发动机振动特性分析与试验
航空发动机整机振动典型故障分析
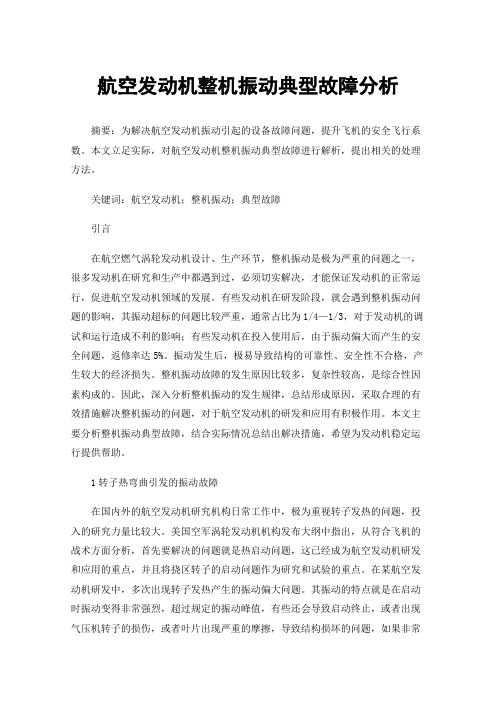
航空发动机整机振动典型故障分析摘要:为解决航空发动机振动引起的设备故障问题,提升飞机的安全飞行系数。
本文立足实际,对航空发动机整机振动典型故障进行解析,提出相关的处理方法。
关键词:航空发动机;整机振动;典型故障引言在航空燃气涡轮发动机设计、生产环节,整机振动是极为严重的问题之一,很多发动机在研究和生产中都遇到过,必须切实解决,才能保证发动机的正常运行,促进航空发动机领域的发展。
有些发动机在研发阶段,就会遇到整机振动问题的影响,其振动超标的问题比较严重,通常占比为1/4—1/3,对于发动机的调试和运行造成不利的影响;有些发动机在投入使用后,由于振动偏大而产生的安全问题,返修率达5%。
振动发生后,极易导致结构的可靠性、安全性不合格,产生较大的经济损失。
整机振动故障的发生原因比较多,复杂性较高,是综合性因素构成的。
因此,深入分析整机振动的发生规律,总结形成原因,采取合理的有效措施解决整机振动的问题,对于航空发动机的研发和应用有积极作用。
本文主要分析整机振动典型故障,结合实际情况总结出解决措施,希望为发动机稳定运行提供帮助。
1转子热弯曲引发的振动故障在国内外的航空发动机研究机构日常工作中,极为重视转子发热的问题,投入的研究力量比较大。
美国空军涡轮发动机机构发布大纲中指出,从符合飞机的战术方面分析,首先要解决的问题就是热启动问题,这已经成为航空发动机研发和应用的重点,并且将挠区转子的启动问题作为研究和试验的重点。
在某航空发动机研发中,多次出现转子发热产生的振动偏大问题。
其振动的特点就是在启动时振动变得非常强烈,超过规定的振动峰值,有些还会导致启动终止,或者出现气压机转子的损伤,或者叶片出现严重的摩擦,导致结构损坏的问题,如果非常严重的情况下,极易导致转子出现掉角、裂纹的问题。
热启动时,转子热弯曲的问题就会出现在发动机停车后,这是系统工作温度相对较高,叶片—轮盘—转轴封闭机匣内,在冷却的过程中。
外部的气流会持续性进入到发动机内部,因为外部气流的温度比较低,发动机内部温度高,热气流会不断的向上移动,而冷气流则会向下移动。
用模态分析测定发动机叶片振动特性

用模态分析测定发动机叶片振动特性作者:杨伟来源:《科学与财富》2011年第09期[摘要] 本文主要介绍了利用模态分析的方法,对发动机叶片进行振动特性分析。
重点介绍了利用锤击法测定某发动机1级涡轮叶片的模态参数。
详细分析了在模态试验中的各项工作以及容易引起测量误差的地方,并结合试验总结了一些在模态分析中的经验教训。
[关键词] 模态分析锤击静频振型传递函数固有频率激励一、前言在发动机的生产、研制和使用中,必须测定叶片振动特性参数。
叶片振动特性参数通常是指:叶片的静频、振型、阻尼和振动应力等。
用锤击法作结构振动的模态分析是近年来迅速发展起来的。
对叶片做锤击振动试验,首先要在叶片的叶身部分划线确定敲击点。
由于敲击点信息在数据处理后可以反映该点的振动位移,所以最好要避开节线。
一般情况下用锤击法作叶片静频参数测定,如单求频率和阻尼时,只要敲击一点并只测一点响应即可。
二、模态理论简述由振动理论可知:一个线性振动系统,当它按自身某一阶固有频率作自由谐振时,整个系统将具有确定的振动形态(简称振型或模态)。
所谓振动模态分析法,就是利用系统固有模态的正交性,对通常所选取的物理坐标进行线性变换,这个用模态坐标和模态参数所描述的各个独立方程,称为模态方程。
【1】模态分析的首要任务是要求出系统各阶的模态参数(例如系统的固有频率和振型;模态质量或模态刚度,以及模态阻尼等)。
一个具有N个自由度的线性振动系统,若不计及阻尼的影响,则其自由振动的运动微分方程的一般形式可以表示为:因此模态试验的目的是为模态参数识别提供可靠的频率响应函数或脉冲相应函数【1】。
三、模态试验模态试验测试系统主要由以下几个部分组成:激振部分、信号测量与数据采集部分、信号分析和频响函数估计部分。
3.1结构的安装进行模态试验的结构在实际的工作环境中,总处于一定的约束状态。
设置试验时,选择结构的支承方式首先考虑是否模拟其真实的约束状态。
通常用一种非常柔软的悬挂系统将被试结构支承起来,以模拟自由支承。
汽车发动机传动系统的振动特性分析
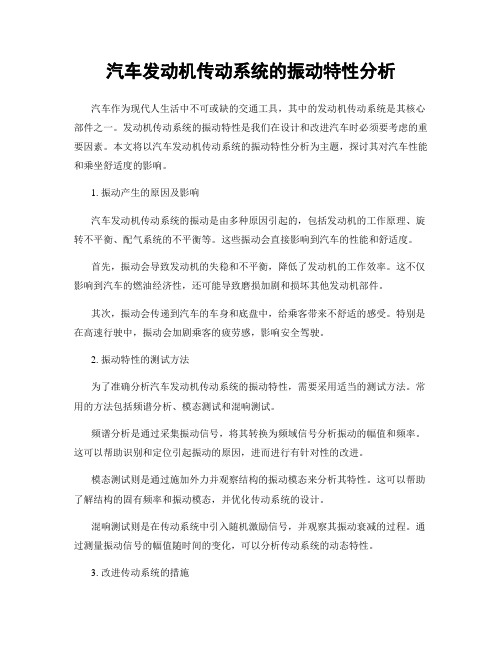
汽车发动机传动系统的振动特性分析汽车作为现代人生活中不可或缺的交通工具,其中的发动机传动系统是其核心部件之一。
发动机传动系统的振动特性是我们在设计和改进汽车时必须要考虑的重要因素。
本文将以汽车发动机传动系统的振动特性分析为主题,探讨其对汽车性能和乘坐舒适度的影响。
1. 振动产生的原因及影响汽车发动机传动系统的振动是由多种原因引起的,包括发动机的工作原理、旋转不平衡、配气系统的不平衡等。
这些振动会直接影响到汽车的性能和舒适度。
首先,振动会导致发动机的失稳和不平衡,降低了发动机的工作效率。
这不仅影响到汽车的燃油经济性,还可能导致磨损加剧和损坏其他发动机部件。
其次,振动会传递到汽车的车身和底盘中,给乘客带来不舒适的感受。
特别是在高速行驶中,振动会加剧乘客的疲劳感,影响安全驾驶。
2. 振动特性的测试方法为了准确分析汽车发动机传动系统的振动特性,需要采用适当的测试方法。
常用的方法包括频谱分析、模态测试和混响测试。
频谱分析是通过采集振动信号,将其转换为频域信号分析振动的幅值和频率。
这可以帮助识别和定位引起振动的原因,进而进行有针对性的改进。
模态测试则是通过施加外力并观察结构的振动模态来分析其特性。
这可以帮助了解结构的固有频率和振动模态,并优化传动系统的设计。
混响测试则是在传动系统中引入随机激励信号,并观察其振动衰减的过程。
通过测量振动信号的幅值随时间的变化,可以分析传动系统的动态特性。
3. 改进传动系统的措施针对振动特性的测试结果,可以采取一系列措施来改进汽车发动机传动系统的性能和舒适度。
首先,可以通过在发动机的旋转部件上增加平衡块来解决由旋转不平衡引起的振动。
这可以有效地减少发动机的振动幅值,提升其工作稳定性。
其次,可以通过优化传动系统的结构和材料来减少振动的传递和共振。
例如,使用吸振材料和减震器来吸收和消散振动能量,降低振动的幅度和频率。
此外,合理设计传动系统的支撑结构和减振装置,也可以有效地减少振动的传递。
发动机剧烈抖动实验报告

一、实验背景近年来,汽车发动机抖动现象日益普遍,给驾驶者带来了诸多不便。
为了探究发动机抖动的原因,并寻求有效的解决措施,本实验对一辆2019年生产的1.5T涡轮增压发动机进行了深入研究。
二、实验目的1. 分析发动机抖动的原因;2. 探索解决发动机抖动的方法;3. 为发动机抖动问题提供理论依据。
三、实验方法1. 实验设备:发动机试验台、示波器、万用表、诊断仪等;2. 实验步骤:(1)对发动机进行基础检查,确保发动机运行正常;(2)利用诊断仪读取发动机故障码,初步判断抖动原因;(3)使用示波器检测发动机点火系统、燃油系统、润滑系统等关键部件的工作状态;(4)分析实验数据,找出抖动原因;(5)针对抖动原因,提出解决措施。
四、实验结果与分析1. 实验数据(1)点火系统:点火提前角、点火波形正常;(2)燃油系统:喷油脉宽、喷油压力正常;(3)润滑系统:机油压力、机油温度正常;(4)发动机振动:怠速时振动较大,中高速时振动逐渐减小。
2. 结果分析(1)点火系统:点火系统工作正常,排除点火系统原因;(2)燃油系统:燃油系统工作正常,排除燃油系统原因;(3)润滑系统:润滑系统工作正常,排除润滑系统原因;(4)发动机振动:怠速时振动较大,可能原因如下:a. 活塞连杆机构磨损严重,导致活塞与气缸壁间隙过大;b. 气门弹簧老化,导致气门关闭不严;c. 发动机内部积碳过多,导致燃烧不完全。
五、解决措施1. 对发动机进行拆解,检查活塞连杆机构、气门弹簧等部件;2. 清除发动机内部积碳,提高燃烧效率;3. 更换磨损严重的活塞连杆机构、气门弹簧等部件;4. 对发动机进行磨合,确保各部件配合良好。
六、实验结论通过对发动机抖动原因的分析,确定了活塞连杆机构磨损严重、气门弹簧老化、发动机内部积碳过多等原因。
通过采取相应的解决措施,可以有效解决发动机抖动问题,提高发动机性能。
七、实验总结本次实验对发动机抖动原因进行了深入研究,为发动机抖动问题提供了理论依据。
航空发动机整机振动特性分析

航空发动机整机振动特性分析摘要:本文以涡轮转子工作状态受扭情况分析为出发点,探讨了涡轮转子对涡桨发动机整机振动的影响。
分析得出:关键零组件的机械加工质量是影响航空发动机整机振动的最主要因素,两转子的动平衡质量是影响整机振动的直接因素,装配过程的调整质量是影响整机振动的诱发因素。
并给出了一些可行的整机振动控制措施。
关键词:涡桨发动机航空发动机整机振动控制措施涡轮转子1涡轮转子工作状态受扭情况由于转子系统的振动主要取决于转子系统的质心偏离旋转中心线的距离,即挠度;而对同一轴类零件,抗弯刚度是定值时,挠度大小只与轴所受扭矩成正比。
本文按理想模式简单估算涡轮轴在几种极限状态受扭情况,把其对振动的影响做一个直观的量化比较。
涡轮转子在工作状态下,轴主要受到如下三种扭矩作用:a.涡轮轴内花键分度圆偏心,引起转子质心偏离旋转中心线,质心上的离心力对轴产生扭矩M1。
b.涡轮转子与压气机转子采用松动花键联接,两转子不同心时,花键联接间有摩擦力矩存在,对轴产生扭矩M2。
c.由于涡轮轴加工的形位公差的存在,造成质心偏离旋转中心线,整个涡轮转子作用在质心上的离心力对轴产生扭矩M3。
2 花键联接间摩擦力矩产生的过程发动机压气机转子与涡轮转子采用松动花键联接,花键联接间隙允许两转子不同心,即旋转轴不同直线。
当涡轮轴相对压气机转子旋转轴中心线偏斜(或涡轮轴弯曲变形)时,花键联接下方的点啮合部分最短,上方的点啮合部分最长。
当发动机转子转动时,便可看到沿圆周的各花键齿的啮合长度不断变化。
设想在和涡轮轴一起进动的坐标面上观察,看到转子以一定速度自转,在0位置点啮合长度最短,在2位置啮合长度最长,当转子转动时,花键联接由0-1-2转动,涡轮轴内花键向左深入压气机转子后轴颈外花键中,齿上受到向右的摩擦力作用,相对的一面原在2位置的齿转到3位置再转到0位置,齿逐渐向右移动减小啮合长度,齿上受到向左的摩擦力作用。
在0-1-2面和2-3-0面的摩擦力大小相等方向相反形成摩擦力矩,力矩的方向垂直于涡轮轴,这种摩擦力矩使涡轮转子产生振动失稳。
发动机扭转振动试验研究

10.16638/ki.1671-7988.2020.18.037发动机扭转振动试验研究程勉宏,龚鹏,李播博(沈阳航空航天大学机电工程学院,辽宁沈阳110100)摘要:曲轴的扭转振动是影响发动机安全运行的重要因素之一,因此曲轴扭转振动是发动机研发过程要解决的重要课题。
文章以两款不同的直列四缸发动机为研究对象,用测速齿盘作为发动机扭转振动的测量信号齿盘,介绍了测试齿盘的测试方法,并在发动机台架上进行发动机扭振试验测试,为发动机性能改善提供帮助。
关键词:扭转振动;测速齿盘;试验研究中图分类号:U467.2 文献标识码:A 文章编号:1671-7988(2020)18-108-03An Experimental Research on the Torsional Vibration of Automotive EngineCheng Mianhong, Gong Peng, Li Bobo(School of Mechanical and Electrical Engineering, Shenyang University of Aeronautics and Astronautics,Liaoning Shenyang 110100)Abstract: The torsional vibration of crankshaft is one of the main factors promising the safe operation of engine, therefore the torsional vibration of crankshaft is the key issue during the R&D process of engine. In this paper, the torsional vibration of crankshaft in two different inline four-cylinder engines was studied experimentally. A speed measuring tooth disc was employed as the signal disc during the experimental test for the torsional vibration of the engine. The test procedure was introduced and the bench tests of torsional vibration were carried out for both engines. The results could provide some guidance for engine performance improvement.Keywords: Torsional vibration; Speed measuring tooth disc; Experimental researchCLC NO.: U467.2 Document Code: A Article ID: 1671-7988(2020)18-108-031 前言随着社会的发展,人们对汽车乘座的舒适性要求越来越高,有关汽车发动机的噪声、振动和行驶平顺性(NVH)的研究愈来愈受到人们的重视,发动机曲轴系的扭转振动是汽车发动机NVH分析的重要组成部分。
航空发动机涡扇叶颤振分析与抑制技术研究
航空发动机涡扇叶颤振分析与抑制技术研究航空发动机作为现代航空技术的重要组成部分,其运行状态对于飞机的安全和性能具有重要影响。
然而,在发动机运行过程中,叶片颤振等问题可能会出现,对发动机的安全和性能带来不利影响。
本文将重点探讨航空发动机涡扇叶颤振分析与抑制技术的研究,为保障航空安全做出贡献。
一、航空发动机涡扇叶颤振的原因与机理1.1 原因涡扇叶片颤振是航空发动机中普遍存在的问题,其产生的原因较为复杂。
主要包括以下几点:(1)不同叶片之间的谐波干涉:当叶片振动频率相同或者相差很小时,容易出现谐波干涉。
(2)气动不稳定性:发动机工作时,通过叶片表面的气流产生激振力,其中存在一定的气动不稳定性。
当激振力足够强或者气流不稳定时,便会引起叶片振动。
(3)叶片本身的刚度和阻尼特性:叶片的刚度和阻尼特性是决定其自振频率和阻尼比的重要因素。
当叶片的刚度或阻尼发生变化时,其自振频率和阻尼比也会发生变化,从而引起叶片颤振。
1.2 机理涡扇叶片颤振的机理是叶片激振和非线性能量转移的结果。
其中,叶片激振包括气动激振和结构激振两种方式。
气动激振是由通过叶片表面的气流产生的气动力引起的,而结构激振则是由叶片自身的振动引起的。
叶片振动会使得非线性能量转移到其它振动模态上,这些模态的振幅进一步增强,最终致使叶片颤振。
对于航空发动机来说,叶片颤振问题的解决一直为人所关注。
二、航空发动机涡扇叶颤振的分析方法航空发动机涡扇叶颤振的分析方法主要包括数值模拟和试验两种方式,其中数值模拟采用计算流体力学(CFD)和有限元分析(FEA)等方法,试验则包括基础实验和高速实验。
2.1 数值模拟数值模拟是一种重要的分析涡扇叶颤振的方法,其中,计算流体力学(CFD)和有限元分析(FEA)应用广泛。
(1)计算流体力学(CFD)分析:CFD方法是一种解决流动问题的数值计算方法,可用于模拟空气流动和叶片气动力之间的相互作用。
CFD方法可以提供叶片表面的气动压力、速度和气动力等重要参数,从而帮助确定叶片的气动稳定性和颤振特性。
JIS D1601-1995 汽车零部件振动试验方法(中文版)
IDC 629.113.01 : 620.173.5D 1601汽车零件振动试验方法JIS D 1601平成7年2月1日修改日本工业标准调查会审议(日本标准协会发行)日本工业标准JIS汽车零件振动试验方法D1601-19951.适用范围 本标准规定了汽车零件(以下称零件)的振动试验方法。
2.试验种类 试验种类分以下几类。
⑴ 共振点检测试验 求零件共振振动频率的试验⑵ 振动性能试验 研究施振时零件性能的试验⑶ 振动耐久试验 研究以一定的振动频率激振,相对于振动的零件耐久性的试验⑷ 扫描振动耐久试验 研究按同样的比例连续增减振动频率激振,相对于振动的零件耐久性的试验3.振动条件分类 振动性能试验及振动耐久试验的振动条件分以下几种。
⑴ 零件的振动条件,按被安装的汽车的种类分:1种 主要指轿车系列2种 主要指公共汽车系列3种 主要指货车系列4种 主要指二轮汽车系列⑵ 零件振动条件按,被安装的状态分:A种 安装在车体或悬架装置的弹簧上,振动较小时B种 安装在车体或悬架装置的弹簧上,振动较大时C种 安装在发动机上,振动较小时D种 安装在悬架装置的弹簧下和安装在发动机上,振动较大时,振动条件分类及相应产品示例如参考表1。
4.试验条件4.1试验顺序 试验按共振点检测试验,振动性能试验,振动耐久试验或扫描振动耐久试验的顺序 进行。
不过,共振点检测试验和振动性能试验,或共振点检测试验和振动性能试验及扫描振动耐久试验同时进行也可以。
4.2 零件的安装 零件安装在振动试验台上的状态原则上应接近于零件的使用状态。
4.3 零件的动作 试验原则上要按零件的动作状态进行。
4.4 施振方法 相对于零件的安装状态,按顺序施加上下、左右、前后垂直的简谐振动。
但是,简谐振动的高次谐波含有率⑴,原则上在振动加速度的25%以内。
注⑴:简谐振动的高次谐波含有率的计算如下:⑴以正弦波振动的振动加速度±a(m/s2),按下式计算:a=Kf2A×10-3其中,K=2π2≈19.74f:振动频率(Hz)A:全振幅(mm)24附图2 振动频率67Hz时的振幅7D 1601 1995附图3 振动频率133Hz时的振幅8附图4 振动频率167Hz时的振幅9附图5 振动频率200Hz时的振幅10附图6 振动频率400Hz时的振幅1112。
《汽车动力总成悬置系统振动分析及优化设计》
《汽车动力总成悬置系统振动分析及优化设计》篇一一、引言随着汽车工业的快速发展,汽车动力总成悬置系统的性能对整车舒适性和耐久性的影响日益显著。
汽车动力总成悬置系统作为连接发动机和车身的重要部分,其振动特性的优劣直接关系到整车的运行平稳性和乘坐舒适性。
因此,对汽车动力总成悬置系统的振动进行分析及优化设计显得尤为重要。
本文旨在探讨汽车动力总成悬置系统的振动分析方法及优化设计策略。
二、汽车动力总成悬置系统概述汽车动力总成悬置系统主要由发动机、悬置支架、橡胶衬套、减震器等组成,其作用是支撑和固定发动机,减少发动机振动对整车的影响,保证车辆行驶的平稳性和乘坐的舒适性。
三、汽车动力总成悬置系统振动分析1. 振动来源分析汽车动力总成悬置系统的振动主要来源于发动机的运转和路面传递的振动。
发动机的运转会引发振动和噪声,这些振动和噪声会通过悬置系统传递到整车。
此外,路面不平度等外界因素也会引起汽车的振动,进而影响到动力总成悬置系统的稳定性。
2. 振动传递路径分析汽车动力总成悬置系统的振动传递路径主要包括发动机与悬置支架之间的连接、悬置支架与车身之间的连接等。
在振动传递过程中,各部分之间的相互作用和影响会导致振动的传递和衰减过程复杂多变。
3. 振动特性分析针对汽车动力总成悬置系统的振动特性,可采用实验和仿真分析方法。
实验方法主要包括模态测试、频谱分析等,可获取系统在不同工况下的振动特性;仿真分析则可通过建立动力学模型,分析系统在不同参数下的振动响应。
四、汽车动力总成悬置系统优化设计针对汽车动力总成悬置系统的振动问题,可采取以下优化设计策略:1. 材料选择与结构优化选用高强度、低刚度的材料,如铝合金等,以减轻系统重量,提高系统刚度和减震性能。
同时,对系统结构进行优化设计,如改进悬置支架的结构布局、优化橡胶衬套的形状和硬度等。
2. 动力学参数优化通过仿真分析,调整系统动力学参数,如刚度、阻尼等,以改善系统的振动特性。
同时,根据实际工况和需求,合理匹配发动机与车身的连接方式,以降低整车的振动水平。
发动机振动特性分析与试验(精)
发动机振动特性分析与试验(精)发动机振动特性分析与试验作者:长安汽车工程研究院来源:AI汽车制造业完善的项目前期工作预示着更少的项目后期风险,这也是CAE工作的重要意义之一。
在整机开发的前期(概念设计和布置设计阶段),由于没有成熟样机进行NVH试验,很难通过试验的方法预测产品的NVH水平。
因此,通过仿真的方法对整机NVH 性能进行分析甚至优化显得十分重要。
众所周知,发动机NVH是个复杂的概念,包括发动机的振动、噪声以及个体对振动和噪声的主观评价等。
客观地说,噪声与振动也相互联系,因为发动机一部分噪声由结构表面振动直接辐射,另一部分由发动机燃烧和进排气通过空气传播。
除此之外,发动机附件(如风扇)也存在噪声贡献。
本文仅考虑发动机结构振动问题,即在主轴承载荷、燃烧爆发压力和运动件惯性力的作用下,对发动机结构振动进行分析以及与试验的对比。
发动机结构噪声的激励源主要包括燃烧爆发压力、气门冲击、活塞敲击、主轴承冲击、前端齿轮/链驱动和变速器激2. 动力总成模态压缩缩减有限元模型,得到动力总成的刚度、质量、几何以及自由度信息,用于多体动力学分析。
3. 运动件简化模型建立发动机中的部分动件不用进行有限元建模,可作简化处理,形成梁-质量点模型,用于多体动力学分析。
其中包括:活塞组、连杆组和曲轴及其前后端。
4. 动力总成多体动力学分析在定义了动力总成各零部件间连接并且已知各种载荷的情况下,对动力总成进行时域下的多体动力学分析,并对得到的发动机时域和频域下的动态特性进行评判,同时,其输出用于结构振动分析。
5. 动力总成结构振动分析基于多体动力学分析结果,对整个动力总成有限元模型进行强迫振动分析,得到发动机本体、变速器以及各种外围件的表面振动特性,进行评判和结构优化。
实例分析1. 分析对象以一款成熟的直列四缸1.5L发动机为平台,针对其结构振动问题,对其进行结构振动CAE分析,并与其台架试验结果相比较。
发动机的部分参数如下:缸径75mm,冲程85mm,缸间距84mm,最大缸压6MPa。
- 1、下载文档前请自行甄别文档内容的完整性,平台不提供额外的编辑、内容补充、找答案等附加服务。
- 2、"仅部分预览"的文档,不可在线预览部分如存在完整性等问题,可反馈申请退款(可完整预览的文档不适用该条件!)。
- 3、如文档侵犯您的权益,请联系客服反馈,我们会尽快为您处理(人工客服工作时间:9:00-18:30)。
发动机振动特性分析与试验
作者:长安汽车工程研究院 来源:AI 汽车制造业
完善的项目前期工作预示着更少的项目
后期风险,这也是CAE 工作的重要意义之一。
在整机开发的前期(概念设计和布置设计阶段),由于没有成熟样机进行NVH 试验,很难通过试验的方法预测产品的NVH 水平。
因此,通过仿真的方法对整机NVH 性能进行分析甚至优化显得十分重要。
众所周知,发动机NVH 是个复杂的概念,包括发动机的振动、噪声以及个体对振动和噪声的主观评价等。
客观地说,噪声与振动也相互联系,因为发动机一部分噪声由结构表面振动直接辐射,另一部分由发动机燃烧和进排气通过空气传播。
除此之外,发动机附件(如风扇)也存在噪声贡献。
本文仅考虑发动机结构振动问题,即在主轴承载荷、燃烧爆发压力和运动件惯性力的作用下,对发动机结构振动进行分析以及与试验的对比。
发动机结构噪声的激励源主要包括燃烧爆发压力、气门冲击、活塞敲击、主轴承冲击、前端齿轮/链驱动和变速器激励等,这些结构振动又通过缸盖罩、缸盖、缸体和油底壳等传出噪声。
发动机结构振动分析方法简介
图1 发动机结构振动分析方法
如图1所示,发动机结构噪声分析方法包括以下几个步骤:
1. 动力总成FE 建模及模态校核
建立完整的短发动机和变速器装配的有限元模型;对该有限元模型进行模态分析,通过分析结果判断各零件间连接是否完好;通过分析结果判断动力总成整体模态所在频率范围是否合理,零部件的局部模态频率是否合理,若存在整体或局部模态不合理的情况,需要对结构进行初步更改或优化。
2. 动力总成模态压缩
缩减有限元模型,得到动力总成的刚度、质量、几何以及自由度信息,用于多体动力学分析。
3. 运动件简化模型建立
发动机中的部分动件不用进行有限元建模,可作简化处理,形成梁-质量点模型,用于多体动力学分析。
其中包括:活塞组、连杆组和曲轴及其前后端。
4. 动力总成多体动力学分析
在定义了动力总成各零部件间连接并且已知各种载荷的情况下,对动力总成进行时域下的多体动力学分析,并对得到的发动机时域和频域下的动态特性进行评判,同时,其输出用于结构振动分析。
5. 动力总成结构振动分析
基于多体动力学分析结果,对整个动力总成有限元模型进行强迫振动分析,得到发动机本体、变速器以及各种外围件的表面振动特性,进行评判和结构优化。
实例分析
1. 分析对象
以一款成熟的直列四缸1.5L发动机为平台,针对其结构振动问题,对其进行结构振动CAE 分析,并与其台架试验结果相比较。
发动机的部分参数如下:缸径75mm,冲程85mm,缸间距84mm,最大缸压6MPa。
2. 坐标定义
为了便于以后叙述,对动力总成进行了坐标定义(见图2)。
图2 动力总成坐标系
3. 动力总成有限元建模及模态校核
整个动力总成包括42万节点和54万单元。
其中,缸体、缸盖和缸盖罩为六面体单元;油底壳、进排气歧管为四边形壳单元;变速器及支架为二阶四面体单元;其他外围零件则简化为质量点,并通过梁单元与机体相连。
图3为其有限元模型,模态分析结果和试验结果如表所示。
图3 动力总成有限元模型
动力总成固有频率结果
通过上表可以看出,CAE分析和模态试验得到的动力总成主要模态结果比较接近,在允许的误差以内。
所以,此模型具有可信性,可以用于强迫响应计算。
当然,从分析和试验的结果也可以看出,本款发动机的整体弯曲模态偏低,有必要进行结构优化。
动力总成动力学分析
1. 整机台架振动试验
在半消声室中进行整机振动测试(见图4),其中,对多处重要的发动机及其外围部件表面位置安装了传感器。
本实例选择了3处传感器位置进行分析,包括变速器支架端(三向传感器)、差速器底部(三向传感器)以及缸体群部中部(单向传感器)。
传感器输出为速度信号。
试验中测试了发动机在2 000r/min、4500r/min和5 500r/min共3个转速下的振动特性,其中,每个转速下分别对空载、半载和满载进行了测试。
图4 台架及部分传感安装
2. 动力学仿真分析
通过EXCITE Power Unit建立的动力学模型主要包括发动机零部件、零部件间连接和加载载荷信息。
动力学模型为非线性系统,其中包括所有的线性零部件和部分非线性的零部件连接。
由于客观条件的限制,加载载荷只考虑了燃烧压力、主轴承载荷,而配气机构载荷、变速器载荷和活塞敲击没有考虑在内。
另外,分析得到的结果为动力总成的表面速度,用于与试验结果进行对比。
主轴承载荷和气缸爆发压力见图5、图6。
图5 主轴承载荷
图6 气缸爆发压力
计算工况选择发动机满载工况,转速从2 000r/min到5500r/min,每500r/min 计算一次。
3.仿真结果与试验结果的比较
(1)变速器支架端振动结果比较
仿真和试验的1/3倍频程结果和Campbell如图7~9所示。
图7 变速器支架端振动结果比较(2 000r/mim)
图8 变速器支架端振动结果比较(5 500 r/mim)
图9 变速器支架端振动结果比较-Campbell
从结果可以看出,X方向上:计算与试验结果都在4 000r/min以上出现宽频带的响应;500Hz 以下的频率范围中,计算与试验同时反映出3.5和5.5谐次的振动响应,幅值接近105dB;250~500Hz范围内,计算和试验的幅值状态也一致;高速下,高频带700~800Hz反映出另一共振区域,但频率稍有差异。
Y 方向上:计算与试验结果都明确反映了2.5谐次的振动响应;4 500r/mim以上,计算与试验结果都明确反映出200~700Hz的宽频带响应,幅值大小也基本一致。
Z方向上:计算与试验结果都明确反映了2谐次和3.5谐次的振动响应;计算与试验结果都明确反映出,Z向振动以300以下的谐频响应为主,在220Hz附近受动力总成弯曲模态的影响,但无明显的共振现象发生。
(2)差速器底部振动结果比较
类似于变速器支架端振动结果的比较,进行差速器底部仿真和试验结果的比较,得到以下结论:各个转速下,除低频外,两者在整个分析频域下都比较接近;低频处的不协调可能是由于悬置橡胶参数的不准确造成的,需要对橡胶参数进行进一步测试。
(3)缸体群部中部振动结果比较
类似于变速器支架端振动结果的比较,进行缸体群部中部仿真和试验结果的比较可以看出:大部分分析频率范围内,试验和仿真结果比较接近。
结语
基于有限元及系统动力学耦合方法进行发动机振动分析,在一定程度上能够有效地、准确地预测发动机(包括变速器)本身的振动特性。
在没有试验样机的情况下,能够使用该方法结合AVL-EXCITE和相应的有限元分析软件,对发动机的振动特性进行正确地预测和合理的优化工作。
该方法可用于整机振级的判定、悬置位置选择及特性校验、振源及传递特性分析等。