机械加工件检验标准
自动化设备机械加工件来料检验标准
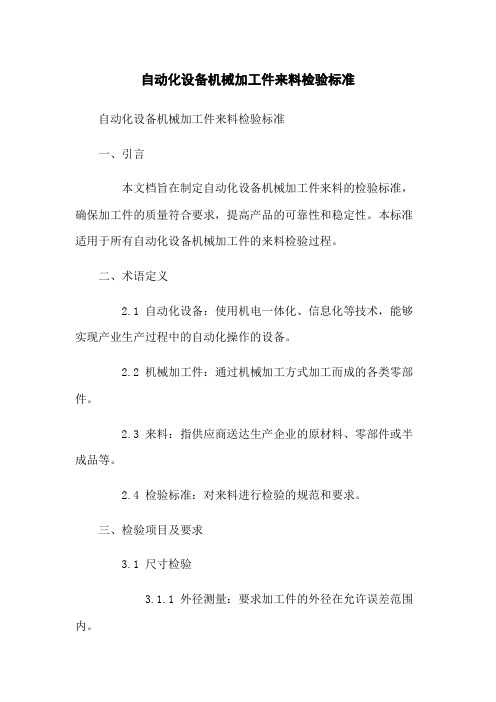
自动化设备机械加工件来料检验标准自动化设备机械加工件来料检验标准一、引言本文档旨在制定自动化设备机械加工件来料的检验标准,确保加工件的质量符合要求,提高产品的可靠性和稳定性。
本标准适用于所有自动化设备机械加工件的来料检验过程。
二、术语定义2.1 自动化设备:使用机电一体化、信息化等技术,能够实现产业生产过程中的自动化操作的设备。
2.2 机械加工件:通过机械加工方式加工而成的各类零部件。
2.3 来料:指供应商送达生产企业的原材料、零部件或半成品等。
2.4 检验标准:对来料进行检验的规范和要求。
三、检验项目及要求3.1 尺寸检验3.1.1 外径测量:要求加工件的外径在允许误差范围内。
3.1.2 内径测量:要求加工件的内径在允许误差范围内。
3.1.3 高度测量:要求加工件的高度在允许误差范围内。
3.2 表面质量检验3.2.1 表面粗糙度检测:要求加工件的表面粗糙度符合要求的等级。
3.2.2 表面缺陷检测:要求加工件的表面没有明显的裂纹、磨损或划痕等缺陷。
3.3 材料成分分析3.3.1 化学成分检测:要求加工件的化学成分符合设计要求。
3.3.2 金相组织检测:要求加工件的金相组织均匀、无明显气孔和夹杂物。
3.4 力学性能检验3.4.1 抗拉强度检测:要求加工件的抗拉强度在允许误差范围内。
3.4.2 延伸率检测:要求加工件的延伸率在允许误差范围内。
四、检验方法4.1 尺寸检验方法4.1.1 使用测量仪器对加工件进行尺寸测量。
4.1.2 根据设计图纸要求,对测量结果进行判断。
4.2 表面质量检验方法4.2.1 使用表面粗糙度仪对加工件表面进行粗糙度检测。
4.2.2 使用目视和触摸等方法对加工件表面进行缺陷检测。
4.3 材料成分分析方法4.3.1 采用化学分析方法对加工件的成分进行检测。
4.3.2 采用金相显微镜等设备对加工件的金相组织进行检测。
4.4 力学性能检验方法4.4.1 使用拉伸试验机对加工件进行抗拉强度检测。
机加工件外观检验标准

机加工件外观检验标准(总3页) -本页仅作为预览文档封面,使用时请删除本页-加工件外观检验标准1 范围本程序规定了无任何表面处理一般加工件(机加工部位)在样品验证、月度抽检和批次检验的过程中外观可接收的标准。
本程序适用各车间一般机加工件的外观质量检验。
2 定义粗糙度:表面光洁程度。
撞伤:工件上的浅坑。
划痕:浅的沟槽。
污渍:工件上的可见的油渍。
毛刺:机加工后产生的尖锐突起。
3. 外观等级分类产品分类:A一般结构件 B 轴类 C 其他类部件表面可见程度分类:Ⅰ经常被注意到的(客户在使用时经常会看到的,正面的)。
Ⅱ偶尔被注意到的(客户在使用时不经常看到的,侧面和底面的)。
Ⅲ难以被注意的(只用在安装或维修时才能看到的,内部的)。
4. 职责负责对送检的零件按本作业指导书进行检验,并判定合格或不合格。
根据公司产品质量要求的变化及时修正本作业指导书。
5. 验收标准机加工件材料应符合图纸要求。
通用要求工件表面应没有污渍(不可擦除的)。
工件不得有锐边(以一般手指触摸没有扎手感),不得有毛刺。
表面粗糙度应符合图纸要求。
螺纹孔内不得有切削液,攻丝油等(防锈油除外)残留。
工件表面不允许有锈斑,锈迹。
表面撞伤,划伤判定标准。
注:表内缺陷数是在200mmX300mm范围内。
如物料还需要再进行表面处理,焊接等二次加工的,按不影响使用和二次加工判定。
如遇特殊异常(严重撞伤,明显有损观瞻的)由车间与客户协商处理。
7 包装和保护供方应采用合适的流转器具装运工件,避免跌落与磕碰。
如工件的表面要求比较高,应制作专用的流转器具或进行必要的包装。
8、外观存在的问题。
机械加工工艺流程检验标准及规范
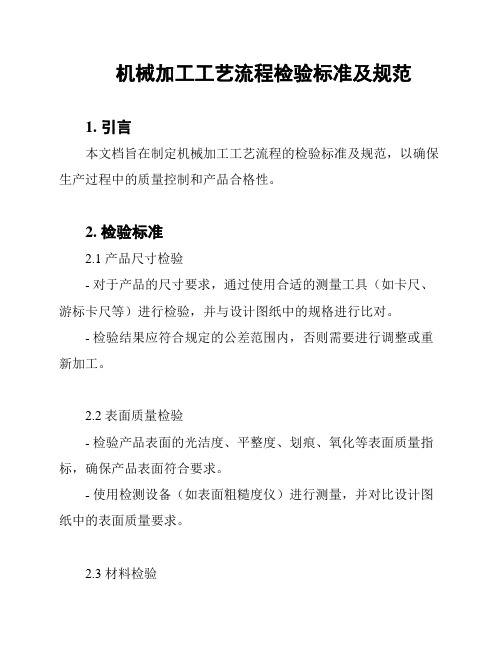
机械加工工艺流程检验标准及规范1. 引言本文档旨在制定机械加工工艺流程的检验标准及规范,以确保生产过程中的质量控制和产品合格性。
2. 检验标准2.1 产品尺寸检验- 对于产品的尺寸要求,通过使用合适的测量工具(如卡尺、游标卡尺等)进行检验,并与设计图纸中的规格进行比对。
- 检验结果应符合规定的公差范围内,否则需要进行调整或重新加工。
2.2 表面质量检验- 检验产品表面的光洁度、平整度、划痕、氧化等表面质量指标,确保产品表面符合要求。
- 使用检测设备(如表面粗糙度仪)进行测量,并对比设计图纸中的表面质量要求。
2.3 材料检验- 对使用的材料进行检验,确保其符合设计要求和相关标准。
- 检查材料的外观、密度、硬度等指标,并与相关标准进行对比。
2.4 装配与安装检验- 对于需装配和安装的零部件,进行装配和安装前的检验,确保其符合设计要求。
- 检验装配和安装的精度、间隙、螺纹连接等,并根据相应标准进行评估。
2.5 功能性检验- 对产品的功能进行检验,确保其符合设计要求。
- 进行实际操作或使用测试设备进行功能性测试,并进行性能指标评估。
3. 规范3.1 检验程序规范- 制定机械加工工艺流程的检验程序规范,定义各项检验的顺序和方法。
- 确保检验过程的可追溯性和一致性。
3.2 检验记录规范- 规定检验过程中产生的记录方法和要求。
- 记录检验结果、异常情况、处理措施等信息。
3.3 不合格品处理规范- 规定不合格产品的处理流程和责任分工,并制定相应的纠正和预防措施。
4. 结论制定机械加工工艺流程的检验标准及规范对于保证产品质量和生产效率具有重要意义。
本文档提出了产品尺寸、表面质量、材料、装配与安装、功能性等方面的检验标准,并规定了相应的检验程序和记录规范,以及不合格品的处理规范。
机械加工检验通用规范最新版

机械加工检验通用规范最新版机械加工检验通用规范(最新版)机械加工是工业制造中的重要环节,为了确保加工质量和产品合格率,机械加工检验是必不可少的环节。
机械加工检验通用规范是对机械加工过程中的检验要求和方法进行规范的文件,它起到统一标准、提高效率、保证质量的作用。
以下是最新版机械加工检验通用规范的概述,主要包括检验对象、检验要求、检验方法和结果判定等几个方面。
1.检验对象:机械加工检验通用规范适用于各种机械加工产品的检验,包括金属零件、塑料制品、机械装置等,涵盖了机械加工过程中的各个环节。
2.检验要求:机械加工检验的主要目的是确定产品是否符合设计要求和技术条件。
同时,还需要检验产品的功能性、安全性、可靠性、稳定性等指标,确保产品能够达到预期的使用效果。
3.检验方法:机械加工检验涉及到的检验方法有很多种,主要根据不同产品的特点和检验要求来选择适用的方法。
常见的检验方法包括外观检查、尺寸测量、材料分析、物理性能测试、功能性测试等。
在选择合适的方法时,需要根据产品的特点和检验要求进行综合考虑。
4.结果判定:机械加工检验的结果判定要根据检验数据和要求进行评估,并给出相应的结论。
对于合格的产品,可以出具合格证明;对于不合格的产品,需要进行分类处理,包括返修、报废、退换货等。
在结果判定过程中,要确保判定结果的准确性和公正性。
总的来说,机械加工检验通用规范最新版对机械加工过程中的检验要求和方法进行了全面规范,对于提高产品质量和加工效率具有重要意义。
机械加工企业应该根据最新版的规范开展机械加工检验工作,确保产品的合格率和质量水平,提升企业竞争力。
同时,还应该不断更新和完善机械加工检验通用规范,以适应新的技术和工艺的发展。
机械加工零件检验标准
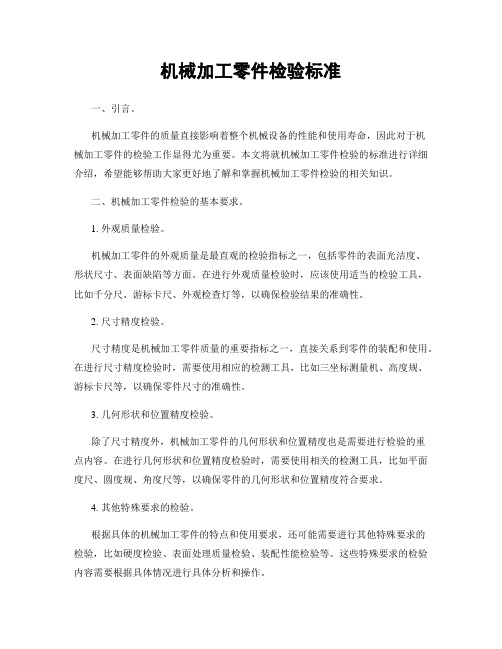
机械加工零件检验标准一、引言。
机械加工零件的质量直接影响着整个机械设备的性能和使用寿命,因此对于机械加工零件的检验工作显得尤为重要。
本文将就机械加工零件检验的标准进行详细介绍,希望能够帮助大家更好地了解和掌握机械加工零件检验的相关知识。
二、机械加工零件检验的基本要求。
1. 外观质量检验。
机械加工零件的外观质量是最直观的检验指标之一,包括零件的表面光洁度、形状尺寸、表面缺陷等方面。
在进行外观质量检验时,应该使用适当的检验工具,比如千分尺、游标卡尺、外观检查灯等,以确保检验结果的准确性。
2. 尺寸精度检验。
尺寸精度是机械加工零件质量的重要指标之一,直接关系到零件的装配和使用。
在进行尺寸精度检验时,需要使用相应的检测工具,比如三坐标测量机、高度规、游标卡尺等,以确保零件尺寸的准确性。
3. 几何形状和位置精度检验。
除了尺寸精度外,机械加工零件的几何形状和位置精度也是需要进行检验的重点内容。
在进行几何形状和位置精度检验时,需要使用相关的检测工具,比如平面度尺、圆度规、角度尺等,以确保零件的几何形状和位置精度符合要求。
4. 其他特殊要求的检验。
根据具体的机械加工零件的特点和使用要求,还可能需要进行其他特殊要求的检验,比如硬度检验、表面处理质量检验、装配性能检验等。
这些特殊要求的检验内容需要根据具体情况进行具体分析和操作。
三、机械加工零件检验的标准。
1. 国家标准。
国家对于机械加工零件的检验工作制定了相关的标准,比如GB/T 1184-1996《精密量规》、GB/T 1184-1996《精密量规》等,这些国家标准是机械加工零件检验工作的重要依据,需要严格遵守和执行。
2. 行业标准。
除了国家标准外,不同的行业还可能制定了针对机械加工零件的检验标准,比如汽车行业的相关标准、航空航天行业的相关标准等,这些行业标准是根据具体行业的特点和要求而制定的,需要根据实际情况进行具体执行。
3. 企业标准。
一些大型企业可能会根据自身的生产特点和质量要求,制定了针对机械加工零件的检验标准,这些企业标准是企业质量管理体系的重要组成部分,需要严格执行和遵守。
【最新】机械加工检验标准及方法
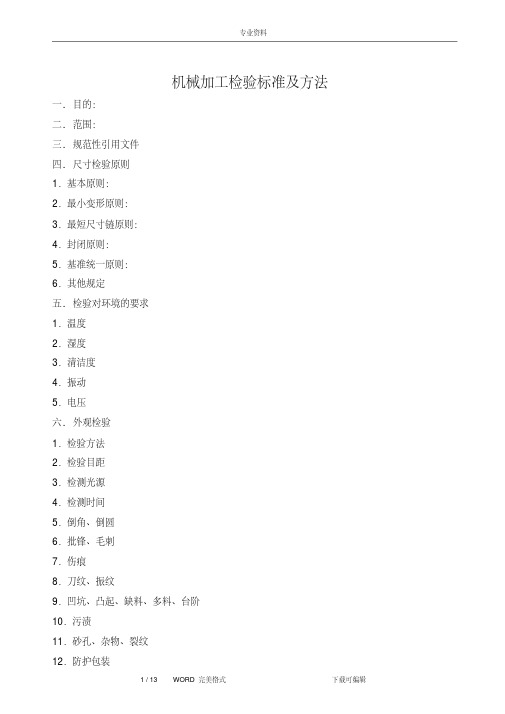
机械加工检验标准及方法一. 目的:二. 范围:三. 规范性引用文件四. 尺寸检验原则1.基本原则:2.最小变形原则:3.最短尺寸链原则:4.封闭原则:5.基准统一原则:6.其他规定五. 检验对环境的要求1.温度2.湿度3.清洁度4.振动5.电压六. 外观检验1.检验方法2.检验目距3.检测光源4.检测时间5.倒角、倒圆6.批锋、毛刺7.伤痕8.刀纹、振纹9.凹坑、凸起、缺料、多料、台阶10.污渍11.砂孔、杂物、裂纹12.防护包装七. 表面粗糙度的检验1.基本要求2.检验方法:3.测量方向4.测量部位5.取样长度八. 线性尺寸和角度尺寸公差要求1.基本要求2 线性尺寸未注公差九.形状和位置公差的检验1.基本要求3.检测方法十.螺纹的检验1.使用螺纹量规检验螺纹制件2.单项检验十一.外协加工件的检验规定1.来料检验2. 成品检验计划十二.判定规则附注:1.泰勒原则一. 目的:为了明确公司金属切削加工检验标准,使检验作业有所遵循,特制定本标准。
二. 范围:本标准适用于切削加工(包括外协、制程、出货过程)各检验特性的检验。
在本标准中,切削加工指的是:车削加工、铣削加工、磨削加工、镗削加工、刨削加工、孔加工、拉削加工和钳工作业等。
本标准规定了尺寸检验的基本原则、对环境的要求、外观检验标准、线性尺寸公差要求、形位公差要求、表面粗糙度的检验、螺纹的检验和判定准则。
注:本标准不适用于铸造、锻造、钣金、冲压、焊接加工后的检验,其检验标准另行制定。
本标准不拟对长度、角度、锥度的测量方法进行描述,可参看相关技术手册;形位公差的测量可参看GB/T1958-1980;齿轮、蜗杆的检验可参看相关技术手册。
三. 规范性引用文件下列文件中的条款通过本标准的引用而成为本标准的条款。
凡是注日期的引用文件,其随后所有的修改单(不包括勘误的内容)或修订版均不适用于本标准,然而,鼓励根据本标准达成协议的各方研究是否可使用这些文件的最新版本。
机械加工检验标准及方法(1)

机械加工检验标准及方法(1)机械加工是现代工业生产中不可或缺的一环,机械加工检验是确保机械加工产品质量的重要环节。
为了确保机械加工产品的合格率,合理地制定适合生产的检验标准及方法是必要的。
本文将详细介绍机械加工检验标准及方法。
机械加工检验标准机械加工产生的产品有尺寸精度、表面质量、几何精度、材料硬度等多个方面的品质要求。
机械加工检验标准是指根据机械加工产品的不同品质要求,制定出一系列检验标准,用于对机械加工产品进行检验。
常见的机械加工检验标准有GB、ISO、JIS等标准。
在实际操作中,应根据机械加工产品的实际需求和使用要求,选择合适的检验标准进行检验。
同时,对于特定的机械加工产品,也可以根据实际需求制定符合实际情况的检验标准。
机械加工材料的检验方法机械加工材料的检验是确保机械加工产品质量的关键环节。
在机械加工成品的检验过程中,不仅要对成品进行检验,还要对原材料进行检验。
下面我们将详细介绍机械加工材料的检验方法。
金属材料的检验方法金属表面缺陷的检验钢材表面缺陷常见有裂纹、划痕、气泡、硅酸盐夹杂物等。
缺陷类型众多,方法不同。
一般来说,通过目视检查、手摸检查、探伤、磁粉探伤等方法可检测出钢材表面缺陷。
但有些缺陷需要通过仔细打磨能够去除,在制作机械零件时才可使用。
金属含量的检验从金属材料中提取样品,经过化学分析,就可以得到其组成。
从而判断其是什么金属及含量是否符合标准。
非金属材料的检验方法干燥状态的检验如混凝土等,在干燥状态下检测其强度。
取样检验如塑料等,可在规定的机器、水平面等条件下,按规定的方法将试样切割成均匀大小的试样,然后采用拉伸、弯曲等方法进行检验。
机械加工验收方法验收是机械加工产品交付使用前的最后一道程序。
通过验收可以确定机械加工产品是否符合质量标准,以及确认产品的使用性能是否符合用户要求。
机械加工产品的验收方法主要包括自检、互检和专家检查。
自检自检主要是由机械加工产品生产者自己进行,通过严格的自我检查,查找产品的问题,使其能够符合相应的质量标准。
机械加工件检测标准

机械加工件检测标准1、目的:通过严格执行三检,“首件检验”、“巡回检验”、“完工检验”将检验工件与工序控制紧密结合,对每一工序的质量问题或可能出现的质量问题不放过,不合格品不能转入下工序,从而提高产品质量。
2、适用范围:所有加工件3.检验原则3.1.检验人员必须具有一定的专业知识和实际工作经验,且能满足现行产品对检验工作的各项要求。
3.2.检验人员所用的计量器具必须是经计量部门校验合格并在规定周期内。
3.3.检验人员验收产品前应熟读相关图样和技术文件,了解零件的关键尺寸及装配关系要点。
3.4 检验人员必须严格按照图样和技术文件所规定的要求对零件进行判定。
4.检验依据检测依据按图纸及工艺卡检测5.检测种类:“工序自检”“首件检验”、“巡回检验”、“完工检验”5.1.工序自检:工件完成工序后进行自检,自检合格后在工艺卡进行签字;5.2.首件检验:批量工件必须首件检验后,才能开始加工5.2.1.对首件,根据加工工艺要求,核实首件产品或工件(毛坯)产品的质量特性是否符合要求。
对首批检查的工件,操作者必须做好自检,在操作者缺乏检测手段时,也应对工件外观质量自检,合格后送质量专员检查。
无论在任何情况下,首件检验未经检验合格,不得进行批量生产或继续加工作业。
5.2.2.工作班开始加工的第一个工件;5.2.3.调换操作者后加工的第一个工件;5.2.4. 更换(调整)工艺装备或更换模具后加工的第一个工件;5.2.5.更换材料批(炉)号后加工的第一个工件;5.2.6. 代用材料后加工的第一个工件;5.2.7.检验内容:根据检验标准的要求,核对首件产品的质量特性值是否真正符合要求;对首件检验合格,批准生产加工,首件检验不合格,进行不合格品的处理,同时分析不合格原因,采取改进措施后加工,产品继续首件检验,直至合格为止。
5.3.巡回检验:5.3.1.由检验人员在生产现场,进行日常巡回监督检查,重点监控工序质量和典型零件质量;5.3.2根据检验标准、图纸和工艺的要求、检验、核对巡检产品的质量特性值是否真正符合要求;5.3.3.若巡检某质量特性值不合格,应按《不合格品报告单》处理,同时。
- 1、下载文档前请自行甄别文档内容的完整性,平台不提供额外的编辑、内容补充、找答案等附加服务。
- 2、"仅部分预览"的文档,不可在线预览部分如存在完整性等问题,可反馈申请退款(可完整预览的文档不适用该条件!)。
- 3、如文档侵犯您的权益,请联系客服反馈,我们会尽快为您处理(人工客服工作时间:9:00-18:30)。
机械加工件检验标准
1.目的
规范机械加工件的检验标准,以使各工序过程的产品质量得以控制。
2.适用范围
本标准适用于机械加工件的检验,图纸和技术文件并同使用。
如与国家标准和技术规范冲突时,以国家标准和技术规范为准。
3.引用标准
本标准的尺寸未注单位为mm。
JB/T5000.9《重型机械通用技术条件切削加工件》
GB/T 1031《表面粗糙度参数及其数值》
GB/T1800.4《极限与配合标准公差等级和孔轴的极限偏差表》
GB/T 3 《普通螺纹收尾、肩距、退刀槽和倒角》
GB/T197《普通螺纹公差》
GB/T 1184 《形状和位置公差未注公差值》
GB/T 1804 《一般公差未注公差的线性和角度尺寸的公差》
GB/T5277《紧固件螺栓和螺钉通孔》
4.原材料检验
机械加工件所用板料,棒料的材质,规格和数量是否符合按图加工所需。
详细做好原材料入库记录。
不合格材料办理好退货手续。
5.工序质量检验
5.1零件加工后应符合产品图样和技术条件及JB/T 5000.9《重型机械通用技术条件切削加工件》规定。
5.2 零件应按工序检查、验收,在前道工序检查合格后方可转入下道工序。
5.3 铸钢件、铸铁件、有色金属铸件、锻件加工后如发现有砂眼、缩孔、夹渣、裂纹等缺陷时,在不降低零件强度和使用性能的前提下,允许按照相关标准的有关规定修补,经检验合格后方可继续加工。
5.4 加工后的零件不允许有毛刺,除产品图样有要求外,不允许有尖棱、尖角。
5.5 精加工后的零件不允许直接摆放在地面上,应采取必要的支撑、保护措施。
加工面不允
许有锈蚀和影响性能、寿命或外观的磕碰、划伤等缺陷。
5.6 精加工后的配合面、摩擦面和定位面等工作表面不允许打印标记。
5.7 最终工序为热处理的零件,热处理后表面不应有氧化皮。
精加工后的配合面、齿面不应有退火、发蓝、变色的现象。
5.8对于生产图样中要求电镀锌或热镀锌的零件,图中要求的配合面尺寸为含镀层后的尺寸。
5.9表面电镀锌涂层的质量要求:
1)镀层外观光滑细致、无起泡、起层、剥落、烧焦及海绵状沉淀;
2)经铬酸钝化后,应具有绿黄略带有红色的彩虹色;
3)镀层表面允许有不严重的流痕及轻微的刮痕印,允许工件边缘色彩稍淡;
4)钝化膜有一定的光泽,不到呈暗褐无光的泥巴色;
5)钝化膜应牢固,用布揩擦不掉;在50℃~60℃的热水中煮1小时,颜色无显著减退。
6)镀层厚度8~12μm。
5.10 表面热镀锌涂层的质量要求:
1)表面应均匀、无毛刺、过烧、挂花、伤痕等缺陷,不得有影响安装的锌瘤。
2)镀层厚度35~45μm。
5.11 达克罗涂层的质量要求:
1)锌铬涂层应连续、无漏涂、气泡、剥落、裂纹、麻点、杂物等缺陷,涂层应基本均匀,无明显的局部过厚现象,涂层不应变色,但允许有小黄点斑点存在。
2)涂层厚度:5.8μm,二涂二烘。
按GB/T 6462要求金相显微镜测量。
3)耐盐雾腐蚀性能:480小时后无红锈。
4)耐水性能:按要求耐水试验后,按GB/T5270要求胶带附着强度试验,涂层不得剥落和露底。
5)耐湿热性能:按要求耐湿热试验,240小时不得有红锈。
5.12 图样中未注特征的规定
5.12.1 零件图样中未注明倒角时,按JB/T 5000.9中表1规定倒角。
5.12.2零件图样中未注明倒圆尺寸又无清根要求时,应按JB/T5000.9中表2规定倒圆。
5.12.3螺纹
1) 普通螺纹精度按GB/T 197规定的6H/6g执行。
2)普通螺纹收尾、肩距、退刀槽和倒角尺寸按GB/T 3执行。
3)加工的螺纹表面不允许有黑皮、磕碰、乱扣和毛刺等缺陷。
4)内、外螺纹旋入侧在加工螺纹前必须倒角,外螺纹为45°,内螺纹为60°,倒角深度等于牙型高度。
5)普通螺纹表面粗糙度:内螺纹不大于Ra12.5μm,外螺纹不大于Ra6.3μm。
5.12.4 中心孔
1)中心孔需保留或去除,应在图样上注明,则视为中心孔保留或去除均可。
2)中心孔的类型、尺寸按相应标准执行。
3)中心孔錐面的表面粗糙度: 用于粗加工时Ra值不大于6.3μm;用于精加工时Ra值不大于3.2μm;用于精密零件加工时Ra值不大于1.6μm。
5.13 图样中未注公差的规定
5.13.1 长度尺寸的未注公差见JB/T 5000.9中表3。
5.13.2 倒圆半径和倒角高度的未注公差见JB/T5000.9中表4。
5.13.3 角度(倾斜度)的未注公差见JB/T5000.9中表5。
5.13.4 未注直线度和平面度见JB/T5000.9中表6。
5.13.5未注垂直度公差见JB/T5000.9中表7。
5.13.6 未注对称度公差见JB/T 5000.9中表8。
5.13.7未注同轴度和圆跳动公差见JB/T5000.9中表9。
5.13.8 键槽的未注对称度公差见JB/T5000.9中表10。
5.13.9 未注圆度、圆柱度、线轮廓度和面轮廓度未注公差值应小于未注尺寸公差值。
5.13.10未注平行度公差值取两平行要素的直线度(平面度)和其之间尺寸的未注公差值中较大者。
6.验收程序
6.1 验收前准备
1)熟悉图纸资料,并准备符合验收标准要求的量器具。
2)对要求精密度较高的加工件,应请相关工程技术人员协助安装配合后验收。
6.2 外观检查验收
1)检查机加工件的光洁度是否符合要求。
2)检查机加工件外表有无残损、锈蚀、碰伤及螺纹外形和旋向是否正确。
3)如发现问题,应做详细记录备查。
6.3 数量验收
1)依据加工清单,检查加工件的材质,规格及数量;并逐件清查核对。
2)做好数量验收记录,写明验收地点、时间、参加人员、种类、品名、应到和实到数量。
6.4 质量验收
1)严格按照图纸要求及标准规定进行验收。
2)认真做好记录,如出现质量问题,应将详细情况书面通知加工单位,视情况决定是否退货、更换。
3)有特殊要求的情况下,可组织相关人员共同验收,待组装合格后方可签署验收文件。
4)一般验收期限为2天,特殊情况需看使用验收效果的视情况确定。
5)验收不合格的加工件,必须在规定验收期限内办理检修或退货手续。
附表:JB/T5000.9《重型机械通用技术条件切削加工件》。