几种催化裂化烟气脱硫技术
烟气脱硫脱硝技术进展 催化裂化烟气脱硫脱硝技术
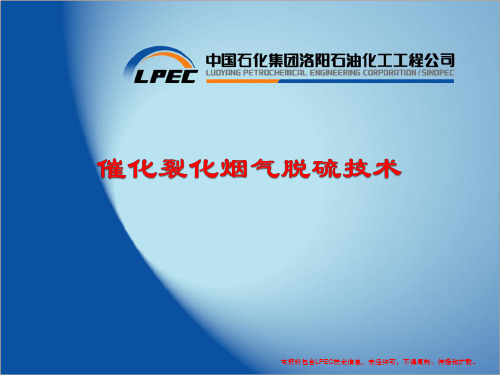
本资料包含LPEC技术信息,未经许可,不得复制、传播和扩散。
– 该工艺由两个主要部分组成
湿式气体洗涤器(WGS) 净化处理单元(PTU) WGS主要包括一个文丘里管和一个分离塔。 碱性液体与烟气同向进入文丘里管,洗涤液体在缩径段的壁上形 成一层薄膜,然后在咽喉段的入口处被分割成液滴,由于相对速 度差的存在,气体与液滴间发生惯性碰撞,颗粒在咽喉段被捕捉 ,SOX在咽喉段和扩径段被脱除。 液体和碱性物(如NaOH)直接进入分离塔,洗涤液在分离塔中 初步净化,以保持系统中固体和溶解盐的浓度平衡,而后循环使 用,其中部分进入PTU进一步处理,将化学需氧量和悬浮物降到 合理的水平。
本资料包含LPEC技术信息,未经许可,不得复制、传播和扩散。
– 为保证烟气中没有液滴,烟气进入液滴分离器。 – 从洗涤系统排出的洗涤液包括悬浮的细小颗粒及溶解的亚
硫酸钠和硫酸钠。
洗涤液处理系统可以将固体悬浮物分离,并且将亚硫酸钠氧化为 硫酸钠降低COD值,从而可以进入炼厂水处理系统或直接排放 。 系统包括一个澄清池脱除悬浮固体,以及一个过滤器。 氧化系统为一个塔,空气出入塔内,将亚硫酸钠氧化为硫酸钠。
本资料包含LPEC技术信息,未经许可,不得复制、传播和扩散。
Thiopaq DeSOx
本资料包含LPEC技术信息,未经许可,不得复制、传播和扩散。
WGS烟气脱硫技术 – Exxon公司是最早从事装置烟气排放技术研究的的公司,典 型的工艺为WGS工艺。 – 1974年建成第一套湿式气体洗涤系统,到1999年已建成 15套。 – 烟气量处理最大的为1290dam3/h,脱硫率可达到94%~ 97%。
动力波(Dyna-wave)洗涤技术 – 该技术于70年代由美国杜邦公司开发并获得专利,初期主 要用于空气污染控制。 – 它是使气体通过一个强烈湍动的液膜泡沫区,利用泡沫区 液体表面积大而且迅速更新的特点,强化了气液传质、传 热过程。 – 它能同时完成烟道气急冷、酸性气体脱出及固体粉尘脱出 三个功能。 – 可用于多个工业领域,如冶金工业的炉窑、电厂、水泥厂、 工业废弃物焚烧、钛白粉厂、炼焦厂、炼油厂、锅炉等。
催化裂化装置烟气脱硫技术选择

工艺方法——催化裂化烟气脱硫技术

工艺方法——催化裂化烟气脱硫技术工艺简介催化裂化是石油炼制的重要过程之一,在催化剂的作用下,通过加热的方式促使重油发生裂化反应生产裂化气、汽油和柴油。
催化裂化工艺流程中产生的烟气含有大量的硫化物,对设备造成了腐蚀,同时对环境产生了很大的影响。
1、干法、半干法脱硫技术干法脱硫技术主要使用干粉作为吸收剂,半干法脱硫一般使用润湿的干粉吸收剂进行硫化物的吸收,两种方法的吸收剂都是通过颗粒回收系统进行吸收剂的回收。
干法和半干法脱硫的主要优点是可以在不降低烟气温度的基础上完成硫化物吸附,避免了硫化物扩散和脱硫作业的水污染问题。
缺点是硫化物的吸附只在脱硫剂的表面进行,内部反应时间长,需要大型的吸附塔和大量的吸附剂才能完成脱硫作业。
干法脱硫比较有代表性的公司,比如Engelhard公司开发的SO2干法脱硫工艺(ESR)是一种比较先进的干法脱硫技术,该工艺采用干燥脱硫剂固体流化床,硫化物脱除率达到95%以上,脱硫剂可以全部再生,并且投资少,操作费用较低。
2、EDV湿法烟气脱硫技术EDV湿法洗涤脱硫技术由Belco公司开发,20世纪90年代中期开始工业应用,问世以来显示出了较为优异的操作性和可靠性。
EDV 烟气脱硫技术主要由氧化镁制浆系统、烟气洗涤系统和废水处理系统组成,利用对烟气喷射的方法,通过烟气的急冷降温处理,在烟气温度恢复正常后,在温度变化过程中脱除烟气中的有害物质,使得烟气中的硫化物凝结最后采用系统过滤烟气,完成烟气的气液分离。
氢氧化镁溶液放置到卸料机上以后,倒入适量的水进行搅拌,制成脱硫溶液,在配置过程中需要控制好水的加入量。
3、加氢预处理技术原油的加氢预处理可以有效处理原油中的硫化物,通过加氢预处理,对于减少原油中硫化物、重金属等杂质具有良好的效果。
加氢预处理技术在对原油进行有害物质处理的过程中,可以进一步提高原油中轻质产品的回收率和回收质量,从而改善催化裂化工艺产品的质量,满足现代炼油企业催化裂化技术发展的需求,从而满足炼化企业快速发展的需求。
催化裂化烟气同时脱硫、脱硝新技术

催化裂化烟气同时脱硫、脱硝新技术随着工业的发展,烟气污染对环境和人类健康造成了严重的影响。
而其中硫氧化物和氮氧化物是主要的污染物之一。
因此,研究开发一种能够同时高效脱除烟气中的硫氧化物和氮氧化物的催化裂化新技术显得尤为重要。
催化裂化烟气同时脱硫、脱硝技术是一种基于催化作用的先进技术,能够在高温条件下实现烟气中硫氧化物和氮氧化物的去除,有效减少其对环境的影响。
该技术综合应用了催化剂、吸附剂等多种材料,通过化学反应达到同时脱硫、脱硝的目的。
首先,催化剂在催化裂化过程中起到了重要的作用。
催化剂可以降低反应温度和活化能,提高反应速率和选择性,从而促进硫氧化物和氮氧化物的催化转化。
催化剂的选择和设计对于技术的效率和稳定性具有关键影响。
目前常用的催化剂包括贵金属类、过渡金属氧化物类等,其性能和稳定性经过多次研究得到不断改善。
其次,吸附剂在催化裂化烟气处理中也起到了重要作用。
吸附剂可以吸附烟气中的硫氧化物和氮氧化物,使其从气相转化为固相,从而实现脱硫、脱硝的效果。
常用的吸附剂有活性炭、分子筛等,其物理性能和吸附能力的改进对于技术的性能和经济效益具有重要意义。
通过将催化剂和吸附剂结合使用,催化裂化烟气同时脱硫、脱硝技术能够较好地解决烟气污染问题。
催化裂化烟气处理工艺中,烟气经过预处理后,进入催化裂化装置,通过催化剂的作用,使硫氧化物和氮氧化物发生催化反应转化为无害物质。
然后,烟气经过吸附剂的处理,吸附剂将烟气中的硫氧化物和氮氧化物吸附下来,使其被固定在吸附剂上,达到脱硫、脱硝的效果。
最后,经过处理后的烟气排放出去时,其硫氧化物和氮氧化物含量大幅降低,对环境的影响也得到了有效的控制。
总的来说,催化裂化烟气同时脱硫、脱硝新技术是一种高效、环保的烟气处理技术。
通过合理选择和设计催化剂和吸附剂,可以实现烟气中硫氧化物和氮氧化物的高效去除,减少对环境的影响。
随着技术的不断进步和优化,催化裂化烟气处理技术将会在工业生产中得到广泛应用,为改善环境质量和保护人类健康做出贡献。
工艺方法——石油催化裂化烟气脱硫技术
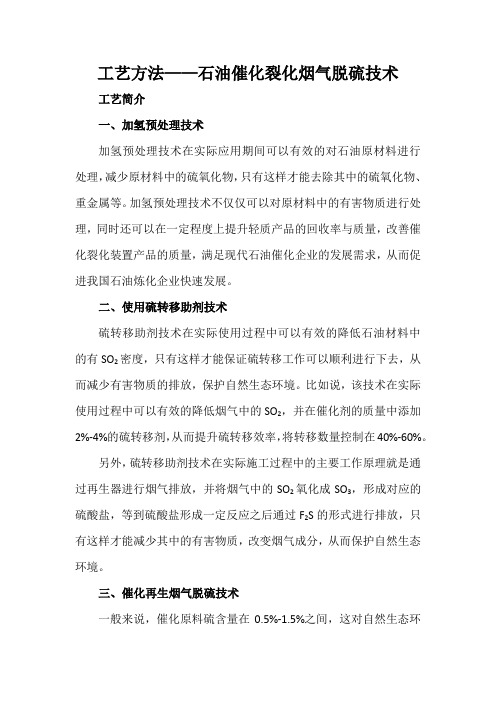
工艺方法——石油催化裂化烟气脱硫技术工艺简介一、加氢预处理技术加氢预处理技术在实际应用期间可以有效的对石油原材料进行处理,减少原材料中的硫氧化物,只有这样才能去除其中的硫氧化物、重金属等。
加氢预处理技术不仅仅可以对原材料中的有害物质进行处理,同时还可以在一定程度上提升轻质产品的回收率与质量,改善催化裂化装置产品的质量,满足现代石油催化企业的发展需求,从而促进我国石油炼化企业快速发展。
二、使用硫转移助剂技术硫转移助剂技术在实际使用过程中可以有效的降低石油材料中的有SO2密度,只有这样才能保证硫转移工作可以顺利进行下去,从而减少有害物质的排放,保护自然生态环境。
比如说,该技术在实际使用过程中可以有效的降低烟气中的SO2,并在催化剂的质量中添加2%-4%的硫转移剂,从而提升硫转移效率,将转移数量控制在40%-60%。
另外,硫转移助剂技术在实际施工过程中的主要工作原理就是通过再生器进行烟气排放,并将烟气中的SO2氧化成SO3,形成对应的硫酸盐,等到硫酸盐形成一定反应之后通过F2S的形式进行排放,只有这样才能减少其中的有害物质,改变烟气成分,从而保护自然生态环境。
三、催化再生烟气脱硫技术一般来说,催化原料硫含量在0.5%-1.5%之间,这对自然生态环境的发展来说造成很大的影响。
要想从根本上解决这一问题就可以通过吸附法的形式硫含量吸附,并选择一些可再生能力较强的固定吸附剂进行吸附,只有这样才能降低其中的硫含量,从而减少有害物质的排放。
这种催化再生烟气脱硫技术在实际使用过程中的投资成本较低,运营费用较小,可以有效的清除烟气中的硫氮化物,满足炼油企业日常生产、发展时的需求。
四、EDV烟气脱硫技术EDV烟气脱硫技术主要由氧化镁制浆系统、烟气洗涤系统、废水处理系统组成,当烟气进入到对应的喷射系统中,烟气就会通急冷区降温的形式进行处理,等到温度恢复正常之后,烟气中有害物质就会自动去除。
最后,再通过洗涤系统进行烟气过滤,做好烟气与液滴的分离工作。
催化裂化烟气脱硫脱硝工艺流程

催化裂化烟气脱硫脱硝工艺流程一、催化裂化烟气脱硫催化裂化烟气脱硫主要包括湿法脱硫和干法脱硫两种方法。
1.1湿法脱硫湿法脱硫通常采用碱性溶液(如氢氧化钠、氢氧化钙等)吸收烟气中的二氧化硫,生成亚硫酸盐或硫酸盐,然后进行氧化、结晶和分离,从而达到脱硫的目的。
湿法脱硫技术成熟,脱硫效率高,但对设备腐蚀严重,会产生大量废渣。
1.2干法脱硫干法脱硫采用固体吸收剂(如氧化钙、活性炭等)在干燥状态下吸收烟气中的二氧化硫,生成硫酸钙或其他稳定的硫化物,从而达到脱硫的目的。
干法脱硫设备简单,操作方便,无腐蚀问题,但脱硫效率相对较低,吸收剂消耗量大。
二、催化裂化烟气脱硝催化裂化烟气脱硝主要包括选择性催化还原法(SCR)和选择性非催化还原法(SNCR)两种方法。
2.1选择性催化还原法(SCR)SCR技术是在催化剂的作用下,使用还原剂(如氨气、尿素等)将烟气中的氮氧化物还原成氮气和水蒸气,从而达到脱硝的目的。
SCR技术脱硝效率高,技术成熟,但对催化剂的依赖较大,催化剂易失活或中毒。
2.2选择性非催化还原法(SNCR)SNCR技术是在高温条件下,使用还原剂(如氨气、尿素等)将烟气中的氮氧化物还原成氮气和水蒸气,不需要催化剂的参与。
SNCR技术设备简单,投资少,但脱硝效率相对较低,且容易造成氨气泄漏。
三、工艺流程优化为了提高催化裂化烟气脱硫脱硝的效率,需要对工艺流程进行优化。
具体措施包括:3.1反应温度控制反应温度是影响脱硫脱硝效率的重要因素。
控制合适的反应温度可以提高吸收剂或催化剂的活性,从而提高脱硫脱硝效率。
3.2液气比选择对于湿法脱硫技术,液气比是影响脱硫效率的关键因素。
适当提高液气比可以提高二氧化硫的吸收率,但会增加设备和运行成本。
因此需要根据实际情况选择合适的液气比。
?催化裂化再生烟气处理技术

催化裂化再生烟气处理技术
催化裂化装置催化剂再生时产生颗粒物、氮氧化物、二氧化硫污染物,其烟气具有烟气量小、烟气成分浓度波动大等特点。
山东明晟再生烟气处理技术可对上述污染物进行控制,处理后烟气满足《石油炼制工业污染物排放标准》(GB31570-2015)排放要求。
工艺流程:
选择性催化还原法(SCR)脱硝+布袋除尘+氨法脱硫
催化裂化装置的再生烟气在300~400℃温度下首先进入SCR脱硝反应装置,在催化剂作用下,烟气中NOx与NH3反应生成N2和H2O。
经脱硝后烟气通过余热锅炉进行余热回收后进入布袋除尘器,经除尘后进入脱硫塔,利用氨化的吸收循环液脱除烟气中二氧化硫后达标排放。
二氧化硫经氨化吸收循环液吸收后形成亚硫酸铵溶液,在氧化系统中经空气氧化为硫酸铵溶液,硫酸铵溶液经入口高温烟气蒸发浓缩后达到一定固含量。
一定固含量的硫酸铵浆液经稠厚器、离心机、干燥机分离干燥后形成水分<1%的副产物硫酸铵,再进入包装机包装为硫酸铵成品。
整套工艺系统包含SCR脱硝系统、布袋除尘系统、烟气系统、吸收系统、氧化系统、浓缩系统、后处理系统等。
1.布袋除尘收集下来废催化剂,通过输送设备输送到催化裂化装置原有废催化剂罐内,达到危废回收完全处理,跟随催化裂化装置产生的废催化剂一同处理。
2.氨法脱硫产出硫酸铵颗粒,形成公司产品销售,回收部分费用。
3.无高盐废水排放,不产生二次污染。
催化裂化烟气脱硝脱硫除尘新技术
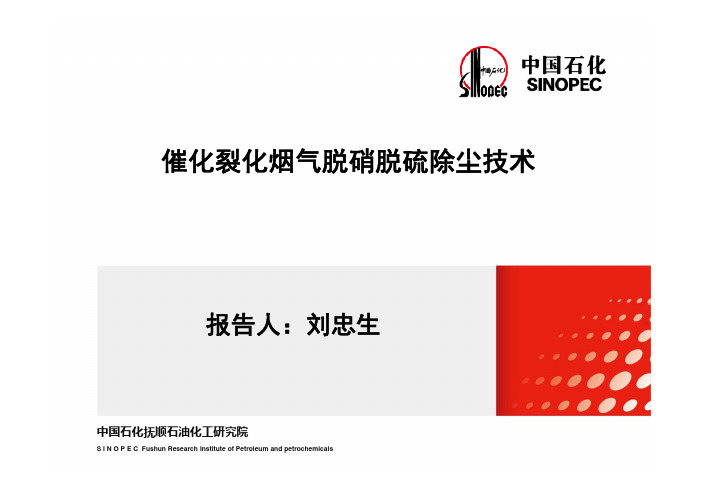
2017/9/12
中国石化抚顺石油化工研究院
S I N O P E C Fushun Research Institute of Petroleum and Petrochemicals
FN‐2脱硝催化剂生产
催化剂生产过程
催化剂生产过程
催化剂产品
中国石化抚顺石油化工研究院
S I N O P E C Fushun Research Institute of Petroleum and Petrochemicals
中国石化抚顺石油化工研究院
S I N O P E C Fushun Research Institute of Petroleum and Petrochemicals
4.2 传统文丘里洗涤器的不足
美国环保局将WGS传统文丘里洗涤 器列为FCC烟气脱硫最佳实用技术;
采用传统文丘里脱除亚微米的粉尘,
2017/9/12
中国石化抚顺石油化工研究院
S I N O P E C Fushun Research Institute of Petroleum and Petrochemicals
4 新型湍冲文丘里湿法脱硫除尘一体化工艺
2017/9/12
中国石化抚顺石油化工研究院
S I N O P E C Fushun Research Institute of Petroleum and Petrochemicals
脱硝采用氨选择性催化还原法(NH3-SCR) 和臭氧氧化法 除尘脱硫主要用氢氧化钠 (或碳酸钠) 碱液洗涤法。
中国石化抚顺石油化工研究院
S I N O P E C Fushun Research Institute of Petroleum and Petrochemicals
- 1、下载文档前请自行甄别文档内容的完整性,平台不提供额外的编辑、内容补充、找答案等附加服务。
- 2、"仅部分预览"的文档,不可在线预览部分如存在完整性等问题,可反馈申请退款(可完整预览的文档不适用该条件!)。
- 3、如文档侵犯您的权益,请联系客服反馈,我们会尽快为您处理(人工客服工作时间:9:00-18:30)。
几种催化裂化烟气脱硫技术
一、主要技术简介
目前催化裂化烟气污染物排放控制技术可分别为干法、湿法两大类,进一步又可分为采添加脱SOx、NOx助剂,催化原料预处理技术,增设烟气脱SOx、脱NOx设施三类。
国外工业运行的催化裂化烟气脱SOx技术以湿法为主,吸收剂(洗涤液)有钠碱、氢氧化镁Mg(OH)2和海水等。
湿法洗涤脱SOx设施一般由吸收(洗涤)单元和废液净化处理单元组成,前者是烟气脱硫技术的核心。
应用较多的有诺顿公司的VSS技术,DuPont BELCO公司的EDV和LABSORBTM 技术、Hamon公司的WGS技术、Shell公司的CANSOLV技术等。
1.1 ExxonMobil公司WGS技术
1974年,当时在Exxon公司工作的John Cunic先生(先就职于美国诺顿公司)开发了第一套FCCU烟气洗涤技术,将喷射式文丘里管JEV应用到催化裂化烟气脱硫装置上。
也就是现在由Hamon公司出售的WGS技术(ExxonMobil 授权Hamon工程公司进行WGS技术的出售及设计工作)。
优点:采用JEV(喷射式文丘里管)时压降低。
缺点:采用HEV(高性能文丘里管)时压降高。
1.2 DuPont BELCO公司的EDV技术
该技术于1994年完成第一套商业应用。
EDV由急冷喷嘴、多层吸收喷嘴及滤清模块(滤清模块有多个文丘里组成)水珠分离器组成。
上世纪90年代,诺顿公司主要给ExxonMobil公司升级维护WGS系统,ExxonMobil公司又不允许将其WGS洗涤技术推广到其他石化企业,造成90年代到2000年,DuPont BELCO 公司销售了多套EDV系统。
优点:业绩较多
缺点:系统在添加滤清模块的情况下压降会升高,可达4-7Kpa
1.3 CANSOLV公司的CANSOLV技术
CANSOLV公司1997年成立于加拿大,CANSOLV再生脱硫2002年开始第一套工业化商业运行。
CANSOLV再生胺法脱硫系统有两部分组成洗涤-吸收和再生-净化,在炼油厂成功业绩全世界只有1套,它主要由以下几点
优点:可回收SO2
缺点:预洗涤部分运行强酸环境,再生部分需要消耗大量的蒸汽;吸收剂每年需要补充5%-10%,受到吸收剂厂家的制约。
收回的SO2需要改造硫磺装置。
1.4 Norton工程公司的VSS技术
Norton公司成立于1993年,世界第一套催化烟气脱硫装置(WGS技术)的发明者John Cunic先生同时来到诺顿公司,自1993年至今ExxonMobil的催化烟气脱硫装置的维护、扩建、新建以及ExxonMobil授权BP等公司使用的WGS均由诺顿公司完成设计和设备提供。
优点:诺顿公司是一家石化工程公司,对石化装置非常了解。
提供的VSS 洗涤系统可以根据装置的烟气量设计出最合理的压降、能耗的脱硫系统。
缺点:国内业绩较少,目前只有几套装置运行。
二、工艺介绍
2.1诺顿工程公司(Norton Engineering)VSS技术
美国诺顿工程公司是埃克森美孚,康菲石油,壳牌,BP,墨西哥石油公司等世界一流石化企业的技术供应商。
2001年,诺顿公司开发完成自有的催化裂化装置烟气洗涤技术—VSS湿法洗涤工艺。
该工艺主要包括两部分:文丘里洗涤部分和净化处理部分。
使用碱性溶液作为吸收剂(洗涤液),洗涤流程简图如下:
CLEAN GAS
SLURRY
PUMP
文丘里洗涤部分流程图
废液净化处理部分流程图
文丘里洗涤部分由进气管道、文丘里管、联接弯头、分离塔、烟囱等组成。
烟气从进气管道出来之后,首先进入文丘里管,在这里烟气和液体进行激烈接触,进而除去粉尘、硫氧化物以及烟气中其它可溶于水的杂质。
用于催化裂化烟气脱硫的文丘里管有两种,即高能文丘里管HEV 和喷射式文丘里管JEV 。
烟气再经联接弯头进入分离塔,联接弯头的作用是将经过洗涤之后的干净烟气和洗涤液输送至下游的分离塔。
分离塔是一个包含简单内件(除雾格栅和升气管)的开放型容器,主要作用是将干净气体从含有污染物的洗涤液中分离出来。
另外,还具有储存循环洗涤液的作用,洗涤液的液位通过对补充水的水量进行控制。
在催化裂化系统发生运行波动的时候(如大量跑催化剂),储存在分离塔中所储存的大量洗涤液可以保证整个洗涤系统中的循环液仍处于流体状态。
为节省空间,烟囱直接安装在分离桶的上方。
为了进一步提高可靠性,根据洗涤液的氯化物含量,烟囱由不锈钢或碳钢复合不锈钢制造。
排出的洗涤液进入净化处理部分。
首先在氧化罐进行曝气氧化处理,以降低废液的COD 含量;之后在澄清池中沉降,将其中催化剂颗粒沉淀,含有一定量液体的催化剂沉淀物经过滤脱水,以固体物(催化剂)运出厂外处理;最后通过冷却结晶装置将Na2SO4或者Na2SO3盐结晶出来,不但解决了高盐废水的排放问题,还可以产生副产品获得收益。
诺顿工程公司的VSS 技术以压降低和使用寿命长著称
2.2贝尔格公司(Belco )EDV 技术
EDV
湿法洗涤技术由美国贝尔格技术公司开发,包括烟气洗涤系统和排液
AIR
BLOWER
处理系统两部分。
该技术采用模块化组合,其吸收系统包括激冷和吸收模块、滤清模块、水珠分离器等几个部分,这几部分均设置在一座塔内。
烟气进入洗涤塔后,在激冷区达到降温饱和,并除去气体中较大的颗粒;在吸收区,随后与专用喷嘴喷出的吸收液逆向接触,脱去SO2。
微细颗粒和微细水珠在喷嘴上方的滤清元件中被清除,净化的烟气进入液滴分离器进行气液分离。
分离液滴后的清洁气体通过上部的烟囱排入大气,吸收剂溶液循环使用,为防止催化剂积累,装置运行中将排出部分洗涤液进入排出液处理系统。
EDV湿法烟气洗涤系统的工艺采用分层式的烟气净化处理程序,具有广泛的使用业绩。
2.3 ExxonMobil公司WGS技术(哈曼公司)
该工艺主要包括两部分:湿法气体洗涤装置(WGSR)和净化处理装置(PTU)。
使用碱性溶液作为吸收剂(洗涤液)。
烟气首先进入WGSR,并在其中脱除颗粒和SOx。
WGSR主要包括一个文丘里管和分离塔。
吸收剂与烟气同向进入文丘里管,吸收过程发生在文丘里管湍流部分,催化剂颗粒在咽喉段被捕捉,用缓冲溶液洗涤除去;SOx在咽喉段和扩径段被吸收,生成亚硫酸钠及硫酸钠。
气液混合物进入分离塔中,实现清洁气体与脏吸收剂液体分离。
分离塔中的脱夹带设施具有高效、低堵塞、低压力降的特点,将气体夹带的吸收剂液体脱除。
清洁气体通过分离器上部的烟囱排入大气。
吸收剂溶液循环使用,为防止催化剂积累,装置运行中将排出部分洗涤液进入洗涤液处理装置。
1974年世界第一套催化烟气脱硫装置在Exxon炼油厂,之后一段时间只在该技术的原有拥有者的Exxon炼油厂内建成几套,其中仅1990年代投产的就有
7套。
但是目前埃克森美孚,康菲石油,壳牌,BP,墨西哥石油公司等炼油厂均有多套烟气脱硫装置在运行。
1993年-2002年WGS的技术由诺顿公司完成全部的设计、升级、维护改扩建。
2003-2005年由诺顿公司帮助Exxon公司培训Hamon 公司。
Exxon公司现把WGS技术授权由Hamon公司做PDP,Hamon公司的湿气洗涤工艺(WGS)如图所示。
Hamon排出液处理系统与Belco洗涤液处理装置流程基本相同。
排出的洗涤液在澄清池中沉降,将其中催化剂颗粒沉淀,含有一定量液体的催化剂沉淀物经过滤脱水,固体物(催化剂)运出厂外填埋。
澄清池分离的澄清液约含5%的可溶解盐(主要是硫酸钠),排到后处理设施(PTU),经过pH值调节混合器、氧化塔(含盐污水排放),用空气氧化法降低其COD,氧化处理后排液进入污水处理场进一步生化处理。