制度是先决条件。
挂窑皮期间,稳定的喂料量和稳定的窑速是至关重要的。
喂料量过多或窑速过快,窑内温度就不容易控制,粘挂的窑皮就不平整,不坚固。
所以新窑第一次挂窑皮起始喂料量和窑速最好能控制设计产量的35%左右。
挂到一定程度以后再视窑皮粘挂情况逐渐缓慢增加。
4.4 挂窑皮期间的喷嘴位置一般情况下,喷嘴位置应尽量靠前(往外拉)一点,同时偏料,火焰宜短不宜长。
这样高温区较集中,高温点靠前,使窑皮由窑前逐渐往窑内推进。
随着生喂料量的逐渐增加,喷嘴要相应往窑内移动。
待窑产量增加到正常情况,喷嘴也随之移到正常生产的位置。
挂窑皮期间切忌火焰太长,否则高温区不集中,窑皮挂得远或前薄后厚,甚至出现前面窑皮尚未挂好,后面已经形成结圈等不利情况。
5 回转窑火焰的调节目前国内预分解窑大多采用三风道或四风道燃烧器,而火焰形状则是通过内流风和外流风的合理匹配来进行调整的。
- 1、下载文档前请自行甄别文档内容的完整性,平台不提供额外的编辑、内容补充、找答案等附加服务。
- 2、"仅部分预览"的文档,不可在线预览部分如存在完整性等问题,可反馈申请退款(可完整预览的文档不适用该条件!)。
- 3、如文档侵犯您的权益,请联系客服反馈,我们会尽快为您处理(人工客服工作时间:9:00-18:30)。
电液动鄂式闸阀 汽车外运
烟 囱
静电除尘器
高温风机
液压推杆(12个)
余热锅炉
转运溜槽 回转窑 冷却器篦条筛 下部冷却室 电动卸料机(4台) 链斗(链斗称) 三通分料器 1#、2#多斗提升机 三通分料器 电动振筛 三通分料器 1#、2#块灰仓 电液动鄂式闸阀 汽车外运至炼钢
全灰
1#皮带机 三通分料器 2#皮带机
犁式分料器(6个)
3#粉料仓
10#粉灰仓
4#—9#粉料仓 电液动鄂式闸阀 火车外运烧结
火车运输石灰石 桥式抓斗起重机 石灰石堆棚 桥式抓斗起重机 受料地坑 电液动鄂式闸阀
6 0 0 t / d 活 性 石 灰 石 回 转 窑 工 艺 流 程 图
称量皮带 (电磁除铁器) 1#大倾角 电动振筛
筛 上 物
筛下物<15mm
碎石仓
>15㎜
2#大倾角 预热器上部料仓 下料溜管(12个)
各独立仓室(12个)