SYT6717-2008油管和套管内涂层技术条件
石油化工设备和管道涂料防腐蚀技术规范

G=δρAα / m
式中 G 涂料的计算使用量(g) δ 一道漆膜的厚度( μm ) α 涂装道数(道) ρ 涂料的密度(g/cm3) A 涂履面积( m2 ) m 涂料固体百分含量
(二)、表面处理 1、 钢材表面的锈蚀等级,分为下列四级:
A级— 全面地覆盖着氧化皮而几乎没有铁锈的钢材表面; B级— 己发生锈蚀,且部分氧化皮已经剥落的钢材表面; C级— 氧化皮己因锈蚀而剥落或可以刮除,且有少量点蚀的钢材表面; D级— 氧化皮己因锈蚀而全面剥离,且已普遍发生点蚀的钢材表面。
续表
涂料
涂料性 能和用途
种类
酚醛 树脂 涂料
耐 烃类溶剂
√
溶 脂、酮类溶剂 ×
剂 氯化溶剂
×
耐潮湿
√
耐水
√
常温
√
≤100
√
耐温 (℃)
101~200
×
201~350 ×
351~500 ×
耐候性
○
附着力
√
沥青涂 料
× × × √ √ √ × × × × × ○
醇酸 树脂 涂料
○ × × ○ × √ √ × × × √ √
2、 钢材表面的除锈等级,分为下列四级:
St2— 彻底的手工和动力工具除锈钢材表面无可见的油脂和污垢,且没有 附着不牢的氧化皮、铁锈和油漆涂层等附着物。 St3— 非常彻底的手工和动力工具除锈钢材表面无可见的油脂和污垢,且 没有附着不牢的氧化皮、铁锈和油漆涂层等附着物,除锈应比St2更为彻 底,底材显露部分的表面应具有金属光泽。 Sat2— 彻底的喷射或抛射除锈钢材表面无可见的油脂和污垢,且氧化皮、 铁锈和油漆涂层等附着物已基本清除,其残留物应是牢固附着的。 Sat2. 5— 非常彻底的喷射或抛射除锈钢材表面无可见的油脂、污垢、氧 化皮、铁锈和油漆涂层等附着物,任何残留的痕迹应仅是点状或条纹状 的轻微色斑。
管道涂漆和绝热检修技术标准

管道涂漆和绝热检修技术标准l. 管道及其绝热保护层表面的涂漆颜色标志,应按《首钢集团涂装颜色标准》规定进行,涂料应有制造厂合格证明书。
2.如果不涂漆、要刷色标。
3.涂漆前应清除被涂表面的铁锈、焊渣、毛刺、油水等污物。
4.管道涂漆的种类、层数等应符合设计要求,并参照涂料产品说明书进行施工。
一般应用防锈漆打底,调和漆罩面。
5.现场涂漆可用用刷涂或喷涂法施工。
涂层应均匀,不得漏涂。
涂刷色环时,要求间距均匀,宽度一致。
6.现场涂漆应在其自然干燥,多层涂刷的前后间隔时间,应保证漆膜干燥,涂层末经充分干燥,不得进行下一工序施工。
7.涂层质量应符合下列要求7.1涂层均匀,颜色一致。
7.2涂膜附着牢固,无剥落、皱纹、气泡、针孔等缺陷。
7.3涂层完整,无损坏、无漏涂。
管道绝热1.绝热层施工应在试压及涂漆合格后进行。
施工前,管道外表面应保持清洁干燥。
绝热材料的种类、规格、性能应符合设计及环保要求。
2.非水平管道的绝热层施工应自下而上进行。
防潮层、保护层搭接时,其宽度应为30~ 5Omm。
3.绝热层同层的预制管壳应错缝,内、外层盖缝,外层的水平接缝应在侧面。
预制管壳缝隙一般应小于:热保温 5mm,冷保温 2mm。
缝隙应用胶泥填充密实。
每个预制管壳最少应用两道镀锌铁丝或箍带捆扎,不得采用螺旋形捆扎。
4.绝热层用的毡、席材料应与绝热表面紧贴,但不得填塞伴热管与主管之间的加热空间。
绝热层毡、席的环缝和纵缝接头间不得有空隙,其捆扎的镀锌铁丝或箍带间距为150~2OOmm。
疏松的毡席制品应分层施工,并扎紧。
5.阀门或法兰处的绝热施工,当有热紧或冷紧要求时,应在管道热、冷紧完毕后进行。
绝热层结构应易于拆装。
法兰一侧应留有螺栓长度加 25mm的空隙。
阀门的绝热层应不妨碍填料的更换。
6. 冷保温管道和地沟内的热保温管道应有防潮层,防潮层的施工应在干燥的绝热层上。
防潮层在管道连接支管及金属件上的施工范围应由绝热层边缘向外延伸展出15Omm或至垫木处,并予以封闭。
确认继续有效石油天然气行业标准汇总表

SY/T 0520-2008
原油粘度测定旋转粘度计平衡法
22
SY/T 0521-2008
原油析蜡点测定显微观测法
23
SY/T 0522-2008
原油析蜡点测定 旋转粘度计法
24
SY/T 0523-2008
油田水处理过滤器
25
SY/T 0525.2-1993
石油储罐回转接头
26
SY/T 0528-2008
16
SY/T 0080-2008
油气田柴油机发电站设计规范
17
SY/T 0083-2008
除油罐设计规范
18
SY/T 0094-1999
管道防腐层阴极剥离试验方法(粘 结电解槽法)
19
SY/T 0448-2008
油气田油气处理用钢制容器施工技 术规范
20
SY/T 0516-2008
绝缘接头与绝缘法兰技术规范
43
SY/T 5363-1997
含油气层系划分
44
SY/T 5366-2000
油田开发井取心资料技术要求
45
SY/T 5379-1991
钻井液切力计技术条件
46
SY/T 5387-2000
常规油藏试采地质技术要求
47
SY/T 5390-1991
钻井液腐蚀性能检测方法钻杆腐 蚀环法
48
SY/T 5398-1991
油气田及管道腐蚀与防护工程基本 词汇
6
SY/T 0045-2008
原油电脱水设计规范
7
SY/T 0062-2000
管道防腐层针入度试验方法
8
SY/T 0063-1999
管道防腐层检漏试验方法
SYT6717-2008油管和套管内涂层技术条件

1油管和套管内涂层技术条件1、范围本标准规定了油管、套管非金属内涂层的结构、技术要求、涂层涂敷、质量检验、标志、贮存、装卸与运输等内容。
本标准适用于符合GB/T 19830 中外径为φ26.67mm~φ114.30㎜(1.050in ~41/2in)的各种类型、规格的油管和外径为φ114.30mm~φ508.00㎜(41/2in~20in)的各种类型、规格的套管内涂层。
采用本标准非金属内涂层的油管、套管,推荐在井液pH值为3~13,温度不高于150℃的工况下长期使用。
2、规范性引用标准下列标准中的条款通过本标准的引用而成为本标准的条款。
凡是注日期的引用标准,其随后所有的修改单(不包括勘误的内容)或修订版均不适用于本标准,然而,鼓励根据本标准达成协议的各方研究是否可使用这些标准的最新版本。
凡是不注日期的引用标准,其最新版本适用于本标准。
GBZ 1 工业企业设计卫生标准GB/T 1727 漆膜一般制备方法GB/T 7692 涂装作业安全规程涂漆前处理工艺及其通风净化GB/T 8923 涂装前钢材表面锈蚀等级和除锈等级GB 12348 工业企业厂界噪声标准GB/T 19830 石油天然气工业油气井套管或油管用钢管(GB/T 19830 -2005, ISO 11960-2001,IDT)SY/T 0063 管道防腐层检漏试验方法(SY/T 0063-1999,eqv ASTM G62:1992)SY/T 0315 钢制管道单层溶解环氧粉末外涂层技术规范SY/T 5199 套管、油管和管线管用螺纹脂(SY/T 5199-1997,neq API RP5A3)API RP 5C1 套管、油管的维护和使用推荐做法ASTM D 714 色漆起泡程度的测定NACE TM 0384 干膜厚度小于10mil*的钢管内涂层漏点检验3、术语3.1液体涂层由一层底层和一层面层或一层底层两层面层组成。
3.2 粉末涂层面层为粉末,底层按照涂料厂家推荐可以为液体、粉末或不使用。
成品油管套管短节完工检验作业指导书
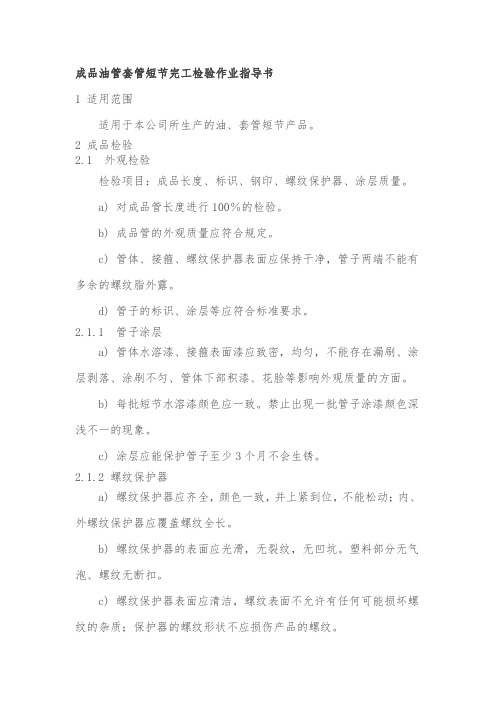
成品油管套管短节完工检验作业指导书1 适用范围适用于本公司所生产的油、套管短节产品。
2 成品检验2.1 外观检验检验项目:成品长度、标识、钢印、螺纹保护器、涂层质量。
a) 对成品管长度进行100%的检验。
b) 成品管的外观质量应符合规定。
c) 管体、接箍、螺纹保护器表面应保持干净,管子两端不能有多余的螺纹脂外露。
d) 管子的标识、涂层等应符合标准要求。
2.1.1 管子涂层a) 管体水溶漆、接箍表面漆应致密,均匀,不能存在漏刷、涂层剥落、涂刷不匀、管体下部积漆、花脸等影响外观质量的方面。
b) 每批短节水溶漆颜色应一致。
禁止出现一批管子涂漆颜色深浅不一的现象。
c) 涂层应能保护管子至少3个月不会生锈。
2.1.2 螺纹保护器a) 螺纹保护器应齐全,颜色一致,并上紧到位,不能松动;内、外螺纹保护器应覆盖螺纹全长。
b) 螺纹保护器的表面应光滑,无裂纹,无凹坑。
塑料部分无气泡、螺纹无断扣。
c) 螺纹保护器表面应清洁,螺纹表面不允许有任何可能损坏螺纹的杂质;保护器的螺纹形状不应损伤产品的螺纹。
d) 螺纹保护器的材料不应含有能够引起螺纹腐蚀或促使螺纹保护器粘结螺纹的成分,并不得与所有的螺纹脂起化学反应。
能达到适用于-46~66℃的服役温度并储存至少一年的要求e)螺纹保护器的设计、材料和机械强度应能使螺纹隔绝脏物和水并保护螺纹和管端在正常装卸和运输过程中不受损。
2.1.3 标识a) 产品标识应清晰、准确、规范、美观,不得存在歪扭、模糊、标识内容不清等影响外观的现象。
b) 管子标记形式详见工艺卡。
c) 在管子接箍端不大于0.6m的距离,环绕管子漆印色带,在接箍整个外表面上涂漆,包括相应的色带。
管体和接箍的色带要清晰、规范、美观,不能粗细不一,歪扭模糊。
d) 管体和接箍的钢级色标应符合标准的规定。
用卷尺对成品短节的长度进行100%的检验。
短节长度符合表2的要求。
管道内涂层作业线技术资料-76-508

思远工程安装有限责任公司技术管理文件管道内涂层作业线技术资料胜利油田思远工程安装有限责任公司2007年5月胜利油田思远工程安装有限责任公司技术管理文件目录1、钢管内涂层作业线使用说明1.1、作业线总体说明1.2、内喷砂除锈作业装置使用说明1.3、内吹扫作业装置使用说明1.4、内喷涂作业装置使用说明1.5、控制系统使用说明2、钢管内涂层作业线各岗位技术控制规范3、钢管内涂层作业线供电电缆规格4、易换件明细4.1、喷砂胶管(专用)4.2、喷嘴(专用)1、钢管内涂层作业线使用说明1.1、作业线总体说明1.1.1、作业线的用途本作业线可实现对钢管内壁进行喷砂清理作业,对喷砂清理后的钢管进行压缩空气吹扫,使钢管内表面干净、洁净、无污染物,之后对钢管内壁进行高速旋涂,使钢管内表面形成一层均匀的涂层薄膜,变频技术的应用使作业线操作简单、方便,生产过程中控制质量更加方便,产品各工序质量稳定、可靠。
1.1.2、主要技术参数1.1.2.1、作业线适应管径φ76-φ508mm L:9-12 M(内喷砂除锈作业时要求各钢管长度一致)1.1.2.2、除锈质量:清洁度:Sa2.5级锚纹深度:25-70μm除锈质量:GB/T8923-1998(涂装前钢材表面锈蚀等级和除锈等级)吹扫质量:管内表面无粉尘涂敷质量:内涂层表面均匀一致、光亮,无明显流淌痕迹;符合标准。
1.1.3、内喷砂及内吹扫采用集中收集旋风+布袋式除尘器处理方式,粉尘排放<120mg/m3。
1.1.4、作业线耗气量 P=1.0 MPa Q=55 m 3/min1.1.5、作业线装机总容量:135KW1.1.6、作业线工艺流程:1.1.7、作业线的组成钢管内喷涂作业线由三大部分组成:1)钢管内喷砂除锈装置;2)钢管内吹扫装置;3)钢管内喷涂装置。
1.1.8、作业线特点:1)各装置采用平行布置及运行方式,占地面积小,操作简单、方便。
2)各装置单独作业,质量控制方便。
API SPEC 5CT 第7版《套管及油管规范》简化版
石油管材用水溶漆技术要求
一、用途:水溶漆主要用于金属表面,具有防腐、固化快干、附着力强等特点。
二、厂商资质:1.材料制造商需通过ISo9001国际质量体系认证,且在有效期内。
2.材料制造商需具有危险化学品生产的安全生产许可证,且在有效期内。
3.产品必须是环境标志产品。
4.产品通过国家涂料产品质量监督检验中心鉴定。
三、种类:水溶漆(水性漆),稀释剂为水;四、颜色:黑色、棕色等;五、技术指标:1.漆膜耐冲击力符合GB/T6739《涂膜硬度铅笔测试法》的规定;2.漆膜耐冲击性符合GB/T1732《漆膜耐冲击测定法》的规定;3.漆膜耐汽油等化学试剂性符合GB/T9274《色漆和清漆耐液体介质的测定》的规定;4.漆膜耐温热性符合GB/T1740《漆膜耐湿热测定法》的规定;5.漆膜耐候性符合GB/T1767《水泥胶砂强度检验方法》的规定;6.液体粘度符合GB/T1723《涂料粘度测定法》要求;7.漆膜表干时间≤0.3小时,实干时间〈24小时;8.防腐蚀,抗露天暴晒,耐海水腐蚀,一年内金属涂层不出现锈蚀或卷边;9.材料无毒性和刺激性小,抗挥发性好;10.涂-4杯粘度(25°)控制25~35S;11.用200目滤网应无杂质;六、包装:1.产品应装于清洁、干燥、密封、内无机械杂质的容器内;2.产品名称、成分、稀释剂、合格证书、使用说明、有效期等资料齐全;七、检验在交货前,卖方应对货物质量、规格、性能、数量等进行全面的检验,并出具一份证明货物符合合同规定要求的检验证书,检验证书是付款时必要的文件组成部分,但不作为有关质量、规格、数量的最终检验。
一、用途:油漆主要用于金属表面,具有识别、固化快干、附着力强等特点。
二、资质:1.材料制造商需通过IS09001国际质量体系认证,且在有效期内。
2.材料制造商需具有危险化学品生产的安全生产许可证,且在有效期内。
3.产品必须是环境标志产品。
4.产品通过国家涂料产品质量监督检验中心鉴定。
三、种类:油漆,稀释剂为醇酸稀料;四、颜色:白色、红色、绿色、黄色、棕色等;五、技术指标:1.漆膜耐冲击力符合GBb6739《涂膜硬度铅笔测试法》的规定;2.漆膜耐冲击性符合GBb1732《漆膜耐冲击测定法》的规定;3.漆膜耐汽油等化学试剂性符合GB/T9274《色漆和清漆耐液体介质的测定》的规定;4.漆膜耐温热性符合GB/T1740《漆膜耐湿热测定法》的规定;5.漆膜耐候性符合GB/T1767《水泥胶砂强度检验方法》的规定;6.漆膜表干时间0.3小时,实干时间1小时左右。
油套管主要技术标准、检测项目与尺寸公差范围
紧密距
管段至消失点总长度
L4±
接箍
外径
W
最小接箍
长度
NL
接箍镗孔
直径
Q-0
接箍镗孔
深度
q+0.79-0
管体
直径
D
S1
P1
4 1/2
±
3
±
0
±
8
0
±
≥
12.7
5
0
±
≥
5 1/2
3
±
≥
6 5/8
8
0
±
≥
7
8
±
≥
7 5/8
±
0
±
≥
11.0
9 5/8
3
8
±
≥
10 3/4
±
≥
11 3/4
±
13 3/8
3
±
3
管体加厚外径D4
规格3 1/2 ~ 4管子:+2.78mm
-0.75%Dmm
4
管体壁厚t
-12.5%,即≥87.5%名义壁厚
5
管体直度
全长;弦高≤0.20%L;管端:下移量≤3.18mm(直尺长度≥1.83m)
6
接箍外径W
油管:±1%W; P110及以下钢级套管:±1%W;但不超过±
7
接箍长度N
≥名义长度
±
±
0
±
±
±
≥123.82
2 7/8
±
±
≥
3 1/2
±
±
≥
4
±
±
≥
4 1/2
±
±
≥
EU
管线管油管和套管的主要技术要求
管线管、油管和套管的主要技术要求A 目前国内外广泛使用的油气输送钢管采用的标准目前国内外广泛使用的油气输送钢管采用的标准有:(1)美国石油学会的API SPEC 5L《管线管规范》;(2)国际标准ISO 3183—1、2、3《石油天然气输送钢管交货技术条件》;(3)对于一些重要的长输管线,根据具体的使用环境都有自己的补充采购技术条件。
B 在API油气输送钢管标准中钢管的分类及其主要区别按照API SPEC 5L的规定,输送钢管分为PLSl和PLS2两个产品级别,对这两类产品规定了不同的技术条件。
其主要区别是:相对于PLS1、PLS2级别对碳当量、断裂韧性、最大屈服强度和最大抗拉强度规定了强度要求。
对硫、磷等有害元素的控制也更加严格:无缝管的无损检验成为强制要求。
对质保书必须填写的内容及试验完成后可追溯性成为强制要求。
C 在IS0油气输送钢管标准中钢管的分级及其主要区别在ISO 3183油气输送钢管标准中,钢管按照质量要求之间的差异,共分为A、B、C三部分,也被称为A、B、C三级要求。
其主要区别是:在ISO 3183一1A级标准要求中制定了与API SPEC 5L的规定相当的基本质量要求,这些主要的质量要求是通用的;在ISO 3183—2B级标准要求中除基本要求之外附加了有关韧性和无损检验方面的要求;还有某些特殊用途,例如酸性环境、海洋条件及低温条件等对钢管的质量和试验有着非常严格的要求,这些主要反映在IS0 3183_3C级标准要求中。
D 油气输送管道对钢的主要性能要求油气输送管道对钢的主要性能要求包括:(1)强度一般的油气输送管道都是根据钢材的屈服强度设计的。
采用屈服强度较高的钢制管,可以提高管道工作压力,获得较好的经济效益:因此.管道用钢的屈服强度已经从最初的碳素钢逐步发展起来,20世纪40年代为)X42一X52钢级.60年代末达到X60一x70钢级。
现已正式生产和正式使用屈服强度已达到更高的X80~X100钢级。
- 1、下载文档前请自行甄别文档内容的完整性,平台不提供额外的编辑、内容补充、找答案等附加服务。
- 2、"仅部分预览"的文档,不可在线预览部分如存在完整性等问题,可反馈申请退款(可完整预览的文档不适用该条件!)。
- 3、如文档侵犯您的权益,请联系客服反馈,我们会尽快为您处理(人工客服工作时间:9:00-18:30)。
油管和套管内涂层技术条件1、范围本标准规定了油管、套管非金属内涂层的结构、技术要求、涂层涂敷、质量检验、标志、贮存、装卸与运输等内容。
本标准适用于符合GB/T 19830 中外径为φ26.67mm~φ114.30㎜(1.050in~41/2in)的各种类型、规格的油管和外径为φ114.30mm~φ508.00㎜(41/2in~20in)的各种类型、规格的套管内涂层。
采用本标准非金属内涂层的油管、套管,推荐在井液pH值为3~13,温度不高于150℃的工况下长期使用。
2、规范性引用标准下列标准中的条款通过本标准的引用而成为本标准的条款。
凡是注日期的引用标准,其随后所有的修改单(不包括勘误的内容)或修订版均不适用于本标准,然而,鼓励根据本标准达成协议的各方研究是否可使用这些标准的最新版本。
凡是不注日期的引用标准,其最新版本适用于本标准。
GBZ 1 工业企业设计卫生标准GB/T 1727 漆膜一般制备方法GB/T 7692 涂装作业安全规程涂漆前处理工艺及其通风净化GB/T 8923 涂装前钢材表面锈蚀等级和除锈等级GB 12348 工业企业厂界噪声标准GB/T 19830 石油天然气工业油气井套管或油管用钢管(GB/T 19830 -2005, ISO 11960-2001,IDT)SY/T 0063 管道防腐层检漏试验方法(SY/T 0063-1999,eqv ASTM G62:1992)SY/T 0315 钢制管道单层溶解环氧粉末外涂层技术规范SY/T 5199 套管、油管和管线管用螺纹脂(SY/T 5199-1997,neq API RP 5A3)API RP 5C1 套管、油管的维护和使用推荐做法ASTM D 714 色漆起泡程度的测定NACE TM 0384 干膜厚度小于10mil*的钢管内涂层漏点检验3、术语3.1液体涂层由一层底层和一层面层或一层底层两层面层组成。
3.2 粉末涂层面层为粉末,底层按照涂料厂家推荐可以为液体、粉末或不使用。
4、技术要求4.1油管、套管内的图层的技术要求符合表1的规定。
4.2油管、套管内表面应全部涂覆,外螺纹端部和接箍接箍内中间部位螺纹涂覆范围由用户和涂层加工厂协商确定。
4.3 油管、套管外表应采用中性透明防腐涂料或用户要求的其它表面防腐涂料进行防护,要求光滑均匀,不起皮脱落。
表1 油管、套管涂层的技术要求5、涂层涂敷5.1 内表面预处理5.1.1 涂敷前应彻底清理螺纹及管体内表面的油脂和污垢等附着物。
5.1.2 应在室温和空气相对湿度小于90%的条件下进行喷砂除锈处理,除锈等级应达到GB/T 8923规定的Sa 21/2~3级的要求,锚纹深度印大道25μm~76μm。
油管、套管内表面应无目视可见的裂纹、蚀坑和毛刺等管体缺欠。
5.1.3 喷砂处理后,应将油管、套管内表面附着的灰尘及磨料清理干净。
5.2 底层和面层的涂敷5.2.1 为防止涂敷前油管、套管内表面氧化、受潮、生锈或二次污染,经喷砂处理过的油管、套管至底层喷涂的间隔时间应符合表2的要求。
表2 喷砂除锈处理后的油管、套管至底漆喷涂的间隔时间要求5.2.2 底层和面层的涂敷宜在响度是对小于90%、温度10℃~35℃、通风两哈的环境中进行;当相对湿度大于90%时,应停止作业。
5.2.3 油管、套管通风后应严格按涂料使用说明送入烘烤炉内进行烘烤。
炉膛内温度误差应控制在±10℃以内。
5.2.4每次烘烤结束后至再次涂敷前的间隔时间不应超过24h。
5.3返工5.3.1超过表2规定的间隔时间的喷砂油管、套管,应重新进行喷砂处理。
5.3.2超过5.2.4规定的间隔时间的图层底的油管、套管和不合格的涂层油管、套管,应根据涂层性能采用的方法将涂层清理干净,重新涂敷。
6检验6.1油管、套管的入厂检验涂层加工厂应按照用户提供的货物清单对油管、套管的外观、规格以及数量等进行验收。
新油管、套管管体内表面应无棱角和毛刺。
不满足涂敷要求的旧油管、套管不能涂敷。
6.2 涂料的检验6.2.1 涂敷厂对每种牌(型)号的涂料,在使用前应由通过国家计量认证的检验机构对涂料进行检测。
涂料的涂层性能应满足表1的规定。
性能达不到规定要求的,不应使用。
6.2.2 涂料均应有出厂质量证明书、质量检测报告、使用说明书、出厂合格证等、6.2.3 涂料均应包装完好,标签标明涂料型号、生产日期、有效期等信息。
6.3 表面预处理的检验6.3.1喷砂处理后的油管、套管应用不小于100lm亮度的照明工具逐根进行表面喷砂质量的目视检验。
6.3.2 按GB/T 8923中相应的照片或标准进行目视比较检查,表面清洁度应达到Sa 21/2~3级的要求。
6.3.3 喷砂处理后的油管、套管内表面的锚纹深度宜采用锚纹深度测试仪和复制胶带测定,表面锚纹深度应达到25μm~76μm;每50根测量一次,每次检测一次。
6.4 涂敷过程的检验6.4.1 用不小于100lm亮度的照明工具从油管、套管两端逐根进行底、面层涂敷后的外观检验。
6.4.2 涂敷后的湿膜外观应无流淌、垂滴、气泡等可见缺陷。
6.4.3 用湿膜规检测底、面漆的湿膜厚度。
应对每班首根管子的湿膜厚度进行检测,以每5根检测一次。
在油管、套管外螺纹接头端相隔90°艰涩两点,并用湿膜规修复好监测出的涂层。
6.4.4 每班应至少检验一次相对湿度,气候突变时应每2h检测一次。
6.5 出厂检验6.5.1 总则:出厂检验应在涂层固化并冷却后进行。
所有内涂层油管、套管都要按6.5.2~6.5.3的要求检测,达不到质量指标的均应返工。
6.5.2逐根检测项目。
6.5.2.1 外观:用不小于100lm亮度的照明工具从油管、套管两端逐根进行目视检测,要求涂层干膜平整、光滑、无气泡、橘皮和流淌等可见缺陷。
6.5.2.2 厚度:采用涂层测量仪测量涂层厚度,应在距管端约100mm处涂层部位的同一截面上、相隔90°测四个点,测量的数值应符合表1规定的干膜厚度要求。
测量方法见附录A。
6.5.2.3 漏点:每根油管、套管在内涂层的全长范围内的漏点数量应符合表1的要求。
检测社设备、检测方法和校检周期按NACE TM 0384的规定执行。
6.5.3 抽样检测的项目。
6.5.3.1 同城附着力的检测:同城附着力应不低于B级。
每个合同至少检测一次,数量较大的合同每500根检测一次。
检测方法和质量判定见附录B。
6.5.3.2 高压釜试验:技术要求见表1,取样于试样方法见附录C。
超过3×105Kkg 的合同,每个合同试验一次。
6.6 型式试验6.6.1 型式试验项目:按表1的项目进行试验。
6.6.2 有下面情况之一是,进行型式试验。
a)产品进行鉴定时;b)主要设备、原材料、工艺有较大改变,影响产品性能时;c)根据预期服役条件需要进行适用性评价时;d)质量监督部门提出质量检验要求时。
7 标志、贮存、装卸、运输和防护7.1 漆印标记7.1.1 涂刷外防锈漆后进行产品标志,标记一律用白色油漆喷涂,字体一律采用宋体货客户要求,代号宜采用大写英文字母,数字采用阿拉伯数字,字样大小应与标记符号相同。
7.1.2 漆印标记的内容a)商标:涂层公司商标或公司名称;b)涂层厂生产编号;c)涂层类型d)其他用户要求。
7.1.3在油管、套管外表面任一端不小于610mm(24in)处漆印标志,但一批次的油管、套管的标记方向应一致。
7.2 贮存涂层油管、套管的贮存应当按API RK 5C1的规定执行。
7.3 装卸、运输油管、套管的装卸和运输应当按API RK 5C1的规定执行。
7.4 防护7.4.1 涂层油管、套管经成品检验合格后,应先清洁两端的螺纹部位,然后涂敷一层油管和套管用螺纹脂。
螺纹脂应符合SY/T 5199的要求,戴好防护帽.7.4.2 涂敷外防锈漆采用喷涂或刷涂方法,在油管、套管的外层涂敷一层中性透明防腐材料或用户要求的其他表面防腐涂料,外观要求光滑均匀,不起皮脱落。
7.4.3 油管套管在井场存放时,两端应带有保护帽,并将保护帽的方孔封上。
7.4.4 现场使用的垫杠应有足够的强度和刚度。
7.4.5 每层油管、套管均应使用楔子以防止滚动。
7.4.6 不应将铁撬杠或钢管等硬物直接插入油管、套管的内部移动油管、套管。
7.4.7 不应在存放油管、套管垛上放置重物。
7.4.8 涂层油管、套管的贮存过程中,不应接触可能对涂层造成损害的腐蚀介质。
8 卫生、安全与环境保护8.1 油管、套管内涂层涂敷过程中的劳动安全、卫生应符合GB/T 7692的管理规定。
8.2 在油管、套管的表面处理和喷涂生产过程中,各设备生产的噪声应符合GB 12348的有关规定。
8.3 在表面处理工序,空气中的粉尘含量应符合GBZ 1的有关规定。
8.4 作业线中所有旋转和运动机械均应有防护罩等安全保护措施。
8.5 喷涂区的电气设备应符合国家有关爆炸危险场所电气设备的安全规定。
电气设备应实施整体防爆,操作部分应有触电保护器。
9 质量证明文件交货时应提交下列资料:a)所有涂料的质量证明书、合格证;b)所有涂料内涂层生产过程中的质量检测报告及油管、套管内涂层的质检报告;c)内涂层生产质量证明书,内容应包括产品名称、生产编号、涂料名称及型号、涂层质量指标、技术负责人及质量负责人等;d)用户要求的其他技术资料。