列管式换热器结构设计共80页文档
列管式换热器结构设计共80页文档
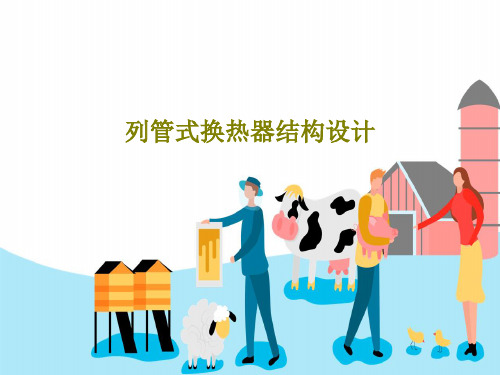
66、节制使快乐增加并使享受加强。 ——德 谟克利 特 67、今天应做的事没有做,明天再早也 是耽误 了。——裴斯 泰洛齐 68、决定一个人的一生,以及整个命运 的,只 是一瞬 之间。 ——歌 德 69、懒人无法享受休息之乐。——拉布 克 70、浪费时间是一桩大罪过。——卢梭
列管式换热器结构设计
11、用道德的示范来造就一个人,显然比用法律来约束他更有价值。—— 希腊
12、法律是无私的对谁都一视同仁。在每件事上,她都不徇私情。—— 托马斯
13、公正的法律限制不了好的自由,因为好人不会去做法律不允许的事 情。——弗劳德
14、法律是为了保护无辜而制定的。——爱略特 15、像房子一样,法律和法律都是相互依存的。——伯克
列管式换热器的设计

物性数据ρ2=879 kg/m3
CP2=1.813 kJ/kg·K
μ2=4.4×10-4N·S/m2
λ2= =1.384×10-4kW/m·K
2、水蒸汽(下标1表示)的物性数据
定性温度 蒸汽压力200Kpa下的沸点为Ts=119.6℃
物性数据ρ1=1.1273 kg/m3
γ1=2206.4 kJ/kg
蒸汽体积流量V=Gν=0.564×0.903=0.510 m3/s
取蒸汽流速u’=20 m/s
=0.180m=180mm
选用无缝热轧钢管(YB231-64)Φ194×6mm,长200mm。
3、冷凝水排出口
选用水煤气管 即Φ42.25×3.25mm,长100mm。
(七)、校核流体压力降
1、管程总压力降
1、列管式换热器是目前化工生产中应用最广泛的一种换热器,它的结构简单、坚固、容易制造、材料范围广泛,处理能力可以很大,适应性强。但在传热效率、设备紧凑性、单位传热面积的金属消耗量等方面还稍次于其他板式换热器。此次设计所采用的固定管板式换热器是其中最简单的一种。
2、由于水蒸汽的对流传热系数比苯侧的对流传热系数大得多,根据壁温总是趋近于对流传热系数较大的一侧流体的温度实际情况,壁温与流体温度相差无几,因此本次设计不采用热补偿装置。
实际管数n=NT-NTb-n3=169-23=146根,每程73根排列管
实际流速
m/s
与初假设苯的流速u’2=0.55m/s相近,可行。
3、换热器长径比
符合要求( )
(五)、校核计算
1、校核总传热系数K值
(1)管内对流传热系数α2
W/m2·℃
(2)管外对流传热系数α1
式中:n为水平管束垂直列上的管数,n=7;
化工原理课程设计---列管式换热器的设计
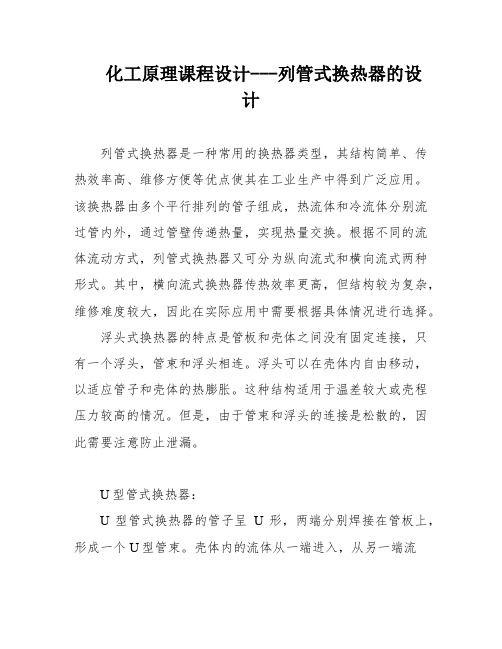
化工原理课程设计---列管式换热器的设计列管式换热器是一种常用的换热器类型,其结构简单、传热效率高、维修方便等优点使其在工业生产中得到广泛应用。
该换热器由多个平行排列的管子组成,热流体和冷流体分别流过管内外,通过管壁传递热量,实现热量交换。
根据不同的流体流动方式,列管式换热器又可分为纵向流式和横向流式两种形式。
其中,横向流式换热器传热效率更高,但结构较为复杂,维修难度较大,因此在实际应用中需要根据具体情况进行选择。
浮头式换热器的特点是管板和壳体之间没有固定连接,只有一个浮头,管束和浮头相连。
浮头可以在壳体内自由移动,以适应管子和壳体的热膨胀。
这种结构适用于温差较大或壳程压力较高的情况。
但是,由于管束和浮头的连接是松散的,因此需要注意防止泄漏。
U型管式换热器:U型管式换热器的管子呈U形,两端分别焊接在管板上,形成一个U型管束。
壳体内的流体从一端进入,从另一端流出,管内的流体也是如此。
这种结构适用于流体腐蚀性较强的情况,因为管子可以很容易地更换。
多管程换热器:多管程换热器是将管束分成多个组,每组管子单独连接到管板上,形成多个管程。
这种结构可以提高传热效率,但也会增加流体阻力。
因此,需要根据具体情况来选择多管程的数量。
总之,列管式换热器是一种广泛应用于化工及酒精生产的换热器。
不同的结构适用于不同的工艺条件,需要根据具体情况来选择合适的换热器。
在使用过程中,需要注意保养和维护,及时清洗和更换损坏的部件,以保证换热器的正常运行。
换热器的一块管板与外壳用法兰连接,另一块管板不与外壳连接,这种结构称为浮头式换热器。
浮头式换热器的优点是管束可以拉出以便清洗,管束的膨胀不受壳体约束,因此在两种介质温差大的情况下,不会因管束与壳体的热膨胀量不同而产生温差应力。
但其缺点是结构复杂,造价高。
填料式换热器的管束一端可以自由膨胀,结构比浮头式简单,造价也较低。
但壳程内介质有外漏的可能,因此不应处理易挥发、易燃、易爆和有毒的介质。
列管式换热器(设计举例)
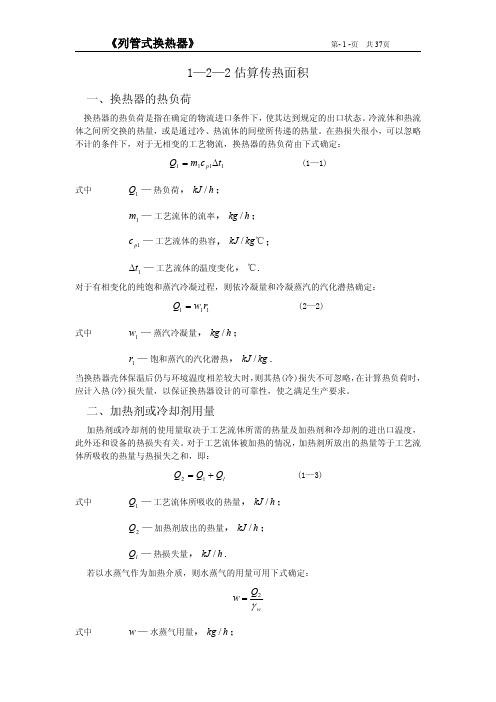
六、管束的分程方法
在设计中,如采用多管程,则需要在管箱中安装分程隔板。分程时,应使各程管子数目 大致相等,隔板形式要简单,密封长度要短。为使制造、维修和操作方便,一般采用为偶数 管程。 管程的分程方法常采用平行和 T 形方式。其中后管箱中隔板形式和介质的流通顺序见图 1—14。
七、壳体内径
换热器壳体内径取决于传热管数,管心距和传热管的排列方式。 对于单管程换热器,壳体内径由下式确定:
《列管式换热器》
第- 6 -页
共 37页
二、选取管长、确定管程数和总管数
选定了管径和管内流速后,可依下式确定换热器的单程管子数:
ns
V
4
(1—9)
2
d1 u
式中
n s — 单程管子数目;
V — 管程流体的体积流量, m 3 / s ;
d1 — 传热管内径, m ;
u — 管内流体速度, m / s .
《列管式换热器》
第- 5 -页
共 37页
管内流速的大小对于传热膜系数及压力降的影响较大,所以选择时要全面分析比较。一 般要求所选择的流速应使流体处于湍流状态,即雷诺系数大于 10000.只有在流体粘度过大 时, 为避免压力降过大才不得不采用层流状态。 特别对于传热阻力较大的流体或易结垢流体 应选取较大流速,以利于增加传热系数,降低结垢程度和结垢速度。另外还要考虑在所选择 的流速下, 换热器应有适当的管长和管程数, 并保证不会由于流体的动力冲击导致管子强烈 振动而损坏换热器。 列管式换热器中常见的流速范围见表(1—3)~(1—5), 可在设计中参考。
二、加热剂或冷却剂用量
加热剂或冷却剂的使用量取决于工艺流体所需的热量及加热剂和冷却剂的进出口温度, 此外还和设备的热损失有关。 对于工艺流体被加热的情况, 加热剂所放出的热量等于工艺流 体所吸收的热量与热损失之和,即:
列管式换热器的设计.doc

列管式换热器的设计列管式换热器的应用已有很悠久的历史。
现在,它被当作一种传统的标准换热设备在很多工业部门中大量使用,尤其在化工、石油、能源设备等部门所使用的换热设备中,列管式换热器仍处于主导地位。
同时板式换热器也已成为高效、紧凑的换热设备,大量地应用于工业中。
为此本章对这两类换热器的工艺设计进行介绍。
列管式换热器的设计资料较完善,已有系列化标准。
目前我国列管式换热器的设计、制造、检验、验收按“钢制管壳式(即列管式)换热器”(GB151)标准执行。
列管式换热器的设计和分析包括热力设计、流动设计、结构设计以及强度设计。
其中以热力设计最为重要。
不仅在设计一台新的换热器时需要进行热力设计,而且对于已生产出来的,甚至已投人使用的换热器在检验它是否满足使用要求对,均需进行这方面的工作。
热力设计指的是根据使用单位提出的基本要求,合理地选择运行参数,并根据传热学的知识进行传热计算。
流动设计主要是计算压降,其目的就是为换热器的辅助设备——例如泵的选择做准备。
当然,热力设计和流动设计两者是密切关联的,特别是进行热力计算时常需从流动设计中获取某些参数。
结构设计指的是根据传热面积的大小计算其主要零部件的尺寸,例如管子的直径、长度、根数、壳体的直径、折流板的长度和数目、隔板的数目及布置以及连接管的尺寸,等等。
在某些情况下还需对换热器的主要零部件——特别是受压部件做应力计算,并校核其强度。
对于在高温高压下工作的换热器,更不能忽视这方面的工作。
这是保证安全生产的前提。
在做强度计算时,应尽量采用国产的标准材料和部件,根据我国压力容器安全技术规定进行计算或校核(该部分内容属设备计算,此处从略)。
列管式换热器的工艺设计主要包括以下内容:①根据换热任务和有关要求确定设计方案;②初步确定换热器的结构和尺寸;③核算换热器的传热面积和流体阻力;④确定换热器的工艺结构。
1.1设计方案的确定1.1.1换热器类型的选择(1)固定管板式换热器这类换热器如图2-1(a)所示。
(完整版)列管式换热器设计

第一章列管式换热器的设计1.1概述列管式换热器是一种较早发展起来的型式,设计资料和数据比较完善,目前在许多国家中已有系列化标准。
列管式换热器在换热效率,紧凑性和金属消耗量等方面不及其他新型换热器,但是它具有结构牢固,适应性大,材料范围广泛等独特优点,因而在各种换热器的竞争发展中得以继续应用下去。
目前仍是化工、石油和石油化工中换热器的主要类型,在高温高压和大型换热器中,仍占绝对优势。
例如在炼油厂中作为加热或冷却用的换热器、蒸馏操作中蒸馏釜(或再沸器)和冷凝器、化工厂中蒸发设备的加热室等,大都采用列管式换热器[3]。
1.2列管换热器型式的选择列管式换热器种类很多,目前广泛使用的按其温度差补偿结构来分,主要有以下几种:(1)固定管板式换热器:这类换热器的结构比较简单、紧凑,造价便宜,但管外不能机械清洗。
此种换热器管束连接在管板上,管板分别焊在外壳两端,并在其上连接有顶盖,顶盖和壳体装有流体进出口接管。
通常在管外装置一系列垂直于管束的挡板。
同时管子和管板与外壳的连接都是刚性的,而管内管外是两种不同温度的流体。
因此,当管壁与壳壁温度相差较大时,由于两者的热膨胀不同,产生了很大的温差应力,以致管子扭弯或使管子从管板上松脱,甚至毁坏整个换热器。
为了克服温差应力必须有温度补偿装置,一般在管壁与壳壁温度相差50℃以上时,为安全起见,换热器应有温差补偿装置。
(2)浮头换热器:换热器的一块管板用法兰与外壳相连接,另一块管板不与外壳连接,以便管子受热或冷却时可以自由伸缩,但在这块管板上来连接有一个顶盖,称之为“浮头”,所以这种换热器叫做浮头式换热器。
这种型式的优点为:管束可以拉出,以便清洗;管束的膨胀不受壳体的约束,因而当两种换热介质的温差大时,不会因管束与壳体的热膨胀量的不同而产生温差应力。
其缺点为结构复杂,造价高。
(3)填料函式换热器:这类换热器管束一端可以自由膨胀,结构与比浮头式简单,造价也比浮头式低。
但壳程内介质有外漏的可能,壳程终不应处理易挥发、易爆、易燃和有毒的介质。
化工原理课程设计列管式换热器

———列管式换热器
第1页 ,共79页。
一、设计方案的确定
1、换热器类型的选择 2、流动空间的选择 3、流速的确定 4、流动方式的选择 5、流体出口温度的确定
二、列管式换热器的结构
三、列管式换热器设计计算
第2页 ,共79页。
1、换热器类型的选择
固定管板式换热器
固定管板式换热器管束连接在管板上 ,管板与壳体焊接。
第3页 ,共79页。
优点: 1)传热面积比浮头式换热器大20%-30%; 2) 旁路漏流较水; 3)锻件使用较少; 4) 没有内漏。
缺点: 1) 不适用于换热管与壳程圆筒的热膨胀变形差很大 的场合 , 管板与管头之间易产生温差应力而损坏; (为了减少热应力 ,通常在固定管板式换热器中设置 柔性元件. 如: 设置膨胀节. 来吸收热膨胀差)
力之和 。一般进 、 出口阻力可忽略不计 , 故管程总阻力的计算式为
每程直管阻力;
每程回弯阻力
式中 ΔPi 、ΔPr------分别为直管及回弯管中
因摩擦阻力引起的压强降 ,N/m2
Ft-----结垢校正因数 ,无因次 ,对于φ25×2.5mm的管子 ,取为1.4,
对于φ19×2mm的管子 ,取为1.5;
圆缺形
第21页 ,共79页。
. 圆盘形
两相邻挡板的距离(板间距)h为外壳内径D的(0.2~ 1)倍 。板间距过小 ,不便于制造和检修 ,阻力也较 大 。板间距过大 ,流体就难于垂直地流过管束 ,使 对流传热系数下降。
我国系列标准中采用的挡板间距为:
固定管板式有100mm , 150mm ,200mm ,300mm ,450mm ,600mm , 700mm七种
第20页 ,共79页。
列管式换热器设计正文
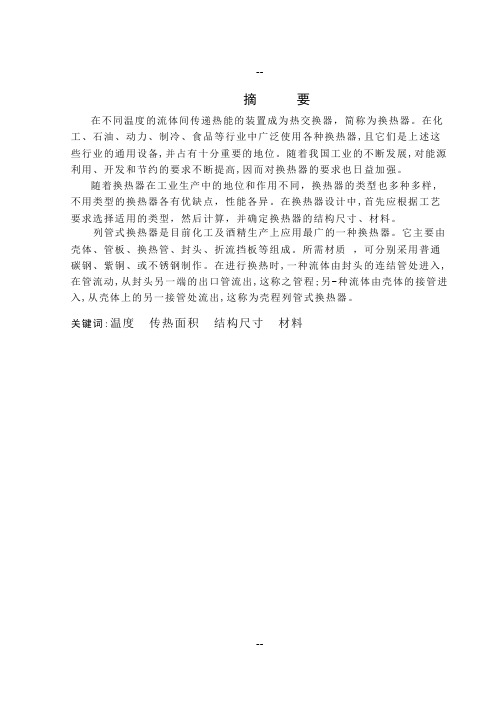
摘要在不同温度的流体间传递热能的装置成为热交换器,简称为换热器。
在化工、石油、动力、制冷、食品等行业中广泛使用各种换热器,且它们是上述这些行业的通用设备,并占有十分重要的地位。
随着我国工业的不断发展,对能源利用、开发和节约的要求不断提高,因而对换热器的要求也日益加强。
随着换热器在工业生产中的地位和作用不同,换热器的类型也多种多样,不用类型的换热器各有优缺点,性能各异。
在换热器设计中,首先应根据工艺要求选择适用的类型,然后计算,并确定换热器的结构尺寸、材料。
列管式换热器是目前化工及酒精生产上应用最广的一种换热器。
它主要由壳体、管板、换热管、封头、折流挡板等组成。
所需材质,可分别采用普通碳钢、紫铜、或不锈钢制作。
在进行换热时,一种流体由封头的连结管处进入,在管流动,从封头另一端的出口管流出,这称之管程;另-种流体由壳体的接管进入,从壳体上的另一接管处流出,这称为壳程列管式换热器。
关键词:温度传热面积结构尺寸材料1.前言1.1列管式换热器设计的意义换热器是建筑采热取暖生产中必不可少的设备,近几年由于新技术的发展,各种类型的换热器越来越受工业界的重视,而换热器又是节能措施中较为关键的设备,广泛应用于化工、医药、食品饮料、酒精生产、制冷、民用等工艺;因此,无论是从工业的发展还是从能源的有效利用,换热器的合理设计、制造、选型和运行都具有非常重要的意义。
1.2列管式换热器的工作原理进行换热的冷热两种流体,一种在管内流动,称为管程流体;另一种在管外流动,称为壳程流体。
为提高管外流体的传热分系数,通常在壳体内安装若干挡板。
挡板可提高壳程流体速度,迫使流体ﻫ按规定路程多次横向通过管束,增强流体湍流程度。
换热管在管板上按等边三角形或正方形排列。
等边三角形排列较紧凑,管外流体湍动程度高,传热分系数大;正方形排列则管外清洗方便,适用于易ﻫ结垢的流体。
ﻫ流体每通过管束一次称为一个管程;每通过壳体一次称为一个壳程。
按换热方式可分为单壳程单管程换热器、双管程、多管程、多壳程换热器。
- 1、下载文档前请自行甄别文档内容的完整性,平台不提供额外的编辑、内容补充、找答案等附加服务。
- 2、"仅部分预览"的文档,不可在线预览部分如存在完整性等问题,可反馈申请退款(可完整预览的文档不适用该条件!)。
- 3、如文档侵犯您的权益,请联系客服反馈,我们会尽快为您处理(人工客服工作时间:9:00-18:30)。
路,对于需要将管束经常抽出清洗者,采用此结构。
管板与隔板的连接形式 如图 (a)为隔板与管板焊接, (b)是隔板用螺栓联接在焊于管板的角铁上的可
拆结构.
3、分割流板
在壳体上有对称的两个进口及一个出口时,如图中 J型壳体
列管式换热器结构设计
第三章 列管换热器结构设计
目录 第一节 列管式换热器零部件的工艺结构设计 第二节 列管式换热器机械结构设计 第三节 其他结构设计 第四节 列管式换热器机械设计 第五节 设计示例
第一节 列管式换热器零部件的工艺结构设计
一、分程隔板
在换热器中,要提高流体的给热系数,常采用 隔板来增加程数以提高流体速度。 1、管程分程隔板
(2)管孔中心距 折流板上管孔中心距见表4-7,公差为相邻两孔±0.03, 任意两Ⅳ±1.00mm。
(3)管孔加工 折流板上管孔加工后两端必须倒时,无需设置折流板; 换热器无支承跨距超过表4-6规定时,应设置支持板; 浮头式换热器浮头端必须设置支持板,支持板可采
(2)拉杆尺寸 按图4-10和表4-9决定
(3)拉杆布置 应尽量均匀布置在管束的外边缘
四、旁路挡板、防冲板
1、旁路档板 主要作用:
为防止壳程物料从这些旁路大量短路,在管边缘的 适当位置安装旁路挡板和在分程部位的适当的地方安 装假管或带定距管的拉杆来增大旁路的阻力,迫使物 料通过管束进行换热。
2、防冲板
ρv2>740kg/m.s2
防冲板的安装形式(图4-15)
五、接管
1、接管的一般要求: (1)接管不应凸出壳体内表面 (2)接管应尽量沿径向或轴向布置 (3)设计温度在3000C以上时, (4)用整体法兰。对利用接管仍不能放气和排液,应设置
放气口 (5)操作允许时,接管与外部管线的连接也可采用焊接。 (6)必要时可设置温度计接口、压力表及液面计接口。
3、由工艺条件决定管内流体给热系数αi很小而管外 α0又很大时,这时就没有必要通过减少间距B来提 高壳程的给热系数α0
4、折流板一般应使靠近管板的第一块或最后一块折 流板尽可能靠近壳程进、出口接管,靠近管板的折 流板与管板间距离如图4-7所示:
2、弓形折流板排列方式确定 (1)水平切口(图a、b,缺口上下布置) (2)垂直切口(图c,缺口左右布置) (3)倾斜切口(图4-5a,缺口倾斜布置) (4)双弓形缺口与双弓形板交替(图4-5b)
当承受脉动流体或隔板压差很大时,隔板的厚度应适 当增厚,当厚度大于10mm的分程隔板,在距端部15mm处开 始削成楔形,使端部保持10mm。
2、纵向隔板 在壳侧介质流量较小的情况下,在壳程内安装一
平行于传热管的纵向隔板。如图4-2
防止短路的方式: 如图4-3所示: (a)为隔板直接与筒体内壁焊接,但必须考虑
用加厚的环板。
三、拉杆、定距管
1、拉杆的结构形式 (1)采用全焊接方法 如图4-9(c)。 (2)拉杆定距管结构 最常见的形式如图4-9 (3)螺纹与焊接相结合如图4-9(a) (4)定距螺栓拉杆如图4-9(e)
拉杆的结构形式(图4-9)
2、拉杆直径、数量和尺寸
(1)拉杆直径和数量 按表4-7和表4-8选取
(1)防冲板的用途及其设置条件 用途: 为了防止壳程物料进口流体对换热管表面的直接冲刷, 引起侵蚀及振动。
设置条件: 对有腐蚀或磨蚀的气体和蒸汽应设置防冲板。 对于流体物料,当其值超过下列值,设置防冲板。 ① 非腐蚀、非磨蚀的单相流体ρv2>2230kg/m.s2 ② 其他流体、包括沸点下的流体,其中
2、接管直径的确定 管径的选择取决于: 1)适宜的流速处理量, 2)结构协调, 3)强度要求
❖ 在选取时常综合考虑如下几种因素: ❖ (1)使接管内的流速为相应管、壳程流速的1.2~
1.4倍。 ❖ (2)在压降允许的条件下,使接管内流速为下值:
管程接管 ρv2〈3300kg/m.s2
壳程接管 ρv2 〈 2200kg/m.s2
二 折流板或支撑板
几种常见的折流板形式见图4-5所示
1、弓形折流板的主要几何参数 弓形折流板引导流体以垂直方向横穿过管束,
能提供高度的湍动和良好的传热,主要几何参数是 切口尺寸h和挡板间距B.
在上述原则下确定的尺寸不是绝对的,应考虑制造、安 装及实际情况进行圆整及调节为适用于工程上尺寸。 1、切口高度h按20%(或25%)Di确定后还考虑折流板制造 中,可能产生的管口变形。 2、间距B=(1/5~1)Di之间确定、从最小50mm起按50mm, 100mm,200mm,300mm,450mm,600mm圆整。
❖ (3)管、壳程接管内的流速参考表4-10、 表4-11选 取。
l
4.接管位置最小尺寸 如图
带补强圈 L1≥B/2+(b-4)+C; 无补强圈 L1≥ d0/2+(b-4)+C;
管箱接管最小尺寸见图4-17按下式估算:
带补强圈 L2≥B/2+hf+C; 无补强圈 L2≥ d0/2+ hf+C
3、折流板与壳程间隙 折留板与壳程间隙依据制造安装调节,在保证顺利装 入的前提下,越小越好,一般浮头式和U型管式换热器 可允许比固定管板式大1mm,折流板外圆直径和下偏差 见表4-2。
4、折流板厚度 折流板厚度与壳体直径、换热管有无支承长度有关,
其数值不得小于表4-3规定。 5、折流板的管孔 (1)折流板的管孔直径与公差按GB151规定:Ⅰ级换热 器,管孔直径与允许差按表4-4规定;Ⅱ级换热器按表45规定。
管程分程隔板是用来将管内流体分程,一个管程 意味着流体在管内走一次,管程分程隔板装置在管箱 内,根据所需分的程数的不同有不同的组合.
应使各程管子数目大致相等,形式要简单,焊缝 尽量少,密封长度要短,温度不超过28℃左右为宜。
(1)分程隔板结构 分程隔板应采用与封头、管箱短节同等材料,除密封
面外,应满焊于管箱上。设计时要求管箱隔板的密封面与 管箱法兰密封面,管板密封面与分程槽面必须处于同一基 准面。 (2)分程隔板厚度及有关尺寸