列管式换热器课程设计报告书
列管式换热器课程设计报告书
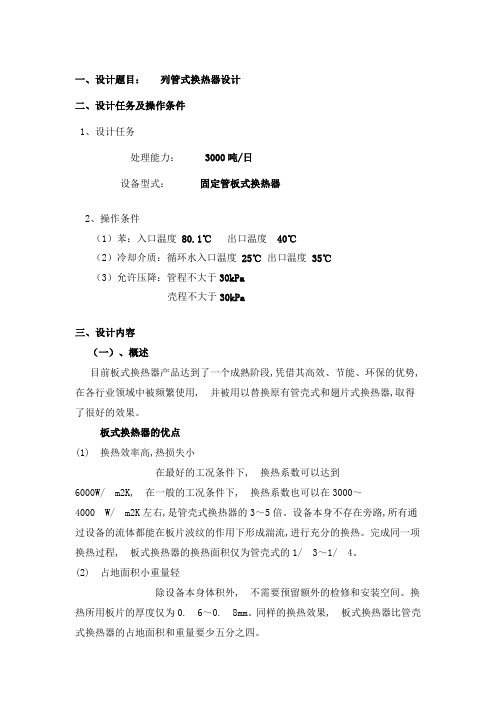
一、设计题目:列管式换热器设计二、设计任务及操作条件1、设计任务处理能力:3000吨/日设备型式:固定管板式换热器2、操作条件(1)苯:入口温度80.1℃出口温度40℃(2)冷却介质:循环水入口温度25℃出口温度35℃(3)允许压降:管程不大于30kPa壳程不大于30kPa三、设计内容(一)、概述目前板式换热器产品达到了一个成熟阶段,凭借其高效、节能、环保的优势,在各行业领域中被频繁使用, 并被用以替换原有管壳式和翅片式换热器,取得了很好的效果。
板式换热器的优点(1) 换热效率高,热损失小在最好的工况条件下, 换热系数可以达到6000W/ m2K, 在一般的工况条件下, 换热系数也可以在3000~4000 W/ m2K左右,是管壳式换热器的3~5倍。
设备本身不存在旁路,所有通过设备的流体都能在板片波纹的作用下形成湍流,进行充分的换热。
完成同一项换热过程, 板式换热器的换热面积仅为管壳式的1/ 3~1/ 4。
(2) 占地面积小重量轻除设备本身体积外, 不需要预留额外的检修和安装空间。
换热所用板片的厚度仅为0. 6~0. 8mm。
同样的换热效果, 板式换热器比管壳式换热器的占地面积和重量要少五分之四。
(3) 污垢系数低流体在板片间剧烈翻腾形成湍流, 优秀的板片设计避免了死区的存在, 使得杂质不易在通道中沉积堵塞,保证了良好的换热效果。
(4) 检修、清洗方便换热板片通过夹紧螺柱的夹紧力组装在一起,当检修、清洗时, 仅需松开夹紧螺柱即可卸下板片进行冲刷清洗。
(5) 产品适用面广设备最高耐温可达180 ℃, 耐压2. 0MPa , 特别适应各种工艺过程中的加热、冷却、热回收、冷凝以及单元设备食品消毒等方面, 在低品位热能回收方面, 具有明显的经济效益。
各类材料的换热板片也可适应工况对腐蚀性的要求。
当然板式换热器也存在一定的缺点, 比如工作压力和工作温度不是很高, 限制了其在较为复杂工况中的使用。
同时由于板片通道较小,也不适宜用于杂质较多,颗粒较大的介质。
化工原理课程设计 列管式换热器
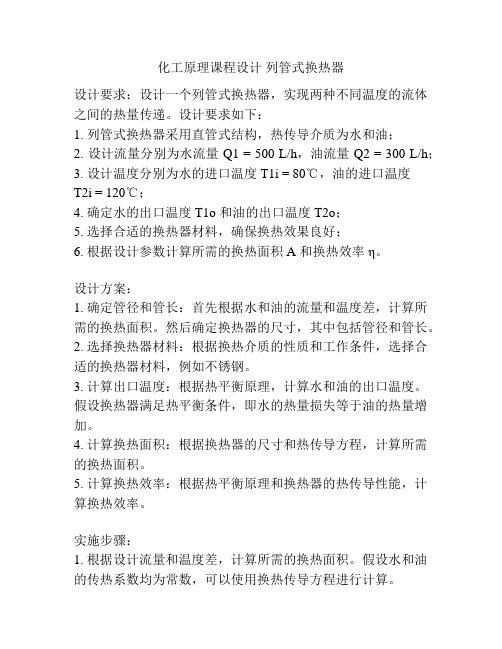
化工原理课程设计列管式换热器设计要求:设计一个列管式换热器,实现两种不同温度的流体之间的热量传递。
设计要求如下:1. 列管式换热器采用直管式结构,热传导介质为水和油;2. 设计流量分别为水流量 Q1 = 500 L/h,油流量 Q2 = 300 L/h;3. 设计温度分别为水的进口温度 T1i = 80℃,油的进口温度T2i = 120℃;4. 确定水的出口温度 T1o 和油的出口温度 T2o;5. 选择合适的换热器材料,确保换热效果良好;6. 根据设计参数计算所需的换热面积 A 和换热效率η。
设计方案:1. 确定管径和管长:首先根据水和油的流量和温度差,计算所需的换热面积。
然后确定换热器的尺寸,其中包括管径和管长。
2. 选择换热器材料:根据换热介质的性质和工作条件,选择合适的换热器材料,例如不锈钢。
3. 计算出口温度:根据热平衡原理,计算水和油的出口温度。
假设换热器满足热平衡条件,即水的热量损失等于油的热量增加。
4. 计算换热面积:根据换热器的尺寸和热传导方程,计算所需的换热面积。
5. 计算换热效率:根据热平衡原理和换热器的热传导性能,计算换热效率。
实施步骤:1. 根据设计流量和温度差,计算所需的换热面积。
假设水和油的传热系数均为常数,可以使用换热传导方程进行计算。
2. 根据所需的换热面积和理论计算值,选择合适的换热器尺寸。
3. 根据所选换热器材料,计算换热器的尺寸和管径。
假设管壁温度近似等于流体温度。
4. 根据热平衡原理,计算出口温度。
假设热平衡条件满足,即水的热量损失等于油的热量增加。
5. 根据所选材料和尺寸,计算换热效率。
假设换热器的热传导系数为常数,使用换热效率计算公式进行计算。
总结:本课程设计主要针对列管式换热器的设计,通过选择合适的换热器材料和计算换热器的尺寸,实现了水和油之间的热量传递。
根据设计要求,通过计算出口温度和换热效率,验证了设计方案的合理性。
设计过程需要考虑多方面的因素,如流体性质、流量和温度差等。
化工原理课程设计---列管式换热器的设计
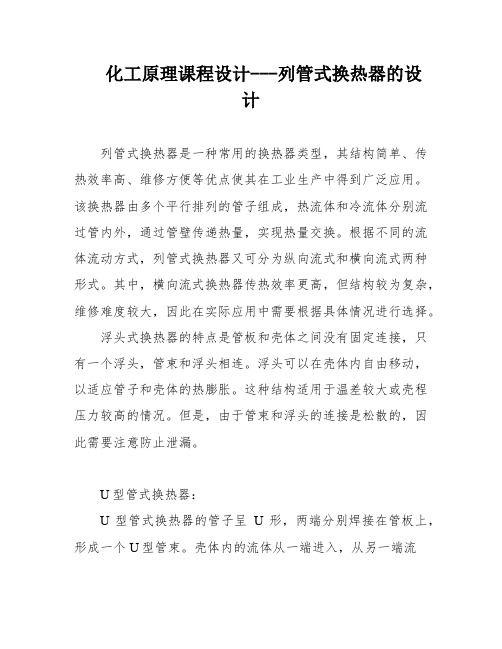
化工原理课程设计---列管式换热器的设计列管式换热器是一种常用的换热器类型,其结构简单、传热效率高、维修方便等优点使其在工业生产中得到广泛应用。
该换热器由多个平行排列的管子组成,热流体和冷流体分别流过管内外,通过管壁传递热量,实现热量交换。
根据不同的流体流动方式,列管式换热器又可分为纵向流式和横向流式两种形式。
其中,横向流式换热器传热效率更高,但结构较为复杂,维修难度较大,因此在实际应用中需要根据具体情况进行选择。
浮头式换热器的特点是管板和壳体之间没有固定连接,只有一个浮头,管束和浮头相连。
浮头可以在壳体内自由移动,以适应管子和壳体的热膨胀。
这种结构适用于温差较大或壳程压力较高的情况。
但是,由于管束和浮头的连接是松散的,因此需要注意防止泄漏。
U型管式换热器:U型管式换热器的管子呈U形,两端分别焊接在管板上,形成一个U型管束。
壳体内的流体从一端进入,从另一端流出,管内的流体也是如此。
这种结构适用于流体腐蚀性较强的情况,因为管子可以很容易地更换。
多管程换热器:多管程换热器是将管束分成多个组,每组管子单独连接到管板上,形成多个管程。
这种结构可以提高传热效率,但也会增加流体阻力。
因此,需要根据具体情况来选择多管程的数量。
总之,列管式换热器是一种广泛应用于化工及酒精生产的换热器。
不同的结构适用于不同的工艺条件,需要根据具体情况来选择合适的换热器。
在使用过程中,需要注意保养和维护,及时清洗和更换损坏的部件,以保证换热器的正常运行。
换热器的一块管板与外壳用法兰连接,另一块管板不与外壳连接,这种结构称为浮头式换热器。
浮头式换热器的优点是管束可以拉出以便清洗,管束的膨胀不受壳体约束,因此在两种介质温差大的情况下,不会因管束与壳体的热膨胀量不同而产生温差应力。
但其缺点是结构复杂,造价高。
填料式换热器的管束一端可以自由膨胀,结构比浮头式简单,造价也较低。
但壳程内介质有外漏的可能,因此不应处理易挥发、易燃、易爆和有毒的介质。
列管式换热器的设计(化工原理课程设计)
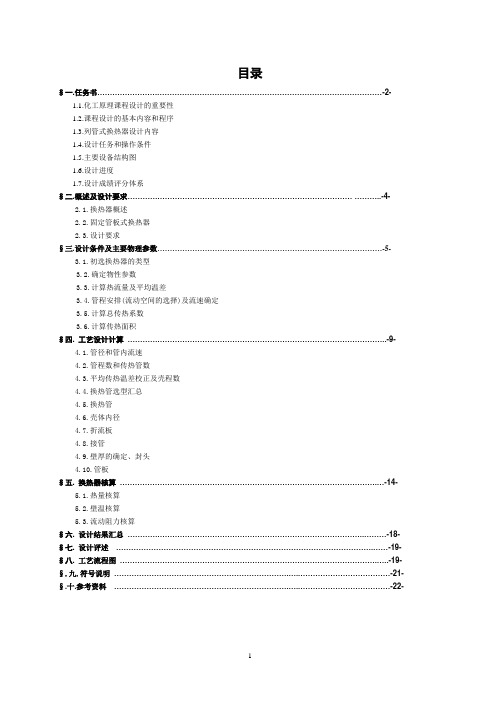
目录§一.任务书 (2)1.1.化工原理课程设计的重要性1.2.课程设计的基本内容和程序1.3.列管式换热器设计内容1.4.设计任务和操作条件1.5.主要设备结构图1.6.设计进度1.7.设计成绩评分体系§二.概述及设计要求 (4)2.1.换热器概述2.2.固定管板式换热器2.3.设计要求§三.设计条件及主要物理参数 (5)3.1.初选换热器的类型3.2.确定物性参数3.3.计算热流量及平均温差3.4.管程安排(流动空间的选择)及流速确定3.5.计算总传热系数3.6.计算传热面积§四. 工艺设计计算 (9)4.1.管径和管内流速4.2.管程数和传热管数4.3.平均传热温差校正及壳程数4.4.换热管选型汇总4.5.换热管4.6.壳体内径4.7.折流板4.8.接管4.9.壁厚的确定、封头4.10.管板§五.换热器核算 (14)5.1.热量核算5.2.壁温核算5.3.流动阻力核算§六. 设计结果汇总 (18)§七. 设计评述 (19)§八. 工艺流程图 (19)§.九.符号说明 (21)§.十.参考资料 (22)§一.化工原理课程设计任务书1.1.化工原理课程设计的重要性化工原理课程设计是学生学完基础课程以及化工原理课程以后,进一步学习工程设计的基础知识,培养学生工程设计能力的重要教学环节,也是学生综合运用化工原理和相关选修课程的知识,联系生产实际,完成以单元操作为主的一次工程设计的实践。
通过这一环节,使学生掌握单元操作设计的基本程序和方法,熟悉查阅技术资料、国家技术标准,正确选用公式和数据,运用简洁文字和工程语言正确表述设计思想和结果;并在此过程中使学生养成尊重实际问题向实践学习,实事求是的科学态度,逐步树立正确的设计思想、经济观点和严谨、认真的工作作风,提高学生综合运用所学的知识,独立解决实际问题的能力。
列管式换热器课程设计报告书
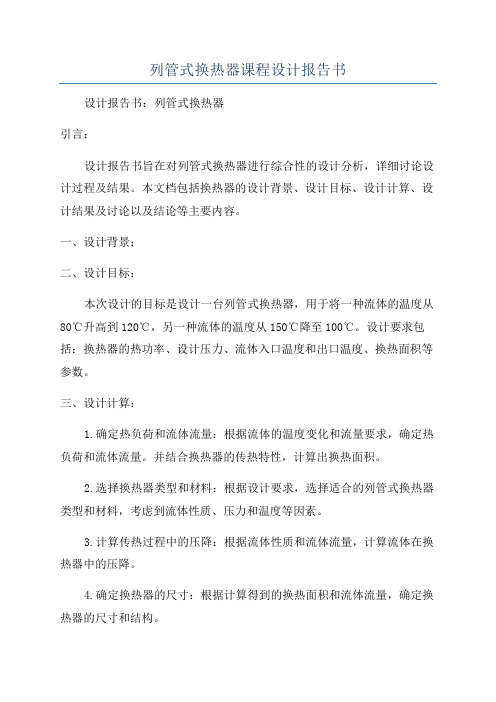
列管式换热器课程设计报告书设计报告书:列管式换热器引言:设计报告书旨在对列管式换热器进行综合性的设计分析,详细讨论设计过程及结果。
本文档包括换热器的设计背景、设计目标、设计计算、设计结果及讨论以及结论等主要内容。
一、设计背景:二、设计目标:本次设计的目标是设计一台列管式换热器,用于将一种流体的温度从80℃升高到120℃,另一种流体的温度从150℃降至100℃。
设计要求包括:换热器的热功率、设计压力、流体入口温度和出口温度、换热面积等参数。
三、设计计算:1.确定热负荷和流体流量:根据流体的温度变化和流量要求,确定热负荷和流体流量。
并结合换热器的传热特性,计算出换热面积。
2.选择换热器类型和材料:根据设计要求,选择适合的列管式换热器类型和材料,考虑到流体性质、压力和温度等因素。
3.计算传热过程中的压降:根据流体性质和流体流量,计算流体在换热器中的压降。
4.确定换热器的尺寸:根据计算得到的换热面积和流体流量,确定换热器的尺寸和结构。
四、设计结果及讨论:根据实际情况及设计计算,确定了列管式换热器的参数和结构。
设计结果展示了换热器的尺寸、换热面积、流量参数等,并进行了相关讨论。
同时,设计结果还包括选择的换热器材料、设计压力和温度等。
五、结论:本次设计报告书综合分析了列管式换热器的设计过程及结果。
根据设计目标和计算得出的结果,可得出以下结论:1.设计的列管式换热器满足了设计要求,能够实现流体的热交换。
2.使用合适的材料和尺寸,可以优化换热器的性能和效率。
3.设计过程中需要考虑流体的性质、温度、压力和流量等因素,以确保换热器的安全和稳定运行。
结语:本设计报告书详细介绍了列管式换热器的设计背景、设计目标、设计计算、设计结果及讨论,以及最终得出的结论。
通过本次设计,我们加深了对列管式换热器的理解,并提高了设计能力。
在实际工程中,将根据需求及具体情况进行设计,并综合考虑各种因素,以确保换热器的优化运行。
(完整版)列管式换热器设计

第一章列管式换热器的设计1.1概述列管式换热器是一种较早发展起来的型式,设计资料和数据比较完善,目前在许多国家中已有系列化标准。
列管式换热器在换热效率,紧凑性和金属消耗量等方面不及其他新型换热器,但是它具有结构牢固,适应性大,材料范围广泛等独特优点,因而在各种换热器的竞争发展中得以继续应用下去。
目前仍是化工、石油和石油化工中换热器的主要类型,在高温高压和大型换热器中,仍占绝对优势。
例如在炼油厂中作为加热或冷却用的换热器、蒸馏操作中蒸馏釜(或再沸器)和冷凝器、化工厂中蒸发设备的加热室等,大都采用列管式换热器[3]。
1.2列管换热器型式的选择列管式换热器种类很多,目前广泛使用的按其温度差补偿结构来分,主要有以下几种:(1)固定管板式换热器:这类换热器的结构比较简单、紧凑,造价便宜,但管外不能机械清洗。
此种换热器管束连接在管板上,管板分别焊在外壳两端,并在其上连接有顶盖,顶盖和壳体装有流体进出口接管。
通常在管外装置一系列垂直于管束的挡板。
同时管子和管板与外壳的连接都是刚性的,而管内管外是两种不同温度的流体。
因此,当管壁与壳壁温度相差较大时,由于两者的热膨胀不同,产生了很大的温差应力,以致管子扭弯或使管子从管板上松脱,甚至毁坏整个换热器。
为了克服温差应力必须有温度补偿装置,一般在管壁与壳壁温度相差50℃以上时,为安全起见,换热器应有温差补偿装置。
(2)浮头换热器:换热器的一块管板用法兰与外壳相连接,另一块管板不与外壳连接,以便管子受热或冷却时可以自由伸缩,但在这块管板上来连接有一个顶盖,称之为“浮头”,所以这种换热器叫做浮头式换热器。
这种型式的优点为:管束可以拉出,以便清洗;管束的膨胀不受壳体的约束,因而当两种换热介质的温差大时,不会因管束与壳体的热膨胀量的不同而产生温差应力。
其缺点为结构复杂,造价高。
(3)填料函式换热器:这类换热器管束一端可以自由膨胀,结构与比浮头式简单,造价也比浮头式低。
但壳程内介质有外漏的可能,壳程终不应处理易挥发、易爆、易燃和有毒的介质。
列管式换热器课程设计报告书

列管式换热器课程设计报告书列管式换热器是一种常见的换热设备,其结构简单、效率高,广泛应用于石化、电力、制药等工业领域。
为了进一步了解列管式换热器的工作原理和设计方法,本课程设计以列管式换热器的设计与优化为主题,旨在培养学生运用所学知识解决实际工程问题的能力。
一、课程设计的目标与任务本课程设计的目标是通过学习列管式换热器的设计原理和方法,培养学生的设计能力和创新思维,使其掌握列管式换热器的设计与优化方法。
具体任务如下:1.研究列管式换热器的原理和结构,了解其工作过程和基本参数;2.学习换热器设计的基本原理和方法,包括换热面积计算、传热系数估算等;3.进行列管式换热器的设计计算和优化分析;4.编写课程设计报告书,总结设计过程和结果。
二、课程设计的内容和方法1.理论学习通过教材、参考书籍和互联网资源,学习列管式换热器的基本原理、结构和工作过程。
学生还需深入了解换热器的传热理论和设计方法,了解不同种类的换热器。
2.设计计算学生根据教师提供的设计要求和实际工况数据,进行列管式换热器的设计计算。
包括换热面积的计算、传热系数的估算、管束的选择等。
学生可以借助计算机软件进行设计计算,加深对设计原理和方法的理解。
3.优化分析学生在设计计算的基础上,进行列管式换热器的优化分析。
通过调整设计参数,寻求更优的设计方案。
优化目标可以包括换热效率、压降、材料成本等。
学生需要运用数学方法和工程经验,进行综合评价和决策。
4.报告撰写学生根据设计计算和优化分析的结果,撰写课程设计报告书。
报告需要包括设计计算的过程和结果、优化分析的方法和结果、结论和建议等。
同时,学生还需要附上设计过程中的数据、图表和计算公式,以便他人理解和复现设计过程。
三、评价方法和标准1.设计计算和优化分析的准确性和合理性;2.报告书的内容完整、结构合理、文字准确、图表清晰;3.学生对设计中关键问题的分析和讨论;4.学生对设计过程的理解程度和设计思路的合理性。
化工原理课程设计列管式换热器
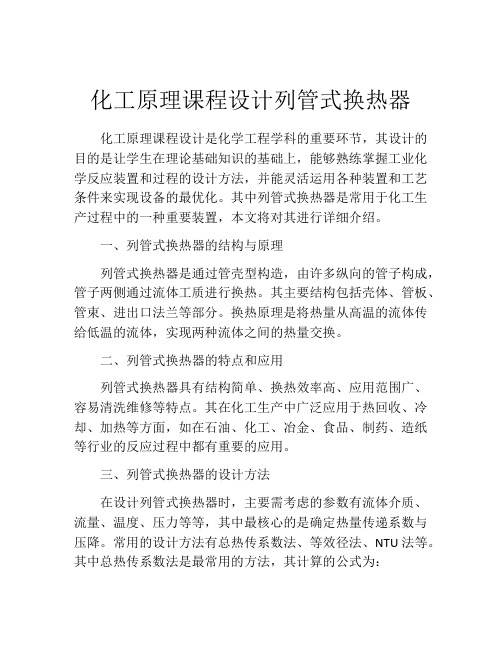
化工原理课程设计列管式换热器化工原理课程设计是化学工程学科的重要环节,其设计的目的是让学生在理论基础知识的基础上,能够熟练掌握工业化学反应装置和过程的设计方法,并能灵活运用各种装置和工艺条件来实现设备的最优化。
其中列管式换热器是常用于化工生产过程中的一种重要装置,本文将对其进行详细介绍。
一、列管式换热器的结构与原理列管式换热器是通过管壳型构造,由许多纵向的管子构成,管子两侧通过流体工质进行换热。
其主要结构包括壳体、管板、管束、进出口法兰等部分。
换热原理是将热量从高温的流体传给低温的流体,实现两种流体之间的热量交换。
二、列管式换热器的特点和应用列管式换热器具有结构简单、换热效率高、应用范围广、容易清洗维修等特点。
其在化工生产中广泛应用于热回收、冷却、加热等方面,如在石油、化工、冶金、食品、制药、造纸等行业的反应过程中都有重要的应用。
三、列管式换热器的设计方法在设计列管式换热器时,主要需考虑的参数有流体介质、流量、温度、压力等等,其中最核心的是确定热量传递系数与压降。
常用的设计方法有总热传系数法、等效径法、NTU法等。
其中总热传系数法是最常用的方法,其计算的公式为:1/U = 1/hi + Δx/k + Δy/ho其中U为总热传系数,hi、ho分别为热传分界面内的内、外热传系数,k为扩散系数(介质传热系数),Δx、Δy为介质的平均厚度与壁层厚度。
在设计时应根据具体情况选用合适的计算方法。
四、列管式换热器的操作和维护在使用列管式换热器时,应注意清洗维护工作。
由于该装置的结构特殊,应定期进行化学清洗,以避免沉积物和腐蚀物堵塞换热器内壁。
同时还应注意防止介质的过于浓缩,以免产生结晶、沉积、腐蚀等情况。
综上所述,列管式换热器是化工生产中不可缺少的一种装置,其结构特殊、应用范围广泛、换热效率高,并且容易维护操作,是值得研究和推广的一种装置。
在化工原理的课程设计中,学生能够通过对列管式换热器的深入理解和设计方案的完善,培养出创新思维和实际操作能力,为将来化工行业的发展奠定坚实的基础。
- 1、下载文档前请自行甄别文档内容的完整性,平台不提供额外的编辑、内容补充、找答案等附加服务。
- 2、"仅部分预览"的文档,不可在线预览部分如存在完整性等问题,可反馈申请退款(可完整预览的文档不适用该条件!)。
- 3、如文档侵犯您的权益,请联系客服反馈,我们会尽快为您处理(人工客服工作时间:9:00-18:30)。
——大学《化工原理》列管式换热器课程设计说明书学院:班级:学号:姓名:指导教师:时间:年月日目录一、化工原理课程设计任务书............................................................................ . (2)二、确定设计方案............................................................................ (3)1.选择换热器的类型2.管程安排三、确定物性数据............................................................................ (4)四、估算传热面积............................................................................ (5)1.热流量2.平均传热温差3.传热面积4.冷却水用量五、工艺结构尺寸............................................................................ (6)1.管径和管内流速2.管程数和传热管数3.传热温差校平均正及壳程数4.传热管排列和分程方法5.壳体内径 6.折流挡板 (7)7.其他附件8.接管六、换热器核算............................................................................ . (8)1.热流量核算2.壁温计算 (10)3.换热器内流体的流动阻力七、结构设计............................................................................ . (13)1.浮头管板及钩圈法兰结构设计2.管箱法兰和管箱侧壳体法兰设计3.管箱结构设计4.固定端管板结构设计 5.外头盖法兰、外头盖侧法兰设计 (14)6.外头盖结构设计7.垫片选择8.鞍座选用及安装位置确定9.折流板布置10.说明八、强度设计计算............................................................................ .. (15)1.筒体壁厚计算2.外头盖短节、封头厚度计算3.管箱短节、封头厚度计算 (16)4.管箱短节开孔补强校核 (17)5.壳体接管开孔补强校核 6.固定管板计算 (18)7.浮头管板及钩圈 (19)8.无折边球封头计算9.浮头法兰计算 (20)九、参考文献............................................................................ .. (20)一、化工原理课程设计任务书某生产过程的流程如图3-20所示。
反应器的混合气体经与进料物流换热后,用循环冷却水将其从110℃进一步冷却至60℃之后,进入吸收塔吸收其中的可溶性组分。
已知混合气体的流量为231801kg h,压力为6.9MPa,循环冷却水的压力为0.4MPa,循环水的入口温度为29℃,出口的温度为39℃,试设计一列管式换热器,完成生产任务。
已知:混合气体在85℃下的有关物性数据如下(来自生产中的实测值) 密度 3190kg m ρ= 定压比热容1 3.297p c kj kg =℃ 热导率10.0279w m λ=℃ 粘度51 1.510Pa s μ-=⨯循环水在34℃下的物性数据: 密度 31994.3kg m ρ= 定压比热容1 4.174p c kj kg =K 热导率10.624w m λ=K 粘度310.74210Pa s μ-=⨯二、确定设计方案1. 选择换热器的类型两流体温的变化情况:热流体进口温度110℃ 出口温度60℃;冷流体进口温度29℃,出口温度为39℃,该换热器用循环冷却水冷却,冬季操作时,其进口温度会降低,考虑到这一因素,估计该换热器的管壁温度和壳体温度之差较大,因此初步确定选用浮头式换热器。
2. 管程安排从两物流的操作压力看,应使混合气体走管程,循环冷却水走壳程。
但由于循环冷却水较易结垢,若其流速太低,将会加快污垢增长速度,使换热器的热流量下降,所以从总体考虑,应使循环水走管程,混和气体走壳程。
三、确定物性数据定性温度:对于一般气体和水等低黏度流体,其定性温度可取流体进出口温度的平均值。
故壳程混和气体的定性温度为T=260110+ =85℃ 管程流体的定性温度为t=3422939=+℃根据定性温度,分别查取壳程和管程流体的有关物性数据。
对混合气体来说,最可靠的无形数据是实测值。
若不具备此条件,则应分别查取混合无辜组分的有关物性数据,然后按照相应的加和方法求出混和气体的物性数据。
混和气体在85℃下的有关物性数据如下(来自生产中的实测值): 密度 31/90m kg =ρ定压比热容 1p c =3.297kj/kg •℃热导率 1λ=0.0279w/m •℃粘度 1μ=1.5×10-5Pa •s循环水在34℃ 下的物性数据:密度 1ρ=994.3㎏/m 3定压比热容 1p c =4.174kj/kg •K热导率1λ=0.624w/m •K粘度 1μ=0.742×10-3Pa •s四、估算传热面积1.热流量Q 1=111t c m p ∆=231801× 3.297×(110-60)=3.82×107kj/h=10614.554kw2.平均传热温差先按照纯逆流计算,得 m t ∆=K3.48296039110ln)2960()39110(=-----3.传热面积由于壳程气体的压力较高,故可选取较大的K 值。
假设K=320W/(㎡k)则估算的传热面积为Ap=2176.6863.4832010614554m t K Q m =⨯=∆4.冷却水用量 m =ipi t c Q ∆1=h kg s kg /2.915486/3.2541010174.4106145543==⨯⨯五、工艺结构尺寸1.管径和管内流速 选用Φ25×2.5较高级冷拔传热管(碳钢),取管内流速u 1=1.3m/s 。
2.管程数和传热管数 可依据传热管内径和流速确定单程传热管数 Ns=6273.102.0785.0)3.9943600/(2.915486422≈⨯⨯⨯=ud Vi π按单程管计算,所需的传热管长度为 L=m n d A so p14627025.014.376.686≈⨯⨯=π按单程管设计,传热管过长,宜采用多管程结构。
根据本设计实际情况,采用非标设计,现取传热管长l=7m ,则该换热器的管程数为 Np=2714==l L 传热管总根数 Nt=627×2=12543.传热温差校平均正及壳程数 平均温差校正系数: R=5293960110t t T -T 1221=--=-P=124.0291102939t T t t 1112=--=--按单壳程,双管程结构,查【化学工业出版社《化工原理》(第三版)上册】:图5-19得:96.0=∆t ε平均传热温差46.448.30.96=⨯=∆=∆∆塑m t mt tεK由于平均传热温差校正系数大于0.8,同时壳程流体流量较大,故取单壳程合适。
4.传热管排列和分程方法采用组合排列法,即每程内均按正三角形排列,隔板两侧采用正方形排列。
见【化学工业出版社《化工原理》(第三版)上册】:图6-13。
取管心距t=1.25d 0,则 t=1.25×25=31.25≈32㎜隔板中心到离其最.近一排管中心距离: S=t/2+6=32/2+6=22㎜ 各程相邻管的管心距为44㎜。
管数的分程方法,每程各有传热管627根,其前后管程中隔板设置和介质的流通顺序按【化学工业出版社《化工原理》(第三版)上册】:图6-8选取。
5.壳体内径 采用多管程结构,进行壳体内径估算。
取管板利用率η=0.75 ,则壳体内径 为:D=1.05tmm N T 137457.0/12543205.1/=⨯=η按卷制壳体的进级档,可取D=1400mm筒体直径校核计算:壳体的内径i D 应等于或大于(在浮头式换热器中)管板的直径,所以管板直径 的计算可以决定壳体的内径,其表达式为:e 21n t D c i +-=)( 管子按正三角形排列:3912541.1N 1.1n t c =⨯==取e=1.20d =1.2⨯25=30mm∴i D =32 ⨯(39-1)+2 ⨯30 =1276mm 按壳体直径标准系列尺寸进行圆整:i D =1400mm6.折流挡板 采用圆缺形折流挡板,去折流板圆缺高度为壳体内径的25%,则切去的圆缺高度为h=0.25×1400=350m ,故可取h=350mm取折流板间距B=0.3D ,则 B=0.3×1400=420mm ,可取B 为450mm 。
折流板数目1414.5145070001N B ≈=-=-=折流板间距传热管长折流板圆缺面水平装配,见图:【化学工业出版社《化工原理》(第三版)上册】:图6-9。
7.其他附件拉杆数量与直径选取,本换热器壳体内径为1400mm ,故其拉杆直径为Ф16拉杆数量8,其中长度5950mm 的六根,5500mm 的两根。
壳程入口处,应设置防冲挡板。
8.接管壳程流体进出口接管:取接管内气体流速为u 1=10m/s ,则接管内径为302.01014.3)903600/(23180144VD 1=⨯⨯⨯==πμ圆整后可取管内径为300mm 。
管程流体进出口接管:取接管内液体流速u 2=2.5m/s ,则接管内径为361.05.214.3)3.9943600/(2.91548642=⨯⨯⨯=D圆整后去管内径为360mm六、换热器核算1. 热流量核算(1)壳程表面传热系数 用克恩法计算,见式【化学工业出版社《化工原理》(第三版) 上册】:式(5-72a ): 14.03155.0010)(Pr Re 36.0wed μμλα= 当量直径,依【化学工业出版社《化工原理》(第三版)上册】:式(5-73a )得e d =m d d t oo 02.0]423[422=-ππ 壳程流通截面积:1378.0)32251(1400450)1(S =-⨯=-=t d BD o o 壳程流体流速及其雷诺数分别为s m u o /2.51378.0)903600/(231801=⨯=624000105.1902.502.0u d Re 50e =⨯⨯⨯==-1μρo普朗特数773.10279.0105.110297.3c Pr 53p -⨯⨯⨯==λμ粘度校正1)(14.0≈wμμK m w o ⋅=⨯⨯⨯=23155.0/7.935773.162400002.00279.036.0α(2)管内表面传热系数: 4.08.0Pr Re 023.0iii d λα=管程流体流通截面积:1969.02125402.0785.02=⨯⨯=i S 管程流体流速:s m u i /3.11969.0)3.9943600/(2.915486=⨯=雷诺数: 34841)10742.0/(3.9943.102.0Re 3≈⨯⨯⨯=-普朗特数:96.4624.010742.010174.4Pr 33=⨯⨯⨯=K /585896.43484102.0624.0023.024.08.0⋅=⨯⨯⨯=m w i α(3)污垢热阻和管壁热阻:【化学工业出版社《化工原理》(第三版)上册】:表5-5取: 管外侧污垢热阻 w k m R o /0004.02⋅= 管内侧污垢热阻w k m R i /0006.02⋅=管壁热阻按【化学工业出版社《化工原理》(第三版)上册】:图5-4查得碳钢在该条 件下的热导率为50w/(m ·K)。