船舶液压设备
液压装置原理在船上的应用

液压装置原理在船上的应用1. 引言液压装置是一种利用液体传递能量的工作原理,在船舶工程中具有广泛的应用。
通过利用液体的不可压缩性和传递力的特性,液压装置可以实现各种船舶工作过程中的动力传递、控制和操作。
本文将介绍液压装置在船上的原理和应用。
2. 液压装置原理液压装置的工作原理是基于液体的不可压缩性。
液压装置将液体从一个位置传输到另一个位置,实现力的传递和动力的控制。
主要包括以下几个基本组成部件:2.1 液体媒介液压装置中使用的液体通常是油,具有良好的润滑性和密封性能。
油液通过泵送、输送和控制来传递力和实现机械的工作。
2.2 液压泵液压泵是液压装置的动力源,通过机械能将液体压缩并推送到系统中。
液压泵可以分为齿轮泵、叶片泵和柱塞泵等类型,根据具体应用的需要选择合适的泵。
2.3 液压缸液压缸是液压装置中的执行部件,通过液体的压力将机械能转化为力,推动船舶各个部件的运动。
液压缸通常由缸筒、活塞和密封件组成。
2.4 液压阀液压阀是液压装置中的控制部件,用于控制液体的流向、流量和压力。
常见的液压阀有换向阀、节流阀、溢流阀等,通过控制液压阀的开关和调节来实现对液压装置的控制。
3. 液压装置在船上的应用液压装置在船舶工程中有广泛应用,涵盖了船舶各个系统和设备的动力传输、控制和操作。
以下是液压装置在船上常见的应用场景:3.1 舵机系统舵机系统是船舶控制系统中的重要组成部分,通过液压装置实现舵盘的转动。
液压装置通过液压泵提供动力,推动液压缸来转动舵盘,从而控制船舶的方向。
3.2 起重设备在船舶的起重设备中,液压装置被广泛应用于起重机、绞车和船舶各个舱口的开闭装置。
液压装置提供了强大的力量和精确的控制,能够满足各种起重操作的需求。
3.3 舱门系统在船舶的舱门系统中,液压装置用于控制舱门的开启和关闭。
通过控制液压阀和液压缸的工作,舱门可以快速、平稳地打开或关闭,确保船舶的密封性和安全性。
3.4 自动控制系统液压装置在船舶的自动控制系统中起着关键作用。
液压控制系统在船舶自动化中的应用
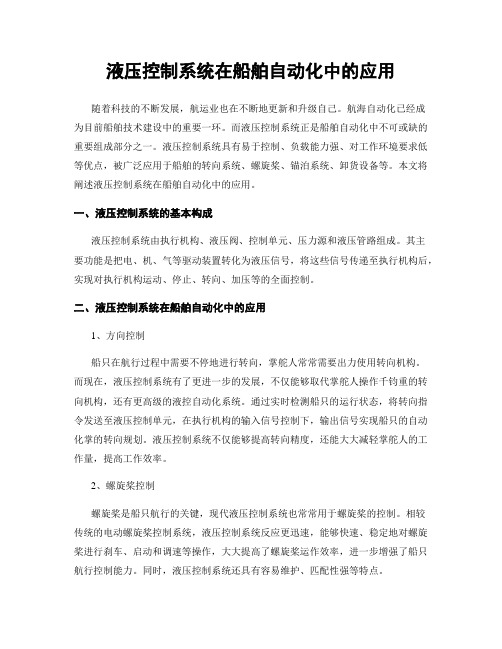
液压控制系统在船舶自动化中的应用随着科技的不断发展,航运业也在不断地更新和升级自己。
航海自动化已经成为目前船舶技术建设中的重要一环。
而液压控制系统正是船舶自动化中不可或缺的重要组成部分之一。
液压控制系统具有易于控制、负载能力强、对工作环境要求低等优点,被广泛应用于船舶的转向系统、螺旋桨、锚泊系统、卸货设备等。
本文将阐述液压控制系统在船舶自动化中的应用。
一、液压控制系统的基本构成液压控制系统由执行机构、液压阀、控制单元、压力源和液压管路组成。
其主要功能是把电、机、气等驱动装置转化为液压信号,将这些信号传递至执行机构后,实现对执行机构运动、停止、转向、加压等的全面控制。
二、液压控制系统在船舶自动化中的应用1、方向控制船只在航行过程中需要不停地进行转向,掌舵人常常需要出力使用转向机构。
而现在,液压控制系统有了更进一步的发展,不仅能够取代掌舵人操作千钧重的转向机构,还有更高级的液控自动化系统。
通过实时检测船只的运行状态,将转向指令发送至液压控制单元,在执行机构的输入信号控制下,输出信号实现船只的自动化掌的转向规划。
液压控制系统不仅能够提高转向精度,还能大大减轻掌舵人的工作量,提高工作效率。
2、螺旋桨控制螺旋桨是船只航行的关键,现代液压控制系统也常常用于螺旋桨的控制。
相较传统的电动螺旋桨控制系统,液压控制系统反应更迅速,能够快速、稳定地对螺旋桨进行刹车、启动和调速等操作,大大提高了螺旋桨运作效率,进一步增强了船只航行控制能力。
同时,液压控制系统还具有容易维护、匹配性强等特点。
3、卸货设备控制在船舶的航行中,经常需要进行货物的装卸。
卸货设备是其中最重要也最关键的环节之一。
传统的卸货设备控制一般都使用电动控制方式,但由于其本身劣势,维护和保养费用较高。
因此,液压控制系统越来越受到船员的欢迎。
液压卸货设备可以通过变换压力或流量,实现平稳地卸货操作,而且胜任重载货物。
在卸货设备控制上,液压控制系统操作也异常操作简便,对于船员的操作难度也大大降低。
船舶液压舵机的若干方面论述

船舶液压舵机的若干方面论述1、舵设备一套完整的舵设备是由舵、舵机、舵角指示器、舵机传动装置和舵角控制装置等设备构成。
在船舶航海及作业过程中,这套设备主要负责把控、调转、保持航向。
在以上设备组成成分当中,最易发生故障的部分便是舵机,因此,船舶设备管理人员、电机员、轮机员等人员要针对该部分的日常保养引起重视。
2、舵机和转舵装置常规的舵机分为两类,一种是电动舵,一种是液压舵机,本文主要分析液压舵机,这是因为现代船舶大体上多使用液压舵机。
液压舵机的原理,顾名思义,是利用液体压力作为舵转动的动力,结构由二个或四个带活塞的液压缸组成,在各液压管与电动泵连接时必须保证液压管系和液缸中盛满液体,也就是使整个液压腔中保持真空,只有液压油介质。
舵机开起时,电动泵转动,电动泵则开始吸排液体,给液压缸提供动力储备,操舵时,通过控制液压油的走向,使得活塞前后移动,从而带动舵柄相接的活塞杆一前一后运动,从而实现转舵。
这类转舵系统最突出的优点便是省力、简易、准确度高、效能高,这也是现代船舶大量使用该类装置的原因。
3、液压舵机的基本要求作为保证操纵性以确保航行安全的重要设备的舵机。
IMO的《国际海上人命安全公约》(SOLAS)和我国《海船规范》均对其提出明确规范与要求,其基本精神是要求舵机必须具有足够的转舵扭矩和转舵速度。
4、操舵器及操舵传动装置操舵传动装置有电动和液压两种。
1.液压操舵传动装置以安装在舵机舱的受动器、安装在驾驶室的液压机以及连接此两者的管系组成。
因为油压的不可缩性以及流向、油压和流量的可控性,所以可将动能转化为液压能,然后进一步转化为机械能,完成转舵。
2.电动操舵传动装置中的手柄操舵与随从操舵并称为该装置的两套独立的操舵系统,其功能在于其中一套系统产生故障之后,即刻可以更换至另一套系统,确保航海安全与航向不偏离。
5、液压舵机的常见故障与分析对于舵机发生故障时原因或部位不明时,首先应该查看舵机油泵的运转状况,事先准备好用于试验的备用泵,并且通过应急操舵来搜寻故障出现的大致范围,最后进行全面罗列分析,找出问题的根源所在并及时排除。
船舶液压知识

第二讲 液压元器件
• 第一节 液压符号 • • 1、固定节流阀
2、可调节流阀
3、粘度节流阀
4、软管连接
5、固定排量油泵
6、变量油泵
7、固定排量双向马达
7、变量双向马达
8、滤器
9、带有指示的滤器
10、具有旁通功能的滤器
11、定压式压力开关
12、可调式压力开关
13、单向止回阀
五.刹车回路
• 该回路是由独立的油泵供油,由 齿轮泵
16排出的液压油,经过阀26保持在 55KG/CM2 ,经电磁阀23,24,25分别控制 钩头马达,吊臂马达,旋转马达的刹车,而这 些电磁阀 则受控制于相应操纵手柄上的微 动开关.当手柄动作时,电磁阀有电,刹车打 开,以便使马达做相应的转动,为了在旋转 停车时,造成吊臂的强烈摆动.旋转刹车回路 中设有单向节流阀32以保证旋转刹车的温 柔性.
叶片马达转子结构
• 1.转子 • 2.5.配油口 • 3.内曲线定子 • 4.补偿弹簧 • 6.柱销 • 7.摇臂 • 8.叶片 • 9.顶杆
3.曲轴连杆式马达
• 工作原理 • 通过配油轴向相应的
4.5缸内注油,同时将 相应的2.3缸卸油,在 马达曲轴上产生径向 侧推分力.
• 通过带动配油轴的转
四. 密封装置类型
• 1. O形圈 DXdXd0
2.Y型密封
• Y形密封使用安装要求 • 1).Y形密封适用于对偶零件做往复
直线运动时的密封。
• 2).在无液体压力下,靠密封圈两
唇边的预压缩量保持自封性
• 3).在 液体压力作用下,使Y形密封
圈两唇边张开,贴紧相对滑动零件 表面和沟槽底面起密封作用。其密 封能力随压力的增高而有所提高, 并能自动补偿磨损
船舶液压系统总结

船舶液压系统总结一、引言船舶液压系统在现代船舶的设计和运行中起着重要的作用。
它们广泛应用于各种船舶设备和系统,包括舵机、起重设备、船舶起重机、锚机等等。
本文将对船舶液压系统进行总结,介绍其工作原理、常见部件以及维护保养等方面内容。
二、工作原理船舶液压系统基于液压原理工作。
其核心是利用流体传递力量,并通过控制液体的流动来实现工作机构的运动。
液压系统通常由液压泵、液压缸和液压阀组成。
液压泵通过产生高压液体,将其输送到液压缸中;液压阀用于控制液体的流动方向和压力。
液压系统能够提供稳定的动力、精确的控制以及高效的传递力量,适用于各种工况。
三、常见部件1. 液压泵液压泵是液压系统的“心脏”,负责产生压力并将液体输送到液压系统中的各个执行元件。
常见的液压泵包括齿轮泵、柱塞泵和涡轮泵等。
液压泵通常需要与驱动装置(如电动机)配合使用。
2. 液压缸液压缸是液压系统中的执行元件,负责将液体的能量转化为机械运动。
液压缸通常由缸体、活塞和密封件组成。
根据需要,液压缸可以实现直线运动或旋转运动。
3. 液压阀液压阀用于控制液体的流动方向、压力和流量。
常见的液压阀包括比例阀、安全阀、方向控制阀和流量控制阀等。
液压阀的选择和设置对于系统的工作效果具有重要影响。
4. 液压油箱液压油箱存储和供给液体,并提供冷却和过滤功能。
液压油箱通常由油箱本体、油位测量器、冷却器和过滤装置等组成。
适当的油量和质量对于系统的正常运行至关重要。
5. 液压管路液压管路用于输送液体,在系统各个部件之间传递压力和动力。
液压管路应具备足够的强度和密封性,避免泄漏和压力损失。
四、维护保养良好的维护保养能够延长船舶液压系统的使用寿命,提高系统的可靠性和效率。
以下是一些常见的维护保养要点:1.定期检查液压系统的油质和油位,及时更换和维护液压油箱。
2.清洁液压元件和管路,防止灰尘和污垢对系统的影响。
3.定期检查液压泵、液压缸和液压阀的工作状态,及时修理或更换故障部件。
船舶常用液压系统
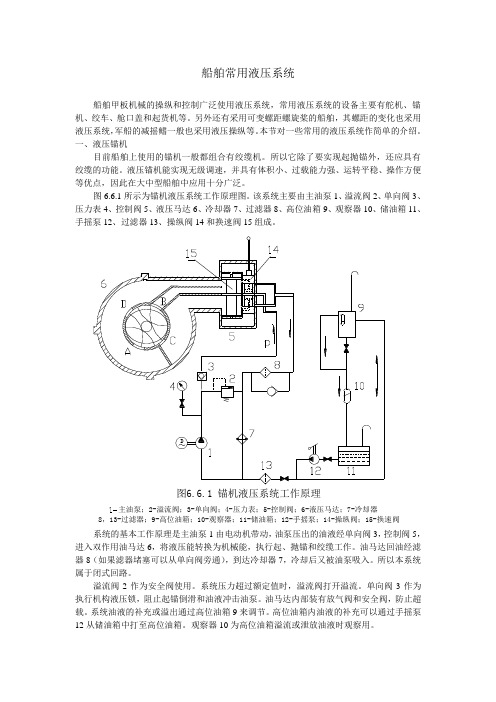
⑸图6.6.2(d)为高速倒车时控制阀阀芯的工作位置。此时控制阀内的换速阀15仍在上方位置,操纵阀14也移至上方位置。油泵压出的油液,经单向阀进入操纵阀的下半部,从阀芯内孔(虚线孔道)流过换速阀的下半部,进入油马达。油流流动方向正好与图6.6.2(c)所示相反,也是单路进油,单路排油,油马达上部工作腔不工作。油马达作顺时针方向旋转。锚机也在高速小扭矩下运转。
2.主油路系统
由于由两个完全相同和独立的系统组成,我们以图6.6.3中右面一半的主油路为例进行
叙述。主油路系统由主泵、活塞油缸Ⅰ和Ⅲ及锥阀1至8组成。其工作原理简述如下:设主泵ZB1的油流方向a为出油口,b为吸油口,这时主泵ZB1输出的压力油分两路,一路是当系统油压超过额定压力时,经由单向阀与溢流阀组成的双向溢流阀组回至主泵吸油口b;而另一路通过液动阀YF1(如图所示位置)进入 锥阀3、7(如图所示位置)。
1.副油路系统
由齿轮泵CB1、溢流阀Y1及精滤器等组成副油路系统,其功能之一是作为主油路的补油系统,在主油路不工作时,使整个主油路充满着油液。在主油路工作时,始终与主油路的主泵吸油口相通,使主泵吸油口始终维持正压状态,避免空气进入主油路系统。同时能将经冷
却的油液带入主油路中,以利于降低系统的油温。功能之二是作为主油路中的YF1、YF2、DY1、DY2、DY3和DY4阀的控制压力油路。
⑷图6.6.2(c)所示为高速正车时控制阀阀芯的工作位置。此时控制阀内的换速阀15移至上方位置(即高速位置),而操纵阀14在下方位置。油泵压出的油液,经单向阀进入操纵阀的上半部,从阀芯内孔(虚线孔道)流过换速阀的上半部,单路进入油马达的下部工作腔A,推动油马达作逆时针方向旋转,C为排油腔。排油的一部分在油马达的上部工作腔B、D作无效循环(由于两腔压差很小)。因此原来
液压舵机
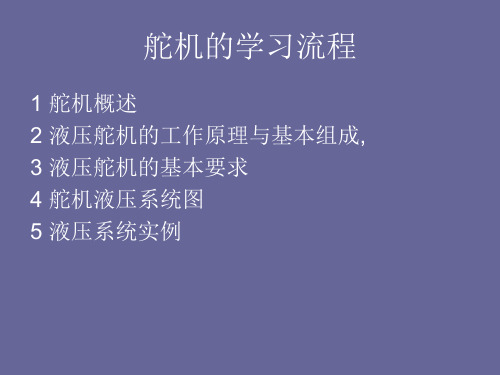
1 舵机概述 2 液压舵机的工作原理与基本组成, 3 液压舵机的基本要求 4 舵机液压系统图 5 液压系统实例
舵机实物图
一、舵机概述 • 舵机是船舶上的一种大甲板机械。舵机的大小由外舾 装按照船级社的规范决定,选型时主要考虑 二、船用舵机类型 • 船用舵机目前多用电液式,即液压设备由电动设备进 行遥控操作。有两种类型: 一种是往复柱塞式舵机,其 原理是通过高低压油的转换而作工产生直线运动,并通过 舵柄转换成旋转运动。另一种是转叶式舵机,其原理是高 低压油直接作用于转子,体积小而高效,但成本较高。 三、工作原理 • 控制电路板接受来自信号线的控制信号(具体信号待会再 讲),控制电机转动,电机带动一系列齿轮组,减速后传 动至输出舵盘。舵机的输出轴和位置反馈电位计是相连的, 舵盘转动的同时,带动位置反馈电位计,电位计将输出一 个电压信号到控制电路板,进行反馈,然后控制电路板根 据所在位置决定电机的转动方向和速度,从而达到目标停 止。
单泵四缸工况——适用于开阔水面正常航行。其最 大扭矩等于公称转舵扭矩,转舵时间能满足规范 要求。 双泵四缸工况——适用于进出港、窄水道航行或其 他要求转舵速度较快的场合,转舵速度较单泵四 缸工况约提高一倍,而转舵扭矩与上述工况相同。 单泵双缸工况——在某缸有故障时采用,这时转舵 速度较单泵四缸工作时约提高一倍,转舵扭矩则 比四缸工作大约减小一半,故必须用限制舵角 (或降低速度)的方法来限制水动力矩,否则工 作油压就可能超过最大工作压力而使安全阀开启。
四、基本组成 液压舵机是电动液压舵机的一种简称,他基本上 由转舵机构、液压系统和操舵控制系统三部分组 成是根据液体的不可压缩性及其流量、压力和流 向的可控性来实现转舵的 • 1、泵控型液压舵机 • 双向变量油泵设于舵机室,由电动机驱动作单 向持续回转,而油泵的流量和吸排方向,则通过 与浮动杆的C相连接的控制杆控制,即依靠油泵 控制C偏离中位的方向和距离,来决定泵的吸排 方向和流量。
船舶液压设备故障的成因分析和诊断

损 、 压元件 的工作不 正常和使用 寿命 的缩 短 。 液
1 14液 压油温过 高或过低 、 .. 油液污染 变质 和
系统压 力恢复正 常 。
某 轮德 国 JW —H G U D 6 4克令 吊在 S A G N SH12
能是液压 泵长期使 用 , 损较 甚 , 磨 内漏 泄量 加 大引
起 。拆 卸检查 齿 轮 泵 , 现泵 齿 轮 磨 损 程 度并 不 发 严重 , 向间隙径 向间 隙稍 有增 大 , 新调 整 间 隙 轴 重 装复后试 车 , 障仍 未 解决 。但 试 车 发 现 系统 原 故
来在 1 2×17 a下 运 转 , 力 平 稳 ,现 在 8× . 0P 压
12 1内在原 因 : 计 安装 不合 要求 , 件加 .. 设 零
工精 度不够 、 质 不 佳 、 能 不好 , 材 性 以及 设 备 经 长
・
4 ・ 9
20 年第4 08 期
期使 用后零 部件 的正 常磨损 等 。
青岛远洋船员学 院学报
V L2 N . O .9 O4
备运转 情况 的不 同 , 清故 障是 在 什 么 条 件 下 产 查
此 要求液压 设 备 必 须具 备 较 高 的 可靠 性 , 以保 证
船舶的安 全航行 和正常运 营。 某轮 在港 卸货期 间 , 由于 下雨 , 紧急关 舱 作业
时 , 现 舱 口 盖 液 压 系 统 压 力 由原 来 的 1 2× 发 .
由此可见, 即使是同一故障现象 , 产生故障的
20 年第 4 08 期
- 1、下载文档前请自行甄别文档内容的完整性,平台不提供额外的编辑、内容补充、找答案等附加服务。
- 2、"仅部分预览"的文档,不可在线预览部分如存在完整性等问题,可反馈申请退款(可完整预览的文档不适用该条件!)。
- 3、如文档侵犯您的权益,请联系客服反馈,我们会尽快为您处理(人工客服工作时间:9:00-18:30)。
船舶液压设备一、液压元件1、液压控制阀分类单向阀溢流阀节流阀a、方向控制阀:换向阀b、压力控制;减压阀c、流量控制阀;普通调速阀液压锁顺序阀溢流节流阀低压选择阀卸荷阀梭阀2、电磁换向阀性能指标:额定压力、额定流量、内漏泄量、压力损失 允许流量不够时可采用:电液换向阀弹簧对中型的换向阀采用:Y 型、H 型 作导阀 油压对中型的换向阀采用:P 型 作导阀3、直动、先导式溢流阀特点4、可作为卸荷阀使用的是:外控顺序阀、先导式溢流阀5、溢流阀与减压阀的比较:6、溢流阀与顺序阀的比较:7、普通调速阀与溢流节流阀的比较:普通调速阀溢流节流阀结构组合 定差减压阀+节流阀 串联定差溢流阀+节流阀 并联压力补偿(负荷增大)减压阀阀口开大 溢流阀阀口开小 调速性 稳定性较好,弹簧较软 稳定性较差,弹簧较硬 油源配合 定压油源,耗功大 定量油源,耗功小适用场合小功率,调速性能要求高的场合大功率,调速性能要求不高的场合泵出口设有溢流阀带安全阀直动式溢流阀先导式溢流阀 动态性能好,静态性能差动态超调量小,偏差大动态性能差,静态性能好 动态超调量大,偏差小偏差值的大小取决于:弹簧刚度 弹簧刚度取决于:油压大小 主阀、导阀弹簧:较软改变导阀弹簧初张力:可改变溢流阀的设定压力稳态压力变化量大,压力超调量较小 稳态压力变化量小,压力超调量较大 用于小流量,低压场合。
宜作安全阀用于大流量,高压场合。
宜作定压阀作用工作形式 泄油方式 管路联接方式溢流阀 进口压力控制,保持阀前压力 常开、常闭 内泄 并接 减压阀出口压力控制,保持阀后压力常开外泄串接出口联接 进出口压差 泄油方式 卸荷方式 管路联接方式溢流阀 油箱/低压油路 很大 内泄 泄压 并接 顺序阀执行元件很小外泄加压串接二、液压泵1、叶片泵A、叶片泵叶片夹角θ、封油区圆心角ε、定子圆弧段圆心角β之间的大小关系:β≥ε≥θβ<ε会发生困油现象ε<θ使吸排口沟通漏泄增加B、单作用与双作用比较单作用双作用叶片底端空间吸排区分分别通吸排油腔通排油腔开“盲孔”使叶片轴向力平衡-排出口叶片转入端开节流槽(三角槽)-减轻液压冲击径向液压力不平衡/非卸荷式平衡/卸荷式叶片槽倾角后倾角前倾角叶片外端倒角后倒角后倒角类型变量泵定量泵2、轴向柱塞泵轴向柱塞泵非对称型配油盘中线相对斜盘中线顺偏转阻尼孔油缸转入端/ 减小液压冲击负重迭型配油盘配油角β>封油角α/ 消除困油开“盲孔”改善润滑三、液压马达1、调速①容积调速:(常采用变量泵/变量马达)改变油泵的q,从而改变马达的供入流量Q改变马达的q②节流调速:(改变流量调节阀供油量)用控制流量控制阀来调节马达的供入流量→存在节流损失,油液会发热2、高、低速马达:n > 500 r/min 为高速有齿轮式、螺杆式、轴向柱塞式n < 500 r/min 为低速有叶片式、径向柱柱塞式3、四种马达的比较低速液压马达性能比较A 、连杆式马达容积效率最高,扭矩脉动率最大,径向负荷最大 进、出油管:轴转式——配油壳上 壳转式——配油轴上B 、内曲线式马达起动效率最高,适用压力最大进、出油管:轴转式——配油轴上(不转) 壳转式——缸体上四、舵机转 舵 机 构十字头式(滑式)拔叉式滚轮式摆缸式转叶式转 舵 扭 矩 舵角↑ ↑ ↑ ↓ ↓ 不变 工作压力 — 最低 最高 — 较低 扭矩特性 最好 — 最差 最差— 侧推力 有(双缸) 无 内部有漏泄无(内部有漏泄)型式往复式 往复式往复式往复式(双作用)回转式单作用 液压马达 多作用 液压马达 名称 连杆 五星轮(静力)内曲 叶片部件受力 比压大 静力平衡 导轨压力大 叶片顶部 径向负荷不平衡基本平衡 完全平衡 完全平衡总效率% 容积效率 机械效率 起动效率 90 96.8 93 83-909095 95 83-9090 95 95 9876.5 <90 <85 80-85最低转速 2-3 20.5 4-6 扭矩脉动率 7.5% 4.9% 0 - 适用压力额定 20.5 17 29 13.5 最大24 28 39 18.5 单位排量的重量(N/ml)1.01.61.350.8双出轴 一般不能 有 不行 可以 壳转式 有 有 有 没有 变量方式偏心距(无级)有效列数有效列数作用数阀控型与泵控型舵机阀控型泵控型系统开式(回油至油箱)、闭式闭式(回油至泵进口)、半闭式主泵单向定量泵双向变量泵安全阀换向阀与定量泵之间换向阀与转舵没油缸之间泵出口转舵改变阀芯位置,主泵吸、排方向不变主泵变量机构偏离中位方向主泵回转方向和速度不变,流量和排油方向可变反馈信号发送器舵柄(带动)舵柄、遥控伺服机构(带动)优点系统简单运行经济性好缺点运行经济性差初投资高差别采用不同的方法控制转舵方向四、液压起货机(单吊杆:3部绞车。
双吊车:2部绞车)1、液压系统的分类1)按工作油压高低分工作油压低压系统: 6.3MPa以下中低压系统: 6.3-10MPa中高压系统:10-20MPa高压系统:20MPa以上采用高压系统优点:尺寸重量较小,效率较高缺点:装置较复杂,制造管理要求高2)按油循环方式分①开式系统:定义:油泵从油箱吸油,执行件回油回油箱特点:简单,初置费较低;散热冷却好,便于气体分离和杂质沉淀,但易混入空气和杂质。
换向阀换向、节流调速,有换向冲击和节流损失,油易发热。
→适用于功率较小场合。
②闭式系统定义:执行件的回油直接进泵的进口特点:一般采用变量泵换向和容积调速,换向平稳,经济性好。
但散热和净化相对较困难,需设辅助系统对油液进行补充、冷却和净化。
3)按控制方式分①泵控系统执行件的运动方向由泵控制一般选用变量泵+闭式系统②阀控系统执行件运动方向由换向阀控制,一般为定量泵+开式系统(也可为闭式系统)2、起货机液压系统类型及特点比较阀控型泵控型系统开式/闭式闭式/半闭式换向换向节流阀液压泵的排油方向调速换向节流阀(并联节流、定差节流调速阀)节流调速变量液压泵容积调速限速平衡阀(直控、远控)、单向节流阀减少变量泵的排量补油不补/高位油箱辅泵主泵单向定量泵/单向变量泵双向变量泵①阀控型闭式系统采用变量油马达(一般是有级变量)时,也辅以容积调速,或采用有级容积调速,辅以节流调速②要进一步限速时也用换向阀节流作能耗限速③如零位不准,也可以设中位旁通阀,改为机械制动3、回转机构液压系统的负荷特点:工作负荷:惯性力+运动阻力A、系统两侧油路高压限制值相同B、启动和停止时惯性负荷相对较大C、匀速转动时,工作负荷始终与运动方向相反D、普通船舶克令吊一般无须限速措施,若考虑恶劣海况下,即船舶倾斜时仍能工作则两则油路都需有限制措施(限速措施)E、设有机械制动器(若无船舶倾斜、风力影响可不用)F、无须专门限制功率的措施泵控型承受高压:液压泵至执行元件进油口的管路在运动时的管路4、对起货机的试验要求1、每台克令吊或每根吊杆应按规定的试验负荷进行试验1)试验负荷(SWL:安全试验负荷)SWL≤20t试验负荷:1.25×SWL20≤50 SWL+5>50 1.1×SWL试验方法吊臂应放在规定的最大臂幅(吊杆规定仰角)位置重物悬挂时间不少于5 min在无法吊起全部负重时,可减少负荷,但不少于1.1SWL试验时应经船检部门同意2)试验内容①在试验负荷下慢速进行起升②最低设计幅度下按设计的极限角度回转③相应动作的制动试验④慢速全程行走试验⑤不同臂幅相应试验负荷试验3)对超负荷保护装置、超力矩保护装置应进行动作试验,负荷指示器应校核5、克令吊的安全保护装置1机械限位保护:1)吊钩高位保护:吊钩离吊臂前端某短距离时无法起升吊钩或下放吊臂2)吊索终端保护:吊索巻满滚筒时吊钩停止提升,滚筒上只剩3圈时停止落钩3)吊臂高位(75°)和低位(25°)保护:吊臂用油缸控制时无须设高位保护吊臂低位保护常设在水平线以上仰角25°处,吊货工作时不允许吊臂仰角低于此限制。
工作结束需要放下吊臂时,必须按下专门按钮。
2设备连锁保护:通风门连锁保护,油冷却器连锁保护等3液压油工作状况保护补油低压控制油低压高油压高油温低油位等保护4电气系统保护:过电流短路等保护五、锚机和绞缆机1、对锚机的基本技术要求1)锚机必须由独立的原动机或电动机驱动。
(采用刚性连接)对于液压锚机,其液压管路如果与其他液压甲板机械管路相连接时,应保证锚机的正常工作不受影响。
2)海船锚机进行起锚试验时,试验水域的深度应>82.5 m,起单锚的速度从82.5 m深度到27.5 m 深度,应≦9 m/min。
(三节锚链进水悬挂,回收二节的平均速度)3)锚机应具有足够的功率,且应能连续工作,其额定拉力和过载拉力应满足下列要求:①锚机应能连续工作30min②应能在过载拉力作用下(不要求速度)连续工作2min。
过载拉力应不小于额定拉力的1.5倍。
4)所有动力操纵的锚机均应能够倒转。
5)保护和刹车装置①锚机的链轮与驱动轴之间应装有离合器,离合器应有可靠的锁紧装置。
②锚机的链轮应装有可靠的制动器,制动器制紧后,应能承受45%锚链断裂负荷的静拉力。
③锚链必须装设有效的止链器,止链器应能承受相当于锚链的试验负荷。
6)液压锚机系统部件应进行液压试验。
所有泵、阀件和附件的受压部件在装配前在车间进行液压试验。
2、对绞缆机的基本技术要求保证船舶在受到6级以下风力作用时仍能系住船舶(风向垂直于船体中心线);绞缆机的拉力大小应符合“钢质海船入级与建造规范”的要求;额定负荷时绞缆速度为15m/min,空载时为公称速度的2-3倍(一般在15~30m/min,最大可达50m/min,达到额定拉力时,可降至最小值)3、自动绞缆机→自动控制缆绳张力(收放缆速度、缆机功率)的绞缆机①采用具有软特性的有级变速交流异步电动机②缆绳收紧后采用低速档。
③当缆绳张力很低时←电动机正转收缆,其转差率s<⒈④当缆绳收紧后张力增加,电机扭矩达到额定值MH时,电动机堵转,s=⒈⑤而当缆绳张力过大时,电机反转松出缆绳,s>1。
六、防止液压装置超负荷(功率)运行:装置负荷可由液压泵工作电流来衡量。
有载负荷包括执行件的负荷、液压泵和执行件的机械摩擦损失、管路流动损失等。
举例:1)空转电流与空载电流2)有载电流(电压)与空载电流(电压)之差3)执行机构空载油压与压降。