埋弧焊工艺参数及焊接技术
埋弧焊工艺参数及焊接技术

埋弧焊工艺参数及焊接技术(2)埋弧焊2006-10-30 10:03:31 阅读461 评论0 字号:大中小订阅(3) 对接接头双面焊一般工件厚度从10 ~40mm 的对接接头,通常采用双面焊。
接头形式根据钢种、接头性能要求的不同,可采用图18 所示的I 形、Y 形、X 形坡口。
图18不同板厚的接头形式a)I形坡口对接焊b)Y形坡口对接焊c)X形坡口对接焊这种方法对焊接工艺参数的波动和工件装配质量都不敏感,其焊接技术关键是保证第一面焊的熔深和熔池的不流溢和不烧穿。
焊接第一面的实施方法有悬空法、加焊剂垫法以及利用薄钢带、石棉绳、石棉板等做成临时工艺垫板法进行焊接。
1) 悬空焊装配时不留间隙或只留很小的间隙( 一般不超过lmm) 。
第一面焊接达到的熔深一般小于工件厚度的一半。
反面焊接的熔深要求达到工件厚度的60 %~70 %,以保证工件完全焊透。
不开坡口的对接接头悬空焊的焊接参数,如表9 所示。
表9 不开口对接接头悬空双面焊的焊接条件工件厚度/mm 焊丝直径/mm 焊接顺序焊接电流/A 电弧电压/V 焊接速度/cm.min -16 4 正380 ~420 30 58反430 ~470 30 558 4 正440 ~480 30 50反480 ~530 31 5010 4 正530 ~570 31 46反590 ~640 33 4612 4 正620 ~660 35 42反680 ~720 35 4114 4 正680 ~720 37 41反730 ~770 40 3816 5 正800 ~850 34 ~6 63反850 ~900 36 ~8 4317 5 正850 ~900 35 ~37 60反900 ~950 37 ~39 4818 5 正850 ~900 36 ~38 60反900 ~950 38 ~40 4020 5 正850 ~900 36 ~38 42反900 ~1000 38 ~40 4022 5 正900 ~950 37 ~39 453反1000 ~1050 38 ~40 402) 在焊剂垫上焊接如图19 所示,焊接第一面时采用预留间隙不开坡口的方法最为经济。
埋弧焊焊接工艺

埋弧焊焊接工艺
1、加衬铁情况下的筒体与封头对接应留有3-4mm的缝隙,便于使用二保焊打底;对于10mm 以上板材或没有加衬铁的情况,要双面焊接(即里面电弧焊焊接,外面二保焊打底)。
2、12mm及以上板材或10mm大直径工件,里面电弧焊焊接完毕后,外边要使用气爆焊条进行气爆处理,然后二保焊打底,最后埋弧焊接。
3、在埋弧焊焊接之前,要对工件焊缝周围进行抛光处理,包括焊缝、焊缝左右约5cm范围以内,彻底去除油污、焊渣、氧化层等影响焊接工艺的杂物。
4、采用符合规定的焊丝和焊剂,调整电压、电流、焊接速度使之符合工艺要求。
5、焊枪头对准焊缝中心偏下的位置,滚轮架向焊枪头相反的一侧转动,焊丝伸出保护帽长度大约为焊丝直径的4-5倍,不小于10mm;
6、原则上对于环缝的焊接不允许有两个或以上的焊接接头,焊剂要提前添加,防止缺少焊剂额情况。
7、埋弧焊地线要牢固可靠的紧紧连接至工件本身,防止断弧的发生。
8、埋弧焊剂可循环使用,但是要筛除杂质,防止气孔或出现不溶物。
焊缝成型图例
当其他条件不变时,增大电流,溶深加大,余高加大,易产生高温裂纹;
减小电流,溶深减小,余高、宽度不足
当电压加大时,余高不足,溶深减小,宽度加大
电压减小时,溶深大,宽度小,余高大
焊接速度与溶深溶宽成反比关系。
埋弧焊最主要的焊接工艺参数有:电压、电流、焊接速度、焊丝伸出长度。
16mm板埋弧焊焊接参数

16mm板埋弧焊焊接参数16mm板埋弧焊是一种常见的焊接工艺,它广泛应用于钢结构、压力容器、管道、桥梁和船舶等领域。
在进行板埋弧焊时,需要确定适当的焊接参数,以确保焊接质量和工作效率。
下面是16mm板埋弧焊的相关参考内容。
1. 焊接电流:板埋弧焊的焊接电流是焊接参数中最重要的指标之一。
焊接电流的选择应根据所焊接的材料、板厚和焊接位置来确定。
通常情况下,16mm板的埋弧焊电流范围为200-400安培。
较高的电流可以提高焊接速度和熔深,但也会增加热输入和变形的风险。
因此,应根据具体情况选择适当的焊接电流。
2. 焊接电压:焊接电压是控制焊接电弧稳定性和熔池形状的关键参数。
对于16mm板的埋弧焊,一般选择焊接电压为24-30伏。
较低的电压可以使焊接电弧更稳定,但同时会降低焊接速度和熔池形成能力。
较高的电压可以提高焊接速度,但会增加飞溅和热应力的风险。
因此,应根据具体情况选择适当的焊接电压。
3. 焊接速度:焊接速度是确定焊接参数的重要因素之一。
焊接速度的选择应根据焊接电流和焊接电压来确定。
一般情况下,16mm板的埋弧焊焊接速度为10-20cm/min。
较低的焊接速度可以提高焊接熔深和焊缝强度,但会增加工作时间和成本。
较高的焊接速度可以提高生产效率,但焊接熔深会减小。
因此,应根据具体情况选择适当的焊接速度。
4. 焊接极性:埋弧焊的电极可使用直流极性(DC+)或直流反极性(DC-),选择合适的焊接极性是保证焊接质量的关键。
对于16mm板的埋弧焊,一般采用直流反极性。
直流反极性可以提高焊接速度和焊缝质量,同时减小喷溅现象。
而直流极性则更适用于焊接较厚的板材。
因此,应根据具体情况选择合适的焊接极性。
5. 焊接工艺:在进行16mm板的埋弧焊时,还需选确定适当的焊接工艺,如焊接电弧长度、焊接角度和焊接时机等。
通常情况下,焊接电弧长度应保持在10-15mm,焊接角度应保持在20-45度范围内。
此外,焊接板材的准备工作、预热温度等也会对焊接质量产生影响,应根据具体情况进行调整。
埋弧焊工艺参数及焊接技术

埋弧焊工艺参数及焊接技术埋弧焊是一种常见的焊接方法,广泛应用于工业领域。
在进行埋弧焊时,正确设置工艺参数是保证焊接质量的重要因素之一。
本文将介绍埋弧焊的工艺参数以及焊接技术,帮助读者更好地理解和掌握这一焊接方法。
1. 埋弧焊工艺参数1.1 电流与电压在埋弧焊中,电流和电压是两个关键的工艺参数。
合理的电流和电压设定可以保证焊接的稳定性和质量。
一般来说,电流的选择应该根据焊接材料和焊接件的厚度来确定。
较粗的焊接件需要较大的电流,而较薄的焊接件则需要较小的电流。
电压的选择则影响焊接过程中的弧长以及熔池的形成和稳定性。
通常情况下,较高的电压可以获得较长的弧长,适用于焊接较厚的材料。
而较低的电压则适用于焊接薄板材料。
1.2 焊接速度焊接速度是指焊接电弧沿焊缝移动的速度。
合理的焊接速度能够控制焊接过程中的热输入,从而保证焊接接头的质量。
焊接速度的选择应该综合考虑焊接材料的热导性、电流和电压等参数。
一般来说,焊接速度过快容易导致焊缝出现缺陷,而速度过慢则容易引起过烧。
1.3 焊接角度焊接角度是指焊条或焊枪与焊缝法线之间的夹角。
合理的焊接角度可以影响焊接过程中的熔池形成和焊缝形状。
一般来说,焊接角度过大可能导致熔池过大,焊接质量不稳定。
而焊接角度过小则会影响焊接速度和焊缝的形成。
2. 焊接技术2.1 预热在进行埋弧焊前,预热焊接部位是提高焊接质量的技术之一。
预热可以减轻焊接部位的残余应力,提高焊接强度和韧性。
预热温度的选择应考虑焊接材料的类型和厚度等因素,并通过试验和实践来确定最佳的预热温度。
2.2 清洁焊接前的清洁工作十分重要,可以有效地避免焊接缺陷的产生。
焊接部位应清除油污、氧化物和其他杂质,确保焊接表面干净。
这可以通过机械清洁、溶剂清洗、除锈剂处理等方法来完成。
2.3 间隙控制在焊接过程中,合适的间隙控制能够保证焊缝的形状和尺寸。
间隙的选择应根据焊接件的要求和所使用的焊接方法来决定。
一般来说,焊接件的间隙应视焊接材料的膨胀和热收缩特性来决定。
埋弧焊工艺参数及焊接技术
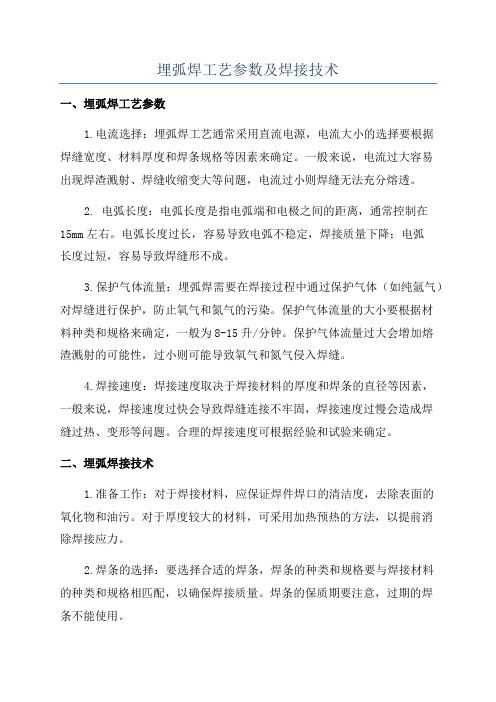
埋弧焊工艺参数及焊接技术一、埋弧焊工艺参数1.电流选择:埋弧焊工艺通常采用直流电源,电流大小的选择要根据焊缝宽度、材料厚度和焊条规格等因素来确定。
一般来说,电流过大容易出现焊渣溅射、焊缝收缩变大等问题,电流过小则焊缝无法充分熔透。
2. 电弧长度:电弧长度是指电弧端和电极之间的距离,通常控制在15mm左右。
电弧长度过长,容易导致电弧不稳定,焊接质量下降;电弧长度过短,容易导致焊缝形不成。
3.保护气体流量:埋弧焊需要在焊接过程中通过保护气体(如纯氩气)对焊缝进行保护,防止氧气和氮气的污染。
保护气体流量的大小要根据材料种类和规格来确定,一般为8-15升/分钟。
保护气体流量过大会增加熔渣溅射的可能性,过小则可能导致氧气和氮气侵入焊缝。
4.焊接速度:焊接速度取决于焊接材料的厚度和焊条的直径等因素,一般来说,焊接速度过快会导致焊缝连接不牢固,焊接速度过慢会造成焊缝过热、变形等问题。
合理的焊接速度可根据经验和试验来确定。
二、埋弧焊接技术1.准备工作:对于焊接材料,应保证焊件焊口的清洁度,去除表面的氧化物和油污。
对于厚度较大的材料,可采用加热预热的方法,以提前消除焊接应力。
2.焊条的选择:要选择合适的焊条,焊条的种类和规格要与焊接材料的种类和规格相匹配,以确保焊接质量。
焊条的保质期要注意,过期的焊条不能使用。
3.焊接过程:焊接时,要保证电弧稳定,焊条与工件的距离适当,不得与气缝直接接触。
焊接位置要选择合适,以便操作方便。
焊接方向要与主应力方向垂直。
4.焊后处理:焊接后,应采取适当的焊后处理措施,如退火、热处理等,以提高焊接接头的性能和质量。
总结:埋弧焊工艺参数及焊接技术对焊接质量和效率具有重要影响。
通过选择合适的电流、电弧长度和保护气体流量等参数,合理控制焊接速度,做好焊前准备和焊后处理工作,可以保证埋弧焊接的质量和可靠性。
同时,焊工应具备良好的焊接技术和操作经验,能够正确操作焊接设备和工具,严格按照操作规程进行焊接,以确保焊接质量和安全。
半自动埋弧焊工艺参数

半自动埋弧焊工艺参数1.电流和电压电流和电压是半自动埋弧焊中最基本的焊接参数。
电流的大小决定焊丝熔化速度和热输入量,而电压的高低则决定着焊丝进出电弧的稳定性。
一般来说,焊接厚板时所需的电流较大,焊接细密部件时所需的电流较小。
电压的选择要根据焊接工件的材质和厚度来确定,一般较大电压适用于焊接较厚的工件,较小电压适用于焊接较薄的工件。
2.电弧长度电弧长度指的是焊丝露出焊枪嘴外部的长度。
电弧长度的大小会影响焊丝的熔化速度和热输入量。
一般来说,焊接厚板时所需的电弧长度较大,焊接细密部件时所需的电弧长度较小。
然而,过长的电弧长度容易导致焊缝过宽,过短的电弧长度则容易导致焊缝不深。
3.电弧稳定性电弧稳定性是半自动埋弧焊中一个非常重要的参数。
电弧不稳定会导致焊缝质量下降以及焊接速度变慢。
为了保持电弧的稳定性,可以适当增大电流或电压,或者采用较为稳定的焊丝。
4.焊接速度焊接速度是指焊接过程中焊接焊缝的移动速度。
焊接速度的选择要根据焊接工件的材质和厚度来确定。
一般来说,焊接厚板时所需的焊接速度较慢,焊接细密部件时所需的焊接速度较快。
焊接速度的选择应该使焊接焊缝质量最佳,并且能够保持焊接过程的稳定性。
5.焊丝直径和种类焊丝的直径和种类对焊接质量有很大影响。
一般来说,焊接厚板时所需的焊丝直径较大,焊接细密部件时所需的焊丝直径较小。
焊丝的种类可以根据工件的材质来选择,一般有碳钢焊丝、不锈钢焊丝、铝焊丝等。
6.保护气体保护气体在半自动埋弧焊中起到保护焊缝免受氧化的作用。
常用的保护气体有纯CO2气体和混合气体。
纯CO2气体适用于焊接碳钢工件,而混合气体适用于焊接不锈钢和铝合金工件。
保护气体的流量要适中,不能过大或过小。
总的来说,半自动埋弧焊的参数选择要根据具体情况来确定。
在实际操作中,需要根据焊接工件的材质、厚度以及焊接要求来选择合适的焊接参数,以保证焊接质量和焊接效率的最佳平衡。
不锈钢埋弧焊焊接工艺参数
不锈钢埋弧焊焊接工艺参数
不锈钢埋弧焊是一种常用的焊接方法,其主要工艺参数包括:
1. 电流大小:根据不锈钢材料的类型、规格和厚度,选择适当的电流大小,一般建议在180-260A之间。
2. 电极直径:不锈钢埋弧焊一般采用直径为2.5mm或
3.2mm的电极,直径越大,焊接速度越快。
3. 焊接速度:焊接速度的快慢对焊缝质量和焊接效率都有一定影响,应根据实际情况选择合适的焊接速度。
4. 电弧长度:电弧长度的选择与焊接速度和电流大小有关,一般建议电弧长度为3-5mm。
5. 焊接气体保护:不锈钢埋弧焊需要保护气体,一般采用
Ar+2%O2的混合气体,气体流量一般为15-25L/min。
6. 预热温度:当不锈钢厚度大于6mm时,需要进行预热处理,一般建议预热温度为150-200℃。
以上是不锈钢埋弧焊焊接工艺参数的常见选择,具体的工艺参数应根据实际情况进行调整。
埋弧焊工艺标准
埋弧焊工艺标准
埋弧焊是一种在焊剂层下完成电弧焊接的方法。
在进行埋弧焊之前,需要进行一系列准备工作,包括焊件的坡口加工、待焊部位的表面清理、焊件的装配以及焊丝表面的清理、焊剂的烘干等。
具体标准如下:
1. 坡口加工:坡口加工要求按GB 986—1988执行,以保证焊缝根部不出现未焊透或夹渣,并减少填充金属量。
坡口的加工可使用刨边机、机械化或半机械化气割机、碳弧气刨等。
2. 待焊部位的清理:在焊前应将坡口及坡口两侧各20mm区域内及待焊部位的表面铁锈、氧化皮、油污等清理干净。
3. 焊件的装配:装配焊件时要保证间隙均匀,高低平整,错边量小,定位焊缝长度一般大于30mm,并且定位焊缝质量与主焊缝质量要求一致。
必要时采用专用工装、卡具。
4. 预热:当埋弧焊焊接的板厚在60mm以上时,焊前必须对焊道及两侧2倍板厚范围内预热,预热温度为100~150℃,板厚为40~60mm时,预热温度宜为60~80℃。
5. 保温:焊接完成前不得中途停止超过15分钟,当必须停止时,应采取保温措施缓冷,重新施焊前必须再次预热,层间温度控制在℃,焊接完后应采用保温棉及时进行保温。
此外,在焊接工艺上主要采取气保焊打底,埋弧自动焊填充及盖面,打底厚度根据板厚而定。
以上信息仅供参考,如需获取更多详细信息,建议查阅埋弧焊工艺标准书籍或咨询专业人士。
埋弧焊焊接参数范文
埋弧焊焊接参数范文埋弧焊是一种常用的电弧焊接方法,它通过在焊接区域形成一个保护层来提供保护和稳定的电弧,并使用焊丝作为填充材料。
埋弧焊具有高效、高质量和广泛适用的优点,被广泛应用于船舶、桥梁、石油和化工等领域。
1.电流:电流是埋弧焊中最重要的参数之一,它直接影响焊接速度和焊缝质量。
选择适当的电流可确保焊缝的熔深和焊缝的质量。
一般来说,焊接厚度越大,需要使用更大的电流。
电流的选择应根据焊接材料的类型、规格和焊接件的要求进行。
2.电压:电压是埋弧焊中另一个重要的参数。
它直接影响焊接电弧长度和焊接速度。
适当的电压可以保持稳定的电弧形态,防止电弧抖动和飞溅。
一般来说,焊接厚度越大,需要使用更高的电压。
电压的选择应根据焊接材料的类型、规格和焊接件的要求进行。
3.保护气体流量:埋弧焊中使用保护气体来保护焊缝和焊丝,防止氧化和污染。
保护气体流量的大小应根据焊接材料的类型、规格和焊接件的要求进行选择。
一般来说,焊接厚度越大,需要使用更大的保护气体流量。
保护气体流量的选择应确保能够有效地覆盖焊接区域,并防止气体逃逸。
4.焊接速度:焊接速度是埋弧焊中另一个重要的参数。
焊接速度的快慢直接影响焊缝的形成和焊缝的质量。
一般来说,焊接厚度越大,焊接速度越慢。
焊接速度的选择应根据焊接材料的类型、规格和焊接件的要求进行。
5.间隙:焊接间隙是指两个焊接接头之间的距离。
焊接间隙的大小影响焊缝的形成和焊缝的质量。
一般来说,焊接间隙越小,焊接质量越好。
焊接间隙的选择应根据焊接材料的类型、规格和焊接件的要求进行。
6.焊丝直径:焊丝直径是埋弧焊中另一个重要的参数。
焊丝直径的选择应根据焊接材料的类型、规格和焊接件的要求进行。
一般来说,焊接厚度越大,焊丝直径越大。
7.焊接角度:焊接角度是指焊接枪与焊接面之间的夹角。
焊接角度的选择应根据焊接材料的类型、规格和焊接件的要求进行。
一般来说,焊接厚度越大,焊接角度越大。
以上是埋弧焊焊接参数选择和调整的一些基本内容。
埋弧焊工艺参数及焊接技术
埋弧焊工艺参数及焊接技术Last revision on 21 December 2020埋弧焊工艺参数及焊接技术1.3.1影响焊缝形状、性能的因素埋弧焊主要适用于平焊位置焊接,如果采用一定工装辅具也可以实现角焊和横焊位置的焊接。
埋弧焊时影响焊缝形状和性能的因素主要是焊接工艺参数、工艺条件等。
本节主要讨论平焊位置的情况。
(1) 焊接工艺参数的影响影响埋弧焊焊缝形状和尺寸的焊接工艺参数有焊接电流、电弧电压、焊接速度和焊丝直径等。
1)焊接电流当其他条件不变时,增加焊接电流对焊缝熔深的影响(如图1所示),无论是 Y 形坡口还是 I 形坡口,正常焊接条件下,熔深与焊接电流变化成正比,即状的影响,如图2所示。
电流小,熔深浅,余高和宽度不足;电流过大,熔深大,余高过大,易产生高温裂纹图1 焊接电流与熔深的关系(φ)图2 焊接电流对焊缝断面形状的影响a)I形接头b)Y形接头2)电弧电压电弧电压和电弧长度成正比,在相同的电弧电压和焊接电流时,如果选用的焊剂不同,电弧空间电场强度不同,则电弧长度不同。
如果其他条件不变,改变电弧电压对焊缝形状的影响如图3所示。
电弧电压低,熔深大,焊缝宽度窄,易产生热裂纹:电弧电压高时,焊缝宽度增加,余高不够。
埋弧焊时,电弧电压是依据焊接电流调整的,即一定焊接电流要保持一定的弧长才可能保证焊接电弧的稳定燃烧,所以电弧电压的变化范围是有限的图3电弧电压对焊缝断面形状的影响a)I形接头b)Y形接头3)焊接速度焊接速度对熔深和熔宽都有影响,通常焊接速度小,焊接熔池大,焊缝熔深和熔宽均较大,随着焊接速度增加,焊缝熔深和熔都将减小,即熔深和熔宽与焊接速度成反比,如图 4 所示。
焊接速度对焊缝断面形状的影响,如图 5 所示。
焊接速度过小,熔化金属量多,焊缝成形差:焊接速度较大时,熔化金属量不足,容易产生咬边。
实际焊接时,为了提高生产率,在增加焊接速度的同时必须加大电弧功率,才能保证焊缝质量。
图4 焊接速度对焊缝形成的影响H-熔深B-熔宽图5焊接速度对焊缝断面形状的影响a)I形接头b)Y形接头4)焊丝直径焊接电流、电弧电压、焊接速度一定时,焊丝直径不同,焊缝形状会发生变化。
- 1、下载文档前请自行甄别文档内容的完整性,平台不提供额外的编辑、内容补充、找答案等附加服务。
- 2、"仅部分预览"的文档,不可在线预览部分如存在完整性等问题,可反馈申请退款(可完整预览的文档不适用该条件!)。
- 3、如文档侵犯您的权益,请联系客服反馈,我们会尽快为您处理(人工客服工作时间:9:00-18:30)。
1.3埋弧焊工艺参数及焊接技术1. 3. 1??影响焊缝形状、性能的因素埋弧焊主要适用于平焊位置焊接,如果采用一定工装辅具也可以实现角焊和横焊位 置的焊接。
埋弧焊时影响焊缝形状和性能的因素主要是焊接工艺参数、工艺条件等。
本 节主要讨论平焊位置的情况。
(1)焊接工艺参数的影响 影响埋弧焊焊缝形状和尺寸的焊接工艺参数有焊接电流、 电弧电压、焊接速度和焊丝直径等。
1) 焊接电流 当其他条件不变时,增加焊接电流对焊缝熔深的影响(如图1所示),无 论是Y形坡口还是I 形坡口,正常焊接条件下,熔深与焊接电流变化成正比,即状的 影响,如图2所示。
电流小,熔深浅,余高和宽度不足;电流过大,熔深大,余高过大, 易产生咼温裂纹图2焊接电流对焊缝断面形状的影响a)I 形接头 b) Y 形接头2)电弧电压 电弧电压和电弧长度成正比,在相同的电弧电压和焊接电流时,如果 选用的焊剂不同, 电弧空间电场强度不同,则电弧长度不同。
如果其他条件不变,改变 电弧电压对焊缝形状的影响如图 3所示。
电弧电压低,熔深大,焊缝宽度窄,易产生热 裂纹:电弧电压高时,焊缝宽度增加,余高不够。
埋弧焊时,电弧电压是依据焊接电流 调整的,即一定焊接电流要保持一定的弧长才可能保证焊接电弧的稳定燃烧,所以电弧 电压的变化范围是有限的图3电弧电压对焊缝断面形状的影响a)I 形接头b) Y 形接头3) 焊接速度????旱接速度对熔深和熔宽都有影响,通常焊接速度小,焊接熔池大,焊缝熔深和熔宽均较大,随着焊接速度增加,焊缝熔深和熔都将减小,即熔深和熔宽与焊 接速度成反比,如图 4所示。
焊接速度对焊缝断面形状的影响,如图5所示。
焊接速图1焊接电流与熔深的关系(4.8mm )度过小,熔化金属量多,焊缝成形差:焊接速度较大时,熔化金属量不足,容易产生咬边。
实际焊接时,为了提高生产率,在增加焊接速度的同时必须加大电弧功率,才能保证焊缝质量。
图4焊接速度对焊缝形成的影响H—熔深E—熔宽图5 焊接速度对焊缝断面形状的影响a)l形接头b) Y形接头4) 焊丝直径???旱接电流、电弧电压、焊接速度一定时,焊丝直径不同,焊缝形状会发生变化。
表1所示的电流密度对焊缝形状尺寸的影响,从表中可见,其他条件不变,熔深与焊丝直径成反比关系,但这种关系随电流密度的增加而减弱,这是由于随着电流密度的增加,熔池熔化金属量不断增加,熔融金属后排困难,熔深增加较慢,并随着熔化金属量的增加,余高增加焊缝成形变差,所以埋弧焊时增加焊接电流的同时要增加电弧电压,以保证焊缝成形质量。
( U=30-32V,U w =33cm/ min)表1电流密度对焊缝形状尺寸的影响1) 对接坡口形状、间隙的影响???在其他条件相同时,增加坡口深度和宽度,焊缝熔深增加,熔宽略有减小,余高显着减小,如图6所示。
在对接焊缝中,如果改变间隙大小,也可以调整焊缝形状,同时板厚及散热条件对焊缝熔宽和余高也有显着影响,如表2所示。
2)焊丝倾角和工件斜度的影响??旱丝的倾斜方向分为前倾和后倾两种,见图7。
倾斜的方向和大小不同,电弧对熔池的吹力和热的作用就不同,对焊缝成形的影响也不同。
图7a为焊丝前倾,图7b为焊丝后倾。
焊丝在一定倾角内后倾时,电弧力后排熔池金属的作用减弱,熔池底部液体金属增厚,故熔深减小。
而电弧对熔池前方的母材预热作用加强,故熔宽增大。
图7c是后倾角对熔深、熔宽的影响。
实际工作中焊丝前倾只在某些特殊情况下使用,例如焊接小直径圆筒形工件的环缝等。
图7焊丝倾角对焊缝形成的影响a)前倾b)后倾c)焊丝后倾角度对焊缝形成的影响工件倾斜焊接时有上坡焊和下坡焊两种情况,它们对焊缝成形的影响明显不同,见图&上坡焊时(图8a、b),若斜度B角>?6°〜12°则焊缝余高过大,两侧出现咬边,成形明显恶化。
实际工作中应避免采用上坡焊。
下坡焊的效果与上坡焊相反,见图8c)、d)。
图8工件斜度对焊缝形成的影响a)上坡斜?b)上坡斜工件斜度的影响c)下坡斜d)下坡斜工件斜度的影响工件斜度3)焊剂堆高的影响埋弧焊焊剂堆高一般在25〜40mm,应保证在丝极周围埋住电弧。
当使用粘结焊剂或烧结焊剂时,由于密度小,焊剂堆高比熔炼焊剂高出20%〜50%。
焊剂堆咼越大,焊缝余咼越大,熔深越浅。
(3)焊接工艺条件对焊缝金属性能的影响当焊接条件变化时,母材的稀释率、焊剂熔化比率(焊剂熔化量/焊丝熔化量)均发生变化,从而对焊缝金属性能产生影响,其中焊接电流和电弧电压的影响较大。
图9〜图11给出了焊接电流、电弧电压和焊接速度对焊剂熔化比率的影响。
由于焊剂熔化比率的变化,焊缝金属的化学成分、力学性能均发生变化,特别是烧结焊剂中合金元素的加入对焊缝金属化学成分的影响最大。
图12〜图14给出各种焊接条件变化时对焊缝金属Mn、Si含量的影响。
图9焊接电流对焊剂熔化比率的影响图10电弧电压对焊剂熔化比率的影响图11焊接速度对焊剂熔化比率的影响图12焊接电流对焊缝金属化学成分的影响当板厚小于14mm ,可以不开坡口,装配时留有一定间隙:板厚为 14〜22mm ,— 般开V 形坡口;板厚22 -50mm 时开X 形坡口。
对于锅炉汽包等压力容器通常采用 U 形或双U 形坡口,以确保底层熔透和消除夹渣。
埋弧焊焊缝坡口的基本形式和尺寸设计时,请查阅 GB /T986〜1988。
坡口加工方法常采用刨边机和气割机,加工精度有一定要求。
2) 装配点固 埋弧焊要求接头间隙均匀无错边,装配时需根据不同板厚进行定间距、 定位焊,如表3所示。
另外直缝接头两端尚需加引弧板和熄弧板,以减少引弧和引出时 产生缺陷。
板厚t/mm 焊缝长度/mm 定位长度/mm <25 300 〜500 50 〜70 <25200 〜50070 〜1003) 焊前清理 坡口内水锈、夹杂铁末,点焊后放置时间较长而受潮氧化等焊接时容 易产生气孔,焊前需提高工件温度或用喷砂等方法进行处理。
(2) 对接接头单面焊 对接接头埋弧焊时,工件可以开坡口或不开坡口。
开坡口不仅 为了保证熔深,而且有时还为了达到其他的工艺目的。
如焊接合金钢时,可以控制熔合 比;而在焊接低碳钢时,可以控制焊缝余高等。
在不开坡口的情况下,埋弧焊可以一次 焊透20mm 以下的工件,但要120 110too90SO M a1电 3E-8S0A电 H :3QV卜A熔炼輝剂|O —MnL 亠-SiSi?05040 3020100 图13电弧电压对焊缝金属化学成分的影响图14焊接速度对焊缝金属化学成分的影响1.3.2埋弧焊实施方法及工艺参数选择(1)焊前准备1)坡口设计及加工 同其他焊接方法相比,埋弧焊接母材稀释率较大,母材成分对焊 缝性能影响较大,埋弧焊坡口设计必须考虑到这一点。
依据单丝埋弧焊使用电流范围,7050 1020 25 30 3545焊接 ilJB /cm min 4求预留5〜6mm的间隙,否则厚度超过14—16mm的板料必须开坡口才能用单面焊一次焊透。
对接接头单面焊可采用以下几种方法:在焊剂垫上焊,在焊剂铜垫板上焊,在永久性垫板或锁底接头上焊,以及在临时衬垫上焊和悬空焊等。
分述如下:在焊剂垫上焊接用这种方法焊接时,焊缝成形的质量主要取决于焊剂垫托力的大小和均匀与否,以及装配间隙的均匀与否。
图14说明焊剂垫托力与焊缝成形的关系。
板厚2〜8mm的对接接头在具有焊剂垫的电磁平台上焊接所用的参数列于表4。
电磁平台在焊接中起固定板料的作用。
图15在焊剂垫上对焊接a)焊接情况b)焊剂托力不足c)焊剂拖力很大d)焊剂拖力过大板厚10—20mm的I形坡口对接接头预留装配间隙并在焊剂垫上进行单面焊的焊接参数,见表5。
所用的焊剂垫应尽可能选用细颗粒焊剂。
在焊剂铜垫板上焊接这种方法采用带沟槽的铜垫板,沟槽中铺撒焊剂,焊接时,这部分焊剂起焊剂垫的作用,同时又保护铜垫板免受电弧直接作用。
沟槽起焊缝背面成形作用。
这种工艺对工件装配质量、垫板上焊剂托力均匀与否均不敏感。
板料可用电磁平台固定,也可用龙门压力架固定。
铜垫板的尺寸见图16和表6。
在龙门架焊剂铜垫板上的焊接参数见表7。
3)在永久性垫板或锁底接头上焊接当焊件结构允许焊后保留永久性垫板时,厚10mm以下的工件可采用永久性垫板单面焊方法。
永久性钢垫板的尺寸如表8所示。
垫板必须紧贴在待焊板缘上,垫板与工件板面间的间隙不得超过0.5〜1mm。
表8对接用的永久性钢垫板[1](单位:mm)| 6 〜10 (0.3 〜0.4 )S厚度大于10mm的工件,可采用锁底接头焊接方法,如图17所示(详见GB/T986-1988 )。
此法用于小直径厚壁圆筒形工件的环缝焊接,效果很好。
4)在临时性的衬垫上焊接这种方法采用柔性的热固化焊剂衬垫贴合在接缝背面进行焊接。
衬垫材料需要专门制造或由焊接材料制造部门供应。
另外还有采用陶瓷材料制造的衬垫进行单面焊的方法。
5)悬空焊当工件装配质量良好并且没有间隙的情况下,可以采用不加垫板的悬空焊。
用这种方法进行单面焊时,工件不能完全熔透。
一般的熔深不超过2/3板厚,否则容易烧穿。
这种方法只用于不要求完全焊透的接头。
(3)对接接头双面焊一般工件厚度从10〜40mm的对接接头,通常采用双面焊。
接头形式根据钢种、接头性能要求的不同,可采用图18所示的I形、丫形、X形坡口。
这种方法对焊接工艺参数的波动和工件装配质量都不敏感,其焊接技术关键是保证第一面焊的熔深和熔池的不流溢和不烧穿。
焊接第一面的实施方法有悬空法、加焊剂垫法以及利用薄钢带、石棉绳、石棉板等做成临时工艺垫板法进行焊接。
1)悬空焊装配时不留间隙或只留很小的间隙(一般不超过lmm)。
第一面焊接达到的熔深一般小于工件厚度的一半。
反面焊接的熔深要求达到工件厚度的60 %〜70 %,以保证工件完全焊透。
不开坡口的对接接头悬空焊的焊接参数,如表9所示2)在焊剂垫上焊接如图19所示,焊接第一面时采用预留间隙不开坡口的方法最为经济。
第一面的焊接参数应保证熔深超过工件厚度的60 %〜70 %。
焊完第一面后翻转工件,进行反面焊接,其参数可以与正面的相同以保证工件完全焊透。
预留间隙双面焊的焊接条件依工件的不同而异,表10a、b分别为两组数据,可供参考。
在预留间隙的重形坡口内,焊前均匀塞填干净焊剂,然后在焊剂垫上施焊,可减少产生夹渣的可能,并可改善焊缝成形。
第一面焊道焊接后,是否需要清根,视第一道焊缝的质量而^定。
图19焊剂垫的结构实例a)软管气压式b)皮膜气压式C )平带张紧式1 ――焊件4 ――充气软管7 ――气室2 ――焊剂5 ――橡皮膜8 ――平带3——帆布6——压板9——带轮表10a对接接头预留间隙双面焊的焊接条件①采用交流电,HJ431,第一面在焊剂焊剂垫上焊表10b对接接头预留间隙双面焊的焊接条件如果工件需要开坡口,坡口形式按工件厚度决定。