钢烧结矿烧结指标及冶金性能的影响
210978870_烧结负压对烧结矿质量的影响

管理及其他M anagement and other烧结负压对烧结矿质量的影响王 彬1,汪世峰1,丁广伟1,杨爱民2,3,4,5,6,李 杰2,3,4,5,6摘要:中国钢铁行业存在烧结矿质量低下的问题,因此提高烧结矿质量对于钢铁行业发展起到重要作用。
烧结生产的工艺流程复杂,需要优化和调整的细节较多,如烧结负压、燃料配比、料层高度等因素均对烧结矿的质量产生较大影响。
为了进一步提高烧结矿的质量和成品率,本文展开了一系列相关研究。
研究结果表明,随着烧结负压的增加,烧结时间变快、废气温度降低、烧结矿成品率、<10mm粒级指标变差、烧结矿转鼓强度变差。
因此在实际生产中要合理控制烧结负压,从而得到理想指标的烧结矿,这对于改善烧结矿产质量和优化烧结工艺具有重要的指导作用。
关键词:烧结矿;烧结负压;烧结矿性能;烧结优化随着经济社会的发展,我国对于钢铁的需求迅速增加,钢铁的质量问题变得尤为重要,烧结矿作为钢铁主要原材料,如何提高烧结矿的质量成为了核心问题。
在烧结生产的过程中,主要的工艺参数为:料层高度、混合料水分、燃料配比、烧结负压,这些参数对烧结矿的质量产生直接影响。
印度金尔尔钢铁公司曾在烧结料层上开展了烧结负压在900mm~1700mm水柱范围内的烧结杯试验。
试验结果表明:在1300mm水柱负压下,烧结机的利用系数达到最大。
我国首钢、武钢和梅山等厂也曾对抽风机转子进行了改造,通过提高抽风负压,实验也取得了不同程度的效果。
Xinying Ren等利用转鼓指数的变化对烧结矿质量的影响进行了研究,利用机器学习相关算法预测了烧结转鼓强度,通过大量数据试验建立了有关转鼓指数的预测模型。
张兰泉在《烧结过程大风量高负压问题的探讨》中探讨了负压对烧结矿的厚度以及生产率的影响,指出风机负压提高,适宜的料层厚度会随之提高;料层的厚度增加生产率得到提高,但达到一定程度后生产率则会有所降低。
周江虹在《烧结过程风量合理分布实验研究》中通过烧结杯模拟,改变烧结负压,在最优的方案下提高了烧结成品率、利用系数以及垂直烧结速度。
不同碱度对烧结矿冶金性能的影响

不同碱度对烧结矿冶金性能的影响摘要:在龙钢公司3#配比基础上,保持FeO在9.5±0.5范围内,通过碱度的变化,对烧结矿低温粉化指数、高温还原指数等方面进行研究。
低温粉化率在2.1±0.05左右最佳,高温还原率在2.0±0.05最佳。
综合评定当FeO稳定在9.5±0.5,碱度在2.0±0.05时烧结矿冶金性能最好。
关键词:碱度低温粉化高温还原冶金性能1前言近年来随着内外的试验研究及现有的烧结规律研究表明,当碱度升高达到一定值时,其冶金性能达到最好状态,当碱度再次升高时,其冶金性能状态有所下滑。
近年来,随着烧结技术的提升,对生产质量的要求也越来越高,合适的碱度变化成为烧结研究的主要问题。
本文主要研究碱度含量对烧结矿冶金性能的影响,通过合理的控制碱度来降低成本,稳定烧结矿质量,进而保证高炉的顺利运行,从而为公司降本增产提供有利的指导性参考。
2实验原料主要原料包括超特、巴混、纽曼及生灰、返矿、固体燃料等。
实验原料均取自烧结原料现场,所有原料均科学随机取样并且一次性取够八次实验所需的样。
实验原料化学成分见表1。
3实验方法与方案3.1实验方法实验参数混合料水分为7.0±0.2%,烧结杯为Ø300X1000mm,混合料质量为110kg,混合时间为300s,烧结料层厚度为800mm,烧结点火温度为1200℃,点火时间为30s,烧结点火负压为12KPa,铺地料5kg。
实验将烧结废气开始下降定为烧结终点,采用人工布料,烧结过程用计算机控制。
3.2试验方案设计五组烧结杯试验,其中FeO均控制为9.5±0.5,碱度含量分别为2.1±0.05,2.0±0.05,1.9±0.05,1.8±0.05,1.7±0.05,分别对应方案1-5,对烧结矿冶金性能进行研究;表1 含铁原料化学成分/%名称烧损率TFeFeOSiO2CaOMgOAl2O3矿1956.45.88.08.083.2矿23.9662.6.724.62.02.061.58矿35.6154.4.489.25.09.13.6矿44.5462.454.19.09.162.32矿5505002A.499.6.11.03.09.87矿B 2.559.85.5.34.22.59矿C -1.0963.226.623.44.434.11.08矿D 1.661.68.65.61.14.761.1矿E 7.0559.7.434.49.02.052.4矿F-1.862.7255.26.873.87.75矿G-1.8463.124.311.07.55.341.64表2 烧结矿主要成分/% 表3低温还原粉化、还原度指数/%实验方TFe%FeO%SiO2%CaO%MgO%Al2O3%案方案155.019.045.3411.122.002.18方案255.699.485.2910.471.822.04方案355.139.285.4510.561.852.18方案455.809.725.369.501.772.08方案556.329.095.209.111.712.186.3mm% 3.15mm%5mm%I%方案144.172.037.6961.332.08方案237.9770.836.4675.901.98方案337.5668.338.4673.061.94方案429.1165.78.7174.061.77方案536.7166.875.4571.861.754 试验结果分析4.1 碱度与低温粉化指数的关系图1碱度与低温粉化指数的关系图2碱度与高温还原指数关系图由表3和图1可看知,以1.75为基准,碱度提高到1.77时RDI+3.15从66.87%降到 65.7%,降低了1.17%主要原因是由于碱度的增加,SiO2的含量相对较低,作为粘结相的硅酸盐的含量相对较低,妨碍了铁矿石内部间的连晶作用,致使烧结矿抗膨胀粉化能力减弱,进而使烧结矿低温粉化指数降低;当碱度增加到2.08时,低温粉化指数RDI+3.15增加到72.03%,主要是因为碱度的增加,使铁酸钙和硅酸盐都增加,铁酸钙和硅酸盐相结合抑制了低温还原过程中体积的膨胀,进而使粉化指数显著提高;当碱度在2.1左右出现最大值,烧结矿碱度与低温还原粉化指数在部分区域内呈明显的增长关系。
烧结质量指标
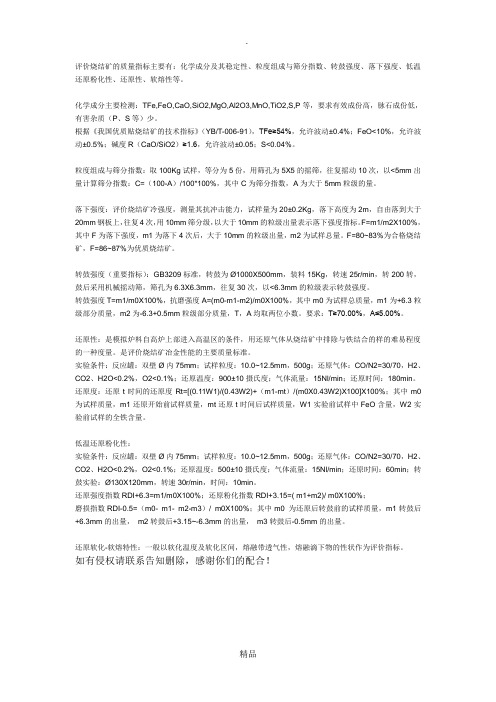
.评价烧结矿的质量指标主要有:化学成分及其稳定性、粒度组成与筛分指数、转鼓强度、落下强度、低温还原粉化性、还原性、软熔性等。
化学成分主要检测:TFe,FeO,CaO,SiO2,MgO,Al2O3,MnO,TiO2,S,P等,要求有效成份高,脉石成份低,有害杂质(P、S等)少。
根据《我国优质贴烧结矿的技术指标》(YB/T-006-91),TFe≥54%,允许波动±0.4%;FeO<10%,允许波动±0.5%;碱度R(CaO/SiO2)≥1.6,允许波动±0.05;S<0.04%。
粒度组成与筛分指数:取100Kg试样,等分为5份,用筛孔为5X5的摇筛,往复摇动10次,以<5mm出量计算筛分指数:C=(100-A)/100*100%,其中C为筛分指数,A为大于5mm粒级的量。
落下强度:评价烧结矿冷强度,测量其抗冲击能力,试样量为20±0.2Kg,落下高度为2m,自由落到大于20mm钢板上,往复4次,用10mm筛分级,以大于10mm的粒级出量表示落下强度指标。
F=m1/m2X100%,其中F为落下强度,m1为落下4次后,大于10mm的粒级出量,m2为试样总量。
F=80~83%为合格烧结矿,F=86~87%为优质烧结矿。
转鼓强度(重要指标):GB3209标准,转鼓为Ø1000X500mm,装料15Kg,转速25r/min,转200转,鼓后采用机械摇动筛,筛孔为6.3X6.3mm,往复30次,以<6.3mm的粒级表示转鼓强度。
转鼓强度T=m1/m0X100%,抗磨强度A=(m0-m1-m2)/m0X100%,其中m0为试样总质量,m1为+6.3粒级部分质量,m2为-6.3+0.5mm粒级部分质量,T,A均取两位小数。
要求:T≥70.00%,A≤5.00%。
还原性:是模拟炉料自高炉上部进入高温区的条件,用还原气体从烧结矿中排除与铁结合的样的难易程度的一种度量。
烧结矿质量及其对高炉冶炼主要操作指标的影响

高炉主要操作指标
利用系数
燃料比
1.228
813
1.998
559.4
2.412
535.0
2.153
496.7
2.28
478.0
0.788
793.2
0.463
878.0
1.519
556.9
1.719
547.6
2.147
538.0
0.472
986
1.234
610
2.04
601
2.20
550
近几年有不少钢铁企业采用低品位、大渣量的做法,主观愿望想降低成本,实际适得其反,造
2 烧结矿质量的内涵和价值
烧结矿的质量由化学成分、物理性能和冶金性能三部分组成,它们三者间的关系是:化学成分是基 础,物理性能是保证,冶金性能是关键。
2.1 烧结矿的主要化学成分及其价值
烧结矿的主要化学成分包括品位和SiO2、碱度、MgO、Al2O3和FeO,还有S、P、Ka2O、ZnO和Cl等有 害元素。 2.1.1 含铁品位对烧结矿质量的价值
900℃还原/% 80.75 80.10 77.12 85.51 81.56 79.12
烧结生产之所以要配MgO是为了满足高炉炼铁炉渣流动性、脱硫和脱碱(K2O+Na2O)的需 求。
2.1.6 FeO含量对烧结矿质量的价值 FeO含量也是烧结矿的一个重要内容,FeO含量的高低直接影响烧结矿的强度、粒度和冶金
烧结矿冶金性能的有关参数

烧结矿冶金性能的有关参数一、低温还原粉化性能(1)RDI-3.15=30%时RDI+6.3一般在41%左右这个范围的低温还原粉化性能有一定恶化,但仍处在可维护中、小高炉冶炼所允许的范围之内。
(2)RDI-3.15=20—25%时RDI+6.3一般在60—50%这个范围基本能满足较高冶强的顺行要求。
(3)RDI-3.15=17—19%时RDI+6.3一般在67—63%这个范围的低温还原粉化性能应该说非常好,非常有利于改善高炉块状带的透气性,但要注意对还原性能的检验,还原度不能低于75%。
(4)RD=I-0.5一般在6—7%范围一般烧结矿中磁铁矿和硅酸铁含量的增加,有利于改善低温粉化性能,同时随着FeO%含量的相应提高(从6%逐步提高到12%以下)也有利于低温还原粉化性能的改善。
二、烧结矿的还原性能还原度RI(900℃时)在75—80%左右时,应该是比较好的还原性能指标。
凡还原度的降低都不利于降低高炉冶炼燃料比,一般情况下,当采取减少低温粉化率措施的同时,还原度相应降低,它往往也与难还原的磁铁矿和硅酸铁含量的增加有关,FeO%>10%RG,还原度也会出现明显的降低趋势。
三、烧结矿荷重软化性能一般烧结矿碱度在1.85±0.1条件下,软化的开始温度在1200—1220℃,软化终了温度在1320—1330℃,软化温度区间在110—120℃,凡软化温度区间(T2—T1)变小,对降低高炉软熔带的透气性是有利的。
反之,如果软化开始温度↓软化温度区间自然变大,不利于软熔带透气性的改善,一般影响烧结矿荷重软化性能,主要有两个因素:一是烧结矿的还原性能:烧结矿还原性能的改善有利于烧结矿在升温过程中形成液相的温度升高,导致烧结矿的软化开始温度升高。
二是烧结矿中脉石的熔点,在烧结矿碱度基本不变的条件下,烧结矿中脉石的熔点不变,R2低熔点低,R2高熔点高。
烧结矿质量对高炉冶炼的影响 精品

吉林电子信息职业技术学院毕业论文烧结矿质量对高炉冶炼的影响摘要烧结矿是高炉炼铁生产的主要原料之一,烧结矿的性能和质量直接影响高炉冶炼的顺行、操作制度和技术经济指标。
本论文通过对烧结矿的还原,滴落实验,验证不同粒度的半焦、无烟煤代替焦粉作燃料的铁矿烧结技术的比较优势。
以及改变其粒度等方面对烧结进行分析、研究。
本项研究内容包括:原、燃料的物理化学性质、燃料的性能及反应性、烧结矿质量指标的评价;在不同原料配比条件下改变燃料粒度的烧结实验;烧结矿的物理化学性能和冶金性能等检测;对燃料种类和配比对烧结矿生产指标、烧结矿化学成分、矿物组成、还原性能、还原粉化性能、软熔滴落性能的影响进行评价,实验结果及其分析。
实验结果证明:半焦在>5mm粒级控制在15%的粒度下是很好的烧结燃料。
无烟煤相对做烧结燃料效果不好;<3mm粒级控制在70%左右为宜。
关键词:烧结矿,无烟煤,焦粉,半焦,矿物组成,烧结矿冶金性能,改变粒度I吉林电子信息职业技术学院毕业论文目录第一章绪论·············································································································· - 6 -1.1烧结生产的目的·············································································································- 6 -1.2烧结用原料条件·············································································································- 7 -1.3燃料的粒度 ······················································································································- 7 -1.4燃料的基本性质·············································································································- 8 -1.4.1燃料的工业分析、元素分析 ......................................................................... - 8 -1.4.2燃料的灰成分和灰熔点·······························································································- 10 -第二章烧结的作用·································································································- 11 -2.1烧结矿的作用 ···············································································································- 11 -2.2烧结机的作用 ···············································································································- 12 -2.3烧结矿中MgO 作用机理 ····························································································- 12 -第三章烧结生成工艺及生产的工艺流程·························································- 13 -3.1烧结生成工艺 ···············································································································- 13 -3.2烧结生产的工艺流程··································································································- 13 -3.2.1烧结原料的准备 ..................................................................................... - 14 -3.2.2配料与混合............................................................................................... - 14 -3.2.3烧结生产 ................................................................................................... - 15 -第四章烧结矿对高炉冶炼的影响·····································································- 18 -4.1烧结矿指标对高炉冶炼过程的影响·······································································- 18 -4.2烧结矿指标和冶金性能的影响因素·······································································- 20 -第五章结论·········································································································- 24 -参考文献·················································································································- 25 -致谢·································································································错误!未定义书签。
FeO对烧结矿产质量的影响
FeO 对烧结矿产质量的影响王志远 何明杰(杭州钢铁集团公司炼铁厂 杭州 310022)摘 要:在实验室内,研究了在杭钢当前用料情况下,FeO 含量对烧结利用系数、成品率和转鼓强度及其冶金性能的影响,并确定烧结合适的FeO 含量。
关键词:Fe O;用系数;转鼓强度;冶金性能0 前言FeO 是影响烧结产量、烧结矿强度和冶金性能等指标的重要因素,也是评价烧结矿质量的重要指标之一,对高炉冶炼的技术经济指标具有较大的影响。
因此,研究烧结矿适宜FeO 含量对稳定烧结生产,保证高炉顺行具有重要意义。
烧结矿FeO 含量不仅受配碳量、混合料水分、料层厚度、返矿配加量等因素的交互影响,还与原料结构、烧结矿碱度、MgO 含量等因素有关,是多个变量共同作用的结果。
本文利用烧结杯试验系统,通过调整焦粉配比,研究了烧结矿FeO 对烧结矿产量、强度和冶金性能影响。
1 试验原料试验用原燃料取自杭钢炼铁厂烧结车间。
各种原燃料的化学成分、配比见表1。
烧结矿化学成分为:TFe55.01%、SiO 2为5.80、R2为1.80。
2 试验方法与方案2.1 试验方法烧结试验在300mm @700m m 烧结杯中进行,点火负压为7kPa ,烧结负压14kpa ,点火时间90s ,混合料水分7.5%,在圆筒混合机内制粒5min 。
固定料层650mm ,铺底料厚度30mm 。
烧结矿化学成分由杭钢炼铁厂原料化验室检测,冶金性能按国家标准的还原炉和熔滴炉检测。
2.2 试验方案烧结的化学成分在TFe55.01%左右,SiO 2为5.80,R2为1.80,混匀矿配比固定,通过调整焦粉配比,来调整烧结矿中FeO 的含量。
其中烧结矿中FeO 含量的选择参照在杭钢原料条件下可能达到的范围,通过烧结杯得到的FeO 含量为6.49%、7.77%、8.51%、9.07%、9.21%、10.58%、10.94%等七个试验用烧结矿,以此考察FeO 对烧结产量、烧结矿强度和冶金性能的影响。
烧结知识问答
烧结高级1. 简述铁矿粉烧结的意义和作用。
答:铁矿粉烧结具有如下重要意义和作用:⑴通过烧结,可为高炉提供化学成分稳定、粒度均匀、还原性好、冶金性能高的优质烧结矿,为高炉优质、高产、低耗、长寿创造良好的条件;⑵可去除硫、锌等有害杂质;⑶可利用工业生产的废弃物,如高炉炉尘、炼钢炉尘、轧钢皮、硫酸渣、钢渣等;⑷可回收有色金属和稀有、稀土金属。
2. 烧结矿质量对高炉冶炼有哪些方面影响?答:⑴烧结矿品位每升高1%高炉焦比降低2%产量提高3%⑵烧结矿FeO变动,影响高炉焦比和产量,同时影响烧结矿的还原性和软容性能;⑶烧结矿碱度稳定是稳定高炉炉况的重要条件之一;⑷烧结矿强度对高炉冶炼有较大影响。
入炉矿含粉率升高,将导致高炉焦比升高、产量降低;⑸烧结矿还原性对高炉的影响,主要体现在烧结矿FeO含量,FeO高低影响着高炉冶炼的直接还原度(rd )。
直接还原度增加,焦比升高、产量降低;⑹烧结矿的低温还原粉化率(RDI)升高,高炉产量下降、焦比升高;⑺烧结矿荷重软化温度升高,高炉的透气性改善,产量提高;⑻熔滴性能直接影响高炉内熔滴带的位置和厚度,影响Si、Mn等元素的直接还原,从而影响生铁的成分和高炉技术经济指标。
3. 简述烧结方法的分类。
答:按照烧结设备和供风方式的不同,烧结方法可分为:⑴鼓风烧结:烧结锅、平地吹。
属于小型厂的土法烧结,逐渐被淘汰。
⑵抽风烧结:①连续式:带式烧结机和环式烧结机等;②间歇式:固定式烧结机,如盘式烧结机和箱式烧结机;移动式烧结机,如步进式烧结机。
⑶在烟气中烧结:回转窑烧结和悬浮烧结。
目前普遍采用的是带式烧结机。
4. 烧结生产工艺流程包括那几大系统?各系统的主要作用是什么?答:⑴原料准备系统:包括含铁原料的中和混匀、燃料破碎和熔剂破碎等;⑵配料系统:将匀料。
燃料、熔剂、循环返矿等按一定比例进行配合;⑶混匀制粒系统:将配合后的物料进行混匀并造球,保证成分均匀并具备一定的粒度组成,满足烧结过程和烧结矿质量的需要;⑷烧结系统:将准备好的烧结料铺在烧结台车上,点火、抽风烧结。
18烧结矿冶金性能对其质量和高炉指标的影响
T10
1091 1092 1085
T40
1134 1247 1227
ΔT
43 155 142
Ts
1267 1435 1448
Td
1333 1450 1464
ΔT
66 15 16
ΔPm·9.8pa
S值(Kpa℃)
33.63 11.76 21.64
102 130 188
济钢
75.1
74.6
42.3
- - - 63.96 39.5
主要参考文献
序言:
烧结矿的冶金性能包括 900℃还原性(RI)、500℃低温还原粉化性 能( RDI )、荷重还原软化性能( TBS 、 TBE 、Δ TB )和熔融滴落性能 (Ts、Td、ΔT、ΔPm、S值)。这四项性能中900还原性是基本性能, 它不仅直接影响煤气利用率和燃料比,同时由于还原程度的不同,还 影响其还原强度(RDI)和软熔性能。500℃低温还原性能是反映烧结 矿在高炉上部还原强度的,它是高炉上部透气性的限制性环节。在高 炉冶炼进程中,高炉上部的阻力损失约占总阻力损失的 15%。烧结矿 的荷重还原软化性能是反映其在高炉炉身下部和炉腰部分软化带透气 性的,这部分的透气阻力约占高炉总阻力损失的25% 。熔融滴落性能 是烧结矿冶金性能最重要的部分,因为它约占高炉总阻力损失的60%, 是高炉下部透气性的限制性环节,要保持高炉长期顺行稳定,必须十 分重视含铁原料在熔融带的透气阻力。烧结矿在高炉的块状带、软化 带和熔融滴落带不同部位的性状和透气阻力的变化(详见示图)决定 着高炉内不同部位顺行和稳定,因此研究和分析清楚冶金性能对烧结 矿质量和高炉主要操作指标的影响是十分重要和必要的。
烧结矿的荷重还原软化性能是指其装入高炉后,随炉料下降,温度上升不断被 还原,到达炉身下部和炉腰部位,烧结矿表现出体积开始收缩即开始软化(TBS) 和 软 化 终 了 ( TBE ) 的 特 性 , 高 碱 度 烧 结 矿 的 TBS 应 ≥ 1100 ℃ , 软 化 温 度 区 间 (ΔTB= TBE -TBS)应≤150℃,烧结矿开始软化温度的高低取决于其矿物组成和 气孔结构强度〔1〕开始软化温度的变化往往是气孔结构强度起主导作用的结果, 这就是说,软化终了温度往往是矿物组成起主导作用。由高炉内各带透气阻力的 示图可知,软化带的阻力损失约占25%,是反映炉料在炉身下部和炉腰部位顺行状 况的,当烧结矿的开始软化温度低于950℃,软化温度区间>300℃时,高炉必须会 产生严重的悬料,因此为了保持高炉顺行稳定,烧结矿应具有良好的荷重还原软 化性能。关于荷重还原性能对高炉主要操作指标的影响 ,意大利的皮昂比诺 ( Piombimo )公司 4# 高炉曾于 1980 年做过统计,含铁原料的 TBS 由 1285 ℃提高到 1335℃,高炉的透气性ΔP由5.2kpa降低到4.75kpa(下降8.7%),产量提高了 16%, 日本神户公司的加古川厂和新日铁的广畑厂均通过改善酸性球团矿的软熔性能有 效地改善了高炉操作指标〔7〕。
《钢铁冶金》第二章铁矿烧结
四、燃料燃烧和传热
❖ 烧结料中固体碳的燃烧为形成粘结所必须的液相和进行 各种反应提供了必要的条件(温度、气氛)。烧结过程所需 要的热量的80~90%为燃料燃烧供给。然而燃料在烧结混 合料中所占比例很小,按重量计仅3~5%,按体积计约 10%。在碳量少,分布稀疏的条件下,要使燃料迅速而 充分地燃烧,必须供给过量的空气,空气过剩系数达 1.4~1.5或更高。
❖ 随着烧结过程的进行,燃烧层向下移动,烧结矿层增厚, 自动蓄热作用愈显著,愈到下层燃烧温度愈高。这就出现 上层温度不足(一般为1150℃左右),液相不多,强度较低, 返矿较多;而下部温度过高,液相多,过熔,强度虽高而 还原性差,即上下烧结矿质量不均的现象。为改善这种状 况,提出了具有不同配碳量的双层或多层烧结的方法。即 上层含碳量应高于平均含碳量,而下层应低于平均含碳量, 以保证上下层温度均匀,质量一致。而且节省燃料。苏联 采用分层烧结某矿粉,下部含碳量低1.2%,节省燃料10%, 联邦德国某厂使用双层烧结,节省燃料15%,日本用此法 节省燃料10%。
❖ 随着烧结料层的增厚,自动蓄热量增,有利于降低燃料 消耗,但随着料层厚度增加,蓄热量的增加逐渐减少,所 以燃耗降低幅度也减小。当烧结矿层形成一个稳定的蓄热 层后,则蓄热量将不再增加,燃耗也不再降低。因此,从 热量利用角度看,厚料层烧结是有利的,但不是愈厚愈好, 在一定的条件下,存在着一个界限料层高度。同时料层高 度的进一步增加还受到透气性的限制。
❖ 在某一层中可能同时进行几种反应,而一种反应又可能在几层中进行。 下面对各过程分别进行研究和讨论。
二、烧结料中水分的蒸发、分解和凝结
❖ 任何粉料在空气中总含有一定水分,烧结料也不例外。除 了各种原料本身带来和吸收大气水分外,在混合时为使矿 粉成球,提高料层透气性,常外加一定量的水,使混合料 中含水达7~8%。这种水叫游离水或吸附水。100℃即可 大量蒸发除去。如用褐铁矿烧结,则还含有较多结晶水 (化合水)。需要在200~300℃才开始分解放出,若含有粘 土 质 高 岭 土 矿 物 (Al2O3·2SiO2·H2O) 则 需 要 在 400~600℃ 才能分解,甚至900~1000℃才能去尽。
- 1、下载文档前请自行甄别文档内容的完整性,平台不提供额外的编辑、内容补充、找答案等附加服务。
- 2、"仅部分预览"的文档,不可在线预览部分如存在完整性等问题,可反馈申请退款(可完整预览的文档不适用该条件!)。
- 3、如文档侵犯您的权益,请联系客服反馈,我们会尽快为您处理(人工客服工作时间:9:00-18:30)。
<0.5
2.21 1.87
降MgO前 降MgO后
25.89 26.42
由表10可见,降低MgO前、后,成品烧结矿的粒度组成没有明显变化。烧结矿的 低温还原粉化指标得到改善,其中>6.3mm部分由80.77%提高到89.07%,>3.15mm 部分由92.49%提高到95.47%,而<0.5mm部分则由2.21%降至1.87%。(注:烧结矿低 温粉化指标均为烧结矿喷洒CaCl2溶液后指标) 5结论 在试验室不加菱镁石,即烧结矿中MgO含量降低后: 5.1烧结混合料的指标稍有变差的趋势,具体为混合料中>3mm百分数稍有减少,平均 粒径相差不多。 5.2试验期烧结矿成品率增加了0.85%,利用系数略有提高,ISO转鼓指数变化不大, 略有提高。 5.3成品烧结矿品位提高0.86%。 5.4成品烧结矿低温粉化指标变好,其中>6.3mm部分增加了1.59%,>3.15mm部分增 加了O.86%,<0.5mm部分减少了0.72%。 而在生产实践中: 5.5降低菱镁石的配比后,成品烧结矿中的MgO由2.O%降至1.8%,烧结机的利用系 数有所增加,烧结矿的转鼓强度升高。 5.6烧结矿中的MgO含量降低后,烧结矿的低温还原粉化指标得到改善。
O.33%。
3.3
MgO含量对成品烧结矿粒度的影响 不同MgO含量的烧结矿粒度组成见表5。
表5 试验编号 加MgO 不加MgO
>40 5.65 3.28
不同条件成品烧结矿粒度组成(mm%)
40~25
22.25 25.29
25~16
30.53 31.3l
16~10
25.57 24.17
10"--5 20.20 15.96
表8
时间 降MgO前 降M90后
>3.15mm部分提
二烧车间降低烧结矿中MgO前、后的配料比
一次配料 大磁
32 30
二次配料 石灰石
5.5 6
鞍千
27 27
巴西
16 16
尘泥
5 7
生石灰
6 5.5
镁石
2.4 2.O
焦粉
1.6 1.7
生石灰
2.2 1.9
焦粉
1.6 1.6
表9
时间 降MgO前 降MgO后 利用系数t/m2h
表10
时间
>40
降MgO前、后烧结矿的成品粒度组成及低温还原粉化
成品粒度组成(%)
40~25
15.56 15.9l
低温还原粉化(%)
10~5
20.79 20.97
25~16
15.60 15.62
16~10
17.15 16.87
<5
4.46 4.35
>6.3 80.77 89.07
>3.15 92.49 95.47
MgO含量对鞍钢烧结矿烧结指标 及冶金性能的影响
于素荣刘艳辉李跃民
(鞍钢股份炼铁总厂)
摘要本文分析了MgO含量对烧结指标及冶金性能的影响,分析结果表明,MgO含量降低后, 烧结成品率和利用系数提高,成品烧结矿的转鼓强度略有提高,低温还原粉化指标改善。这个结论 在生产实践中也得到了证实。
关键词MgO
转鼓强度
由表9可见,降低MgO后烧结机的利用系数增加了O.103 t/m2.h,ISO转鼓指数升 高了0.64%,主要是因为MgO降低,减少了MgC03分解吸热,改变了烧结时液相的熔 化温度,使熔化温度降低,烧结矿化比较充分,颗粒之间黏结的强度较高,所以表现为 烧结矿的转鼓强度增加,烧结机的利用系数增加。而筛分指数随MgO含量的降低没有 明显的变化。 从理论上讲,降低MgO后,相对熔剂量减少,烧结矿的TFe品位应该升高。但是 由于后期生产中将2%高品位的大磁换成了低品位的尘泥,致使烧结矿的品位略有降低。
低温还原粉化
1
前言
由于以前鞍钢高炉渣中镁含量较高,用于生产水泥时影响了水泥质量,如果高炉适 当降低炉渣中氧化镁含量,将有利于改善这种情况。针对这一问题,鞍钢炼铁总厂研究 所以二烧车间现场生产原料条件为基础,在试验室中进行了加MgO与不加MgO两种 条件的烧结杯对比试验,以探讨MgO对该车间烧结生产指标和烧结矿冶金性能的影响。 2试验原、燃料条件和试验方法 2.1试验原、燃料条件 本试验采用二烧车间现场原、燃料条件。基准期配加MgO,试验期不加MgO,(鞍 钢烧结矿中的MgO均以菱镁石形式添加),其它条件保持不变。试验用原、燃料化学成 份见表1,试验配料比见表2。
垂烧速度
mm/min 19.32 19.54
一淤雯
表4
加MgO
试验条件\
不加MgO
烧成率
%
83.38 83.94
成品率
%
65.24 66.07
利用系数
t/m2.h 1.580 1.618
ISO转鼓,>6.3mm
%
64.67 65.00
燃耗
K卧
61.51 61.43
从表4数据可以看出,撤掉MgO后,垂直烧结速度变化不大,成品率稍有提高, 从基准期的65.24%提高到试验期的66.07%,提高了O.83%;利用系数略有提高,从 1.580Vmz.h提高到1.61 8ffm2.h,提高了O.038t/m2.h。ISO转鼓指数变化不大,提高了
MgO
O.57 O.25 0.35 O.15 2.37 2.37 41.83 1.93 O.60
Ig 0.84 0.7l 0.42 2.98 10.00 16.20 49.52 43.44 85.84
H20 9.8 9.6 10.0 7.8 0 O 0.6 1.2 15.0
表2
原料与配比 加MgO 不加MgO 齐大山
3.1
MgO含量对混合料的影响 不同试验条件下的烧结混合料指标见表3。
不同原料条件下混合料指标变化
>3 mm H20பைடு நூலகம்
i裳
表3
试验条件\
不加MgO 加MgO
平均粒径
mm 4.3l 4.27
静态料层阻力Pa
5m3/h 525 550 lOm3/h 1425 1450
%
59.57 57.05
%
7.3 7.4
57
表7
加MgO 不加MgO
不同条件成品烧结矿冶金性能指标,(%)
>6.3mm 51.77 53.36 >3.15mm 80.85 81.71 <O.5mm 5.28 4.56
从表7可以看出,混合料中撤掉菱镁石后,成品烧结矿的低温还原粉化强度提高, 其中>6.3mm部分从51.77%提高到53.36%,提高了1.59个百分点, 高了O.86个百分点;烧结矿的低温还原粉化率降低了0.72个百分点。 4生产实践 上世纪70年代,鞍钢成品烧结矿中MgO含量一直在2.3%~2.5%之间波动,为了 适应高炉生产的需要,2005年的4月份,二烧车间曾在保证烧结矿碱度和料层不变的 条件下,将MgO由原来的2.3%~2.5%降至2.1%,进而降至2.0%。 从2007年3月21日开始,二烧车间再次降低了烧结矿中MgO含量,即在保证其 他烧结条件不变的情况下,把镁石配比由2.4%降至2.O%,使烧结矿中的MgO含量由 原来的2.O%降至1.8%。生产具体配比见表8,烧结主要技术指标见表9,成品矿的粒 度组成及低温还原粉化见表10。
平均粒径
19.88 20.37
从表5看,撤掉MgO后,成品烧结矿粒度主要集中在中间三个粒级上。>40mm 粒级减少2.37个百分点,lO"..,5mm部分减少了4.24个百分点,平均粒径略有增大。
3.4
MgO含量对成品烧结矿化学成份的影响 不同原料条件下成品烧结矿化学成分见表6。
表6
TFe
不同条件成品烧结矿化学成份(计算值)
从表3可以看出,与基准期相比,在水分相近情况下,不加MgO(撤掉菱镁石) 混合料中大于3mm部分稍有减少,减少了2.52个百分点,混合料平均粒径变化不大, 仅减小了O.04mm,即减小了0.93%,混合料静态料层阻力变化不大。
3.2
MgO含量对烧结各项指标的影响 不同原料条件的烧结主要指标见表4。
不同原料条件下的烧结主要指标
32 32
不同原料条件的试验配料比
大磁
40 40
富矿
8 8
活性生石灰
2.5 2.5
生石灰
5.O 5.0
菱镁石
3.O O
石灰石
2.1 2.1
焦粉
4.2 4.2
返矿
18 18
2.2试验设备与试验方法
本试验在鞍钢炼铁总厂研究所试验室进行,烧结过程中烧结料层为550mm,点火 负压为8820Pa,点火时间为2min,点火结束后烧结负压调到10780Pa。 3试验结果与分析
表1
名称 弓浮 齐大山 大磁 富矿 活性生石灰 生石灰 菱镁石 石灰石 焦粉
TFe 68.70 67.50 66.46 63.88 0.69 0.69 1.25 0.56 0.20
试验用原、燃料化学成份(%)
FeO 27.18 19.18 28.2 O.7 Si02 3.80 3.93 6.37 3.34 3.35 3.35 3.07 1.89 7.20 CaO O.16 O.18 0.14 0.14 85.00 80.00 2.80 51.93 O.30
1.333 1.436
降MgO前、后的烧结主要技术经济指标
转鼓指数
%
80.70 81.34
筛分
%
4.39 4.35 TFe 57.87 57.41 Fe0 7.88 8.16 CaO 10.41 10.87
化学成分%
Si02 4.74 4.92 R 2.20 2.21
MgO
2.02 1.84
S 0.024 0.028
Si02 5.31 5.29 CaO lO.6l 10.57
%
MgO