催化裂化装置反应再生单元停工操作法
催化裂化装置产品精制碱渣处理烟气中和单元停工操作法

催化裂化装置产品精制碱渣处理烟气中和单元停工操作法一、轻燃油精制部分1.系统退碱液V26101、 V26102、R26101AB、T26101碱液汇总后去V26106,V26106碱渣通过P26102去槽车出装。
2.系统水顶油精制系统水顶油:轻燃油精制系统水顶油和吸收稳定系统水顶油同时进行,走正常流程出装置T22304底→MI26101→精制系统→出装,V26102反复抽空三次以上。
3.在轻燃油线水顶时,碱液系统接受水洗,碱液系统中水集于V26106统一排放。
4.水洗顶油结束,打开各塔、罐排污阀放水,放完后关排污阀。
注意:在水顶油过程中,T22302、T22304、V26102要反复抽空3~4次,系统中残留轻燃油才能较彻底清除。
吸收稳定和轻燃油精制系统水顶结束后,关进出该系统的界区阀,8字盲板倒向。
5.系统内各塔罐底部通入蒸汽进行蒸煮,开各塔罐顶部放空。
二、液化气干气脱硫单元1.干气由T22303来→管线P26201→管线P26207→燃料气管网→火炬跨过V26202、T26202。
2.液化气由正常流程从精制系统送至罐区。
3.干气、液化气与胺液系统分离,胺液系统循环再生。
4.停进料后,尽量保证T26201、T26202压力,配和溶剂继续循环再生8小时,直至分析合格为止。
5.溶剂停止再生后,联系溶剂再生岗位以30℃/h 逐渐降低温度,用溶剂三塔循环量控制降温速度。
6.当溶剂再生系统具备退溶剂条件时,将T26201、T26202中胺液退至再生系统,退溶剂时,胺液在现场玻璃板液面计留50%可视液位,严防干气、液化气入溶剂再生系统。
7.由稳定单元给水,液化气脱硫醇系统开始水顶液化气。
8.液化气 干气脱硫单元水运P26201给水T26201溶剂再生系统T26202LV22514FV22508LV22512FV22506水运结束后就地排放。
三、液化气脱硫醇单元1. 液化气脱硫醇系统退碱液V26301、V26303、T26301、T26303碱液汇总后去V26106,V26106碱渣通过P26102去槽车出装。
催化裂化装置气分单元停工操作法

催化裂化装置气分单元停工操作法一、气分装置停车操作1.停车前各塔罐液位逐渐降低至20%左右。
2.接到停车指令后,切断进料,关闭V24001进料调节阀和手阀。
3.注意观察V24001罐液面,当P24001抽空V24001罐无物料时,停P24001。
4.T24001切断进料后,逐渐减少T24001回流量,减小E24002加热蒸汽量,当V24002罐无物料时,切出E24003。
停T24001回流泵P24002和T24002进料泵P24003,T24001底物料自压去中间罐区,压空后关闭塔底抽出阀,逐步减少塔底重沸器加热蒸汽量,缓慢降温,最后全关蒸气调节阀FV24153。
5.T24002停止进料后,逐渐减少T24002回流量,减小E24004加热蒸汽量,当回流罐V24003无物料后,停回流泵P24004,切出E24005,维持T24002塔压力,待T24002底物料压空后,停止向T24003A进料,关塔底抽出阀,逐步减少塔底重沸器加热蒸汽量,缓慢降温,最后全关FV24157。
6.停T24003A进料时,逐渐减少T24003A塔底取热量,维持T24003B塔底返回量,丙烯产品走不合格线出装置,逐渐减少T24003B顶回流量,加大出装量,同时注意T24003B 底液面,减少内回流量。
7.T24003A/B塔物料全部由丙烷不合格线出装。
8.当V24004无物料时,停回流泵P24006和丙烯产品泵P24007;T24003B底液位空时,停精丙烯塔中间泵P24005,T24003A塔底物料自压出装。
二、系统退料、泄压1.操作要点(1)改好残余物料出装流程。
(2)全装置共分3个系统:T24001塔系统、T24002塔系统、精丙烯塔系统。
各个系统必须隔开,严禁窜压。
(3)按压力由高到低的顺序,先后打开T24002、V24003、T24001、V24002、T24003A、T24003B、V24004底部停工抽出阀,启动P24009抽残料出装。
催化裂化装置吸收稳定单元停工操作法

催化裂化装置吸收稳定单元停工操作法一、吸收稳定单元退油当反应切断进料后,分馏岗位将V22203A、B中轻燃油抽空后,停T22304至T22301的补充吸收油,退油原则尽量将油赶至T22304,各抽出泵抽空后停泵,退油结束。
分馏一中扫线开始前T22304油退完。
轻油由T22301V22302T22302T22304精制单元出装置贫吸收油走付线不经T22303,直接返T22201A,T22303中油压回T22201A,现场注意T22303液位不要压空,严禁干气窜入T22201A。
稳定塔在再沸器出口温度变化不大的情况下,加大稳定轻燃油出装量,在保证塔顶温度不变的情况下尽量加大液化气外送量,V22303无液面时,停P22306AB。
二、吸收稳定单元水顶油1. 分馏未吹扫干净E22310管程,T22304严禁进水,防止突沸。
2. 不合格轻燃油出装置线:新鲜水P22202FV22218管线P22218/2管线P22222不合格轻罐油3. 新鲜水走正常流程进T22301:P22202给水FV22218T22301P22203给水FV222184. T22301一中、二中回流线:一中:二中:P22303LV22302E22303T22301 P22304LV22303E22304T223015. 凝缩油线:T22301P22302FV22302V22302P22301FV22306E22305T22302FV22305V22301注水P22309LV229016. 脱乙烷轻燃油线:T22302P22305FV22307E22307T223047. 稳定塔回流线:P22306给水FV22308T223048. T22301补充吸收剂线:P22307FV22301T22301T223049. 吸收稳定单元撇油。
吸收稳定单元改为三塔循环流程,2小时后,将T22301、V22302抽空,水全部集中在T22302、T22304中,两塔内水位要高,以撇油线在P22307入口见水为准。
催化裂化装置反应再生单元停工操作法

催化裂化装置反应再生单元停工操作法一、反应切断进料,停富气压缩机1. 首先将重油提升管酸性水、粗轻燃油、船燃油、以及轻燃油提升管急冷油、凝缩油、回炼液化气进料停止;同时将两个提升管预提升干气改为预提升蒸汽。
2. 重油提升管以10t/h的速度降低进料负荷,轻燃油提升管保持相同速率降低轻燃油进料,同时联系油品罐区降低原料油进装量,使V22201液位降至20%。
3. 缓慢关闭烟机入口蝶阀,待烟机入口碟阀全关后,全关烟机入口闸阀,再生压力由烟机旁路双动滑阀控制。
4. 反应进料降量要平稳,随着生焦量的减少,相应的减少主风量,控制烟气氧含量维持在3~5%,同时保证再生器出口温度≮650℃,温度低可喷燃烧油,控制反应温度在510℃左右。
5. 随着反应负荷降低,外取热器、油浆、塔底油及二中取热量会逐渐减少,因此要逐步提高开工锅炉的发汽量,保证系统蒸汽压力平稳。
6. 随着反应负荷降低,调整富气压缩机转速,逐步降低反应压力至80KPa;再生压力相应降至100KPa。
7. 当重油进料量降至60t/h时,首先关闭轻燃油提升管进料,再投重油提升管进料联锁,切断进料,原料油改走关原料油进料喷嘴切断回炼油回炼,。
V22202事故旁通线去手阀。
8. 反应切断进料,两器循环烧焦2小时后,再生器喷燃烧油维持系统温降速度小于30℃/h。
9. 反应切断进料后,富气压缩机反飞动阀全开,此时反应压力改由富气机入口大、小放火炬阀控制,此时应控制好两器压力平衡,避免压力波动过大。
10. 视低压蒸汽用量,关闭富气压缩机透平蒸汽,停富气压缩机。
关闭富气压缩机进出口气动闸阀,润滑油油运30分钟后停润滑油循环。
二、转、卸催化剂1. 反应切断进料,可启用再生器大型卸料线开始卸剂,控制卸料温度≯430℃,卸料过程应密切注意管线及催化剂罐受热情况。
2. 当提升管出口温度低于480℃,此时可进行转剂,应维持负压差(再生器压力100KPa,反应器压力120KPa),先关死两个再生滑阀(应现场手动摇死),将反应器内催化剂转入再生器。
140万吨重油催化裂化装置操作规程

目录第一章装置概况 (1)第一节装置简介 (1)第二节物料平衡及催化剂 (4)第三节主要工艺流程说明 (6)第四节主要设计条件及工艺计算汇总 (21)第五节消耗指标及能耗 (34)第六节装置设备规格表 (42)第七节机械规格表 (50)第八节安全阀规格表 (62)第九节装置仪表规格表 (63)第十节反再部分设备仪表管嘴明细表 (81)第十一节限流孔板表 (86)第十二节装置开工以来大的动改项目汇总 (88)第二章岗位操作法 (89)第一节反应――再生单元操作法 (89)第二节 CO焚烧炉-余热锅炉单元操作法 (131)第三节机组单元操作法 (169)第一部分三机组单元操作法 (169)第二部分备用风机操作法 (193)第三部分增压风机操作法 (202)第四部分气压机单元操作法 (209)第四节分馏单元操作法 (233)第五节吸收-稳定单元操作法 (253)第六节汽油脱臭单元操作法 (273)第七节脱硫单元操作法 (278)第八节特殊设备操作法 (291)第九节装置开停工步骤 (300)第十节装置生产运行大事记 (301)第三章装置安全常识 (307)第一节基本概念 (307)第二节基本常识 (310)第三节基本技能 (315)第四节有关规定、规章制度、标准 (317)第一章装置概况第一节装置简介一. 装置设计依据及规模中国石油化工股份有限公司济南分公司为原油一次加工能力500万吨/年的大型燃料-润滑-化工型石油加工企业。
鉴于分公司原油加工量逐年递增的实际情况,原有二次加工能力已不能满足生产发展的需要,增上本套140万吨/年重油催化裂化装置,对提高济南分公司原油加工深度及为下游化工装置提供原料将发挥重要作用。
本装置催化裂化部分由中国石化北京设计院设计,设计规模为140万吨/年,产品精制部分由济炼设计室设计,设计规模为干气10万吨/年、液化气20万吨/年、汽油70万吨/年,由中石化第二、第十建安公司建设安装。
催化裂化装置反应再生系统工艺流程
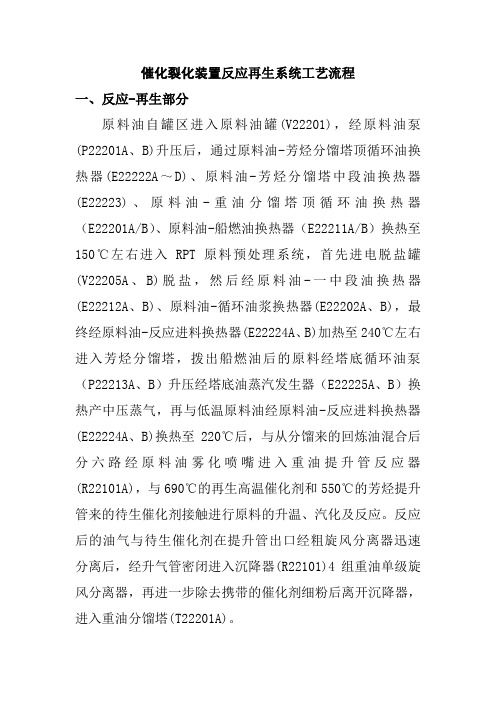
催化裂化装置反应再生系统工艺流程一、反应-再生部分原料油自罐区进入原料油罐(V22201),经原料油泵(P22201A、B)升压后,通过原料油-芳烃分馏塔顶循环油换热器(E22222A~D)、原料油-芳烃分馏塔中段油换热器(E22223)、原料油-重油分馏塔顶循环油换热器(E22201A/B)、原料油-船燃油换热器(E22211A/B)换热至150℃左右进入RPT原料预处理系统,首先进电脱盐罐(V22205A、B)脱盐,然后经原料油-一中段油换热器(E22212A、B)、原料油-循环油浆换热器(E22202A、B),最终经原料油-反应进料换热器(E22224A、B)加热至240℃左右进入芳烃分馏塔,拨出船燃油后的原料经塔底循环油泵(P22213A、B)升压经塔底油蒸汽发生器(E22225A、B)换热产中压蒸气,再与低温原料油经原料油-反应进料换热器(E22224A、B)换热至220℃后,与从分馏来的回炼油混合后分六路经原料油雾化喷嘴进入重油提升管反应器(R22101A),与690℃的再生高温催化剂和550℃的芳烃提升管来的待生催化剂接触进行原料的升温、汽化及反应。
反应后的油气与待生催化剂在提升管出口经粗旋风分离器迅速分离后,经升气管密闭进入沉降器(R22101)4组重油单级旋风分离器,再进一步除去携带的催化剂细粉后离开沉降器,进入重油分馏塔(T22201A)。
重油分馏塔分馏后的塔顶油气经冷凝冷却后进入油气分离器(V22203A),分离出的粗轻燃油分四路经雾化喷嘴进入芳烃提升管反应器(R22101B),与690℃催化剂接触进行原料的升温、汽化及反应。
反应后的油气与待生催化剂在提升管出口经粗旋风分离器迅速分离后,经升气管密闭进入沉降器内轻燃油单级旋风分离器,再进一步除去携带的催化剂细粉后离开沉降器,进入芳烃分馏塔(T22201B)。
油气分离出来的待生催化剂与重油部分的待生催化剂一起进入反应沉降器的汽提段。
重油催化裂化反应再生单元操作法
重油催化裂化反应再生单元操作法一、正常操作1.提升管出口温度(8TIC101)的控制反应温度对反应速度、产品分布和质量、再生烧焦率和设备结焦都有很大影响,它是日常生产中调节反应转化率和改变生产方案的最主要的调节参数之一。
提升管出口温度的设计值为510~538℃。
该温度的确定:1)用于改变生产方案:液化气方案(510~515℃)汽油方案(503~510℃)柴油方案(497~503℃)2)控制设备结焦:a.反应终了温度偏高,热裂化反应严重,热裂化缩合结焦--“硬焦”。
b.反应终了温度偏低,油气中重沸物冷凝、聚合结焦--“软焦”。
3) 降低再生烧焦率:减少非反应焦--可汽提炭,温度在汽提影响因素中起很大作用。
4) 对产品质量的影响:提高温度可以提高汽油辛烷值,但随着温度的升高汽油烯烃含量增加。
主要影响因素:1)催化剂循环量增加,反应温度上升。
2)原料油预热温度(8TIC201)上升,反应温度上升。
3)进料量及回炼比的变化。
4)进料性质改变影响反应转化率,反应温度变化。
5)原料带水,反应温度下降。
6)二再温度(8TI154)升高,反应温度上升。
7)反应沉降器压力(8PI108)升高,反应温度下降。
8)提升管注汽量的变化。
9)预提升介质及介质量的变化。
10)终止剂注入量增大,反应温度下降。
11)再生斜管流化不好,反应温度变化。
12)新鲜催化剂补充量的变化。
13)再生剂定炭高低的变化。
14)钝化剂是否加注及注入量多少的影响。
15)反应助剂是否加入及加入量多少的影响。
16)仪表或滑阀失灵。
调节方法:1)正常情况下,通过8TIC101调节再生滑阀开度改变催化剂循环量来自动控制提升管出口温度。
2)注入终止剂后,可视转化率和产品分布情况适当调整反应温度。
3)适当调整外取热器取热量,保证相对平稳的再生温度。
4)再生斜管流化不好时应尽快查明原因进行处理,以建立良好的催化剂循环量。
5)滑阀失灵引起自锁时(除跟踪失调外),应相对平稳各操作参数,尽量减少波动。
第三章催化裂化装置岗位操作法
第三章岗位操作法1. 反应岗位操作法1.1 任务、操作原则:根据原料油性质、催化剂性质、生产方案,选择合适的操作参数,控制好物料、热量、压力三大平衡,保持两器流化畅通,精心调节,发现问题及时联系处理,避免各类事故的发生。
使用分子筛催化剂,将重质原料油在提升管反应器内转化为干气、液化气、汽油、柴油、油浆和焦炭等,优化再生条件,提高烧焦强度,保持催化剂活性,控制合适的反应深度,精心调节,提高目的产品收率,降低能耗。
将反应后的油气送至分馏塔,再生烟气送至烟机余热锅炉。
在装置中,由于热平衡的制约,各操作变量相互关联,难以将某一操作变量孤立出来研究。
相反,在实验室试验装置中,靠电加热,催化裂解的操作变量能够独立于热平衡,使改变某一操作变量,维持其它变量恒定成为可能,并研究其对催化裂解的影响,其结果对工业装置有很大的指导性。
对催化裂解的关键操作变量分别讨论力图突出某一变量的影响,但因催化裂解各操作变量的相互关联性,难以将某一变量的影响和其它变量的影响严格区分开来,只有深刻理解其间的关联,才能深刻理解操作变量对催化裂解的影响。
(一)反应温度反应温度对反应速度和产品质量都有重大影响,催化裂解反应温度一般比蜡油催化裂化要高15--30℃。
1.据文献介绍,反应温度每提高10℃,反应速度提高10~20%。
2.•高反应温度可以提高液化气中烯烃产率(C3、C4)。
汽油辛烷值提高了,但产率下降。
3.•低反应温度又适逢大回炼比和低活性催化剂,可以显著提高轻油收率。
同时,柴油的十六烷值和汽油的诱导期升高,因油气中的烯烃随着裂解条件的缓和而减少。
4. 在大比例掺炼渣油时,如热量过剩,采用低反应温度有利于催化裂解装置维持热平衡,如热量不过剩,则可以提高掺炼比。
(二)反应压力反应压力是独立操作变量,但一般是不能任意改变的,须从装置的压力、设备及各部分情况来综合考虑。
反应压力的提高增加了反应物的浓度和反应时间,有利于提高反应速度和转化率。
催化裂化装置停工方案
加氢裂化装置正常停工一般程序和方法
加氢裂化装置正常停工一般程序和方法1.1停工前的准备1.1.1停工前先通知调度、原料、化验、仪表、电修、钳工等有关单位。
1.1.2停工时由于管线易凝,应彻底检查伴热是否开大畅通,确保装置内外管线不被蜡油凝堵。
1.1.3列出所有的盲板,并准备好盲板。
1.1.4氮气分析,必须保证氮气纯度>99.9%。
严防氮气置换时氧气进入系统,产生爆炸性气体。
1.1.5联系调度、原料,准备好停工常二线柴油约1000吨,经DAO线进装置。
1.1.6准备好碱Na2CO31000kg。
1.1.7停工过程中,要有意识的测试个紧急停车系统的正常。
1.2停工步骤(一)反应1.停DAO,反应降温降量,分馏产品改线1.1停DAO,处理管线逐步降低DAO的掺炼比例直至停DAO,调整好操作保证产品质量合格。
DAO管线先用冲洗油(本装置柴油)置换,再用蒸汽吹扫。
1.2反应降温降量1.2.1以15℃/h的降温速度,把R1002的入口温度降低20℃,增加R1002床层间的冷氢量,当R1002的所有床层温度比正常低20℃或更多时,降量至40t/h,每次降量5t,稳定1小时后再下一次降量。
降量过程中尽可能保证转化率不变。
若部分循环,降量同时逐渐降低循环油量直至停循环,若减压塔底油外放不及,则尾油部分改走减压侧线流程。
1.2.2当新鲜进料量降为正常值的一半后,在30分钟内降低R1001入口15℃。
用冷氢控制R1001催化剂床层出口温度相等。
R1002的出口温度比正常低15℃更多以后,在1小时内降低R1002所有催化剂床层入口温度25℃。
1.2.3 R1002中所有催化剂床层温度低于正常值45℃或更多时,逐渐中断新鲜进料和循环油,并继续氢气循环。
在中断进料后,尽快用循环氢把油自高压泵出口把进料线,炉管,换热器组的油冲洗入R1001。
注意:启用吹扫氢时,要缓慢进行。
1.2.4降温时,用TIC1114、TIC1147及使用床层急冷氢,降反应器入口温度的同时,相应地降低后几个床层温度,使各床层降温同步进行。
- 1、下载文档前请自行甄别文档内容的完整性,平台不提供额外的编辑、内容补充、找答案等附加服务。
- 2、"仅部分预览"的文档,不可在线预览部分如存在完整性等问题,可反馈申请退款(可完整预览的文档不适用该条件!)。
- 3、如文档侵犯您的权益,请联系客服反馈,我们会尽快为您处理(人工客服工作时间:9:00-18:30)。
催化裂化装置反应再生单元停工操作法
一、反应切断进料,停富气压缩机
1. 首先将重油提升管酸性水、粗轻燃油、船燃油、以及轻燃油提升管急冷油、凝缩油、回炼液化气进料停止;同时将两个提升管预提升干气改为预提升蒸汽。
2. 重油提升管以10t/h的速度降低进料负荷,轻燃油提升管保持相同速率降低轻燃油进料,同时联系油品罐区降低原料油进装量,使V22201液位降至20%。
3. 缓慢关闭烟机入口蝶阀,待烟机入口碟阀全关后,全关烟机入口闸阀,再生压力由烟机旁路双动滑阀控制。
4. 反应进料降量要平稳,随着生焦量的减少,相应的减少主风量,控制烟气氧含量维持在3~5%,同时保证再生器出口温度≮650℃,温度低可喷燃烧油,控制反应温度在510℃左右。
5. 随着反应负荷降低,外取热器、油浆、塔底油及二中取热量会逐渐减少,因此要逐步提高开工锅炉的发汽量,保证系统蒸汽压力平稳。
6. 随着反应负荷降低,调整富气压缩机转速,逐步降低反应压力至80KPa;再生压力相应降至100KPa。
7. 当重油进料量降至60t/h时,首先关闭轻燃油提升管进料,再投重油提升管进料联锁,切断进料,原料油改走关原
料油进料喷嘴切断回炼油回炼,。
V22202事故旁通线去
手阀。
8. 反应切断进料,两器循环烧焦2小时后,再生器喷燃烧油维持系统温降速度小于30℃/h。
9. 反应切断进料后,富气压缩机反飞动阀全开,此时反应压力改由富气机入口大、小放火炬阀控制,此时应控制好两器压力平衡,避免压力波动过大。
10. 视低压蒸汽用量,关闭富气压缩机透平蒸汽,停富气压缩机。
关闭富气压缩机进出口气动闸阀,润滑油油运30分钟后停润滑油循环。
二、转、卸催化剂
1. 反应切断进料,可启用再生器大型卸料线开始卸剂,控制卸料温度≯430℃,卸料过程应密切注意管线及催化剂罐受热情况。
2. 当提升管出口温度低于480℃,此时可进行转剂,应维持负压差(再生器压力100KPa,反应器压力120KPa),先关死两个再生滑阀(应现场手动摇死),将反应器内催化剂转入再生器。
待反应器藏量、密度回零,且沉降器汽提段压降、待生塞阀压降回零,说明反应器及待生立管催化剂卸净,此时,关闭待生塞阀(现场手动摇死),切断两器。
3. 反应沉降器加大蒸汽量尽快赶油气,当催化剂卸净后,关闭雾化、防焦蒸汽,保留预提升蒸汽和汽提蒸汽。
此
时分馏岗位方可停止油浆循环。
.
4. 催化剂全部转入再生器后,调整主风量,保证再生器的
藏量与密度,便于卸出催化剂。
5. 外取热器催化剂通过外取热器底部部卸料线卸出;重油
再生斜管和轻燃油再生斜管催化剂通过滑阀前卸料线卸出。
6. 待两器系统催化剂卸净,启用V22105底部卸料线,卸出三旋内催化剂。
三、装盲板SB22201/22205,两器吹扫,停主风机。
1. 再生器催化剂卸净后,将主风切出再生器,全开反
应器顶、盲板SB22201/22205前、提升管底部放空,停所有进反应器的蒸汽,与分馏岗位配合装盲板SB22201/22205。
2. 盲板SB22201/22205装好后,反应器给汽提蒸汽及
预提升蒸汽,吹扫12小时后,停所有蒸汽。
3. 再生器引入主风进行吹扫,全开烟机旁路双动滑阀,由烟囱直接放空,当再生器出口降至200℃,联系机组停主
风机。
4. 主风机停运后,关闭反-再系统所有工艺用反吹、松动风(汽),并关闭非净化风进两器总阀。
5. 联系检修单位开人孔、降温。
四、余热锅炉系统停车步骤
1. 随着反应降量,取热量减少,应及时调整V22401给%以上。
50液面V22401水量,保证.
2. 随着烟气温度的降低,应逐步减少进B22401的烟气量,增加烟囱的烟气直接排放量。
3. 适当加大外取热器汽水分离器排水量。
4. 当外取热中部温度降至150℃,可停止V22401上水,关闭外取热水循环,当E22215A、B油浆温度低于250℃时,停止V22402上水,同时也可停止V22403、V22404上水。
5. V22401、22402、22403、22404蒸汽放空,缓慢降压。
6. 锅炉给水泵P22402AB继续向开工锅炉补水,维持停工各装置用汽。