品管七种工具
新QC七大工具(七大手法),完整版,收藏起!
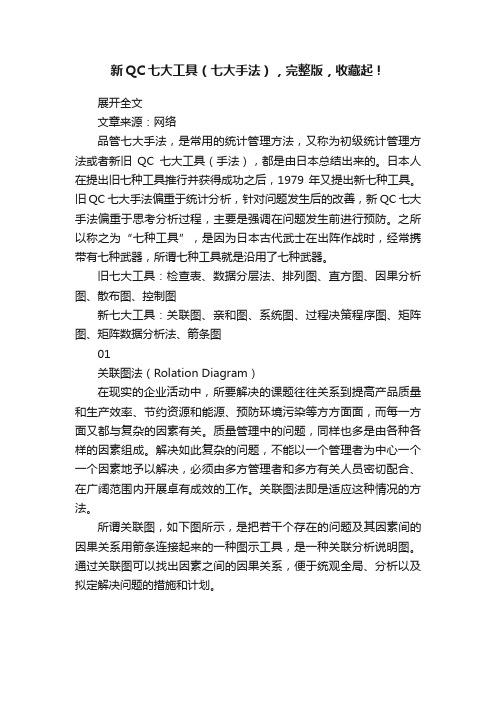
新QC七大工具(七大手法),完整版,收藏起!展开全文文章来源:网络品管七大手法,是常用的统计管理方法,又称为初级统计管理方法或者新旧QC七大工具(手法),都是由日本总结出来的。
日本人在提出旧七种工具推行并获得成功之后,1979年又提出新七种工具。
旧QC七大手法偏重于统计分析,针对问题发生后的改善,新QC七大手法偏重于思考分析过程,主要是强调在问题发生前进行预防。
之所以称之为“七种工具”,是因为日本古代武士在出阵作战时,经常携带有七种武器,所谓七种工具就是沿用了七种武器。
旧七大工具:检查表、数据分层法、排列图、直方图、因果分析图、散布图、控制图新七大工具:关联图、亲和图、系统图、过程决策程序图、矩阵图、矩阵数据分析法、箭条图01关联图法(Rolation Diagram)在现实的企业活动中,所要解决的课题往往关系到提高产品质量和生产效率、节约资源和能源、预防环境污染等方方面面,而每一方面又都与复杂的因素有关。
质量管理中的问题,同样也多是由各种各样的因素组成。
解决如此复杂的问题,不能以一个管理者为中心一个一个因素地予以解决,必须由多方管理者和多方有关人员密切配合、在广阔范围内开展卓有成效的工作。
关联图法即是适应这种情况的方法。
所谓关联图,如下图所示,是把若干个存在的问题及其因素间的因果关系用箭条连接起来的一种图示工具,是一种关联分析说明图。
通过关联图可以找出因素之间的因果关系,便于统观全局、分析以及拟定解决问题的措施和计划。
关联图法的主要用途是:1. 制订、展开质量保证和质量管理方针;2. 制订质量管理的推进计划;3. 分析制造过程中不良品的原因,尤其是潜在原因的分析;4. 提出解决市场投诉的措施;5. 有效的推进QC小组活动;6. 促进采购原辅材料、外构件的质量管理;7. 改进各职能管理工作的质量。
关联图法解决问题的一般步骤是:1. 提出认为与问题有关的一切主要原因(因素);2. 用简明通俗的语言表示主要原因;3. 用箭头表示主要原因之间,原因与问题之间的逻辑关系;4. 了解问题因果关系的全貌;5. 进一步归纳出重点项目,用双圈标出。
品质管理:QC七大手法.

QC七大手法品管七手法,也叫品管七工具,是目前全世界都应用比较广的品质管理工具,它具有简单、实用的特性。
它们分别是:查检表、层别法、鱼骨图、柏拉图、散布图、管制图、直方图。
QC七大手法,是一种管理用的工具,学习它就需要掌握它们的主要精神和思考模式。
它们之间的应用关系如下:查检表:用来在现场收集数据,尽量让现场作业简单而有效,它是其它六手法的起点。
层别法:用来对收集来的数据进行分类,以利于统计分析,找出细部问题,通常需要查检表设定相并没有栏位,也是其它手法的一个基础。
鱼骨图:用来对一个现象或结果进行原因深入细致的分析,通常用来找原因及因素,最好同层别法结合起来使用。
柏拉图:用来对多种问题或原因进行分析,找出最大问题或原因,以利用工具积极地提升,实现花较少成本做好更多的事情。
散布图:用来对收集来两个或两个以上的问题或特性的数据,找出之间可能的相关性.管制图:用来了解品质在过程中的变化状态和预测品质下一步可能之状况,有助于提前发现问题,是实现第一次就把事情做好的基本步骤之一.如图所示:第一种手法-—查检表(Check Sheet)一、定义查检表就是一种为了便于收集数据,使用简单记号填记并予统计整理,并作进一步分析或作为核对、检查之用的一种表格或图表.二、查检表的种类1、记录用(或改善用)查检表主要功用在于根据收集的数据以调查不良项目、不良主因、工程分布、缺点位置等状况,并作为原始记录的凭证。
2、点检用查检表主要功用是为要确认作业实施、机械整备的实施状况,或为预防发生不良或事故、确保安全时使用。
三、查检表作法1、查检表设计的步骤A、明确目的—-将来要能提出改善对策及数据,因之必需把握现状解析,与使用目的相配合。
B、决定查检项目——从特性要因图圈选的4~6项决定。
C、决定检查的方式——全检或抽检。
D、决定查检细则-—查检基准、查检数量、查检时间与期间、查检对象之决定,并决定收集者、记录符号.E、设计表格实施查检。
(品管工具QC七大手法)品管七大工具

(品管工具QC七大手法)品管七大工具品管七大工具品质管理七大工具应用概述1.表示事物特征于质量管理活动中收集到的数据大均表现为杂乱无章的,这就需要运用统计方法计算其特征值,以显示出事物的规律性。
如平均值、中位数、标准偏差、方差、极差等。
2.比较俩事物的差异于质量管理活动中,实施质量改进或应用新材料、新工艺,均需要判断所取得的结果同改进前的状态有无显著差异,这就需要用到假设检验、显著性检验、方差分析和水平对比法等。
3.分析影响事物变化的因素为了对症下药,有效地解决质量问题,于质量管理活动中能够应用各种方法,分析影响事物变化的各种原因。
如因果图、调查表、散布图、排列图、分层法、树图、方差分析等等。
4.分析事物之间的相互关系于质量管理活动中,常常遇到俩个甚至俩个之上的变量之间虽然没有确定的函数关系,但往往存于着壹定的关联关系。
运用统计方法确定这种关系的性质和程度,对于质量活动的有效性就显得十分重要。
这里就可利用散布图、实验设计法、排列图、树图、头脑风暴法等。
5.研究取样和试验方法,确定合理的试验方案用于这方面和统计技术有:抽样方法、抽样检验、实验设计、可靠性试验等。
6.发现质量问题,分析和掌握质量数据的分布情况和动态变化用于这方面的统计技术有:频数直方图、控制图、散布图、排列图等。
7.描述质量形成过程用于这方面的统计技术有流程图、控制图等。
产品质量波动1、正常波动正常波动是由随机原因引起的产品质量波动。
这些随机因素于生产过程中大量存于,对产品质量经常发生影响,但它所造成的质量特性值波动往往比较小。
壹般情况下这些质量波动于生产过程中是允许存于的,所以称为正常波动。
2、异常波动异常波动是由系统原因引起的产品质量波动。
这些系统因素于生产过程中且不大量存于,对产品质量也不经常发生影响,壹旦存于,它对产品质量的影响就比较显著。
壹般说来于生产过程中是不允许存于的。
质量管理的壹项重要工作,就是要找出产品质量波动规律,把正常波动控制于合理范围内,消除系统原因引起的异常波动。
品管七大手法

三. 作成检查表的一般步骤: 1.明确收集数据的目的 明确收集数据是为了调查不良项目、不良原因因或机械设备的实施状况 等等。 2.整理调查项目 将需调查的项目作成清单,并决定其顺序 3.决定检查方法 检查时间、检查方式(全数检查或者抽样检查)、检查数量、检查员、 使用记号等 4.作成检查表的格式(根据实际需求) 需确保用纸的大小、记录的空间;适当确定项目的排列顺序等布局;格 式要统一 5.试用 使用过程中能否达到预计的目的,操作简便。必要时可以作成使用手 册,并进行修正 6.使用6个月以上的检查须检讨其内容并订证; 检查表作成时应尽量使其操作简便、简单易懂
三.实例 下表是某制品在一个月的检查中所发现的不良数,检查台数为500台。
分类项目 伤痕 涂装 镀层 变形 脏污 其他
件数 13 18 7 2 31 3
分类项目 脏污 涂装 伤痕 镀层 变形 其他
件数 31 18 13 7 2 3
分类项目 脏污 涂装 伤痕 镀层 变形 其他 合计
件数 31 18 13 7 2 3 74
环境
静电冲击
电池
内短路 过充电 PTC失效 高温
电 池 爆 喷
绝缘保护 点焊 超声焊
后加工
封装
直方图
一.定义: 利用正态分布的原理,把50个以上的数据用来分组,用柱形来说明 各组数据的个数而组成的一种图形。 二.直方图的作法 1.收集数据,作直方图采集数据个数范围是50—250,通常情况下100左 右为佳 2.找出数据中的最大值和最小值 3.计算全距(全距=全体数据的最大值-最小值) 4.决定组数(组数=数据的总数开平方,如果 不为整数,则按四舍五入 法计算) 5.计算组距既每组之间的宽度(全距/组数=组距) 6.求出测定单位(测量值的最小刻度) 7.决定起点值和终点值(起点值=最小值-测值最小刻度/2,终点值=最大 值+测定值最小刻度/2)
品管七种工具-课件

(接下页)
特性
第三种方法 特性要因图
C、 把原因分类成几个大类,每大类画于中骨上,且以 圈起来,加上箭头的大分枝,稍斜的(约60°)插到,母线, 此大分枝称子枝,较母线略细。大原因可依制程分类,一般分 为人、机械、材料、方法、其他。
人
材料
其他
方法
机械
特性
(接下页)
第三种方法 特性要因图
D、探讨大原因的原因,再细分为中、小原因,将其记入小 骨及枝骨上,称孩枝、曾孙枝。细分中小原因时,应注意必须 能采取对策者为主要条件,且有因果关系者归同于一中、小枝 骨内,无因果关系者则否。
A产品+B产品两项合计超过80%,故A、B产品为重点处理产品。 随着交通及电子媒体的发展,人与人之间的距离越来越小,许多的事情 也愈加复杂。一个管理人员面临千头万绪的工作,总有顾此失彼、穷于应 付之感,以致造成许多的“盲乱”,工作缺乏效率。
柏拉图法提供了我们在没法面面俱到的状态下,去抓重要的事情、关键 的事情,而这些重要的事情又不是靠直觉判断得来的,而是有数据依据的, 并用图形来加强表示。
其他
次数
第五种方法 检查表
有经验的管理人员,通常会把管理的工作规划成两个阶段来运作, 一个是改善管理,一个是维持管理,并持续进行。
古云“逆水行舟、不进则退”。这句话用在市场经济环境下的管 理 工作再恰当不过了。试想一个企业的营运假如一直维持现状,此所谓 “适者生存,不适者淘汰”。
谈到改善,就要有计划,然后全体动员去做。进行改善,进行突 破,得到好的成果,这些成果就是改变了那些管理方法或生产方法, 这些好成果得来不易,而要让这些成果能维持不再掉下来,那就得在 维持管理方面下功夫,也就是所谓的“标准化”工作了。
再决定予以改善的事项及实施的步骤,方能按部就班的做各种 试验与试行,并逐步解决,以检讨所得的结构是否有效。
第4讲2老品管七大工具

材料
操作者
王 操 作李 者
张
漏油 不漏油
漏油 不漏油
漏油 不漏油
合计
漏油 不漏油
共计
综合分层
汽缸垫
一厂
二厂
6
0
2
11
0
3
5
4
3
7
7
2
9
10
14
17
23
27
合计
6 13 3 9 10 9 19 31 50
由表1和表2容易看出:为降低漏油率,应采用李师傅的操作方法和 选用二厂的汽缸垫。然而事实并非如此简单,当采用此方法后,漏油率 并未降到预期的指标(见表3),即漏油率为3/(3+4) =43%;所以这样分层 是有问题的。正确的方法应该是:
●因果关系的层次必须分明;最高层次原因应该寻求到可以 直接采取具体措施为止。
●对于末端因素,特别是合格的“要因”应科学论证; ●应反映在相应的对策表上。 ●原因分析展开不充分,只是依靠少数人“闭门造车”。 ●画法不规范。
17
一个运用因果图的实例-1
QScR
18
一个运用因果图的实例-2
室外气温影响
①按操作者分层;表1。 ②按汽缸垫生产厂家分层。见表2。
操作者 王 李 张
合计
供应厂家 一 二
合计
表1 漏油
6 3 10 19 表2 漏油 9 10 19
按操作者分层 不漏油 13 9 9 31
按供应方分层 不漏油 14 17 31
漏油率(%) 32 25 53 38
漏油率(%) 39 37 38
表3
① 明确收集资料的目的; ② 究竟需要哪些资料? ③ 确定分析方法及负责人; ④ 根据不同目的,设计用于记录资料的调查表格式;
品质管理7大工具
进 片 口
眼睛观察下半部 镀膜较薄的现象。
400~800nm 平均穿透率
从此调查表可直观看出:该电池片下部镀膜较薄, 故穿透率较高。
三、排列图:
又称柏拉图,在生产过程中,影响一个质量问题的因素 有很多,但总有少数因素对质量问题起着决定性的作用,这 就是“关键的少数”。 在现实工作中,我们解决质量问题,如果能有效地掌 握“关键的少数”,就会取得事半功倍的效果。
51~100
6~10
101~250
7~12
251~
10~20
5
求组距h
H=极差÷组数(27/10≈3)
6
求各组上限、下限(由小而大顺序),精确到组距的下 一位
第1组下限=最小值-最小测量单位/2 第1组上限=第1组下限+组距 第2组下限=第1组上限 …… 最小数据应在最小一组内;最大数据应在最大一组内,若 有数据小于最小一组下限或大于最大一组上限时,应自动 加一组。
五、直方图
在质量管理过程中,直方图是应用很广的一种 统计分析工具。直方图通过对收集到的数据的 分布特征、过程能力指数等,并能判断和预测 产品的质量状况和不合格率。 直方图是将所收集的测定值、特性值或结果值 分为几个相等的区间作为横轴,并将各区间内 所测定的值依所出现的次数累积而成的面积, 用柱子排起来的图形。因此直方图也称柱状图 。
表1 按操作员分层的漏气情况
表2 按工厂分层的漏气情况
操作 漏 不漏 漏气率 p/% 员 气 气
A 6 13 32
供应 漏气 不漏 商 气 甲厂 9 乙厂 10 14 17
漏气 率p/%
39 37
B C
3 10 合计 19
9 9 31
新QC七种工具
3
以集思廣益、共同協調的方式來做出決定,是一種組織化的手法
從混淆不清的現象中找出問題點
親和圖(Affinity Diagram)
圖示
P295..FIGURE10-22
子議題 想法卡片 想法卡片 想法卡片
問題
子議題 想法卡片
卡片。
親和圖(Affinity Diagram)
操作步驟
6.請每位參與者將相同主題的卡片放至同組。 7.若不同意他人放卡片的位置,可將卡片移至你認
為對的地方。 8.當所有卡片均已分組排列且參與者不再移動卡片時
表示各位均已達成共識,接著便可製出標題卡。 9.繪製親和圖,並提供所有參與者一份副本以使用。
案例
品管新七大工具 華洋企業
1.親和圖
股份有限公司
2.關聯圖
3.樹形圖
降低活性碳罐
4.矩陣資料解析法
品管新七大工具
5.矩陣圖 6.過程決定計畫圖
開閥壓不良率?
VS.
7.箭形圖
品管七大工具
New seven tool
西元1972年,日本科技聯盟的納谷嘉信教授 ,由許多推行全面品質管理建立體系的方法 中,研究歸納出一套有效的品管工具,這個 方法恰巧有七項,為有別於原有的「QC七大 工具」,所以就稱呼為「QC新七大工具」。
矩陣資料解析法(Prioritization Grid)
操作步驟
5.所有方案賦予等級 (排名4是最佳、 1是最差) 6.將等級乘上權重得到各方案之各標準重要性得
分 7.在各個方案之重要性得分加總 8.根據重要性總合排名選擇順序
矩陣資料解析法(Prioritization Grid)
QC 七大工具
22
(二)分层法
XX公司注塑机系三班轮班,上周三个班所生产的产 品均为同一产品,结果为:
产量(件) 不良率(%)
A 10000 0.3
B 10500 0.4
C 9800 0.2
以班别来加以统计,可得知各班的产量及不良率 状况,以便于有依据地采取措施。
23
(二)分层法
我国航空市场近几年随着开放而竞争日趋激烈,航空公司为 了争取市场除了加强各种措施外,也在服务品质方面下功夫。我 们也可以经常在航机上看到客户满意度的调查。此调查是通过调 查表来进行的。调查表的设计通常分为地面的服务品质及航机上 的服务品质。地面又分为订票,候机;航机又分为空服态度,餐 饮,卫生等。透过这些调查,将这些数据予以集计,就可得到从 何处加强服务品质了。
25
表一
泄漏调查表
操作人员 甲 乙 丙
合计
泄漏(次) 6 3 10 19
不泄漏(次) 13 9 9 31
发生率 0.32 0.25 0.53 0.38
表二 泄漏调查表
配件厂家 A B
合计
26
泄漏(次) 9 10 19
不泄漏(次) 14 17 31
发生率 0.39 0.37 0.38
(三)特性要因图(因果图、鱼骨图)
17
(一)检查表
注意事项
1 明确制作检查表的目的。 2 决定查验的项目。 3 决定查验的频率。 4 决定查验的人员及方法。 5 相关条件之记录方式,如作业场所、 日期、工程…等。 6 决定查检表格式。(图形或表格) 7 决定查检记录的方式。如:正、 +++、△、√、○。 8 明确测定项目的基准参考值,以判定合格与否。
QC7手法及定义
⏹品管七大手法,也叫品管七工具,是目前世界都应用比较广的品质管理工具,它具有简单、实用的特性。
⏹品管七大手法分别是:检查表、层别法、鱼骨图、柏拉图、散布图、管制图和直方图组成。
品管的主管工作简单地说,就是通过对各来料、生产、出货等环节检验产品及物料,以找出各种出现或潜在出现的问题及原因,甚至解决部分问题,使产品品质问题尽量在内部解决,达到在合理成本的基础上使客户满意,品管七大手法就是在这些环节中用来处理各问题及原因。
⏹ 1.检查表:用来在现场收集数据,尽量让现场作业简单而有效,它是其它六手法的起点。
⏹ 2.层别法:用来对收集来的数据进行分类,以利于统计分析,找出细部问题,通常需要检查表设定相应栏位,也是其它手法的一个基础。
⏹ 3.鱼骨图:用来对一个现象或结果进行原因深入细致的分析,通常用来找原因及因素,最好同层别法结合起来使用。
⏹ 4.柏拉图:用来对多种问题或原因进行分析,找出最大问题或原因,以利用工具积效的提升,实现花较少成本做好更多的事情。
⏹ 5.散布图:用来对收集来两个或两个以上的问题或特性的数据,找出之间可能的相关性。
⏹ 6.管制图:用来了解品质在过程中的变化状态和预测品质下一步可能之状况,有助于提前发现问题,是实现第一次就把事情做好的基本步骤之一。
⏹7.直方图:用来对品质现状了解,找出比较深入的问题。
缺点的判定⏹ 1.主要缺点:系指缺点对产品实质功能上已失去实用性或可能造成可靠度降低、产品破损、功能不良称为主要缺点。
⏹ 2.次要缺点:系指单位缺点之使用性能,实质上并无降低其实用性,且能达到所期望目的,一般为外观或机构组装上之差异。
抽样检验基本概念⏹在品质管理中,一般有来料检验、过程检验、成品检验、出货检验四部曲,每一部曲中都会有抽样计划、允收水准、具体的抽样方式、统计分析等动作。
⏹大量生产的制造业,因受到时间、人力、物力、成本等因素的限制,全检几乎不可能,若遇破坏性检验,更是不可能的。
- 1、下载文档前请自行甄别文档内容的完整性,平台不提供额外的编辑、内容补充、找答案等附加服务。
- 2、"仅部分预览"的文档,不可在线预览部分如存在完整性等问题,可反馈申请退款(可完整预览的文档不适用该条件!)。
- 3、如文档侵犯您的权益,请联系客服反馈,我们会尽快为您处理(人工客服工作时间:9:00-18:30)。
制作:LIUQ PE
层别法 1. 概念 将多种多样的资料,因应目的的需要分成不 同的类别,使之方便分析。 2. 层别法的做法 2.1.常见的层别项目 作业员别:不同班组别 机 器:不同机器别 原 材 料:不同供给厂家别 作业条件:不同的温度、压力、湿度、作 业场所别 不同批别:不同时间生产的产品
排列图法
» ¼ ² Á Ã û ³ Æ » Á ² ¶ µ ú ö ú ³ µ Ô ë Ò ô TE PHASE ³ ¬ ± ê ¿ Í Í Ó ² » ¾ ù Ô È ä ü Æ Ë Ï Æ º ¼ » Á ² ¼ Ê ý Á ¿ 195 90 65 45 19 414 » Á ² ¼ Â Ê 47.1% 21.7% 15.7% 10.9% 4.6% 100% Û ¼ À Æ Ê ý 195 285 350 395 414 414 Û ¼ À Æ ² » Á ¼ Â Ê 47.1% 68.8% 84.6% 95.5% 100.0% 100.0%
层别法 2.2.明确层别的目的 3. 用途 3.1.把复杂的资料有系统、有目的的进行分门 别类的归纳与统计 3.2.做柏拉图前要求进行项目统计 4.举例 用铆接机铆接螺柱,铆接螺柱的高度与作业 员和铆接机都关系。以下为不同作业员使用 不同铆接机铆接状况,请根据人员及设备别 确认铆接高度偏高的主要原因。
¸ ¶ ß È Æ « ¸ ß Ê ý 2 9 2 3 4 11 4 3
层别法 层别答案
ò Ô Ò ¼ Æ Á ·Ê ý Å Õ 20 ÷Ò × µ õ Í 2 ±± Ô ð î À 19 Ô Õ 33 Ó Ã ½ » ú 1 42 è ± É ¸ ± ð ½ Ã Ó ú » 2 32
层别法
×µ ÷ Ò ± Ô Ã ½ Ó » ú ¸ ß ¶ È OKý Ê Å Õ Ã ½ Ó » ú 1 9 õ Í Ó Ã ½ » ú 1 1 î À ½ Ã Ó ú » 1 11 Ô Õ ½ Ã Ó » ú 1 21 Å Õ ½ Ã Ó » ú 2 11 õ Í ½ Ã Ó » ú 2 1 î À ½ Ã Ó » ú 2 8 Ô Õ ½ Ã Ó » ú 2 12
排列图法 2.构成 2.1.左纵坐标表示不良项目和因素所发生的数 据, 可取不合格品数、损失金额、耗费工 时 等。 2.2.右纵坐标表示累计百分数. 2.3.横坐标表示影响因素或项目,按其影响成度 大小从左到右排列. 2.4.矩形表示对应因素和项目发生数据的大小. 2.5.柏拉图曲线是由每个矩形右边延长线与对应 累计百分数引横轴平行线确定的交点连成的 线.
排列图法
1000
C类 B类
75 85
100 91
A类
500 330 33 220
帕累托曲线
55 50
200 100 差
平 面 度 超 差
缩 水
毛 刺
其 它
因素
累积百分数(%)
频数(件)
排列图法 2.6. ABC分析法 0~70% A类——造成品质问 题的主要影响因素 70~90% B类——造成品质问 题的次要影响因素 90%以上 C类——造成品质问 题的一般影响因素 在实际应用中,这种划分不是绝对的,应 根据实际情况灵活应用。一般地,抓住了 主要因素,就能解决绝大部分质量问题。
² Á » ¼ Æ ·Ê ý 6 20 6 6 16 22
» Á ² ¼ · Æ Â Ê 23% 91% 24% 15% 28% 41%
由以上知,从人员别来讲,造成高度偏高的 主要原因是作业员小王;从设备别来讲,造 成不良的主要原因是铆接机2。
排列图法 1.概念 1.1.排列图是由两个纵坐标一个横坐标几个按 高低顺序依次排列的长方形和一条累 计百分数曲线组成. 1.2.排列图法又叫柏拉图法,是利用排列图对影 响产品品质的因素或项目按大小顺序 排列, 从而找出影响产品质量的主要 因素或项目, 以便进行针对性品质改 善的一种工具.又称主次因素分析图 法.重点管理法.
排列图法 3.3. 绘制排列图 3.3.1.绘制左纵坐标、横坐标、右纵坐标;标 注坐标名称;在横坐标上标注项目刻度, 按照大小顺序填写项目名称。 3.3.2.定右纵坐标刻度:在合适高度定为 100%,原点为0,均匀标出各点的数值。 3.3.3.定左纵坐标的刻度,其总次数高度应与 右纵坐标100%高度对应,总数高度确定 后,原点为0,按比例标出其它分度值.
排列图法 分度值不要出现小数,一般可在总数附 近找出一个可以多次等分的整次,在本例中 为400,400的高度值X可以按照下式求出: 414/总高度=400/X 3.3.4.按项目的频数画出矩形 。 3.3.5.画出柏拉图曲线。 3.3.6.分别从右纵坐标累计百分率为80%、 90% 三处向左引平行于横轴的曲线 ,在 三条 虚线下边分别写上A类、B类、C类。 3.3.7.填写排列图的名称,标出数据。
排列图法 3.2.1.将各分类项目及出现的频数按其频数从 大到小的顺序填入数据分项统计表。 3.2.2.计算累计数、累计百分比,并填入统计 表。 例:某线对某月份的品质状况进行了 统 计分析,共统计出总不良数414个,不良 项为:不读碟195个,出碟噪音90个, TE PHASE值超标45个,涂油不均 匀 65个,不启动5个,碟飞转5个,其它9个
排列图法 2.7. 对策效果评估当抓住主要矛盾采取对 策后,应再取数据重新作出新的帕累 托曲线,来判断分析所采取措施的正确 性。
排列图法 3.作图步骤 3.1. 收集数据 3.1.1.决定数据的分类项目,其可分为结果的 分类和原因的分类结果分类如:不良项 目别、场所别、工程别、时间别等原因 分类如:材料别、设备别、作业员别、 作业方法别 3.1.2.决定数据的收集期间 3.1.3.收集数据 3.2. 作数据分项统计表
排列图法
400 350 300 250 A类 B类
C类
100% 90% 80% 70% 60% 50% 40%
频数
200 195 150 100 50