数控车床手工编程技巧
数控车床简化编程技巧

X (6 X )Z ( 6 Z ),R ( 2 R );
X ( )Z ( 8 X8 Z )l 或者
,
X ( )Z ( 4 X4 Z)
X ( )Z ( 5 X5 Z) G0 X ( 3 X7)Z ( ) Z7
G0 一00 ( 1Z 1); C1
M
…
拦旦 磐 圭持 煮燕
数控车床简化编程技巧
浙江 盾安 阀门有 限公 司 ( 诸暨 313 ) 赵 1 8 5 敏
1 运用 工件坐标 系偏 移和调 用子程 序的方 法 .
实现 连续加工 产品
我 们 通 常 在 棒 料 上 加 工 如 图 1 示 的 产 品 , 以 所 前 的 做 法 是 : 当 程 序 结 束 加 工 完 一 个 产 品 时 ,再 把 料 往 外 拉 出 ,拉 出 长 度 以 刀 架 或 刀 头 为 定 位
1
子 程 序
O0 0 0 2 M 0 2 0 TO1 : 3 S1 0 0l G( ⅪX3 O: 2. Z0 :
装 置 ,再 加 工 下 一 个 产
品 。 这 样 仅 增 加 了 操
作 员 工 的 劳 动 强 度 , 而 且 生 产 效 率 低 , 为 解 决
7 2 2 21 0
咖, 咖
荐
冷工 加
O0 ) 001 G 9 l ;8
Z0. 5;
程 和 普通 编 程 对 比 ,如 表2 所示 。
表
图样直接输入编程 X ( )Z ( ),C ( ); X3 Z3 C1
T 1 1 ( 械拉料 器) 00; 机
G01 3 0 5 0l X3 . FI 0
“ Z 1 2” 3
、
“ Z一15 ,分 别 按 软 6”
数控车床手动编程技巧探究
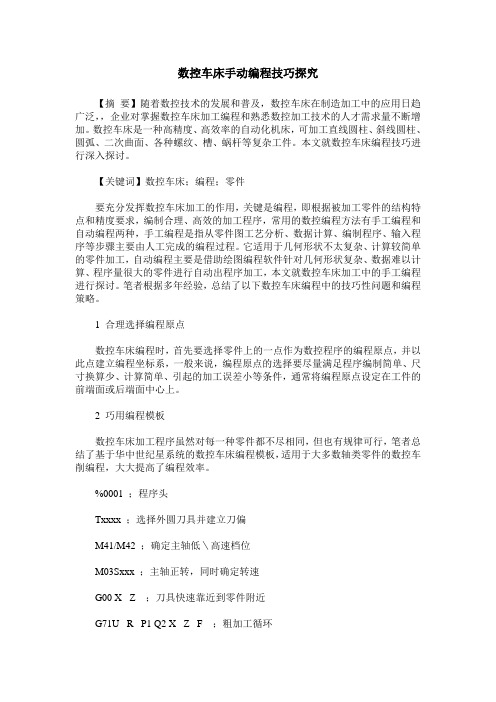
数控车床手动编程技巧探究【摘要】随着数控技术的发展和普及,数控车床在制造加工中的应用日趋广泛,,企业对掌握数控车床加工编程和熟悉数控加工技术的人才需求量不断增加。
数控车床是一种高精度、高效率的自动化机床,可加工直线圆柱、斜线圆柱、圆弧、二次曲面、各种螺纹、槽、蜗杆等复杂工件。
本文就数控车床编程技巧进行深入探讨。
【关键词】数控车床;编程;零件要充分发挥数控车床加工的作用,关键是编程,即根据被加工零件的结构特点和精度要求,编制合理、高效的加工程序,常用的数控编程方法有手工编程和自动编程两种,手工编程是指从零件图工艺分析、数据计算、编制程序、输入程序等步骤主要由人工完成的编程过程。
它适用于几何形状不太复杂、计算较简单的零件加工,自动编程主要是借助绘图编程软件针对几何形状复杂、数据难以计算、程序量很大的零件进行自动出程序加工,本文就数控车床加工中的手工编程进行探讨。
笔者根据多年经验,总结了以下数控车床编程中的技巧性问题和编程策略。
1 合理选择编程原点数控车床编程时,首先要选择零件上的一点作为数控程序的编程原点,并以此点建立编程坐标系,一般来说,编程原点的选择要尽量满足程序编制简单、尺寸换算少、计算简单、引起的加工误差小等条件,通常将编程原点设定在工件的前端面或后端面中心上。
2 巧用编程模板数控车床加工程序虽然对每一种零件都不尽相同,但也有规律可行,笔者总结了基于华中世纪星系统的数控车床编程模板,适用于大多数轴类零件的数控车削编程,大大提高了编程效率。
%0001 ;程序头Txxxx ;选择外圆刀具并建立刀偏M41/M42 ;确定主轴低\高速档位M03Sxxx ;主轴正转,同时确定转速G00 X_ Z_ ;刀具快速靠近到零件附近G71U_ R_ P1 Q2 X_ Z_ F_ ;粗加工循环N1G00/G01……………… ;精加工程序N2 G00/G01…G00X100 ;退刀Z100……M05 ;主轴停止M30 ;程序结束并复位3 理解X、Z坐标含义两轴联动的数控车床一般只有X、Z轴运动,Y轴为虚轴,故参与编程的为X、Z轴,一般情况下X轴表示直径方向尺寸,且为正值;Z轴表示长度方向尺寸,若编程原点设定在前端面中心,则多为负值;若编程原点设定在后端面中心,则为正值4 编程时合理选择进给路线进给路线是刀具在加工过程中的运动轨迹,即刀具从对刀点开始进给运动起,直到结束加工程序后退刀返回该点及所经过的路径,是编写程序的重要依据之一。
数控车床编程
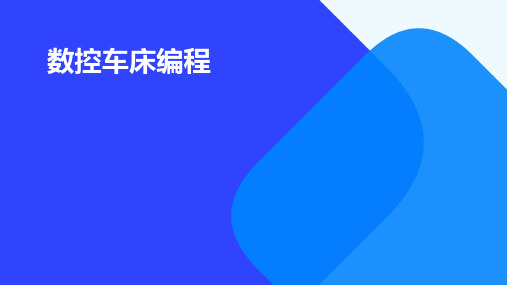
T代码编程语言
T代码编程语言主要用于刀具参数的设置和管理,如刀具号、刀具补偿值 等。
T代码编程语言可以提高加工精度和加工效率,通过合理设置刀具参数, 可以减少换刀次数和加工误差。
T代码编程语言需要在G代码编程语言的基础上使用,以实现完整的加工过 程控制。
03
数控车床编程实例
简单零件的数控车床编程
04
数控车床编程技巧
优化加工路径
减少空行程
在编程时,应尽量减少刀具在空行程中的移动距离,以提高加工效 率。
合理选择切削参数
根据工件材料、刀具类型和加工要求,合理选择切削速度、进给速 度和切削深度等参数,以优化加工效率和加工质量。
考虑刀具补偿
在编程时,应考虑刀具的长度、直径和刀尖半径等参数,进行适当 的补偿,以减小加工误差。
ABCD
第二步是确定加工方案, 包括选择合适的刀具、切 削参数、加工路径等。
第四步是程序调试和优化, 通过实际加工测试和调整, 确保程序能够满足加工要 求。
数控车床编程的注意事项
注意事项一
确保刀具路径的安全性,避免 刀具与工件发生碰撞。
注意事项二
合理选择切削参数,以减小刀 具磨损和保证加工质量。
注意事项三
据,优化生产计划和调度。
跨平台协作
在工业4.0中,数控车床编程将实现与其他制造系统的跨平台 协作,实现数据共享和流程整合,提高生产效率和灵活性。
数控车床编程的未来发展方向
人工智能与机器学习技术的应用
01
未来数控车床编程将更加注重人工智能和机器程。
个性化定制的需求满足
02
随着个性化需求的增加,数控车床编程将更加注重个性化定制,
满足不同加工需求和工艺要求。
数控车倒角C与自动倒圆角R编程方法【详解】

不少人觉得数控车床手工编程遇到圆弧,倒角,计算点位坐标的时候比较繁琐。
今天这篇文章分享两个知识点,让你编程省心又省力。
1, 倒角的图纸标注2,直接图纸编程方法一,倒角的图纸标注1,相互倾斜的两个面上进行倒角,尤其是倒圆角时候,这部分尺寸非常混乱,因此为了明确这部分的尺寸标注,一般情况下,图纸是从倒角的交点处标注。
比如上面简图,两边倒圆角,是以两边延长线的交点P为基准标注的。
而编程的时候,如使用G02/G03需要计算出圆弧起点和终点坐标值。
但是图纸标注的时候大多是以倒角的交点处标注,这也是为什么数车师傅遇到圆弧,采用手工算点比较繁琐的原因了。
2,45度倒角标注,一般用字母C 表示(英语chamfer的第一个字母表示),比如下图:C3此含义是:倒角的斜度为45度,长度为3mm,需要注意的是这个长度不是斜边长度,,而是直边长,如下图所示:二,直接图纸编程方法。
顾名思义也就是按照图纸标注的尺寸来编程。
其格式如下:G01X _Z_R_ (圆弧)G01X _Z_A_ (倒角)也就是在G01指令后面直接添加A或R 。
其中:A为倒角R为倒圆角比如下面简图:A后面的倒角度数是倒角边与Z轴的夹角。
注意:倒角边和Z轴会出现两个比如下面简图:倒角边与Z轴的夹角,仔细看上图,夹角会出现两个数值。
比如C3的倒角:(夹角开口朝向)与Z轴正方向夹角135°与Z轴负方向夹角45°比如上图20度的倒角:与Z轴正方向夹角160°与Z轴负方向夹角20°好,我上面编程的时候选择了与Z轴负方向的夹角,所以A后面为负。
当然你也可以选择与Z轴正方向的夹角,那么下面程序完全等同于上面程序:基于以上分析,我们看下面简图的程序:(车内孔)备注:在用直接图纸编程方式的时候,有些机床需要在A,或R前面添加“逗号”。
比如:G01X24. ,A45.G01 X30. ,A20. ,R5.你可以找到系统参数#3405把第四位CCR设为1,那么字母A,R前面就不需要添加“逗号”。
华中数控818a系统车床手工编程

华中数控818a系统车床手工编程华中数控818a系统是一种智能化数控系统,广泛应用于车床加工领域。
本文将介绍华中数控818a系统车床手工编程的相关知识和技巧。
一、华中数控818a系统概述华中数控818a系统是一种高性能的数控系统,具有强大的功能和灵活的操作。
它采用了先进的技术,能够实现高精度、高效率的车床加工。
该系统具有友好的人机界面,操作简单方便,适用于各类车床加工任务。
二、手工编程基础知识1. G代码和M代码在华中数控818a系统中,手工编程主要使用G代码和M代码。
G代码用于控制刀具的运动轨迹和加工方式,例如G00表示快速定位,G01表示直线插补。
M代码用于控制辅助功能,例如M03表示主轴正转,M08表示冷却液开启。
2. 坐标系和坐标轴华中数控818a系统采用直角坐标系,通过定义坐标轴的正方向和原点位置,确定工件相对于刀具的位置关系。
常用的坐标轴有X轴、Y 轴和Z轴,分别对应工件的长、宽和高方向。
3. 工件坐标系和机床坐标系在手工编程中,需要建立工件坐标系和机床坐标系之间的转换关系。
工件坐标系是以工件为参照,确定工件上各个点的坐标。
而机床坐标系是以机床为参照,确定刀具相对于机床的位置。
三、手工编程步骤1. 确定加工工艺在进行手工编程前,首先需要确定加工工艺,包括切削速度、进给速度、切削深度等参数。
这些参数的选择应根据工件材料和加工要求进行合理的设置。
2. 建立工件坐标系根据工件的几何形状和尺寸,建立工件坐标系。
可以选择工件上的某个点作为原点,然后确定X轴和Y轴的方向,最后确定Z轴的方向。
3. 建立机床坐标系建立机床坐标系是为了将工件坐标系转换为机床坐标系。
根据机床的结构和坐标轴的定义,确定机床坐标系的原点和方向。
4. 编写G代码和M代码根据加工工艺和工件几何形状,编写相应的G代码和M代码。
G代码主要用于控制刀具的运动轨迹,而M代码则用于控制辅助功能。
5. 调试和优化完成手工编程后,需要进行调试和优化。
数控车床编程实例详解(30个例子)

数控车床编程实例详解(30个例子)1. 基础G00轨迹移动G00指令可以用于快速移动机床上的工具,不做切削。
例如,要将铣刀从(0,0,0)点移动到(100,100,0)可以使用下面的编程:G00 X100 Y100 Z02. 简单的G01直线插补3. 向X正方向设定工件原点在某些情况下,需要在工件上设计的特定原点作为整个程序的起点。
在下面的例子中,我们将工件原点移到X轴上的10毫米位置:G92 X104. G02 G03 模拟圆弧G02和G03指令可以用于沿着一条圆弧轨迹移动工具。
例如,以下代码将插入一个逆时针圆弧:G03 X50 Y50 I25 J05. 床上对刀长度测量刀具长度对刀是数控车床操作的重要步骤。
在这个例子中,我们使用手动设定对刀。
首先,我们将铣刀移动到Z轴处的一个位置,然后将刀具轻轻放置在工件上以测量其长度。
最后,我们将刀具测量值输入机床,以便于适当地调整刀具长度。
6. 坐标旋转在某些情况下,需要在XY平面上绕特定角度旋转工件,以便于确保最佳切削角度。
在这个例子中,我们将工件绕着Z轴旋转45度:G68 X0 Y0 R457. 使用M code 启动或停止旋转工件M03用于启动旋转工作台的主轴,M05用于关闭它。
例如,以下代码段启动了工作台的主轴,并等待它旋转到合适速度,以便于切削。
8. 镜像轨迹在制造工具或零件时,可能需要将一个轮廓沿着特定轴镜像。
例如,以下代码镜像X 轴上的轮廓:G01 X50 Y0G01 X0 Y50G01 X-50 Y0G01 X0 Y-50MHE29. 使用G04指令延迟程序G04指令用于程序内部的延迟。
例如,以下代码让机床停顿1秒钟:G04 P100010. 利用G10指令改变工作坐标系G10指令可以用于更改工作坐标系。
例如,下面的代码段将当前坐标系设定为{X50 Y50 Z0}:11. 使用G17, G18和G19指令绘制园形、X-Y平面和Z-X平面G17G02 X50 Y50 I25 J0G02 X0 Y0 I-25 J0G02 X-50 Y50 I0 J25G02 X0 Y100 I25 J0G02 X50 Y50 I0 J-25G02 X0 Y0 I-25 J0MHE2M30指令可以用于彻底结束程序。
数控加工工艺与编程第六章

演讲人:何文
CONTENTS 目录
01 数控车床编程的特点和方法 02 数控车床的对刀 03 数控车床编程实例
6.1数控车床编程的特点和方法
第6章 数控车床的手工编程
数控车床主要用于加工轴类、盘类等回转体零件。车削中心则可在一次装夹中完成更 多的加工工序,大大提高加工精度和生产效率,特别适合于复杂形状回转类零件的加工。通 过加工程序的运行,可自动完成内外圆柱面、圆锥面、成型表面、螺纹和端面等工序的切削加 工,并能进行车槽、钻孔、铰孔等加工。 数控车床的编程特点
第6章 数控车床的手工编程
(3)有的机床具有主轴恒线速控制(G96)和恒转速控制(G97 )的指令功能,那么,对于 端面螺纹和锥面螺纹的加工来说,若恒线速控制有效,则主轴转速将是变化的,这样加工出 的螺纹螺距也将是变化的,所以,在螺纹加工过程中就不应该使用恒线速控制功能。从粗加 工到精加工,主轴转速必须保持一常数。否则,螺距将发生变化。
第6章 数控车床的手工编程
第6章 数控车床的手工编程
循环过程如图6-8所示X,Z为端平面切削终点坐标值,U,W端面切削终点相对循环 起点的坐标增量。
第6章 数控车床的手工编程
2 切削锥面循环时,编程格式:G94 x(U)_ z(W)_ K_ F 循环过程如图6-9所示,K为端面切削始点至终点位移在Z轴方向的坐标增量,图中轨 协K的方向是Z轴的负方向,值为负,反之为正。
⑤精车之前,如需换精加工刀具,则应注意换刀点的选择。批量小不换刀,批量大换刀。 ⑥a的定位:不要使第一刀切在毛坯表皮上,否则容易崩掉刀。可以允许a=毛坯直径。
第6章 数控车床的手工编程
}2)端面粗加工循环(U}2} (U72与G71均为粗加工循环指令,而G72是沿着平行于X轴进行切削循环加工的,适合加工斋类零件。 如图6-11所示,编程格式为
数控车床的编程与调试

数控车床的编程与调试数控车床是一种通过数控系统控制工件加工的机床。
它能够自动完成各种复杂的加工工序,提高工作效率和加工质量。
本文将介绍数控车床的编程与调试方法,以帮助读者更好地了解和掌握这一技术。
一、数控车床编程数控车床编程是指根据工件的加工要求,利用数控系统编写相应的加工程序,将其加载到数控车床上执行的过程。
下面是一般的数控车床编程流程:1. 理解工件要求:首先需要了解工件的尺寸、形状和加工要求等。
这是编写加工程序的基础。
2. 选择编程语言:数控车床编程可以采用不同的编程语言,如G代码、M代码等。
根据实际需要选择合适的编程语言。
3. 编写加工程序:根据工件的要求,编写相应的加工程序。
加工程序包括各种加工指令和参数设置等。
4. 模拟验证:在加载到数控车床之前,可以通过模拟验证来检查加工程序的正确性和合理性。
模拟验证可以减少后续调试的工作量。
5. 加载程序:当加工程序通过模拟验证后,将其加载到数控车床的数控系统中。
可以通过USB或者局域网等方式进行加载。
二、数控车床调试数控车床调试是指在实际加工之前,对数控车床进行参数设置和功能调试的过程。
下面是一般的数控车床调试步骤:1. 安全检查:在进行调试之前,首先要进行安全检查,确保机床的各项安全装置完好可用。
2. 系统参数设置:通过数控系统的参数设置功能,对机床的各项参数进行调整和配置。
参数设置的目的是使机床的功能和性能达到最佳状态。
3. 功能检查:对机床的各个功能进行检查,包括主轴、进给系统、刀具切削等。
通过检查,可以确保各个功能正常工作。
4. 机床调整:根据加工要求,对机床进行必要的调整,如刀具的安装和调整,工件夹持装置的设置等。
5. 故障排除:如果在调试过程中遇到故障,应及时进行排除。
可以根据故障码和机床的相关手册进行故障排查。
6. 加工测试:当机床调试完成后,进行加工测试。
通过加工测试,可以检查加工程序的正确性和加工质量。
三、总结数控车床的编程与调试是使用数控车床进行加工的重要环节。
- 1、下载文档前请自行甄别文档内容的完整性,平台不提供额外的编辑、内容补充、找答案等附加服务。
- 2、"仅部分预览"的文档,不可在线预览部分如存在完整性等问题,可反馈申请退款(可完整预览的文档不适用该条件!)。
- 3、如文档侵犯您的权益,请联系客服反馈,我们会尽快为您处理(人工客服工作时间:9:00-18:30)。
数控车床手工编程技巧
摘要:只有合理运用编程技巧,编制出准确、高效率的加工程序,才能保证加工出符合图纸要求的合格工件,才能使数控车床的功能得到合理的应用与充分的发挥,从而提高生产效率,提高经济效益。
关键词:编程;进给路线;数控;合理
数控编程方法有手工编程和自动编程两种,手工编程是指从零件图样分析、工艺处理、数据计算、编写程序单、输入程序到程序校验等各步骤主要由人工完成的编程过程。
由于每个人的加工方法不同,编制加工程序也各不相同,但最终的目的是为了提高数控车床的生产效率,因此合理运用编程技巧,编制高效率的加工程序,尤为重要。
本文将从五个方面阐述数控车削手工编程技巧。
一、分析零件图样,正确选择程序原点
在数控车削编程时,首先要分析零件图样,选择工件上的一点作为数控程序原点,并以此为原点建立一个工件坐标系。
工件坐标系的合理确定,对数控编程及加工时的工件找正都很重要。
程序原点的选择要尽量满足程序编制简单,尺寸换算少,引起的加工误差小等条件。
为了提高零件加工精度,方便计算和编程,我们通常将程序原点设定在工件轴线与工件前端面、后端面、卡爪前端面的交点上,尽量使编程基准与设计、装配基准重合。
二、合理选择进给路线
进给路线是刀具在整个加工工序中的运动轨迹,即刀具从对刀
点开始进给运动起,直到结束加工程序后退刀返回该点及所经过的路径,是编写程序的重要依据之一。
合理地选择进给路线对于数控加工是很重要的。
应考虑以下几个方面:
(一)尽量缩短进给路线,减少空走刀行程,提高生产效率
(1)巧用起刀点。
如在循环加工中,根据工件的实际加工情况,将起刀点与对刀点分离,在确保安全和满足换刀需要的前提条件下,使起刀点尽量靠近工件,减少空走刀行程,缩短进给路线,节省在加工过程中的执行时间。
(2)在编制复杂轮廓的加工程序时,通过合理安排“回零”路线,使前一刀的终点与后一刀的起点间的距离尽量短,或者为零,以缩短进给路线,提高生产效率。
(3)粗加工或半精加工时,毛坯余量较大,应采用合适的循环加工方式,在兼顾被加工零件的刚性及加工工艺性等要求下,采取最短的切削进给路线,减少空行程时间,提高生产效率,降低刀具磨损。
(二)保证加工零件的精度和表面粗糙度的要求
(1)合理选取起刀点、切入点和切入方式,保证切入过程平稳,没有冲击。
为保证工件轮廓表面加工后的粗糙度要求,精加工时,最终轮廓应安排在最后一次走刀连续加工出来。
认真考虑刀具的切入和切出路线,尽量减少在轮廓处停刀,以避免切削力突然变化造成弹性变形而留下刀痕。
一般应沿着零件表面的切向切入和切出,尽量避免沿工件轮廓垂直方向进、退刀而划伤工件。
(2)选择工件在加工后变形较小的路线。
对细长零件或薄壁零件,应采用分几次走刀加工到最后尺寸,或采取对称去余量法安排进给路线。
在确定轴向移动尺寸时,应考虑刀具的引入长度和超越长度。
(三)保证加工过程的安全性
要避免刀具与非加工面的干涉,并避免刀具与工件相撞。
如工件中遇槽需要加工,在编程时要注意进退刀点应与槽方向垂直,进刀速度不能用“g0”速度。
“g0”指令在退刀时尽量避免“x、z”同时移动使用。
(四)有利于简化数值计算,减少程序段数目和编制程序工作量
在实际的生产操作中,经常会碰到某一固定的加工操作重复出现,可以把这部分操作编写成子程序,事先存入到存储器中,根据需要随时调用,使程序编写变得简单、快捷。
对那些图形一样、尺寸不同或工艺路径一样、只是位置数据不同的系列零件的编程,可以采用宏指令编程,减少乃至免除编程时进行烦琐的数值计算,精简程序量。
三、合理调用g命令使程序段最少
按照每个单独的几何要素(即直线、斜线和圆弧等)分别编制出相应的加工程序,其构成加工程序的各条程序即程序段。
在加工程序的编制工作中,总是希望以最少的程序段数即可实现对零件的加工,以使程序简洁,减少出错的几率及提高编程工作的效率。
由于数控车床装置普遍具有直线和圆弧插补运算的功能,除了非圆弧曲线外,程序段数可以由构成零件的几何要素及由工艺路线确定的各条程序得到,这时应考虑使程序段最少原则。
选择合理的g命令,可以使程序段减少,但也要兼顾走刀路线最短。
四、优化参数,平衡刀具负荷,减少刀具磨损
由于零件结构的千变万化,有可能导致刀具切削负荷的不平衡。
而由于自身几何形状的差异导致不同刀具在刚度、强度方面存在较大差异,例如:正外圆刀与切断刀之间,正外圆刀与反外圆刀之间。
如果在编程时不考虑这些差异,用强度、刚度弱的刀具承受较大的切削载荷,就会导致刀具的非正常磨损甚至损坏,而零件的加工质量达不到要求。
因此编程时必须分析零件结构,用强度、刚度较高的刀具承受较大的切削载荷,用强度、刚度小的刀具承受较小的切削载荷,使不同的刀具都可以采用合理的切削用量,具有大体相近的寿命,减少磨刀及更换刀具的次数。
五、合理选择切削用量
数控车削中的切削用量是表示机床主体的主运动和进给运动大小的重要参数,包括切削深度、主轴转速、进给速度。
它们的选择与普车所要求的基本对应一致,但数控车床加工的零件往往较复杂,切削用量按一定的原则初定后,还应结合零件实际加工情况随时进行调整,调整方法是利用数控车床的操作面板上各种倍率开关,随时进行调整,来实现切削用量的合理配置,这对操作者来说应该具有一定的实际生产加工经验。
总之,随着科学技术的飞速发展,数控车床由于具有优越的加工特点,在机械制造业中的应用越来越广泛,为了充分发挥数控车床的作用,我们需要在编程中掌握一定的技巧,编制出合理、高效的加工程序,保证加工出符合图纸要求的合格工件,同时能使数控车床的功能得到合理的应用与充分的发挥,使数控车床能安全、可靠、高效地工作。