生产线的改善方法及改善思路
生产线平衡分析与改善(最全面的IE分析-生产线平衡)

2023/12/24
8
二、流水生产线概述
1、 流水生产的基本概念 ● 流水线生产的分类
➢单人单产品式 ➢单产品固定式 ➢多产品固定式 ➢自由流水式 ➢连续传动流水式 ➢ 间歇传动流水式 ➢分组式
设某一产品从原料到成品,需经过A、B、C、D四个工序,其基本标 准工时(秒/个)及相关生产效率、良率、投入机台/人员数分别见表11: 可以求各工序每小时产量为: A工序每小时产量=(3600秒÷6.90)×90%×95%×1=470.87个 B工序每小时产量=(3600秒÷5.1)×80%×99.5%×1=470.87个 C工序每小时产量=(3600秒÷34.40)×100%×99.9%×2=209.09个 D工序每小时产量=(3600秒÷30.40)×100%×99.5%×2=238.8个 。
IE工业工程
-----生产线平衡
主讲:
课 程 内容
生产线平衡 一、生产线平衡的概述 二、流水生产线概述 三、生产线平衡的设计 四、生产线平衡的方法及改善原则 5、案例分析
2023/12/24
2
1.概念
一、生产线平衡的概述
生产线平衡即对生产的全部工序进行平均化,调整作业 负荷,以使各作业的时间尽可能相近的技术手段与方法,它 是生产流程设计及作业标准化中最重要的方法,是通过平衡 生产线使现场真正实施生产同步化,从而达到“一个流”的 理想。
2023/12/24
。
28
四、生产线平衡的改善方法与原则
2、平衡率改善的图示。
2023/12/24
29
四、生产线平衡的改善方法与原则
自动化生产线如何改善生产线的协调性
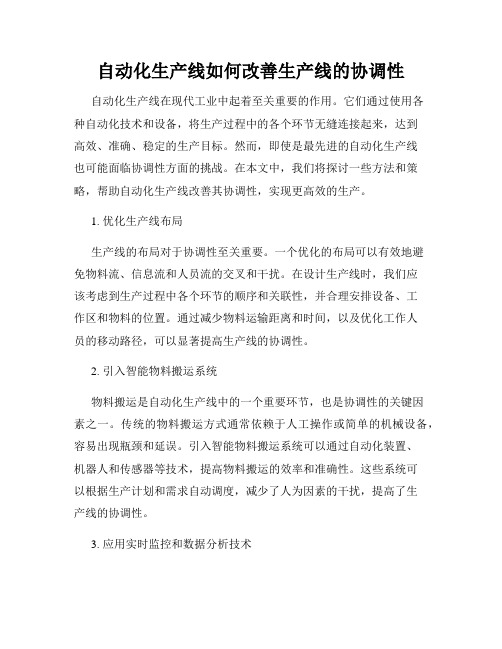
自动化生产线如何改善生产线的协调性自动化生产线在现代工业中起着至关重要的作用。
它们通过使用各种自动化技术和设备,将生产过程中的各个环节无缝连接起来,达到高效、准确、稳定的生产目标。
然而,即使是最先进的自动化生产线也可能面临协调性方面的挑战。
在本文中,我们将探讨一些方法和策略,帮助自动化生产线改善其协调性,实现更高效的生产。
1. 优化生产线布局生产线的布局对于协调性至关重要。
一个优化的布局可以有效地避免物料流、信息流和人员流的交叉和干扰。
在设计生产线时,我们应该考虑到生产过程中各个环节的顺序和关联性,并合理安排设备、工作区和物料的位置。
通过减少物料运输距离和时间,以及优化工作人员的移动路径,可以显著提高生产线的协调性。
2. 引入智能物料搬运系统物料搬运是自动化生产线中的一个重要环节,也是协调性的关键因素之一。
传统的物料搬运方式通常依赖于人工操作或简单的机械设备,容易出现瓶颈和延误。
引入智能物料搬运系统可以通过自动化装置、机器人和传感器等技术,提高物料搬运的效率和准确性。
这些系统可以根据生产计划和需求自动调度,减少了人为因素的干扰,提高了生产线的协调性。
3. 应用实时监控和数据分析技术实时监控和数据分析是改善协调性的重要工具。
通过安装传感器、监控设备和数据采集系统,我们可以实时了解生产线的运行状态和性能指标。
这些数据可以被用于监控生产进度、识别潜在问题、预测设备故障,并进行即时调整。
同时,利用数据分析技术可以挖掘隐藏在大量数据中的规律和模式,优化生产计划和资源调度,提高生产线的协调性和生产效率。
4. 强化通信和协作良好的通信和协作是实现生产线协调性的关键。
在自动化生产线中,不同设备、系统和部门之间的信息传递和协作往往非常重要。
为了确保信息的及时传递和沟通的顺畅进行,我们可以采用各种通信工具和技术,如使用互联网、局域网或移动通讯设备等。
此外,建立跨部门和跨功能的团队合作机制,鼓励信息共享和协作,可以加强生产线各个环节之间的协调性。
生产线改善方法及改善思路
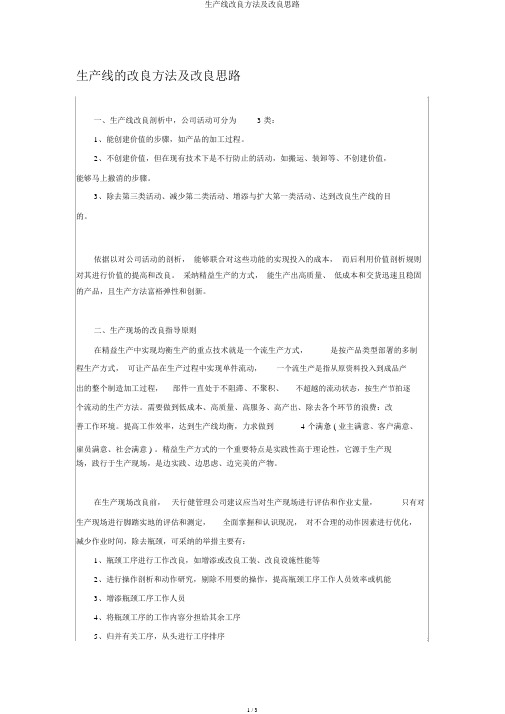
生产线的改良方法及改良思路一、生产线改良剖析中,公司活动可分为 3 类:1、能创建价值的步骤,如产品的加工过程。
2、不创建价值,但在现有技术下是不行防止的活动,如搬运、装卸等、不创建价值,能够马上撤消的步骤。
3、除去第三类活动、减少第二类活动、增添与扩大第一类活动、达到改良生产线的目的。
依据以对公司活动的剖析,能够联合对这些功能的实现投入的成本,而后利用价值剖析规则对其进行价值的提高和改良。
采纳精益生产的方式,能生产出高质量、低成本和交货迅速且稳固的产品,且生产方法富裕弹性和创新。
二、生产现场的改良指导原则在精益生产中实现均衡生产的重点技术就是一个流生产方式,是按产品类型部署的多制程生产方式,可让产品在生产过程中实现单件流动,一个流生产是指从原资料投入到成品产出的整个制造加工过程,部件一直处于不阻滞、不聚积、不超越的流动状态,按生产节拍逐个流动的生产方法。
需要做到低成本、高质量、高服务、高产出、除去各个环节的浪费:改善工作环境。
提高工作效率,达到生产线均衡,力求做到 4 个满惫 ( 业主满意、客户满意、雇员满意、社会满意 ) 。
精益生产方式的一个重要特点是实践性高于理论性,它源于生产现场,践行于生产现场,是边实践、边思虑、边完美的产物。
在生产现场改良前,天行健管理公司建议应当对生产现场进行评估和作业丈量,只有对生产现场进行脚踏实地的评估和测定,全面掌握和认识现况,对不合理的动作因素进行优化,减少作业时间,除去瓶颈,可采纳的举措主要有:1、瓶颈工序进行工作改良,如增添或改良工装、改良设施性能等2、进行操作剖析和动作研究,剔除不用要的操作,提高瓶颈工序工作人员效率或机能3、增添瓶颈工序工作人员4、将瓶颈工序的工作内容分担给其余工序5、归并有关工序,从头进行工序排序6、拆分工作时间较短的工序并入其余工序二、生产线上的改良方法,须依据以下原则:1、有益于实现少人化2、有益于操作者的作业3、有益于物流与信息传达的控制4、有益于质量保证5、有益于全员生产维修(TPM, Total ProductiveMaintenance(全面生产性维修;总生产维修制 ) 展开6、有益于实现标准作业7、有益于保障安全三、生产线的四种改良思路1、均衡生产线生产线均衡是对生产线上的所有工位进行均匀化、调整作业负荷,以使各作业时间尽可能使每用邻近的技术手段与方法。
试谈流水生产线的改善

试谈流水生产线的改善一、引言流水生产线是一种高效的生产组织方式,它通过将生产过程划分为一系列的工序,流程连续、顺序紧凑,提高了生产效率和产品质量。
然而,在实践中,流水生产线也存在一些问题和挑战,如生产过程中的浪费、低效率、质量问题等。
因此,对流水生产线进行改善是提高生产效率和质量的关键。
本文将探讨流水生产线的改善方法和实践经验,旨在为企业提供有益的参考。
二、流水生产线改善的必要性1. 提高生产效率流水生产线的核心目标之一是提高生产效率。
通过对生产过程的优化和改进,可以减少生产时间和资源浪费,实现高效生产。
改善流水生产线可以提高生产效率,缩短生产周期,提高企业的竞争力。
2. 降低生产成本流水生产线改善的另一个重要目标是降低生产成本。
通过优化工艺流程、减少不必要的环节和浪费,可以降低材料、人力、能源等资源的使用量,以达到降低生产成本的目的。
3. 提高产品质量流水生产线改善不仅可以提高生产效率和降低生产成本,还可以提高产品质量。
通过改进生产工艺、强化质量控制和质量管理,可以减少产品缺陷和质量问题,提高产品的一致性和可靠性。
三、流水生产线改善的方法和实践经验1. 优化工艺流程优化工艺流程是改善流水生产线的重要方法之一。
首先,需要对生产过程进行全面的分析和评估,找出存在的问题和瓶颈。
然后,根据问题的具体情况,制定改进方案,优化工艺流程,提高生产效率和质量。
例如,对生产过程中的重复工序进行合并,通过并行操作来提高生产效率;对工序之间的传递和协作进行优化,减少等待时间和延误。
2. 引入自动化设备引入自动化设备是改善流水生产线的另一个有效方法。
自动化设备可以代替人工完成繁重的、重复的操作,提高生产效率和质量,并减少人力资源的需求。
例如,可以引入机器人或自动化装置来完成装配、包装等任务,从而提高生产效率和减少人为差错。
3. 强化质量控制强化质量控制是改善流水生产线的关键。
在流水生产线中,质量控制必须贯穿整个生产过程,从原材料采购到成品交付,每个环节都要进行严格的检查和监控。
砂石骨料生产线的常见问题及改进措施

砂石骨料生产线的常见问题及改进措施砂石骨料生产线是建筑行业中非常重要的生产设备之一,它的稳定运行和高效生产对于保障建筑行业的发展具有重要意义。
在生产过程中常常会遇到一些问题,这些问题不仅影响生产效率,还可能会降低产品质量,甚至对设备造成损坏。
研究常见问题及改进措施对于提高砂石骨料生产线的生产效率和产品质量具有重要意义。
一、常见问题及原因分析1. 设备故障设备故障是砂石骨料生产线常见的问题之一。
设备故障可能是由于设备老化、使用不当、缺乏维护保养等原因导致的。
设备故障会严重影响生产效率,甚至造成停产。
2. 粗细料混合不均匀在砂石骨料的生产过程中,粗细料的混合均匀度对产品质量有着重要影响。
如果粗细料混合不均匀,会导致产品质量下降,甚至出现裂纹、强度不足等问题。
3. 能耗过高砂石骨料生产线通常需要耗费大量的能源,如果能耗过高,不仅会增加生产成本,还会对环境造成不良影响。
4. 产品质量波动大砂石骨料生产线在生产过程中,产品质量波动大是一个常见问题。
产品质量波动大不仅会增加生产成本,还会影响客户对产品的信任度。
以上这些问题都会严重影响砂石骨料生产线的生产效率和产品质量,有必要对这些问题进行改进。
二、改进措施1. 设备维护保养对于设备故障问题,可以通过加强设备的维护保养来降低故障率。
定期对设备进行维护保养,及时更换老化部件,可以有效提高设备的使用寿命,降低故障率。
2. 设备更新升级对于老化严重的设备,可以考虑进行更新升级。
新型设备通常具有更高的生产效率和更低的故障率,可以显著改善生产线的生产效率和产品质量。
3. 加强自动化控制在砂石骨料生产线生产过程中,加强自动化控制可以有效减少人为操作的失误,提高生产的稳定性和一致性,降低能耗,减少产品质量波动。
4. 使用高效节能设备为了降低能耗过高的问题,可以考虑使用高效节能设备,如高效破碎机、新型篦式给料机等,这些设备可以降低能耗,减少生产成本。
5. 优化生产工艺在砂石骨料生产线生产过程中,可以通过优化生产工艺,调整料流量、筛分参数等方式,使得粗细料混合更加均匀,提高产品质量。
工业工程中的生产线连续改善与优化
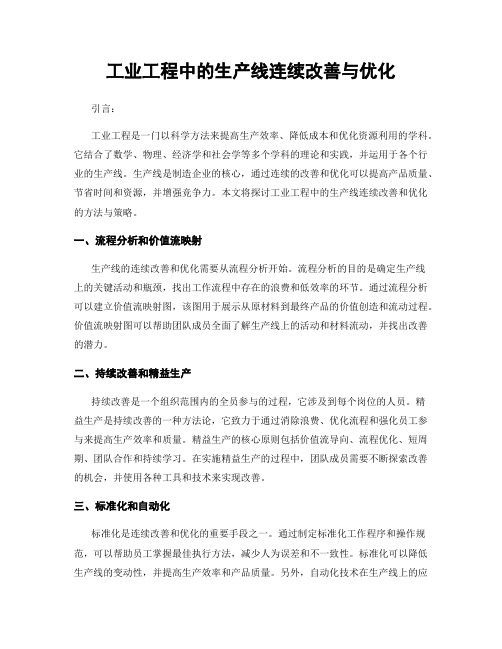
工业工程中的生产线连续改善与优化引言:工业工程是一门以科学方法来提高生产效率、降低成本和优化资源利用的学科。
它结合了数学、物理、经济学和社会学等多个学科的理论和实践,并运用于各个行业的生产线。
生产线是制造企业的核心,通过连续的改善和优化可以提高产品质量、节省时间和资源,并增强竞争力。
本文将探讨工业工程中的生产线连续改善和优化的方法与策略。
一、流程分析和价值流映射生产线的连续改善和优化需要从流程分析开始。
流程分析的目的是确定生产线上的关键活动和瓶颈,找出工作流程中存在的浪费和低效率的环节。
通过流程分析可以建立价值流映射图,该图用于展示从原材料到最终产品的价值创造和流动过程。
价值流映射图可以帮助团队成员全面了解生产线上的活动和材料流动,并找出改善的潜力。
二、持续改善和精益生产持续改善是一个组织范围内的全员参与的过程,它涉及到每个岗位的人员。
精益生产是持续改善的一种方法论,它致力于通过消除浪费、优化流程和强化员工参与来提高生产效率和质量。
精益生产的核心原则包括价值流导向、流程优化、短周期、团队合作和持续学习。
在实施精益生产的过程中,团队成员需要不断探索改善的机会,并使用各种工具和技术来实现改善。
三、标准化和自动化标准化是连续改善和优化的重要手段之一。
通过制定标准化工作程序和操作规范,可以帮助员工掌握最佳执行方法,减少人为误差和不一致性。
标准化可以降低生产线的变动性,并提高生产效率和产品质量。
另外,自动化技术在生产线上的应用也是提高效率和质量的重要手段。
自动化可以减少人力需求,提高生产速度和准确性,同时还可以减少人为因素对生产线稳定性的影响。
四、数据分析和反馈机制数据分析是生产线连续改善和优化的重要依据。
通过收集和分析生产数据,可以识别出问题和机会,并根据数据结果制定改善和优化的策略。
数据分析可以涉及到生产速度、产品质量、设备利用率和人员效率等方面的指标。
此外,建立良好的反馈机制也是促进生产线连续改善的重要手段。
生产线效率改善方案
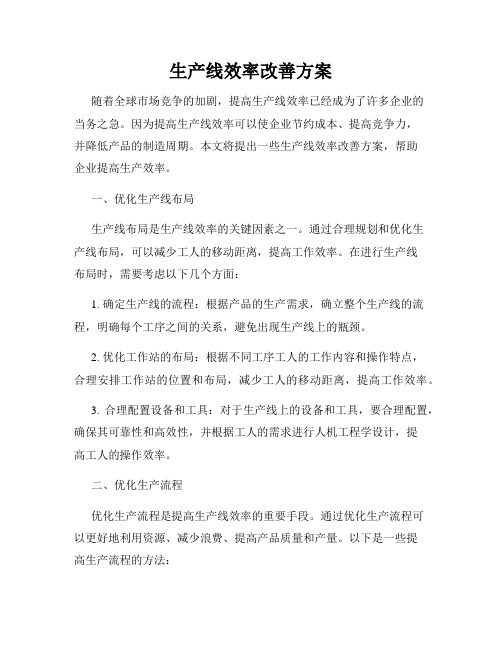
生产线效率改善方案随着全球市场竞争的加剧,提高生产线效率已经成为了许多企业的当务之急。
因为提高生产线效率可以使企业节约成本、提高竞争力,并降低产品的制造周期。
本文将提出一些生产线效率改善方案,帮助企业提高生产效率。
一、优化生产线布局生产线布局是生产线效率的关键因素之一。
通过合理规划和优化生产线布局,可以减少工人的移动距离,提高工作效率。
在进行生产线布局时,需要考虑以下几个方面:1. 确定生产线的流程:根据产品的生产需求,确立整个生产线的流程,明确每个工序之间的关系,避免出现生产线上的瓶颈。
2. 优化工作站的布局:根据不同工序工人的工作内容和操作特点,合理安排工作站的位置和布局,减少工人的移动距离,提高工作效率。
3. 合理配置设备和工具:对于生产线上的设备和工具,要合理配置,确保其可靠性和高效性,并根据工人的需求进行人机工程学设计,提高工人的操作效率。
二、优化生产流程优化生产流程是提高生产线效率的重要手段。
通过优化生产流程可以更好地利用资源、减少浪费、提高产品质量和产量。
以下是一些提高生产流程的方法:1. 进行价值流分析(Value Stream Mapping,VSM):价值流分析是一种系统性的工具,可以帮助企业实现生产流程的精益化,通过识别和消除非价值增加的活动,提高生产效率。
2. 使用自动化设备和技术:自动化设备和技术可以大大提高生产效率。
例如,可以使用机器人代替人工进行部分操作,减少人为错误和人力资源浪费。
3. 实施精益生产方法:精益生产是一种管理方法,致力于通过消除浪费来提高生产效率。
通过实施精益生产方法,企业可以减少库存、缩短制造周期、降低成本,并提高产品质量。
三、改善员工培训和福利员工是企业生产线上最重要的资源,他们的知识和技能直接影响到生产效率。
因此,改善员工培训和福利非常重要。
以下是一些改善员工培训和福利的建议:1. 提供专业培训:为员工提供专业培训,使他们获得更多的技能和知识,提高工作效率和生产质量。
车间问题点及改善方案
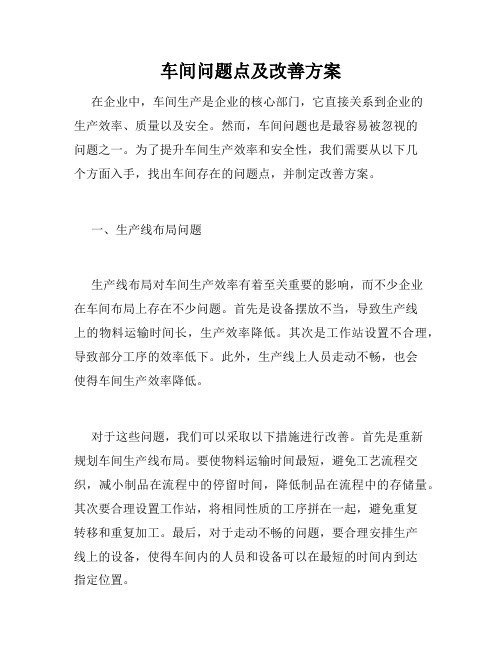
车间问题点及改善方案在企业中,车间生产是企业的核心部门,它直接关系到企业的生产效率、质量以及安全。
然而,车间问题也是最容易被忽视的问题之一。
为了提升车间生产效率和安全性,我们需要从以下几个方面入手,找出车间存在的问题点,并制定改善方案。
一、生产线布局问题生产线布局对车间生产效率有着至关重要的影响,而不少企业在车间布局上存在不少问题。
首先是设备摆放不当,导致生产线上的物料运输时间长,生产效率降低。
其次是工作站设置不合理,导致部分工序的效率低下。
此外,生产线上人员走动不畅,也会使得车间生产效率降低。
对于这些问题,我们可以采取以下措施进行改善。
首先是重新规划车间生产线布局。
要使物料运输时间最短,避免工艺流程交织,减小制品在流程中的停留时间,降低制品在流程中的存储量。
其次要合理设置工作站,将相同性质的工序拼在一起,避免重复转移和重复加工。
最后,对于走动不畅的问题,要合理安排生产线上的设备,使得车间内的人员和设备可以在最短的时间内到达指定位置。
二、材料管理问题车间生产过程中的材料管理也是一个非常重要的问题。
在车间生产过程中,材料如果管理不当,就有可能影响生产进度、增加生产成本,甚至导致产品质量下降。
其中,最常见的问题点包括材料丢失、材料错误配料等。
为了解决这些问题,我们可以在材料管理方面采取以下措施。
首先,要制定严格的材料管理制度,加强对于材料的入库、出库以及销售等环节的监管,杜绝材料流失和错误配料的问题。
其次,使用条形码等智能技术来对材料进行管理,提高管理效率,并减少人为操作所带来的问题。
三、人员管理问题人员管理是车间生产的基本问题,也是车间管理中容易被忽视的一个方面。
通常来说,车间内的员工数量较大,工作职责比较分散,如果人员管理不当,就会导致人力资源的浪费,进而影响到生产效率。
常见的问题包括人员招聘不当、人员流动问题等。
对于这些问题,我们可以采取以下措施,加以解决。
首先要做好人员招聘,对于符合要求的员工从源头上把控好质量。
- 1、下载文档前请自行甄别文档内容的完整性,平台不提供额外的编辑、内容补充、找答案等附加服务。
- 2、"仅部分预览"的文档,不可在线预览部分如存在完整性等问题,可反馈申请退款(可完整预览的文档不适用该条件!)。
- 3、如文档侵犯您的权益,请联系客服反馈,我们会尽快为您处理(人工客服工作时间:9:00-18:30)。
生产线的改善方法及改善思路
一、生产线改善分析中,企业活动可分为3类:
1、能创造价值的步骤,如产品的加工过程。
2、不创造价值,但在现有技术下是不可避免的活动,如搬运、装卸等、不创造价值,可以立即取消的步骤。
3、消除第三类活动、减少第二类活动、增加与扩大第一类活动、达到改善生产线的目的。
根据以对企业活动的分析,可以结合对这些功能的实现投入的成本,然后利用价值分析规则对其进行价值的提升和改善。
采用精益生产的方式,能生产出高品质、低成本和交货快速且稳定的产品,且生产方法富有弹性和创新。
二、生产现场的改善指导原则
在精益生产中实现均衡生产的关键技术就是一个流生产方式,是按产品类别布置的多制程生产方式,可让产品在生产过程中实现单件流动,一个流生产是指从原材料投入到成品产出的整个制造加工过程,零件始终处于不停滞、不堆积、不超越的流动状态,按生产节拍逐个流动的生产方法。
需要做到低成本、高品质、高服务、高产出、消除各个环节的浪费:改善工作环境。
提高工作效率,达到生产线平衡,力争做到4个满惫(业主满意、客户满意、雇员满意、社会满意)。
精益生产方式的一个重要特征是实践性高于理论性,它源于生产现场,践行于生产现场,是边实践、边思考、边完善的产物。
在生产现场改善前,天行健管理公司建议应该对生产现场进行评估和作业测量,只有对生产现场进行实事求是的评估和测定,全面掌握和认识现况,对不合理的动作要素进行优化,减少作业时间,消除瓶颈,可采取的措施主要有:
1、瓶颈工序进行工作改善,如增加或改善工装、改善设备性能等
2、进行操作分析和动作研究,剔除不必要的操作,提高瓶颈工序工作人员效率或机能
3、增加瓶颈工序工作人员
4、将瓶颈工序的工作内容分担给其他工序
5、合并相关工序,重新进行工序排序
6、拆分工作时间较短的工序并入其他工序
二、生产线上的改善方法,须遵循以下原则:
1、有利于实现少人化
2、有利于操作者的作业
3、有利于物流与信息传递的控制
4、有利于质量保证
5、有利于全员生产维修(TPM, Total ProductiveMaintenance(全面生产性维修; 总生产维修制)开展
6、有利于实现标准作业
7、有利于保障安全
三、生产线的四种改善思路
1、平衡生产线
生产线平衡是对生产线上的全部工位进行平均化、调整作业负荷,以使各作业时间尽可能使用相近的技术手段与方法。
对整个作业内容进行重新组合,按照目标节拍进行调整,每一次作业内容的调整需与技术、生产等相关部门进行沟通协调,以增强改善活动的可操作性。
2、优化工序
制件的运动不间断、不堆积、不超越、不落地;创造无中断、无绕道、无交叉、无回流、无等待、无废品的增值活动流,制定创造价值流的行动方案。
优化工序流程的目的是通过对现场的宏观分析,减少和消除不合理、不增值的工艺内容、方法和程序,设计出最优化、经济、合理的工艺程序,缩短制造周期。
3、动作分析
动作分析是研究分析人在进行各种工作操作时的动作要素,**无效动作,使操作简便有效、轻松经济、以提高工作效率。
发现操作人员的无效动作、浪费现象或不安全因素; 简化操作,减少工人疲劳,提高操作安全性,建议在此基础上制定出标准作业程序。
对生产流程的安排,应遵守流程路线经济原则:
①路线越短越好
②减少停滞和消除重诬
③禁止逆行,消除交叉路线
④禁止孤岛加工
⑤减少动作的数量
⑥双手同时进行动作,其生产过程中采集的数据要真实、要及时利用、分析、判断、对出现的问题要及时解决并跟踪反馈。
4、实行“三现”机制
以现场为中心,处理事情以现场、现事、现物(三现)为主体,以车间主管为首的“三现”全员参与机制。
“三现”要求快速、有效地处理现场的异常状况,实现高效服务。
生产现场改善的5条黄金法则:
①如果发生问题,首先去现场
②检查问题发生的现场
③立刻采取暂时性措施
④查找问题发生的真正原因,拟定永久行动对策
⑤验证永久行动对策的有效性,使其标准化,以避免类似问题的再次发生。