最新通用机加件检验作业指导书.pdf
机械加工通用作业指导书

带式输送机机械加工、焊接、滚筒作业指导书编制:审核:批准:山西交城县兴星冶金设备厂机械加工通用作业指导书1、操作者应仔细看清图纸和工艺文件的各项说明,保持图纸和工艺文件的清洁与完整,并应严格按设计图纸、工艺规程和技术标准进行零部件的加工,不得随意自行更改。
2、操作者按照工艺要求查看借用的工、夹、量、刀具是否符合工艺及使用要求,若有疑问,应立即与组长或车间生产管理者联系。
3、操作者应将工、夹、量、刀具分别整齐地放置在工具箱上或其它适当的地方,但不准直接放在机床上,并应妥善保管好,不得任意拆卸而改变原来尺寸或形状。
4、在加工前,操作者首先应检查、抽查毛坯或经由上道工序加工并和本工序有关的尺寸,以确定余量是否符合工艺要求。
5、操作者应按照工艺规定的定位基面安装零件。
工艺未规定定位基面的,允许操作者自行选择定位基面和装夹方法,但是必须保证加工出来的工件符合图纸和工艺上的尺寸和精度要求。
在装夹工具前,应将夹具和工件清理干净,在定位基面上不得有铁屑、毛刺、污物及磕碰现象。
6、预压紧工件后,应按工艺要求进行工件的校正,若工艺未作出规定时,可按下列方法校正工件:6.1、当在本工序或本工步中加工到成品尺寸,且以后该加工面不再加工,装配时也不再调整或刮研时,可以按定位基面到加工面技术要求的1/3值校正,最后加工完成后应保证图纸中的技术要求。
6.2、在本工序或本工步中加工的加工面以后尚需加工或刮研,则按该加工面下道工序余量的1/3值校正,加工后要按此检验。
6.3、在本工序或本工步中加工的加工面到成品尺寸,以后该加工面不再加工,且图纸、工艺卡片内对该加工面与定位面无任何要求时,加工后应达到通用技术标准。
7、按工艺要求进行压紧,如工艺上无要求,零件压紧时注意压紧力的位置、大小和方向,并允许自加各种辅助支承,以增强刚性。
压紧前与压紧后都要测量,防止变形和磕碰。
8、凡加工面末到成品尺寸而工艺卡片又未规定工序的粗糙度时,粗车、粗铣、粗刨、粗镗和粗插的表面粗糙度应为Ra6.3(△4),磨削前的各种表面粗糙Z应为Rd3.2(△5),粗磨时外围的表面粗糙度应为Ra0.8(△7),平面、轴、孔互为Ral.6(△6);刮研前的加工面应为Ra3.2~Ral.6(△5~△6)。
机加工件来料检验作业指导书

审查
制定
a.交验制品表面不允许存在扭曲、弯曲变形、裂纹、缺损、伤痕、开裂等缺陷;
b.焊接件焊口应焊接牢固可靠,表面光滑平整,不允许存在气孔,砂眼,漏焊,夹杂等焊接缺陷;表面去掉焊杂涂刷防腐底漆;
c.切割件表面不允许存在、开裂、及凹凸缺Байду номын сангаас、伤痕毛剌等缺陷;
d.切削件表面应符合图纸精度标准要求,棱角倒钝;
e.糟弯件、压弯件、冷作件表面应光滑平整,不允许有凹凸不平弯曲、扭曲、毛刺等制造缺陷;
分发编号:
零部件名称
机加工件
DAB分类
D
外购外协件检验指导书
文件编号
版次
3.0
图号
通用
规格、型号
通用
发行日期
页次
1/1
序号
检验项目
技术要求
验收器具
抽检比例
备注
名称
规格
1
2
3
4
标志:
外观:
几何尺寸:
机械性能:
1)送检单与零件号名称、图号、规格、型号、数量是否一致,是否有检验合格标志;
1)表面应平整光滑,不允许存在以下缺陷:
f.组合配件、组合总成件必需满足图纸装配设计要求,转动灵活,装配牢固可靠;表面去污浊毛刺;并进行防腐处理;
1)尺寸及公差应符合图纸要求;
1)配件物理机械性能及化学元素应附合图纸材料要求;
2)配套件材质检验报告由配套厂家提供;(安全项)
目测
目测
万能量具
材质报告
厂方报告
材料批次
No.
修订日期
修订内容
修订单
机加制程检验作业指导书
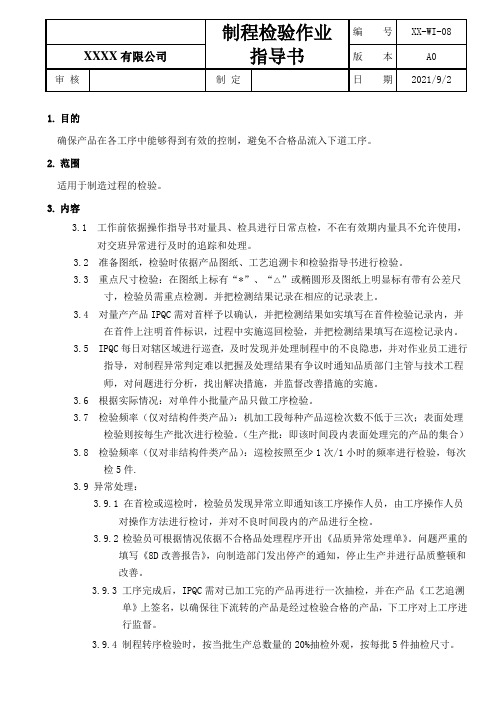
1.目的确保产品在各工序中能够得到有效的控制,避免不合格品流入下道工序。
2.范围适用于制造过程的检验。
3.内容3.1 工作前依据操作指导书对量具、检具进行日常点检,不在有效期内量具不允许使用,对交班异常进行及时的追踪和处理。
3.2 准备图纸,检验时依据产品图纸、工艺追溯卡和检验指导书进行检验。
3.3 重点尺寸检验:在图纸上标有“*”、“△”或椭圆形及图纸上明显标有带有公差尺寸,检验员需重点检测。
并把检测结果记录在相应的记录表上。
3.4 对量产产品IPQC需对首样予以确认,并把检测结果如实填写在首件检验记录内,并在首件上注明首件标识,过程中实施巡回检验,并把检测结果填写在巡检记录内。
3.5 IPQC每日对辖区域进行巡查,及时发现并处理制程中的不良隐患,并对作业员工进行指导,对制程异常判定难以把握及处理结果有争议时通知品质部门主管与技术工程师,对问题进行分析,找出解决措施,并监督改善措施的实施。
3.6 根据实际情况:对单件小批量产品只做工序检验。
3.7 检验频率(仅对结构件类产品):机加工段每种产品巡检次数不低于三次;表面处理检验则按每生产批次进行检验。
(生产批:即该时间段内表面处理完的产品的集合)3.8 检验频率(仅对非结构件类产品):巡检按照至少1次/1小时的频率进行检验,每次检5件.3.9 异常处理:3.9.1 在首检或巡检时,检验员发现异常立即通知该工序操作人员,由工序操作人员对操作方法进行检讨,并对不良时间段内的产品进行全检。
3.9.2 检验员可根据情况依据不合格品处理程序开出《品质异常处理单》。
问题严重的填写《8D改善报告》,向制造部门发出停产的通知,停止生产并进行品质整顿和改善。
3.9.3 工序完成后,IPQC需对已加工完的产品再进行一次抽检,并在产品《工艺追溯单》上签名,以确保往下流转的产品是经过检验合格的产品,下工序对上工序进行监督。
3.9.4 制程转序检验时,按当批生产总数量的20%抽检外观,按每批5件抽检尺寸。
机加工作业指导书
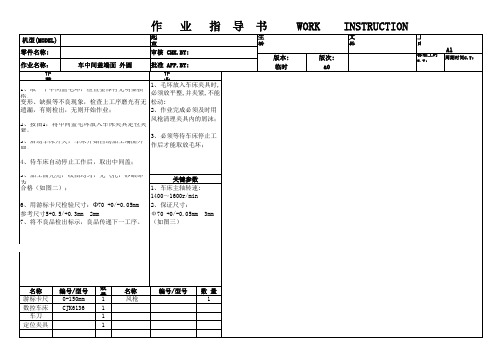
NG(不上锡) NG(上锡过量)
NG(锡尖) OK(上锡良好)
编号/型号
0-200mm 18-35mm
数量 1 1 1
NG(不上锡) NG(上锡过量)
NG(锡尖) OK(上锡良好)
作
业
指导书
WORK INSTRUCTION
机型(MODEL) 零件名称:
中间盖
起 草 审核 CHK.BY:
作业名称:
钻2-Ф3.3通孔
批准 APP.BY:
作
作
1、取一个業中间盖毛坯,检查整体有无明显损 伤、
变形、缺损等不良现象,有则检出,无则开
1、毛业坏放入台钻时,必须 放平整,并夹紧,不能松 动;
始作业;
生 效
版本: 临时
文 件
版次:
工 序
标准工时 S.T:
周期时间C.T:
2、作业完成必须及时用
2、将中间放入台钻开始攻丝;
风枪清理夹具内的屑沫;
批准 APP.BY:
作
作
1、取一个業中间盖毛坯,检查整体有无明显损 伤、
变形、缺损等不良现象,有则检出,无则开
1、毛业坏放入台钻时,必须 放平整,并夹紧,不能松 动;
始作业;
2、作业完成必须及时用
2、将中间盖放入台钻定位;
风枪清理夹具内的屑沫;
生 效
版本: 临时
版次:
文
工
件
序
标准工时
WI/TD001-SM05302A/A S.T:
关键参数 1、车床主轴转速: 1400~1600r/min 2、保证尺寸: 5+0.1/0.03mm 厚度8mm的尺寸 见图三
名称
编号/型号
数 量
机械加工检验作业指导书

精心整理1目的:为了保证我公司加工所有产品符合质量要求,指导我司在产品实现过程中实施质量过程控制, 通过严格执行三检,“首件检验”、“巡回检验”、“终检”将检验工作与工序控制紧密结合,对每一工序的质量问题或可能出现的质量问题不放过,剔除不合格品,使其不能投入下工序或出厂, 从而达到工序控制的目的而特制定本作业指导书。
2适用范围:本作业指导书适用于本公司所有自制产品零部件的检验。
3检测依据及判定标准:12 412体3456向5a b c d e 6a 术无论在任何情况下,首件检验未经检验合格,不得进行批量生产或继续加工作业(注意:除了开 发新品新工艺以外、检验一般不参与首件调试过程数据验证与记录,避免检验越权生产干涉,同 时也避免生产一线技术员对工艺准备、工艺指导、工艺监督不作为或推卸责任)。
b )作好首检检验记录,要求按工件种类分类、班别、机台及操作者填写首检记录,以便于追溯。
c )检验状态分为:合格、不合格、待检、检后待定;产品标识要求填写“工件料号/名称、规格、首检合格、日期、检验者等”要素,首检报告同样填写并要求与路线单一起放置直至本工序批次加 工结束、工序完工检验结束后收回并整理存档1年。
7巡回检验:精心整理由检验人员在生产现场,进行日常工艺纪律巡回监督检查,重点监控工序质量和工艺纪律,并做 好记录、并对质量异常出具《制程质量异常处理单》。
a )根据检验工艺规程和作业指导书的要求、检验、核对巡检产品的质量特性值是否真正符合要求。
b )若巡检时某质量特性值不合格,应按《不合格品控制程序》处理,同时,立即对本次巡检与上次巡检(或首检)间隔中生产的产品的不合格质量特性值逐件100%检查,剔除不合格品--追溯。
c )对巡检中剔除的不合格品按《不合格品的控制程序》进行处理。
d )对投入批量生产的工件某尺寸在机加工过程中有争议时,应立即报告技术部门进行分析性检查、 仲裁性检测,必要时核实工艺装备或工艺卡,严禁不合格工艺装备或工艺卡继续生产和现场毛坯 流入下道工序。
机械加工产品检验作业指导书

机械加工产品检验作业指导书————————————————————————————————作者:————————————————————————————————日期:一汽解放青岛汽车厂质量保证部技术文件编号:IPQC-JYZD-7-2009 批准:宋宗强机械加工产品检验作业指导书2008年12月31日发布2009年1月1日实施一汽解放青岛汽车厂质量保证部发布前言本检验作业指导书依据有关汽车标准及一汽解放青岛汽车厂技术文件制定。
是一汽解放青岛汽车厂质量保证部技术文件之一。
本检验作业指导书与国家标准、企业标准及相关技术文件相一致。
从实施之日起,原《IPQC-JYZD-7-2008机械加工产品验作业指导书》同时废止。
各相关部门检验机械加工产品质量时,都需要按本检验作业指导书的规定执行。
本标准由一汽解放青岛汽车厂质量保证部起草。
本检验作业指导书起草人:林桂升本检验作业指导书审核人:石建通1 主要内容与适用范围本检验作业指导书规定了机械加工产品的检验方式及质量记录。
本检验作业指导书主要适用于机加工车间。
2 引用标准下列标准包括的条文,通过在本检验作业指导书中的引用而构成本标准的条文。
在本检验作业指导书发布时,所示版本均为有效。
所有标准都会被修订,使用本标准的各方应探讨使用下列标准最新版本的可能性。
CA/CBG-1-82 切削零件未注公差尺寸的公差CA/CBG-9-91 未注公差角度的极限偏差3 检验及质量记录规定3.1所有机加工产品必须按产品标准、技术要求等进行自检控制。
3.2检验零件时,按控制计划合理选用量检具,并正确操作。
3.3未注公差尺寸的极限偏差3.3.1 切削零件的轴类、孔类、非孔轴类的未注公差尺寸的公差按下表执行。
基本尺寸mm 轴类孔类非孔轴类公差带mm大于至轴径长度厚度孔(直径≤50)孔(直径>50)槽宽镗孔深度和凸肩高钻孔深度和扩大通孔深度3-0.25+0.14+0.25±0.12+0.253 6-0.30+0.18+0.30±0.15+0.306 10-0.36+0.22+0.36±0.18+0.3610 18-0.43+0.27+0.43±0.21+0.4318 30-0.52+0.33+0.52±0.26+0.5230 50-0.62+0.39+0.62±0.31+0.6250 80-0.74+0.74±0.37+0.7480 120-0.87+0.87±0.43+0.87120 180-1+1±0.5+1基本尺寸mm 轴类孔类非孔轴类公差带mm180 250-1.15+1.15±0.57+1.15250 315-1.3+1.3±0.65+1.3315 400-1.4+1.4±0.7+1.4400 500-1.55+1.55±0.72+1.55500 630-1.75+1.75±0.82630 800-2+2.0±1.0800 1000-2.3+2.3±1.21000 1250-2.6+2.6±1.31250 1600-3.1+3.1±1.551600 2000-3.7+3.7±1.852000 2500-4.4+4.4±2.22500 3150-5.4+5.4±2.73.3.2 两孔的中心距和孔与零件边缘距离的未注公差尺寸的公差按下表执行。
通用机加件检验作业指导书

6.检验步骤……………………………………………………………2
7.过程检验……………………………………………………………2
8.成品检验……………………………………………………………3
9. 相关文件及记录……………………………………………………7
8.
外观缺
陷类型
缺陷所处
表面类型
允许范围
A级表面
B级表面
C级表面
基材花斑
金属表面
不允许
不允许
S总≤被测面积的5%
浅划痕
所有表面
不允许
L≤50×0.4,P≤2
P≤5
深划痕
所有表面
不允许
不允许
不允许
凹 坑
非拉丝和
喷砂面
不允许
直径≤0.5,P≤2
不限制
凹凸痕
所有表面
不允许
不允许
直径≤2.0,P≤5抛光区Fra bibliotek金属表面
不允许
不允许
S总≤被测面积的5%
烧 伤
拉丝面
不允许
不允许
不限制
水 印
电镀、氧化
不允许
S≤3.0,P≤2
不限制
露 白
镀彩锌
不允许
不允许
S≤4.0,P≤3
修 补
喷塑、电泳漆
不允许
S≤3.0,P≤1
S总≤被测面积的5%
颗 粒
所有表面
不允许
直径≤1.0,P≤2
直径≤3.0,P≤5
挂具印
所有表面
不允许
不允许
不限制
d、凹坑:由于基体材料缺陷,或在加工过程中操作不当等原因而在材料表面留下的小坑状痕迹;
机加工检验作业指导书

机加工检验作业指导书一、适用范围
生产部各部门自制件及外协件
二、作业要求
1、凡机械加工件必须符合产品图样、工艺规程和作业要求。
2、经加工的零件表面不允许有锈蚀和磕碰、划伤、裂纹等缺陷。
3、除有特殊要求外,加工后的零件不允许留有尖棱、尖角和毛刺。
4、滚压精加工的表面,滚压后不得有剥离及脱皮现象。
5、精加工后的表面、摩擦面和定位面等工作表面不允许在其上打印标记。
6、经加工后的零件在搬运、存放时,必须防止受到损伤、腐蚀及变形。
7、成组配对加工的零件需有标记。
三、未注尺寸公差参阅附件:技术标准 JB/T 5936-91
四、未注形状和位置公差参阅附件:技术标准 JB/T 5936-91
五、未注公差角度的极限偏差参阅附件:技术标准 JB/T 5936-91
六、螺纹、键和键槽参阅附件:技术标准 JB/T 5936-91
七、中心孔
1、图样中未注明、加工中又需要中心孔的零件,在不影响使用和外观的情况下,加工
后中心孔可以保留。
2、中心孔需符合GB 145的规定。
八、检验规则
1、凡经机械加工件,由制造厂质量检验部门按图样、有关技术文件和本要求进行检查
和验收。
2、机械加工件的外观按规定要求进行检查。
3、主要机械加工件需每件检查几何形状与尺寸。
九、标志
1、入库的机械加工件应有的标志
2、标志的位置应不使机械加工件的质量受到损伤。
3、机械加工件入库应附有吊牌。
其中应注明:名称、零件名称、图号;制造日
期。
编制:标准:审核:审批:。
- 1、下载文档前请自行甄别文档内容的完整性,平台不提供额外的编辑、内容补充、找答案等附加服务。
- 2、"仅部分预览"的文档,不可在线预览部分如存在完整性等问题,可反馈申请退款(可完整预览的文档不适用该条件!)。
- 3、如文档侵犯您的权益,请联系客服反馈,我们会尽快为您处理(人工客服工作时间:9:00-18:30)。
通用机加件检验规范文件属性三阶文件修订履历序号修改内容(摘要)版本制作核准生效日期1 新增 A 杨建涂松2011.11.13目录项目内容页次1. 目的 (2)2.适用范围 (2)3. 职责 (2)4. 述语定义 (2)5. 检验设备 (2)6. 检验步骤 (2)7. 过程检验 (2)8. 成品检验 (3)9. 相关文件及记录 (7)APPROV AL AUDIT FORMULATE ISSUED 刘锦锋涂松杨建品质部通用机加件检验规范文件属性三阶文件1.目的为保证我司机加件产品的质量,又减少图纸对通用要求的描述,特制定通用检验标准,提供依据,做到检验标准明确且规范化、标准化。
2.适用范围适用于本公司切削机加件,包括铸件、型材等的切削加工部分的加工过程控制及成品检验;3.职责3.1 品质工程师:负责制定和修订此检验规范适合本公司的适用性3.2品质工程师:根据此规范要求,制定来料、过程、成品检验作业指导书;3.2品质主管:对检验员的培训,及抽样作业监督3.4检验员根据此规范进行来料、过程和成品的检验。
4术语定义4.1 A级表面:在使用过程中经常被客户看见且被关注的部分;4.2 B级表面:在使用过程中常常被客户看见的部分但不会过分关注;4.3 C级表面:在使用过程中很少被客户注意到的表面部分。
5.检验设备5.1 检验设备和量具等精度、性能需要满足零件各检项目的需求。
6.检验步骤6.1 对照图纸要求之版本,是否与实物一致;6.2 清点图纸要求之数量,是否与实际相符;6.3 识别图纸要求之材料,是否与实物相符;6.4 审查图纸的尺寸、形位公差、外观、粗糙度等,选用合理检验方法和量具,保证检测数据的准确性。
6.5 审查技术说明:留意是否有对称件,不同类型的热处理、粗糙度等对特殊加工的要求。
6.6 审查图纸上英文/日文的注解说明;6.7 按次序对工件进行检验,检完一个尺寸,作一个记号,不能漏检;6.8 检验出来的不合格品,记录并标识清楚交由上级领导进行确认和处理。
7.过程检验:7.1 材料检验原材料符合图纸要求,达到本公司原材料检验标准。
7.2 设备检验加工设备及各项参数应能保证加工零件的精度。
7.3 尺寸检验:7.3.1 图纸上标注公差的,按标注值检验;7.3.2 图纸上未注公差的,按技术要求中的未注公差检验;7.4 形位公差检验:7.4.1 图纸上标注公差的,按标注值检验;7.4.2 图纸上未注公差的,按技术要求中的未注形位公差检验;未注形位公差由加工工艺保证,通用机加件检验规范文件属性三阶文件常规情况不检,有争议时进行检验7.5 粗糙度检验7.5.1 使用样块比较法,以表面粗糙度比较样块工作面上粗糙度值为准,用目视法与被测表面进行比较判定、被测表面的粗糙度值,需要时可用显微镜比较法,有争议时可用粗糙度仪检测,图纸有特殊要求时按图纸要求检验,用样块比较时,样块和被测表面材质、加工方法应一致,有电镀、喷涂等表面处的零件,图中粗糙度默认是表面处前的加工粗糙度。
7.6 螺纹检验:7.6.1 图纸标注螺纹公差等级的,按图纸要求检验,图纸未标注时,按下述原则7.6.2 普通螺纹黙认公差等级:内螺纹6H,外螺纹6g 例如:(M8);7.6.3 统一螺纹黙认公差等级:内螺纹2B,外螺纹2A 例如:(1/4-20 UNC);7.6.4 加工过程中必须用校对合格螺纹塞规/环规检验,要求“通规通、止规止”;7.7.外观检验:7.7.1表面不可有划伤、碰伤、刀伤、刀纹平整无段差台阶等;7.7.2去毛刺要求:用手沿零件加工边角的任何位置及方向触摸均无刮卡现象;7.7.3螺纹倒角:内螺纹倒角至大径,外螺纹倒角至小径;7.7.4机加件锐边(角)倒钝:常规情况下不检验倒钝值,存在有争议时以此为检验标准;7.7.4.1最短直壁大于2mm,倒0.5mm以下倒角或圆角,不刮手;7.7.4.2最短直壁小于或等于2mm,倒不超过0.2倍直壁倒角或圆角,不刮手;8成品检验8.1检验方案定义:8.1.1 抽检:所谓抽检是指从一个批次中抽出N个作为样本,进行全部的特性检验。
抽取的数量可以根据《AQL抽样检验作业指导书》文件执行,确定有代表性即可。
抽检一般是随机的,也就是从所有产品中随便拿取一定数量的单件作为样本来进行检验。
并以这些样本的检验结果来判定这些样本所代表的整批次产品的性能或质量。
8.1.2 全检:所谓全检是指根据某种标准对被检查产品进行全部的特性检验8.1.3 抽检&全检相互结合:根据我司客户产品质量需求采用的抽检与全检相互结合的检验方式进行验。
8.2 一致性:同批来料、外观、颜色、表面光洁度、加工工艺、表面处理、互换性、字唛、包装等.均应有良好的一致性。
8.3 尺寸检验:8.3.1 图纸上标注公差的,按标注值检验;8.3.2 图纸上未注公差的,按技术要求中的未注公差检验;8.4 形位公差检验:8.4.1 图纸上标注公差的,按标注值检验;8.4.2 图纸上未注公差的,按技术要求中的未注形位公差检验;未注形位公差由加工工艺保证,常规情况不检,有争议时进行检验8.5粗糙度检验8.5.1 使用样块比较法,以表面粗糙度比较样块工作面上粗糙度值为准,用目视法与被测表面进行比较判定、被测表面的粗糙度值,需要时可用显微镜比较法,有争议时可用粗糙度仪检测,图纸有特殊要求时按图纸要求检验,用样块比较时,样块和被测表面材质、加工方法应一致,有电镀、喷涂等表面处的零件,图中粗糙度默认是表面处前的加工粗糙度。
通用机加件检验规范文件属性三阶文件8.6 螺纹检验:8.6.1 图纸标注螺纹公差等级的,按图纸要求检验,图纸未标注时,按下述原则8.6.2 普通螺纹黙认公差等级:内螺纹6H,外螺纹6g 例如:(M8);8.6.3 统一螺纹黙认公差等级:内螺纹2B,外螺纹2A 例如:(1/4-20 UNC);8.6.4 成品检验时按照客户要求选择实配或经螺纹塞规/环规检验合格的螺母/螺钉检验螺纹,能顺畅通过或装配即合格。
8.7.外观检验:8.7.1外观检视条件及方法:--视力:校正视力 1.0以上;--目视距离:检查物距离眼睛A级面约40cm, B、C级面约70cm远;--目视角度:45度~90度(检查时产品应转动);--目视时间:A级面10秒/面,B、C面6秒/面;--灯光:大于500 LUX的照明度或公司车间正常照明度。
8.7.2表面光滑、平整、无毛刺、变形、锈蚀、裂纹、压折、夹渣、气孔等;预埋件、铆接件应牢靠、无松动,螺纹无缺损、无腐蚀等;不允许有加工遗留物存留在物件上;8.7.3去毛刺要求:用手沿零件加工边角的任何位置及方向触摸均无刮卡现象;8.7.4螺纹倒角:内螺纹倒角至大径,外螺纹倒角至小径;8.7.5机加件锐边(角)倒钝:常规情况下不检验倒钝值,存在有争议时以此为检验标准;8.7.5.1最短直壁大于2mm,倒0.5mm以下倒角或圆角,不刮手;8.7.5.2最短直壁小于或等于2mm,倒不超过0.2倍直壁倒角或圆角,不刮手;8.7.6零件的喷塑、喷漆层应均匀、连续,无缩孔、起泡、开裂、剥落、粉化、流挂、露底(局部无涂层或涂料覆盖不严)、指印等缺陷;8.7.7热处理方法应符合有效版本图纸要求,热处理后不应有过烧、氧化、脱碳、热裂、变形、斑点、翘曲、及表面晶粒不均不良现象。
8.7.8 表面处理:8.7.8.1表面处理方法应符合有效版本图纸要求,处理后表面光滑平整、无斑点、烧焦、起泡、水纹、镀层脱落、镀层不全以及电镀酸性渗渣物等存在;8.7.8.2表面处理后,零件表面允许有不可避免的轻微夹具印痕和轻微的水印;在不影响装配的情况下,边、棱角处允许有轻微的粗糙;非重要表面允许有轻微的水纹或个别的斑点;8.7.9其余外观缺陷要求请参见下表:外观缺陷类型缺陷所处表面类型允许范围A级表面B级表面C级表面基材花斑金属表面不允许不允许S总≤被测面积的5% 浅划痕所有表面不允许L≤50×0.4,P≤2 P≤5深划痕所有表面不允许不允许不允许通用机加件检验规范文件属性三阶文件凹坑非拉丝和喷砂面不允许直径≤0.5,P≤2 不限制凹凸痕所有表面不允许不允许直径≤2.0,P≤5抛光区金属表面不允许不允许S总≤被测面积的5% 烧伤拉丝面不允许不允许不限制水印电镀、氧化不允许S≤3.0,P≤2 不限制露白镀彩锌不允许不允许S≤4.0,P≤3修补喷塑、电泳漆不允许S≤3.0,P≤1 S总≤被测面积的5% 颗粒所有表面不允许直径≤1.0,P≤2 直径≤3.0,P≤5挂具印所有表面不允许不允许不限制图文损伤印刷图文不允许不允许不允许色点所有表面不允许S≤0.5,P≤3L≤50 S总≤被测面积的2% 露底电镀、喷涂不允许不允许不允许注S为单个缺陷面积(mm2),P为缺陷数量(个),L为缺陷长度或间距(mm)8.8.0说明:a、基材花斑:电抛光、电镀或氧化前因基体材料腐蚀、或者材料中的杂质、材料微孔等原因所造成的、与周围材质表面不同光泽或粗糙度的斑块状花纹外观;b、浅划痕:膜层表面划伤,但未伤及底层(即底层未暴露);对其它无膜层表面则为:目测不明显、手指甲触摸无凹凸感、未伤及材料本体的伤痕;c、深划痕:膜层表面划伤,且已伤至底层(即底层已暴露出来);对其它无膜层表面则为:目测明显、手指甲触摸有凹凸感、伤及材料本体的伤痕;d、凹坑:由于基体材料缺陷,或在加工过程中操作不当等原因而在材料表面留下的小坑状痕迹;e、凹凸痕:因基材受撞击或加工不良等而呈现出的明显变形、凹凸不平的现象,手摸时有不平感觉;f、抛光区:对基材上的腐蚀、划伤、焊接或铆接等部位进行机械打磨抛光后表现出的局部高光泽、光亮区域;g、烧伤:拉丝、电抛光、电镀处理时因操作不当、造成零件表面过热而留下的烧蚀痕迹;h、水印:电镀、氧化或电抛光后因清洗水未及时干燥或干燥不彻底所形成的斑纹、印迹;i、露白:镀彩锌钝化膜因磨擦而被去除、露出新层,或因缝隙截留溶液导致的无钝化膜现象,呈现为区别于周围颜色的白色;j、修补:因膜层损伤而用涂料所作的局部遮盖;k、颗粒:因材料夹杂物或外来物的影响而在表面形成的、颜色与正常表面一致的凸起现象;l、挂具印:指电镀、电抛光、氧化、喷涂等表面处理生产过程中,因装挂用辅助工具的遮挡而使其与零件相接触的部位产生局部无膜层的现象;通用机加件检验规范文件属性三阶文件m、图文损伤:印刷图文因局部脱落或擦伤、附着不良、污染等所造成的图形、字迹不完整不清晰的现象;n、色点:由材料、模具、环境或设备中的灰尘或夹杂物等影响在涂层中形成的不同色的斑点;o、露底:电镀层或喷涂层未能完全覆盖而露出基层表面;8.8.1对机加件的非喷漆(粉)表面可允许有下列缺陷:8.8.1.1 A级表面每100mm×100mm范围内允许有数量不超过一个且直径不超过0.50mm的轻微麻点、轻微的小划伤、极轻微的压痕及不可避免的轻微夹具伤痕;8.8.1.2 B、C级表面允许有:局部的轻微麻点、压坑(压坑深度不大于板材厚度公差的一半,直径不超过 1.0mm且须保证板材的最小厚度,且每100×100mm内不得超过5个);个别的轻微擦划伤(划痕长度不大于50mm);局部轻微的氧化色或顺轧制方向的暗色;8.8.1.3 使用材料应符合有效版本图纸的要求,材料本身应无变形、划伤、氧化、变色等;8.8.1.4 丝印颜色符合图纸要求,文字规范,图案清晰,直线平直、弧线规则,粗细均匀,无重影、无毛边无断线、无偏移、无异物、无油墨堆积及凸起、鼓泡、凹陷现象;8.8.1.5 热处理方法应符合有效版本图纸要求,热处理后不应有过烧、氧化、脱碳、热裂、变形、斑点、翘曲、及表面晶粒不均等不良现象;8.8.1.6 喷砂和拉丝的目数按图纸要求,图纸未作要求时喷砂和拉丝均按100目的标准;喷砂后零件表面不得有明显变形;拉丝后整个表面纹路均匀,拉丝方向按图纸要求,图纸未作要求时与零件长边方向一致,拉丝后表面不得有烧伤痕迹;8.8.2 喷漆(粉)件表面外观要求:8.8.2.1 喷漆或喷粉件颜色、纹理参照有效的颜色样板及签样检验;8.8.2.2 颜色检验:标准要求△E≤1.0;检验时以目视检验为主,不得有明显色差。