数控车床加工多头螺纹
数控车床上加工多头螺纹的方法

数控车床上加工多头螺纹的方法发表时间:2020-12-24T09:18:01.710Z 来源:《当代教育家》2020年31期作者:姚燕红袁石裕[导读] 双头螺纹是在轴向等距分布的螺旋线所形成的螺纹,多头螺纹每旋转一周时,螺母(或螺杆)能移动几倍的螺距,所以多头螺纹常用于快速移动的机构中。
杭州市萧山区第一中等职业学校摘要:本文介绍用分层斜进法在数控机床上切削公制多头梯形螺纹(牙型角30°)的编程、计算和切削方法,进一步对职业学校学生数控加工实训起到技能提高的效果。
关键语:数控车;多头梯形螺纹;程序;斜进法双头螺纹是在轴向等距分布的螺旋线所形成的螺纹,多头螺纹每旋转一周时,螺母(或螺杆)能移动几倍的螺距,所以多头螺纹常用于快速移动的机构中。
加工切削多头螺纹时,最主要的问题是解决螺纹的分头方法,如果分头出现误差,就会使切削的多头螺纹螺距不等,从而严重影响内外螺纹的配合精度,降低使用寿命,在普通机床上加工双头螺纹的方法有轴向分头法和圆周分头法两大类,但由于学生的操作水平有限及机床的细小误差,在普通机床上加工双头螺纹加工很难保证达到准确的分头,特别是三头螺纹以上的多头螺纹加工更为困难。
利用数控车床加工多头螺纹不但能达到准确、高精度的分头,而且在切削过程中采用斜进法,提高了生产率减少劳动时间,学生在操作编程中只要掌握方法——在程序段中Z轴方向移动一个螺距即可,从而减少了因分头误差所带来的加工困难。
一、数控车床上加工多头螺纹方法的选择当螺距P>4毫米时的双头梯形螺纹在数控车床上的切削方法通常有三种:1、左右切削法采用左右切削法是由于左右切削定位次数过多,其程序的段数也相当多,随着螺距越大,其程序段数也越多,学生在编辑过程中数据容易混淆和输入繁琐。
2、切槽法用车槽法,则要多安装一把切槽刀,计算每次切削深度,最主要的是用切槽刀切削后,梯形车刀的定样难以确定,对于基本功不扎实的同学,会更加困难。
3、分层斜进法如果改用分层斜进法时,在每次往复行程后,只需改变一个Z轴方向值,而且编程和计算简单快捷,不仅适用于所有学生,且节约时间,提高了上课效率。
使用数控车床加工多头螺纹的方法
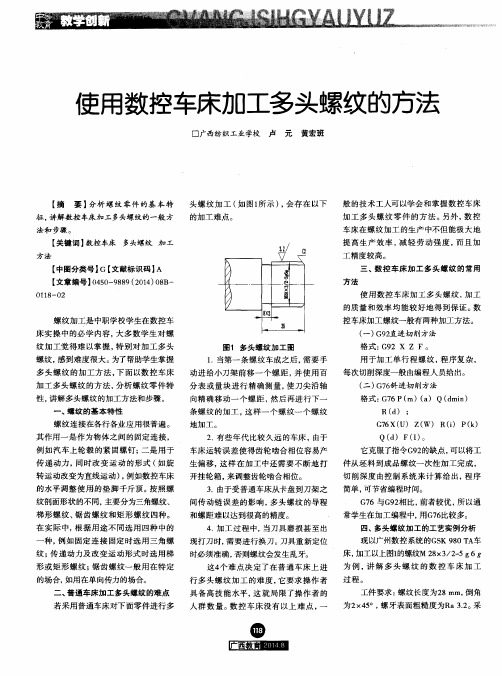
动进 给小刀架前 移 一个 螺 距 , 并 使 用 百
分 表或 量块 进行 精 确测量 , 使刀 尖沿轴
向精 确移 动一 个 螺距 , 然 后再进 行下 一 条螺 纹 的加工 , 这样 一 个螺 纹一个 螺 纹
地加工 。
、
螺 纹 的 基 本 特 性
螺 纹连 接在各行各业应 用很普遍 。
【 中图分类号】 G【 文献标识码】 A
【 文章编号 】 0 4 5 0 — 9 8 8 9 ( 2 0 1 4 ) 0 8 B 一
01 1 8—02
萋
×
蚕
8  ̄ 2
使用 数控 车床加 工 多头螺 纹 , 加 工
的质 量和 效率 均 能较 好地得 到保证 。 数
螺 纹加工是 中职 学校学生在数 控车 床实操 中的必 学 内容 , 大 多 数学 生对 螺
床, 加工 以上图1 的螺纹M 2 8 x 3 / 2 - 5 g 6 g
这4 个 难 点决 定 了在 普通 车床 上 进
行 多头 螺纹 加 工 的难度 , 它要 求操 作 者
为例 , 讲 解 多 头 螺 纹 的数 控 车 床 加 工
过程。
具 备高 技 能水平 , 这 就局 限 了操 作者 的
3 /2 的已知参 数 : 螺 纹 的公 称直径d= 2 8 mm, 导程 为L= 3 1 T I I T I , 螺距 P=1 . 5 mm,
头数 n = 2 mm。
性, 讲 解多头螺纹 的加工方法和步骤 。
一
1 .当第 一条 螺纹 车成之 后, 需要 手
用于 加工单 行程 螺 纹 程 人员给 出。
( 二) G7 6 斜 进 切 削 方 法 格式 : G 7 6 P( m)( a )Q( d ai r n ) R( d ); G7 6 X( U) Z( W ) R( i )P ( k ) Q( d ) F( I ) 。
大直径大导程多头梯形内螺纹的数控加工

!" #$%&’()(*+
大直径大导程多头梯形内螺纹的数控加工
郝宏伟
( 河北工业职业技术学院, 河北 石家庄 !"!!#$)
摘 要 ! 介绍了采用数控化改造的 !"#$#% 立车设备,加工大直径零件上的大导程多头梯形左旋内螺纹的加工方法。 阐述了螺纹车刀的选用、 螺纹分度法的确定、 螺纹加工工艺的确定、 螺纹的数控加工程序, 以及叶轮硬化后使用轴头螺 纹规修螺纹的方法。利用该数控加工方法加工叶轮上的螺纹, 既能够保证螺纹的加工精度, 又可以减少刀具重磨和重定 位次数, 缩短辅助时间, 提高生产效率。 关键词 !大直径; 大导程; 多头内螺纹; 数控加工 , %$$(& $)&$$*)&$$ 中图分类号 !!&’#( 文献标识码 !" 文章编号 !#$$%&%’’’
/%$ 01# /#$ 0$ 234$,$ 5367 /4$ 6%3$ 643# 6#3&%$ 613%$ 6&3&$ 683%1 6738,7 /9$ 0$ 23$ 53$ /1$ 0$ 53:;<(6#= /&$ 0$ 236% /8$ )%%%$$$4 ’364 /7$ 0$ 23 (4$,$ />$ 0$ 53$ /%$$ -9$ ?@A
! !"
加工程序 利用周向分度法基本原理进行分度 ! 运用斜向单面
683(%1 673 (7,1’&6%3%$ 673 (8,%&’’ 6%34$ 673(1,74 ’ (6%39$ 6434# 673 (#,#7 (
再次 ! 使用若干次循环 ! 分别对上 ) 下面光刀 ! 直至轴 头螺纹规下去为止 !并预留出螺纹硬化变形收缩量 " 6%3$
数控车加工多线螺纹的方法

随着机械行业的快速发展,对各种零件的螺纹精度和加工效率提出了更高的要求。
多线螺纹是螺纹加工中常见的一种,可以成倍提高传动效率,传统制造中利用普通车床加工多线螺纹,由于效率低、精度差以及劳动强度高等弊端,逐渐被数控加工所取代。
螺纹的加工原理螺纹的加工是靠刀具的移动与主轴回转同步运动来实现的,装在数控机床主轴上的位置编码器实时读取主轴的转速,并转换为刀具的进给速度。
通常,螺纹的切削是沿着同样的刀具轨迹从粗切到精切重复进行,因为螺纹切削是在主轴上的位置编码器输出一转信号时开始的,所以螺纹切削是从固定点开始且刀具在工件上的切削轨迹不变。
多线螺纹的分线方法多线螺纹是在普通螺纹的基础上增加分线的工序,常采用的有轴向分线法和圆周角度分线法。
轴向分线法是在车好一条螺旋线之后,把车刀沿螺纹轴线方向移动一个螺距再车第二条螺旋槽,这种方法适合主轴上没有安装位置检测装置的机床,它适合加工一些起始点在工件的任何一侧而不是中部的螺纹,否则可能会发生刀具与工件干涉。
圆周角度分线法是根据螺旋线在圆周上等距分布的特点,利用等分圆周角度来分线。
采用圆周角度分线法需要机床主轴具有分度功能,但在加工过程中不受任何限制,这种方法对于一些有特殊要求的螺纹更为实用。
实例验证以加工如下图所示产品外表面6线矩形螺纹为例,用两种方法来说明在数控车床上是如何加工多线螺纹的。
工件的6线矩形螺纹首先,分析该工件螺纹为6线矩形螺纹,螺纹的起始点在工件的中间部位,如果采用轴向分线法,两端的退刀槽都没有足够的刀具移动空间,轴向移动螺纹起点必然造成刀尖与工件干涉。
因此,选用圆周角度分线法,该螺纹为6条螺旋线,分线角度为360°/6=60°。
选用与螺旋槽相同宽度且带有螺旋升角的矩形螺纹刀,以减少刀具与工件的切削抗力。
螺旋升角的计算公式为:tanψ=nP/πd 2 ,其中ψ为螺纹升角,nP为螺纹导程(n为螺纹线数,P为螺距),d 2 为中径。
(1)此程序利用机床螺纹加工指令G32,并由宏指令控制加工该6线螺纹(FANUC 0i系统):G54 工件坐标系选择G28 U0 W0 返回原点(换刀点)T0101 选刀S50 M03 主轴50r/min,正转M08 冷却开N10 #1=0 为变量赋初值N20 #2=68 为变量赋初值N30 G00 Z-31 到螺纹起刀点X#2G32 Z-121 F44 Q#1 螺纹切削指令,Q为螺纹起始角度值,单位为0.001°G00 X70 退刀#2=#2-0.1 切削以每次0.1mm为吃刀量IF[#2 GE 64.5] GOTO30 如果变量值≥64.5,则跳到N30句,否则向下#1=#1+60000 变量以60°递增(分线角度为60°)IF[#1 LT 360000] GOTO20 如果变量值<360°,跳到N20句,否则向下G28 U0 W0 返回原点(换刀点)M05 主轴停转M09 冷却关M30 程序结束并返回(2)此程序为车削中心利用C轴与Z轴两轴联动插补功能,采用圆柱坐标编程,并由宏指令控制加工该6线螺纹:G54 工件坐标系选择G28 U0 W0 返回原点(换刀点)T0101 选刀M43 启动C轴功能G00 C0 C轴定位0°M08 冷却开N10 #1=0 为变量赋初值N20 #2=68 为变量赋初值N30 G00 C#1 到螺纹起刀点X#2G01 G98 Z-122 H-744.545 F1200 H为C的增量地址,利用Z、C轴联动加工,进给速度1 200mm/minG00 X70 退刀Z-31#2=#2-0.1 切削以每次0.1mm为吃刀量IF[#2 GE 64.5] GOTO30 如果变量值≥64.5,则跳到N30句,否则向下#1=#1+60 变量以60°递增(分线角度为60°)IF[#1 LT 360] GOTO20 如果变量值<360°,跳到N20句执行,否则向下G28 U0 W0 返回原点(换刀点)M40 C轴功能取消M09 冷却关M30 程序结束并返回其中C轴所转角度计算如下:H=(螺纹起始点与终止点的距离/螺纹导程)×360°。
数控车教学中多头螺纹加工方法的探究

用西门子数控立车加工大导程多头螺纹数控编程
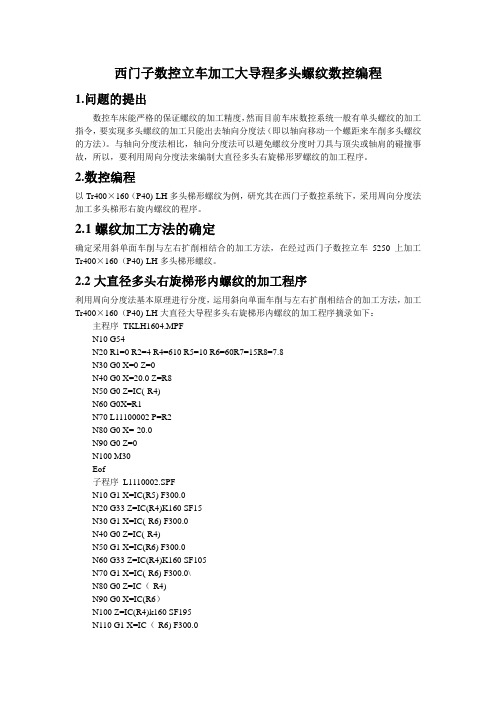
西门子数控立车加工大导程多头螺纹数控编程1.问题的提出数控车床能严格的保证螺纹的加工精度,然而目前车床数控系统一般有单头螺纹的加工指令,要实现多头螺纹的加工只能出去轴向分度法(即以轴向移动一个螺距来车削多头螺纹的方法)。
与轴向分度法相比,轴向分度法可以避免螺纹分度时刀具与顶尖或轴肩的碰撞事故,所以,要利用周向分度法来编制大直径多头右旋梯形罗螺纹的加工程序。
2.数控编程以Tr400×160(P40)-LH多头梯形螺纹为例,研究其在西门子数控系统下,采用周向分度法加工多头梯形右旋内螺纹的程序。
2.1螺纹加工方法的确定确定采用斜单面车削与左右扩削相结合的加工方法,在经过西门子数控立车5250上加工Tr400×160(P40)-LH多头梯形螺纹。
2.2大直径多头右旋梯形内螺纹的加工程序利用周向分度法基本原理进行分度,运用斜向单面车削与左右扩削相结合的加工方法,加工Tr400×160(P40)-LH大直径大导程多头右旋梯形内螺纹的加工程序摘录如下:主程序TKLH1604.MPFN10 G54N20 R1=0 R2=4 R4=610 R5=10 R6=60R7=15R8=7.8N30 G0 X=0 Z=0N40 G0 X=20.0 Z=R8N50 G0 Z=IC(-R4)N60 G0X=R1N70 L11100002 P=R2N80 G0 X=-20.0N90 G0 Z=0N100 M30Eof子程序L1110002.SPFN10 G1 X=IC(R5) F300.0N20 G33 Z=IC(R4)K160 SF15N30 G1 X=IC(-R6) F300.0N40 G0 Z=IC(-R4)N50 G1 X=IC(R6) F300.0N60 G33 Z=IC(R4)K160 SF105N70 G1 X=IC(-R6) F300.0\N80 G0 Z=IC(-R4)N90 G0 X=IC(R6)N100 Z=IC(R4)k160 SF195N110 G1 X=IC(-R6) F300.0N120 G0 Z=IC(-R4)N130 G0 Z=IC(R6)N140 G33 Z=IC(R4)k160 SF285N150 G1 X=IC(-R6) F300.0N160 R4=R4+R5*TAN(R7)/2N170 G0 Z=IC(-R4)N180 G0 X=IC(R6)N190 RET其中:R1:X轴定位点(直径量);R2:车削次数,即子程序调用次数;R4:起刀点;R5:每次吃刀深度;R6:退刀距离;R7:刀具角度(15度为牙型上面,-15度为牙型下面);R8:Z轴定位点。
多头螺纹编程实例
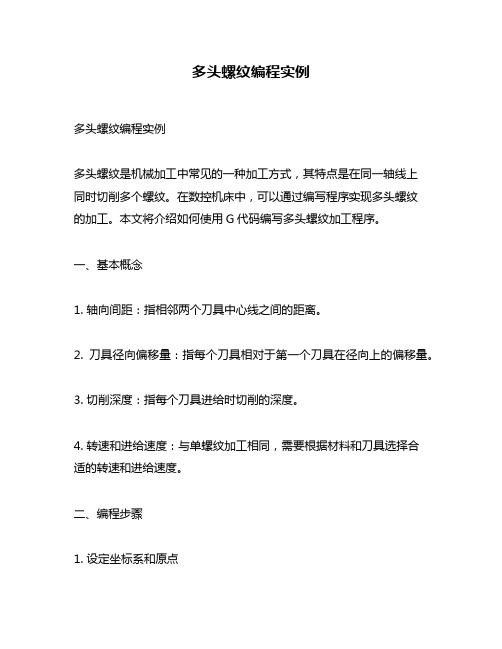
多头螺纹编程实例多头螺纹编程实例多头螺纹是机械加工中常见的一种加工方式,其特点是在同一轴线上同时切削多个螺纹。
在数控机床中,可以通过编写程序实现多头螺纹的加工。
本文将介绍如何使用G代码编写多头螺纹加工程序。
一、基本概念1. 轴向间距:指相邻两个刀具中心线之间的距离。
2. 刀具径向偏移量:指每个刀具相对于第一个刀具在径向上的偏移量。
3. 切削深度:指每个刀具进给时切削的深度。
4. 转速和进给速度:与单螺纹加工相同,需要根据材料和刀具选择合适的转速和进给速度。
二、编程步骤1. 设定坐标系和原点首先需要设定坐标系和原点。
通常情况下,选择X轴为主轴,设定X 轴为机床坐标系下的正方向,并将第一个刀具的圆心作为原点。
2. 设定参数设定轴向间距、刀具径向偏移量、切削深度等参数。
根据实际情况选择合适的数值。
3. 编写程序在编写程序时,需要考虑多个刀具同时切削的情况。
可以使用G76指令实现多头螺纹加工。
G76指令的格式如下:G76 X_ Z_ P_ Q_ R_ K_其中X、Z分别为第一个刀具的坐标;P为每个螺纹的轴向距离;Q为每个刀具在径向上的偏移量;R为每个刀具进给时切削的深度;K为螺纹类型,通常选择1。
例如,设定轴向间距为2mm,刀具径向偏移量为0.5mm,切削深度为0.2mm,则可以编写如下程序:N10 G90 G54 G96 S1000 M3N20 T01 M6N30 G00 X0 Z0N40 G01 Z-5 F200N50 G76 X10 Z-5 P2 Q0.5 R0.2 K1N60 M5 M9 M304. 调试程序在编写完成程序后,需要进行调试。
可以使用模拟器或手动模拟进行调试。
注意检查每个刀具的进给方向和深度是否正确。
三、注意事项1. 切勿让不同刀具之间相互干涉。
2. 切勿让刀具切削过深,以免造成机床震动和刀具破裂。
3. 切勿让刀具与工件相撞。
4. 在编写程序时,应根据实际情况选择合适的参数和加工方式。
凯恩帝双头梯形螺纹编程实例
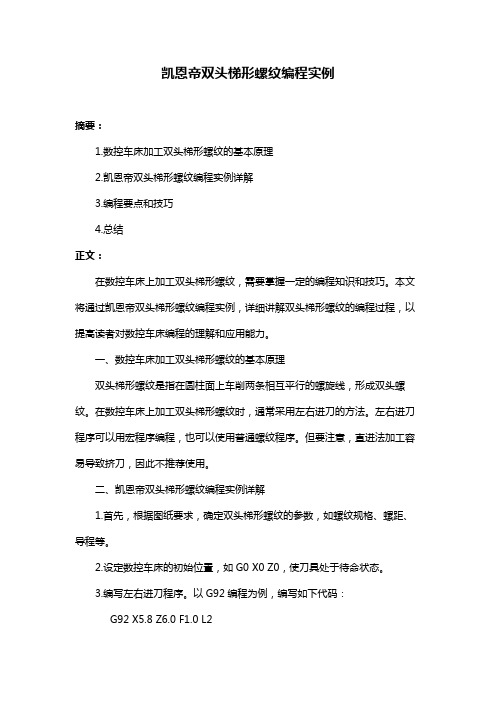
凯恩帝双头梯形螺纹编程实例摘要:1.数控车床加工双头梯形螺纹的基本原理2.凯恩帝双头梯形螺纹编程实例详解3.编程要点和技巧4.总结正文:在数控车床上加工双头梯形螺纹,需要掌握一定的编程知识和技巧。
本文将通过凯恩帝双头梯形螺纹编程实例,详细讲解双头梯形螺纹的编程过程,以提高读者对数控车床编程的理解和应用能力。
一、数控车床加工双头梯形螺纹的基本原理双头梯形螺纹是指在圆柱面上车削两条相互平行的螺旋线,形成双头螺纹。
在数控车床上加工双头梯形螺纹时,通常采用左右进刀的方法。
左右进刀程序可以用宏程序编程,也可以使用普通螺纹程序。
但要注意,直进法加工容易导致挤刀,因此不推荐使用。
二、凯恩帝双头梯形螺纹编程实例详解1.首先,根据图纸要求,确定双头梯形螺纹的参数,如螺纹规格、螺距、导程等。
2.设定数控车床的初始位置,如G0 X0 Z0,使刀具处于待命状态。
3.编写左右进刀程序。
以G92编程为例,编写如下代码:G92 X5.8 Z6.0 F1.0 L2其中,X5.8表示初始位置,Z6.0表示加工深度,F1.0表示进给速度,L2表示螺纹长度。
4.编写左螺纹加工程序。
以G76编程为例,编写如下代码:G76 P(m)(r)(a) Q(dmin) R(d)G76 X(u) Z(w) R(i) P(k) Q(d) F(f)其中,m表示螺纹类型(双头),r表示刀尖半径,a表示左右进刀角度,dmin表示最小切削直径,d表示梯形螺纹槽底直径,i表示刀具补偿,k 表示下一刀的初始位置,f表示进给速度。
5.编写右螺纹加工程序。
与左螺纹加工程序类似,只需将G76编程中的m 值改为双头,并调整相应的参数即可。
6.结束加工,编写如下代码:M30三、编程要点和技巧1.刀尖宽度要小于梯形螺纹槽底的宽度,以保证左右进刀余量。
2.左右进刀时,注意调整刀具的初始位置和角度,避免切削过程中出现刀具碰撞。
3.加工双头梯形螺纹时,可采用G92编程方法,简化编程过程。
- 1、下载文档前请自行甄别文档内容的完整性,平台不提供额外的编辑、内容补充、找答案等附加服务。
- 2、"仅部分预览"的文档,不可在线预览部分如存在完整性等问题,可反馈申请退款(可完整预览的文档不适用该条件!)。
- 3、如文档侵犯您的权益,请联系客服反馈,我们会尽快为您处理(人工客服工作时间:9:00-18:30)。
数控车床加工多头螺纹
摘要:数控车床主要用来加工盘类或轴类零件,利用数控车床加工多头螺纹,能大大提高生产效率,保证螺纹加工精度,减轻操作者的劳动强度。
我通过多年的实践经验,对多头螺纹的加工要点和操作要领进行了总结,为多头螺纹的数控加工提供了理论依据。
关键词:数控车床多头螺纹编程
在普通车床上进行多头螺纹车削一直是一个加工难点:当第一条螺纹车成之后,需要手动进给小刀架并用百分表校正,使刀尖沿轴向精确移动一个螺距再加工第二条螺纹;或者打开挂轮箱,调整齿轮啮合相位,再依次加工其余各头螺纹。
受普通车床丝杠螺距误差、挂轮箱传动误差、小拖板移动误差等多方面的影响,多头螺纹的导程和螺距难以达到很高的精度。
而且,在整个加工过程中,不可避免地存在刀具磨损甚至打刀等问题,一旦换刀,新刀必须精确定位在未完成的那条螺纹线上。
这一切都要求操作者具备丰富的经验和高超的技能。
然而,在批量生产中,单靠操作者的个人经验和技能是不能保证生产效率和产品质量的。
在制造业现代化的今天,高精度数控机床和高性能数控系统的应用使许多普通机床和传统工艺难以控制的精度变得容易实现,而且生产效率和产品质量也得到了很大程度的保证。
下面我将从四个方面对数控车床加工多头螺纹进行分析:
一、螺纹的基本特征
在机械制造中,螺纹联接被广泛应用,例如数控车床的的主轴与卡盘的联结,方刀架上螺钉对刀具的紧固,丝杠螺母的传动等。
圆柱或圆锥母体表面上制出的螺旋线形的、具有特定截面的连续凸起部分。
螺纹按其母体形状分为圆柱螺纹和圆锥螺纹;按其在母体所处位置分为外螺纹、内螺纹,按其截面形状(牙型)分为三角形螺纹、矩形螺纹、梯形螺纹、锯齿形螺纹及其他特殊形状螺纹,三角形螺纹主要用于联接,矩形、梯形和锯齿形螺纹主要用于传动;按螺旋线方向分为左旋螺纹和右旋螺纹,一般用右旋螺纹;按螺旋线的数量分为单线螺纹、双线螺纹及多线螺纹;联接用的多为单线,传动用的采用双线或多线;按牙的大小分为粗牙螺纹和细牙螺纹等,按使用场合和功能不同,可分为紧固螺纹、管螺纹、传动螺纹、专用螺纹等。
由于用途不同,它们的技术要求和加工方法也不一样
二、螺纹的加工方法
(一)螺纹的加工方法
随着制造技术的发展,螺纹的加工,除采用普通机床加工外,常采用数控机床加工。
这样既能减轻加工螺纹的难度又能提高工作效率,并且能保证螺纹加工质量。
在目前的数控车床中,螺纹切削一般有三种方法:
(1)直进法
易获得较准确的牙型,但切削力较大,常用于螺距小于3mm的三角形螺纹。
加工方法是在加工过程中对刀具的z轴(轴向方向)不进行改变,分次进给(直径方向),来完成螺纹的切削。
(2)斜进法
在每次往复行程后,除了做横向进刀以外,只在纵向的一个方向微量进给。
(3)左右切削法
在每次往复行程后,除了做横向进刀外,还需要向左或向右微量进给。
对于加工大螺距的螺纹,多头螺纹等零件,由于加工面太宽,接触面大。
用直进法,对于机床、具和工件都会产生很大的影响,甚至打刀、飞活和蒙车等现象,所以,只有采取左右车削法来完成。
加工方法是通过改变z轴的的方向,也是进刀的起始点,来完成对螺纹一个侧面的加工,完了再加工另外一个侧面,最后对两侧面和底面进行修光,这种方法叫做左右进刀法,注意是一个侧面一个侧面的加工,这样以减小刀具和工件的接触面积,作用是扩槽。
可一刀左,下一刀右的方法加工。
(二)多头螺纹加工的控制
在运用程序加工螺纹时,要注意对以下问题的控制:
(1)切削用量的确定。
螺纹加工要求主轴转速和刀具的进给速度之间保持严格的速比关系。
即主轴每转一转,刀具应均匀地移动一个导程的距离。
由于一般螺距远大于车外圆时的每转进给值,所以主轴转速不可随意,主轴转速S与F值的乘积不得大于轴向进给限制值。
在车削螺纹时,车床的主轴转速将受到螺纹的螺距大小,驱动电机的升降频特性,以及螺纹插补运算速度等多种因素影响,不同的数控系统,推荐的主轴转速选择范围也不同。
所以,编程时应按照数控车床操作说明书所规定的主轴转速车削螺纹。
由于x 轴、z 轴加减速难以完全一致,会使螺距产生误差,因此,螺纹切削时不可进行主轴转速调整,以防车出不完全螺纹。
更不要停止主轴,主轴停止将可能导致刀具和工件损坏。
另一方面,刀具切削部分在螺纹加工时的工作条件是非常恶劣的,不仅切削力大,而且摩擦剧烈,发热严重,刀具材料本身对切削线速度也有一定的限制。
一般尺寸的螺纹加工,主轴转速S 控制在60~ 200 r/m in即可。
特殊大尺寸螺纹,有必要验算线速度,这里不再赘述。
(2)表面粗糙度要求
螺纹加工的最后一刀基本采用重复切削的方法,这样可以获得更光滑的牙表面,达到粗
(3)批量加工过程控制
对试件切削运行程序之前除正常要求对刀外,在数控系统中要设定刀具磨损值,第一次加工完后用螺纹千分尺进行精密测量并记录数据,将磨损值相应减少,进行第二次自动加工,并将测量数据记录,以后将磨损补偿值的递减幅度减少并观察它的减幅与中径的减幅的关系,重复进行,直至将中径尺寸调试到公差带的中心为止。
在以后的批量加工中,尺寸的变化可以用螺纹环规抽检,并通过更改程序中x数据,也可以通过调整刀具磨损值进行补偿。
(4)螺纹外径控制
由于外螺纹多数为塑性材料,需考虑螺纹加工牙型的膨胀量。
一般连接螺纹加工前的工件直径等于螺纹公称直径减去0.1 P,即螺纹大径减0.1倍螺距,一般根据材料变形能力大小取比螺纹大径小0.1~ 0.5 mm。
三、螺纹的编程方法
当前主流数控系统( FANUC 、GSK 等) 提供了单一螺纹加工指令G32 、攻丝循环指令G33、变螺距螺纹加工指令G34和螺纹固定循环加工指令G92、G76. 小螺距螺纹加工时宜用G32或G92,大螺距螺纹加工时宜用G76,变螺距螺纹用G34; 加工高精度小螺距螺纹宜用G32、G92;加工高精度、大螺距螺纹时可采用G92、G76混合编程,先用G76 粗加工,再用G92 精加工; 轴向小直径内螺纹可以用G33编程。
在实际编程和加工中要根据螺纹精度、尺寸、材质等因素合理选择、灵活使用以上4种指令。
在保证技术要求的前提下,努力简化程序,提高编程和加工效率。
具体指令的应用我们只要按照机床编程说明书的要求完成相应零件的编程就可以了。
我们也可以不用什么专用的指令。
不管是什么数控系统,都用一种方法来解决:即只要保证加工第二条螺旋线的起点跟加工第一条螺旋线的起点在Z方向相差一个螺距就行来,如加工3,4,5,6……线道理也是一样的,下面我们来举例说明。
例:公称直径30,导程4,双头螺纹。
编程如下:
G00 X35 Z5(第一条螺旋线的起点)
G76 (加工第一条螺旋线。
注意:F值为导程,牙型高的计算是以螺距计算的。
)
G00 X35 Z7 (后移一个螺距,第二条螺旋线的起点。
前移和后移都可以,安全起见一般后移)
G76(加工第二条螺旋线)
G00 X100 Z200
四、多头螺纹加工的注意事项
数控车床加工螺纹时,程序可以通过试车调整得到优化,其中常出现的问题是刀具磨损和打刀。
为了提高刀具的使用寿命,保证螺纹的加工精度,应注意以下几点:
(1)在数控机床上车削多线螺纹的关键是分线要准确,其工艺、刀具方面与普通机床基本相同。
在车螺纹前精车外圆工序,应保证一定的尺寸精度、圆度、圆柱度和表面粗糙度,以保证加工余量均匀,车削平稳。
(2)每次进给量可以凭经验选取不用查表,这里应注意车螺纹时,螺纹底径应车削到的尺寸。
走刀进行中,不能改变主轴转速倍率开关。
(3)应保持良好的冷却和润滑。
(4)车削低碳钢、不锈钢等材料时,会出现不易断屑的长条状切屑,应防止其卷入车刀和工件之间,使刀尖受挤压断裂。
操作者必须注意人身安全。
(5)在实际加工中,发生过因为打刀而使刀片而后刀体一起损坏的情况,所以有必要增加一个刀位作为备用。
需要注意:在对刀时必须保证这两个刀位上螺纹刀刀尖点坐标一致以
综上所述,多头螺纹的加工只有掌握好其工艺参数,熟悉其控制因素,方能做好多头螺纹。
同时数控技术的发展是与现代计算机技术、电子技术发展同步的,同时也是根据生产发展的需要而发展的。
现在数控技术已经成熟,发展将更深更广更快。
未来的CNC系统将会使机械更好用,更便宜。
参考文献
1.刘洪数控设备与编程机械工业出版社2006
2.王林数控车编程与操作北京邮电出版社2008
.。