世界名企汽车模具制造技术
hasco标准

HASCO标准HASCO标准是什么?为什么它是世界上最广泛使用的模具配件生产标准之一?HASCO标准有哪些优点和特点?如何利用HASCO标准提高模具设计和制造的效率和质量?本文将为您详细介绍HASCO标准的相关知识,帮助您更好地了解和应用这一国际领先的模具技术。
HASCO标准的由来和发展HASCO是德国哈斯科公司(HASCO Hasenclever GmbH + Co KG)的简称,该公司成立于1924年,是世界上最早从事模具配件生产和销售的企业之一。
哈斯科公司以其创新精神和卓越品质,开发了一系列符合国际标准的模具配件,为全球的模具设计和制造提供了便捷、高效、可靠的解决方案。
¹HASCO标准是哈斯科公司根据多年的模具经验和客户需求,制定的一套完整、系统、统一的模具配件生产标准,包括了模具基础、顶针、热流道系统、定位零件、注塑机配件、多喷嘴系统等各种类型和规格的模具配件。
HASCO标准不仅适用于哈斯科公司自己生产的模具配件,也适用于其他厂家按照HASCO标准生产的模具配件,实现了不同厂家、不同国家、不同类型的模具配件之间的互换性和兼容性。
²HASCO标准自从诞生以来,就受到了全球模具行业的广泛认可和欢迎,成为了世界三大模具配件生产标准之一,与美国的DME标准、日本的MISUMI标准齐名。
目前,HASCO标准已经被应用于汽车、电子、医疗、消费品等各个领域的模具设计和制造,覆盖了世界上90%以上的市场。
³HASCO标准的优点和特点HASCO标准之所以能够在激烈的国际竞争中脱颖而出,得益于其以下几个方面的优点和特点:互配性强:HASCO标准采用了统一的尺寸和公差,保证了不同厂家、不同国家、不同类型的模具配件之间可以无缝对接,无需进行额外的加工或调整。
这样可以大大节省了模具设计和制造的时间和成本,提高了模具的通用性和灵活性。
设计简洁:HASCO标准遵循了“简单即美”的设计理念,尽量减少了多余的零件和结构,使得每一个模具配件都能够发挥最大的功能和效果。
先进汽车模具技术成为推进汽车自主品牌发展的关键

模 具工 业 2 0 1 3 年第3 9 卷第 1 O 期
的 问题 , 这 些 问题 加 大 了我 国模 具 企业 发展 的压力 。单 个模 具 企业 力量 薄 弱 , 解 决 问题 的 能力有 限 。因此 ,
业 内专 家倡 导模 具 企业 结成 联盟 , 共 渡难 关 。
面对 各 种 阻碍 模 具 企 业 发 展 的难 题 , 各 模 具 企业 之 间应 比 以往 任 何 时候 都 要 加 强沟 通 和 理解 , 消 除 隔 阂, 增 强 行业 内部 团 结 。模 具 企业 在 互 相信 任 的基 础 上 , 可逐 步 构建 诚 信体 系 , 在 互 惠互 利 的基础 上 加 强合 作, 逐 渐 形成 战术 上 的组合 和 战略 上 的联 盟 。 此外 , 模具 企 业 还 可 以联 盟 的 名义 承 接业 务 , 根据 企 业 情况 和 各 自特 点进 行 专业 分 工 。这 不 仅 可 以避 免恶 性 竞 争 , 减 少 内耗 , 维护 企 业 利 益 , 还可 以充 分 发挥 各 自优 势 , 扬 长避 短 。这 种联 盟 形 式还 有 利 于整 合 资源 , 实现 资源 共享 , 避 免重 复 投 资 , 减 少投 资风 险 , 提 高 设 备利 用 率 。一 些 企业 还 可 以建 立 “ 协作 加 工 网” 的形 式进 行 合作 。总之 , 一切 有 利于 模 具企 业 结成 联 盟 , 有 利 于 加强 模 具企 业 间合 作关 系 的方 式 , 都将 有 利
主化 制 造 依赖 丁模 具 生产 。在汽 车 主机 厂 , 模 具企 业 应 该处 于 ,
必将 带 动汽 车模 具 市场 的持 续 、 稳 定 发展 。
模 具 行业 扩产 上量 告 一段 落 逐 步 向高端 方 向发 展
名企认定标准

一、符合下列条件之一者,认定为名企:
(1)近三年世界500强企业、中国国营(民营)500强企业、浙江省国营(民营)100强企业、浙江省高新技术企业、温州市100强企业。
(2)温州各行业协会副会长及以上单位企业。
(3)注册资金的分类认定:(限温州企业)
制造类企业(含机械设计与制造、模具设计与制造、数控技术、阀门设计与制造、汽摩零部件制造、电机与电器、机电一体化技术、电气自动化技术、家具设计与制造、计算机控制技术、汽车电子技术等专业),注册资金5000万及以上;
土建类企业(含建筑设计技术、建筑装饰工程技术、建筑工程技术、工程造价、环境艺术设计、房地产经营与估价等专业),旅游类企业(含旅游管理、酒店管理等专业),轻纺食品类企业(含服装设计、鞋类设计与工艺等专业),注册资金1000万及以上;
电子信息类企业(含计算机应用技术、信息系统运行与维护、计算机网络技术、计算机多媒体技术、计算机信息管理、软件开发与项目管理、电子信息工程技术等专业),注册资金500万及以上;
财经类企业(含电子商务、会计、金融与证券、国际商务、市场营销、工商企业管理等专业),文化教育类企业(含商务英语、文秘等专业),艺术设计传媒类企业(含传媒策划与管理艺术、服装表演等专业),注册资金100万及以上;(需提供营业执照复印件或网站)。
(4)资质认定:
温州市建筑类一级资质、装饰类乙级资质及以上企业,餐饮旅游业四星级及以上企业(需提供认定证书复印件或网站)。
二、其他温州知名企业,由学院协商认定。
三、应聘到政府机关、事业单位的,考录为村官、公务员、专升本的,自主创业的毕业生均纳入进名企比例的统计口径。
近三年全球汽车零部件配套供应商百强及其业务简介

和电力系统在内的发动机及其相关技术,并
提供相应的售后服务。)
奥托立夫(瑞典 公司主要产品为汽车电子
安全系统,座椅安全带系统以及电子控制单
20
元,汽车方向盘系统等。 奥托立夫中国目 前生产的产品涵盖了方向盘、座椅安全带系
日立汽车系统
本特勒
统、安全系统的电子控制系统等汽车安全方
面的产品,市场占有率持续保持领先地位
槛板,以钢材为原材料,并以其优良的品质
成为供应商的战略性伙伴。)
海拉(德国 产品关注于各种车身电子及其
电子部件,包括舒适控制元件(CCU)/车身控
33
制模块(BCM),遥控钥匙,无钥匙进入和一键 启动系统,记忆座椅模块(MSM),油门踏板传
感器(APS),中央锁定执行器,空调电子,真空
泵,机油传感器,驾驶辅助系统,照明电子等
天纳克(美国 天纳克在汽车悬挂系统和排
气系统及产品领域方面是全球领先的设计者
34 、制造商和销售商之一,为全球各地的整车
制造厂商以及汽车售后配件市场提供优质的
产品和服务。)
35 丰田合成(日本)
NSK(日本 NSK广泛提供高性能、优质且环
36
保的汽车相关产品。包括各种轴承及电动助 力转向装置(EPS)在内的NSK产品,作为“
捷太格特(日本 JTEKT是全世界无种类之分
21
的机床行业的机能零部件生产厂家;而且, 是所有种类的转向系统的供应商、是传动系
法雷奥
伟世通
列部品和轴承的供应商。)
伟世通(美国 自1993年开辟中国市场至
今,伟世通与中国各大汽车制造商进行了广
泛的合作,目前已迅速发展为伟世通亚太
22 (上海)有限公司及十几家大型合资企业
全球知名汽车零部件企业
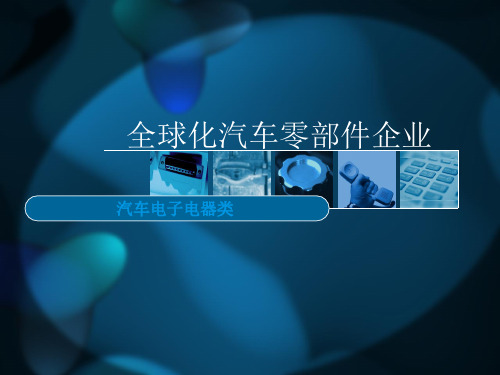
下属三个主要部门
• 汽车技术部:博世集团是世界第二大汽车装 备供应商。产品包括汽油系统、柴油系统、 底盘系统、能源及车身系统、汽车多媒体、 汽车电子、采埃孚转向机系统(和ZF公司合 资)和售后市场等八大部门 • 消费品与智能建筑技术部:博世在这个领域 的产品主要有电动工具,热动技术和家用电 器,还包括安防系统,宽带网络。 • 工业技术部:博世自动化技术部门与曼内斯 曼-力士乐股份公司的合并
德国大陆集团
• 德国大陆集团(Continental AG)始建于 1871年,总部位于德国汉诺威市,是世界第 三大轮胎制造企业(马牌轮胎),欧洲最大 的汽车配件供应商。德国大陆集团在全球 27 个国家拥有 100 多个工厂、研发机构和测试 中心,员工总数超过 80,000 。
在华业务
• 1996年进入中国,大陆集团与上汽集团开展 合作。在上海、长春、宁波、张家港等地建 立了10余家合资企业。大陆汽车系统还从其 合资公司上海联合投资有限公司和上海新泰 工业有限公司,收购了生产电子制动系统和 车身电子模块中使用的电子控制组件业务, 成立了全资控股的上海大陆汽车系统公司。 2004年,大陆汽车系统又在连云港设立了专 门生产汽车传感器的合资企业。
• 法雷奥官方网站网址: /
伟世通公司
• 总部位于美国密歇根州的伟世通在全球拥有 81,000名员工。伟世通公司为全球汽车生产 厂商设计和制造创新的空调系统,汽车内饰, 以及包括照明在内的电子系统,并提供多种 产品以满足汽车售后市场的需求。 • 汽车电子领域的主要产品包括音响、信息娱 乐、驾驶信息、动力总成控制和照明。目前, 伟世通在全球汽车电子供应商中处于领军地 位,全球电子产品部的成立将进一步加强伟 世通在汽车电子行业的优势。
在华业务
潍坊市汽车模具制造跃居国内前列

主体项 目,0万 吨高 架 棒材 工 程 已竣工 投 产 。该 工程 产 品 精度 高 , 9 质量 好 , 成 为凌 钢 扩 大 和 占领 市 场 、 将 实 ① 由 中冶 京 诚设 计 , 国二 十 冶施 工 。整 个 项 目仅 用 了 现 新 的效 益增 长 的主 导 产 品 。 中 10天 的时 间就 竣工 投 产 ,创 造 了全 国 同类 生产 线建 8
的 3 余名参展人员, 0 陆续从德国 法兰克福 20 欧洲 单位参展, 08 共租下 1 个标准摊位( 8 中国参展模具企业 { 髦 譬 1
模具技术和设备展览会上凯旋归来 , 各参展企业 与各 共 3 家 , 2 宁海县 占总参展家数 的 4%) 8 。 I 1 国客户达成意向模具报价 1 0 , 0余万 欧元 ,其 中宁海 0 受当前金融危机 的影 响 , 特别是全球汽车行业发 l
“ 面对危 积极 机, 应对” 演讲中, 的 详细分析了 模具行
』 J J 箍
宁海模具展团在欧模展达成意向报价千余万欧元
i】 菇f 盏
20 08年 1 月 35日, 2 ~ 浙江宁海县 1 家模具企业 塑、 4 跃飞模具 、 双林模具 、 大鹏模具 、 南杰模塑等 1 4家 l
此, 广东省模具 工业协会决定今后 每年召开一次类似 { { 苟
研讨会得到 了 省 规模 比较大 、 内容 比较丰富 的先进技术交流 I 代
会和专家们的大力支持。 中国模协副秘书长周永泰在 会, 为模具工业不断发展做出努力。
①
J各 s 3 - L j
汽车零部件模具的制造与设计
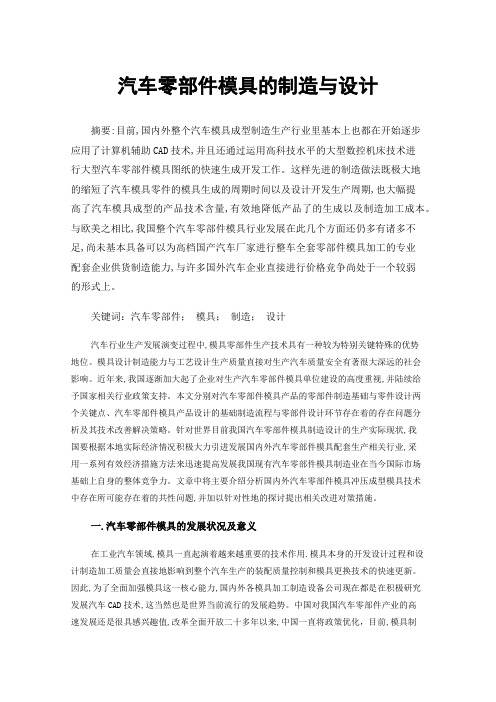
汽车零部件模具的制造与设计摘要:目前,国内外整个汽车模具成型制造生产行业里基本上也都在开始逐步应用了计算机辅助CAD技术,并且还通过运用高科技水平的大型数控机床技术进行大型汽车零部件模具图纸的快速生成开发工作。
这样先进的制造做法既极大地的缩短了汽车模具零件的模具生成的周期时间以及设计开发生产周期,也大幅提高了汽车模具成型的产品技术含量,有效地降低产品了的生成以及制造加工成本。
与欧美之相比,我国整个汽车零部件模具行业发展在此几个方面还仍多有诸多不足,尚未基本具备可以为高档国产汽车厂家进行整车全套零部件模具加工的专业配套企业供货制造能力,与许多国外汽车企业直接进行价格竞争尚处于一个较弱的形式上。
关键词:汽车零部件;模具;制造;设计汽车行业生产发展演变过程中,模具零部件生产技术具有一种较为特别关键特殊的优势地位。
模具设计制造能力与工艺设计生产质量直接对生产汽车质量安全有著很大深远的社会影响。
近年来,我国逐渐加大起了企业对生产汽车零部件模具单位建设的高度重视,并陆续给予国家相关行业政策支持。
本文分别对汽车零部件模具产品的零部件制造基础与零件设计两个关键点、汽车零部件模具产品设计的基础制造流程与零部件设计环节存在着的存在问题分析及其技术改善解决策略。
针对世界目前我国汽车零部件模具制造设计的生产实际现状,我国要根据本地实际经济情况积极大力引进发展国内外汽车零部件模具配套生产相关行业,采用一系列有效经济措施方法来迅速提高发展我国现有汽车零部件模具制造业在当今国际市场基础上自身的整体竞争力。
文章中将主要介绍分析国内外汽车零部件模具冲压成型模具技术中存在所可能存在着的共性问题,并加以针对性地的探讨提出相关改进对策措施。
一.汽车零部件模具的发展状况及意义在工业汽车领域,模具一直起演着越来越重要的技术作用.模具本身的开发设计过程和设计制造加工质量会直接地影响到整个汽车生产的装配质量控制和模具更换技术的快速更新。
因此,为了全面加强模具这一核心能力,国内外各模具加工制造设备公司现在都是在积极研究发展汽车CAD技术,这当然也是世界当前流行的发展趋势。
TD技术--汽车模具表面超硬改性技术
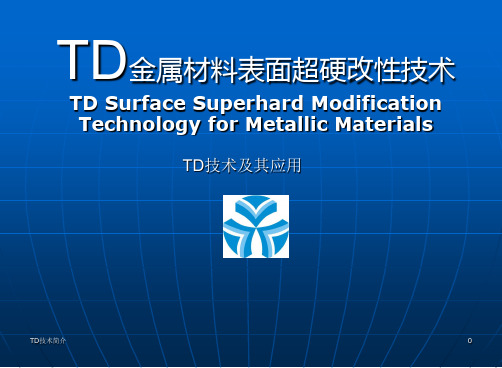
TD技术简介
22
二十二、本工艺与其他比较先进的强化 技术的主要参数和性能对比
强化方法 表面成分 TD VCV NbC QPQ(氮化) Fe2N-Fe3 渗硼(粉末) FeB Fe2B CVD TiN TiC PVD TiN TiC 硬质合金 钨、钴类
热处理方式
硬化层厚度/um
盐浴
6~15
气体 盐浴
国 产 日本 美国 进口 德国 英国 韩国
TD技术简介
CrWMn Cr12
Cr12MoV等
SKD-11 DC-53 DC-54 D2 D6 A2
X120Cr12 X165CrMoV12 BD2 BD2A
STD11
15
十六、选择TD的理由
(一)、成本理由
直接成本 工件的使用寿命大大提高,降低了制作费用 间接成本 经TD处理后的模具加工的产品废次品率大幅降低,且不用经常 拆装、维修模具,劳动效率大幅提高。 用作机械部件、标准件其使用寿命大幅延长,提高了设备的利用率。
(二)、专业领域的使用: 标准件、机械部件、石化、钢铁、机械、航 空航天、金属加工等行业对一些既要求高耐磨又要求高韧性的特殊零 部件。
(三)、部分领域取代硬质合金:
1、硬质合金韧性差; 2、硬质合金加工难度大、成本高、周期长。
TD技术简介
18
十八、TD在汽车车身及其底盘件的应用
横梁 天窗 车门 A、B柱 油底壳 底盘连接件 纵梁 翼子板 天窗 车身 侧门防撞梁 … …
国外工业发达国家的应用超过75% 国内应用不到百万分之一
TD技术简介
8
九、技术特点
1、模具表面硬度大大提高,全面解决冷作模具磨损、拉毛等面疲劳失
效现象。适合于汽车、钢管、机械、电子、金属加工、标准件等行业; 2、与基体冶金结合,表现出最优异的抗剥离性; 3、可重复处理; 4、不论工件形腔如何复杂,都能形成均匀的被覆层,且处理过程中相对 传统工艺模具变形较小; 5、光洁度度在Ra0.4以内与处理前无变化。
- 1、下载文档前请自行甄别文档内容的完整性,平台不提供额外的编辑、内容补充、找答案等附加服务。
- 2、"仅部分预览"的文档,不可在线预览部分如存在完整性等问题,可反馈申请退款(可完整预览的文档不适用该条件!)。
- 3、如文档侵犯您的权益,请联系客服反馈,我们会尽快为您处理(人工客服工作时间:9:00-18:30)。
FT 汽车模具制造技术一、FT 模具设计与制造部门概况FT 汽车公司中与冲压模具设计制造有关的部门主要有两个,其中负责模具设计的是第八生产技术部,负责模具制造的是 ST 部(ST 为冲模的英文缩写)。
它们都直属于总公司, 生产技术1-8部属于生产准备部门,冲模部( ST 部)属于工机制造部门。
1、 第8生产技术部其主要职责是模具设计和冲压设备准备, 加上它所属的计划、 生产准备、 部属等科室共 有将近 350 人。
其中与模具设计有关的技术室有三个,它们是由从事的产品制件的类型来划分的:部 门 职 责一室车身周边件模具设计(车门、机盖、后行李厢盖)二室 主车身件模具设计(侧围、翼子板、顶盖等)三室 底板、梁架件模具设计(地板、发动机舱等)每个室又分为冲压工艺与模具结构设计两个组。
专业化分工是 FT 模具设计部门工作的特点a . 模具设计内容细分FT 把模具设计分成三个工序:工序设计、模面设计和结构设计,分工明确,分别由专 门人员负责。
工序设计主要完成工序草图、 dl 图设计、 作详细的模具设计任务书、模面构想 等,模具设计的主要创造性劳动都在这一步靠人脑完成。
模面设计几乎是单纯的曲面造型, 结构设计的重点在于模具结构的具体实现。
b . 人员专业化分工细微各个室只负责一类产品件, 每个人在一定时间内负责同一个件, 甚至是同一类模具。
由 于 FT 每年开发的新车可达十种,这就是说,可能有的人在一年内画十套非常相似的前车门 外板拉延模,其专业化程度可想而知。
c. 模具的社会大分工日本的模具制造专业性分工很强, FT 虽然自己的模具制造能力很强,但它并不是什么 模具都干。
比如,整车所有件的冲压工艺和模具的整车协调,都由他自己负责,但模具设计和制造他只干车身内外覆盖件,地板和梁架件全部到定点厂家外协。
不但FT 如此,国外的大汽车公司所属模具厂无不如此,比如日本大发公司模具厂,甚至只做侧围、翼子板、 顶盖 等有限的几种外覆盖件。
这可以看作是一种发展趋势,在韩国、台湾甚至是专业模具厂家也 是向只做几种件的更人员约 70 人 约 75 人 约 30 人专业方向发展。
2、模具制造部(ST部)FTST部负责模具制造和新车整车模具的协调,并一直到大批量生产之前的冲压生产准备。
ST部构成:科室责任人员技术至生产技术开发、生产计划生产准备、设备计划89人NC课NC编程、检杳175人实型课验具、实型制造142人机械课机械加工173人钳工课钳工、装配237人调试课试模、调试204人总共:1020人主要数控加工设备:构造面加工数控铳床39台型面加工高速、五轴五面铳15台新型一体化加工设备6台其他小件加工设备31台3、FT的模具设计和制造能力模具设计与制造能力:每年大约可开发10个轿车整车模具;模具产量(标准套)约2000套/年;内制率60% (外协40%);主要产品中:模具占80% ;验具占7% ;其他占13% ;全年完成模具制造成本预算近200亿日元。
人均模具产量2标准套/人。
年模具制造成本(不含设计)约600万日元/套工时成本(平均)约1万日元/小时整车模具设计制造周期12个月(由车身设计完成至新车批量生产)其中包括整车全部模具设计周期5个月制造周期5个月调试周期6个月由此可见,FT —年的轿车生产能力大约500万辆(日本国内部分约占50%),是中国大陆轿车产量的十倍,而模具设计制造能力也超过我们全国汽车模具生产能力的数倍。
FT的整车模具制造周期,远远短于我们的一般单套模具制造周期,它的标准单套模具制造周期为三至四个月,在我们看来还是一个梦想。
我们的模具质量水平与FT相比相差更远。
3、FT 一般模具制造周期FT把模具的制造计划形成了标准化,根据模具的复杂程度可分为短周期、标准周期和长周期三种。
现以单套模具的设计制造周期(拉延模,标准周期)为例:冲压工艺20天模具设计20天模面设计8天NC编程15天实型制作7天铸造12天机加工9天钳工装配7天单套拉延模总周期62天,其中制造周期52天以上周期包括模具的设计、制造直至模具初次试模完成为止。
如果再考虑产品件各序模具的总周期,单个制件各序模具的总周期,要在拉延模的基础上再加22天(包括模具调试, 但不包括整车调试),总共84天。
以上天数均为工作日(节假日除外),换算为日历日大约为20天等于一个月,也就是单套模具制造周期三至四个月。
FT的模具制造也是按照准时化生产方式进行的,全部倒排计划,计划到每一个工作日,不提前投产,避免增加在产模具。
我们的倒排计划往往是为赶工期,人为的压缩工期。
而FT的倒排计划,是为了在必要的时候生产出必要的产品,避免提前投产造成生产过剩的浪费。
FT模具制造技术近十年来本人曾在日本多家模具制造厂进行过较为深入的学习和考察,先后累计时间达6个多月。
对比以后发现,FT的模具技术在日本的模具厂家中也是十分突出的,无论是能力、效率及技术都不愧为世界一流水平。
通过对FT的了解我们可以看到,世界汽车模具制造技术正在向这些方向发展:计算机前的操作逐步代替现场操作,以高精度加工代替人的手工劳动,模具的设计、制造高度标准化,单件生产方式向流水线式生产方式发展等等。
结合我们国内的模具制造情况,FT在以下一些地方与我们有很大的不同,值得我们很好的借鉴。
1、冲压工艺设计a、精细模面设计我们常说的模具设计实际上分为三个部分:冲压工艺设计、模面设计和结构设计。
这三种设计的内容和侧重点是完全不同的,FT的工作流程为先有冲压工艺设计然后指导模面设计和模具结构设计,分别由不同的人来做,专业分工很明确。
传统的冲压工艺设计采用工序图或是DL图,它的模面设计是非常粗略的,以这样的图纸指导下的工艺造型,必须在后序靠人工修整、制造工艺祢补,造成模具制造的人工钳修量很大、周期延长。
FT在设计阶段通过计算机的曲面造型,完成模面的精细设计。
比如:针对进料量不同设计各种拉延筋,同一套模不同部位的拉延筋截面不同,防回弹、过拉延处理,最小压料面设计,凸凹模不等间隙设计等等。
精细模面设计的结果,可以极大的减少型面加工,减少钳修,减少试模工时,它的作用非同小可。
对比之下,国内的模具设计还停留在结构设计阶段,模面设计没有受到很好的重视,模面实际上是靠后天完成,模具设计的落后造成了制造的落后,也就毫不奇怪了。
b、板料成型分析技术应用情况FT公司从5-6年前,开始应用有限元法做计算机模拟板料成型分析,主要应用的解算软件为美国的dyna3d,他们经过了近三年的努力才达到实用水平。
目前,FT建立了一个整车身各种典型件的分析结果库。
对一个新车型的件,如果成型性没有太大的变化,只是参考原工艺不做分析,只有特殊的新造型才做板料成型分析。
FT的新车要做样车,对造型特殊的件除了做板料成型分析外一般还要做简易模进行验证。
因此,FT人认为目前板料成型分析还不是一件必需的、简单的事,无论是周期还是成本都有很大代价。
本人认为,FT的车型开发量很大,车型之间变化不大、类似件很多,又积累了丰富的人的经验,板料成型分析确实用武之地不多,建立一个分析结果库是一个好方法(日本富士模具公司也是这么做的)。
反观国内现状,一方面模具厂专业分工很低,各种件都会遇到,难有现成经验,似乎更需要板料成型技术。
另一方面,技术水平低支持环境差(如:板料参数、摩擦系数等难掌握),模具厂应用起来,要达到实用(不讲效果、不计代价的研究不算)也是非常困难的。
即使是成立专业分析公司,考虑用户数量、周期、价格等因素,恐怕也难成立。
目前,这项技术在国内的实际应用效果还难有定论。
c、模面设计经验积累机制FT的设计部门除手工勾画草图以外,设计已全部计算机化,一般设计人员除一台工作站外还有一台笔记本电脑。
但,真正创造性的设计还是靠人脑,特别是靠人的经验积累。
FT特别强调经验积累机制:只有集体的经验不能有只属于个人的经验,比如:资料的统一管理,草图设计的小组讨论,图纸的多部门集体审核,设计标准、规范的经常性增改等等。
经验积累机制是FT能够不断提高模面精细设计的主要手段。
比如:模具加工完成之后,一般模具型面不用研合,刃口不必对间隙,钳工只负责安装,在初次试模时也不能随便修调模具,调试模具有模面设计人员在场,初次试模缺陷需要记录下来。
最后的休整结果,像拉延筋、拉延圆角变动、对称件的不对称现象等,还要进行现场测量。
这些资料的积累、整理、分析、存档,都是模面设计的经验积累,并随时加入到下一次的设计中去。
FT的模具设计和调试过程,真正做到了是一个闭环制造系统, 借助于这种自我完善的经验积累机制, 模具的设计越来越精细,越来越准确。
d 、间隙图设计在FT ,模面设计实际上是由曲面造型和 NC 编程两部分共同完成的,为了传达和描述模面设计思想,就产生了除DL 图、模具图之外的第三种图---间隙图也叫质量保证图。
间隙图本人在以前还没有见识过,这可能是 FT 的一种创造。
模具的设计不是单纯为了设计出一种机器,能够完成它一定的动作就完了(这只能叫作结构设计) ,模具设计的最终目的是为了保证它所压出的产品件是合格的高质量的,间隙图就是这样一种专为保证产品件质量的图。
质量保证图中,主要包括这样几项内容:模具实际符型面区域、 各个符型区域的间隙值、工艺要求的模面变化情况、拉延圆角的变化、各种模面的挖空等等。
凡是无法通过曲面造型实现的模面设计,都通过间隙图的传达,依靠 NC 编程的设计来实现,在这里 NC编程也不再是单纯的实现模具结构的加工, 它实际上也参与到模面设计中来了。
因此,间隙图的应用也是精细模面设计的一种必然。
e 、大规模生产对模具的影响FT 的生产规模是世界一流的,它在模具设计如何适应大规模生产的要求方面具有丰富 的经验。
提高材料利用率:对于大批量汽车生产来说,提高板料的利用率是模具设计的第一大事。
只要把材料利用率提高几个百分点,模具的成本就可乎略不计了。
如果一套模具40万人民币,只相当于100吨钢板的价格,以寿命 50万件计算,平均每件节约 0.2Kg 钢板,就足可节约 出这套模具费用了。
减少冲压工序:模具设计的趋势是, 零件的合并,左右对称件合模,前后顺序件合模等 等,原来几个件合成一个件,不同的件合在一套模,模具越来越大,单件工序大大减少,整 车模具数量越来越少,这对降低冲压的成本起关键作用。
例如:FT 把整车制件的模具系数,由过去的3点几降到2左右。
冲压自动化:为适应冲压线完全自动化, 模具必须考虑机械手上下料, 废料的自动排出, 气动、自动和传感装置普遍采用等等。
模具的快速装换:冲压线的换模时间,也成为一个模具设计必须考虑的问题。
模完全以单动代替双动,模具自动卡紧,换模不换气顶杆等等。
2、模具结构的设计和加工设计有两种目的:一个是面向设计本身, 一个是面向制造。