压力容器焊接工艺说明书
钢制压力容器焊接规程 JBT 4709-92

中华人民共和国行业标准钢制压力容器焊接规程JB/T 4709-921 主题内容与适用范围本标准规定了钢制压力容器焊接的基本要求.本标准适用于焊接、手弧焊、埋弧焊、气体保护焊、电渣焊焊接的钢制压力容器.2 焊接材料2.1 焊接材料包括焊条、焊丝、焊剂、气体保护焊、电渣焊焊接的钢制压力容器.2.2 焊接材料选用原则应根据母材的化学成分、力学性能、焊接性能结合压力容器的结构特点和使用条件综合考虑选用焊接材料,必要时通过试验确定.焊缝金属的性能应高于或等于相应母材标准规定值的下限或满足图样规定的技术要求.对各类钢的焊缝金属要求如下:2.2.1 相同钢号相焊的焊缝金属2.2.1.1 碳素钢、碳锰低合金钢的焊缝金属应保证力学性能,且需控制抗拉度上限.2.2.1.2 相低合金钢的焊缝金属应保证化学成分和力学性能,且需控制抗拉强度上限.2.2.1.3 低温用低合金钢的焊缝金属应保证力学性能,特别应保证夏比(V型)低温冲击韧性.2.2.1.4 高合金钢的焊缝金属应保证力学性能和耐腐蚀性能.2.2.1.5 不锈钢复合钢板基层的焊缝金属应保证力学性能,且需控制抗拉强度的上限;复层的焊缝金属应保证耐腐蚀性能,当有力学性能要求时还应保证力学性能.复层焊缝与基层焊缝,以及复层焊缝与基层钢板交界处推荐采用过渡层. 2.2.2 不同钢号相焊的焊缝金属2.2.2.1 不同钢号的碳素钢、低合金钢之间的焊缝金属应保证力学性能.推荐采用与强度级别较低的母材相匹配的焊接材料.2.2.2.2 碳素钢、低合金钢与奥氏体高合金钢之间的焊缝金属应保证抗裂性能.推荐采用铬镍含量较奥氏体高合金钢母材高的焊接材料.2.3 焊接材料必须有产品质量证明书,并符合相应标准的规定,且满足图样的技术要求,进厂时按有关质保体系规定验收或复验,合格手方准使用.2.4 常用钢号推荐选用的焊接材料见表1,不同钢号相焊推荐选用的焊接材料见表2.3 焊接工艺评定和焊工3.1 施焊下列各类焊缝的焊接工艺必须按JB4708-92《钢制压力容器焊接工艺评定》标准评定合格.a. 受压元件焊缝;b. 与受压元件相焊的焊缝;c. 上述焊缝的定位焊缝;d. 受压元件母材表面堆焊、补焊.3.2 施焊下列各类焊缝的焊工必须按原劳动人事部颁发的《锅炉压力容器焊工考试规则》规定考试合格.a. 受压元件焊缝;b. 与受压元件相焊的焊缝;c. 熔入永久焊缝内的定位焊缝;d. 受压元件母材表面耐蚀层堆焊.4 焊前准备4.1 焊接坡口焊接坡口应根据图样要求或工艺条件选用标准坡口或自行设计.选择坡口形式和尺寸应考虑下列因素:a. 焊缝填充金属尽量少;b. 避免产生缺陷;c. 减少残余焊接变形与应力;d. 有利于焊接防护;e. 焊工操作方便;f. 复合钢板的坡口应有利于减少过渡层焊缝金属的稀释率.4.2 坡口置备4.2.1 碳素钢和标准抗拉强度不大于540MPa的碳锰低合金钢可采用冷加工,也可采用热加工方法置备坡口.4.2.2 标准抗拉强度大于540MPa的碳锰低合金钢、铬钼低合金钢和高合金钢宜采用冷加工法.若采用热加工方法,对影响焊接质量的表面层,应用冷加工方法去除.4.3 焊接坡口应保持平整,不得有裂纹、分层、夹渣等缺陷,尺寸应符合图样规定.4.4 坡口表面及两侧(手弧焊各10mm,埋弧焊、气体保护焊各20mm,电渣焊各40mm)应将水、铁锈、油污、积渣和其它有害杂质清理干净.4.5 奥氏体高合金钢坡口丙侧各100 mm范围内应刷涂料,以防止沾附焊接飞溅.4.6 焊条、焊剂按规定烘干、保温;焊丝需去除油、锈;保护气体应保持干燥. 4.7 预热4.7.1 根据母材的化学成分、焊接性能、厚度、焊接接头的拘束程度、焊接方法和焊接环境等综合考虑是否预热,必要时通过试验确定.常用钢号推荐的预热温度见表3.4.7.2 不同钢号相焊时,预热温度按预热温度要求较高的钢号选取.4.7.3 采取局部预热时,应防止局部应力过大.预热的范围为焊缝两侧各不小于焊件厚度的3倍,且不小于100 mm.4.7.4 需要预热的焊件在整个焊过程中应不低于预热温度.4.7.5 当用热加工法下料、开坡口、清根、开槽或施焊临时焊缝时,亦需考虑预热要求.4.8 焊接设备等应处于正常工作状态,安全可靠,仪表应定期校验.4.9 定位焊4.9.1 焊接接头拘束度大时,推荐采用低氢型药皮焊条施焊.4.9.2 定位焊缝不得有裂纹,否则必须清除重焊.如存在气孔、夹渣时亦应去除.4.9.3 熔入永久焊缝内的定位焊缝两应便于接弧,否则应予修整.4.10 避免强行组装,组装后接头需经检验合格, 方可施焊.5 焊接要求5.1 焊工必须按图样、工艺文件、技术标准施焊.5.2 焊接环境5.2.1 焊接环境出现下列任一情况时,须采取有效防护措施,否则禁止施焊.a. 风速:气体保护焊时大于2m/s,其它焊接方法大于10 m/s;b. 相对湿度大于90%;c. 雨雪环境;d. 焊件温度低于-20℃.5.2.2 当焊件温度为0~-20℃时,应在始焊处100mm范围内预热到15℃以上.5.3 应在引弧板或坡口内引弧,禁止在非焊接部位引弧.焊缝应在引出版上收弧,弧坑应填满.5.4 防止地线、电缆线、焊钳与焊件打弧.5.5 电弧擦伤处的弧坑需经打磨,使基均匀过渡到母材表面,若打磨后的母材厚度小于规定值时,则需补焊.5.6 受压元件的角焊缝的根部应保证焊透.5.7 双面焊须清理焊根,显露出正底的焊缝金属.对于自动焊,若经试验确认能保证焊透,亦可不作清根处理.5.8 接弧处应保证焊透与熔合.5.9 施焊过程中应控制层间温度不超过规定的范围.当焊件预热时,应控制层间温度不得低于预热温度.5.10 每条焊缝应尽可能一次焊完.当中断焊拉旮,对冷却纹敏感的焊件应及时采取后热、缓冷等措施.重新施焊时,仍需按规定进行预热.5.11 采用锤击改善焊接质量时,第一层焊缝和盖面焊缝不宜锤击.5.12 引弧板、引出板、产品焊接试板和焊接工艺纪律检查试板不应锤击打落.6 后热6.1 对冷裂纹敏感性较大的低合金钢和拘束度较大的焊件应采取后热措施. 6.2 后热应在焊后立即进行.6.3 后热温度一般为200~350℃,保温时间可参照表4回火最短保温时间的规定.6.4 若焊后立即进行热处理可不作后热.7 焊后热处理7.1 根据母材的化学成分、焊接性能、厚度、焊接接头的拘束程度、容器使用条件和有关标准综合确定是否需要进行焊后热处理.7.2 常用钢号推荐的焊后热处理规范见表4.7.2.1 调质钢焊后热处理应低于调质处理时的回火温度.7.2.2 不同钢相焊时,焊后热处理规范应按焊后热处理温度要求较高的钢号执行,但温度不应超过两者中任一钢号的下临界点A C1.7.2.3 非受压元件与受压元件相焊时,应按受压元件的焊后热处理规范.7.2.4 采用电渣焊焊缝、焊后必须进行正火+回火的热处理.7.3 对有再热裂纹倾向的钢,在焊后热处理时应注意防止产生再热裂纹.7.4 奥氏体高合金钢制压力容器一般不进行焊后消除应力热处理.7.5 焊后热处理应在补焊后和压力试验前进行.7.6 应尽可能采取整体热处理.当分段热处理时,热重叠部份长度至少为1500mm,加热区以外部份应采取措施,防止产生有害的温度梯度.7.7 补焊和筒体环缝采取局部热处理时,焊缝每侧加热带宽度不得小于容器厚度的2倍;接管与容器相焊整圈焊缝热处理时,加热带宽度不得小于壳体厚度的6倍.加热区以外部位采取措施,防止产生有害的温度梯度.7.8 焊后热处理工艺7.8.1 焊件进炉时炉内温度不得高于400℃.7.8.2 焊件升温至400℃后,加热区升温速不得超过5000/δ℃/h(δ----厚度, mm),且不得超过200℃/h,最小可为50℃/h.7.8.3 焊件升温期间,加热区内任意长度为5000mm内的温差不得大于120℃. 7.8.4 焊件保温期间,加热区最高与最低温度之差不宜大于65℃.7.8.5 升温和保温期间应控制加热区气体,防止焊件表面过度氧化.7.8.6 焊件出炉时,炉温不得高于400℃,加热区降温速度不得超过6500/δ℃/h,且不得超过260℃/h.最小可为50℃/h.7.8.7 焊件出炉时,炉温不得高于400℃,出炉后应在静止的空气中冷却.8 焊缝返修8.1 对需要焊接返修的缺陷应当分析产生原因,提出改进措施,按标准进行焊接工艺评定,编制焊接返修工艺.8.2 焊缝同一部位返修次数不宜超过2次.8.3 返修前需将缺陷清除干净,必要时可采用表面探伤检验确认.8.4 待补焊部位应开宽度均匀、表面平整、便于施焊凹槽,且两端有一定坡度.8.5 如需预热,预热温度应较原焊缝相同.8.7 要求热处理的容器如在热处理后返修补焊时,必须重作热处理.9 焊接检验9.1 焊接检验主要方面9.1.1 焊前a. 母材、焊接材料;b. 焊接设备、仪表、工艺装备;c. 焊接坡口、接头装置及清理;d. 焊工资格;e. 焊接工艺文件.9.1.2 施焊过程中a. 焊接规范参数;b. 执行焊接工艺情况;c . 执行技术标准情况;d. 执行图样规定情况.9.1.3 焊后a. 实际施焊记录;b. 焊缝外观及尺寸;c. 后热、焊后热处理;e. 产品焊接试板、焊接工艺纪律检查试板;f. 无损检验;g. 致密性试验.附加说明:本标准由全国压力容器标准化技术委员会提出,由全国压力容器标准经技术委员会制造分委员会归口.本标准由机械电子工业部合肥通用机械研究所负责起草.本标准主要起草人戈兆文.附件:国家技术监督局文件技监局标发[1992]122号关于压力容器行业标准归口管理及编号的批复机电部、化工部、中国石化总公司、劳动部:压力容器产品的科研、设计、生产、使用及监督检验涉及部门较多,根据目前情况,压力容器行业标准难以确定某一个部门归口管理.为了不影响行业标准的制、修订工作,经反复研究协商,现对压力容器行业标准归口管理、编号等有关问题规定如下:1.压力容器行业标准由机电部、化工部、中国石化总公司、劳动部共同审批发布.2.压力容器行业标准代号,使用机械行业标准代号(JB)3.机电部从机械行业标准(JB)编号中划出一段(JB4700-4999)作为压力容器行业标准编号,并委托“全国压力容器标准化技术委员会”代四部门管理.4.压力容器行业标准制定过程中的协调问题、组织技术审查、办理标准的报批等工作由“全国压力容器标委会”与以上四个部门联系.5.“全国压力容器标准化技术委员会”受国家技术监督局直接领导,由机电部、化工部、中国石化总公司、劳动部四部共同管理.压力容器行业标准的规划、计划,由“全国压力容器标委会”负责协调,通过后提出建议,分别列入标准起草单位的主管部门的计划.标准送审稿必须通过“全国压力容器标委会”审查通过后上的四个部门共同审批、发布,并报国家技术监督局备案.国家技术监督局一九九二年三月十一日。
压力容器的焊接工艺
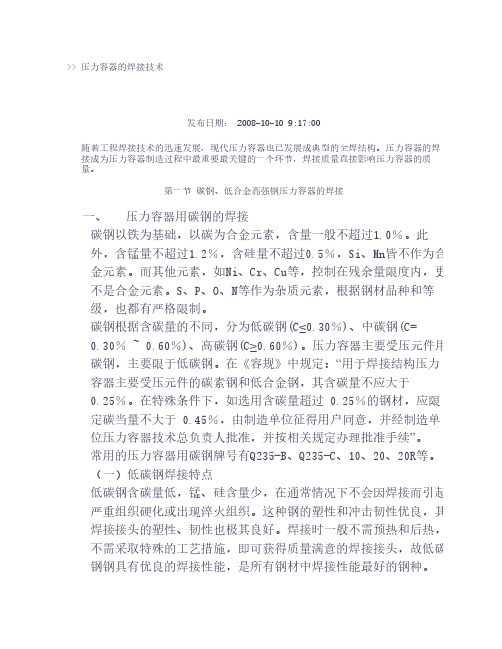
严格的限制,因为这种钢焊接热影响区脆化倾向较小,但对于含
钒、铌、钛等微合金化元素的钢,则应选用较小的焊接线能量。
(3)对于碳及合金元素含量较高、屈服强度也较高的低合金高强
钢,如18MnMoNbR,由于这种钢淬硬倾向较大,又要考虑其热影响
区的过热倾向,则在选用较小线能量的同时,还要增加焊前预热、
焊后及时后热等措施。
>> 压力容器的焊接技术
发布日期: 2008-10-10 9:17:00
随着工程焊接技术的迅速发展,现代压力容器也已发展成典型的全焊结构。压力容器的焊 接成为压力容器制造过程中最重要最关键的一个环节,焊接质量直接影响压力容器的质 量。
第一节 碳钢、低合金高强钢压力容器的焊接
一、 压力容器用碳钢的焊接 碳钢以铁为基础,以碳为合金元素,含量一般不超过1.0%。此 外,含锰量不超过1.2%,含硅量不超过0.5%,Si、Mn皆不作为合 金元素。而其他元素,如Ni、Cr、Cu等,控制在残余量限度内,更 不是合金元素。S、P、O、N等作为杂质元素,根据钢材品种和等 级,也都有严格限制。 碳钢根据含碳量的不同,分为低碳钢(C≤0.30%)、中碳钢(C= 0.30% ~ 0.60%)、高碳钢(C≥0.60%)。压力容器主要受压元件用 碳钢,主要限于低碳钢。在《容规》中规定:“用于焊接结构压力 容器主要受压元件的碳素钢和低合金钢,其含碳量不应大于 0.25%。在特殊条件下,如选用含碳量超过 0.25%的钢材,应限 定碳当量不大于 0.45%,由制造单位征得用户同意,并经制造单 位压力容器技术总负责人批准,并按相关规定办理批准手续”。 常用的压力容器用碳钢牌号有Q235-B、Q235-C、10、20、20R等。 (一)低碳钢焊接特点 低碳钢含碳量低,锰、硅含量少,在通常情况下不会因焊接而引起 严重组织硬化或出现淬火组织。这种钢的塑性和冲击韧性优良,其 焊接接头的塑性、韧性也极其良好。焊接时一般不需预热和后热, 不需采取特殊的工艺措施,即可获得质量满意的焊接接头,故低碳 钢钢具有优良的焊接性能,是所有钢材中焊接性能最好的钢种。
铝制压力容器焊接工艺规程

铝制压力容器焊接工艺规程1适用范围本工艺标准适用于铝及铝合金压力容器的手工钨极氩弧焊和熔化极氩弧焊的焊接;2准备2.1铝及铝合金的焊接除应执行本工艺标准外,还应符合国家颁布的有关标准、法律法规及规定;下列文件中的条款通过本标准的引用而成为本标准的条款,凡是不注日期的引用文件其最新版本适用于本标准《铝及铝合金轧制板材》《铝及铝合金热挤压管》第一部分:无缝圆管《铝及铝合金拉(轧)制无缝管》《铝及铝合金焊丝》《铝及铝合金焊接管》《铝制焊接容器》2.2材料2.2.1一般规定工程中使用的母材和焊丝应具备出厂质量合格证或质量复验合格报告,并优先选用已列入国家标准或行业标准的母材和焊丝,母材和焊丝应妥善保管,防止损伤、污染和腐蚀;当选用国外材料时,其使用范围应符合相应标准的规定,并应有该材料的质量证明书;2.2.2母材2.2.2.1工程选用的母材应符合现行的国家标准规定;2.2.2.2当对母材有特殊要求时,应在设计图样或相应的技术条件上标明;2.2.2.3施工单位对设备、容器和管道的材料的代用,必须事先取得原设计单位的设计修改证明文件,并对改动部位作详细记载;2.2.2.4损伤和锈蚀严重的母材不得在工程中使用;2.2.3焊接材料2.2.3.1母材焊接所选用的焊丝应符合现行的国家标准《铝及铝合金焊丝》GB/T10858的规定;2.2.3.2选用焊丝时应综合考虑母材的化学成分、力学性能及使用条件因素,并应符合下列规定;(1)焊接纯铝时应选用纯度与母材相同或比母材高的焊丝;(2)焊接铝锰合金时应选用含锰量与母材相近的焊丝或铝硅合金焊丝;(3)焊接铝镁合金时应选用含镁量与母材相同或比母材高的焊丝;(4)异种铝及铝合金的焊接应选用与抗拉强度较高的母材相应的焊丝2.2.3.3焊接时所使用的氩气应符合现行的国家标准《纯氩》GB4842的规定;2.2.3.4手工钨极氩弧焊电极应选用铈钨极,也可选用钍钨极,施焊前应根据焊接电流的大小正确选用钨极直径;2.3作业人员2.3.1铝及铝合金施工应具有符合国家质量技术监督或国家压力容器、压力管道监察机构有关法规要求的质量管理体系;2.3.2主要作业人员:焊工,管道工,无损探伤工2.3.3从事铝及铝合金焊接的焊工必须持有国家质量技术监督检验检疫总局颁发的锅炉压力容器压力管道特殊作业操作资格证,及按有关标准要求考试合格的焊工担任;2.3.4铝及铝合金的无损探伤检测应由持有国家有关部门颁发的无损检测人员资格证书的人员担任;2.4主要工机具2.4.1手工钨极氩弧焊采用交流氩弧焊机;2.4.2熔化极氩弧焊机采用半自动熔化极氩弧焊机;2.4.3角向磨光机及配套的铣刀片、不锈钢丝刷、锉刀、刮刀等机械工具;2.4.4水冷式氩弧焊枪;3焊接工艺3.1焊接工艺评定铝及铝合金材料的焊接工艺评定应当按JB/T4734-《铝制焊接容器》附录B的要求评定,或者按设计要求的标准进行评定;3.2焊工培训及考试3.2.1从事铝及铝合金材料焊接的焊工应进行培训和考试,考试包括基本知识和焊接操作技能两部分,基本知识考试合格后才能参加操作技能的考试,考试内容应与焊工所从事的工作范围相适应;3.2.2铝及铝合金焊接的焊工考试可以按JB/T4734-2000《铝制焊接容器》附录A铝容器焊工考试规则的要求进行;衬铝容器的焊工考试分别按铝及钢各自的考试规则进行,即铝的焊工考试按JB/T4734附录A 进行,钢的焊工考试按国家质量监督检验检疫总局颁发的《锅炉压力容器压力管道焊工考试与管理规则》进行;3.3焊接工艺流程3.4制造过程3.4.1施工单位在焊接施工前应根据焊接工艺评定报告编制焊接工艺规程(或焊接工艺指导书、焊接工艺卡);3.4.2焊接场所应保持清洁,并有防风防雨雪措施,相对湿度一般不应大于80%,环境温度应不低于5℃;3.4.3使用的氩弧焊机必须有适合焊接的电特性和足够的电流容量,且具有参数稳定,调节灵活和安全可靠的使用性能;3.4.4铝材可采用机械或等离子弧切割下料,坡口加工应采用机械方法,加工后的坡口表面应平整且无毛刺和飞边,坡口型式和尺寸应根据接头型式、母材厚度、焊接位置、焊接方法、有无垫板及使用条件等,并参照焊接工艺评定结果确定;3.4.5施工中可根据结构形式、焊接位置及施工条件,在焊接背面加临时垫板,若焊缝背面加永久性保留垫板,应征得原设计单位同意;垫板可使用不锈钢、碳钢或铜等对焊缝质量无不良影响的材料;3.4.6施焊前应将焊丝、焊件坡口及其附近表面的油污和氧化膜清除(若使用垫板其表面亦按同样要求清除),清除顺序及方法如下;3.4.6.1用丙酮或四氯化碳等有机溶剂除去表面油污,坡口两侧的清除范围应不小于50mm;3.4.6.2清除油污后,焊丝应采用化学法,坡口宜采用机械法(也可采用化学法)清除表面氧化膜;机械法:坡口及其附近表面可用铣刀铣、锉削、刮削或直接用直径为0.2mm左右的不锈钢丝刷清除至露出金属光泽,两侧的清除范围距坡口边缘应不小于30mm,使用的不锈钢丝刷应定期进行脱脂处理;化学法:用约70℃,5%~10%的NaOH溶液浸泡30~60分钟后,接着用约15%的HNO3(常温)浸泡2min左右后,用温水洗净,再进行100℃左右的烘干,使其完全干燥;3.4.6.3清理好的焊件和焊丝在焊前严禁沾污,并在8h内施焊,否则应重新进行清理;3.4.7焊丝选用3.4.7.1焊丝(包括填充丝)应使用焊接接头的抗拉强度不低于母材标准下限值或规定值,耐蚀性能和塑性不低于母材或与母材相当,能满足使用要求而且具有良好的焊接工艺性能;焊丝一般采用GB/T10858中的相应牌号,也可采用与母材牌号相当的铝线材作焊丝,线材可按GB/T3197《焊条用铝及铝合金线材》;3.4.7.2在施焊母材(容器、管道)要求耐蚀性的情况下,当母材为同牌号纯铝时,焊丝纯度不得低于母材,当母材为同牌号铝合金时,焊丝所含镁、锰等耐蚀合金元素的含量范围不得低于母材;当异种牌号的铝材焊接时应按耐蚀性能高的母材选用焊丝;3.4.7.3不宜将SalMg-2、SalMg-3、SalMg-5以及含镁量高于3%的焊丝用于接触65℃以上腐蚀介质的铝制容器和管道;3.4.7.4铝及铝合金焊丝选用见下表3.4.8焊缝组对要求3.4.8.1管道焊件组对时,应做到内壁平齐,其错边量b应符合下列规定:当壁厚S≤5mm时,b≤0.5mm当壁厚S>5mm时,b≤0.1S且b≤2mm3.4.8.2设备容器焊件组对时,其错边量b应符合下列规定:纵焊缝:当壁厚S≤5mm时,b≤0.5mm当壁厚S>5mm时,b≤0.1S且b≤2mm环焊缝:b≤0.2S且b≤5mm3.4.8.3不等厚度对接焊件组对时,薄件端面应位于厚件端面之内,当表面错边量超过3mm或单面焊焊缝根部超过2mm时应按下图的规定加工厚板边缘;3.4.8.4定位焊(1)定位焊缝应符合下列规定:焊件组对可使铝材定位板在坡口外点焊定位,也可在坡口内点固;焊接定位焊缝时,选用的焊丝应与母材相匹配;定位焊缝应有适当的长度、间距和高度,以保证其有足够的强度而不致在焊接过程中开裂;定位焊缝如发现缺陷应及时处理,对作为正式焊缝一部分的根部定位焊缝,还应将其表面的黑粉、氧化膜清除,并将两端修整成缓坡形,拆除定位板时不应损伤母材,拆除后应将残留焊肉打磨至与母材表面齐平;3.5焊接过程及应注意的问题3.5.1手工钨级氩弧焊应采用交流电源,熔化极氩弧焊应采用直流电源,焊丝接正极,焊机使用前,应检查其接地是否完好,冷却水路和气路是否畅通,其各项功能是否能正常工作;3.5.2为了减少焊接变形,应采用合理的施焊方法和顺序,或进行刚性固定,并预先考虑收缩余量;3.5.3正式焊接前,可在试板上进行堆焊试验,调整好各工艺参数,并确认无气孔后再进行正式焊接;3.5.4在保证焊缝熔透和熔合良好的条件下,应在焊接工艺规程允许范围内尽量采用大电流、快焊速施焊,焊丝的横向摆动幅度不宜超过其直径的三倍;3.5.5无特殊要求时焊件焊前不进行予热,多层焊时层面温度应尽可能低,不宜高于100℃;3.5.6焊接过程中焊丝端部不应离开氩气保护区,焊丝送进时与焊缝表面的夹角宜在15℃左右,焊枪与焊缝表面的夹角宜保持在80°~90°之间;对于厚度≥4mm的立焊和横焊位置的焊缝,当条件允许时底层焊接可采用双面同步氩弧焊工艺;3.5.7焊接过程中,焊层内的氧化膜、过高焊肉及其它焊接缺陷必须清除,对需要清根的双面焊或进行封底焊的焊缝应采用机械法清理焊根;3.5.8纵焊缝两端应装上铝制的引弧板和熄弧板,纵环焊缝清除弧坑后接续焊时,也宜在引弧板上引燃电弧,待电弧燃烧稳定后再进行焊接;3.5.9当喷嘴上有明显阻碍氩气气流流通的飞溅物附着时,必须将飞溅物清除或更换喷嘴,当钨极出现污染、形状不规则等现象时,必须修整或更换;3.6焊接工艺参数各种焊接方法工艺参数的选择见下表:注:①焊接电流系指底层焊接时每台焊机的电流值②覆盖层由一名焊工施焊其焊接工艺参数见《手工钨极氩弧焊焊接工艺参数》③当母材厚度≥10mm 时,焊前可进行100~150℃预热;3.7焊接环境3.7.1当施焊环境出现下列任一情况,且无有效防护措施时,禁止施焊:3.7.1.1气体保护焊风速大于1.5m/s;3.7.1.2相对湿度大于80%:3.7.1.3焊件温度低于5℃3.7.1.4雨雪环境3.7.2当焊件温度低于5℃时,应在始焊处100mm范围内预热到15左右(指焊前不预热的情况);3.8焊缝返修3.8.1焊缝返修应在压力试验之前进行,对要求焊缝返修的缺陷应当分析产生原因,提出改进措施,编制焊接返修工艺;3.8.2返修前需将缺陷清除干净,必要时可采用表面无损检测确定;3.8.3焊缝返修应由合格的焊工担任,返修工艺措施应经焊接技术负责人批准,同一部位的返修次数不应超过两次,对经过两次返修仍不合格的焊缝如再进行返修应经施工技术负责人批准;3.8.4返修焊缝性能和质量要求应与原焊缝相同;3.9产品焊接试板铝制压力容器的制造、组焊要按JB/T4734的要求焊制产品焊接试板,产品试板的要求,检验方法、取样部位、试验方法及合格标准按JB/T4734规定执行;4焊接质量检验4.1焊前检验包括4.1.1母材、焊接材料4.1.2焊接设备、仪表、工艺装备4.1.3焊接坡口、接头装配及清理4.1.4焊工资格4.1.5焊接工艺文件4.2施焊过程中的检验包括4.2.1焊接规范参数4.2.2执行焊接工艺情况4.2.3执行技术标准情况4.2.4执行图样情况4.3焊后检验包括4.3.1实际施焊记录4.3.2焊缝外观及尺寸4.3.3产品焊接试板、焊接工艺纪律检查试板(铝制容器及设计要求时)4.3.4无损检测4.3.5压力试验、致密性试验4.4焊缝外观质量要求4.4.1焊缝外观质量要求4.4.2角焊缝的焊角高度应等于或大于两焊件中较薄焊件母材厚度的70%且不应小于3mm;4.4.3焊缝应与表面圆滑过渡,其表面不得有裂纹、未熔合、气孔、氧化物夹渣等缺陷;5成品保护5.1焊缝完成后严禁敲打、碰砸焊缝及热影响区,对装有仪表、调节阀等区域应遮挡保护;5.2严禁在近缝区点焊临时支架;5.3凡在管道附近进行切割作业时应及时挡护,杜绝切割残渣、氧化物伤及管道和焊缝; 5.4严禁利用已完成的管道做支吊点;。
焊接手册(ASME规范)
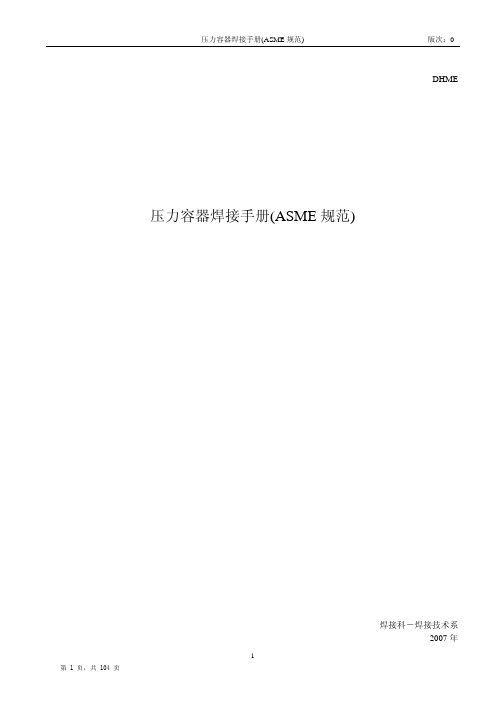
DHME 压力容器焊接手册(ASME规范)焊接科-焊接技术系2007年目录第一章 总则1.1目的1.2适用范围1.3参考文献第二章 设计规范2.1 编制WPS2.2 评定PQR2.3 设备焊接坡口设计第三章 采购要求3.1 焊接材料采购技术要求3.2 焊接材料选择指南第一章 总则1.1目的作为焊接ASME规范容器的参考基准。
1.2 适用范围本手册适用于按照ASME规范建造的压力容器焊接的设计、采购、检验等。
1.3参考文献1)ASME规范第VIII-1卷。
2)ASME规范第VIII-2卷。
3)ASME规范第IX卷。
4)ASME规范第II-C卷。
第二章 设计规范2.1 焊接工艺规程WPS2.1.1 工艺评定用焊接工艺规程工件焊接前,应编制工艺评定用焊接工艺规程(格式如正式的焊接工艺规程),评定试件应按工艺评定用焊接工艺规程焊接。
此焊接工艺规程在工艺评定合格前,不得用于正式产品焊接。
2.1.2 合格的焊接工艺规程工艺评定合格后,根据工艺评定的记录(电流、电压、焊接速度等),修改工艺评定用焊接工艺规程而编制出合格的焊接工艺规程。
2.2 焊接工艺规程的格式及填表方法如下:焊接工艺规程WELDING PROCEDURE SPECIFICATIONS (WPS)Company Name 公司名称 (1) Reviewed By:签字人 (2) Welding Procedure Specification No.WPS 编号 (3) Date 日期 (4) Supporting PQR No.(s)所依据的PQR编号 (5) Revision No.修改文件号 (6) Date 日期 (7)Welding Process(es) 焊接方法 (8) Type(s)自动化等级(自动,手工,机动或半自动) (9) (Automatic, Manual, Machine, or Semi-Auto.)* Each base metal-filler metal combination should be recorded individually对于每一种母材—填充金属的组合均需分别填表焊接工艺规程WELDING PROCEDURE SPECIFICATION (WPS)WPS No. Rev.POSITION QW-405 焊接位置Position(s) of Groove 坡口的位置 (31) Welding Progression: Up 向上 (32) Down 向下 (32) Position(s) of Fillet 角焊缝位置 (33) POSTWELD HEAT TREATMENT QW-407 焊后热处理Temperature Range 温度范围 (37) Time Range 时间范围 (38)Preheat QW-406 预热Preheat Temp. Min.预热温度最小 (34) Interpass Temp. Max.层间温度最大 (35) Preheat Maintenance预热的保持方式 (36) (Continuous or special heating where applicable should be recorded) GAS QW-408 气体Percent Composition 百分组成Gas(es) (Mixture) Flow Rate气体 (混合保护气体) 流量Shielding 保护气体 (39) Trailing尾部保护气体 (40) Backing背面保护气 (41)ELECTRICAL CHARACTERISTICS QW-409电特性Current AC or DC 交流或直流 (42) Polarity极性 (43)Amps(Range) 安培(范围) (44) Volts(Range)伏特(范围) (45)(Amps and Volts range should be recorded for each electrode size,position, and thickness, etc. This information may be listed in a tabularform similar to that shown below.)(安培和伏特范围应按每种焊丝尺寸,位置和厚度等分别记录,可按以下表的方式记录)Tungsten Electrode Size and Type (46)钨极规格和类型 (Pure Tungsten,2%Thoriated etc.)(纯钨极或2%钍钨极等) Mode of Metal Transfer for GMAW (47)金属过渡方式(GMAW) (Spray arc,short circuiting arc,etc)(射流或断路等) Electrode wire feed speed range (48)送丝速度范围TECHNIQUE QW-410String or Weave Bead无摆动焊或摆动焊 (49) Orifice or Gas Cup Size嘴孔或喷嘴尺寸 (50) Initial and Interpass Cleaning (Brushing,Grinding,etc)打底焊道和中间焊道的清理方法(清理和打磨等等) (51) Method of Back Gouging背面清理方法 (52) Oscillation摆动 (53) Contact Tube to Work Distance导电嘴—工件距离 (54) Multiple or Single Pass (Per side)多道焊或单道焊(每边) (55)Multiple or Single Electrodes多丝焊或单丝焊 (56) Travel Speed(Range)焊接速度(范围) (57) Peening锤击 (58) Other其它 (59)焊层 焊接方法 填充金属Filler Metal电流Current电压范围焊接速度范围其它例如:备注,说明,加热丝,施焊技术,焊炬角度等等Weld Layer(s) Process 种类Class直径Dia.极性Type Polar安培Amp RangeVolt Range TravelSpeedRangeOther(e.g. Remarks,Comments,Hot WireAddition, Technique, Torch Angle,Etc.)(60)PREPARED BY 编制 DATE日期 APPROVED BY 批准 DATE日期(1) 公司名称 如“大连日立机械设备有限公司”(2) 签字人 通常由DHME质保部-质保科长签字(3) WPS 编号 DHME编号规则AWPS+年号+流水号(4) 日期(5) PQR编号 支持工艺规程的PQR,编号规则APQR+年号+流水号(6) 修改文件号 从0开始(7) 日期(8) 焊接方法 SMAW+SAW或GTAW(9) 自动化等级 焊接方法的自动化程度,如:SMAW:手工GMAW&FCAW:半自动SAW:机动或自动GTAW:手工或自动(10) 接头 接头形状单面V形,双面V形,单面U形,双面U形,角焊缝,坡口焊缝&角焊缝,堆焊焊缝(11) 衬垫 记为 “√”,双面焊作为有垫板对待(12) 衬垫材料 如SA516-70,或母材及焊缝金属(13) 母材分类号 查QW-422,或AWS B2.1(14) 母材组号 查QW-422,或AWS B2.1若无冲击试验要求,此处可不填写“N/A”(15) 规格型号和等级 母材的型号和等级SA240-304(16) 化学成分和力学性能 母材的化学成分和力学性能填入无P-No.的母材的化学成分和力学性能(17) 坡口焊,母材厚度范围 按照QW-450(18) 角焊,母材厚度范围 按照QW-202.1,QW-451.3,QW-451.4,通常为“不限”(19) 坡口焊的管径范围 管件焊接时,填入管径(20) 角焊的母材厚度范围 通常为“不限”(21) 填充金属的ASME SFA号,或AWS A号 如“5.1”等或“GB/T5117”(22) 填充金属的等级 如“E7016”如“ER70S-2”(23) 填充金属的F-No. 按QW-432,无分类号填入“-”(24) 填充金属的A-No. 按QW-442,可按熔敷金属的化学分析结果、标准值、质量证明书(应注意焊接方法,焊接条件应与产品一致)(25) 填充金属尺寸 填充金属的尺寸(26) 坡口焊缝金属厚度 根据评定的结果填写(27) 角焊缝焊缝金属厚度 通常为“不限”(28) 焊丝-焊剂(等级) 填写焊丝和焊剂的型号,如“F7A2-EH14”(29) 焊剂牌号 当有冲击试验要求时,填写焊剂的“商品牌号”,如“G-80”当焊接高合金时,如奥氏体不锈钢时,必须填写焊剂的“商品牌号”,如“AT-SJ601”(30) 熔化性填充 当使用熔化性嵌条时,填写嵌条的类型,商品名称(31) 坡口的位置 坡口焊的位置,应按照评定结果,1G-6G(32) 焊接行进方向 3G,3F,5G,6G位置时必须填写,按照评定结果,“√”(33) 角焊缝位置 角缝焊接的位置,应按照评定结果,1F-4F(34) 预热温度 最低的预热温度,按照评定结果,堆焊时应分层填写,QW-406.1,QW-281.2(e) (35) 层间温度 最高的层间温度,按照评定结果, QW-406.3,QW-281.2(e)(36) 预热的保持方式 填入预热保持方法,需要消氢处理时,填入后热规范(37) 焊后热处理温度范围 按照焊接工艺评定,或“-”(38) 焊后热处理保温时间 焊后热处理的保温时间范围,按照评定结果(有冲击试验要求时),或“-” (39) 保护气体的类别,混合比,气体流量 按照评定结果(40) 尾部保护气体的类别,混合比,气体流量按照评定结果(41) 背面保护气体的类别,混合比,气体流量 按照评定结果(42) 电流 DC或AC(43) 电流极性 RP与SP,EN与EP,DC+与DC-,AC无极性之分(44) 焊接电流范围(45) 电弧电压范围(46) 钨极类型和尺寸 按照ISO6848,SFA-5.12(47) GMAW的金属过渡形式 短路过渡,颗粒过渡,喷射过渡(48) 送丝速度范围QW-409.8 以送丝速度代表电流控制时,填入送丝速度(49) 焊接技巧QW-409.10 直焊,摆动,直焊或摆动(50) 喷孔或喷嘴尺寸QW-410.3 GMAW,GTAW,PAW喷嘴的尺寸(51) 层道清理方法QW-410.5 打磨,打磨或刷(52) 背面清理方法QW-410.6 碳弧气刨,打磨,机加工(53) 机械摆动的参数QW-410.7 当采用机械摆动装置时,填入摆动的频率和幅度(54) 导电嘴-工件距离(干伸长)QW-410.8 SAW:30-40cmGMAW&FCAW:10-25cm(55) 多道焊或单道焊QW-410.9 填入“单道”或“多道”(56) 电极数 如:SAW:单丝SAW:双丝(57) 焊接速度(58) 锤击QW-410.5 填入“是”,“否”(59) 其它(60) 焊接规范 填入评定合格的焊接规范2.2 焊接工艺评定记录PQR焊接工艺评定记录PQR的格式和填写规则如下:焊接工艺评定记录PREHEAT QW-406预热Preheat Temp.预热温度 (25) Interpass Temp.层间温度 (26) Other其它 (27) 侧) (43) Single or Multiple Electrodes多丝焊或单丝焊 (44) Other其它 (45)焊接工艺评定记录PROCEDURE QUALIFICATION RECORD (PQR) PQR NO.Tensile Test QW-150 拉力试验Specimen No.试样号 Width宽Thickness厚Area面积UltimateTotal Load NUltimateUnit Stress MPaType of Failure& Location(46) (47) (48) (49) (50) (51) (52)Guide-Bend Tests QW-160 导引弯曲试验Type and Figure No. 类型和编号 Result 结果(53) (54)Toughness Test QW-170 韧性试验Specimen No. Notch Location Notch Type Test Temp.Impact Values Lateral Exp.侧向膨胀 Drop Weight 落锤试验试样号 缺口位置 缺口类型 试验温度冲击值 % Shear mm Break 断裂 No Break 不断裂(55) (56) (57) (58) (59) (60) (61) (62) (63)Fillet-Weld Test 角焊缝试验Result-Satisfactory: Yes No (64) Penetration into Parent Metal: Yes No 结果满意 是 否 熔透母材: 是 否 Macro-Results (65) 低倍检查结果Other Tests其它试验Type of test试验类型 (66) Deposit Analysis熔敷金属成分 (67) Other其它 (68) Welder's Name 焊工姓名 (69) Clock No.工号 (70) Stamp钢印 (71) Tests conducted by:执行人 (72) Laboratory Test No.实验室试验编号 (73) We certify that the statements in this record are correct and that the test welds were prepared, welded, and tested in accordance with the requirements of Section Ⅸ of the ASME Code.MANUFACTURER 制造厂 PREPARED BY 编制 DATE 日期 CERTIFIED BY 证明 DATE 日期 REVIEWED BY 签字 DATE 日期PQR填写规则:序号内容详细(1)公司名(2) PQR编号(3)日期评定合格日期(4) WPS编号及版号用于施焊评定试件的WPS(5)焊接方法(6)自动化等级 SMAW:手工GTAW:手工、自动SAW:机械化GMAW&FCAW:半自动(7)接头评定试件的坡口形式及焊道层、道布置(8)材料标准如“SA-516”(9)型号和等级“70”(10) P-No. 按QW-422(11) P-No. 按QW-422(12)试件厚度(13)试件直径(14)其它(15) SFA标准如“5.1”(16) AWS等级如“E7016”(17)填充金属F-No. 如“6”(18)焊缝金属A-No. 如“1”,可根据SFA标准、质量证明书、化学分析报告等依据(19)填充金属规格如“Φ4.0”(20)其它(21)焊缝金属厚度如“6.0mm”,对于每种焊接方法,应分别测量。
压力容器焊接工艺
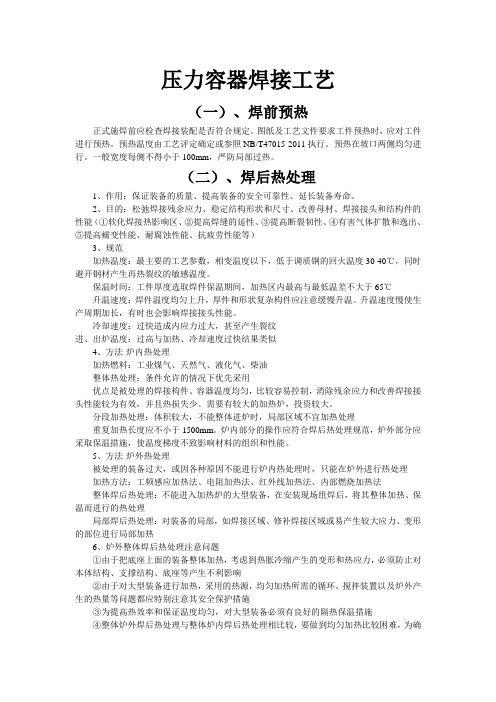
压力容器焊接工艺(一)、焊前预热正式施焊前应检查焊接装配是否符合规定。
图纸及工艺文件要求工件预热时,应对工件进行预热。
预热温度由工艺评定确定或参照NB/T47015-2011执行。
预热在坡口两侧均匀进行。
一般宽度每侧不得小于100mm,严防局部过热。
(二)、焊后热处理1、作用:保证装备的质量、提高装备的安全可靠性、延长装备寿命。
2、目的:松弛焊接残余应力、稳定结构形状和尺寸、改善母材、焊接接头和结构件的性能(①软化焊接热影响区、②提高焊缝的延性、③提高断裂韧性、④有害气体扩散和逸出、⑤提高蠕变性能、耐腐蚀性能、抗疲劳性能等)3、规范加热温度:最主要的工艺参数,相变温度以下,低于调质钢的回火温度30-40℃,同时避开钢材产生再热裂纹的敏感温度。
保温时间:工件厚度选取焊件保温期间,加热区内最高与最低温差不大于65℃升温速度:焊件温度均匀上升,厚件和形状复杂构件应注意缓慢升温。
升温速度慢使生产周期加长,有时也会影响焊接接头性能。
冷却速度:过快造成内应力过大,甚至产生裂纹进、出炉温度:过高与加热、冷却速度过快结果类似4、方法-炉内热处理加热燃料:工业煤气、天然气、液化气、柴油整体热处理:条件允许的情况下优先采用优点是被处理的焊接构件、容器温度均匀,比较容易控制,消除残余应力和改善焊接接头性能较为有效,并且热损失少。
需要有较大的加热炉,投资较大。
分段加热处理:体积较大,不能整体进炉时,局部区域不宜加热处理重复加热长度应不小于1500mm。
炉内部分的操作应符合焊后热处理规范,炉外部分应采取保温措施,使温度梯度不致影响材料的组织和性能。
5、方法-炉外热处理被处理的装备过大,或因各种原因不能进行炉内热处理时,只能在炉外进行热处理加热方法:工频感应加热法、电阻加热法、红外线加热法、内部燃烧加热法整体焊后热处理:不能进入加热炉的大型装备,在安装现场组焊后,将其整体加热、保温而进行的热处理局部焊后热处理:对装备的局部,如焊接区域、修补焊接区域或易产生较大应力、变形的部位进行局部加热6、炉外整体焊后热处理注意问题①由于把底座上面的装备整体加热,考虑到热胀冷缩产生的变形和热应力,必须防止对本体结构、支撑结构、底座等产生不利影响②由于对大型装备进行加热,采用的热源,均匀加热所需的循环、搅拌装置以及炉外产生的热量等问题都应特别注意其安全保护措施③为提高热效率和保证温度均匀,对大型装备必须有良好的隔热保温措施④整体炉外焊后热处理与整体炉内焊后热处理相比较,要做到均匀加热比较困难,为确认整个装备的加热工艺情况是否达到工艺要求,应注意有足够数量且正确配置的温度检测设备,以保证热处理效果7、炉外局部焊后热处理注意问题①局部加热由于温度的分布不均匀、温度梯度较大而容易产生较大的热应力,为了尽量减少这种热应力造成的不利影响,加热的范围可以考虑尽量对称②容器环焊缝的加热带宽度应至少包括焊缝边缘两侧各3倍壁厚的宽度,管子对接焊者为2倍③尽量减少加热区与非加热区域之间的温度梯度差,温度梯度过大时,可能产生残余应力和变形。
9.压力容器焊接技术【精选】

9.压力容器焊接技术9.1薄壁容器的焊接过程设备中的中低压容器大多数为薄壁容器,其特点为壁厚与直径之比很小(δ/D≤0.05)。
对于薄壁容器多采用单层卷板的方法制造筒节,用手工电弧焊和埋弧焊进行纵、环焊缝的焊接。
9.1.1薄壁容器焊接技术(1)焊前准备焊前的准备工作包括坡口加工,焊接区域的清洁以及焊件的装配等。
这些工作应给予足够的重视,不然会影响焊缝质量,严重时还会造成焊后返工。
对于中等厚度以下的容器焊接,常用的坡口形式有齐边坡口,V形坡口和X形坡口。
坡口形式的选择主要考虑以下几个因素:①能否保证焊透;②坡口形式是否易于加工;③尽量提高劳动生产率,节约焊接材料;④焊件焊后的变形尽量小。
例如:容器的壁薄,两面各焊一道即可焊透时,可采用齐边坡口,加工量小,生产效率高。
对于稍厚一些的容器,为保证焊缝质量,应开坡口。
采用何种形式的坡口也要视具体情况而定。
若容器组装后,在内部焊接时通风条件差,焊接的主要工作量应放在容器外侧,这时应选用不对称X形坡口(大口开在外侧)或V形坡口。
(2)容器焊接顺序先焊筒节纵缝,焊好后校圆,再组装焊接环缝。
当筒体直径太大无法校圆时,应先将单筒节的几条纵缝点焊,几个筒节组装点固定后再进行纵缝和环缝的焊接。
要注意的是必须先焊纵缝后焊环缝,因为若先将环缝焊好再焊纵缝时筒体的膨胀和收缩都要受到环缝的限制,其结果会引起过大的应力,甚至产生裂纹。
每条焊缝的焊接次序是先焊筒体里面,焊完后从外面用碳弧气刨清理焊根,将容易产生裂纹和气孔的第一层焊缝基本刨掉,经磁粉或着色探伤确信没有缺陷存在后再焊外侧。
(3)对接直缝的焊接对于中等厚度以下钢板的对接焊缝,采用齐边坡口最简单,并采用埋弧自动焊以提高生产率。
通常有以下几种焊接方法:①无衬垫双面自动焊对焊件的边缘加工和装配要求较高,焊件边缘必须平直,保证装配间隙小于1mm。
为了保证焊缝有足够的熔深又不会烧穿,焊第一面时要控制熔深为板厚的40~50%。
翻面后要控制熔深达到板厚的60~70%,以保证全焊透。
压力容器及管道焊接
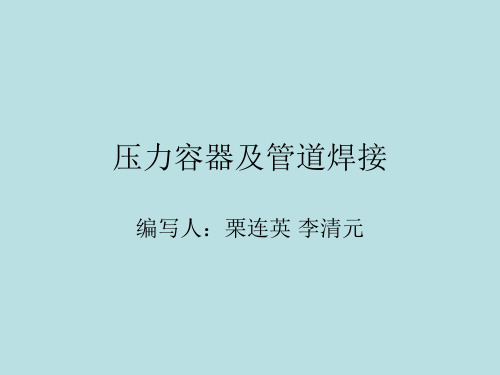
时间 h 1 1 1 1 1 1 1 1 1 1 1 1 1
常用钢号的焊接材料表
钢号 SMAW 型号 标准号 牌号 焊丝钢号 焊剂 标准号 型号 标准号 GMAW 熔化极气体保 护焊 牌号 焊丝钢号 标准号 GTAW 氩弧焊 焊丝钢号 标准号
Q235E4303 A.FQ235A10(管) 20(管)
E5015-G
W607
W707
E5016
J506
16MnR
E5015
J507
H10MnSi H10Mn2
HJ401-H08A HJ402-H10Mn2
HJ431 HJ350
H08Mn2SiAn
H10MSi
16MnD 16MnDR 15MnNiDR 15MnNbR
E5016-G E5015-G E5015-G E5516-G E5515-G
15MnVR
E5515-G
H08Mn2SiA
20MnMo
E5015-G E5515-G
J507RH H10MnSi H10Mn2 J557 H08MnMoA
20MnMoD
E5016-G E5015-G
E5516-G
J506RH J507RH
J556RH J606 J607 H08Mn2MoA
13MnNiMo E6016-D1 NbR E6015-D1
2 焊接的分类及常用的几种方法
• 1)、焊条电弧焊(SMAW)在焊条末端 和工件之间燃烧的电弧所产生的高温,使 药皮、焊芯及工件熔化,药皮熔化过程中 产生的气体和熔渣,不仅使熔池和电弧周 围的空气隔绝,而且和熔化了的焊芯、母 材发生一系列冶金反应,使熔池金属冷却 结晶后形成符合要求的焊缝。焊条电弧焊 是利用手工操纵焊条进行焊接的电弧焊方 法
压力容器焊接技术规程

压力容器焊接技术规程12.1总则12.1.1本章适用于单层焊接压力容器;12.1.2容器的制造、检验与验收除应符合本章规定外,还应符合图样要求;12.1.3容器主要受压部分的焊接接头分为A、B、C四类,如图12-1所示;12.1.4受压元件的材料应有确认的标记。
在制造过程中,如原有确认标记被裁掉或材料分成几块,应于材料切割前完成标记的移植。
对于有防腐要求的不锈钢以及复合钢板制容器,不得在防腐蚀面采用硬印作为材料的确认标记。
12.2焊接材料12.2.1焊条、焊剂及其他焊接材料的贮存库应保持干燥,相对温度不得大于60% 。
12.2.2当焊件温度低于0℃时,应在始焊外100mm范围内预热到15℃左右。
12.3焊接工艺12.3.1焊接工艺评定(1)容器施焊前应进行焊接工艺评定,根据焊接工艺评定报告编制焊接工艺卡,进行容器焊接;(2)焊接工艺评定报告、焊接工艺规程、施焊记录及焊工的识别标记,其保存期不少于7年。
12.3.2坡口表面要求(1)坡口表面不得有裂纹、分层、夹杂等缺陷;(2)标准抗拉强度下限值σb>540MPa低合金钢材及Cr-Mo低合金钢材经火焰切割的坡口表面,应进行磁粉或渗透检测。
当无法进行磁粉或渗透检测时,应由切割工艺保证坡口质量。
(3)施焊前,应清除坡口及其母材两侧表面20mm范围内(以离坡口边缘的距离计)的氧化物、油污、熔渣及其他有害杂质。
12.3.3焊缝表面尺寸要求(1) A、B类接头焊缝的余高e1、e2,按表12-1和图12-2的规定。
图12-1图12-2(2)C、D类接头的焊脚,在图样无规定时,取焊件中较薄者之厚度。
补强圈的焊脚,当补强圈的厚度不小于8mm时,其焊脚等于补强圈厚度的70%,且不小于8mm。
(3)焊缝表面不得有裂纹、气孔、弧坑和飞溅物。
(4)用标准抗拉强度一限值σb>540Mpa的钢材以及Cr-Mo低合金钢钢材和不锈钢材制造的容器以及焊接接头系数φ取为1的容器,其焊缝表面不得有咬边。
- 1、下载文档前请自行甄别文档内容的完整性,平台不提供额外的编辑、内容补充、找答案等附加服务。
- 2、"仅部分预览"的文档,不可在线预览部分如存在完整性等问题,可反馈申请退款(可完整预览的文档不适用该条件!)。
- 3、如文档侵犯您的权益,请联系客服反馈,我们会尽快为您处理(人工客服工作时间:9:00-18:30)。
压力容器焊接工艺说明书
一、零件的名称、批量及材料:
名称:压力容器批量:年产100件材料:20钢
二、零件的作用:
工业生产中具有特定的工艺功能并承受一定压力的设备,称压力容器。
贮运容器、反应容器、换热容器和分离容器均属压力容器。
为了与一般容器(常压容器)相区别,只有同时满足下列三个条件的容器,才称之为压力容器:
(1)最高工作压力≥9.8104Pa(1Kgf/cm2);
(2)容积≥25L,且工作压力与容积之积≥200L.Kgf/cm2(1960104L.Pa);
(3)介质为气体、液化气体或最高工作温度高于标准沸点的液体。
压力容器的用途十分广泛。
它是在石油化学工业、能源工业、科研和军工等国民经济的各个部门都起着重要作用的设备。
三、零件工艺分析:
如零件图所示,其结构不复杂,且是单件小批量生产。
体积较大,选用铸造明显不现实,焊接是首选。
焊接制造该零件的过程中,虽然零件结构简单,在焊接过程中,主要考虑是零件的氧化。
上、下封头拉伸成型后,因开口端变形大,冷变形强化严重,加上板材纤维组织的影响,在残余应力作用下很容易发生断裂。
为防止裂纹产生,拉伸后应进行再结晶退火;为了减少焊接缺陷,焊件接缝附近必须严格清楚铁锈、油污;为去除焊接残余应力并改善焊接接头的组织与性能,瓶体焊接后应该进行整体正火处理,至少要进行去应力退火。
四、确定毛坯的制造形式:
对于该零件,由于它的生产批量为单件或小批量,零件的本身不复杂,主要考虑的是零件的封闭性以及在焊接过程中防止发生焊缝氧化。
零件的壁厚都比较小,相对于铸造成型,采用焊接的方法来制造毛坯是经济而高效的方法。
故对该零件的毛坯选择焊接来制造。
五、零件的焊接工艺分析:
该零件的焊接结构,构造不复杂,但尺寸较大,设计时将它合理的划分成二个部件,然后再进行组焊。
在焊接中,合理布置焊缝可以直接减少焊接工作量,节约熔敷金属总量,同时还可以减少焊接变形,增加焊接结构的安全可靠性。
故在焊接中可采用一些必要的措施。
在该零件的焊接中,焊接方法选择应根据材料的焊接性、工件厚度、生产率要求、各种焊接方法的使用范围和现场设备条件等综合考虑决定。
在该零件的焊接中,可能出现的缺陷主要是焊接变形及氧化。
从而引起零件的精度不够以及以后零件在使用过程中会发生泄露现象,零件焊接后,由于焊缝的氧化则影响零件的工作寿命。
因此,这种危害性比较严重,应尽量避免。
在生产中,一般采用合理的焊接方法,将零件的氧化降到最低程度,并在焊后在焊缝处涂上一层防腐蚀涂料,可以达到更理想的效果。
六、零件的焊接工艺确定:
1、确定焊缝的位置
方案(a)共有三条焊缝,其中包括两条环形焊缝和一条轴向焊缝。
方案(b)只有一条环形焊缝。
方案(a)的优点是上下封头的拉伸变形小,容易成型;缺点是焊缝多,焊接工作量大。
同时,因为筒体上的轴向焊缝处于拉应力最高的位置(径向拉应力为轴向拉应力的两倍),破
坏的可能性很大。
方案(b)只在中部有一环缝,完全避免了方案(a)的缺点,因此选用方案(b)。
2、设计焊接接头
连接瓶体与瓶嘴的焊缝,采用不开坡口的角焊缝即可。
而瓶体主环缝的接头形式,宜采用衬环对接或缩口对接,如果所示。
这样便于上、下封头定位装配。
为确保焊透,尽管焊件厚度不大,仍然开V型坡口。
3、选择焊接方法和焊接材料
瓶体的焊接采用生产率高、焊接质量稳定的埋弧自动焊。
焊接材料可用焊丝H08A、H08MnA 或H10Mn2A,配合HJ431。
瓶嘴的焊接因焊缝直经小,用手弧焊焊接。
焊条可取E4303(J422)。
七、具体工艺过程:
(一)、分件工艺:
1、筒体:材料:20钢
(1)落料、拉深:
①拉深: 440m×440mm×3mm,如图所示,矫正变形。
②拉深: 440mm×440mm×3mm,如图所示,矫正变形。
(2)钳:去毛刺,整形,再结晶退火。
2、罐顶:材料:20钢
(1)冲孔:冲一个半径为52mm的圆孔。
(2)钳:去毛刺,修磨表面,除锈。
(二)、整件工艺
(1)备料:备齐上述各件,并检查各件尺寸。
(2)组焊
1)将瓶嘴和上瓶体按图样要求尺寸点固定好,并焊接。
2)将上瓶体和下瓶体按图样要求尺寸点固定好,除锈并焊接。
(3)钳:矫正焊后变形,去毛刺。
(4)正火处理
(5)水压试验
(6)气密试验
附:工艺说明:
(1)本件功能上起容器的作用,要求表面平整,并要求整体变形不能过大。
并要求焊缝的氧化较小。
(2)焊接材料及焊机的选择:
材料为:20钢,厚度为3mm,埋弧自动焊时,选用H08A焊丝,直径:1.6mm,焊接电流:I=115-500A。
因焊机焊接电流都有一较宽的调节范围,500A以下均行,可以按具体情况选择,
可以选用MZ6-2-500。
手弧焊时,焊条取E403(J422)。