埋弧焊焊接工艺及操作方法
埋弧焊工艺:对接接头双面焊操作方法

埋弧焊工艺:对接接头双面焊操作方法1、焊剂垫法双面焊焊剂垫法双面焊是埋弧焊对接焊中使用最广泛的一种方法,适用于中厚板的焊接。
一般第一面焊缝衬在焊剂垫上进行,翻转进行另一面焊接时,为保证焊透,可用碳弧气刨或其他机械加工方法适当清根。
焊剂垫法双面焊焊接参数见下表。
2、临时工艺垫板法双面焊临时工艺垫板的作用是托住填入间隙的焊剂。
在焊接直焊缝时,垫板为厚度3~4mm、宽度30~50mm的钢带,也可采用石棉绳和板作承托物。
第一面焊接前须留有一定间隙,以保证细粒焊剂能进入。
焊完第一面后,翻转焊件并去除承托物、间隙内的焊剂和焊缝根部的渣壳,然后进行第二面的焊接。
焊剂垫法双面焊焊接参数见下表。
焊剂垫法双面焊焊接参数注:焊件材料为碳钢。
当焊接低合金高强度钢时,电流宜降低10%左右。
坡口形式的详细尺寸按GB/T985.2—2008规定。
各种形式的临时工艺垫板如下图所示。
▲临时工艺垫板a)薄钢带垫b)石棉绳垫c)石棉板垫3、悬空法双面焊利用悬空法焊接时,工件背面不加衬垫,不需要任何辅助设备和装置。
为防止液态金属从间隙中流失或烧穿,要求严格控制间隙,装配时一般不留间隙或间隙≤1mm。
焊接正面的焊接参数应较小,熔深小于焊件厚度的一半;翻转工件后再焊反面,为保证焊透,适当增大焊接电流,保证熔深达到焊件厚度的60%~70%。
悬空双面焊焊接参数见下表。
悬空双面焊焊接参数4、厚板对接焊焊件厚度较大时,大都采用多层焊。
焊道截面仅是一般埋弧焊方法的70%,边缘焊道务必使与坡口相切熔合,并适当形成下凹圆滑过渡。
盖面焊时可先焊坡口两侧,再焊中间焊道,或依次盖面成绕带状。
(1)厚板对接焊的坡口形式厚22~36mm的焊件,常采用V形(带钝边)或X形(带钝边)坡口。
厚度>38mm的焊件,宜采用U形(带钝边)、UV形(带钝边)或双U形(带钝边)坡口,如下图所示。
坡口最好采用机械加工。
▲UV形、双U形坡口(2)要选择脱渣好的焊剂,在焊接过程中要及时回收。
埋弧焊的焊接工艺

埋弧焊的焊接工艺埋弧焊(Submerged Arc Welding,SAW)是一种高效、稳定、经济的电弧焊接工艺。
它采用单面自动焊接技术,焊丝和焊接区域被埋在焊接熔渣中,以保护焊接区域免受空气污染。
埋弧焊接可用于生产钢板、管道、轮胎以及其他工业产品。
埋弧焊接的特点1. 高效:埋弧焊接速度快、连续、产量高,比手工电弧焊接效率高出数倍甚至十倍以上。
2. 稳定:埋弧焊接过程稳定,焊缝质量高,并且焊接不易产生气孔、裂纹等缺陷。
3. 经济:埋弧焊接器材简单、成本低廉,操作简单,可实现自动化生产。
4. 适用面广:埋弧焊接可用于焊接各种金属材料,包括钢、铜、铝等。
埋弧焊接的工艺埋弧焊接的基本设备包括电源、焊机、焊枪、焊丝、焊接电缆和其他辅助设备。
下面是埋弧焊接的具体工艺步骤:1. 准备工作:首先需要对待焊接的材料进行清洗和钝化处理,以便焊接区域不受腐蚀作用。
然后将工件放入夹持装置中,以便焊接。
2. 选用焊接电源:根据待焊接的材料和工件的厚度,选择合适的电源和电流大小。
通常使用直流或低频交流电源。
3. 选用焊丝和熔渣:选择合适的焊丝和熔渣,以确保焊接效果良好。
焊丝的直径通常为2.4mm、3.2mm和4mm,熔渣的成分也需要根据焊接的材料来选用。
4. 安装和调整焊机:将焊丝和熔渣装置安装在焊机上,并根据需要进行调整。
调整项包括焊丝送丝速度、熔渣的喷出速度、焊接电流和焊接电压等。
5. 启动焊接:将焊枪和焊丝放在焊件上,启动焊接过程。
焊丝和熔渣进入焊缝,形成熔池,然后熔池在熔渣的保护下冷却凝固。
6. 检查和清理:当焊接完成后,需要对焊缝进行检查,去除焊接过程中产生的熔渣和焊丝残留物。
最后进行质量检验,以确定焊接是否符合要求。
总结埋弧焊接是一种高效、稳定、经济的焊接工艺,可以用于焊接各种金属材料。
埋弧焊接要求焊接区域被熔渣保护,以保证焊接质量。
在进行埋弧焊接时,需要选用合适的焊丝和熔渣,同时保证焊机的正常工作。
进行完埋弧焊接后,需要对焊缝进行检查和清理,以确保焊接的质量。
埋弧焊工艺参数及焊接技术

埋弧焊工艺参数及焊接技术埋弧焊是一种常见的焊接方法,广泛应用于工业领域。
在进行埋弧焊时,正确设置工艺参数是保证焊接质量的重要因素之一。
本文将介绍埋弧焊的工艺参数以及焊接技术,帮助读者更好地理解和掌握这一焊接方法。
1. 埋弧焊工艺参数1.1 电流与电压在埋弧焊中,电流和电压是两个关键的工艺参数。
合理的电流和电压设定可以保证焊接的稳定性和质量。
一般来说,电流的选择应该根据焊接材料和焊接件的厚度来确定。
较粗的焊接件需要较大的电流,而较薄的焊接件则需要较小的电流。
电压的选择则影响焊接过程中的弧长以及熔池的形成和稳定性。
通常情况下,较高的电压可以获得较长的弧长,适用于焊接较厚的材料。
而较低的电压则适用于焊接薄板材料。
1.2 焊接速度焊接速度是指焊接电弧沿焊缝移动的速度。
合理的焊接速度能够控制焊接过程中的热输入,从而保证焊接接头的质量。
焊接速度的选择应该综合考虑焊接材料的热导性、电流和电压等参数。
一般来说,焊接速度过快容易导致焊缝出现缺陷,而速度过慢则容易引起过烧。
1.3 焊接角度焊接角度是指焊条或焊枪与焊缝法线之间的夹角。
合理的焊接角度可以影响焊接过程中的熔池形成和焊缝形状。
一般来说,焊接角度过大可能导致熔池过大,焊接质量不稳定。
而焊接角度过小则会影响焊接速度和焊缝的形成。
2. 焊接技术2.1 预热在进行埋弧焊前,预热焊接部位是提高焊接质量的技术之一。
预热可以减轻焊接部位的残余应力,提高焊接强度和韧性。
预热温度的选择应考虑焊接材料的类型和厚度等因素,并通过试验和实践来确定最佳的预热温度。
2.2 清洁焊接前的清洁工作十分重要,可以有效地避免焊接缺陷的产生。
焊接部位应清除油污、氧化物和其他杂质,确保焊接表面干净。
这可以通过机械清洁、溶剂清洗、除锈剂处理等方法来完成。
2.3 间隙控制在焊接过程中,合适的间隙控制能够保证焊缝的形状和尺寸。
间隙的选择应根据焊接件的要求和所使用的焊接方法来决定。
一般来说,焊接件的间隙应视焊接材料的膨胀和热收缩特性来决定。
埋弧焊工艺:对接接头单面焊操作方法

埋弧焊工艺:对接接头单面焊操作方法1、单面焊双面成形(1)焊剂垫法焊剂垫以一定压力衬托在焊件背面,帮助焊缝成形。
焊剂垫上单面焊双面成形埋弧焊焊接参数见下表。
焊剂垫上单面焊双面成形埋弧焊焊接参数由于焊接时要求焊剂始终与焊件紧贴,焊缝背面成形难以稳定,为防止焊缝悬空造成衬垫贴不紧而焊穿,一般用压力架、电磁平台等来压紧。
(2)铜垫法和焊剂—铜垫法焊接4mm以下薄板时,可不留装配间隙,直接在铜垫板上焊接,以达到单面焊双面成形。
在焊接较厚板材时,为了改善背面成形条件,常采用焊剂—铜垫法。
此时焊件不开坡口,预留合适的装配间隙,然后均匀地在接缝中撒上焊剂进行焊接,焊接时,焊件与铜垫板间须贴紧夹固。
焊剂铜垫板上单面对接焊焊接参数见下表。
焊剂铜垫板上单面对接焊焊接参数(3)电磁平台—焊剂垫法对接接头板厚在14mm以下,可以单面一次焊透。
超过14mm时应开坡口或留间隙。
间隙在5~6mm时可不开坡口一次焊透20mm。
应当指出,开坡口的目的并非完全是增大一次性焊透量,它还有控制熔合比和调节焊缝余高的明显作用。
电磁平台—焊剂垫上单面对接焊焊接参数见下表。
电磁平台—焊剂垫上单面对接焊焊接参数(4)龙门压力架—焊剂铜垫法在龙门压力架的横梁上有多个气缸,通入压缩空气后,气缸带动压紧装置将焊件压紧在焊剂铜垫上进行焊接。
焊接结束后,通过三通阀使气缸带动压紧装置,升起便可以移走焊件。
焊接背面的成形装置采用焊剂铜垫,铜垫上开有一个成形槽以保证背面成形。
铜衬垫成形槽的截面形状如下图所示。
▲铜衬垫成形槽的截面形状焊剂铜垫截面尺寸见下表。
焊剂铜垫截面尺寸(单位:mm)将焊接部位清理干净,借助焊接平台上的输送滚轮将焊件送入进行装配,留出一定的装配间隙并使间隙中心线对准成形槽的中心线,焊缝两端焊接引弧板和引出板,放下龙门架压紧焊件,顶紧铜垫,在焊接前将细粉焊剂均匀地填入铜垫的成形槽中,然后按照制订的焊接参数进行焊接。
龙门压力架—焊剂铜垫法焊接参数见下表。
埋弧焊焊接工艺及操作方法
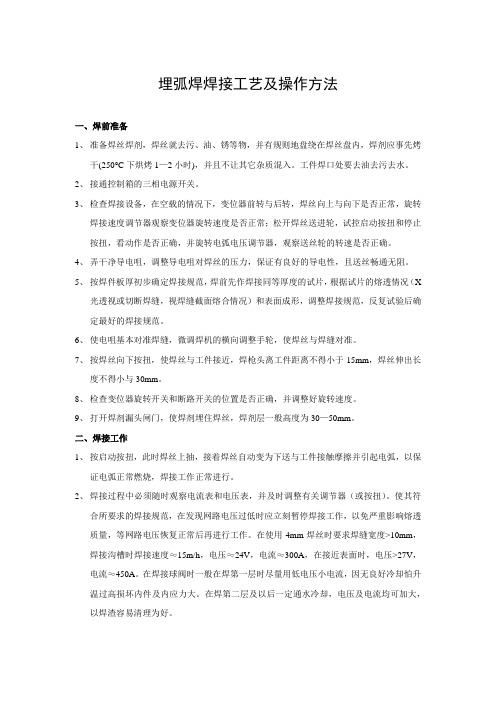
埋弧焊焊接工艺及操作方法一、焊前准备1、准备焊丝焊剂,焊丝就去污、油、锈等物,并有规则地盘绕在焊丝盘内,焊剂应事先烤干(250°C下烘烤1—2小时),并且不让其它杂质混入。
工件焊口处要去油去污去水。
2、接通控制箱的三相电源开关。
3、检查焊接设备,在空载的情况下,变位器前转与后转,焊丝向上与向下是否正常,旋转焊接速度调节器观察变位器旋转速度是否正常;松开焊丝送进轮,试控启动按扭和停止按扭,看动作是否正确,并旋转电弧电压调节器,观察送丝轮的转速是否正确。
4、弄干净导电咀,调整导电咀对焊丝的压力,保证有良好的导电性,且送丝畅通无阻。
5、按焊件板厚初步确定焊接规范,焊前先作焊接同等厚度的试片,根据试片的熔透情况(X光透视或切断焊缝,视焊缝截面熔合情况)和表面成形,调整焊接规范,反复试验后确定最好的焊接规范。
6、使电咀基本对准焊缝,微调焊机的横向调整手轮,使焊丝与焊缝对准。
7、按焊丝向下按扭,使焊丝与工件接近,焊枪头离工件距离不得小于15mm,焊丝伸出长度不得小与30mm。
8、检查变位器旋转开关和断路开关的位置是否正确,并调整好旋转速度。
9、打开焊剂漏头闸门,使焊剂埋住焊丝,焊剂层一般高度为30—50mm。
二、焊接工作1、按启动按扭,此时焊丝上抽,接着焊丝自动变为下送与工件接触摩擦并引起电弧,以保证电弧正常燃烧,焊接工作正常进行。
2、焊接过程中必须随时观察电流表和电压表,并及时调整有关调节器(或按扭)。
使其符合所要求的焊接规范,在发现网路电压过低时应立刻暂停焊接工作,以免严重影响熔透质量,等网路电压恢复正常后再进行工作。
在使用4mm焊丝时要求焊缝宽度>10mm,焊接沟槽时焊接速度≈15m/h,电压≈24V,电流≈300A,在接近表面时,电压>27V,电流≈450A。
在焊接球阀时一般在焊第一层时尽量用低电压小电流,因无良好冷却怕升温过高损坏内件及内应力大。
在焊第二层及以后一定通水冷却,电压及电流均可加大,以焊渣容易清理为好。
45号钢埋弧焊堆焊工艺
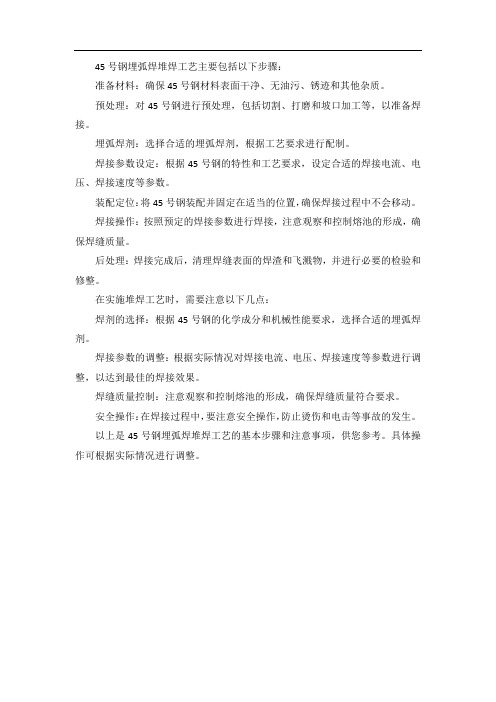
45号钢埋弧焊堆焊工艺主要包括以下步骤:
准备材料:确保45号钢材料表面干净、无油污、锈迹和其他杂质。
预处理:对45号钢进行预处理,包括切割、打磨和坡口加工等,以准备焊接。
埋弧焊剂:选择合适的埋弧焊剂,根据工艺要求进行配制。
焊接参数设定:根据45号钢的特性和工艺要求,设定合适的焊接电流、电压、焊接速度等参数。
装配定位:将45号钢装配并固定在适当的位置,确保焊接过程中不会移动。
焊接操作:按照预定的焊接参数进行焊接,注意观察和控制熔池的形成,确保焊缝质量。
后处理:焊接完成后,清理焊缝表面的焊渣和飞溅物,并进行必要的检验和修整。
在实施堆焊工艺时,需要注意以下几点:
焊剂的选择:根据45号钢的化学成分和机械性能要求,选择合适的埋弧焊剂。
焊接参数的调整:根据实际情况对焊接电流、电压、焊接速度等参数进行调整,以达到最佳的焊接效果。
焊缝质量控制:注意观察和控制熔池的形成,确保焊缝质量符合要求。
安全操作:在焊接过程中,要注意安全操作,防止烫伤和电击等事故的发生。
以上是45号钢埋弧焊堆焊工艺的基本步骤和注意事项,供您参考。
具体操作可根据实际情况进行调整。
埋弧焊工艺参数及焊接技术
埋弧焊工艺参数及焊接技术一、埋弧焊工艺参数1.电流选择:埋弧焊工艺通常采用直流电源,电流大小的选择要根据焊缝宽度、材料厚度和焊条规格等因素来确定。
一般来说,电流过大容易出现焊渣溅射、焊缝收缩变大等问题,电流过小则焊缝无法充分熔透。
2. 电弧长度:电弧长度是指电弧端和电极之间的距离,通常控制在15mm左右。
电弧长度过长,容易导致电弧不稳定,焊接质量下降;电弧长度过短,容易导致焊缝形不成。
3.保护气体流量:埋弧焊需要在焊接过程中通过保护气体(如纯氩气)对焊缝进行保护,防止氧气和氮气的污染。
保护气体流量的大小要根据材料种类和规格来确定,一般为8-15升/分钟。
保护气体流量过大会增加熔渣溅射的可能性,过小则可能导致氧气和氮气侵入焊缝。
4.焊接速度:焊接速度取决于焊接材料的厚度和焊条的直径等因素,一般来说,焊接速度过快会导致焊缝连接不牢固,焊接速度过慢会造成焊缝过热、变形等问题。
合理的焊接速度可根据经验和试验来确定。
二、埋弧焊接技术1.准备工作:对于焊接材料,应保证焊件焊口的清洁度,去除表面的氧化物和油污。
对于厚度较大的材料,可采用加热预热的方法,以提前消除焊接应力。
2.焊条的选择:要选择合适的焊条,焊条的种类和规格要与焊接材料的种类和规格相匹配,以确保焊接质量。
焊条的保质期要注意,过期的焊条不能使用。
3.焊接过程:焊接时,要保证电弧稳定,焊条与工件的距离适当,不得与气缝直接接触。
焊接位置要选择合适,以便操作方便。
焊接方向要与主应力方向垂直。
4.焊后处理:焊接后,应采取适当的焊后处理措施,如退火、热处理等,以提高焊接接头的性能和质量。
总结:埋弧焊工艺参数及焊接技术对焊接质量和效率具有重要影响。
通过选择合适的电流、电弧长度和保护气体流量等参数,合理控制焊接速度,做好焊前准备和焊后处理工作,可以保证埋弧焊接的质量和可靠性。
同时,焊工应具备良好的焊接技术和操作经验,能够正确操作焊接设备和工具,严格按照操作规程进行焊接,以确保焊接质量和安全。
埋弧焊操作规程
埋弧焊操作规程
《埋弧焊操作规程》
一、概述
埋弧焊是一种重要的电弧焊接方法,广泛应用于船舶、桥梁、压力容器等领域。
为了确保操作过程安全、焊接质量稳定,制定埋弧焊操作规程是必不可少的。
二、准备工作
1. 确保焊接设备完好无损,焊丝、焊接电极和焊接材料符合要求;
2. 检查工作环境,确保通风良好,防止焊接过程中产生有害气体;
3. 准备好个人防护用具,如焊接面罩、手套、焊接服等;
4. 对焊接工件进行清洁处理,消除表面油污和杂质;
三、操作流程
1. 使用合适的焊接电流和电压进行预热;
2. 调整焊接速度,控制焊接熔池的形成;
3. 注意焊接角度和位置,确保焊缝的质量和均匀性;
4. 注意保护气体的流动,防止气流受到外界干扰;
5. 在工作中及时更换焊接电极,避免电极断裂和其他意外;
四、安全注意事项
1. 确保焊接操作人员具备相关技术和经验,避免操作不当导致意外;
2. 在焊接过程中,保持工作环境安全,防止有害气体、火花等
造成事故;
3. 合理利用个人防护用具,减少对身体的伤害;
4. 定期对焊接设备进行检测和维护,确保设备的正常使用;
5. 对于特殊焊接情况,需根据具体情况制定相应的操作规程和安全措施。
总之,埋弧焊操作规程是保证焊接作业安全和焊接质量的重要手段,需要严格执行。
只有严格按照规程进行操作,才能够确保埋弧焊工作的顺利进行。
埋弧焊工艺标准
埋弧焊工艺标准
埋弧焊是一种在焊剂层下完成电弧焊接的方法。
在进行埋弧焊之前,需要进行一系列准备工作,包括焊件的坡口加工、待焊部位的表面清理、焊件的装配以及焊丝表面的清理、焊剂的烘干等。
具体标准如下:
1. 坡口加工:坡口加工要求按GB 986—1988执行,以保证焊缝根部不出现未焊透或夹渣,并减少填充金属量。
坡口的加工可使用刨边机、机械化或半机械化气割机、碳弧气刨等。
2. 待焊部位的清理:在焊前应将坡口及坡口两侧各20mm区域内及待焊部位的表面铁锈、氧化皮、油污等清理干净。
3. 焊件的装配:装配焊件时要保证间隙均匀,高低平整,错边量小,定位焊缝长度一般大于30mm,并且定位焊缝质量与主焊缝质量要求一致。
必要时采用专用工装、卡具。
4. 预热:当埋弧焊焊接的板厚在60mm以上时,焊前必须对焊道及两侧2倍板厚范围内预热,预热温度为100~150℃,板厚为40~60mm时,预热温度宜为60~80℃。
5. 保温:焊接完成前不得中途停止超过15分钟,当必须停止时,应采取保温措施缓冷,重新施焊前必须再次预热,层间温度控制在℃,焊接完后应采用保温棉及时进行保温。
此外,在焊接工艺上主要采取气保焊打底,埋弧自动焊填充及盖面,打底厚度根据板厚而定。
以上信息仅供参考,如需获取更多详细信息,建议查阅埋弧焊工艺标准书籍或咨询专业人士。
管道埋弧焊工艺与操作技巧
管道埋弧焊工艺与操作技巧管道埋弧焊,听起来就像是给管道穿一件结实又耐用的“钢铁铠甲”的神奇工艺呢。
这管道埋弧焊啊,就像一场精心编排的舞蹈。
那焊接电源就像是乐队的指挥,控制着整个节奏。
焊条呢,就好比舞者的脚步,每一步都得精准。
焊接的时候,电弧就像一道神秘的光剑,在管道上挥舞,把那些分开的部分连接起来。
你说要是这电弧不稳,就像跳舞的时候脚步乱了,那焊接出来的管道能结实吗?肯定不行啊。
咱先说这焊前的准备工作。
就好比做饭前得把食材都准备好一样,焊接前也要把管道清理得干干净净。
你想啊,如果管道上有油污、铁锈之类的脏东西,那焊条和管道就不能好好地“牵手”了。
这就像两个人握手,要是手上都是泥,能握得紧吗?肯定握不紧。
清理管道得仔仔细细的,就像打扫自己心爱的房间一样,每个角落都不能放过。
还有啊,这焊件的装配也很重要,得保证对接的地方严丝合缝,就像拼图一样,一块一块要对得准准的。
开始焊接的时候呢,焊接速度就像汽车的车速一样,得合适。
太快了,就像开车开得太快,容易出事故,焊接出来的质量就不好,可能会有未焊透之类的毛病。
太慢了呢,又浪费时间,还可能让焊缝变得太宽,就像画画的时候线条画得太粗了,不好看也不结实。
电流和电压也得调整好,这就像调收音机的频道一样,要找到那个最清晰的点。
电流大了,就像洪水泛滥,容易把焊缝冲坏;电流小了,又像涓涓细流,力量不够,焊不透。
再说说这焊接的操作技巧。
焊工师傅的手得稳,这就像狙击手拿枪一样,手抖一下,可能就偏离目标了。
在焊接过程中,要时刻关注熔池的状态,熔池就像一个小湖泊,里面的液体流动得好不好,直接关系到焊接的质量。
如果熔池像沸腾的开水一样,咕噜咕噜乱动,那肯定是有问题的。
而且啊,这焊缝的形状也很重要,要让它看起来平滑、均匀,就像用尺子画出来的线一样直。
这可不容易,需要焊工师傅有一双像老鹰一样敏锐的眼睛,随时发现问题并调整。
还有一个容易被忽视的点,就是焊接环境。
这就像人生活的环境一样,环境不好,人就不舒服。
- 1、下载文档前请自行甄别文档内容的完整性,平台不提供额外的编辑、内容补充、找答案等附加服务。
- 2、"仅部分预览"的文档,不可在线预览部分如存在完整性等问题,可反馈申请退款(可完整预览的文档不适用该条件!)。
- 3、如文档侵犯您的权益,请联系客服反馈,我们会尽快为您处理(人工客服工作时间:9:00-18:30)。
埋弧焊焊接工艺及操作方法
一、焊前准备
1、准备焊丝焊剂,焊丝就去污、油、锈等物,并有规则地盘绕在焊丝盘内,焊剂应事先烤干(250°C下烘烤1—2小时),并且不让其它杂质混入。
工件焊口处要去油去污去水。
2、接通控制箱的三相电源开关。
3、检查焊接设备,在空载的情况下,变位器前转与后转,焊丝向上与向下是否正常,旋转焊接速度调节器观察变位器旋转速度是否正常;松开焊丝送进轮,试控启动按扭和停止按扭,看动作是否正确,并旋转电弧电压调节器,观察送丝轮的转速是否正确。
4、弄干净导电咀,调整导电咀对焊丝的压力,保证有良好的导电性,且送丝畅通无阻。
5、按焊件板厚初步确定焊接规范,焊前先作焊接同等厚度的试片,根据试片的熔透情况(X 光透视或切断焊缝,视焊缝截面熔合情况)和表面成形,调整焊接规范,反复试验后确定最好的焊接规范。
6、使电咀基本对准焊缝,微调焊机的横向调整手轮,使焊丝与焊缝对准。
7、按焊丝向下按扭,使焊丝与工件接近,焊枪头离工件距离不得小于15mm,焊丝伸出长度不得小与30mm。
8、检查变位器旋转开关和断路开关的位置是否正确,并调整好旋转速度。
9、打开焊剂漏头闸门,使焊剂埋住焊丝,焊剂层一般高度为30—50mm。
二、焊接工作
1、按启动按扭,此时焊丝上抽,接着焊丝自动变为下送与工件接触摩擦并引起电弧,以保证电弧正常燃烧,焊接工作正常进行。
2、焊接过程中必须随时观察电流表和电压表,并及时调整有关调节器(或按扭)。
使其符合所要求的焊接规范,在发现网路电压过低时应立刻暂停焊接工作,以免严重影响熔透质量,等网路电压恢复正常后再进行工作。
在使用4mm 焊丝时要求焊缝宽度>10mm,焊接沟槽时焊接速度≈15m/h,电压≈24V,电流≈300A,在接近表面时,电压>27V,电流≈450A。
在焊接球阀时一般在焊第一层时尽量用低电压小电流,因无良好冷却怕升温过高损坏内件及内应力大。
在焊第二层及以后一定通水冷却,电压及电流均可加大,以焊渣容易清理为好。