选择性激光熔化
激光选区熔化成形技术的发展现状及研究进展
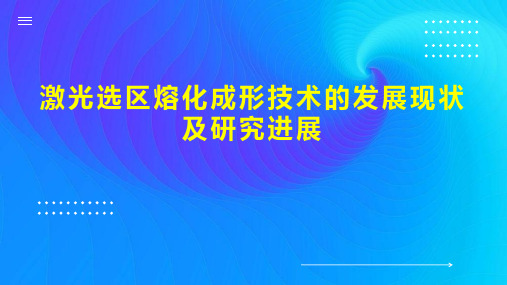
一、激光选区熔化成形技术简介
激光选区熔化成形技术是一种将粉末材料逐层堆积成形的工艺方法。在加工 过程中,高能量密度的激光束对金属粉末进行扫描和熔化,并在短时间内快速冷 却凝固,逐层堆积成复杂的三维零件。该技术具有高精度、高速度和高效率等特 点,被广泛应用于航空航天、汽车、医疗等领域。
二、发展现状
3、铝合金选区激光熔化成形的 力学性能与显微组织
选区激光熔化成形的铝合金材料具有较高的强度和硬度,同时具有良好的耐 磨性和耐腐蚀性。研究者们通过研究不同工艺参数对铝合金显微组织和力学性能 的影响,揭示了显微组织和力学性能之间的内在。例如,通过优化工艺参数,可 以得到细小的晶粒和均匀的相分布,从而提高材料的力学性能。
1、铝合金粉末制备与特性
选区激光熔化成形铝合金的关键之一是制备高质量的铝合金粉末。目前,铝 合金粉末的制备方法主要包括雾化法、机械合金化法、化学法等。其中,雾化法 作为一种常用的制备方法,得到的粉末具有球形度高、粒径分布窄、成分均匀等 优点。然而,雾化法也存在一定的局限性,如设备成本高、生产效率低等。因此, 研究不同制备方法对铝合金粉末特性的影响,有助于优化选区激光熔化成形的材 料体系。
激光选区熔化成形技术的发展现状 及研究进展
目录
01 一、激光选区熔化成 形技术简介
02 二、发展现状
03 三、研究进展
04 四、结论
05 参考内容
激光选区熔化成形技术(Selective Laser Melting,SLM)是一种重要的 金属加工和增材制造技术。自20世纪90年代初问世以来,该技术在全球范围内得 到了广泛和研究。本次演示将介绍激光选区熔化成形技术的发展现状及研究进展。
参考内容
随着制造业的快速发展,选区激光熔化成形(Selective Laser Melting, SLM)技术作为一种先进的金属成形方法,在近年来得到了广泛和应用。该技术 主要利用高能量激光束对金属粉末进行逐层选择性熔化,实现复杂形状零件的近 净成形。铝合金作为一种轻质、高强、耐腐蚀的材料,在航空、航天、汽车等领 域具有广泛的应用前景。本次演示将综述近年来选区激光熔化成形铝合金材料体 系的研究进展,主要包括以下几个方面:
激光选区熔化成形技术

激光选区熔化成形技术
激光选区熔化成形技术是一种先进的制造工艺,用于在金属材料上进行高精度、高效率且具有可重复性的加工过程。
它的基本原理是利用激光束的高能量密度,将金属材料局部加热溶化,然后控制激光束的路径和强度,使其在特定区域内凝固成所需的形状。
激光选区熔化成形技术具有以下特点:
1. 高精度。
能够实现微米级别的加工精度,精度高于传统的机械加工方式。
2. 高效率。
激光选区熔化成形技术的工作速度快,加工效率高,节约时间和成本。
3. 可重复性。
该技术能够实现高度可控制的加工条件,从而具有高度的可重复性。
4. 适用性广。
适用于各种金属材料的加工,包括铁、钢、铜、铝、镁等。
5. 绿色环保。
激光选区熔化成形技术无污染、无废料的工艺过程,不会对环境造成污染。
目前,激光选区熔化成形技术已广泛应用于汽车制造、航空航天、电子设备、医
疗器械等领域,以及各种创新工艺的实现。
选区激光熔化技术

选区激光熔化技术选区激光熔化技术是一种高端的制造工艺,它利用激光束对金属进行加热,使其熔化并在凝固时形成精密的结构。
这种技术在航空航天、汽车、医疗设备等领域得到广泛应用,因为它可以生产高质量、高精度的零部件。
在本文中,我们将介绍选区激光熔化技术的基本原理、应用、优点和限制。
一、选区激光熔化技术的基本原理选区激光熔化技术是一种非接触式的生产工艺,它利用激光束对金属进行加热,使其熔化。
激光束的能量密度非常高,可以使金属迅速升温至其熔点以上。
在激光束的作用下,金属表面的温度会迅速升高,直到熔化。
一旦金属开始熔化,激光束的功率会被调整,以保持金属表面的温度在其熔点以上,但不高于其沸点。
在这种情况下,金属可以熔化,但不会汽化。
在选区激光熔化过程中,激光束被聚焦在金属表面上,形成一个非常小的熔池。
激光束的焦点可以被控制,因此可以精确地控制熔池的位置和大小。
可以使用计算机控制系统来控制激光束的位置和功率,以形成所需的形状。
当金属开始凝固时,激光束的功率会被降低,以保持温度在熔点以下,但高于室温。
在这种情况下,金属会逐渐凝固,形成所需的形状。
二、选区激光熔化技术的应用选区激光熔化技术在许多领域得到了广泛的应用。
其中最常见的是航空航天和汽车工业。
在这些行业中,需要生产高质量、高精度的零部件,以确保安全和可靠性。
选区激光熔化技术可以生产出非常复杂的形状,例如复杂的几何形状和内部结构,这些结构无法通过传统的加工方法实现。
此外,选区激光熔化技术可以生产出非常高质量的表面,这对于需要高精度表面的应用非常重要。
选区激光熔化技术还可以用于医疗设备制造。
医疗设备需要具有高度的可靠性和精度,以确保其有效性和安全性。
选区激光熔化技术可以生产出非常精密的零部件,例如人工关节和牙科支架。
这些部件具有非常复杂的形状和内部结构,可以精确地适应人体的需求。
三、选区激光熔化技术的优点和限制选区激光熔化技术具有许多优点。
首先,它可以生产出非常复杂的形状和内部结构,这些结构无法通过传统的加工方法实现。
选区激光融化技术

选区激光融化技术引言激光融化技术是一种先进的制造技术,被广泛应用于各个领域。
尤其是在选区激光融化技术中,其精确性和可控性使其成为材料制造和3D打印领域的热门研究课题。
本文将对选区激光融化技术进行全面、详细、完整且深入地探讨。
二级标题1:选区激光融化技术的概念和原理选区激光融化技术,也被称为选择性激光熔化技术(Selective Laser Melting,简称SLM),是一种通过激光束瞄准目标材料并进行局部加热,使其融化并与底层材料融为一体的制造技术。
其原理主要包括以下几个方面:1.初始材料:选区激光融化技术使用粉末材料作为初始材料,目前常用的材料包括金属、陶瓷等。
这些粉末材料具有良好的流动性和熔点,适合于激光的加工。
2.光束瞄准:通过计算机控制系统,激光束被精确地瞄准到目标材料的特定位置。
光束的能量密度非常高,能够快速加热目标材料并使其融化。
3.材料融化:一旦激光束照射到目标材料上,能量会被吸收,并导致材料局部融化。
由于激光束的高能量密度,材料融化非常快速。
4.融化层与底层结合:融化的材料与底层材料之间的黏结作用力使其结合在一起,形成一个连续的物体。
这种结合具有很高的强度和密度,使制造出的产品具有良好的性能。
二级标题2:选区激光融化技术的应用选区激光融化技术在各个领域都有着广泛的应用。
以下是一些主要领域的应用示例:三级标题1:航空航天1.制造复杂结构件:选区激光融化技术可以制造出复杂形状的金属件,满足航空航天领域对轻量化和高强度的需求。
2.修复和再制造:选区激光融化技术可以修复损坏的航空航天部件,并使其恢复到原始设计规格。
三级标题2:医疗领域1.制造个性化植入物:选区激光融化技术可以根据患者的具体情况制造个性化的植入物,提高植入物与组织的匹配度。
2.快速制造医疗器械:选区激光融化技术可以快速制造医疗器械,满足紧急救援和手术需求。
三级标题3:汽车制造1.制造复杂结构件:选区激光融化技术可以制造汽车发动机部件等复杂结构件,提高汽车的性能和可靠性。
激光选区熔化工作原理

激光选区熔化工作原理激光选区熔化是一种先进的材料加工技术,它通过使用高能激光束对材料进行加热和熔化,实现对材料的精确加工。
激光选区熔化工艺的原理是利用激光束的高能量密度和高方向性,使选定的区域在瞬间受热并熔化,从而实现对材料的精确熔化和形状控制。
激光选区熔化的工作原理可以简单地分为以下几个步骤。
首先,激光束通过光学系统进行聚焦,集中到非常小的焦点上。
这个焦点就是激光束的能量密度最高的区域,也是激光选区熔化的作用区域。
当激光束到达作用区域时,它的高能量密度会使材料迅速升温,超过了材料的熔点。
在短时间内,材料受热并熔化,形成液态区域。
这个过程发生得非常迅速,激光束的作用时间通常只有几纳秒到几毫秒。
在熔化过程中,激光束的高方向性起到了至关重要的作用。
激光束的高方向性意味着它的能量可以被精确地定位和控制。
因此,激光选区熔化可以实现对材料的精确加工和形状控制。
通过改变激光束的聚焦位置和扫描路径,可以选择性地熔化材料的特定区域,实现精确的加工和形状控制。
除了高方向性,激光束还具有高能量密度的特点。
激光束的高能量密度使得它的熔化效果非常显著。
相比传统的加热方法,激光选区熔化可以在瞬间将材料加热到非常高的温度,远远超过了材料的熔点。
这种高能量密度的加热方式可以实现对材料的快速熔化和形状控制,同时减少了对材料的热影响区域,降低了材料的变形和损伤风险。
激光选区熔化可以应用于各种材料的加工,包括金属、陶瓷、塑料等。
不同的材料对激光的吸收和传导特性有所差异,因此在实际应用中需要针对不同材料进行参数的调整和优化。
通过合理选择激光功率、扫描速度和聚焦位置等参数,可以实现对不同材料的精确熔化和加工。
总的来说,激光选区熔化是一种高精度、高效率的材料加工技术。
它利用激光束的高能量密度和高方向性,实现对材料的精确熔化和形状控制。
激光选区熔化可以应用于各种材料的加工,并具有快速、灵活、无接触等优点。
随着激光技术的不断发展和进步,激光选区熔化将在制造业、电子工业、医疗器械等领域得到广泛应用。
选择性激光熔化技术在增材制造中的应用研究
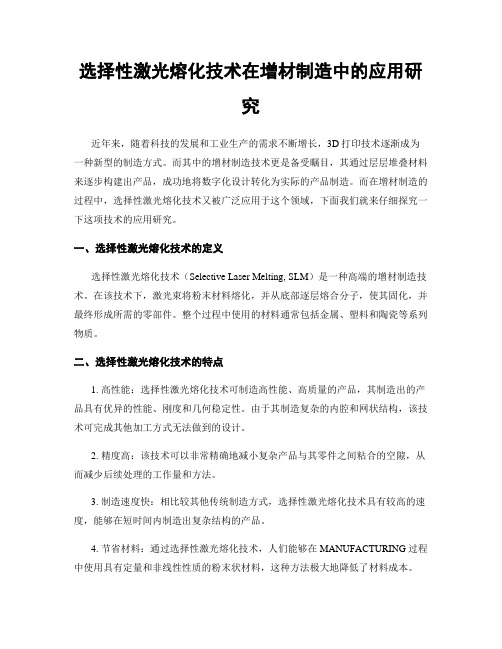
选择性激光熔化技术在增材制造中的应用研究近年来,随着科技的发展和工业生产的需求不断增长,3D打印技术逐渐成为一种新型的制造方式。
而其中的增材制造技术更是备受瞩目,其通过层层堆叠材料来逐步构建出产品,成功地将数字化设计转化为实际的产品制造。
而在增材制造的过程中,选择性激光熔化技术又被广泛应用于这个领域,下面我们就来仔细探究一下这项技术的应用研究。
一、选择性激光熔化技术的定义选择性激光熔化技术(Selective Laser Melting, SLM)是一种高端的增材制造技术。
在该技术下,激光束将粉末材料熔化,并从底部逐层熔合分子,使其固化,并最终形成所需的零部件。
整个过程中使用的材料通常包括金属、塑料和陶瓷等系列物质。
二、选择性激光熔化技术的特点1. 高性能:选择性激光熔化技术可制造高性能、高质量的产品,其制造出的产品具有优异的性能、刚度和几何稳定性。
由于其制造复杂的内腔和网状结构,该技术可完成其他加工方式无法做到的设计。
2. 精度高:该技术可以非常精确地减小复杂产品与其零件之间粘合的空隙,从而减少后续处理的工作量和方法。
3. 制造速度快:相比较其他传统制造方式,选择性激光熔化技术具有较高的速度,能够在短时间内制造出复杂结构的产品。
4. 节省材料:通过选择性激光熔化技术,人们能够在MANUFACTURING过程中使用具有定量和非线性性质的粉末状材料,这种方法极大地降低了材料成本。
三、选择性激光熔化技术在增材制造中的应用研究1. 金属粉末激光熔化金属粉末激光熔化技术已经在医疗、武器、航空和制造等行业得到了广泛的应用。
该技术通过三维扫描获取设计蓝图,并将蓝图转化成后续制造所需的图像信息,最后通过激光熔化粉末的方式进行构造。
这一过程具有材料高温熔融、再凝固、材料变形等特点,需要完整考虑材料物理化学性质、温度过程和强度或韧性等特点。
2. 计算流体动力学仿真技术为了进一步提高激光熔化工艺的效率和精确性,人们还引入了流体力学仿真技术来处理和模拟激光熔化过程中的材料流动和热传导等特点。
slm增材制造原理

SLM增材制造原理引言SLM(Selective Laser Melting,选择性激光熔化)是一种基于粉末床的3D打印技术,它通过激光束逐层熔化金属粉末,来制造复杂形状的零件。
本文将详细解释SLM增材制造的基本原理。
SLM增材制造流程SLM增材制造的流程主要可以分为预处理、建模、切片、制造和后处理五个步骤。
1.预处理:这个步骤主要包括选取合适的金属粉末和准备构建平台。
2.建模:用户可以使用计算机辅助设计(CAD)软件来设计零件,然后将其转换为STL文件格式。
STL文件会包含零件的几何信息,被切片软件用来生成制造路径。
3.切片:切片软件根据STL文件生成切片,每个切片表示一个横截面。
切片具有一定的厚度,决定了零件的分辨率。
每个切片都会被分解成小的像素点,用于生成制造路径。
4.制造:制造过程首先将金属粉末均匀地撒布在构建平台上,然后激光束聚焦在一个像素点上熔化金属粉末,形成一层。
构建平台下降一个切片厚度,然后下一个激光照射点被熔化,如此循环直至制造完成。
5.后处理:制造完成后,零件需要进行后处理。
这可能包括去除残留的金属粉末、热处理、喷砂、磨削、抛光等工序,以去除表面的瑕疵并获得更好的表面质量。
SLM增材制造的基本原理SLM增材制造的基本原理包括材料的熔化、形成零件的路径规划以及材料性能的控制。
1. 材料的熔化SLM增材制造使用激光束来熔化金属粉末,将其形成零件的一层。
激光束的能量会使金属粉末迅速升温并达到熔点,然后在激光束移动的同时快速冷却固化。
这个过程被称为激光熔化。
激光熔化的关键是激光的选择和调控。
激光的能量密度和聚焦能力决定了金属粉末的熔化情况。
在SLM增材制造中,常用的激光是CO2激光或纤维激光,它们具有高能量密度和聚焦能力。
2. 路径规划路径规划是将STL文件中的几何信息转化为制造路径的过程。
在切片软件中,每个切片会被分解成小的像素点,代表零件的一部分。
每个像素点都会对应一个激光照射点,在制造过程中被熔化形成零件的一部分。
slm工艺参数

slm工艺参数
SLM(选择性激光熔化技术)工艺参数主要包括激光功率、扫描速度、扫描间距、层厚、光斑直径等。
这些参数对成型件的精度、致密度、力学性能等方面都有重要影响。
在SLM工艺中,激光功率是影响成型件质量的重要因素之一。
如果激光功率过低,无法熔化粉末材料,会导致成型件出现孔洞、不致密等缺陷;如果激光功率过高,则会导致材料过度熔化、球化、飞溅等问题,进而影响成型件的精度和性能。
因此,需要根据材料特性、工艺要求和设备参数等因素,选择合适的激光功率。
扫描速度也是影响成型件质量的关键因素之一。
扫描速度过慢会导致材料熔化不充分,影响成型件的致密度和强度;扫描速度过快则会导致材料熔化过度,产生球化、飞溅等问题。
因此,需要根据实际情况选择合适的扫描速度。
扫描间距和层厚是相互关联的参数,对成型件的精度和表面质量都有重要影响。
扫描间距过大会导致层与层之间的结合力下降,影响成型件的强度;扫描间距过小则会导致表面质量下降,产生过多的球化和飞溅。
因此,需要根据实际情况选择合适的扫描间距和层厚。
光斑直径也是影响成型件质量的重要因素之一。
光斑直径过大会导致成型件表面粗糙度增加,影响美观度和精度;光斑直径过小则会导致熔池过小,产生球化和飞溅等问题。
因此,需要根据实际情况选择合适的光斑直径。
综上所述,SLM工艺参数的选择需要根据实际情况进行优化和调整,以保证成型件的质量和性能。
在实际操作中,可以通过实验和数据分析来确定最佳的工艺参数组合。
- 1、下载文档前请自行甄别文档内容的完整性,平台不提供额外的编辑、内容补充、找答案等附加服务。
- 2、"仅部分预览"的文档,不可在线预览部分如存在完整性等问题,可反馈申请退款(可完整预览的文档不适用该条件!)。
- 3、如文档侵犯您的权益,请联系客服反馈,我们会尽快为您处理(人工客服工作时间:9:00-18:30)。
•近年来诞生了选择性激光熔化(Selective Laser Melting,SLM)金属粉末的快速成型技术,用它能直接成型出接近完全致密度的金属零件。
SLM技术克服了选择性激光烧结(Selective Laser Sintering。
SLS)技术制造金属零件工艺过程复杂的困扰。
用SLS技术制造金属零件的方法主要有:(1)熔模铸造法:首先采用SLS技术成型高聚物(聚碳酸酯PC、聚苯乙烯PS等)原型零件,然后利用高聚物的热降解性,采用铸造技术成型金属零件。
(2)砂型铸造法:首先利用覆膜砂成型零件型腔和砂芯(即直接制造砂型),然后浇铸出金属零件。
(3)选择性激光间接烧结原型件法:高分子与金属的混合粉末或高分子包覆金属粉末经SLS成型,经脱脂、高温烧结、浸渍等工艺成型金属零件。
(4)选择性激光直接烧结金属原型件法:首先将低熔点金属与高熔点金属粉末混合,其中低熔点金属粉末在成形过程中主要起粘结剂作用。
然后利用SLS技术成型金属零件;最后对零件后处理,包括浸渍低熔点金属、高温烧结、热等静压(Hotisostat ic Pressing,HIP)。
这些方法所制造的金属零件机械性能受低型工艺过程的影响因素比较多。
为此,德国Fraunhofer激光器研究所(Fraunhofer Inst itu te for LaserTechnology,ILT)最早提出了直接制造金属零件的SLM技术。
选择性激光熔化技术的基本原理SLM技术是利用金属粉末在激光束的热作用下完全熔化、经冷却凝固而成型的一种技术。
为了完全熔化金属粉末,要求激光能量密度超过106W/Cm2。
目前用SLM技术的激光器主要有Nd-YAG激光器、Co2激光器、光纤(Fiber)激光器。
这些激光器产生的激光波长分别为1064nm、10640nm、1090nm。
金属粉末对1064nm等较短波长激光的吸收率比较高,而对10640nm等较长波长激光的吸收率较低。
因此在成型金属零件过程中具有较短波长激光器的激光能量利用率高,但是采用较长波长的Co2激光器,其激光能量利用率低。
在高激光能量密度作用下,金属粉末完全熔化,经散热冷却后可实现与固体金属冶金焊合成型。
SLM技术正是通过此过程,层层累积成型出三维实体的快速成型技术。
根据成型件三维CAD模型的分层切片信息,扫描系统(振镜)控制激光束作用于待成型区域内的粉末。
一层扫描完毕后,活塞缸内的活塞会下降一个层厚的距离;接着送粉系统输送一定量的粉末,铺粉系统的辊子铺展一层厚的粉末沉积于已成型层之上。
然后,重复上述2个成型过程,直至所有三维CAD模型的切片层全部扫描完毕。
这样,三维CAD模型通过逐层累积方式直接成型金属零件。
最后,活塞上推,从成型装备中取出零件。
至此,SLM金属粉末直接成型金属零件的全部过程结束。
•选择性激光熔化技术的研究现状与进展目前,国外应用SLM技术可制造模具、工具、生物移植物等金属零件。
但技术仍不够成熟,其应用领域还不够广泛。
SLM技术的研究主要针对以下几个方面:成型装备、金属粉末、成型工艺、成型机理、成型件性能、成型过程模拟和成型件的应用。
1选择性激光熔化装备SLM装备的许多方面都影响成型工艺及成型件的精度、机械性能。
在开发SLM装备方面,只有德国、日本、美国等少数几个国家的生产商成功地开发了商用装备。
这些公司包括德国的MCP、TRUMPF,日本的MATSUUR和美国的PHENIX。
这些公司SLM 装备的不同之处主要体现在激光器、聚焦面光斑尺寸、铺粉方式和活塞缸铺粉层厚等方面。
MCP公司和PHENIX公司的SLM装备应用的激光器为100W光纤激光器,激光波长为1090nm,其主要工作模式为CW/Modulated,光纤激光器激光束的输出模式为TEM00(TransverseElectromagnetic Modes);其光束横截面能量分布为高斯分布,且在传输过程中保持不变,光束质量好,激光束经聚焦后的激光光斑在30un~250um 之间。
TRUMPF公司的SLM装备配备250W盘形激光器,激光波长为1030nm;光斑大小可变范围在200um~400um。
MATSU U RA公司的SLM装备采用500W脉冲式Co2,激光器,激光波长10640nm,其峰值达1.5kW,频率达100kHZ。
光斑大小为600um。
除了以上公司进行SLM装备的商业生产外,还有包括比利时鲁汶大学、日本大阪大学等在内的高校从事SLM装备的研制。
这些高校自行研制的SLM装备和上述公司商用生产的装备相似,主要是在激光器,聚焦光斑、铺粉层厚、铺粉方式等方面有所不同。
目前国内主要有华中科技大学在这方面进行了研究,并不断地跟踪SLM技术的最新发展情况。
华中科技大学快速制造中心已经研制出拥有自主知识产权的商品化SLM设备——HRPM系列金属粉末熔化成型设备。
该设备采用了150W CW Nd—YAG激光器和lOOW CW光纤激光器,由武汉滨湖机电技术产业有限公司生产制造,已在市场上进行了销售,打破了国外公司在这方面的垄断,大大降低了该设备的价格,方便了国内的广大用户。
2选择性激光熔化技术所用粉末适合SLM技术的金属粉末比较广泛。
如果自行设计适合SLM成形的材料成分并制备粉末,其造价比较高,不经济。
因此,目前用于SLM技术研究的粉末主要来源于商用粉末。
可以研究它们的成型性,从而提出该技术选用粉末的标准。
•用于SLM成型的粉末可以分为混合粉末、预合金粉末、单质金属粉末3类。
(1)混合粉末。
混合粉末由一定成分的粉末经混合均匀而成。
设计混合粉末时要考虑激光光斑大小对粉末颗粒粒度的要求。
Kruth J.P.等人研制了铁基混合粉(包含Fe,Ni,Cu,Fe,P)。
因激光光斑为600 u 111,所以要求混合粉中颗粒的最大尺寸不能超过该光斑直径。
应用这种混合粉的SLM成形件不能满足100%致密度要求,因此其机械性能还有待进一步提高。
鲁中良等研制了Fe-Ni-C混合粉末,其组成成分为:ω(Fe)=91.5%、ω(Ni)=8.0%、ω(C)=O.5%。
Fe、Ni粉末为-300目,C粉为-200目。
应用该混合粉末的SLM成型件致密度较低,存在大量的孔隙。
对混合粉的SLM成型研究表明,混合粉的成型件致密度有待提高,其机械性能受致密度、成分均匀度的影响。
(2)预合金粉末。
根据预合金主要成分的不同,预合金粉末可以分为铁基、镍基、钛基、钴基、铝基、铜基、钨基等。
铁基合金粉末包括工具钢M2、工具钢H13、不锈钢316L(1.4404)、Inox 904L、314s—HC、铁合金(Fe-15Cr-1.5B),其SLM成型结果表明:低碳钢比高碳钢的成型性好,成型件的相对致密度仍不能完全达到100%。
镍基合金粉末包括Ni625、NiTi合金、Waspaloy合金、镍基预合金(ω(Ni)=83.6%、ω(Cr)=9.4%、ω(B)=1.8%、ω(S i)=2.8%、ω(Fe)=2.0%、ω(C)=0.4%),其成型结果表明:成型件的相对致密度可达99.7%。
钛合金粉末主要有TiAl6V4合金,其SLM成型结果表明:成型件相对致密度可达95%。
钴合金粉末主要有钴铬合金,其SLM成型结果表明:成型件相对致密度可达96%。
铝合金粉末主要有A16061合金,其SLM成型结果表明:成型件的相对致密度可达91%。
铜合金粉末包括Cu/Sn合金、铜基合金(84.5Cu-8Sn-6.5P一1Ni)、预合金Cu-P,其SLM成型结果表明:成型件的相对致密度可达95%。
钨合金粉末主要有钨铜合金,其SLM成型结果表明:成型件的相对致密度仍然达不到100%。
(3)单质金属粉末。
单质金属粉末主要有钛粉,其SLM成型结果表明:钛粉的成型性较好,成型件的相对致密度可达98%。
综上所述,SLM技术所用粉末主要为单质金属粉末和预合金粉末。
单质金属粉末和预合金粉末的成型件的成分分布、综合机械性能较好。
所以成型工艺研究主要针对预合金、单质金属粉末的工艺优化,以提高成型件的致密度。
3选择性激光熔化成型工艺SLM成型工艺主要研究工艺参数对粉末成型轨迹和致密度的影响规律。
(1)工艺参数对成型轨迹的影响。
在SLM成型过程中,成型轨迹特征受工艺参数的影响。
成型轨迹主要包括激光束对粉末的单点、单道扫描,单层、多道扫描成型的轨迹,通过对成型轨迹的评价来研究工艺参数对成型轨迹的影响规律。
(2)工艺参数对致密度的影响。
金属零件致密度是影响其机械性能的一个主要因素。
金属粉末SLM成型件致密度是一个关键技术指标,受激光波长、激光功率密度和粉末成分的影响。
在Co2激光(波长为10640nm)作用下成型件致密度较低,这与金属粉末对激光的较低吸收率、激光功率密度有关;而YAG激光(波长为1064nm)作用下的成型件致密度较高,是因为其激光功率密度高,金属粉末对激光的吸收率高。
此外,粉末化学成分是影响其润湿性的主要因素,所以低碳成分的铁基合金粉末的润湿性好,其SLM成型件的致密度高。
•4选择性激光熔化成型机理在SLM成型过程中,提高粉末的成型性,就必须提高液态金属的润湿性。
在成型过程中,若液态金属成球,则说明液态金属的润湿性不好。
液态金属对固体金属的润湿性受工艺参数的影响,因此可优化工艺参数来提高特定粉末的润湿能力。
研究结果表明,液态金属在缺少与氧化物发生化学反应的情况下是不能润湿固体氧化膜的,因此在成型过程中要防止氧化,虽然添加合金元素P可提高润湿性,但是元素P会影响成型件的机械性能。
5选择性激光熔化成型件性能S L M成型件性能主要包括残余应力、残余应变、显微组织和机械性能。
(1)残余应力,残余应变。
金属粉末在SLM成型过程中,会因温度梯度产生热应变和残余应力,进而影响成形过程。
研究结果表明:翘曲、裂纹、热应力、表面粗糙、显微组织等问题主要是因成型过程中激光作用下的快热快冷(淬火)所致。
为此,提出了双激光(Co2、Nd-YAG)扫描系统方案。
(2)显微组织。
工艺参数会影响SLM成型件的显微组织。
如果激光扫描速度快,那么冷却速度也会较快,使显微组织更细,有利于提高SLM成型件的机械性能。
(3)机械性能。
S L M成型件的机械性能主要包括强度、硬度、精度和表面粗糙度等。
SLM成型件的弯曲强度受激光工作模式的影响,在脉冲及其反冲作用力工作模式下的SLM成型件,其最大抗弯曲强度为630MPa,未经任何处理的成型件表面粗糙度达10 um~30 um。
因SLM成型件的相对致密度未达到100%,所以抗弯强度等机械性能会受到一定的影响。
6选择性激光熔化成型过程的数值模拟SLM成型过程是一个激光束熔化粉末、相变和凝固冶金结合的过程。
在SLM成型过程中,粉末在极短(毫秒级)的时间内熔化,温度梯度大,通过试验方法测量其温度动态过程比较困难;而通过有限元法模拟分析并揭示其成型过程,能够为制定合理的工艺参数、减少试验次数、成型高质量零件提供重要的理论指导。