生产线平衡概述(IE)
合集下载
IE生产线平衡的资料PPT资料37页

稼动率=投入工时/可供工时 *100% 计划停线工时=计划停线时间*人数 计划停线时间=无计划时间+换线时间+判停时间
上例中,若换线时间是15分钟,则计划停线工时为20人 *15min=300min=5H,则投入工时和稼动率为:
60H-5H=55H 稼动率=55H/60H=92%
2019/10/22
时间测试
分解动作时间量测,一般每个动作测量5 次为宜; 量测人员应站在作业员斜后面1米以外, 以能看清楚全部操作动作为准则; 测试中不能打扰作业员的正常操作和引 起作业员的紧张;
时间测量流程
作业内容
数据与信息记录
测试中判断作业员的速度水平,并作如 实记录,不可修改量测数据; 若有其他特殊情況,也应加以实录;
2019/10/22
6
相关的概念
概念6:平衡损失 平衡损失=(总工时-单件标准时间)*设定产能
时间
T1 T2 T3 T4 T5
等待时间
单个产品平衡损失 =等待时间之和
S1 S2 S3 S4 S5
工站
概念7:平衡率100%代表﹕ 1.工站之间无等待,前后产能一致﹔ 2.工站节拍相同,动作量相同(动作量是指工站中各种必要动
素的时间总量); 3.平衡损失时间为零; 4.设计效率最大化; 5.前后流程的设计可以更完善(如下图).
2019/10/22
7
相关的概念
(交叉流程)
(直通流程 1 ) (直通流程 2 )
概念8:高效率 1. 通常认为高效率就是:快速,简单&大规模 2. 我们认为沒有浪费的时候才是高效率的 操作效率=实际产量/设定产能*100% 整体工厂效率(OPE)=平衡率*稼动率*操作效率
上例中,若换线时间是15分钟,则计划停线工时为20人 *15min=300min=5H,则投入工时和稼动率为:
60H-5H=55H 稼动率=55H/60H=92%
2019/10/22
时间测试
分解动作时间量测,一般每个动作测量5 次为宜; 量测人员应站在作业员斜后面1米以外, 以能看清楚全部操作动作为准则; 测试中不能打扰作业员的正常操作和引 起作业员的紧张;
时间测量流程
作业内容
数据与信息记录
测试中判断作业员的速度水平,并作如 实记录,不可修改量测数据; 若有其他特殊情況,也应加以实录;
2019/10/22
6
相关的概念
概念6:平衡损失 平衡损失=(总工时-单件标准时间)*设定产能
时间
T1 T2 T3 T4 T5
等待时间
单个产品平衡损失 =等待时间之和
S1 S2 S3 S4 S5
工站
概念7:平衡率100%代表﹕ 1.工站之间无等待,前后产能一致﹔ 2.工站节拍相同,动作量相同(动作量是指工站中各种必要动
素的时间总量); 3.平衡损失时间为零; 4.设计效率最大化; 5.前后流程的设计可以更完善(如下图).
2019/10/22
7
相关的概念
(交叉流程)
(直通流程 1 ) (直通流程 2 )
概念8:高效率 1. 通常认为高效率就是:快速,简单&大规模 2. 我们认为沒有浪费的时候才是高效率的 操作效率=实际产量/设定产能*100% 整体工厂效率(OPE)=平衡率*稼动率*操作效率
现场IE改善案例分析--生产线平衡分析改善案例
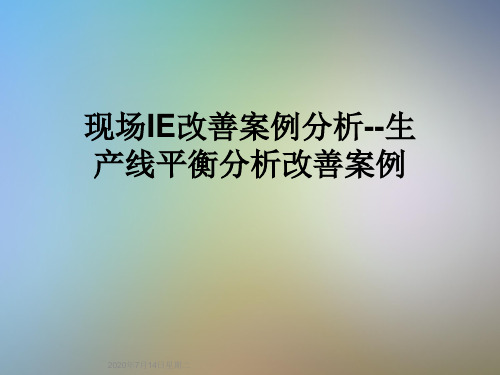
生产线平衡定义
对生产的全部工序进行均衡,调整作业 负荷和工作方式,消除工序不平衡和工 时浪费,实现“一个流”。
出料
入料
平衡生产线的意义
通过平衡生产线可以综合应用到程序分析、动作分析 、layout分析,搬动分析、时间分析等全部IE手法,提 高全员综合素质
在平衡的生产线基础上实现单元生产,提高生产应变 能力,对应市场变化实现柔性生产系统
(4) 4种增值的工作
站在客户的立场上,有四种增值的工作
1、使物料变形 2、组装 3、改变性能 4、部分包装
物料从进厂到出厂,只有不到 10% 的时间是增值的!
工序
符 号
内容
作业内容
分类
加工 作业
○
加工 作业
■产生附加价值的工序及作 业
卖得掉
检查
□
数量检查 ■虽然有必要,但需要进行 品质检查 改善的工序及作业
现场IE改善案例分析--生 产线平衡分析改善案例
2020年7月14日星期二
内容安排
一、线平衡定义 二、生产线平衡分析方法 三、B值、F值的定义与计算 四、线平衡案例分析
一、线平衡定义
生产线平衡定义
什么是生产线平衡
生产线平衡是指构成生产线各道工序所需的 时间处于平衡状态,作业人员的作业时间尽 可能的保持一致,从而消除各道工序间的时 间浪费,进而取得生产线平衡。
减少人手(1)
將工序3里的工作时 间分配至工序2﹑4 及5之內﹐从而工序 3里的人手可调配其 它生产线去
可行性﹕須工序 2﹐4及5內均有足夠 时间接受额外工作。
ቤተ መጻሕፍቲ ባይዱ
生产线平衡-例3﹕减少人手(2人)
降低线体速度,减少生产产量
工作時間
IE生产线平衡资料

详细描述
瓶颈工序分析的目的是找出生产线上存在瓶颈工序的原因,并采取措施对其进行 优化或调整,以提高整个生产线的平衡率和产能。针对瓶颈工序的优化措施可能 包括改进工艺流程、提高设备精度、增加人员培训等。
04
生产线平衡的优化方法
调整工序作业内容
总结词
通过合理分配作业内容,平衡各工序 的工作量,提高生产效率。
实现生产计划的高效执行,缩短产品从投入到产 出的时间,提高整体生产效率。
降低生产成本
通过优化生产流程和减少浪费, 降低原材料、能源和水等资源
的消耗。
减少生产过程中的设备和人 力成本,提高设备和人力资
源的利用效率。
提高生产效率可以降低单位产 品的成本,从而增加企业的市
场竞争力。
提升产品质量
01
生产线平衡有助于确保产品在生产过程中的稳定性和一致性, 减少不良品和次品率。
06
结论
生产线平衡的成果与收益
生产效率提升
质量稳定性增强
通过优化生产线布局和平衡各岗位工作量 ,显著提高了生产效率,缩短了生产周期 ,减少了在制品数量。
平衡的生产线减少了操作员之间的差异, 降低了产品缺陷率,提高了质量的稳定性 和一致性。
减少浪费
提高员工满意度
生产线平衡有助于减少生产过程中的等待 、空闲和搬运等浪费,降低了生产成本。
02
提高生产过程的可控制性和可预测性,及时发现和解决生产过
程中的问题。
通过优化生产流程和提高员工技能,提高产品质量的整体水平,
03
满足客户需求。
03
生产线平衡的评估指标
生产线平衡率
总结词
生产线平衡率是评估生产线平衡状态的重要指标,它反映了生产线上各工序作业时间的均衡程度。
瓶颈工序分析的目的是找出生产线上存在瓶颈工序的原因,并采取措施对其进行 优化或调整,以提高整个生产线的平衡率和产能。针对瓶颈工序的优化措施可能 包括改进工艺流程、提高设备精度、增加人员培训等。
04
生产线平衡的优化方法
调整工序作业内容
总结词
通过合理分配作业内容,平衡各工序 的工作量,提高生产效率。
实现生产计划的高效执行,缩短产品从投入到产 出的时间,提高整体生产效率。
降低生产成本
通过优化生产流程和减少浪费, 降低原材料、能源和水等资源
的消耗。
减少生产过程中的设备和人 力成本,提高设备和人力资
源的利用效率。
提高生产效率可以降低单位产 品的成本,从而增加企业的市
场竞争力。
提升产品质量
01
生产线平衡有助于确保产品在生产过程中的稳定性和一致性, 减少不良品和次品率。
06
结论
生产线平衡的成果与收益
生产效率提升
质量稳定性增强
通过优化生产线布局和平衡各岗位工作量 ,显著提高了生产效率,缩短了生产周期 ,减少了在制品数量。
平衡的生产线减少了操作员之间的差异, 降低了产品缺陷率,提高了质量的稳定性 和一致性。
减少浪费
提高员工满意度
生产线平衡有助于减少生产过程中的等待 、空闲和搬运等浪费,降低了生产成本。
02
提高生产过程的可控制性和可预测性,及时发现和解决生产过
程中的问题。
通过优化生产流程和提高员工技能,提高产品质量的整体水平,
03
满足客户需求。
03
生产线平衡的评估指标
生产线平衡率
总结词
生产线平衡率是评估生产线平衡状态的重要指标,它反映了生产线上各工序作业时间的均衡程度。
IE 系列培训教材(线体平衡)
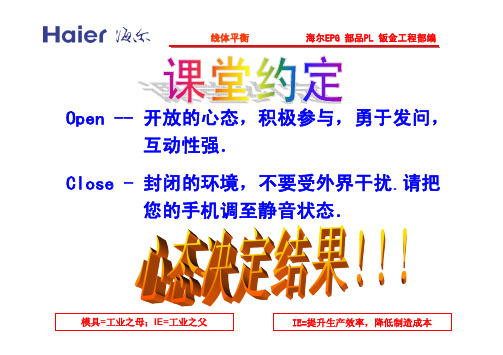
程序分析技巧 1. 通过5W1H系统地分析程序的组成是否合理和必要 2. “ECRS”四大原则: 取消(Eliminate):“完成了什么?是否必要?为什么?” 合並(Combine):“谁完成?何时完成?哪里?如何?” 重排(Rearrange):取消合并重排 简化(Simplify):确认必要简单方法/设備生产.
线体平衡
海尔EPG 部品PL 钣金工程部编
4.5 损失分析
1. 目的:计算分析生产中的所发生的损失,并加以停止. 2. 损失的种类: 平衡损失(流程排位所造成的损失) 操作损失(生产中异常及不良造成的损失) 稼动损失(计划停线损失) 总损失=稼动损失+平衡损失+操作损失
模具=工业之母;IE=工业之父
模具=工业之母;IE=工业之父
IE=提升生产效率,降低制造成本
线体平衡
海尔EPG 部品PL 钣金工程部编
三、相关的概念 概念5:实际产量 实际产量是可供时间内所产出的良品数 1)人均产能(UPPH)=实际产量/投入时间/人数 2)单机台产能=实际产量/投入时间/机台数
模具=工业之母;IE=工业之父
IE=提升生产效率,降低制造成本
线体平衡
海尔EPG 部品PL 钣金工程部编
时间测量流程 数据与信息记录 作业内容
测试中判断作业员的速度水平,并作如实记录,不可修改量测数 据; 若有其他特殊情况,也应加以实录;
数据整理和计算
测试完毕,对数据进行整理和计算,补充测量有怀疑或错漏的数 据; 计算可信度95%所需的样本数量,补测差异样本数量
数据分析与处理
对量测记录之所有数据进行分析,对比ST的差异程度,解决发 现的问题; 若分析发现标准时间制定不当,应及时修改,必要时调整制程.
线体平衡
海尔EPG 部品PL 钣金工程部编
4.5 损失分析
1. 目的:计算分析生产中的所发生的损失,并加以停止. 2. 损失的种类: 平衡损失(流程排位所造成的损失) 操作损失(生产中异常及不良造成的损失) 稼动损失(计划停线损失) 总损失=稼动损失+平衡损失+操作损失
模具=工业之母;IE=工业之父
模具=工业之母;IE=工业之父
IE=提升生产效率,降低制造成本
线体平衡
海尔EPG 部品PL 钣金工程部编
三、相关的概念 概念5:实际产量 实际产量是可供时间内所产出的良品数 1)人均产能(UPPH)=实际产量/投入时间/人数 2)单机台产能=实际产量/投入时间/机台数
模具=工业之母;IE=工业之父
IE=提升生产效率,降低制造成本
线体平衡
海尔EPG 部品PL 钣金工程部编
时间测量流程 数据与信息记录 作业内容
测试中判断作业员的速度水平,并作如实记录,不可修改量测数 据; 若有其他特殊情况,也应加以实录;
数据整理和计算
测试完毕,对数据进行整理和计算,补充测量有怀疑或错漏的数 据; 计算可信度95%所需的样本数量,补测差异样本数量
数据分析与处理
对量测记录之所有数据进行分析,对比ST的差异程度,解决发 现的问题; 若分析发现标准时间制定不当,应及时修改,必要时调整制程.
最新IE生产线平衡资料

IE生产线平衡资料
相关的概念
产出的速度取决于时间 最长的工站,称之瓶颈 瓶颈在哪里? 了解加工的过程
2020/10/22
2
相关的概念
概念1: 平衡率
用语衡量流程中各工站节拍符合度的一個综
合比值;
单件标准时间
平衡率= ----------------------100%
瓶颈时间工位数
时
T2
瓶颈时间
测试样本大小計算
山积表
山积表的使用: [图表生成方法]
山积表:将各分解动作时间,以叠加式直方图表现 的一种研究作业时间结构的手法.
样式:
產品xxx工時山積表
秒
10
8 6
0
0 1.5
1.5 0.5
1.5
10 2
1.5 2
10
0.5 1.3
2
10 3
0 4
4
4
6
1
3
1.5 3
2
2
3.5
3.5
2
2
2020/10/22
4
相关的概念
概念4:设定产能 设定产能(H) =3600(S)/瓶颈时间(S) 设定产能(班)=投入時間/瓶颈时间(S)
思考:1)为什么设定产能(班) =投入工时/总工时 总工时=瓶颈时间*作业人数
2)总工时 VS 单件标准时间
概念5:实际产量 实际产量是可供时间內所产出的良品数 1)人均产能=实际产量/投入时间/人数 2)单机台产能=实际产量/投入时间/机台数
时间测试
分解动作时间量测,一般每个动作测量5 次为宜; ❖ 量测人员应站在作业员斜后面1米以外, 以能看清楚全部操作动作为准则; 测试中不能打扰作业员的正常操作和引 起作业员的紧张;
相关的概念
产出的速度取决于时间 最长的工站,称之瓶颈 瓶颈在哪里? 了解加工的过程
2020/10/22
2
相关的概念
概念1: 平衡率
用语衡量流程中各工站节拍符合度的一個综
合比值;
单件标准时间
平衡率= ----------------------100%
瓶颈时间工位数
时
T2
瓶颈时间
测试样本大小計算
山积表
山积表的使用: [图表生成方法]
山积表:将各分解动作时间,以叠加式直方图表现 的一种研究作业时间结构的手法.
样式:
產品xxx工時山積表
秒
10
8 6
0
0 1.5
1.5 0.5
1.5
10 2
1.5 2
10
0.5 1.3
2
10 3
0 4
4
4
6
1
3
1.5 3
2
2
3.5
3.5
2
2
2020/10/22
4
相关的概念
概念4:设定产能 设定产能(H) =3600(S)/瓶颈时间(S) 设定产能(班)=投入時間/瓶颈时间(S)
思考:1)为什么设定产能(班) =投入工时/总工时 总工时=瓶颈时间*作业人数
2)总工时 VS 单件标准时间
概念5:实际产量 实际产量是可供时间內所产出的良品数 1)人均产能=实际产量/投入时间/人数 2)单机台产能=实际产量/投入时间/机台数
时间测试
分解动作时间量测,一般每个动作测量5 次为宜; ❖ 量测人员应站在作业员斜后面1米以外, 以能看清楚全部操作动作为准则; 测试中不能打扰作业员的正常操作和引 起作业员的紧张;
生产线平衡分析与改善最全面的IE分析生产线平衡
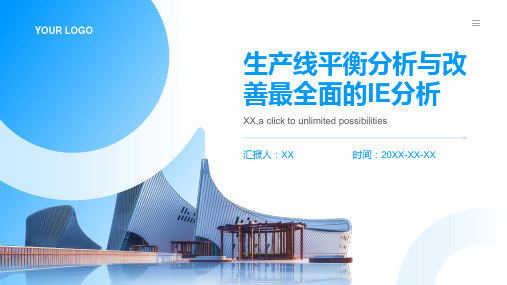
最全面的IE分 析生产线平衡 案例分析
PART 1
单击添加章节标题
P生A产R线T平2衡分析的概念和重要
性
生产线平衡分析的定义
定义:生产线平衡分析是指对生产线上的各个工 序进行平衡,使各工序的工作时间尽可能相近, 从而提高生产效率的过程。
目的:通过对生产线平衡进行分析,可以找出生 产过程中的瓶颈工序,优化生产流程,提高生产 效率,降低生产成本。
跨部门协作:加强各部门之间的沟通与协作,共同推进生产线平衡改善的实施和监控工作。
PIEA分R析T在5生产线平衡改善中的
Hale Waihona Puke 应用IE分析的基本概念和原则
IE分析的定义:工业工程分析, 旨在提高生产效率和降低生产成 本。
IE分析在生产线平衡改善中的应 用:通过分析生产线上的瓶颈、 浪费和不合理之处,提出改善方 案。
注意事项3:考虑人机配合 和作业节拍
注意事项1:分析前要明确 目标和范围
注意事项4:注意设备维护 和保养
PART 4
生产线平衡改善的策略和措施
生产线平衡改善的目标和原则
提高生产效率:通过优化生产线布局和作业分配,降低生产成本,提高产出效率。 降低不良品率:通过平衡生产线上的作业,减少生产过程中的波动和异常,降低不良品率。 提高员工满意度:通过合理分配工作量和减轻员工负担,提高员工的工作积极性和满意度。
生产线平衡分析的工具和技术
作业分析:确定每个作业步骤的时间和顺序,识别瓶颈和浪费。 工艺流程图:可视化生产线流程,找出潜在的改进点。 动作分析:研究工人操作,优化动作,提高效率。 生产计划与调度:合理安排生产计划,确保生产线的平衡。
生产线平衡分析的注意事项
注意事项2:充分了解生产 流程和工艺要求
基础IE知识概述

➢ 工具万能原则 ➢ 易于操作策略 ➢ 适当位置原则 ➢ 定点放置原则 ➢ 双手可及原则 ➢ 工序排列原则 ➢ 使用容器原则 ➢ 用坠送法原则 ➢ 近使用点原则 ➢ 避免担心原则
关于人体应用
➢ 环境舒适原则Байду номын сангаас
关于工具设 备
关于工作场 所利用
三、IE七大手法说明
防错法 动改法 流程法 五五法 人机法 双手法 抽查法
3 为什么润滑油不足
4
为什么不能充分吸 入呢
5
为什么轴受到异常 磨损呢
润滑油不足
因为油泵没有充分 吸入润滑油
油泵的轴受到异常磨损 松了
润滑油中混有 磨损的金属粉屑
短期解决对策
更换保险丝 增大油泵的
容量 更换油泵
更换油泵 在润滑油的入 口处装滤网
三、IE七大手法说明
防错法 动改法 流程法 五五法 人机法 双手法 抽查法
抽查法
试
板 固 检 检板板 板 耐
面 定 焊 焊底底 面 压
Q加1 C锡
1 、 2
2
Q C 1
Q C 2
高 度 测
测 试
试
F C T 测 试
打总
胶 、
检
装
隔
离
柱
装 箱
三、IE七大手法说明
防错法 动改法 流程法 五五法 人机法 双手法 抽查法
五五法
一、简述 所谓5X5W1H: 5W:WHIRE何处,什么地方,——空间 WHEN何时,在什么时候——时间 WHAT何者,是什么东西/事——生产对象 WHO何人,是什么人做/生产主体 WHY为何,为什么如此 1H:HOW如何,怎么做的。
三、IE七大手法说明
防错法 动改法 流程法 五五法 人机法 双手法 抽查法
精选IE工业工程生产线平衡课件
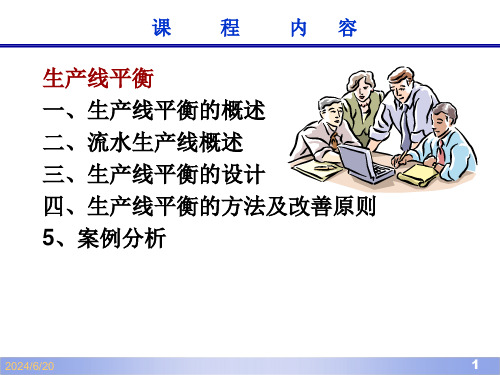
2.目的通过平衡生产线可以达到以下几个目的:⑴ 加快产品流动,减少生产周期。⑵ 消除工程瓶颈,提高作业效率,稳定产品质量,优化作业流程,减少单件产品的工时消耗,降低成本(等同提高人均产量)。⑶ 减少工序在制品,真正实现“一个流”。⑷ 在平衡的生产线基础上实现单元生产,提高生产应变能力,对应市场变化实现柔性生产系统。⑸ 通过平衡生产线可以综合应用程序分析、动作分析、布置分析,搬动分析、时间分析等工业工程方法,提高全员综合素质。
① 确定流水生产的节拍
当流水线的运输批量等于1的情况下,节拍按下式计算:式中 C——流水线节拍; Fe——计划期有效工作时间; N——计划期应完成的产量。
3、 单品种流水线平衡方法
三、流水生产线平衡的设计方法
若按批运输时,则流水线节拍为式中 Q——运输批量。
③生产线平衡率的计算:
若评估上述两方案,对瓶颈工序C进行动作分析的生产线平衡改善方案较增加作业资源的生产线平衡改善方案的效果为佳(无须增加一个工位)
④生产线平衡损失率的计算:
生产线平衡损失率计算公式如下:平衡损失率=(非加工时间总和)÷作业时间总和=∑LTi ÷(生产节拍×N)=1-生产线平衡率LTi---各作业资源非加工时间;N—作业资源数总和。 若以平衡图与生产线平衡损失率做比较,平衡损失率等于平衡图中阴影部分面积(非加工时间)除以平衡图的全部面积(作业时间总和)
G
7
E
H
11
E
I
3
G、H
总时间
66
解:
阶位法的工作步骤如下
① 作图表示装配工艺过程中各作业元素的先后关系,并标明每项作业元素的时间。 ② 从作业元素先后关系图找出每项作业元素的后续作业元素,计算它们的时间总和,即每项作业元素的阶位值。 ③ 按阶位值的大小,由大到小,将作业元素排队,制成作业元素阶位表。 ④ 从阶位值最高的作业元素开始,向工作地分配作业要素。每分配一项作业元素,计算一次在节拍时间内的剩余时间。若剩余时间足够安排另一项作业元素,从阶位表中找出阶位值次高的作业元素分给该工作地。若剩余时间不够安排其它作业元素,就向下一个工作地分配,直到全部作业要素都被安排入工作地为止。
- 1、下载文档前请自行甄别文档内容的完整性,平台不提供额外的编辑、内容补充、找答案等附加服务。
- 2、"仅部分预览"的文档,不可在线预览部分如存在完整性等问题,可反馈申请退款(可完整预览的文档不适用该条件!)。
- 3、如文档侵犯您的权益,请联系客服反馈,我们会尽快为您处理(人工客服工作时间:9:00-18:30)。
生产线平衡--简述
1.生产线平衡的定义 2.生产线平衡的计算 3.提高生产线平衡的方法
1.生产线平衡的定义
• 生产线平衡:即对生产的全部工序进行平均化,调
整作业负荷,以使各作业时间尽可能相近的技术手段与方 法。 • 目的:是消除作业间不平衡的效率损失以及生产过剩。
2.生产线平衡的计算
• 生产线的平衡计算式 :
• 平衡率=(各工序时间总和/(工站数*CT))*100% • CT即节拍,指最长工序(瓶颈工序)时间。
以某条流水线为例,共7个工序,瓶颈工序为工序6:。
如上: 平衡率=T/CT*7=53.64/(8.95*7)=85%
ห้องสมุดไป่ตู้
3.怎样提高生产线平衡
• 1、对瓶颈工序进行作业改善,优化瓶颈工序的作业方法,操作动作, 以及改善工装夹具等。 • 2、运用ECRS原则改善生产流程。
取消(Eliminate):该工作或动作完成了什么?是否必要或可以取消? 合并(Combine): 如果工作或动作不能取消,则考虑能否可与其他工作合 并。 重排(Rearrange): 对工作的顺序进行重新排列。 简化(Simplify); 指工作内容和步骤的简化,亦指动作的简化,能量的节 省。
• 3、增加全能工来平衡流水,只要平衡率提高了,人均产量就等于提 高了,单位产品成本也随之下降。
以上 谢谢观阅!
IE工程师:
1.生产线平衡的定义 2.生产线平衡的计算 3.提高生产线平衡的方法
1.生产线平衡的定义
• 生产线平衡:即对生产的全部工序进行平均化,调
整作业负荷,以使各作业时间尽可能相近的技术手段与方 法。 • 目的:是消除作业间不平衡的效率损失以及生产过剩。
2.生产线平衡的计算
• 生产线的平衡计算式 :
• 平衡率=(各工序时间总和/(工站数*CT))*100% • CT即节拍,指最长工序(瓶颈工序)时间。
以某条流水线为例,共7个工序,瓶颈工序为工序6:。
如上: 平衡率=T/CT*7=53.64/(8.95*7)=85%
ห้องสมุดไป่ตู้
3.怎样提高生产线平衡
• 1、对瓶颈工序进行作业改善,优化瓶颈工序的作业方法,操作动作, 以及改善工装夹具等。 • 2、运用ECRS原则改善生产流程。
取消(Eliminate):该工作或动作完成了什么?是否必要或可以取消? 合并(Combine): 如果工作或动作不能取消,则考虑能否可与其他工作合 并。 重排(Rearrange): 对工作的顺序进行重新排列。 简化(Simplify); 指工作内容和步骤的简化,亦指动作的简化,能量的节 省。
• 3、增加全能工来平衡流水,只要平衡率提高了,人均产量就等于提 高了,单位产品成本也随之下降。
以上 谢谢观阅!
IE工程师: