机械加工工艺培训教材
机械加工工艺过程培训课件)
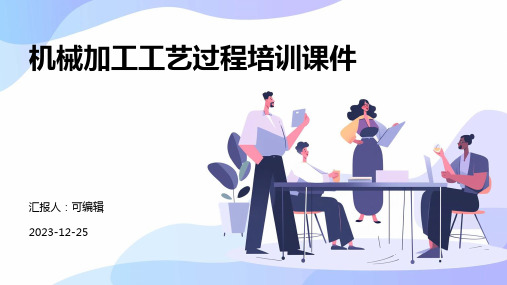
夹具设计应遵循“三化”原则,即标准化、系列化和通用化。设计时应充分考 虑工件的定位和夹紧要求,以提高加工精度和生产效率。同时,夹具的结构应 简单、紧凑,便于制造、装配、调整和使用。
量具与测量技术
量具的种类与选择
量具是用来测量各种几何参数的工具,如直尺、卡尺、千分尺、百分表等。选择合适的量具需要考虑测量精度、 测量范围和测量对象等因素。
氮化硼等也常用于某些特殊用途的刀具制造。
刀具的选择
选择合适的刀具材料需要考虑工件材料、加工要求和加工条件等因素。对于不同的加工 要求和工件材料,应选择相应的刀具材料、刀具几何参数、刀具结构等,以保证加工效
率和加工质量。
夹具设计
夹具的作用与组成
夹具是用来定位和夹紧工件的工艺装备,以确保工件在加工过程中保持正确的 位置。夹具的组成一般包括定位元件、夹紧装置、连接元件以及夹具体等。
争力具有重要意义。
THANKS
感谢观看
切削力的产生与切削 热
金属切削过程中,由于刀具与工件之 间的摩擦和挤压作用,产生了切削力 。切削力的主要作用是将多余的金属 材料从工件上切除,同时也产生了大 量的切削热。
刀具材料与选择
刀具材料的种类
刀具材料主要包括高速钢、硬质合金、陶瓷和超硬材料等。高速钢是一种具有高硬度、 高耐磨性和高耐热性的合金钢,常用于制造复杂刀具;硬质合金是由碳化钨和钴等材料 组成的合金,具有高硬度、高耐磨性和良好的耐热性;陶瓷和超硬材料如金刚工方式的不同,机械加 工工艺可以分为切削加工、磨 削加工、电火花加工等。
根据加工材料的不同,机械加 工工艺可以分为金属加工、非 金属加工等。
根据加工精度的不同,机械加 工工艺可以分为粗加工、半精 加工、精加工等。
机械加工工艺过程培训课件ppt

个性化定制产品将越来越多
随着消费者需求的多样化,个性化定制产品将越来越多,对机械制造 企业的生产能力和技术水平提出更高要求。
谢谢观看
机械加工分类
根据加工方式的不同,机械加工 可分为切削加工和磨削加工两大 类。切削加工又可分为车削、铣 削、钻削、镗削、磨削等。
工艺流程及组成要素
工艺流程
制定工艺规程,选择定位基准和加工 方法,安排加工顺序和工序内容,确 定工艺参数及检验方法等。
组成要素
包括机床、夹具、刀具、量具等工艺 装备以及切削液、润滑油等辅助材料 。
冷却
以不同速度冷却,获得不 同的组织和性能。
热处理对零件性能影响
01
02
03
04
提高硬度和强度
通过淬火等热处理方法,可以 提高零件的硬度和强度,增加
耐磨性和抗疲劳性。
改善韧性
通过回火等热处理方法,可以 改善零件的韧性,减少脆性。
消除内应力
通过退火等热处理方法,可以 消除零件内部的内应力,减少
变形和开裂倾向。
机械加工工艺过程培训课件ppt
目录
• 机械加工工艺概述 • 切削原理及设备介绍 • 夹具设计原理及应用实例 • 量具使用与测量方法 • 热处理技术在机械加工中应用 • 表面处理技术在机械加工中应用 • 总结回顾与展望未来发展趋势
01
机械加工工艺概述
机械加工定义与分类
机械加工定义
利用切削工具或磨具去除或改变 工件材料形状、尺寸和表面质量 等,以达到预期设计要求的工艺 过程。
化学法特点
利用化学反应在材料表面形成新的化 合物或改变原有化合物的性质,如电 镀、化学镀、氧化等。
机加工及其工艺培训教材

图1.1-1工艺过程的组成表1.1-1工艺过程各组成局部的含义名称含义工序一个或一组工人,在一个工作地对同一个或同时对几个工件所连续完成的那一局部工艺过程安装工件经一次装夹后所完成的那一局部工序工位为完成一定的工序局部,一次装夹工件后,工件〔或装配单元〕与夹具或设备的可动局部一起相对刀具或设备的固定局部所占据的每一个位置所完成的那一局部工序工步在加工外表(或装配时的连接外表)和加工(或装配)工具不变的情况下,所连续完成的那一局部工序走刀在一个工步内当加工外表切削佘量较大,需分几次切削时,那么每一次切削称为一次走刀§1.2组成局部的区不区分工序的要紧依据是工作地〔或设备〕是否变动和完成的那一局部工艺内容是否连续。
图1.2-1所示的圆盘零件,单件小批生产时其加工工艺过程如表1.2-1所示;成批生产时其加工工艺过程如表1.2-2所示。
表1.2-1圆盘零件单件小批机械加工工艺过程工序号工序名称工装工步工序内容设备1 车削Ⅰ(用三爪自定心卡盘夹紧毛坯小端外圆)车床1 车大端面2 车大端外圆至φ1003 钻φ20孔4 倒角Ⅱ〔工件调头,用三爪卡盘夹紧毛坏大端外圆〕5 车小端端面,保证尺寸35mm6 车小端外圆至φ48,保证尺寸20mm7 倒角2 钻削Ⅰ〔用夹具装夹工件〕钻床1 依次加工三个φ8孔2 在夹具中修往孔口的锐边和毛刺表1.2-2圆盘零件成批机械加工工艺过程工序号工序名称工装工步工序内容设备1 车削Ⅰ(用三爪自定心卡盘夹紧毛坯小端外圆)车床11 车大端面2 车大端外圆至φ1003 钻φ20孔图1.2-1圆盘零件4 倒角2 车削Ⅰ〔以大端面涨胎心轴〕车床21 车小端端面,保证尺寸35mm2 车小端外圆至φ48,保证尺寸20mm3 倒角3 钻削Ⅰ〔钻床夹具〕钻床1 钻三个φ8孔4 钳工Ⅰ 1 修孔口的锐边和毛刺由表1.2-1可知,该零件的机械加工分车削和钻削两道工序。
因为两者的操作工人、机床及加工的连续性均已发生变化。
机械加工工艺基础知识讲解培训课件

❖ 例如,在车床上加工轴,先从一端加工 出部分表面,然后调头再加工另一端,这 时的工序内容就包括两个安装。
15
❖ (3)工位
❖ 采用转位(或移位)夹具、回转工作 台或在多轴机床上加工时,工件在机床 上一次装夹后,要经过若干个位置依次 进行加工,工件在机床上所占据的每一 个位置上所完成的那一部分工序就称为 工位。
机械加工工艺系统由金属切削机床、刀具、 夹具和工件四个要素组成,它们彼此关联、互 相影响。
该系统的整体目的是在特定的生产条件下, 在保证机械加工工序质量的前提下,采用合理 的工艺过程,降低该工序的加工成本。
8
❖(3)机械制造系统
在工艺系统基础上以整个机械加 工车间为整体的更高一级的系统。该 系统的整体目的就是使该车间能最有 效地全面完成全部零件的机械加工任 务。
形状、尺寸、相对位置和性质等,使其成为成品 或半成品的过程称为工艺过程。 ❖ 工艺:就是制造产品的方法。 ❖ 机械加工工艺过程:采用机械加工的方法,直接 改变毛坯的形状、尺寸和表面质量等,使其成为 零件的过程称为机械加工工艺过程。
2
❖ 生产过程
❖ 工业产品的生产过程:是指由原材料到成品之 间的各个相互联系的劳动过程的总和。
❖ 例如轴类零件如果要切去的金属层很厚,则 需分几次切削,这时每切削一次就称为一次走刀。 因此在切削速度和进给量不变的前提下刀具完成 一次进给运动称为一次走刀。
❖ 下图是一个带半封闭键槽阶梯轴两种生产类 型的工艺过程实例,从中可看出各自的工序、安 装、工位、工步、走刀之间的关系。
19
20
基本概念
17
❖ (4)工步
❖ 在加工表面、切削刀具、切削速度 和进给量不变的条件下,连续完成的那 一部分工序内容称为工步。生产中也常 称为“进给”。
机械加工工艺规程培训课件4)

PART 02
零件加工工艺流程设计
零件结构分析
01
02
03
零件类型
确定零件的类型,如轴类 、盘类、箱体类等。
零件材料
了解零件所使用的材料, 如钢铁、有色金属、非金 属材料等。
零件结构特点
分析零件的结构特点,如 形状、尺寸、精度等。
加工方法选择
粗加工
选择合适的机床和刀具, 对零件进行粗加工,去除 多余的材料。
精加工
选择精确的机床和刀具, 对零件进行精加工,达到 所需的精度和表面质量。
热处理
根据零件材料和加工要求 ,选择合适的热处理方法 ,如淬火、回火等。
工艺流程制定
01
02
03
04
工艺路线
根据加工方法选择和零件结构 特点,制定合理的工艺路线。
工序安排
将加工过程划分为若干个工序 ,并合理安排工序的顺序。
将制定的改进措施付诸实践,并对实施过程进行监控,确保措施的有 效性和可行性。同时,根据实施情况对措施进行持续改进和优化。
PART 06
安全操作规范与培训计划
安全操作规范制定
明确机械加工设备操作规程
01
包括设备启动、运行、停止等步骤,以及安全注意事项和紧急
处理措施。
制定安全操作规程
02
针对不同机械加工设备,制定相应的安全操作规程,包括操作
质量检测与控制方法
质量检测标准与流程
质量检测标准
制定明确的质量检测标准,包括外观、尺寸、性能等方面,确保产品符合设计要 求和客户期望。
质量检测流程
建立规范的质量检测流程,包括来料检验、过程检验和成品检验等环节,确保产 品在各个阶段都经过严格的质量控制。
质量控制方法应用
机械制造工艺基础培训教材(49张PPT)

生产过程——将原材料转变为成品的全过程。
生产过程与工艺过程的关系 3.表面处理工序的安排 2.热处理工序的安排
孔加工方案
平面加工方案
2.选择表面加工方法考虑要点
(1)确定加工方法及分几次加工。 (2)考虑被加工材料的性质。 (3)根据生产类型,考虑生产率和经济性等问题。 (4)根据本企业(或本车间)的现有设备情况和 技术水平,充分利用现有设备,挖掘企业潜力。
?大量生产第二节定位基准的选择一基准及其分类基准用来确定生产对象上几何要素间的几何关系的那些点线面是几何要素之间位置尺寸标注计算和测量的起点
第一节 机械加工工艺过程的组成和特征
一、生产过程与工艺过程
1.生产过程
生产过程——将原材料转变为成品的全过程。
2.工艺过程
工艺过程——在生产过程中,直接改变原材料(或毛坯) 形状、尺寸和性能,使之变为成品或半成品的过程。
在设计图样上,以设 计基准为依据,标出一定 的尺寸或相互位置要求。
主要设计基准
2.工艺基准
工艺基准——工艺过程中所采用的基准。
工序基准 定位基准 测量基准(1)工序基准工序基准——在工序图上用来确定本工序所加工表 面加工后的尺寸、形状、位置的基准。
(2)定位基准
定位基准——在加工中 用作定位的基准。定位基准 用来确定工件在机床上或夹 具中的正确位置。
二、加工阶段的划分
粗加工阶段:切除工件各加工表面的大部分余量。在 粗加工阶段,主要的问题是如何提高生产率。
半精加工阶段:达到一定的准确度要求,完成次要表 面的最终加工,并为主要表面的精加工作好准备。
精加工阶段:完成各主要表面的最终加工,使工件的 加工精度和加工表面质量达到图样规定的要求。
机械加工工艺过程培训课件ppt)ppt
热处理
热处理是将零件加热到一 定温度,并进行保温或冷 却,以达到改变材料机械 性能的目的。
热处理的方法有很多种, 包括淬火、回火、退火等 ,不同的方法适用于不同 的材料和零件。
热处理过程中需要注意控 制加热的温度、时间和冷 却速度,以保证零件的机 械性能。
表面处理
表面处理是对零件表面进行涂覆、喷 涂、电镀等处理,以达到防腐、耐磨 、美观等目的。
机械加工工艺过程培 训课件
汇报人:可编辑 2023-12-23
• 机械加工工艺概述 • 机械加工工艺流程 • 机械加工工艺参数 • 机械加工工艺设备 • 机械加工工艺案例分析
目录
Part
01
机械加工工艺概述
机械加工工艺的定义
机械加工工艺是将原材料转化为成品的过程,涉及一系列的工艺步骤和操作,包括切割 、磨削、钻孔、车削等。
选择合适的刀具角度需要根据工件材 料、刀具材料、切削速度和进给量等 因素综合考虑。
刀具材料
刀具材料是影响机械加工质量和效率 的重要因பைடு நூலகம்之一。常用的刀具材料包 括高速钢、硬质合金、陶瓷和立方氮 化硼等。
选择合适的刀具材料需要根据工件材 料、切削速度、进给量和切削深度等 因素综合考虑。
Part
04
机械加工工艺设备
切削深度
切削深度是指刀尖在工件上切削的深度,也称为背吃刀量 。增大切削深度可以提高加工效率,但过大的切削深度会 导致刀具承受的切削力增大,刀具磨损加剧。
选择合适的切削深度需要根据工件材料、刀具材料、切削 速度和进给量等因素综合考虑。
刀具角度
刀具角度是指刀具切削刃相对于刀具 基面或切削平面之间的夹角。刀具角 度对切削力、切削热、切屑形态和刀 具磨损等都有影响。
机械加工工艺培训教材
五 加工效率及经济性
A、数控机床(CNC)应用; B、自动化/快换化夹具应用; C、低成本自动化(LCA)应用; D、现场动作/布局优化(IE工程);
第三部分 刀具及冷却液
一、刀具材料及其应用 二、常用冷却液
一 刀具材料及其应用
A、工具钢:手工工具广泛应用 /牌号有:T10A/T8A 如:锉刀/手工锯条/刮刀 B、高速钢/峰钢/白钢:牌号有:W18Cr4V 如:钻头/螺纹刀具/车刀/铣刀 C、硬质合金:牌号有:YT15/YG8/YW1 如:机夹刀片/车刀片/焊接式刀头 D、人造金刚石(PCD)如:修磨砂轮用工具 E、立方氮化硼(CBN)只适宜干切削
> 630 ~1000
2.0
+1 -0.4
表2、镗孔/铰孔加工余量及其偏差(MM)
公称孔径D
≤6
镗孔余量D
/
铰孔余量D
0.05
>6~10 > 10 ~18 >18 ~30 >30 ~50 >50 ~60
0.5-10
0.8-1.4
0.1
0.15
0.2
0.25
0.3
我司现采用的机加工余量一般取0.3~0.5mm。
四 加工质量
加工质量由加工精度和加工表面质量两项指标: A、加工精度:指零件加工后实际几何参数(尺寸、形
状和表面间相互位置)与理想几何参数的符合程度。 B、加工表面质量: 1、已加工表面的结几何形状特征。表面粗糙度/波度/
纹理 2、已加工表面层的物理品质。加工硬化程度/冷硬层深
度/表面层残余应力/表面层金相组织变化
动的切削方式; 四、齿轮加工机床 滚齿机:利用齿轮滚刀按展成法加工齿面的方法。
第一部分 基础知识
一、公差与配合 二、形状和位置公差 三、图例解析
机械加工工艺过程培训课件ppt)ppt
进给量
总结词
进给量是指切削工具在单位时间内沿进给方向移动的距离,它决定了切削层的厚度和切削宽度。
详细描述
进给量的大小对切削效率、加工表面质量和刀具寿命也有影响。增加进给量可以减少切削时间,提高 加工效率,但过大的进给量可能导致切削力增大,刀具磨损加快。因此,需要根据具体的加工要求和 刀具性能来选择合适的进给量。
CHAPTER
毛坯制造
毛坯制造方法
根据零件材料和尺寸要求,选择 合适的毛坯制造方法,如铸造、 锻造、焊接等。
毛坯质量要求
确保毛坯的尺寸、形状和表面质 量符合机械加工要位
定位原理
根据零件的几何特征和加工要求,选 择合适的定位基准和定位元件,确保 零件在加工过程中稳定可靠。
成型加工是指通过模具或成型工具对 材料进行塑性变形,以获得所需形状 和尺寸的加工方式,如锻造、铸造等 。
切削加工是指通过切削工具对材料进 行切削,以获得所需形状和尺寸的加 工方式,如铣削、车削等。
特种加工是指采用特殊的加工方法和 设备,对材料进行加工的加工方式, 如激光切割、电火花加工等。
02 机械加工工艺流程
切削速度
总结词
切削速度是指切削工具在切削过程中相对于 工件表面的线速度。
详细描述
切削速度是影响切削效率、加工表面质量和 刀具寿命的重要因素之一。提高切削速度可 以减少切削时间,提高加工效率,但过高的 切削速度可能导致切削力增大、工件表面粗 糙度增加或刀具磨损加快。因此,需要根据 具体的加工要求和材料特性来选择合适的切 削速度。
02
机械加工工艺是制造业的核心技 术之一,广泛应用于汽车、航空 、电子、能源等领域。
机械加工工艺的重要性
机械加工工艺是实现产品设计的重要 手段,是制造业的基础和支撑。
机械加工工艺基础培训课件
工艺路线的拟定
经济精度:在正常加工条件下所能达到的加工精度及表面粗糙度
各种表面不同加工方法的经济精度及表面粗糙度
加工 表面
加工 方法
外圆柱面 和端面
粗车 半精车 精车 粗磨 精磨 研磨 超精加工 金刚车
平面
粗刨(铣) 精刨(铣) 粗磨
经济精度 等级IT
11~13 9~10 7~8 8~9 6 5 5~6 6
Kr =νc60 /(νc60)j Kr越大,性能越好.
机加工工艺过程的基本概念
1.生产过程和工艺过程 生产过程:将原材料转变为成品的全过程。 工艺过程:改变生产对象的形状、尺寸、相对位置和性质,
使其成为成品或半成品的过程。
工艺过程是生产过程的主要部分,其余为辅助过程。
2.工艺过程的组成
工序
安装1 安装2
精磨 刮研 研磨
经济精度 等级IT
11~12 11~12 8~9 7~8 7~8 6~7 6~7 5~6
6~7 6~7 5
表面粗 糙度
μm
12.5~25 6.3~12.5 1.6~3.2 0.8~1.6 0.2~0.8 0.1~0.2 0.025~0.1 0.025~0.1
0.16~1.25 0.16~1.25 0.006~0.1
11~13 8~10 8~9
表面粗 糙度
μm
12.5~50 3.2~6.3 0.8~1.6 0.4~0.8 0.1~0.4 0.012~0.1 0.012~0.1 0.025~0.4
12.5~50 1.6~6.3 1.25~5
加工 表面
圆柱 孔
平面
加工 方法
钻孔 粗镗 半精镗 精镗、铰 粗磨 精磨 珩磨 研磨
正常磨损阶段: 此阶段磨损速度减慢,磨损量随时间的增加均 匀增加,切削稳定,是刀具的有效工作阶段。