管道对接焊接接头射线检测标准比较分析
国内外长输管道对接焊缝射线检测验收标准比较研究

国内外长输管道对接焊缝射线检测验收标准比较研究摘要:管道输送具有经济、安全和不间断的优势,管道建设是一项大规模的焊接工程。
本文介绍了油气长输管线焊接检测标准分析,通过基于国内外标准的长输管道焊接检测差异分析,提出了较适合国内管线焊缝检测要求及方法,并对油气长输管线及城镇燃气管线焊缝检测质量标准进行了对比分析,得出城镇燃气管线焊缝质量要求要高于油气长输管线的质量要求。
关键词:管道;焊接;检测;标准分析;差异分析引言管道是油气长距离运输的最佳方式,随着石油、天然气生产和消费速度的增长,管道建设速度不断加快。
目前,我国油气长输管道长度早已突破10万km,城市燃气管线也早已突破数万公里。
在管道建设过程中,由于管道敷设完全依靠焊接工艺来完成,所以焊接质量在很大程度上决定了工程质量。
因此,为保证工程质量,有必要对焊接的质量加以严格控制。
钢管焊接无损检验就是保证焊接质量最好的一道工序。
目前,针对钢管对接焊缝的检测要求的标准较多,但针对油气长输和城镇燃气管线的焊缝检测存在一定的差异。
为此,本文主要分析了油气长输和城镇燃气管线的焊缝检测的差异,以更有效的推动输气管线和城镇燃气管线的建设。
1 油气长输管线焊接检测标准分析目前,国内外关于油气管道工程中油气长输管线焊接检测的要求不统一。
国内的标准主要是GB50251-2015《输气管道工程设计规范》、GB50253-2014《输油管道工程设计规范》、GB50369-2014《油气长输管道工程施工及验收规范》、中石油三化标准CDP中的CDP-G-OGP-OP-085-2015-1《油气管道工程自动焊焊接技术规定》等。
国外的标准主要是ASMEB31.4《液态烃和其他液态管线输送系统》、ASMEB31.8《输气和配气管道系统》等。
1.1 基于国内标准的长输管道焊接检测要求分析输气管道设计规范GB50251-2015中明确规定:钢管焊接接头应在形状尺寸及外观目视检查合格后进行无损检测。
金属熔化焊对接接头射线检测技术和质量分级

金属熔化焊对接接头射线检测技术和质量分级金属熔化焊对接接头是常见的金属连接方式之一,在工业领域广泛应用。
为了保证接头的质量和安全性,射线检测技术成为了必不可少的检测手段之一。
本文将介绍金属熔化焊对接接头射线检测技术以及质量分级,并为读者提供一些实用的指导意见。
射线检测技术是一种先进的无损检测方法,可以通过透射或散射射线,对金属熔化焊对接接头进行全面的检测。
其原理是利用射线的穿透性和散射性能,通过对射线的影像或图像进行检测和分析,判断接头的质量状况。
常用的射线检测技术有X射线检测和γ射线检测。
X射线检测是通过产生和利用X射线来实现对接头的检测,而γ射线检测则是通过产生和利用γ射线来进行检测。
这两种方法都可以提供清晰的影像和图像,帮助检测人员发现接头中的缺陷和问题。
在金属熔化焊对接接头的射线检测中,通常会对接头的焊缝进行检测。
射线检测可以发现各种缺陷,如气孔、夹渣、裂纹等。
通过分析影像和图像,检测人员可以判断缺陷的位置、大小和形状,为后续的修复和措施提供依据。
对于金属熔化焊对接接头的质量分级,通常会根据检测结果和相关标准进行评估。
根据缺陷的类型、数量和大小等指标,可以将接头分为不同的质量等级。
一般来说,无缺陷的接头可以评为优质接头,而有少量缺陷但不影响使用的接头可以评为良好接头。
如果接头存在严重缺陷,可能会被评为不合格接头。
射线检测技术对金属熔化焊对接接头的检测具有重要意义。
通过准确评估接头的质量,可以确保接头的强度和稳定性,提高接头的使用寿命和安全性。
因此,在进行金属熔化焊对接接头时,应当重视射线检测技术,并且按照相关标准进行质量分级,以保证接头的质量和安全性。
综上所述,金属熔化焊对接接头射线检测技术和质量分级对于保证接头的质量和安全性至关重要。
射线检测技术可以提供全面准确的检测信息,帮助检测人员发现接头中的缺陷和问题。
通过质量分级,可以对接头进行合理评估,并采取相应的修复和措施。
在实际应用中,需要充分认识射线检测技术的重要性,并按照相关标准进行质量分级,以确保金属熔化焊对接接头的质量和安全性。
小径管对接环焊缝射线检测标准的比较
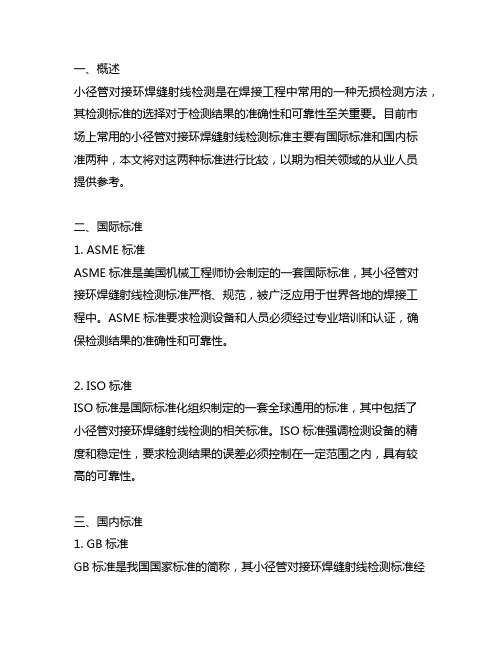
一、概述小径管对接环焊缝射线检测是在焊接工程中常用的一种无损检测方法,其检测标准的选择对于检测结果的准确性和可靠性至关重要。
目前市场上常用的小径管对接环焊缝射线检测标准主要有国际标准和国内标准两种,本文将对这两种标准进行比较,以期为相关领域的从业人员提供参考。
二、国际标准1. ASME标准ASME标准是美国机械工程师协会制定的一套国际标准,其小径管对接环焊缝射线检测标准严格、规范,被广泛应用于世界各地的焊接工程中。
ASME标准要求检测设备和人员必须经过专业培训和认证,确保检测结果的准确性和可靠性。
2. ISO标准ISO标准是国际标准化组织制定的一套全球通用的标准,其中包括了小径管对接环焊缝射线检测的相关标准。
ISO标准强调检测设备的精度和稳定性,要求检测结果的误差必须控制在一定范围之内,具有较高的可靠性。
三、国内标准1. GB标准GB标准是我国国家标准的简称,其小径管对接环焊缝射线检测标准经过多年的实践检验和技术积累,在国内焊接工程领域有着广泛的应用。
GB标准强调了对检测设备和人员的要求,同时结合了国内工程实际情况制定了一些特定的检测方法和要求。
2. JB标准JB标准是我国机械工程行业标准的一种,小径管对接环焊缝射线检测的相关标准内容在其中得到了详细规定。
JB标准注重了对检测设备的性能要求和对检测结果的评定标准,其制定和修订均按照国家相关法规要求进行,具有较高的权威性。
四、比较分析1. 标准适用范围国际标准适用范围广泛,可满足全球各地的焊接工程需求,具有较高的通用性。
而国内标准多数针对国内具体情况进行了调整和修订,更适用于国内的工程项目。
2. 技术要求国际标准注重了检测设备和人员的专业化程度,对于技术要求较高,需要相应的专业培训和认证。
而国内标准更加强调了对检测设备性能和结果评定标准的要求,对于技术人员的要求相对较低。
3. 检测结果可靠性由于国际标准对于检测设备和人员的要求较高,因此其检测结果具有较高的可靠性和准确性。
金属熔化焊对接接头射线检测技术和质量分级
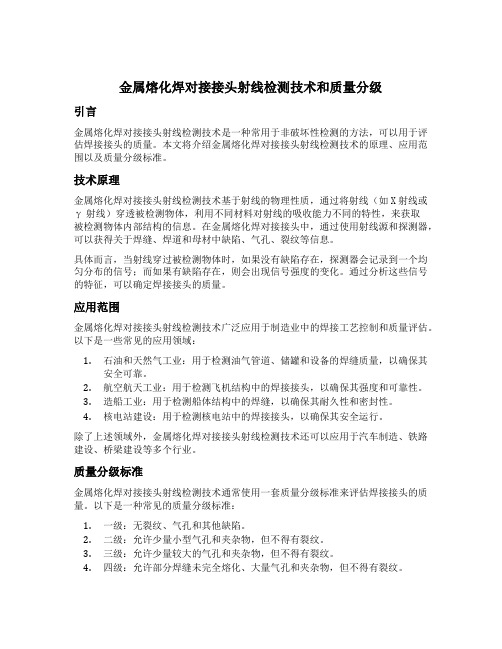
金属熔化焊对接接头射线检测技术和质量分级引言金属熔化焊对接接头射线检测技术是一种常用于非破坏性检测的方法,可以用于评估焊接接头的质量。
本文将介绍金属熔化焊对接接头射线检测技术的原理、应用范围以及质量分级标准。
技术原理金属熔化焊对接接头射线检测技术基于射线的物理性质,通过将射线(如X射线或γ射线)穿透被检测物体,利用不同材料对射线的吸收能力不同的特性,来获取被检测物体内部结构的信息。
在金属熔化焊对接接头中,通过使用射线源和探测器,可以获得关于焊缝、焊道和母材中缺陷、气孔、裂纹等信息。
具体而言,当射线穿过被检测物体时,如果没有缺陷存在,探测器会记录到一个均匀分布的信号;而如果有缺陷存在,则会出现信号强度的变化。
通过分析这些信号的特征,可以确定焊接接头的质量。
应用范围金属熔化焊对接接头射线检测技术广泛应用于制造业中的焊接工艺控制和质量评估。
以下是一些常见的应用领域:1.石油和天然气工业:用于检测油气管道、储罐和设备的焊缝质量,以确保其安全可靠。
2.航空航天工业:用于检测飞机结构中的焊接接头,以确保其强度和可靠性。
3.造船工业:用于检测船体结构中的焊缝,以确保其耐久性和密封性。
4.核电站建设:用于检测核电站中的焊接接头,以确保其安全运行。
除了上述领域外,金属熔化焊对接接头射线检测技术还可以应用于汽车制造、铁路建设、桥梁建设等多个行业。
质量分级标准金属熔化焊对接接头射线检测技术通常使用一套质量分级标准来评估焊接接头的质量。
以下是一种常见的质量分级标准:1.一级:无裂纹、气孔和其他缺陷。
2.二级:允许少量小型气孔和夹杂物,但不得有裂纹。
3.三级:允许少量较大的气孔和夹杂物,但不得有裂纹。
4.四级:允许部分焊缝未完全熔化、大量气孔和夹杂物,但不得有裂纹。
需要注意的是,具体的质量分级标准可能因不同行业和国家而有所差异,上述标准仅作为参考。
结论金属熔化焊对接接头射线检测技术是一种重要的非破坏性检测方法,可以用于评估焊接接头的质量。
DLT 5069-96 钢制承压管道对接焊接接头射线检验篇
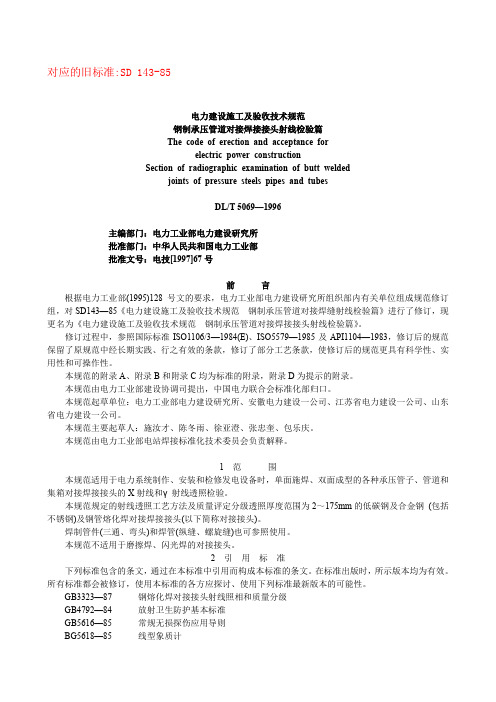
对应的旧标准:SD 143-85电力建设施工及验收技术规范钢制承压管道对接焊接接头射线检验篇The code of erection and acceptance forelectric power constructionSection of radiographic examination of butt weldedjoints of pressure steels pipes and tubesDL/T 5069—1996主编部门:电力工业部电力建设研究所批准部门:中华人民共和国电力工业部批准文号:电技[1997]67号前言根据电力工业部(1995)128号文的要求,电力工业部电力建设研究所组织部内有关单位组成规范修订组,对SD143—85《电力建设施工及验收技术规范钢制承压管道对接焊缝射线检验篇》进行了修订,现更名为《电力建设施工及验收技术规范钢制承压管道对接焊接接头射线检验篇》。
修订过程中,参照国际标准ISO1106/3—1984(E)、ISO5579—1985及API1104—1983,修订后的规范保留了原规范中经长期实践、行之有效的条款,修订了部分工艺条款,使修订后的规范更具有科学性、实用性和可操作性。
本规范的附录A、附录B和附录C均为标准的附录,附录D为提示的附录。
本规范由电力工业部建设协调司提出,中国电力联合会标准化部归口。
本规范起草单位:电力工业部电力建设研究所、安徽电力建设一公司、江苏省电力建设一公司、山东省电力建设一公司。
本规范主要起草人:施汝才、陈冬雨、徐亚澄、张忠奎、包乐庆。
本规范由电力工业部电站焊接标准化技术委员会负责解释。
1范围本规范适用于电力系统制作、安装和检修发电设备时,单面施焊、双面成型的各种承压管子、管道和集箱对接焊接接头的X射线和γ射线透照检验。
本规范规定的射线透照工艺方法及质量评定分级透照厚度范围为2~175mm的低碳钢及合金钢(包括不锈钢)及钢管熔化焊对接焊接接头(以下简称对接接头)。
钢制承压管道对接焊接接头射线检验技术规程 概述说明
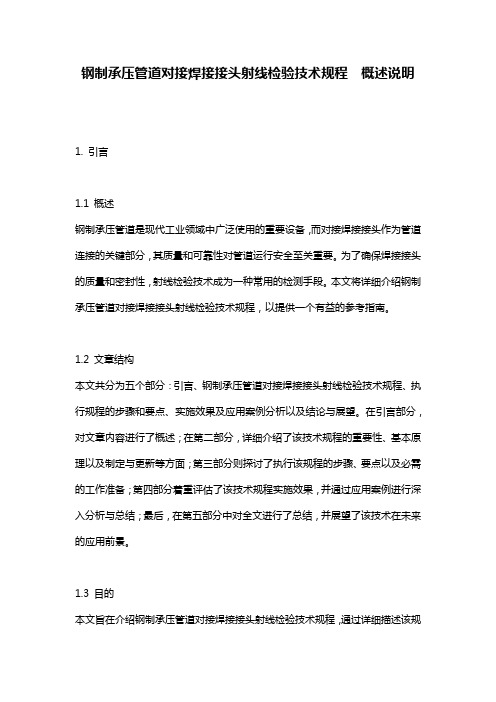
钢制承压管道对接焊接接头射线检验技术规程概述说明1. 引言1.1 概述钢制承压管道是现代工业领域中广泛使用的重要设备,而对接焊接接头作为管道连接的关键部分,其质量和可靠性对管道运行安全至关重要。
为了确保焊接接头的质量和密封性,射线检验技术成为一种常用的检测手段。
本文将详细介绍钢制承压管道对接焊接接头射线检验技术规程,以提供一个有益的参考指南。
1.2 文章结构本文共分为五个部分:引言、钢制承压管道对接焊接接头射线检验技术规程、执行规程的步骤和要点、实施效果及应用案例分析以及结论与展望。
在引言部分,对文章内容进行了概述;在第二部分,详细介绍了该技术规程的重要性、基本原理以及制定与更新等方面;第三部分则探讨了执行该规程的步骤、要点以及必需的工作准备;第四部分着重评估了该技术规程实施效果,并通过应用案例进行深入分析与总结;最后,在第五部分中对全文进行了总结,并展望了该技术在未来的应用前景。
1.3 目的本文旨在介绍钢制承压管道对接焊接接头射线检验技术规程,通过详细描述该规程的重要性、基本原理和实施步骤,帮助读者全面了解和掌握该技术。
同时,通过应用案例的分析与总结,评估该技术规程的实施效果与优劣,并指出其发展方向与挑战。
本文的目标是为相关专业人员提供一个系统化、参考性强的指南,以促进钢制承压管道对接焊接接头射线检验技术水平的不断提高。
2. 钢制承压管道对接焊接接头射线检验技术规程2.1 焊接接头射线检验的重要性钢制承压管道的对接焊接接头是关键部位,其质量直接影响到管道的安全运行。
不合格的焊缝可能导致泄漏或破裂,从而造成严重的事故和损失。
因此,通过射线检验来评估和验证焊缝的质量是至关重要的。
2.2 承压管道射线检验的基本原理承压管道射线检验主要采用X射线或γ射线照相术。
这种方法能够透过金属材料,形成可见影像,以评估材料内部存在的潜在缺陷,如气孔、裂纹、夹杂物等。
通过分析影像中缺陷的特征和大小,可以判断焊缝是否符合规范要求,并采取相应措施进行修补或更换。
不等厚对接管道焊缝射线检测技术总结

不等厚对接管道焊缝射线检测技术总结本文通过对福清核电站一期中GPV系统不等厚对接管道焊接接头的射线照相检测,试验证明,选用合适的透照工艺以及使用双胶片法可使射线照相得到较高的对比灵敏度、合适的黑度等,满足了工程及相关技术标准的要求。
标签:射线检测;双胶片法;GPV系统;不等厚对接管道1 透照工艺试验研究针对以上分析,提高射线照相的对比度和保证黑度是不等厚管道焊缝透照工艺的关键。
认真分析影响射线照相灵敏度和缺陷检出率的各种因素,并排除选择余地少或对射线照相灵敏度影响小的因素,选择以下几个因素进行透照工艺的试验研究。
根据现场的实际情况,不等厚管道射线检测可以采取三种方法:双胶片法、放射源偏心法和高电压法。
1.1 放射源不等厚管道的规格626×33/614×25mm余高为2mm,部分不等厚管道留了射线曝光孔,因此透照方式可以采用选择单壁内透和双壁单影两种方法。
为保证射线照相的对比度、清晰度和颗粒度,直接关系到射线照相的灵敏度,为提高射线照相的灵敏度,根据DL821-2002的要求对于透照厚度差较大的工件,当透照厚度(TA)大于或等于10mm时,采用适宜的γ射线源透照,可获得较大的检测范围,所以放射源选用Ir92,焦点尺寸尽量小。
X射线机选择上方公司的型号为3505。
1.2 底片黑度DL821-2002标准规定X射线底片黑度为 1.5-3.5,γ射线的底片黑度为1.8-3.5。
由于不等厚管道管径不同,存在厚度差,导致底片一半黑一半白,底片黑度无法满足要求,采用了双胶片法、放射源偏心法及高电压法,使底片黑度达到要求。
1.3 像质计的选择及放置图像质量必须能使规定直径的金属丝在底片上清楚的显示出来。
像质计的选择按照表1所示。
像质计应放在被检部位射线源侧,当无法在源侧放置像质计时,可放在胶片侧的工件表面上,此时应在像质计附近附加“F”铅示标记以示区别,像质计灵敏度应该提高一级或通过对比试验使底片的质量达到规定的要求。
工艺管道无损检测(x射线)

应根据每台X光机,胶片和增感屏制作曝光曲线,以此作为曝光规范。当焦距为700㎜时,曝光量应≥15mA·min,当焦距改变时可按平方反比定律对曝光量的推荐值进行换算。
2散射线的屏蔽
为防止散射线的影响应用厚度不小于2mm的铅板屏蔽背散;为检查背散射防护是否合格,应暗袋背面贴附一个“B”字标记。当底片上较黑背景上出现“B”字较淡影像时,说明背散射防护不够,应予重新透照。
6.1.3焊接工作结束后进行无损探伤工作,但具有裂纹倾向的材质,应在焊接完成24h以后才能进行探伤工作。。
6.2一般项目
6.2.1被检测焊缝及热影响区的表面质量(包括余高高度)应经外观检查合格,其表面不得存在:裂纹、气孔、弧坑、咬边和肉眼可见的夹渣等缺陷,焊接接头两侧的飞溅和熔渣,必须清除。
6.2.2底片的黑度应为2.0-4.0,像质计摆放正确,并能观察到标准规定的钢丝影像,标记齐全且不覆盖焊缝,在有效评定范围内不得有影响底片评定的划伤、水迹、脱膜、污斑等,否则应重新拍片。
6.2.3加强过程控制,严把质量关,不合格材料不准进入现场。检查不合格的工序,不得进行下工序,做到“上工序服务下工序,下工序监督上工序”,每道工序经检查人员认可后方可进行下工序,并做好质量记录,具有可追溯性,保证底片编号与单线图焊口编号、记录及报告一一对应。
7
7.1对于整理好的底片应存放在通风、干燥的地方。
7.2在探伤过程中注意被检测工件的保护、不得损坏。
8
8.1环境因素控制措施
8.1.1探伤操作产生的固体废弃物应分类投放到专用垃圾箱内。
8.1.2废显影、定影药液应稀释50倍后测定PH值,当PH值为6-9时,方可排放。
8.2危险源控制措施
8.2.1进入施工现场的探伤人员必须经过安全及射线防护知识的教育,使全体检测人员掌握射线设备操作方法、安全防护、辐射事故预防、事故处理有关安全规定。
- 1、下载文档前请自行甄别文档内容的完整性,平台不提供额外的编辑、内容补充、找答案等附加服务。
- 2、"仅部分预览"的文档,不可在线预览部分如存在完整性等问题,可反馈申请退款(可完整预览的文档不适用该条件!)。
- 3、如文档侵犯您的权益,请联系客服反馈,我们会尽快为您处理(人工客服工作时间:9:00-18:30)。
摘要JB/T 4730-2005《承压设备无损检测》和SY/T 4109-2005《石油天然气钢质管道无损检测》在无损检测行业中都有着广泛的应用,但两个标准有一定的差别,在具体应用中,应根据两个标准的各自特点进行综合考虑。
文章对两个标准射线部分的不同之处进行比较,目的是便于无损检测人员能更好地理解标准,更加准确地使用标准,从而保证无损检测工作质量和工程焊接质量。
一、前言
目前,石油、石化系统油田建设工程中的油气长输、集输管道对接焊缝射线检测所使用的检测标准为SY/T4109-2005《石油天然气钢质管道无损检测》的射线检测;而在用工业管道检验中所执行的无损检测标准为JB/T4730-2005《承压设备无损检测》第二部分射线检测。
由于两标准存在一定的差异,因此在油田集输管道的安装射线检测和在用工业管道定期检验中出现了缺陷质量评定结果不一致的矛盾。
如河南油田技术监测中心在复检原油外输站内一条新建管线时,共拍片26张,如用SY/T4109标准进行质量等级评定,则全部为Ⅲ级以上;而用JB/T4730标准进行质量等级评定,则有11张底片评为Ⅳ级,管道的安全状况等级也定为了Ⅲ级,造成了使用单位和安装单位对监测单位的一些误解。
二、两种标准主要差别的分析比较
(一)适用范围
SY/T4109标准适用于射线照相方法检查壁厚为2~50mm的低碳钢、低合金钢等金属材料的石油天然气长输、集输及其站场的管道环向对接接头的检测与质量分级,同时也明确了不适用于工业管道和公用管道的检测。
JB/T4730标准适用于壁厚大于或等于2mm的低碳钢、低合金钢、奥氐体不锈钢、镍及镍合金、铜及铜合金制承压设备管子及压力管道的熔化焊环向对接焊接接头射线检与质量分级,对管道的最大壁厚未作具体规定。
由此可见,JB4730标准的适用范围大于SY4109标准。
(二)射线检测技术等级JB4730标准根据对接焊件的制造、安装、在用时的检测条件,将射线检测技术分为A、AB、B三个级别;而SY4109标准无此方面的规定,其检测技术等级与JB4730中的AB级相当。
(三)透照布置
1.对于透照方式,按射线源、工件和胶片之间的相互位置,两标准都规定了可采用单壁单影透照、双壁单影透照和双壁双影透照三种方法;同时也规定了在实际可行的情况下优先采用单壁透照22的方式。
2.对于双壁双影透照的小径管,SY4109标准定义为外径小于等于89mm的钢管,而JB4730标准则定义为外径小于等于100mm的钢管。
对于透照次数JB4730标准规定
得更为详细准确一些,当同时满足T(壁厚)≤8mm和g≤D0/4的应采用椭圆成像的方式,不能满足上述条件的则应采用垂直透照重叠成像。
椭圆成像时当T/D0≤0.12时,相隔90°透照2次,当T/D0﹥0.12时相隔120°或60°透照3次;直透照重叠成像时,一般相隔120°或60°透照3次。
SY4109标准没有作出严格的规定,只要求椭圆成像时相隔90°透照2次,椭圆成像有团难时相隔120°透照3次。
3.对于管径在100mm﹤D0≤400mm范围内的钢管,一般都采用双壁单影的透照工艺。
JB4730标准规定在此情况下A级、AB级允许K值取1.2,透照次数可通过计算或查阅附录D得出,比较方便快捷。
SY4109标准规定当钢管公称直径D0≥250mm,其K值应取1.1,通过计算得出最少透照次数;当公称直径D0﹤250mm时,K值和一次透照长度可适当放宽,当射线源距钢管外表面大于15mm时,可分为不少于四段透照,且没有壁厚的限制,这是此标准的一个较大的漏洞。
如对∮108×8mm的钢管进行双壁单影透照时,按标准分4次透照就可以了,经计算此时K值为1.3;而对于∮377×8mm的钢管进行双壁单影透照却要进行5次透照。
(四)焊缝检测质量分级
1.缺陷类型和一般规定
JB4730标准将管道对接焊接接头中的缺陷按性质分为裂纹、未熔合、未焊透、条形缺陷、圆形缺陷、根部内凹和根部咬边共7类缺陷;SY4109标准在此7类缺陷的基础上多增一项“烧穿”这类根部缺陷。
两标准都规定了Ⅰ级焊缝内只允许存在圆形缺陷,其他都为不允许的。
最大的不同之处是:(1)JB4730标准中Ⅱ、Ⅲ级焊缝是不允许任何形式的未焊透存在;而
SY4109标准中Ⅱ、Ⅲ级焊缝中允许根部未熔合和夹层未熔合的存在。
(2)SY4109标准Ⅱ级焊缝不允许存在黑度大于或等于较薄侧母材黑度的烧穿,而JB4730对此未作规定。
2.圆形缺陷的分级
表1圆形缺陷分级对比表由表1可以看出:两标准对于圆形缺陷级别的划分有很大相似之处,特别是管道公称壁厚大于15 mm时是完全一致的。
但当管道公称壁厚在5mm<T≤10 mm时,就存在明显的差异,如ф114×6mm的管道,圆形缺陷为12点,使用SY/T4109标准评定为Ⅲ级,而用JB/T4730标准评定只能定为Ⅳ级,相比之下JB4730标准规定得更为严格。
这主要是因为石油天然气长输管道都为野外作业,施工条件受到各方面的影响,同时圆形缺陷危险程度不高,适当放宽评定尺度也不会影响长输管道的使用寿命。
3.条状缺陷的分级
由表2可以看出:SY/T4109标准是依据管道外径将条状缺陷质量分级划分为两个级别,同时规定了缺陷的最大宽度。
JB/T4730标准没有管径分类和缺陷最大宽度的规定,而是引入了条形缺陷评定区的概念,和圆形缺陷评定区一样,随着管道厚度的增加,评定区的宽度也随之增加。
相比之下JB/T4730标准对条形缺陷的规定要比SY/T4109标准严格许多。
如同样一条ф114×6mm的管道,焊缝中4mm、2mm两处条形缺陷,其间距为2mm,按
SY/T4109标准可评定为Ⅱ,而按JB/T4730标准只能评定为Ⅳ级。
4.未焊透的分级
对于未焊透缺陷JB/T4730标准只允许不加垫板单面焊时存在,对未焊透的深度要采用沟槽对比试块进行测量,并进行了相应的规定;SY/T4109标准则允许未焊透缺陷在任何组焊工艺中存在。
SY/T4109标准将未焊透分为中间未焊透、根部未焊透和由于错口而形成的单侧未焊透;评定时按单个未焊透长度、在焊缝任何连续300mm长度内未焊透累计长度以及小口径管未焊透总长度三个方面进行定级,并对焊透的最大允许尺寸进行了规定。
JB4730标准对未焊透的成形原因未作出规定,评定时按其未焊透最大深度、单个缺陷长度、断续缺陷总长度及小口径管未焊透总长度四个方面进行定级,未规定未焊透的最大允许尺寸。
5.其他缺陷的评定
JB/T 4730标准对根部内凹和根部咬边的评定标准是一样的;而SY/T4109标准则是制定了不同的评定标准,对根部咬边的要求要更加严格一些。
相比之下SY/T4109标准对内凹的评定较JB/T 4730标准宽松,并且规定内凹影像的黑度小于或等于相邻较薄侧母材黑度时不计长度,可评定为Ⅰ级。
JB/T4730标准Ⅱ、Ⅲ级焊缝中不允许存在任何形式的未熔合;SY/T4109标准将坡口未熔合和层间未熔合定义为夹层未熔合,增加了表面未熔合的概念,即将熔焊金属与母材之间未能完全熔化结合且延续到表面的情况定义为表面未熔合。
处于外表面的定义为外表面未熔合,处于根部内表面的定义为根部未熔合。
Ⅱ、Ⅲ级焊缝中允许存在夹层未熔合和根部未熔合。
烧穿对焊缝质量影响较大,易引起泄漏。
一般焊接中较少见,但下向焊工艺焊速较快,易出现此类缺陷。
因此,SY/T4109标准对烧穿缺陷的深度和长度进行了规定;
JB/T4730标准并无此方面的规定。
三、结语
我国目前的工业管道设计、安装施工标准很多,不同的设计安装标准对无损检测标准的要求也不相同;不像压力容器制造统一执行GB150《钢制压力容器》标准和《压力容器安全监察规程》,无损检测执行JB/T4730《压力容器无损检测》标准;因此容易造成在用检验与安装验收检验在质量等级评定上的差异。
所以,各检验单位也应根据具体情况,灵活地运用各种标准,这样才能更好地保证在用压力管道的检验质量。