QSB快速反应
QSB+快速反应流程
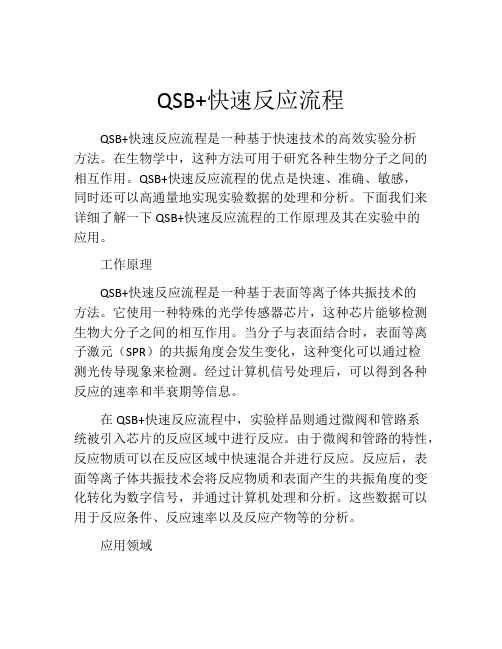
QSB+快速反应流程QSB+快速反应流程是一种基于快速技术的高效实验分析方法。
在生物学中,这种方法可用于研究各种生物分子之间的相互作用。
QSB+快速反应流程的优点是快速、准确、敏感,同时还可以高通量地实现实验数据的处理和分析。
下面我们来详细了解一下QSB+快速反应流程的工作原理及其在实验中的应用。
工作原理QSB+快速反应流程是一种基于表面等离子体共振技术的方法。
它使用一种特殊的光学传感器芯片,这种芯片能够检测生物大分子之间的相互作用。
当分子与表面结合时,表面等离子激元(SPR)的共振角度会发生变化,这种变化可以通过检测光传导现象来检测。
经过计算机信号处理后,可以得到各种反应的速率和半衰期等信息。
在QSB+快速反应流程中,实验样品则通过微阀和管路系统被引入芯片的反应区域中进行反应。
由于微阀和管路的特性,反应物质可以在反应区域中快速混合并进行反应。
反应后,表面等离子体共振技术会将反应物质和表面产生的共振角度的变化转化为数字信号,并通过计算机处理和分析。
这些数据可以用于反应条件、反应速率以及反应产物等的分析。
应用领域QSB+快速反应流程在生物学研究中发挥着重要的作用。
它不仅可以用于研究蛋白质和核酸之间的相互作用,也可以研究生物膜、细胞和受体之间的交互作用等。
具体应用领域包括:蛋白质-蛋白质相互作用研究。
QSB+快速反应流程可以用于研究蛋白质间的相互作用,包括蛋白质复合物的结构和稳定性以及相互作用动力学等。
蛋白质-核酸反应研究。
QSB+快速反应流程可以用于研究蛋白质和核酸之间的相互作用,包括RNA合成和修复等。
受体激活研究。
QSB+快速反应流程可以用于研究受体激活过程中,受体和配体之间的相互作用,以及反应动力学及其与下游信号转导通路之间的关系。
分子诊断和药物筛选。
QSB+快速反应流程可以用于鉴定和筛选与慢性疾病相关的受体,以及对这些受体进行高通量的药物筛选。
总结QSB+快速反应流程是一种基于表面等离子体共振技术的高效实验分析方法。
1编号 Q-1 QSB Plus(通用)质量系统基础
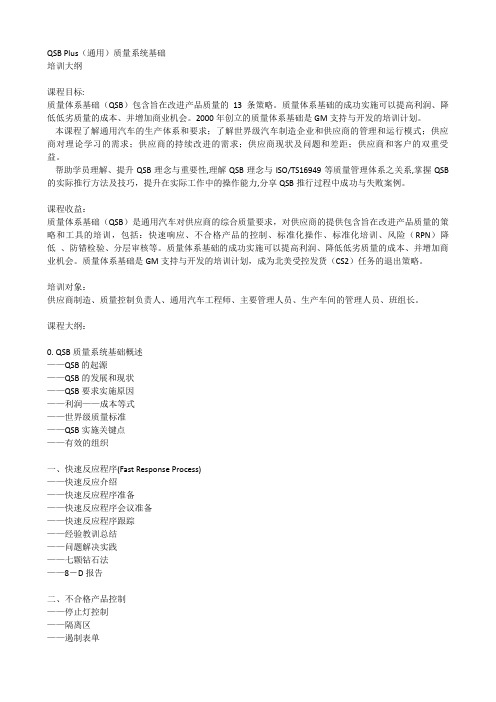
QSB Plus(通用)质量系统基础培训大纲课程目标:质量体系基础(QSB)包含旨在改进产品质量的13条策略。
质量体系基础的成功实施可以提高利润、降低低劣质量的成本、并增加商业机会。
2000年创立的质量体系基础是GM支持与开发的培训计划。
本课程了解通用汽车的生产体系和要求;了解世界级汽车制造企业和供应商的管理和运行模式;供应商对理论学习的需求;供应商的持续改进的需求;供应商现状及问题和差距;供应商和客户的双重受益。
帮助学员理解、提升QSB理念与重要性,理解QSB理念与ISO/TS16949等质量管理体系之关系,掌握QSB 的实际推行方法及技巧,提升在实际工作中的操作能力,分享QSB推行过程中成功与失败案例。
课程收益:质量体系基础(QSB)是通用汽车对供应商的综合质量要求,对供应商的提供包含旨在改进产品质量的策略和工具的培训,包括:快速响应、不合格产品的控制、标准化操作、标准化培训、风险(RPN)降低、防错检验、分层审核等。
质量体系基础的成功实施可以提高利润、降低低劣质量的成本、并增加商业机会。
质量体系基础是GM支持与开发的培训计划,成为北美受控发货(CS2)任务的退出策略。
培训对象:供应商制造、质量控制负责人、通用汽车工程师、主要管理人员、生产车间的管理人员、班组长。
课程大纲:0. QSB质量系统基础概述——QSB 的起源——QSB的发展和现状——QSB要求实施原因——利润——成本等式——世界级质量标准——QSB实施关键点——有效的组织一、快速反应程序(Fast Response Process)——快速反应介绍——快速反应程序准备——快速反应程序会议准备——快速反应程序跟踪——经验教训总结——问题解决实践——七颗钻石法——8-D报告二、不合格产品控制——停止灯控制——隔离区——遏制表单三、验证岗位+防错验证——为什么需要验证岗位?——哪些区域应该设立验证岗位?——如何设立验证岗位?——验证岗位工作内容——为什么要防错验证——防错验证定义——防错验证的要求——防错验证流程——防错验证检查表——防错验证结果四、标准化操作——现场管理三大敌人——超负荷、不均衡、7大浪费——工作区域标准化-七种浪费——5S现场管理——标准化作业指导书——标准化操作的实施——标准化作业要素点——标准化操作文件结构图——工作要素表——标准化操作优点——操作员作业指导书——标准化表单——标准化操作列表五、培训——标准化的操作员培训的重要性——操作工培训四步法——培训记录——培训要求——培训灵活单六、过程分层审核——为什么做分层审核——分层审核定义——分层审核的要求——分层审核检查清单——分层审核的频率——分层审核结构——分层审核的整改七、风险降低——为什么实施风险降低——降低质量风险定义——主动降低风险要求——PRN降低跟踪表——被动风险降低——最大失效清单——实效模式分析 (FMEA)——风险(RPN)降低跟踪——现场风险管理八、异物控制——异物控制的目的——异物的定义——异物控制的要求——异物控制小组重点关注方面九、供应链管理——供应链管理目的——供应链管理要求——供应链质量期望十、变更管理——变更的目的——变更的范围——变更的职责——变更的流程——变更状态跟踪——工程变更请求表——试生产流程——临时替代流程十一、设备维护:从被动走向主动——管理对象与范围——基本定义:预防性/预测性维护、监控维护、故障性维护、维护计划、——维护管理核心流程——备品备件管理——客户工装管理——L1级(使用者)维护管理——维护标准化作业指导书及培训——维护成本管理——逐级上报与快速反应——经验总结——维护管理KPI简介:OEE、TEEP、MTBF、MTTR、纠正/预防维护比率、故障率、备件平均库存周转率、维护计划达成率等十二、生产和物料流管理:确保正确时间与地点使用正确数量的材料——管理对象与范围——基本定义:销售运营计划、主生产计划、生产排程计划、采购计划、工装增补计划等——制造管理核心流程与范围、要点:全部客户要求、长期战略与规划、销售运营计划、销售预测、订单接收与评审、主生产计划等等——内部材料流管理流程与范围、要点——瓶颈/制约因素管理五步法——安全库存管理——包装管理——搬运管理——贮存与库存管理——周转箱(满箱、空箱、零头箱)管理——特殊材料管理——逐级上报与快速反应——经验总结——制造与材料流管理KPI简介:生产计划达成率、库存周转率、周转箱周转率、库存差异率、库存成本率等、OEE、调机/开机时间比率十三、外部物流:零件标签正确吗?——管理对象与范围——基本定义:——收料管理核心流程与要点——发运管理核心流程与要点——采购计划——物流协议——关键供方定义域其物流管理——逐级上报与快速反应——经验总结——外部物流管理KPI简介:超额运费、物流货车满载率、交付符合率、交付准时率、超额运费/运输成本比率。
QSB快速反应
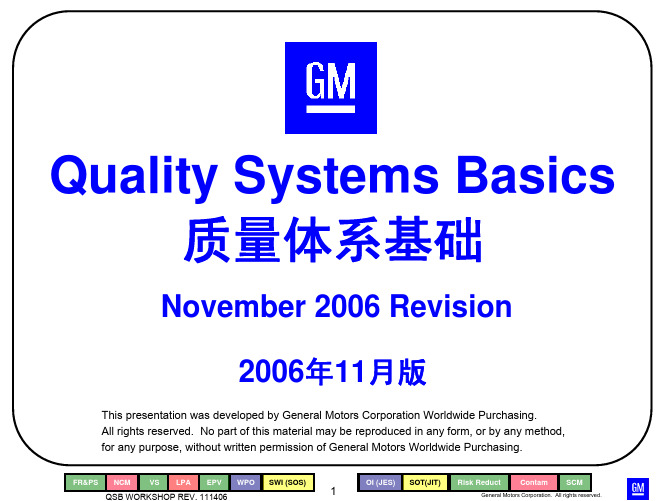
(例)
遏制问题
D4
识别根本原因
D5
实施长期措施
D6
验证措施的有效性
D7
在整个组织内进行教育 和形成制度
D8
总结表扬& 正式解 散团队
FR&PS
NCM
VS
LPA
EPV
WPO
SWI (SOS)
QSB WORKSHOP REV. 111406
15
OI (JES)
SOT(JIT)
Risk Reduct
Contam
Contam
SCM
General Motors Corporation. All rights reserved.
快速反应跟踪板
为优化目视管理,将这个表格尽可能大的显示在会议室 ( 如: 4’ x 8’ 可擦写的白板 ) 推出标准
(例)
PFMEA / 控制计划更新 标准化作业指导书/ 操作员指导书
Risk Reduct
Contam
SCM
General Motors Corporation. All rights reserved.
问题解决的基本原则
• 抛开先入为主的想法。 • 避免对没有数据支持的问题做出反应。 • 将问题分解。 • 直接观察问题的发生现象并发现原因,而不是通过二手信息。 • 在彻底弄清楚究竟发生了什么问题之前,不要进行问题分析。 • 标准是什么?与应该发生情况相比实际到底发生了什么? • 建立原因/结果间的关系。 • 不停地问“为什么?”直到你通过根本原因分析可以预防问题的再次发生 时。
FR&PS
NCM
VS
LPA
EPV
WPO
SWI (SOS)
QSB快速反应流程

QSB快速反应流程快速反应流程(QSB,Quick Service Bulletin)是一种用于迅速处理问题和将解决方案迅速传达给相关人员的流程。
它旨在确保问题能够得到及时解决,以最小程度地对组织的正常运营造成干扰。
以下是一个包含超过1200字的QSB的标准流程:第一步:问题识别(Identification)快速反应流程的第一步是识别问题。
这可以通过多种方式进行,例如通过客户反馈、内部质量监控和检查、日常操作的异常情况等等。
一旦问题被发现,相关人员应该立即报告给负责的团队或部门。
第二步:问题分析(Analysis)第三步:解决方案开发(Solution Development)一旦问题的根本原因得到确认,团队需要制定相应的解决方案。
这通常涉及到制定一系列具体的步骤和行动计划,以修复问题并防止类似问题的再次发生。
解决方案应该是可操作和具体的,以便相关人员能够迅速理解并采取相应行动。
第四步:解决方案验证(Solution Validation)在制定解决方案之后,团队需要进行验证,以确保问题解决方案的有效性。
这可能包括验证方案的实施、测试解决方案的可行性,并确保它真正解决了问题。
如果验证过程中发现问题或需要进行进一步的调整,团队将返回前面的步骤进行修正。
第五步:解决方案发布(Solution Release)在解决方案被验证通过之后,团队需要将其传达给相关人员。
这可能包含编制发布公告、更新相关文件或培训相关人员。
目标是确保解决方案被传达给那些需要知道并实施它的人员。
第六步:问题解决(Problem Resolution)解决方案发布之后,团队需要跟踪问题是否得到解决。
这可以通过定期的监控和检查来实现。
如果发现问题仍未解决或出现新的问题,团队需要立即采取行动进行纠正。
第七步:总结和反馈(Summary and Feedback)在问题解决之后,团队应该进行总结和反馈。
这包括评估问题解决的效果、提取教训和经验,并在需要的情况下更新标准操作程序和其他相关文件。
QSB+快速反应流程

1.目标为了立即对内/外部用户埋怨进行处理,立即对内部质量缺点进行处理及总结经验,提升企业生产效率并最终达成提升企业有效产出之目标。
2.范围本程序适适用于企业生产运作过程中全部表露出内/外部问题。
3.术语和定义3.1快速反应会议是一个靠近生产现场、基于数据和目视化看板沟通会议。
以生产计划(昨/今日)为关注节点,由生产部主管或更高等级管理人员进行主导、各部门主管及关键工程师参与会议。
会议全程站立进行、保持在30分钟内。
3.2是以生产计划为根本并以提升组织有效产出为目标会议。
3.3对过去二十四小时内发生重大质量问题或事件进行检验,定义中长久问题和短期问题、应依据快速反应短期、中长久看板登入标准进行目视化管理。
3.4目标是提升信息共享、快速沟通决议并加以跟踪,从而提升团体沟通有效性。
该会议有效召开是基于问题有效处理和经验总结应用(横向展开等)避免后期问题反复发生。
3.5对分层审核、岗位验证发生重大事件必需在会议上进行评审和跟踪。
3.6要求处理质量问题和时间责任人、完成时间、汇报日期、跟踪方法等,建立快速反应系统。
3.7对分层审核、岗位验证发生重大事件必需在会议上进行评审和跟踪。
3.8要求处理质量问题和事件责任人、完成时间、回报日期、跟踪方法等,完善快速反应系统。
4.职责和要求4.1质量部负责快速反应步骤开发、培训、维护、问题处理之验证等。
4.2企业级快速反应会议主持人通常由生产部部长或质量部部长担任,负责组织每日质量例会;必需时可做合适调整。
4.3和会人员需按时参与、不得迟到、早退、缺席;由会议主持人于会议上明确指定问题处理责任人、相关部门作为小组组员为其提供团体支持。
4.4参会部门及参会人员详见《快反会议参会人员名单》,快反会议要求应由各部门部长亲自参与。
如遇出差或其它客观原因不能按时出席时,应立即向会议主持者请假并委派其它人员替换参与,参会人员需每日会前五分钟进行《快反会议签到表》登记。
由主持人负责统计出勤情况,每个月统计汇总快反会议出勤情况,上报综合管理部。
QSB Audit 翻译版
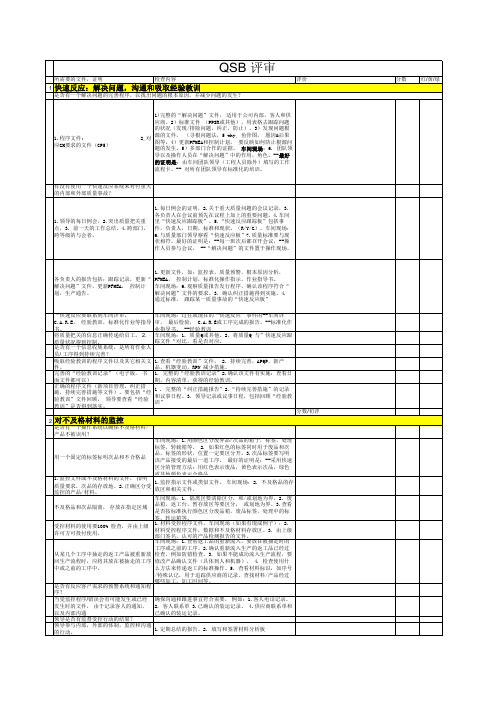
流程卡。-- 对所有团队领导有标准化的培训。
有没有使用一个快速反应系统来对付重大 的内部和外部质量事故?
1.领导的每日例会,2.突出质量把关重 点,3. 前一天的工作总结。4.跨部门, 跨等级的与会者。
1.每日例会的证明,2.关于重大质量问题的会议记录,3. 各负责人在会议前预先在议程上加上的重要问题。4.车间 里“快速反应跟踪板”。5.“快速反应跟踪板”包括事 件,负责人,日期,标准和现状。(R/Y/G)。车间现场: 6.与质量部门领导察看“快速反应板”7.质量标准要与现 状相符。最好的证明是:--每一班次后都召开会议,--操 作人员参与会议, --“解决问题”的文件置于操作现场。
的状况(发现/排除问题,纠正,防止)。3)发现问题根
2,对
源的文件, (寻根问题法,5 why, 鱼骨图, 愿因&后果 图等。4)更新PFMEA和控制计划, 要反映如何防止根源问
题的发生。5)多部门合作的证据。 车间现场:6. 团队领
导以及操作人员在“解决问题”中的作用,角色。--最好
的证明是:由车间团队领导(工程人员除外)填写的工作
通过标准, 跟踪某一质量事故的“快速反应板”
“快速反应要联系到车间评审,
车间现场:过往或现在的“快速反应”事件的--车间评
C.A.R.E, 经验教训,标准化作业等指导 审, 最后检验, C.A.R.E或工序完成的报告。--标准化作
书。
业指导书。 --经验教训
将质量把关的信息正确传递给员工。 2. 车间现场:1. 质量Q或其他。2. 将质量Q 与”快速反应跟
记录新增员工在就近3个月所接受的培训 的培训记录。 记录管理的结果和信息传递的系统 针对经验教训系统的其他分层工序评审
新增员工培训的文件,计划,跟踪表等
001通用汽车QSB分层审核检查表
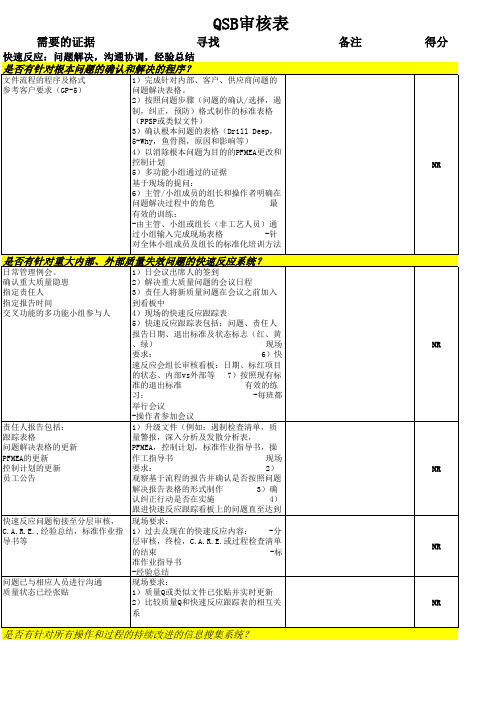
得分
寻找
备注
QSB审核表
需要的证据
户电话日志
2)客户联系清单
3)审核过的装运日志
4)分层的供应商联系方式和审核过的装运文件
套程序和专用表格用以告知客户并进行跟进方面的联系
工位组织
是否有利用和维护工作点组织的系统化的方法?
骤(什么)、关键工序(如何)及原因(为什么),并持续跟进。
3)询问小组成员如何制作高质量的部件。
4)质量检查
流程
1)操作者指导书必须在其工作区域内
是否有针对供应商的系统化的管理体系?
未审核仅存在于以下情况:
1)处于策略性考虑未立即专注---在备注栏中填上日后审核的日期2)计划于日后进行审核---在备注栏中填上日后审核的日期3)问题或策略并不适用于供应商---在备注栏中进行解释
4NR
已执行,未跟进:需要有相应的纠正行动
黄色:部分已执行绿色:完全符合要求NR:还未经过审核
2301评分标准
未执行:需要有相应的纠正行动书面的执行计划:需要有相应的纠正行动
分级。
QSB快速响应制度
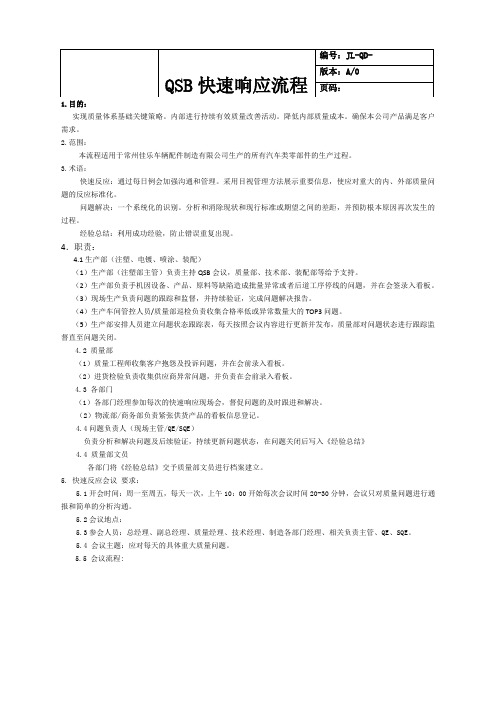
1.目的:实现质量体系基础关键策略。
内部进行持续有效质量改善活动。
降低内部质量成本。
确保本公司产品满足客户需求。
2.范围:本流程适用于常州佳乐车辆配件制造有限公司生产的所有汽车类零部件的生产过程。
3.术语:快速反应:通过每日例会加强沟通和管理。
采用目视管理方法展示重要信息,使应对重大的内、外部质量问题的反应标准化。
问题解决:一个系统化的识别。
分析和消除现状和现行标准或期望之间的差距,并预防根本原因再次发生的过程。
经验总结:利用成功经验,防止错误重复出现。
4.职责:4.1生产部(注塑、电镀、喷涂、装配)(1)生产部(注塑部主管)负责主持QSB会议,质量部、技术部、装配部等给予支持。
(2)生产部负责手机因设备、产品、原料等缺陷造成批量异常或者后道工序停线的问题,并在会签录入看板。
(3)现场生产负责问题的跟踪和监督,并持续验证,完成问题解决报告。
(4)生产车间管控人员/质量部巡检负责收集合格率低或异常数量大的TOP3问题。
(5)生产部安排人员建立问题状态跟踪表,每天按照会议内容进行更新并发布,质量部对问题状态进行跟踪监督直至问题关闭。
4.2 质量部(1)质量工程师收集客户抱怨及投诉问题,并在会前录入看板。
(2)进货检验负责收集供应商异常问题,并负责在会前录入看板。
4.3 各部门(1)各部门经理参加每次的快速响应现场会,督促问题的及时跟进和解决。
(2)物流部/商务部负责紧张供货产品的看板信息登记。
4.4问题负责人(现场主管/QE/SQE)负责分析和解决问题及后续验证,持续更新问题状态,在问题关闭后写入《经验总结》4.4 质量部文员各部门将《经验总结》交予质量部文员进行档案建立。
5. 快速反应会议要求:5.1开会时间:周一至周五,每天一次,上午10:00开始每次会议时间20-30分钟,会议只对质量问题进行通报和简单的分析沟通。
5.2会议地点:5.3参会人员:总经理、副总经理、质量经理、技术经理、制造各部门经理、相关负责主管、QE、SQE。
- 1、下载文档前请自行甄别文档内容的完整性,平台不提供额外的编辑、内容补充、找答案等附加服务。
- 2、"仅部分预览"的文档,不可在线预览部分如存在完整性等问题,可反馈申请退款(可完整预览的文档不适用该条件!)。
- 3、如文档侵犯您的权益,请联系客服反馈,我们会尽快为您处理(人工客服工作时间:9:00-18:30)。
负责人 负责人
五、效果验证
效果验证(连续无重复问题件数/天数/或其它) --- 工厂内部
状态说明 效果验证(连续无重复问题件数/天
六、标准化
6.1 工位 6.2 产品 6.3 员工 6.4 预维 6.5 现场 6.6 FMEA 6.7 控制 6.8 过程
七、问题关闭
问题解决效果是否满意?
是,问题关闭ຫໍສະໝຸດ Y N Y N Y N Y N Y N Y N Y N Y N
否,转到
如 果 如 果 如 果 如 果 如 果 如 果 如 果 如 果
阶段
区域制造工程科经理确认:
区域技术质量厂领导确认:
八、横向展开
这个问题解决的过程和结果能否帮助产品预防类似问题的再次发生?
Yes □(填写“横向展开记录表”) 横向展开记录表
2/4 -实施 3/4 - 反馈断点
连续无重复问题件数/天数/或其它) ---- 客户反馈
阶段
质量部QE确认:
“横向展开记录表”) NO □
改进措施
负责人 完成时间 状态
入经验教训库。
3.3 根本原因分析: 3×5Why在第一行写下鱼刺图分析出的最有可能的原因(策划、探测、制造三个方面) Why?
Why?
Why?
Why?
根本 原因:
Why?
Why?
Why?
Why?
Why?
根本 原因:
Why?
Why?
Why?
Why?
Why?
Why?
根本 原因:
四、措施制定及实施
短期措施(不适用则用“N/A”表示) 长期措施
序号
有类似特性的 产品型号
零件 号/名
称
横向展开 检查点
检查结果
改进措施
备注:如果需要,可以增加附件来诠释问题解决得过程。全部完成后,问题负责人负责录入经验教训库。 编制 日
制造三个方面)
负责人
计划 完成时间
实际 完成时间
状态 断点信息
负责人
计划 完成时间
实际 完成时间
状态 断点信息
状态说明
1/4- 制定 4/4 - 关闭