激光深熔焊接的主要工艺参数(精)
激光焊接工艺参数

激光焊接工艺参数激光焊接是一种高效、高质量、非接触的焊接方法,广泛应用于精密零件的制造、电子产品的组装、汽车工业、航空航天等领域。
激光焊接工艺参数对焊接质量和效率起着重要的影响。
下面将介绍一些常用的激光焊接工艺参数。
1.激光功率:激光焊接的功率决定了熔池的温度和熔化的能量。
功率过高会导致焊缝过深、过宽,功率过低则影响焊接质量。
根据不同材料和焊接要求,选择合适的激光功率,通常在几百瓦到几千瓦之间。
2.焦距:焦距是指激光束通过聚焦镜后在焊接部位形成的焦点与工件表面之间的距离。
焦距的选择与焊接材料的厚度、焊枪的设计、激光束的直径等因素相关。
焦距过大会导致焊接深度不够,焦距过小则容易引起溅射和熔洞。
3.光斑直径:光斑直径影响焊缝的宽度和深度。
通常情况下,焊接深度正比于光斑直径的平方。
选择合适的光斑直径可以控制焊缝的大小和形状。
4.扫描速度:扫描速度是指焊接头在工件上移动的速度。
扫描速度的选择要根据焊接材料的导热性和热膨胀系数来确定。
过高的扫描速度可能导致焊缝无法充分熔化,过低的扫描速度则容易引起过热和熔洞。
5.激光脉冲频率:激光脉冲频率决定了激光束的脉冲数。
较低的脉冲频率可以增加焊缝的深度,较高的脉冲频率则可以增加焊缝的宽度。
根据焊接要求选择合适的脉冲频率。
6.各向异性系数:各向异性系数是指焊接材料在激光束照射下沿不同方向扩散的能力。
不同金属材料的各向异性系数差异较大,选择合适的激光焊接参数可以减小焊缝形状的变化。
7.激光束模式:激光束的光斑形状可以通过调整激光器的谐振腔或使用适当的光学元件来改变。
常见的激光束模式包括高斯模式、倍高斯模式和束团模式等。
不同的光斑形状对焊接质量和效率有影响。
总结起来,激光焊接工艺参数包括激光功率、焦距、光斑直径、扫描速度、激光脉冲频率、各向异性系数和激光束模式等。
通过合理地选择这些参数,可以实现高质量、高效率的激光焊接。
激光焊接的工艺参数及特性分析讲解
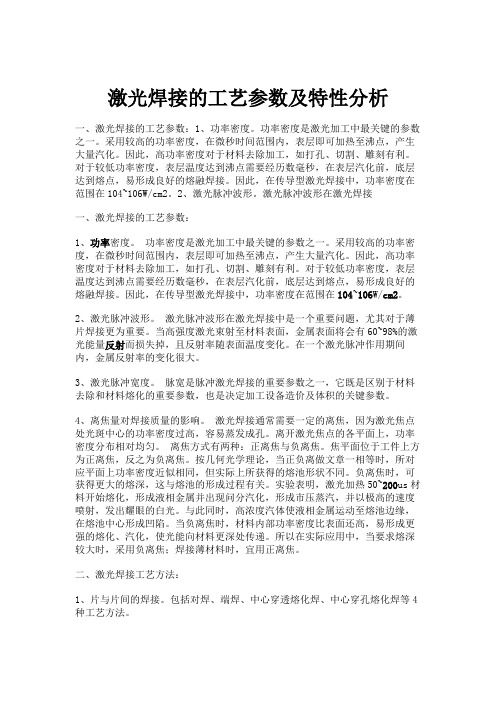
激光焊接的工艺参数及特性分析一、激光焊接的工艺参数:1、功率密度。
功率密度是激光加工中最关键的参数之一。
采用较高的功率密度,在微秒时间范围内,表层即可加热至沸点,产生大量汽化。
因此,高功率密度对于材料去除加工,如打孔、切割、雕刻有利。
对于较低功率密度,表层温度达到沸点需要经历数毫秒,在表层汽化前,底层达到熔点,易形成良好的熔融焊接。
因此,在传导型激光焊接中,功率密度在范围在104~106W/cm2。
2、激光脉冲波形。
激光脉冲波形在激光焊接一、激光焊接的工艺参数:1、功率密度。
功率密度是激光加工中最关键的参数之一。
采用较高的功率密度,在微秒时间范围内,表层即可加热至沸点,产生大量汽化。
因此,高功率密度对于材料去除加工,如打孔、切割、雕刻有利。
对于较低功率密度,表层温度达到沸点需要经历数毫秒,在表层汽化前,底层达到熔点,易形成良好的熔融焊接。
因此,在传导型激光焊接中,功率密度在范围在104~106W/cm2。
2、激光脉冲波形。
激光脉冲波形在激光焊接中是一个重要问题,尤其对于薄片焊接更为重要。
当高强度激光束射至材料表面,金属表面将会有60~98%的激光能量反射而损失掉,且反射率随表面温度变化。
在一个激光脉冲作用期间内,金属反射率的变化很大。
3、激光脉冲宽度。
脉宽是脉冲激光焊接的重要参数之一,它既是区别于材料去除和材料熔化的重要参数,也是决定加工设备造价及体积的关键参数。
4、离焦量对焊接质量的影响。
激光焊接通常需要一定的离焦,因为激光焦点处光斑中心的功率密度过高,容易蒸发成孔。
离开激光焦点的各平面上,功率密度分布相对均匀。
离焦方式有两种:正离焦与负离焦。
焦平面位于工件上方为正离焦,反之为负离焦。
按几何光学理论,当正负离做文章一相等时,所对应平面上功率密度近似相同,但实际上所获得的熔池形状不同。
负离焦时,可获得更大的熔深,这与熔池的形成过程有关。
实验表明,激光加热50~200us材料开始熔化,形成液相金属并出现问分汽化,形成市压蒸汽,并以极高的速度喷射,发出耀眼的白光。
激光深熔焊接的主要工艺参数

激光深熔焊接的主要工艺参数1.激光功率激光功率是指激光输出的功率大小。
激光功率的选择应根据材料的类型、厚度和焊接速度等因素进行调整。
功率过低会导致无法完全融化焊缝,形成不良的焊接缺陷;功率过高会使焊缝产生过多的热影响区,导致焊缝变形和质量降低。
因此,激光功率的选择应根据焊接要求进行合理调节。
2.焦斑大小焦斑大小是指激光束在焊接材料表面形成的点状或圆形热源的直径。
焦斑大小的选择应根据焊接材料的类型和厚度进行调整。
焦斑过大会导致焊接热输入过大,造成材料的过热和烧穿现象;焦斑过小会导致焊接速度降低、焊缝长度增加,降低焊接效率。
因此,合理选择焦斑大小可以提高焊接质量和效率。
3.焦距焦距是指激光焦点到工件表面的距离。
焦距的选择应根据焊接材料的类型、厚度和焦斑大小进行调整。
焦距过小会导致焊接过程中激光束发散,焦点变大,影响焊缝质量;焦距过大会使激光束发散度增加,焦斑变大,导致焊缝质量下降。
因此,选择合适的焦距可以提高焊接质量和效率。
4.焦点位置焦点位置是指激光焦点相对于焊接材料表面的位置。
焦点位置的选择应根据焊接材料的类型、厚度和焦斑大小进行调整。
焦点位置过高会使激光热输入不够,焊缝没有完全熔化;焦点位置过低会导致焊接热输入过大,材料出现烧穿和变形现象。
因此,选择合适的焦点位置可以保证焊接质量和效率。
5.激光扫描速度激光扫描速度是指激光束在焊接过程中的移动速度。
激光扫描速度的选择应根据焊接材料的类型、厚度和焦斑大小进行调整。
扫描速度过慢会使焊缝长度增加,降低焊接效率;扫描速度过快会导致焊接热输入不够,焊缝没有完全熔化。
因此,选择适当的激光扫描速度可以提高焊接质量和效率。
6.气体保护气体保护是指在激光焊接过程中向焊缝区域供应保护气体,主要用于防止焊缝区域氧化和污染。
常用的保护气体有氩气、氮气和二氧化碳等。
优化气体保护可以改善焊缝质量并防止焊缝氧化。
因此,通过合理调节激光功率、焦斑大小、焦距、焦点位置、激光扫描速度和气体保护等工艺参数,可以实现激光深熔焊接的高质量和高效率。
激光焊接的工艺参数及特性分析讲解

激光焊接的工艺参数及特性分析讲解激光焊接是一种高能量密度激光束对焊接材料表面的作用,通过将激光束转化为热能,快速熔化并凝固焊缝来实现材料的连接。
激光焊接具有高耦合性、无接触和非传导性等特点,因此在许多领域得到广泛应用。
本文将对激光焊接的工艺参数及特性进行分析和讲解。
激光焊接的工艺参数主要包括激光功率、激光束面积、焦距、焊接速度和焊接气体等。
其中,激光功率是指单位时间内激光束所携带的能量,对焊接效果起到重要作用。
激光功率过低会导致焊缝不完全熔透,功率过高则容易产生毛刺。
激光束面积与焦距的选择会直接影响到焊接区域的集中度,过小会导致焊缝质量不稳定,过大则会降低焊接深度。
焊接速度决定了焊接过程中激光束的作用时间,过慢会导致过量热输入,过快则会影响焊缝的质量。
焊接气体的选择和流量控制对焊接质量也有着重要影响,一方面可以提供保护气氛,防止焊缝氧化或与空气中的杂质反应;另一方面可以有效盖住激光束与材料的相互作用。
激光焊接的特性分析主要包括焊接速度、热输入、焊缝形貌和焊接缺陷等。
焊接速度是决定焊接效果的重要因素之一,其取值应根据材料的熔化温度和焊缝的质量要求进行合理选择。
热输入则是指焊接过程中单位长度内传递给焊接区域的能量,直接影响着焊缝的熔透度和凝固组织。
热输入过小会导致焊缝凝固不完全,热输入过大则易产生裂纹和变形等缺陷。
焊缝形貌与焊接参数密切相关,激光焊接通常能够产生较窄而深的焊缝,焊缝形貌的良好与否直接关系到焊接质量。
焊接缺陷主要包括焊接裂纹、焊接变形和焊接缺陷等,这些缺陷的产生通常与焊接参数的选择不当和焊接材料的特性有关。
总之,激光焊接的工艺参数及特性对焊接质量起着至关重要的影响。
合理选择并控制这些参数可以提高焊接效率和质量,确保焊接结果符合设计要求。
因此,在实际应用中需要综合考虑各个参数之间的关系,通过优化调整,找到最佳的参数组合,从而实现高质量的激光焊接。
激光焊接工艺参数讲解

激光焊接原理与主要工艺参数作者:opticsky 日期:2006-12-01字体大小: 小中大1.激光焊接原理激光焊接可以采用连续或脉冲激光束加以实现,激光焊接的原理可分为热传导型焊接和激光深熔焊接。
功率密度小于104~105 W/cm2为热传导焊,此时熔深浅、焊接速度慢;功率密度大于105~107 W/cm2时,金属表面受热作用下凹成“孔穴”,形成深熔焊,具有焊接速度快、深宽比大的特点。
其中热传导型激光焊接原理为:激光辐射加热待加工表面,表面热量通过热传导向内部扩散,通过控制激光脉冲的宽度、能量、峰功率和重复频率等激光参数,使工件熔化,形成特定的熔池。
用于齿轮焊接和冶金薄板焊接用的激光焊接机主要涉及激光深熔焊接。
下面重点介绍激光深熔焊接的原理。
激光深熔焊接一般采用连续激光光束完成材料的连接,其冶金物理过程与电子束焊接极为相似,即能量转换机制是通过“小孔”(Key-hole)结构来完成的。
在足够高的功率密度激光照射下,材料产生蒸发并形成小孔。
这个充满蒸气的小孔犹如一个黑体,几乎吸收全部的入射光束能量,孔腔内平衡温度达2500 0C左右,热量从这个高温孔腔外壁传递出来,使包围着这个孔腔四周的金属熔化。
小孔内充满在光束照射下壁体材料连续蒸发产生的高温蒸汽,小孔四壁包围着熔融金属,液态金属四周包围着固体材料(而在大多数常规焊接过程和激光传导焊接中,能量首先沉积于工件表面,然后靠传递输送到内部)。
孔壁外液体流动和壁层表面张力与孔腔内连续产生的蒸汽压力相持并保持着动态平衡。
光束不断进入小孔,小孔外的材料在连续流动,随着光束移动,小孔始终处于流动的稳定状态。
就是说,小孔和围着孔壁的熔融金属随着前导光束前进速度向前移动,熔融金属充填着小孔移开后留下的空隙并随之冷凝,焊缝于是形成。
上述过程的所有这一切发生得如此快,使焊接速度很容易达到每分钟数米。
2. 激光深熔焊接的主要工艺参数1激光功率。
激光焊接中存在一个激光能量密度阈值,低于此值,熔深很浅,一旦达到或超过此值,熔深会大幅度提高。
激光焊接工艺方法和技术

激光焊接工艺方法和技术激光焊接是激光加工材料加工技术应用的重要方面之一。
70年代主要用于焊接薄壁材料和低速焊接,焊接过程属于热传导型,即激光辐射加热工件表面,表面热量通过热传导向内部扩散,通过控制激光脉冲的宽度、能量、峰值功率和重复频率等参数,使工件熔化,形成特定的熔池。
由于激光焊接作为一种高质量、高精度、低变形、高效率和高速度的焊接方法,随着高功率CO2和高功率的YAG 激光器以及光纤传输技术的完善、金属钼焊接聚束物镜等的研制成功,使其在机械制造、航空航天、汽车工业、粉末冶金、生物医学微电子行业等领域的应用越来越广。
一、激光焊接的工艺参数。
1、功率密度。
功率密度是激光加工中最关键的参数之一。
采用较高的功率密度,在微秒时间范围内,表层即可加热至沸点,产生大量汽化。
因此,高功率密度对于材料去除加工,如打孔、切割、雕刻有利。
对于较低功率密度,表层温度达到沸点需要经历数毫秒,在表层汽化前,底层达到熔点,易形成良好的熔融焊接。
因此,在传导型激光焊接中,功率密度在范围在104~106W/cm2。
2、激光脉冲波形。
激光脉冲波形在激光焊接中是一个重要问题,尤其对于薄片焊接更为重要。
当高强度激光束射至材料表面,金属表面将会有60~98%的激光能量反射而损失掉,且反射率随表面温度变化。
在一个激光脉冲作用期间内,金属反射率的变化很大。
3、激光脉冲宽度。
脉宽是脉冲激光焊接的重要参数之一,它既是区别于材料去除和材料熔化的重要参数,也是决定加工设备造价及体积的关键参数。
4、离焦量对焊接质量的影响。
激光焊接通常需要一定的离做文章一,因为激光焦点处光斑中心的功率密度过高,容易蒸发成孔。
离开激光焦点的各平面上,功率密度分布相对均匀。
离焦方式有两种:正离焦与负离焦。
焦平面位于工件上方为正离焦,反之为负离焦。
按几何光学理论,当正负离做文章一相等时,所对应平面上功率密度近似相同,但实际上所获得的熔池形状不同。
负离焦时,可获得更大的熔深,这与熔池的形成过程有关。
影响激光焊接质量的工艺参数

影响激光焊接质量的工艺参数
激光焊接的过程中,有时候会出现焊接不好的情况,大家知道影响这些焊接工艺的参数都有哪些吗?关于影响焊接质量的焊接工艺参数主要有激光输出功率、焊接速度、激光波形、脉冲宽度、离焦量和保护气体。
输出功率、焊接速度对熔深的影响。
激光波形主要有脉冲激光器常用的脉冲波形
和连续焊接时的缝焊波形。
脉冲波形对焊接质量的影响(针对脉冲激光器)
◆对于焊接铜、铝、金、银高反射材料时,为了突破高反射率的屏障,可以利
用带有前置尖峰的激光波形。
但这种波形在高重复率缝焊时不宜采用,容易产生飞溅,形成不规则的孔洞。
◆对于铁、镍等黑色金属,表面反射率低,宜采用矩形波或缓衰减波形。
连续焊接时的缝焊波形:焊波形就是激光功率随焊接时间变化的曲线。
在材料要求焊接密封时此波形尤为重要。
在焊接开始时激光功率缓慢上升,结束时缓慢下降,在连续激光器焊接时,结尾处出现的凹坑,宜采用此波形,减小凹坑程度,
以达到焊接效果。
脉冲宽度(针对脉冲激光器):光的脉冲宽度针对YAG固体激光器来说是焊接的重要参数之一,它决定材料是否熔化,为了保证激光焊接中材料表面不出现强烈
气化,一般假定在脉冲终止时材料表面温度达到沸点。
脉宽越长,焊点直径越大,相同的工作距离时,熔深越深。
激光焊的主要工艺参数对焊接质量的影响

激光焊的主要工艺参数对焊接质量的影响激光焊是一种应用激光技术进行焊接的新型焊接方法。
激光焊具有高能量浓度、局部加热快、热效应小等优点,因此在航空航天、汽车制造、电子设备等领域得到了广泛应用。
激光焊的主要工艺参数包括激光功率、激光束直径、焊接速度、焊缝型式等,这些工艺参数对于焊接质量具有重要影响。
首先,激光功率是指激光发射的能量大小,在激光焊中,激光功率的大小直接影响焊接温度和热输入。
激光焊中,激光功率过小会导致焊接质量不达标,焊缝内可能存在未熔化或未完全熔化的金属颗粒;激光功率过大则容易造成焊缝过宽和过深,引起焊接后的热影响区扩大和凝固裂纹等问题。
因此,选择适当的激光功率对于焊接质量的保障至关重要。
其次,激光束直径是指激光束在焊接过程中的有效焦点直径。
激光束直径的大小会影响激光焊缝的宽度和形状,从而影响焊接质量。
激光束直径过大会导致焊缝宽度过大,影响焊缝质量;而激光束直径过小则会导致焊缝过窄,增加焊接难度。
因此,激光束直径的选择要依据焊接材料和焊接要求进行合理调整,以保证焊接质量。
第三,焊接速度是指激光照射到工件上时,焊接头沿焊缝方向移动的速度。
焊接速度的快慢对焊接质量有直接影响。
焊接速度过快会导致焊接缺陷,如焊缝内夹杂物和未充分熔化区域增加,降低焊缝的连接强度。
而焊接速度过慢会导致焊缝过宽,焊接热影响区增大,易产生开裂等缺陷。
因此,选择适当的焊接速度对于焊接质量的保证至关重要。
此外,焊缝型式也会对焊接质量产生重要影响。
不同的焊缝型式适用于不同的焊接工艺和材料。
一般有点焊、连续焊、螺旋焊等。
选择正确的焊缝型式可以提高焊接强度和焊接质量。
综上所述,激光焊的主要工艺参数包括激光功率、激光束直径、焊接速度和焊缝型式等,这些参数的选择和调整对焊接质量起到重要作用。
在进行激光焊时,需要根据具体的焊接要求和材料特性,合理选择和调整这些工艺参数,以达到理想的焊接质量和性能。
- 1、下载文档前请自行甄别文档内容的完整性,平台不提供额外的编辑、内容补充、找答案等附加服务。
- 2、"仅部分预览"的文档,不可在线预览部分如存在完整性等问题,可反馈申请退款(可完整预览的文档不适用该条件!)。
- 3、如文档侵犯您的权益,请联系客服反馈,我们会尽快为您处理(人工客服工作时间:9:00-18:30)。
(一)激光深熔焊接的主要工艺参数1)激光功率。
激光焊接中存在一个激光能量密度阈值,低于此值,熔深很浅,一旦达到或超过此值,熔深会大幅度提高。
只有当工件上的激光功率密度超过阈值(与材料有关),等离子体才会产生,这标志着稳定深熔焊的进行。
如果激光功率低于此阈值,工件仅发生表面熔化,也即焊接以稳定热传导型进行。
而当激光功率密度处于小孔形成的临界条件附近时,深熔焊和传导焊交替进行,成为不稳定焊接过程,导致熔深波动很大。
激光深熔焊时,激光功率同时控制熔透深度和焊接速度。
焊接的熔深直接与光束功率密度有关,且是入射光束功率和光束焦斑的函数。
一般来说,对一定直径的激光束,熔深随着光束功率提高而增加。
2)光束焦斑。
光束斑点大小是激光焊接的最重要变量之一,因为它决定功率密度。
但对高功率激光来说,对它的测量是一个难题,尽管已经有很多间接测量技术。
光束焦点衍射极限光斑尺寸可以根据光衍射理论计算,但由于聚焦透镜像差的存在,实际光斑要比计算值偏大。
最简单的实测方法是等温度轮廓法,即用厚纸烧焦和穿透聚丙烯板后测量焦斑和穿孔直径。
这种方法要通过测量实践,掌握好激光功率大小和光束作用的时间。
3)材料吸收值。
材料对激光的吸收取决于材料的一些重要性能,如吸收率、反射率、热导率、熔化温度、蒸发温度等,其中最重要的是吸收率。
影响材料对激光光束的吸收率的因素包括两个方面:首先是材料的电阻系数,经过对材料抛光表面的吸收率测量发现,材料吸收率与电阻系数的平方根成正比,而电阻系数又随温度而变化;其次,材料的表面状态(或者光洁度)对光束吸收率有较重要影响,从而对焊接效果产生明显作用。
CO2激光器的输出波长通常为10.6μm,陶瓷、玻璃、橡胶、塑料等非金属对它的吸收率在室温就很高,而金属材料在室温时对它的吸收很差,直到材料一旦熔化乃至气化,它的吸收才急剧增加。
采用表面涂层或表面生成氧化膜的方法,提高材料对光束的吸收很有效。
4)焊接速度。
焊接速度对熔深影响较大,提高速度会使熔深变浅,但速度过低又会导致材料过度熔化、工件焊穿。
所以,对一定激光功率和一定厚度的某特定材料有一个合适的焊接速度范围,并在其中相应速度值时可获得最大熔深。
图10-2给出了1018钢焊接速度与熔深的关系。
5)保护气体。
激光焊接过程常使用惰性气体来保护熔池,当某些材料焊接可不计较表面氧化时则也可不考虑保护,但对大多数应用场合则常使用氦、氩、氮等气体作保护,使工件在焊接过程中免受氧化。
氦气不易电离(电离能量较高),可让激光顺利通过,光束能量不受阻碍地直达工件表面。
这是激光焊接时使用最有效的保护气体,但价格比较贵。
氩气比较便宜,密度较大,所以保护效果较好。
但它易受高温金属等离子体电离,结果屏蔽了部分光束射向工件,减少了焊接的有效激光功率,也损害焊接速度与熔深。
使用氩气保护的焊件表面要比使用氦气保护时来得光滑。
氮气作为保护气体最便宜,但对某些类型不锈钢焊接时并不适用,主要是由于冶金学方面问题,如吸收,有时会在搭接区产生气孔。
使用保护气体的第二个作用是保护聚焦透镜免受金属蒸气污染和液体熔滴的溅射。
特别在高功率激光焊接时,由于其喷出物变得非常有力,此时保护透镜则更为必要。
保护气体的第三个作用是对驱散高功率激光焊接产生的等离子屏蔽很有效。
金属蒸气吸收激光束电离成等离子云,金属蒸气周围的保护气体也会因受热而电离。
如果等离子体存在过多,激光束在某种程度上被等离子体消耗。
等离子体作为第二种能量存在于工作表面,使得熔深变浅、焊接熔池表面变宽。
通过增加电子与离子和中性原子三体碰撞来增加电子的复合速率,以降低等离子体中的电子密度。
中性原子越轻,碰撞频率越高,复合速率越高;另一方面,只有电离能高的保护气体,才不致因气体本身的电离而增加电子密度。
表常用气体和金属的原子(分子)量和电离能=========================================================== ==材料氦氩氮铝镁铁------------------------------------------------------------原子(分子)量 4 40 28 27 24 56电离能(eV) 24.46 15.68 14.5 5.96 7.61 7.83=========================================================== ==从表可知,等离子体云尺寸与采用的保护气体不同而变化,氦气最小,氮气次之,使用氩气时最大。
等离子体尺寸越大,熔深则越浅。
造成这种差别的原因首先由于气体分子的电离程度不同,另外也由于保护气体不同密度引起金属蒸气扩散差别。
氦气电离最小,密度最小,它能很快地驱除从金属熔池产生的上升的金属蒸气。
所以用氦作保护气体,可最大程度地抑制等离子体,从而增加熔深,提高焊接速度;由于质轻而能逸出,不易造成气孔。
当然,从我们实际焊接的效果看,用氩气保护的效果还不错。
等离子云对熔深的影响在低焊接速度区最为明显。
当焊接速度提高时,它的影响就会减弱。
保护气体是通过喷嘴口以一定的压力射出到达工件表面的,喷嘴的流体力学形状和出口的直径大小十分重要。
它必须以足够大以驱使喷出的保护气体覆盖焊接表面,但为了有效保护透镜,阻止金属蒸气污染或金属飞溅损伤透镜,喷口大小也要加以限制。
流量也要加以控制,否则保护气的层流变成紊流,大气卷入熔池,最终形成气孔。
为了提高保护效果,还可用附加的侧向吹气的方式,即通过一较小直径的喷管将保护气体以一定的角度直接射入深熔焊接的小孔。
保护气体不仅抑制了工件表面的等离子体云,而且对孔内的等离子体及小孔的形成施加影响,熔深进一步增大,获得深宽比较为理想的焊缝。
但是,此种方法要求精确控制气流量大小、方向,否则容易产生紊流而破坏熔池,导致焊接过程难以稳定。
6)透镜焦距。
焊接时通常采用聚焦方式会聚激光,一般选用63~254mm(2.5”~10”)焦距的透镜。
聚焦光斑大小与焦距成正比,焦距越短,光斑越小。
但焦距长短也影响焦深,即焦深随着焦距同步增加,所以短焦距可提高功率密度,但因焦深小,必须精确保持透镜与工件的间距,且熔深也不大。
由于受焊接过程中产生的飞溅物和激光模式的影响,实际焊接使用的最短焦深多为焦距126mm(5”)。
当接缝较大或需要通过加大光斑尺寸来增加焊缝时,可选择254mm(10”)焦距的透镜,在此情况下,为了达到深熔小孔效应,需要更高的激光输出功率(功率密度)。
当激光功率超过2kW时,特别是对于10.6μm的CO2激光束,由于采用特殊光学材料构成光学系统,为了避免聚焦透镜遭光学破坏的危险,经常选用反射聚焦方法,一般采用抛光铜镜作反射镜。
由于能有效冷却,它常被推荐用于高功率激光束聚焦。
7)焦点位置。
焊接时,为了保持足够功率密度,焦点位置至关重要。
焦点与工件表面相对位置的变化直接影响焊缝宽度与深度。
图2-6表示焦点位置对1018钢熔深及缝宽的影响。
在大多数激光焊接应用场合,通常将焦点的位置设置在工件表面之下大约所需熔深的1/4处。
8)激光束位置。
对不同的材料进行激光焊接时,激光束位置控制着焊缝的最终质量,特别是对接接头的情况比搭接结头的情况对此更为敏感。
例如,当淬火钢齿轮焊接到低碳钢鼓轮,正确控制激光束位置将有利于产生主要有低碳组分组成的焊缝,这种焊缝具有较好的抗裂性。
有些应用场合,被焊接工件的几何形状需要激光束偏转一个角度,当光束轴线与接头平面间偏转角度在100度以内时,工件对激光能量的吸收不会受到影响。
9)焊接起始、终止点的激光功率渐升、渐降控制。
激光深熔焊接时,不管焊缝深浅,小孔现象始终存在。
当焊接过程终止、关闭功率开关时,焊缝尾端将出现凹坑。
另外,当激光焊层覆盖原先焊缝时,会出现对激光束过度吸收,导致焊件过热或产生气孔。
为了防止上述现象发生,可对功率起止点编制程序,使功率起始和终止时间变成可调,即起始功率用电子学方法在一个短时间内从零升至设置功率值,并调节焊接时间,最后在焊接终止时使功率由设置功率逐渐降至零值。
1. 激光深熔焊特征及优、缺点(一)激光深熔焊的特征1) 高的深宽比。
因为熔融金属围着圆柱形高温蒸气腔体形成并延伸向工件,焊缝就变成深而窄。
2) 最小热输入。
因为小孔内的温度非常高,熔化过程发生得极快,输入工件热量很低,热变形和热影响区很小。
3) 高致密性。
因为充满高温蒸气的小孔有利于焊接熔池搅拌和气体逸出,导致生成无气孔的熔透焊缝。
焊后高的冷却速度又易使焊缝组织细微化。
4) 强固焊缝。
因为炽热热源和对非金属组分的充分吸收,降低杂质含量、改变夹杂尺寸和其在熔池中的分布。
焊接过程无需电极或填充焊丝,熔化区受污染少,使得焊缝强度、韧性至少相当于甚至超过母体金属。
5) 精确控制。
因为聚焦光点很小,焊缝可以高精确定位。
激光输出无“惯性”,可在高速下急停和重新起始,用数控光束移动技术则可焊接复杂工件。
6) 非接触大气焊接过程。
因为能量来自光子束,与工件无物理接触,所以没有外力施加工件。
另外,磁和空气对激光都无影响。
(二)激光深熔焊的优点1) 由于聚焦激光比常规方法具有高得多的功率密度,导致焊接速度快,受热影响区和变形都很小,还可以焊接钛等难焊的材料。
2) 因为光束容易传输和控制,又不需要经常更换焊枪、喷嘴,又没有电子束焊接所需的抽真空,显著减少停机辅助时间,所以有荷系数和生产效率都高。
3) 由于纯化作用和高的冷却速度,焊缝强度、韧性和综合性能高。
4) 由于平均热输入低,加工精度高,可减少再加工费用;另外,激光焊接运转费用也较低,从而可降低工件加工成本。
5) 对光束强度和精细定位能有效控制,容易实现自动化操作。
(三)激光深熔焊的缺点1) 焊接深度有限。
2) 工件装配要求高。
3) 激光系统一次性投资较高。